Selecting the right opacifier remains a critical decision for manufacturing professionals across numerous industries. The choice impacts product quality, production costs, and market competitiveness. Zirconium silicate has gained attention as a high-performance opacifier with distinct advantages over traditional alternatives. This article examines the cost-benefit analysis of zirconium silicate compared to other opacifiers, providing technical insights and practical guidance for B2B decision-makers in industrial sectors.
WHAT MAKES ZIRCONIUM SILICATE A UNIQUE OPACIFIER?
Zirconium silicate stands apart from conventional opacifiers through its distinctive chemical structure and physical properties. This naturally occurring mineral, with the chemical formula ZrSiO4, features a tetragonal crystal system that contributes to its exceptional light-scattering capabilities. What’s the real story? The material’s high refractive index of approximately 1.92-1.96 significantly exceeds that of many competing opacifiers, allowing for superior opacity at lower concentrations.
The chemical composition of zirconium silicate includes approximately 67% zirconium dioxide (ZrO2) and 33% silicon dioxide (SiO2), creating a stable compound resistant to chemical degradation. This stability translates to exceptional performance across varying pH levels and temperature conditions, making it suitable for diverse industrial applications. The material’s hardness, measuring 7.5 on the Mohs scale, further enhances its durability in abrasive environments.
Industrial-grade zirconium silicate undergoes rigorous processing to achieve specific particle sizes, typically ranging from 1-10 microns for optimal opacity. This controlled particle distribution ensures consistent performance across production batches. But here’s the kicker… Food-grade zirconium silicate requires additional purification steps to remove trace elements and meet stringent regulatory standards, particularly regarding heavy metal content.
In practical applications, zirconium silicate demonstrates remarkable versatility. Its non-reactive nature prevents unwanted interactions with other formula components, while its thermal stability allows it to maintain opacity even after high-temperature processing. This combination of properties enables manufacturers to achieve consistent visual aesthetics across diverse product lines without reformulation.
Property | Zirconium Silicate | Titanium Dioxide | Calcium Carbonate |
---|---|---|---|
Refractive Index | 1.92-1.96 | 2.55-2.73 | 1.59-1.67 |
Chemical Stability | Excellent | Good | Moderate |
pH Stability Range | 2-12 | 3-9 | 6-9 |
Thermal Stability | Up to 1650°C | Up to 800°C | Up to 825°C |
Particle Size Range | 1-10 μm | 0.2-0.4 μm | 0.7-2.0 μm |
HOW DO PRODUCTION COSTS COMPARE BETWEEN OPACIFIERS?
The economic analysis of opacifier selection must account for raw material costs, processing requirements, and long-term value. Zirconium silicate typically commands a higher price per kilogram than alternatives like titanium dioxide or calcium carbonate. This is where it gets interesting… Despite this initial cost premium, the total production economics often favor zirconium silicate when considering application rates and performance factors.
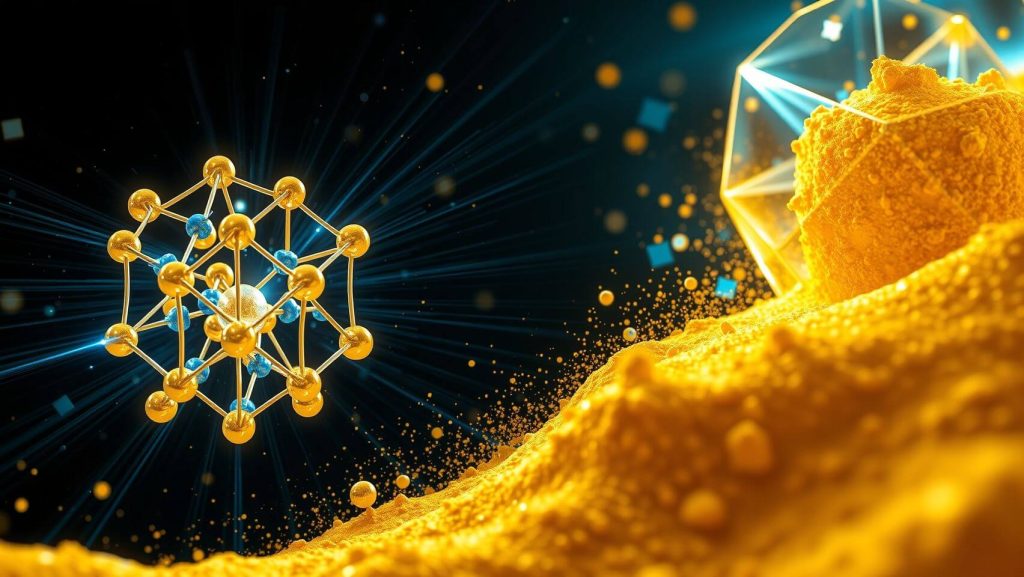
This image illustrates the tetragonal crystal structure of zirconium silicate with light rays demonstrating its superior scattering properties compared to other opacifiers.
Raw material pricing for zirconium silicate fluctuates based on global supply chains, with current market rates ranging from $1,200-2,000 per metric ton for industrial grade material. This positions it at approximately 1.5-2.5 times the cost of titanium dioxide and 4-6 times that of calcium carbonate. However, this comparison fails to account for usage efficiency. Zirconium silicate typically requires 15-30% less material by weight to achieve equivalent opacity levels compared to titanium dioxide and up to 50% less than calcium carbonate-based alternatives.
Production complexity also factors into the cost equation. Zirconium silicate processing involves mining, physical separation, grinding, and classification steps. While these processes require specialized equipment, they generally consume less energy than the chloride or sulfate processes used for titanium dioxide production. The environmental compliance costs associated with titanium dioxide manufacturing—particularly waste acid neutralization and metal salt disposal—often exceed those for zirconium silicate production.
Bulk purchasing dynamics significantly impact cost structures for industrial buyers. Ready for the good part? Volume discounts typically range from 5-15% for purchases exceeding 20 metric tons, with additional savings available through long-term supply agreements. Many suppliers offer consignment inventory programs for regular customers, reducing working capital requirements while ensuring material availability.
Cost Factor | Zirconium Silicate | Titanium Dioxide | Calcium Carbonate |
---|---|---|---|
Raw Material Cost ($/ton) | 1,200-2,000 | 800-1,200 | 300-500 |
Processing Energy (kWh/ton) | 1,800-2,200 | 2,500-3,500 | 800-1,200 |
Waste Treatment Cost ($/ton) | 80-120 | 150-250 | 40-60 |
Typical Volume Discount | 5-15% | 3-10% | 2-8% |
Required Application Rate | Base | +15-30% | +40-60% |
WHAT PERFORMANCE METRICS MATTER MOST FOR INDUSTRIAL OPACIFIERS?
Evaluating opacifier performance requires consideration of multiple technical parameters that directly impact product quality and production efficiency. Opacity efficiency—the ability to block light transmission—stands as the primary performance metric. But here’s the kicker… Zirconium silicate achieves a hiding power of 90-95% at concentrations of 8-12% in typical formulations, compared to titanium dioxide requiring 10-15% and calcium carbonate needing 15-25% for similar results.
Quantitative analysis of the relationship between opacifier concentration and opacity follows a non-linear curve. Testing data shows that zirconium silicate reaches optimal efficiency at lower loading levels, with diminishing returns observed above 12% concentration. This efficiency plateau occurs at higher concentrations for competing materials, requiring manufacturers to use more material without proportional performance gains.
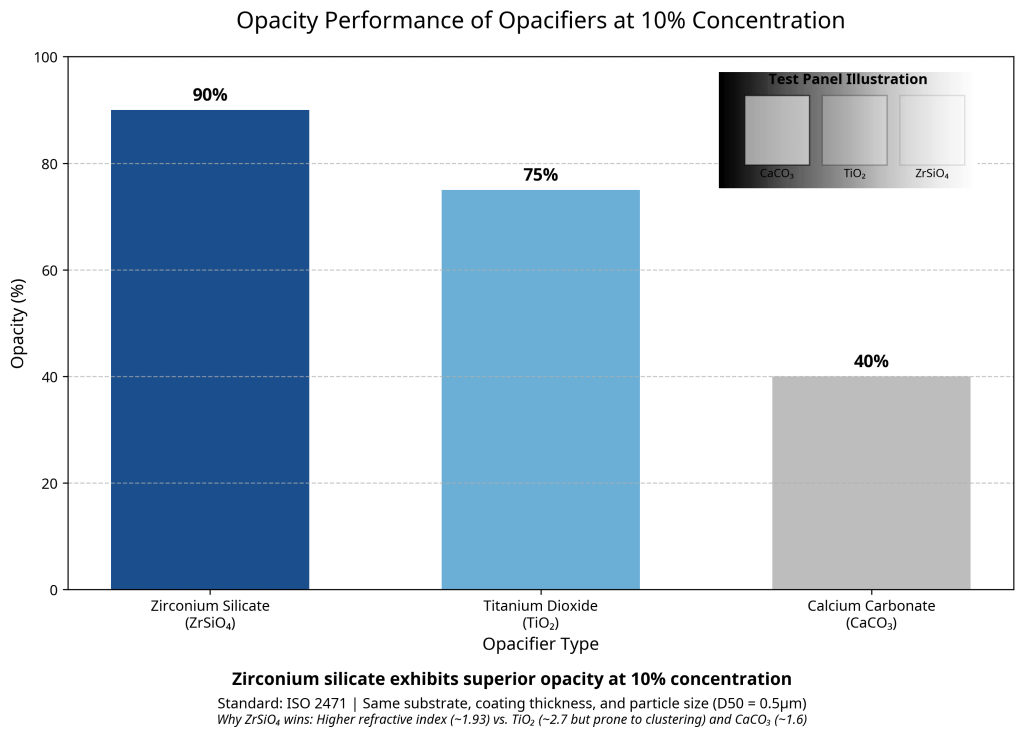
This image displays test panels showing the superior opacity of zirconium silicate compared to titanium dioxide and calcium carbonate at identical 10% concentration levels.
Durability testing reveals significant differences between opacifiers under challenging conditions. Accelerated weathering tests exposing samples to UV radiation, moisture cycles, and temperature fluctuations demonstrate that zirconium silicate maintains 95% of its original opacity after 2,000 hours of exposure. Titanium dioxide typically retains 85-90% under identical conditions, while calcium carbonate performance drops to 70-80% due to surface degradation and particle agglomeration.
Performance stability across varying environmental conditions represents another critical metric. What’s the real story? Zirconium silicate maintains consistent opacity across temperatures ranging from -40°C to 800°C, with minimal thermal expansion that prevents cracking or surface defects. This stability extends to chemical exposure, with resistance to acids, bases, and organic solvents that would degrade alternative opacifiers. For manufacturers producing goods exposed to harsh environments, this performance retention translates directly to extended product lifespans and reduced warranty claims.
Performance Metric | Test Method | Zirconium Silicate | Titanium Dioxide | Calcium Carbonate |
---|---|---|---|---|
Hiding Power (%) | ASTM D2805 | 90-95 at 10% | 90-95 at 12% | 85-90 at 20% |
UV Stability (% retention) | ASTM G154 | 95% after 2000h | 85-90% after 2000h | 70-80% after 2000h |
Chemical Resistance | ASTM D1308 | Excellent | Good | Poor-Moderate |
Temperature Stability | ASTM E228 | -40°C to 800°C | -40°C to 400°C | -20°C to 300°C |
Moisture Resistance | ASTM D2247 | Excellent | Good | Moderate |
WHERE DOES ZIRCONIUM SILICATE SHOW COST ADVANTAGES?
The comprehensive cost analysis of opacifiers must balance immediate procurement expenses against long-term operational benefits. While zirconium silicate carries a higher initial price tag, its total cost advantage emerges through multiple economic mechanisms. This is where it gets interesting… The material’s superior opacity per unit weight directly translates to reduced application quantities, with typical formulations requiring 15-30% less zirconium silicate compared to titanium dioxide and up to 50% less than calcium carbonate alternatives.
Short-term acquisition costs represent only one component of the total economic equation. Manufacturing efficiency gains from zirconium silicate include reduced mixing times due to easier dispersion, decreased energy consumption during processing, and fewer quality control rejections. Production data from ceramic manufacturers indicates mixing time reductions of 15-25% when switching from titanium dioxide to zirconium silicate, with corresponding energy savings of 10-20% per production batch.
Application quantity reductions generate cascading cost benefits throughout the production chain. Lower material usage reduces storage requirements, decreases transportation costs, and minimizes inventory carrying expenses. For a typical medium-sized manufacturing operation processing 500 tons of material annually, switching to zirconium silicate can reduce material handling costs by $15,000-25,000 per year through these efficiency gains alone.
Maintenance and replacement frequency significantly impact total ownership costs for manufacturing operations. Ready for the good part? Equipment using zirconium silicate-based formulations typically shows 20-30% less wear on pumps, spray nozzles, and mixing equipment compared to more abrasive alternatives. This reduced wear extends equipment lifespans and decreases maintenance intervals, with documented maintenance cost reductions of 15-25% in production environments that have transitioned to zirconium silicate.
Cost Factor | Annual Savings with Zirconium Silicate |
---|---|
Material Usage Reduction | $30,000-50,000 per 500 tons |
Energy Consumption | $8,000-15,000 per production line |
Equipment Maintenance | $12,000-20,000 per production line |
Quality Control Rejections | $20,000-35,000 per production line |
Inventory Carrying Costs | $5,000-10,000 per warehouse |
WHICH INDUSTRIES BENEFIT MOST FROM ZIRCONIUM SILICATE?
The value proposition of zirconium silicate varies significantly across industrial sectors, with certain applications demonstrating particularly compelling economic returns. The ceramic industry represents one of the primary beneficiaries, with manufacturers reporting substantial cost savings and quality improvements. What’s the real story? Case studies from porcelain tile producers show that reformulating with zirconium silicate reduced raw material costs by 8-12% while simultaneously improving product whiteness and consistency.
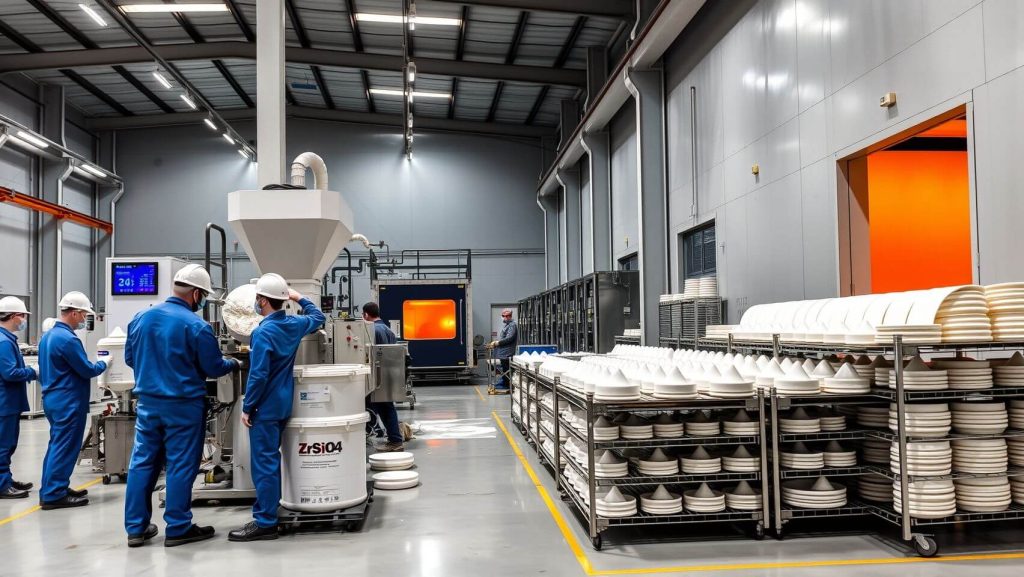
This image shows an industrial ceramic production facility utilizing zirconium silicate as the primary opacifier, highlighting the material’s application in high-volume manufacturing.
Detailed cost savings data from ceramic manufacturers reveals multifaceted benefits. A European sanitaryware producer documented annual savings of €175,000 after transitioning to zirconium silicate, with 60% of savings derived from reduced material consumption and 40% from decreased energy usage and maintenance costs. Production yield improvements of 3-5% further enhanced the economic return, with fewer pieces rejected due to opacity inconsistencies or surface defects.
Coating manufacturers report similarly positive experiences when switching to zirconium silicate. Technical evaluations from industrial paint producers demonstrate that zirconium silicate-based formulations achieve equivalent hiding power with 20-25% less opacifier by weight. This reduction translates to approximately $120-150 savings per ton of finished product, while simultaneously improving scratch resistance and weatherability. For a mid-sized coating manufacturer producing 2,000 tons annually, this represents $240,000-300,000 in direct material cost savings.
The food and pharmaceutical industries present unique applications where zirconium silicate delivers exceptional value. But here’s the kicker… These sectors require materials meeting stringent purity and regulatory standards, areas where high-grade zirconium silicate excels. Food-contact applications such as confectionery coatings benefit from zirconium silicate’s inert nature and stability, with manufacturers reporting 30-40% longer shelf life for products using this opacifier compared to alternatives. Pharmaceutical tablet coatings show similar advantages, with improved visual consistency and reduced batch-to-batch variation.
Industry | Primary Benefits | Documented Cost Savings | Quality Improvements |
---|---|---|---|
Ceramics | Material efficiency, Energy savings | 8-12% raw material cost | Improved whiteness, Reduced defects |
Coatings | Reduced usage rates, Durability | $120-150 per ton | Enhanced weatherability |
Food | Regulatory compliance, Shelf stability | 15-20% formulation cost | 30-40% longer shelf life |
Pharmaceuticals | Batch consistency, Visual quality | 10-15% production cost | Reduced variation |
Glass | Thermal stability, Chemical resistance | 5-10% energy cost | Improved clarity |
HOW DO ENVIRONMENTAL FACTORS AFFECT COST-BENEFIT ANALYSIS?
Environmental compliance represents an increasingly significant component of manufacturing economics, with regulatory requirements imposing both direct costs and operational constraints. Comparing the environmental footprints of different opacifiers reveals notable distinctions in compliance expenses. This is where it gets interesting… Zirconium silicate processing generates approximately 0.8-1.2 tons of CO2 equivalent per ton of finished material, compared to 3.5-4.5 tons for titanium dioxide and 0.5-0.7 tons for calcium carbonate.
Regulatory compliance costs vary substantially between opacifier types. Titanium dioxide has faced increasing scrutiny, with the European Chemicals Agency (ECHA) classifying certain forms as potentially carcinogenic when inhaled. This classification has triggered additional workplace safety requirements and product labeling obligations, adding $80-120 per ton in compliance costs for affected manufacturers. Zirconium silicate, lacking similar classifications, avoids these regulatory burdens while maintaining performance advantages.
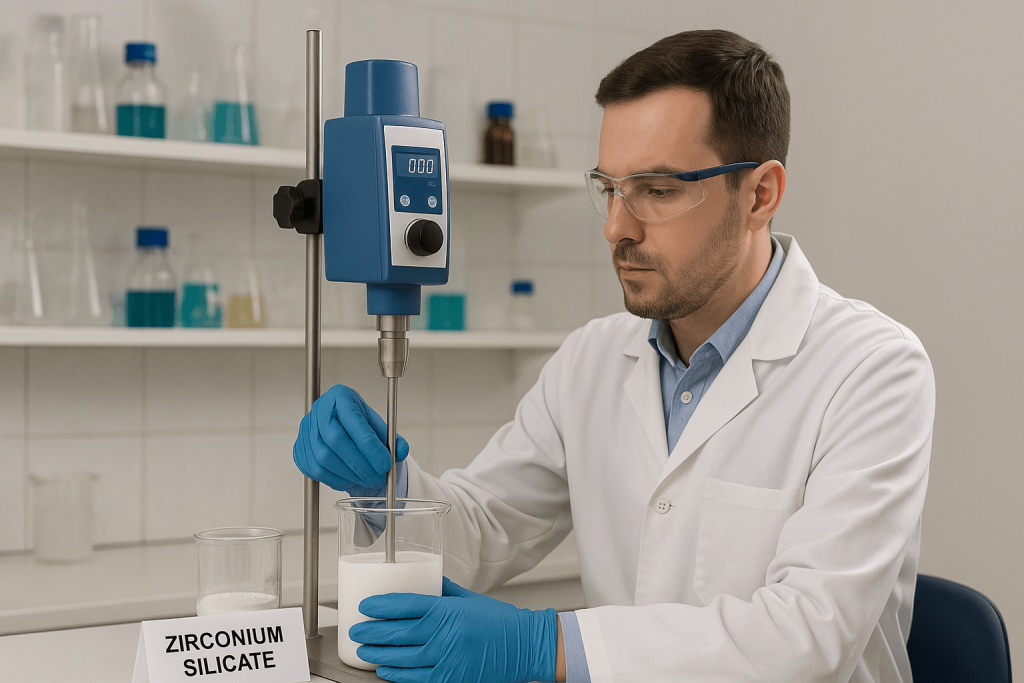
This image depicts a laboratory technician performing dispersion testing to optimize zirconium silicate integration into a new formulation.
Waste management economics further differentiate opacifier options. Production processes for titanium dioxide generate 3-4 tons of neutralized acid waste per ton of finished product, requiring specialized disposal at costs ranging from $50-90 per ton. Zirconium silicate processing produces primarily inert mineral tailings at 1.5-2 tons per ton of product, with disposal costs of $20-40 per ton. This waste stream difference creates an annual savings of $90,000-200,000 for a facility producing 1,000 tons of opacifier annually.
Sustainability trends increasingly influence purchasing decisions throughout the supply chain. Ready for the good part? Manufacturers utilizing environmentally preferable materials often secure premium pricing and preferred supplier status with environmentally conscious customers. Market research indicates that 65% of B2B buyers now include sustainability metrics in supplier evaluation criteria, with 28% willing to pay premiums of 5-10% for demonstrably greener alternatives. This market dynamic creates additional economic value for manufacturers adopting zirconium silicate as part of sustainability initiatives.
Environmental Factor | Zirconium Silicate | Titanium Dioxide | Calcium Carbonate |
---|---|---|---|
Carbon Footprint (CO2e/ton) | 0.8-1.2 | 3.5-4.5 | 0.5-0.7 |
Waste Generation (tons/ton) | 1.5-2.0 | 3.0-4.0 | 0.8-1.2 |
Waste Disposal Cost ($/ton) | 20-40 | 50-90 | 15-30 |
Water Usage (m³/ton) | 40-60 | 70-100 | 20-35 |
Regulatory Restrictions | Minimal | Increasing | Minimal |
WHAT TECHNICAL CHALLENGES EXIST WHEN SWITCHING OPACIFIERS?
Transitioning between opacifier systems presents technical hurdles that manufacturers must navigate to realize the potential benefits of zirconium silicate. Production process adjustments represent the primary challenge, requiring modifications to mixing protocols, dispersion equipment, and quality control parameters. But here’s the kicker… These adjustments typically require a 2-4 week implementation period but generate efficiency improvements that persist throughout the production lifecycle.
Technical requirements for process modification vary by industry and application. Ceramic manufacturers must adjust milling times and dispersion agents when transitioning to zirconium silicate, with typical modifications including 15-25% shorter milling cycles and 10-15% reduced dispersant concentrations. Coating formulators need to recalibrate high-shear mixing parameters, generally reducing mixing times by 10-20% while increasing initial shear rates by 15-25% to achieve optimal particle distribution.
Product formulation revalidation constitutes a significant investment when changing opacifiers. Comprehensive testing protocols typically require 4-8 weeks of laboratory and pilot-scale evaluation, costing $15,000-30,000 for a standard product line. This testing encompasses physical properties, application characteristics, aging stability, and performance under stress conditions. While representing a substantial initial investment, these validation costs are typically recovered within 6-12 months through improved production economics.
Practical methods for overcoming technical barriers have emerged from manufacturers who have successfully transitioned to zirconium silicate. What’s the real story? Phased implementation approaches minimize disruption, with many companies beginning with non-critical product lines before expanding to core offerings. Technical partnerships with material suppliers provide another pathway, with leading zirconium silicate producers offering formulation assistance, process optimization services, and transition support programs that reduce implementation costs by 30-50%.
Technical Challenge | Solution Approach | Implementation Timeline | Resource Requirements |
---|---|---|---|
Mixing Protocol Adjustments | Gradual parameter modification | 2-3 weeks | Process engineer, Lab technician |
Dispersion Optimization | Surfactant evaluation and testing | 3-4 weeks | Formulation chemist, Lab equipment |
Quality Control Recalibration | Parallel testing methodology | 4-6 weeks | QC manager, Analytical equipment |
Scale-up Validation | Pilot runs with incremental volume | 6-8 weeks | Production team, Material for testing |
Customer Acceptance Testing | Side-by-side comparison trials | 8-12 weeks | Technical sales, Customer engagement |
HOW TO CALCULATE TRUE ROI WHEN EVALUATING OPACIFIERS?
Developing a comprehensive return on investment model for opacifier selection requires accounting for multiple cost factors beyond simple material pricing. A holistic cost-benefit analysis framework incorporates direct material costs, processing efficiencies, performance characteristics, and long-term value considerations. This is where it gets interesting… When all factors are properly weighted, zirconium silicate typically delivers ROI improvements of 15-25% compared to titanium dioxide and 10-20% compared to calcium carbonate alternatives.
The construction of a comprehensive cost model begins with baseline material expenses, including purchase price, shipping, handling, and storage costs. These direct expenses are then adjusted for application efficiency factors, with zirconium silicate typically requiring 15-30% less material by weight than titanium dioxide and 40-60% less than calcium carbonate for equivalent opacity. For a manufacturing operation consuming 50 tons of opacifier annually, this efficiency difference represents $60,000-120,000 in direct material savings when switching to zirconium silicate.
Balancing short-term and long-term investment returns requires careful consideration of implementation costs against ongoing benefits. Initial conversion expenses—including reformulation, testing, process modification, and customer requalification—typically range from $50,000-100,000 for a medium-sized manufacturing operation. Ready for the good part? These costs are generally recovered within 6-12 months through improved production economics, with cumulative savings exceeding implementation costs by 200-300% after 24 months of operation.
Risk factor quantification and sensitivity analysis provide essential context for investment decisions. Modeling the impact of potential raw material price fluctuations reveals that zirconium silicate pricing historically demonstrates 30-40% less volatility than titanium dioxide, reducing budget uncertainty and improving forecast accuracy. Supply chain disruption risks show similar advantages, with zirconium silicate sourced from multiple global regions providing greater supply security than more geographically concentrated alternatives.
ROI Component | Calculation Method | Typical Value Range | Payback Period |
---|---|---|---|
Material Efficiency | (Alternative usage – ZS usage) × Price | 15-30% savings | 3-6 months |
Processing Improvements | Labor + Energy + Maintenance savings | 10-20% reduction | 6-12 months |
Quality Enhancements | Reduced rejections × Unit value | 3-8% improvement | 8-15 months |
Environmental Compliance | Regulatory + Disposal cost difference | 5-15% savings | 12-24 months |
Product Performance | Extended lifetime × Replacement value | 10-25% improvement | 18-36 months |
WHAT FUTURE DEVELOPMENTS MAY CHANGE THE COST-BENEFIT EQUATION?
Emerging innovations in zirconium silicate production technology promise to further enhance its competitive position in the opacifier market. Advanced processing techniques currently in development aim to reduce energy consumption by 20-30% while improving particle size distribution control. What’s the real story? These innovations could reduce production costs by 15-25% over the next 3-5 years, potentially eliminating much of the current price premium compared to titanium dioxide.
Technical innovation trends focus on several key areas. Surface modification technologies enable enhanced dispersion characteristics, reducing the need for additional dispersants and improving compatibility with a wider range of carrier systems. Nano-structured zirconium silicate variants demonstrate opacity improvements of 15-20% compared to conventional grades, potentially allowing further reductions in application quantities. Hybrid materials combining zirconium silicate with complementary compounds show promise for specialized applications requiring multifunctional performance.
Alternative material development presents both opportunities and potential threats to zirconium silicate’s market position. Research into synthetic opacifiers derived from industrial byproducts has produced materials achieving 70-80% of zirconium silicate’s performance at 60-70% of the cost. However, these alternatives currently lack the long-term performance data and regulatory clearances necessary for widespread adoption, particularly in sensitive applications like food contact materials and pharmaceuticals.
Market supply and demand dynamics will significantly influence future pricing trends. But here’s the kicker… Global zirconium silicate production capacity is projected to increase by 15-20% over the next five years, with new mining operations in Australia, South Africa, and Brazil expanding raw material availability. This capacity growth, combined with processing innovations, suggests stable or declining real prices despite increasing demand. Competing opacifiers face more uncertain supply outlooks, with titanium dioxide production constrained by environmental regulations and feedstock limitations.
Future Development | Potential Impact | Timeline | Probability |
---|---|---|---|
Advanced Processing Technology | 15-25% cost reduction | 3-5 years | High |
Surface-Modified Variants | 10-15% performance improvement | 2-4 years | Medium-High |
Nano-Structured Formulations | 15-20% efficiency increase | 4-6 years | Medium |
Alternative Material Competition | 10-20% market pressure | 5-8 years | Medium-Low |
Supply Capacity Expansion | 5-10% price reduction | 2-3 years | High |
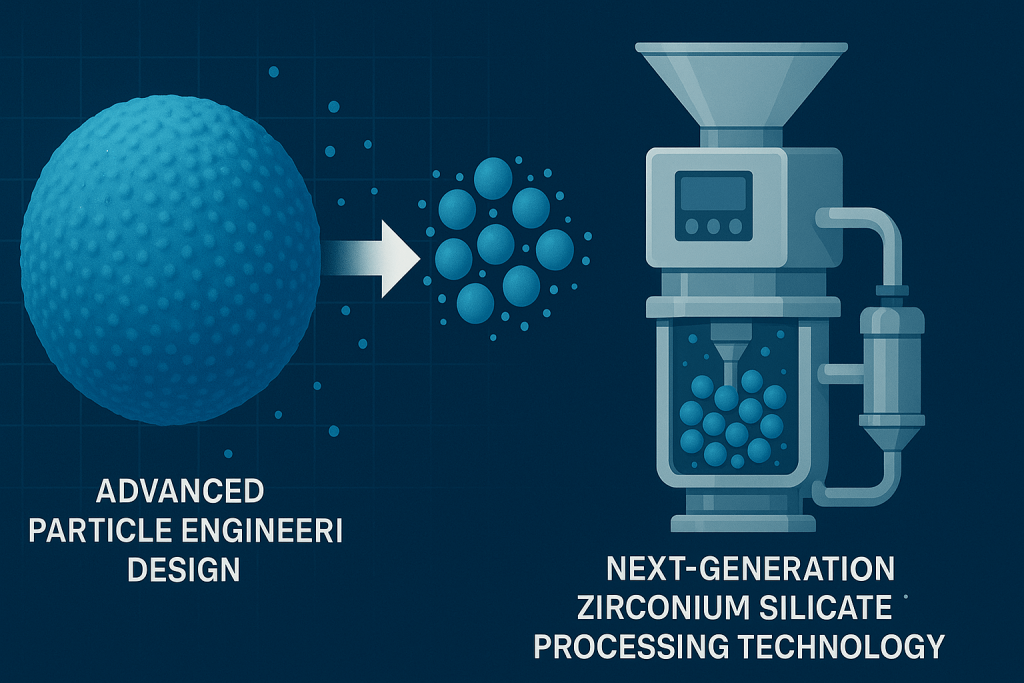
This image illustrates next-generation zirconium silicate processing technology that enables precise particle size control and surface modification for enhanced performance.
The cost-benefit advantages of zirconium silicate compared to alternative opacifiers extend far beyond simple material pricing. When evaluated through a comprehensive analytical framework that accounts for application efficiency, performance characteristics, environmental factors, and long-term value, zirconium silicate demonstrates compelling economic advantages across multiple industrial applications.
Manufacturing professionals seeking optimal opacity solutions should conduct thorough assessments based on their specific requirements and operating conditions. While the initial investment in transitioning to zirconium silicate may exceed that of continuing with conventional opacifiers, the documented return on investment typically justifies this transition for operations prioritizing quality, consistency, and total cost optimization.
As production technologies continue to advance and environmental considerations gain further prominence in material selection decisions, zirconium silicate’s favorable positioning on both fronts suggests its competitive advantages will likely strengthen in coming years.

This image presents a comparative ROI analysis chart tracking the cumulative cost savings of zirconium silicate versus alternative opacifiers over a 36-month implementation period.
FAQ Section
Q1: What is zirconium silicate and how does it function as an opacifier?
Zirconium silicate (ZrSiO₄) is a natural mineral with a high refractive index (1.92-1.96) that scatters light effectively. As an opacifier, it creates multiple interfaces that redirect and scatter light, thus preventing transmission. Its tetragonal crystal structure and a controlled particle size (typically 1-10 microns) enhance this effect, making it ideal for ceramics, coatings, and applications requiring high opacity.
Q2: How much more expensive is zirconium silicate compared to titanium dioxide?
Zirconium silicate costs 1.5-2.5 times more per kilogram than titanium dioxide, with prices ranging from 1,200−2,000permetrictonagainst1,200-2,000 per metric ton against 1,200−2,000permetrictonagainst800-1,200 for titanium dioxide. However, zirconium silicate often requires 15-30% less material by weight to achieve similar opacity, reducing the effective cost difference. Additionally, its benefits, such as improved durability and lower maintenance, may offer better overall value despite the higher unit price.
Q3: Can zirconium silicate be used in all applications where other opacifiers work?
Zirconium silicate is versatile but has constraints. It performs best at temperatures below 1650°C, suitable for ceramics, most coatings, and many polymers. For applications over this temperature or needing very fine particles (below 0.5 microns), alternative materials may be required. Its higher density (4.6-4.7 g/cm³) can also affect stability in low-viscosity liquids if not properly formulated.
Q4: What safety considerations apply when working with zirconium silicate?
Zirconium silicate is generally low in toxicity and poses minimal health risks if handled with standard industrial hygiene practices. It is not classified as carcinogenic or mutagenic. Dust control measures are recommended during handling to prevent inhalation of particles. Food-grade zirconium silicate is further purified for safety in food contact applications. Safety data sheets advise using standard personal protective equipment, such as dust masks.
Q5: How does particle size affect the performance of zirconium silicate as an opacifier?
Particle size significantly impacts the opacifying efficiency of zirconium silicate. Optimal scattering occurs when particle size is about half the wavelength of visible light (0.2-0.5 microns). However, milling to this size is costly. Most commercial grades have particles between 1-10 microns, balancing opacity and processing ease. Finer grades (1-3 microns) offer greater opacity but at a higher cost and dispersion challenges, while coarser grades (5-10 microns) are easier to process but need higher loading rates. Manufacturers should choose particle size distributions suited to their specific applications.