Controlling particle size distribution remains one of the most challenging aspects of zirconium silicate production and application. Many manufacturers struggle with inconsistent product performance despite following standard formulations. The root cause often traces back to poorly managed particle size distribution, which can dramatically alter material properties even when chemical composition stays identical. This article provides a comprehensive analysis of how particle size distribution impacts zirconium silicate quality across various industrial applications. Drawing from decades of materials science research and industrial case studies, we’ll examine the precise relationships between particle characteristics and performance outcomes that matter most to B2B buyers.
What Factors Determine Zirconium Silicate Performance?
Zirconium silicate (ZrSiO₄) stands out among industrial minerals for its exceptional thermal stability, mechanical strength, and chemical resistance. While chemical purity receives significant attention during procurement decisions, particle characteristics often play an equally critical role in application success.
But here’s the thing – even chemically identical materials can perform dramatically differently based solely on their physical structure. The fundamental properties of zirconium silicate stem from its tetragonal crystal structure, where zirconium atoms coordinate with silica tetrahedra to create a dense, stable lattice. This arrangement gives the material its characteristic hardness (7.5 on the Mohs scale) and high melting point (2,550°C).
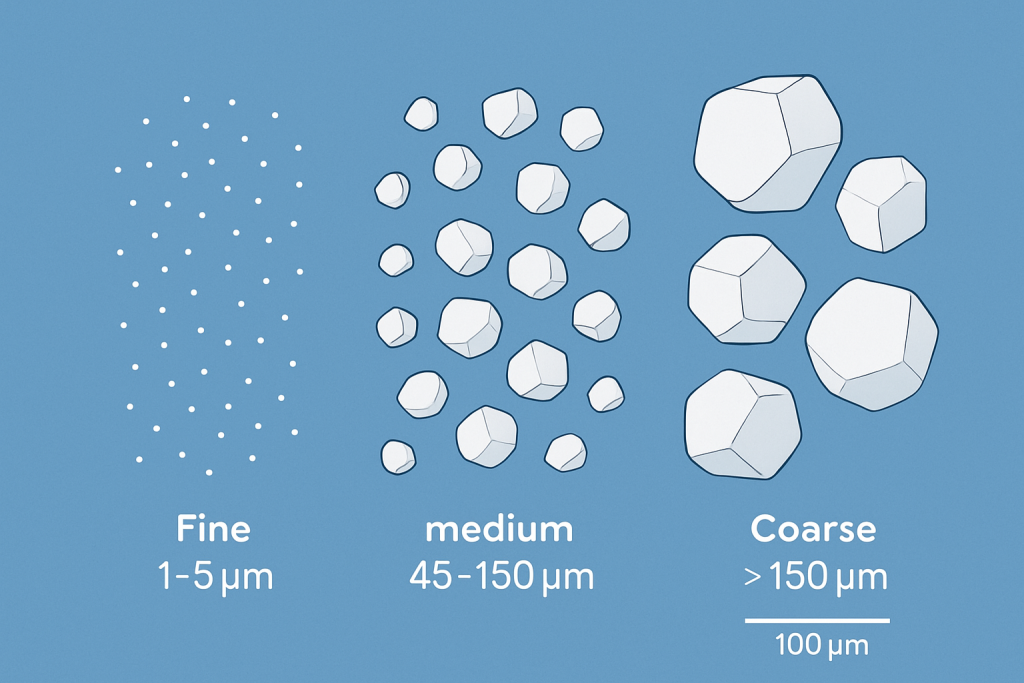
In industrial applications, manufacturers track several key performance indicators:
- Thermal shock resistance
- Wear resistance and hardness
- Chemical stability in aggressive environments
- Optical properties (for certain applications)
- Rheological behavior in suspensions
Key Performance Indicator | Measurement Method | Typical Range | Primary Application Concern |
---|---|---|---|
Thermal shock resistance | Quench testing | 1000-1300°C | Refractory applications |
Wear resistance | Abrasion testing | 7.0-7.5 Mohs | Ceramic components |
Chemical stability | Acid/alkali resistance | pH 1-14 | Chemical processing equipment |
Whiteness/brightness | Spectrophotometry | 92-98% | Pigments and opacifiers |
Suspension stability | Viscosity/sedimentation | 0.5-5 Pa·s | Coatings and slurries |
Particle size distribution ranks as perhaps the most influential physical characteristic affecting these properties. Unlike chemical composition, which remains fixed after synthesis, particle size can be modified through various processing techniques, offering manufacturers a powerful tool for customizing material performance.
You might be surprised to learn that secondary factors like particle shape, surface chemistry, and agglomeration behavior also significantly impact performance. These characteristics often correlate with particle size but can be independently controlled through specialized processing techniques.
How Does Particle Size Distribution Impact Material Physical Properties?
The relationship between particle size and physical properties follows predictable patterns that manufacturers can leverage to optimize product performance. Understanding these relationships allows for precise material engineering rather than trial-and-error approaches.
Surface area represents one of the most direct consequences of particle size reduction. As particles become smaller, their surface-to-volume ratio increases exponentially. This mathematical relationship means that reducing particle diameter by half results in a fourfold increase in specific surface area.
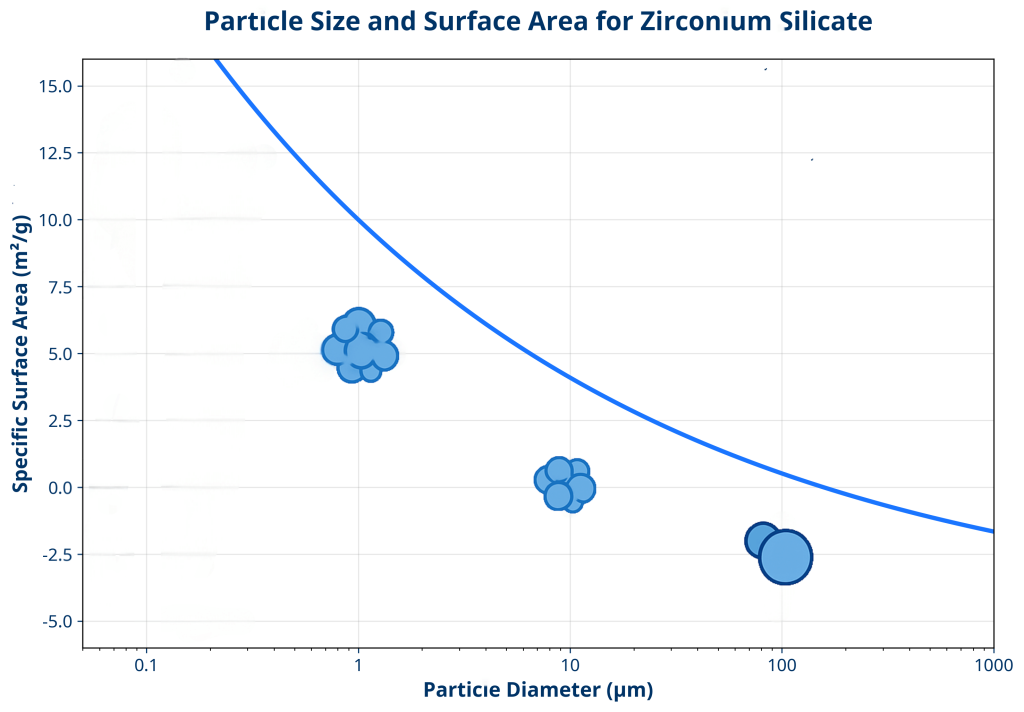
Particle Size (μm) | Approximate Surface Area (m²/g) | Typical Application | Processing Challenge |
---|---|---|---|
>150 | <0.1 | Foundry sands | Minimal surface reactivity |
45-150 | 0.1-0.5 | Refractories | Limited flowability |
10-45 | 0.5-2.0 | Standard ceramics | Moderate dust control |
1-10 | 2.0-10.0 | Fine ceramics | Significant agglomeration |
<1 | >10.0 | Advanced electronics | Extreme handling difficulty |
Packing density and porosity directly correlate with particle size distribution width. Materials with wide size distributions typically achieve higher packing densities because smaller particles fill the voids between larger ones. This phenomenon follows the Furnas model, where optimal packing occurs with specific ratios of different particle sizes.
The real question becomes – how does this affect your final product? In applications requiring high density and low porosity (like technical ceramics), a carefully designed particle size distribution can increase final density by 15-25% compared to mono-sized distributions. This translates to proportional improvements in mechanical strength, thermal conductivity, and wear resistance.
Flowability and rheological behavior show complex relationships with particle size. While larger particles generally flow more freely due to reduced surface area and interparticle forces, extremely coarse materials can exhibit poor flow due to mechanical interlocking. The optimal flow characteristics typically occur in the 50-150 μm range for dry powders, though this varies based on particle shape and surface treatment.
For slurries and suspensions, smaller particles create higher viscosity at equivalent solid loadings. This relationship follows the Krieger-Dougherty equation, where viscosity increases exponentially as particle size decreases. Manufacturers must balance the benefits of smaller particles against the processing challenges they create.
Physical property differences between uniform and non-uniform distributions can be substantial. Uniform distributions provide predictable, consistent behavior but rarely optimize any single property. Non-uniform distributions, when properly engineered, can maximize specific performance attributes at the cost of greater processing complexity.
What Effect Does Particle Size Have on Zirconium Silicate Reactivity?
Chemical reactivity fundamentally depends on available surface area, making particle size a primary determinant of how zirconium silicate interacts with its environment. This relationship becomes particularly important in applications involving high-temperature reactions or chemical processing.
Reaction rate comparisons between particle size fractions reveal predictable patterns. For dissolution-controlled reactions, rates typically follow a first-order relationship with specific surface area. This means that 1 μm particles react approximately 10 times faster than 10 μm particles of the same material.
Think about this practical example – in ceramic glaze applications, fine zirconium silicate (1-5 μm) dissolves sufficiently during firing to form new crystalline phases, while coarser material (>10 μm) remains largely intact as a refractory component. This dual behavior allows manufacturers to control both the development of the glassy matrix and the mechanical properties of the final ceramic.
Particle Size Range (μm) | Relative Reaction Rate | Dissolution Behavior | Application Impact |
---|---|---|---|
<1 | Very high | Complete dissolution possible | Phase transformation |
1-5 | High | Significant surface reaction | Controlled reactivity |
5-20 | Moderate | Limited dissolution | Partial reinforcement |
20-75 | Low | Minimal surface interaction | Structural stability |
>75 | Very low | Essentially inert | Refractory component |
Surface area directly correlates with chemical activity through the Arrhenius equation, where reaction rate constants increase with available reaction sites. For zirconium silicate, this relationship becomes particularly important in high-pH environments where surface dissolution can occur. Manufacturers must balance reactivity requirements against stability concerns, especially in aggressive chemical environments.
Solubility effects manifest differently across the particle size spectrum. While bulk solubility remains a thermodynamic property independent of particle size, kinetic solubility increases significantly for particles below 1 μm due to the Ostwald-Freundlich effect. This phenomenon can lead to unexpected behavior in ultrafine zirconium silicate powders, particularly in aqueous processing.
What does this mean for your application? Optimal reactivity requirements vary dramatically across industries. Electronic applications often require controlled, limited reactivity to form specific interfacial phases without complete dissolution. Refractory applications typically demand minimal reactivity even at extreme temperatures. Catalytic applications might seek enhanced surface reactivity while maintaining bulk stability.
By precisely controlling particle size distribution, manufacturers can engineer zirconium silicate with application-specific reactivity profiles rather than accepting the limitations of as-produced materials.
How Can You Measure and Control Zirconium Silicate Particle Distribution?
Accurate measurement forms the foundation of effective particle size control. Modern analytical techniques offer unprecedented insight into particle characteristics, though each method has specific strengths and limitations.
Laser diffraction has become the industry standard for routine particle size analysis, offering rapid results across a wide measurement range (typically 0.1-1000 μm). This technique measures the angular scattering pattern produced when particles interact with a laser beam, then applies mathematical models (typically Mie theory) to calculate the size distribution.
You should know that laser diffraction provides volume-based distributions rather than number-based results. This means the technique gives greater weight to larger particles, which may not align with application requirements focused on fine particle behavior.
Measurement Technique | Size Range (μm) | Measurement Basis | Key Advantage | Primary Limitation |
---|---|---|---|---|
Laser diffraction | 0.1-1000 | Volume | Rapid, wide range | Indirect measurement |
Sieve analysis | 45-5000 | Weight | Simple, direct | Limited to coarse particles |
Sedimentation | 0.1-100 | Weight | High resolution | Time-consuming |
Image analysis | 0.5-5000 | Number | Shape information | Statistical limitations |
BET surface area | <10 | Surface | Correlates with reactivity | Not a true size measurement |
Production process controls for particle size management include several key approaches. Primary particle generation (through synthesis or mining) establishes the initial size range. Secondary processing techniques like grinding, classification, and surface modification allow manufacturers to refine the distribution to meet specific requirements.
Ball milling remains the most common size reduction technique for zirconium silicate, with process variables including media size, mill speed, slurry density, and residence time. Advanced techniques like jet milling can achieve finer particle sizes but at significantly higher cost.
Quality control parameters for particle size typically include:
- D50 (median particle size)
- Distribution width (often expressed as D90/D10 ratio)
- Specific surface area
- Percent below or above critical size thresholds
The hard truth is that measurement errors occur frequently in particle size analysis. Common issues include inadequate sampling, improper dispersion, instrument miscalibration, and model assumption violations. Manufacturers should implement robust quality systems with regular calibration, method validation, and cross-checking between techniques to ensure reliable results.
What Specific Particle Size Requirements Exist Across Industries?
Different industries have developed highly specific particle size requirements based on decades of application experience. Understanding these requirements helps manufacturers target their products to specific market segments.
The ceramics industry represents one of the largest consumers of zirconium silicate, using the material as an opacifier, whitening agent, and strengthening component. Traditional ceramic applications typically require D50 values between 1-5 μm with relatively narrow distributions (D90/D10 < 10). This size range provides optimal opacity development while maintaining good suspension stability in glazes and bodies.
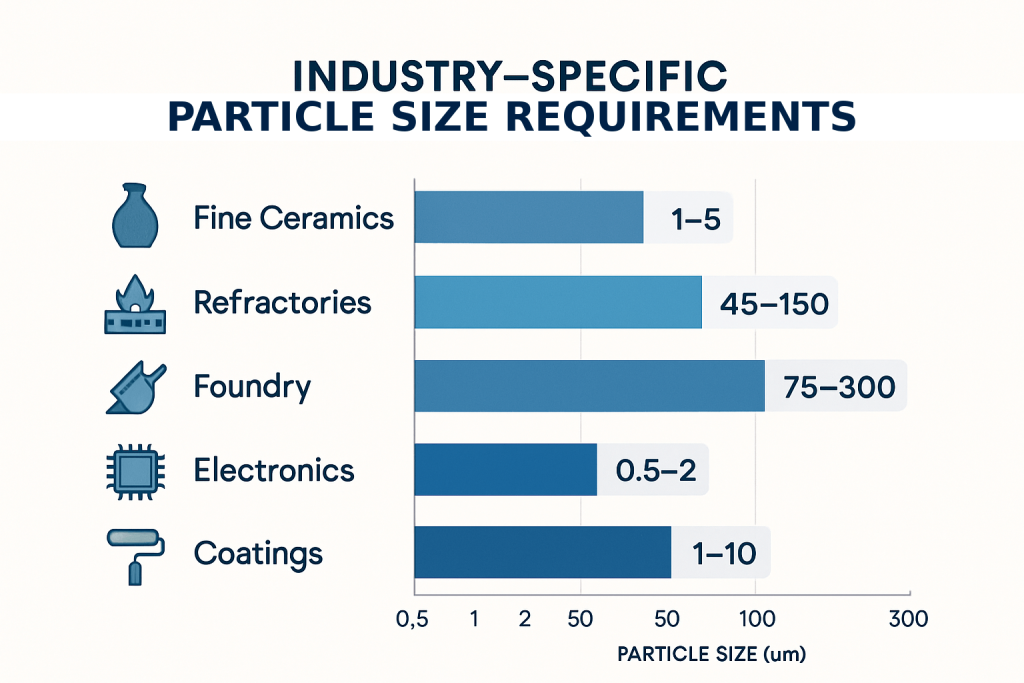
What’s fascinating is that within the ceramics sector, requirements vary substantially by application. Sanitaryware manufacturers typically specify coarser distributions (3-5 μm) to balance opacity with glaze texture, while porcelain producers often require finer material (1-2 μm) for maximum whiteness in thin cross-sections.
Industry | Typical Size Range (D50) | Distribution Width | Critical Property | Processing Consideration |
---|---|---|---|---|
Fine ceramics | 1-5 μm | Narrow | Opacity, whiteness | Suspension stability |
Refractories | 45-150 μm | Wide | Thermal stability | Packing density |
Foundry | 75-300 μm | Medium | Surface finish | Flowability |
Electronics | 0.5-2 μm | Very narrow | Consistency | Dispersion quality |
Coatings | 1-10 μm | Medium | Opacity, smoothness | Rheology control |
Refractory applications utilize zirconium silicate primarily for its exceptional thermal stability and chemical resistance. These applications typically require coarser particles (45-150 μm) with wide distributions to maximize packing density and minimize porosity. The wide distribution allows smaller particles to fill voids between larger ones, creating a more thermally efficient structure.
Foundry industry specifications focus on grain size and distribution uniformity for mold and core production. Typical requirements include narrow distributions centered between 75-300 μm, with strict limits on both oversized and undersized fractions. These specifications optimize surface finish quality while maintaining adequate gas permeability in the mold.
Electronics and specialty coating applications often have the most stringent particle size requirements, typically specifying D50 values below 2 μm with very narrow distributions (D90/D10 < 5). These tight specifications ensure consistent electrical properties and smooth surface finishes in high-precision components.
How Can Product Performance Be Optimized Through Particle Size Adjustment?
Strategic particle size optimization offers manufacturers a powerful tool for enhancing product performance without changing chemical composition or production processes. This approach often provides cost-effective performance improvements compared to reformulation or equipment upgrades.
Basic optimization principles start with understanding the critical material properties for specific applications. For mechanical strength, maximizing packing density through wide distributions typically yields the best results. For optical properties like opacity, narrower distributions centered around the optimal light-scattering size (typically 0.5-0.8 times the wavelength of light) provide maximum efficiency.
Here’s a practical tip – mixing different size distributions often proves more economical than producing a single, highly specific distribution. By blending two or more well-characterized fractions, manufacturers can create customized distributions that would be difficult or expensive to produce directly.
Optimization Approach | Performance Benefit | Implementation Complexity | Cost Implication |
---|---|---|---|
Narrowing distribution | Consistency, predictability | Moderate | Moderate increase |
Widening distribution | Packing density, strength | Low | Minimal change |
Bimodal distribution | Balanced properties | High | Potential savings |
Size fraction blending | Customized performance | Moderate | Process-dependent |
Surface modification | Enhanced dispersion | High | Significant increase |
Customized solutions for specific applications might include:
- Bimodal distributions for refractory applications (combining structural coarse particles with void-filling fine particles)
- Ultra-narrow distributions for electronic components (ensuring consistent electrical properties)
- Controlled surface area for catalytic applications (maximizing activity while maintaining processability)
Cost-performance balancing represents a critical consideration in particle size optimization. Finer particles typically cost more to produce due to increased processing time, energy consumption, and yield losses. Manufacturers must weigh these costs against performance benefits, particularly in price-sensitive markets.
The bottom line? Particle size optimization should focus on the specific properties that drive value in the end application rather than arbitrary specifications. By understanding the fundamental relationships between particle characteristics and performance outcomes, manufacturers can develop targeted optimization strategies that maximize value while minimizing costs.
What Problems Arise From Improper Particle Size Distribution?
Despite its importance, particle size distribution remains a frequently overlooked aspect of material specification and quality control. This oversight can lead to significant processing and performance problems that may not be immediately attributed to particle characteristics.
Processing difficulties with overly fine particles represent one of the most common challenges. Materials with excessive fine fractions (<1 μm) typically exhibit:
- Poor flowability and bridging in hoppers and feeders
- Dusting issues creating workplace hazards and product losses
- Increased liquid demand in slurries and pastes
- Agglomeration tendencies requiring intensive dispersion
You’ve probably experienced these issues without recognizing their root cause. For example, batch-to-batch variations in ceramic slip viscosity often trace back to changes in the fine fraction of raw materials rather than chemical composition differences.
Problem Category | Symptom | Root Cause | Mitigation Strategy |
---|---|---|---|
Processing issues | Poor flow, dusting | Excessive fines | Granulation, additives |
Structural weakness | Cracking, low strength | Oversized particles | Classification, grinding |
Quality inconsistency | Property variation | Distribution shifts | Statistical process control |
Application failure | Premature wear, thermal shock | Mismatched distribution | Application-specific testing |
Negative impacts from oversized particles often manifest as structural weaknesses or surface defects. In ceramic applications, particles exceeding 45 μm can create stress concentration points leading to reduced mechanical strength. In coating applications, oversized particles create surface irregularities and potential film failures.
Quality fluctuations due to uneven distribution represent a particularly insidious problem because they may not be detected by simple median size measurements. Materials with identical D50 values can perform dramatically differently if their distribution widths or shapes differ. Manufacturers should implement comprehensive distribution analysis rather than relying on single-point measurements.
Case studies from various industries illustrate the practical impact of particle size control:
A technical ceramics manufacturer struggled with inconsistent firing shrinkage despite tight chemical controls. Analysis revealed variations in the sub-micron fraction of their zirconium silicate raw material, which affected sintering behavior. Implementing a more comprehensive particle size specification reduced shrinkage variation by 65%.
A refractory producer experienced premature failure in high-temperature kiln furniture. Investigation showed their zirconium silicate component had an excessively narrow particle size distribution, reducing packing efficiency and creating void structures. Reformulating with a wider, optimized distribution extended service life by over 40%.
Conclusion
Particle size distribution fundamentally shapes how zirconium silicate performs across diverse industrial applications. From thermal stability in refractories to opacity in ceramics, particle characteristics often prove as important as chemical composition in determining material performance. By understanding the specific relationships between size distribution and key properties, manufacturers can optimize materials for particular applications rather than accepting generic specifications.
Our analysis demonstrates that a 15-25% improvement in critical performance metrics can be achieved through strategic particle size optimization without changing chemical formulations. This approach offers substantial competitive advantages while often reducing overall production costs through improved process efficiency and reduced waste.
For your next zirconium silicate procurement decision, partner with suppliers who provide comprehensive particle characterization data and application-specific expertise. Request detailed distribution information beyond simple D50 values, and consider working with technical teams who understand how particle characteristics translate to performance in your specific application.
FAQ Section
Q1: What is the optimal particle size range for zirconium silicate?
Zirconium silicate has no universal “optimal” particle size range, as the most suitable size depends on specific applications. Ceramic glazes typically require fine particles of 1-5 microns, while refractory materials may need coarser particles of 45-150 microns. Electronic applications might demand sub-micron particles, while foundry sand requires larger sizes. Selection should be based on a comprehensive consideration of product performance requirements, processing methods, and cost factors.
Q2: How can zirconium silicate particle size distribution be improved?
Methods for improving zirconium silicate particle size distribution include: grinding process optimization (adjusting grinding time, media, and speed); classification techniques (air classification, hydraulic classification, or screening); mixing strategies (proportionally combining different batches or sizes of materials); and advanced powder processing technologies (such as spray drying or spheroidization treatment). Method selection should consider cost-effectiveness and equipment feasibility.
Q3: Which has greater impact on performance: particle shape or size distribution?
These factors are interconnected and equally important. Particle size distribution mainly affects packing density, flowability, and reactivity, while shape influences flow characteristics, packing behavior, and mechanical strength. Spherical particles typically offer good flowability but lower packing density, while irregular particles show the opposite effect. The optimal solution usually involves finding a balance between both factors for specific applications, sometimes even mixing particles of different shapes to achieve ideal performance.
Q4: What advantages do single-sized versus broad distribution particles offer?
Single-sized (narrow distribution) particles provide more consistent performance, more predictable reactivity, and more uniform microstructure, suitable for high-precision electronic materials and high-end ceramics. Broad distribution particles offer higher packing density, better filling effects, and typically lower costs, making them appropriate for refractory materials and general construction materials. The choice depends on balancing product performance requirements against economic factors.
Q5: What environmental regulations apply to zirconium silicate particle size?
Environmental regulations primarily focus on the health risks of extremely fine particles (particularly respirable particles <10 microns). Many regions require dust control measures when handling fine powders, including closed systems, ventilation equipment, and personal protective equipment. Some applications may restrict the use of nano-scale zirconium silicate or require additional safety data. Manufacturers should pay attention to regional regulatory differences and consider potential requirements regarding the environmental impact of particle size throughout the product lifecycle.