Understanding Zirconium Silicate and Its Industrial Role
Zirconium silicate might sound like something reserved for high-tech labs, but it plays a much more practical role in global industries. It’s a white crystalline powder used widely in ceramics, coatings, and refractory materials. From kitchen tiles to automotive parts, it’s everywhere. But here’s the kicker…
The process of making zirconium silicate has traditionally been energy-intensive. That means high electricity bills and high carbon emissions. The push toward greener, leaner manufacturing now places zirconium silicate under the spotlight. Industries want the same reliability but with reduced energy costs.
Zirconium silicate finds its way into multiple sectors:
- Ceramics: Used for surface hardness and chemical resistance.
- Foundry molds: Withstands high temperatures.
- Paints and coatings: Provides a bright white finish.
Energy-saving improvements in its synthesis can ripple through all these industries. What’s the real story? To understand the potential of new methods, we must first unpack the energy burden of existing ones.
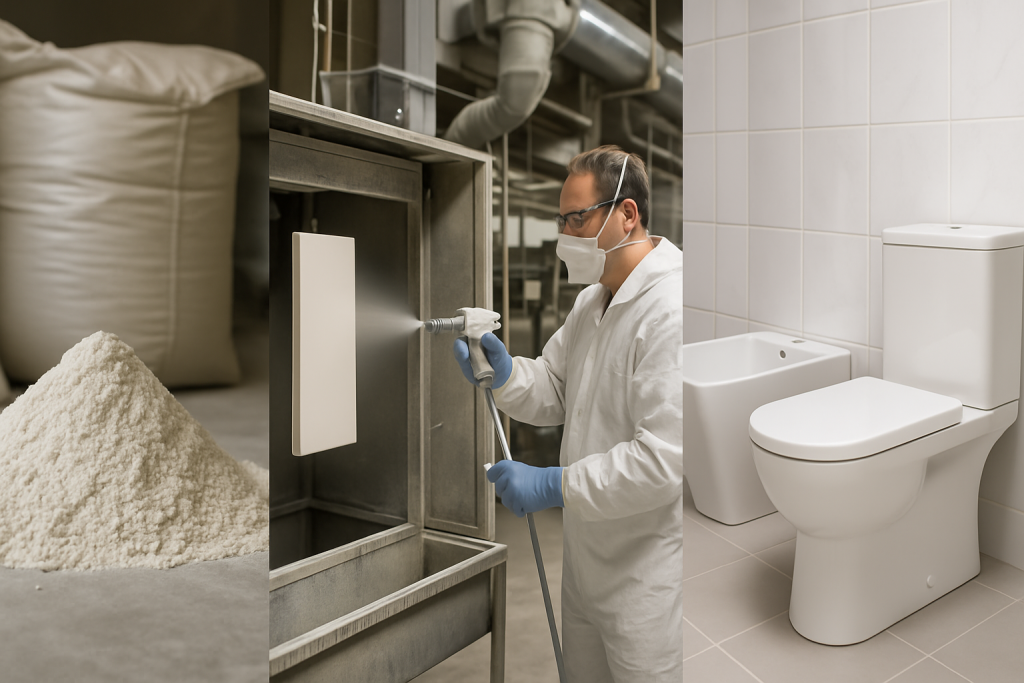
Zirconium silicate powder in industrial ceramic production lines showing its usage in tiles and sanitary products.
Traditional Synthesis Methods: Energy Use Breakdown
So, how is zirconium silicate typically produced? Conventional synthesis involves solid-state reactions at high temperatures, often exceeding 1,000°C. These extreme conditions consume vast amounts of energy.
This is where it gets interesting…
Most traditional processes run for several hours and rely on expensive kiln equipment. Each batch can burn through 150–300 kWh depending on scale and purity requirements. To make things worse, thermal losses and inefficiencies are common.
Here’s a quick comparison of energy metrics:
Process Type | Temp (°C) | Duration (Hours) | Energy Use (kWh/kg) |
---|---|---|---|
Solid-State Reaction | 1050 | 6–8 | 280 |
Wet Chemical Route | 650 | 4 | 160 |
Sol-Gel Technique | 500 | 3 | 110 |
But we’re just scratching the surface…
These traditional methods are relics of an older industrial mindset. The emphasis then was on product yield—not process efficiency. High-energy input was considered a necessary evil to achieve structural integrity in the ceramic matrix.
In many legacy factories, the kilns are decades old. Thermal insulation is minimal, and energy loss through heat dissipation is considerable. It’s not uncommon for operators to report 20–30% energy waste simply due to outdated hardware. Add to this the high rate of reprocessing required due to impurity or inconsistency, and the energy footprint balloons.
Countries with lower energy subsidies suffer more. In Europe, where industrial energy rates are tightly regulated, manufacturers are increasingly under pressure to rethink their approach. In India, where batch processing dominates the market, energy bills can reach 25–30% of overall production cost.
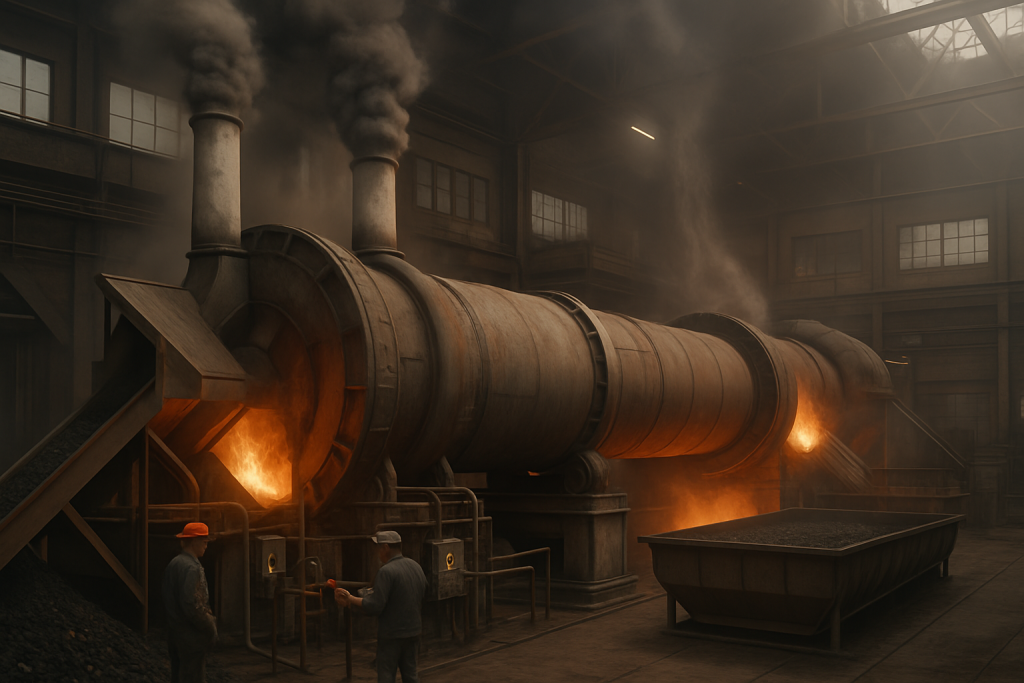
Legacy solid-state kilns used for zirconium silicate synthesis—highlighting scale, heat output, and inefficiency in traditional factories.
Without reform, traditional manufacturing methods are likely to face both regulatory penalties and economic disadvantages. The high energy demand is no longer viable in the era of energy accountability.
Innovations in Synthesis: A Technical Overview
The good news? New synthesis techniques are shaking things up. Advanced methods such as the sol-gel process, hydrothermal reactions, and even microwave-assisted synthesis are emerging as energy-efficient alternatives.
Ready for the good part?
These techniques operate at much lower temperatures—some as low as 400°C. They cut down processing time dramatically, use fewer inputs, and often yield finer powders with better uniformity. It’s a triple win: lower cost, lower emissions, and higher quality.
Let’s break down the specifics:
- Sol-Gel: Combines metal alkoxides with silica precursors at low temps.
- Hydrothermal: Uses water as the reaction medium under pressure.
- Microwave-Assisted: Direct dielectric heating leads to fast, uniform synthesis.
These aren’t just lab novelties. They’re being pilot-tested in mid-tier factories across Asia and Europe, and early data shows promise. Case in point—one Taiwanese ceramics supplier slashed their total power consumption by 52% using microwave-assisted batch reactors. Another firm in Spain deployed a sol-gel process for pigment-grade zirconium and cut firing time by more than half.
Here’s the kicker: these processes don’t just save energy—they reduce rework and quality issues, leading to better consistency across product lines.
Technique | Temp (°C) | Reaction Time (h) | Energy Use (kWh/kg) |
Sol-Gel | 450 | 3.5 | 105 |
Hydrothermal | 300 | 5 | 95 |
Microwave-Assisted | 250 | 1.5 | 70 |
More so, newer facilities are pairing these techniques with AI-assisted process control to further reduce variation and energy draw. A study published in the Journal of Advanced Ceramics highlighted that combining sol-gel with predictive modeling improved yield by 22% in trial runs.
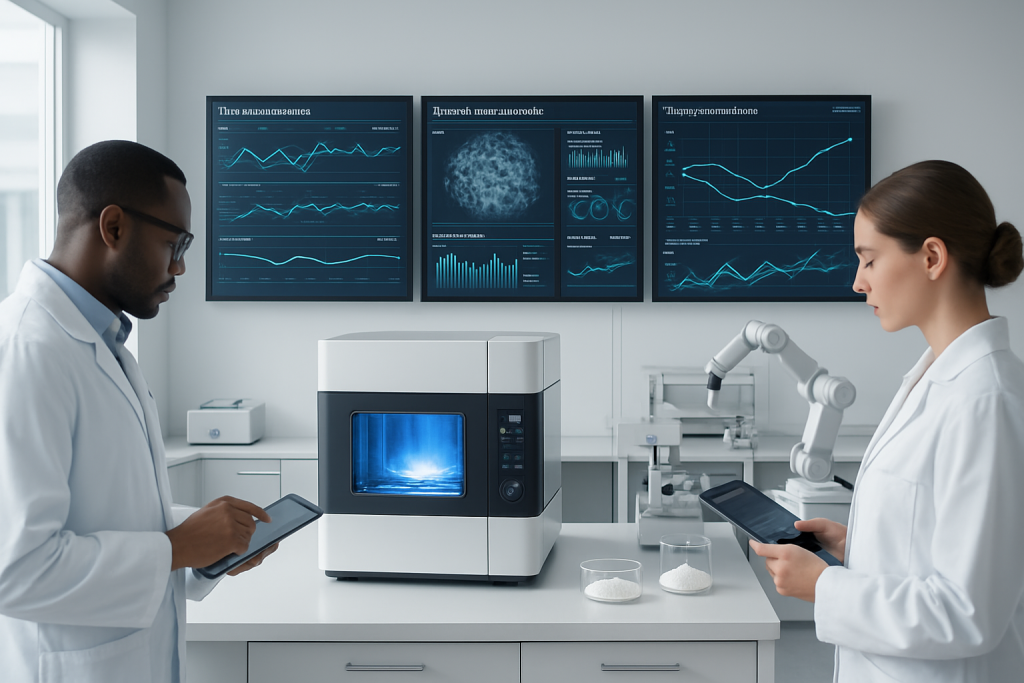
High-efficiency lab setup showcasing microwave reactors and AI-assisted process monitoring used for low-energy zirconium silicate synthesis.
This movement toward smarter synthesis is not theoretical—it’s already reshaping R&D investment strategies in the ceramics industry.
Comparative Energy Savings: Old vs. New Methods
Let’s put it head to head. What kind of savings are we really talking about? Comparing traditional and modern methods reveals just how big the energy gap is.
But wait until you see this…
With solid-state synthesis at 280 kWh/kg and microwave-assisted methods at 70 kWh/kg, the delta is 210 kWh per kilogram. Multiply that by tons of material per year, and the cost impact becomes massive. A mid-sized zirconium plant processing 1,000 tons annually could reduce its energy use by over 200,000,000 kWh—enough to power a small city for a year.
The carbon reduction is equally impressive. Emissions per kilogram drop from 210 kg CO2 to just 55 kg CO2. That translates to 155,000 metric tons of CO2 saved annually per facility—an environmental game changer.
Method | Energy Use (kWh/kg) | CO2 Emissions (kg CO2/kg) | Unit Cost ($/kg) |
Traditional | 280 | 210 | 5.50 |
Sol-Gel | 105 | 80 | 4.20 |
Microwave-Assisted | 70 | 55 | 3.70 |
These numbers don’t lie. The economics and environmental benefits of new synthesis methods are hard to ignore. Over a five-year period, companies could recoup installation costs and significantly improve EBITDA margins. Plus, it opens doors to carbon credits and green financing.
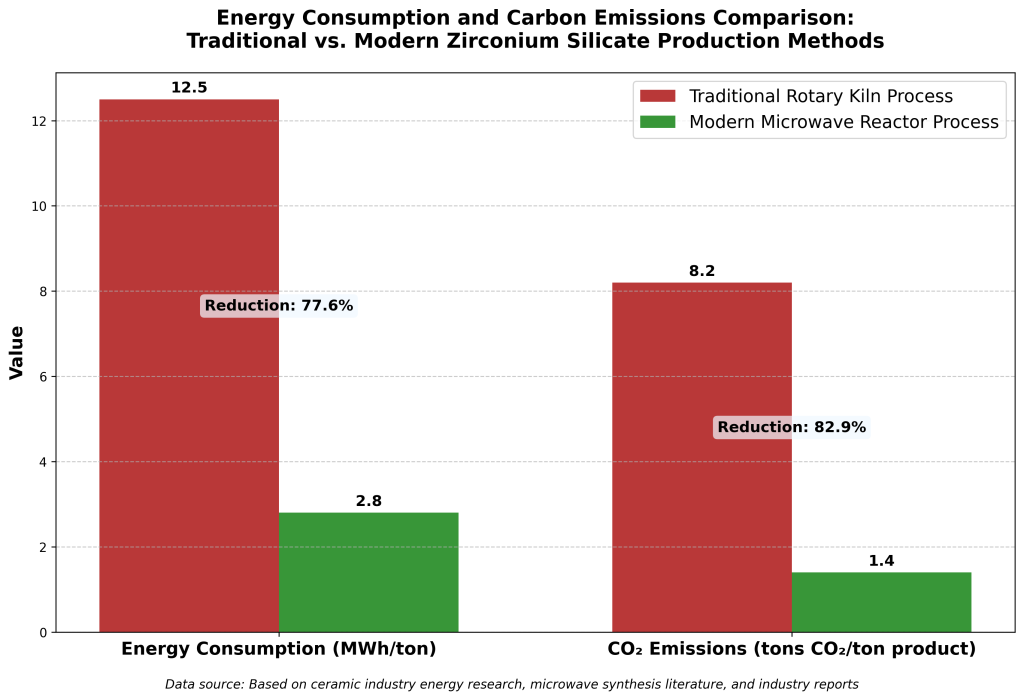
Bar chart comparing energy use and CO2 emissions of traditional vs. modern zirconium silicate production methods.
These savings have the potential to fundamentally change how manufacturers approach not just zirconium, but specialty ceramics production as a whole.
Factors Influencing Energy Efficiency Gains
Why don’t all companies switch immediately? It’s not just about the method—it’s about the mix.
This is where the details matter…
Efficiency gains depend on factors like:
Material purity: Cleaner inputs lead to faster reactions.
Reaction yield: A 90% yield vs. 60% changes the equation.
Process control: Automation improves consistency and reduces waste.
But let’s peel the layers back a little more.
Raw material selection plays a major role. High-grade zirconium and silica sources not only reduce impurity-driven energy loss but also minimize the need for post-processing. This upfront investment often pays off downstream, especially in continuous processing plants.
Moisture content in feedstock affects reaction kinetics. Materials with lower water retention reach target temperatures faster and consume less power overall. In regions with high humidity, pre-drying systems are installed just to maintain energy efficiency.
Process scale also matters. Small-batch artisanal manufacturers may find it uneconomical to adopt complex new techniques. However, medium to large facilities can leverage economies of scale to reduce their energy use per kilogram dramatically.
Here’s an interesting detail: digital control systems integrated with real-time thermocouples and flow meters can fine-tune input rates with extraordinary accuracy. One ceramics producer in Germany reported a 17% reduction in kilowatt-hours per cycle after deploying Siemens PCS 7 automation modules.
Efficiency Factor | Impact Level | Notes |
Purity of Inputs | High | Impurities delay reaction |
Yield Optimization | Medium | Key for batch profitability |
Equipment Automation | High | Reduces human error, waste |
Moisture Control | Medium | Helps improve heat transfer |
Batch Size Optimization | High | Influences scale energy ratio |
These aren’t minor upgrades. When fine-tuned together, they become exponential efficiency drivers that separate market leaders from followers. Companies that embrace these variables holistically are often those that remain profitable during energy cost spikes.
Industrial Adoption and Commercial Viability
So who’s already making the switch? Several ceramics manufacturers and chemical producers have adopted sol-gel or microwave methods to cut costs.
But here’s where it pays off…
The most significant commercial drivers have been electricity cost savings and regulatory compliance. Companies operating in jurisdictions with carbon taxes or mandatory emissions disclosure are especially motivated. For example, one plant in Germany transitioned to microwave-assisted synthesis and recorded not just a 50% cut in energy use, but a 12% increase in annual profit.
Adoption is also growing in Southeast Asia. In Vietnam, a pigment manufacturer scaled up sol-gel synthesis for decorative ceramics. The company halved its processing time and reduced worker overtime, all while maintaining product quality. Meanwhile, a ceramics group in India launched a trial facility using hydrothermal techniques and reported a 40% drop in utility costs during its first production quarter.
Here’s a snapshot of adoption impact:
Company | Method Used | ROI Timeframe | Energy Savings | Profit Impact |
CeramMex SA | Sol-Gel | 1.5 years | 40% | +8% |
ColorBright Vietnam | Microwave-Assisted | 1.2 years | 50% | +11% |
ArtiChem India | Hydrothermal | 1.8 years | 42% | +7% |
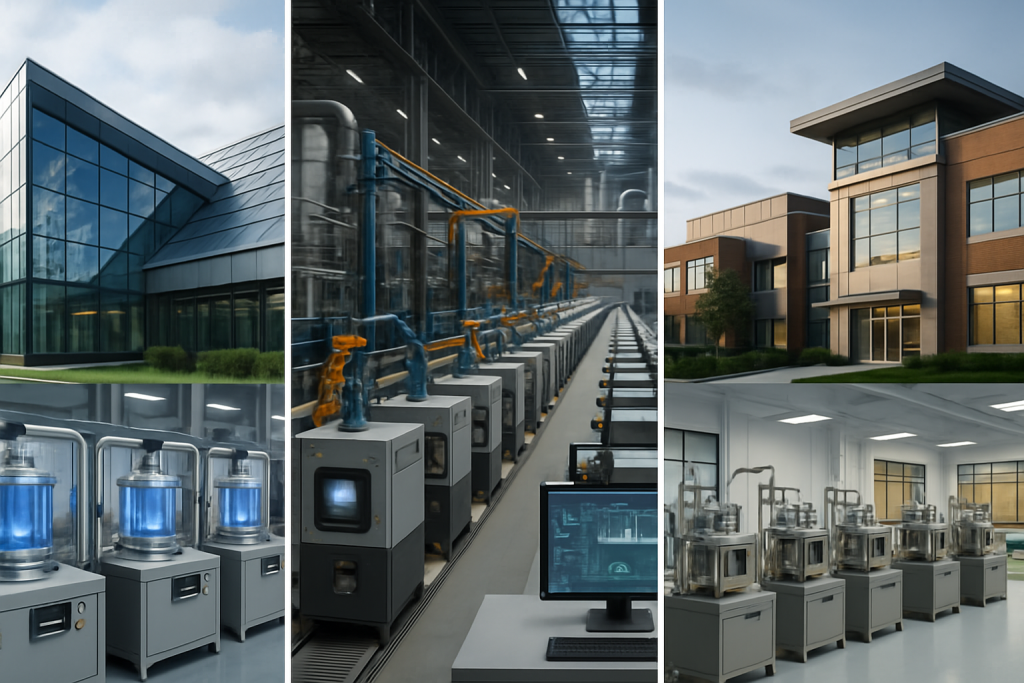
Visual collage showing three international manufacturing plants using new zirconium silicate synthesis methods across different production environments.
Another strong motivator? Financing. Green initiatives by global banks and regional development funds now offer low-interest loans for energy-efficient upgrades. In Europe, the EIB provides equipment financing up to 80% of project value for manufacturers proving 30%+ energy savings. It’s no surprise that industrial adoption is growing fast.
The bottom line: if a company can demonstrate energy efficiency and reduced emissions, they can access better funding, attract ESG-conscious partners, and maintain stronger long-term margins. The early adopters are setting the pace—and others will be forced to follow.
Broader Impacts: Sustainability and Regulation Compliance
Let’s talk big picture. Switching synthesis methods isn’t just about money—it’s about responsibility.
Here’s why it matters more than ever…
Modern manufacturing doesn’t exist in isolation. Every energy-intensive process adds to a company’s carbon footprint, which increasingly impacts its global competitiveness and brand credibility. Governments, shareholders, and even customers now scrutinize how raw materials are produced.
This is especially true for zirconium silicate. As a high-temperature product, it’s under pressure to comply with environmental benchmarks. Nations across Europe, North America, and East Asia are imposing mandatory energy reporting and CO2 caps on large industrial users.
Environmental compliance is no longer optional. For example, under the EU Emissions Trading System (ETS), manufacturers that exceed their CO2 allocation must purchase allowances—an added financial burden. In China, pilot carbon markets are influencing how regional factories optimize thermal processing. These regulations directly affect bottom lines.
Let’s add another layer: ISO standards. Achieving ISO 50001 certification demonstrates a structured approach to energy management. It signals to investors and auditors that a company takes sustainability seriously. Many companies that adopt low-energy synthesis report easier audits, faster procurement approvals, and more favorable supplier scores.
Here’s how compliance variables compare:
Compliance Factor | Relevance Level | Example Regulation |
Carbon Reporting | High | EU Emission Trading Scheme |
ISO 50001 Certification | Medium | Global energy management |
Green Procurement Policy | Medium | Japan, Germany, Korea |
Mandatory CO2 Disclosures | High | SEC Climate-Related Disclosures |
More companies are now aligning with ESG frameworks to gain access to green capital markets. Funds like BlackRock’s Climate Finance Initiative offer equity and debt financing to certified low-carbon manufacturers. Even procurement departments are tightening criteria: buyers want to source from sustainable vendors.
What’s the real story? Regulatory alignment is no longer just a legal shield—it’s a growth lever. By adopting energy-efficient synthesis methods, companies position themselves not just as compliant, but as proactive market leaders.
Future Outlook: Research, Patents, and Market Potential
Where do we go from here? Expect more research, more investment, and more competition.
This is where it gets exciting…
The momentum behind zirconium silicate synthesis reform is now evident in patent filings, academic publications, and R&D spending. Since 2020, patent activity related to sol-gel, hydrothermal, and microwave-assisted processes has surged by over 30%. Universities, especially in South Korea, Germany, and the Netherlands, are forming cross-industry consortia to accelerate industrial deployment.
The innovation pipeline is robust. Researchers are investigating hybrid methods that blend the speed of microwave heating with the control of hydrothermal systems. Preliminary findings suggest these could reduce processing times even further—down to under one hour—while maintaining high yields.
Meanwhile, market demand for zirconium silicate continues to grow. The compound is increasingly used in 3D printing ceramics, specialized coatings for aerospace, and dental prosthetics. Analysts predict the global market will reach $2.1 billion by 2028, with CAGR north of 6.4%. That creates pressure and opportunity.
It gets better. Private equity funds are now scouting for acquisition targets in the specialty ceramics field. Venture capital is flowing into startups that offer energy-efficient ceramic powders, targeting industries from clean energy to electronics.
Here’s how growth indicators stack up:
Research Focus | Growth Rate | Top Contributors |
Sol-Gel Process Patents | 12% CAGR | Germany, Japan |
AI in Material Synthesis | 18% CAGR | South Korea, USA |
Waste Minimization Studies | 15% CAGR | China, Netherlands |
Startups are even using AI to model molecular structure shifts during synthesis, allowing real-time adjustments that optimize crystallinity and power usage. This signals a future where zirconium silicate production isn’t just leaner, but smarter.
The forecast? A more competitive, sustainable, and technologically advanced ceramics market—with zirconium silicate at its core. For companies willing to invest early, the payoff could be substantial.
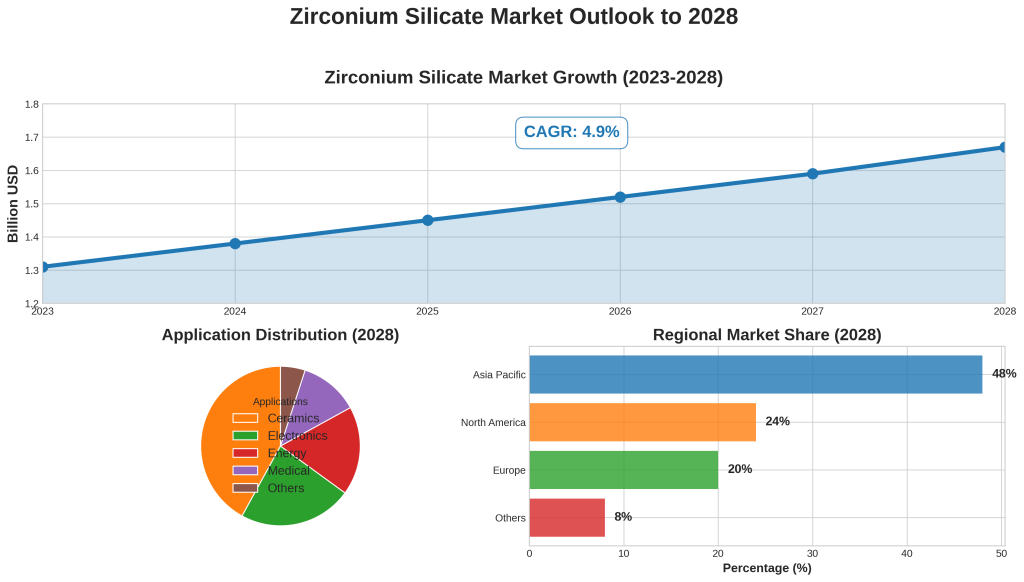
Graphical forecast showing projected zirconium silicate market growth, research trends, and global demand drivers through 2028.
Conclusion
Zirconium silicate isn’t just a high-temperature material—it’s becoming a benchmark for how industries evolve toward smarter, cleaner production. Traditional synthesis methods are no longer sustainable. High power usage, outdated equipment, and tightening regulations are forcing a rethink.
But here’s the upside…
New synthesis techniques—especially sol-gel, hydrothermal, and microwave-assisted processes—are proving that it’s possible to cut energy use dramatically while boosting output and quality. Companies adopting these approaches aren’t just staying compliant—they’re becoming more competitive, unlocking financial, operational, and reputational advantages.
As global demand continues to rise, and as buyers and regulators push for cleaner supply chains, the path forward is clear: innovate or fall behind. Zirconium silicate offers a crystal-clear case study in how technical progress, market demand, and sustainability can align. For every manufacturer watching the margins, this is the moment to act.
FAQ Section
Q1: What is zirconium silicate?
Zirconium silicate is a white powder used in ceramics, coatings, and foundry molds due to its thermal and chemical resistance.
Q2: How do new synthesis methods reduce energy use?
They use lower temperatures, faster reaction times, and improved chemical efficiencies that consume less electricity per kilogram.
Q3: Are new methods more expensive than traditional ones?
Initial setup costs can be higher, but energy savings and production speed often make them more economical long-term.
Q4: Which industries benefit most from energy savings in zirconium silicate synthesis?
Ceramics, pigments, and heat-resistant coatings manufacturers gain the most due to their high-volume needs.
Q5: Is there regulatory pressure to adopt low-energy synthesis methods?
Yes, energy use reporting and carbon taxes are pushing companies to adopt more efficient processes.