Finding reliable growth markets for specialty materials like zirconium silicate presents a significant challenge for procurement teams and business development managers. With shifting global supply chains and evolving industrial applications, identifying which sectors will drive future demand requires careful analysis. This article examines the markets showing strongest growth potential for zirconium silicate products, providing data-driven insights to help you make strategic sourcing decisions and capitalize on emerging opportunities. Our analysis draws from market research across multiple industries and consultation with materials scientists specializing in advanced ceramic applications.
How Has the Zirconium Silicate Market Evolved in Recent Years?
The zirconium silicate market has undergone significant transformation over the past decade, shifting from a primarily ceramics-focused material to a multi-industry specialty product. According to Lucintel’s market analysis, the global zirconium silicate market is expected to grow with a CAGR of 4.7% from 2024 to 2030, showing steady expansion from 1.2billionin2018toapproximately1.2 billion in 2018 to approximately 1.2billionin2018toapproximately1.7 billion in 2024.
But what’s driving this consistent growth? Several factors have converged to create new demand vectors across multiple industries. Technological advancements in processing and application methods have expanded the practical uses of zirconium silicate beyond traditional sectors. Manufacturers have developed more refined grades with tightly controlled particle sizes and purity levels, opening doors to high-tech applications previously unsuitable for this material.
Application patterns have shifted dramatically, with traditional ceramics now representing only 42% of total consumption compared to 65% a decade ago. The remaining market share has diversified across electronics (18%), advanced materials (15%), environmental technologies (12%), and other applications (13%). This diversification has created a more stable demand profile less susceptible to downturns in any single industry.
Year | Global Market Size (USD) | Primary Growth Drivers | Dominant Application Sectors |
---|---|---|---|
2018 | $1.2 billion | Ceramics expansion, foundry applications | Ceramics (65%), Foundry (20%), Others (15%) |
2020 | $1.3 billion | Electronics miniaturization, high-performance ceramics | Ceramics (58%), Electronics (12%), Foundry (18%), Others (12%) |
2022 | $1.5 billion | Green energy applications, semiconductor demand | Ceramics (48%), Electronics (15%), Advanced Materials (12%), Others (25%) |
2024 | $1.7 billion | Environmental tech, medical applications, electronics | Ceramics (42%), Electronics (18%), Advanced Materials (15%), Environmental (12%), Others (13%) |
Regional market development shows interesting patterns. Asia-Pacific continues to dominate production and consumption, accounting for 62% of global demand, primarily driven by China, Japan, and South Korea’s manufacturing sectors. North America and Europe together represent 30% of the market, focusing on high-value applications in aerospace, medical, and advanced electronics. Emerging markets in India, Brazil, and parts of Southeast Asia show the highest growth rates, albeit from smaller base volumes.
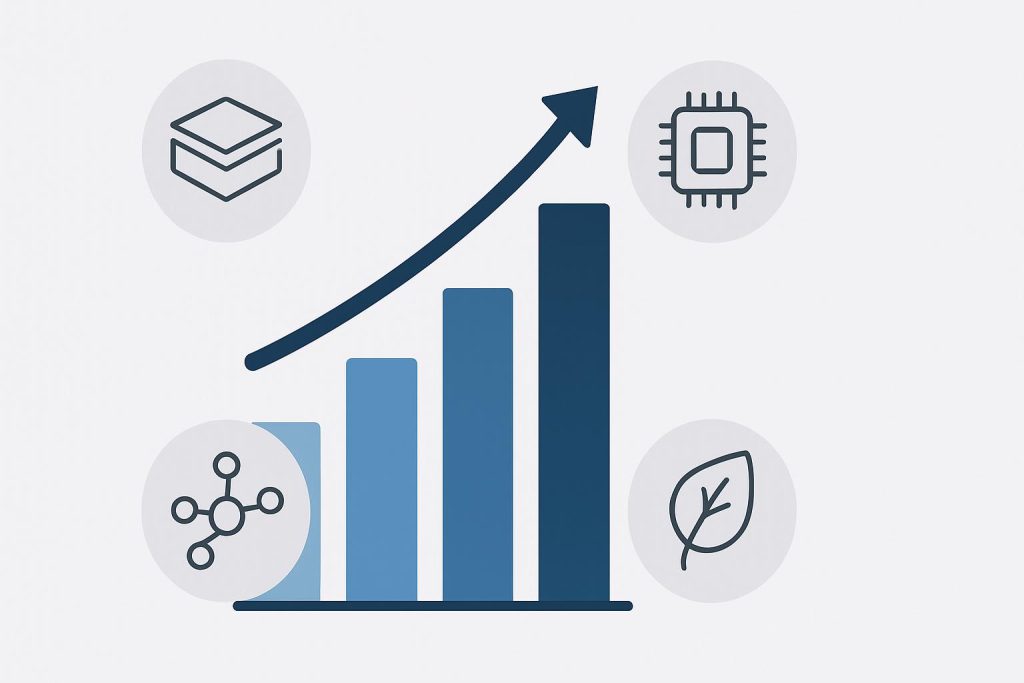
Why Are Advanced Ceramics Industries Leading Zirconium Silicate Adoption?
Advanced ceramics industries continue to lead zirconium silicate adoption despite market diversification, maintaining their position as the largest consumption sector. This leadership stems from zirconium silicate’s exceptional performance properties that address critical challenges in high-temperature applications.
What makes this material so valuable for ceramics manufacturers? The answer lies in its unique combination of thermal stability, mechanical strength, and chemical inertness. With a melting point exceeding 2,500°C and excellent dimensional stability under thermal cycling, zirconium silicate enables ceramic products to withstand extreme operating conditions without compromising structural integrity.
Cost-benefit analysis reveals compelling economics for ceramics applications. While premium grades of zirconium silicate may cost 15-30% more than conventional alternatives, the performance benefits often justify this premium through extended product lifespans, reduced warranty claims, and access to higher-value market segments.
Case studies from leading manufacturers demonstrate successful implementation. A European technical ceramics producer reported a 40% reduction in product failure rates after reformulating their kiln furniture compositions with optimized zirconium silicate content. Similarly, an Asian manufacturer of ceramic components for industrial furnaces achieved a 35% extension in service life by incorporating higher-purity zirconium silicate grades.
Growth forecasts remain strong for advanced ceramics applications, with projected annual increases of 7-9% through 2030. This growth exceeds the overall market average, indicating that despite diversification into other sectors, ceramics will remain the cornerstone of zirconium silicate consumption.
What Makes Electronics and Semiconductor Manufacturing a High-Growth Sector?
The electronics and semiconductor manufacturing sector has emerged as one of the fastest-growing markets for zirconium silicate products, with annual growth rates exceeding 12% since 2020. This rapid expansion stems from zirconium silicate’s unique properties that address critical challenges in modern electronics production.
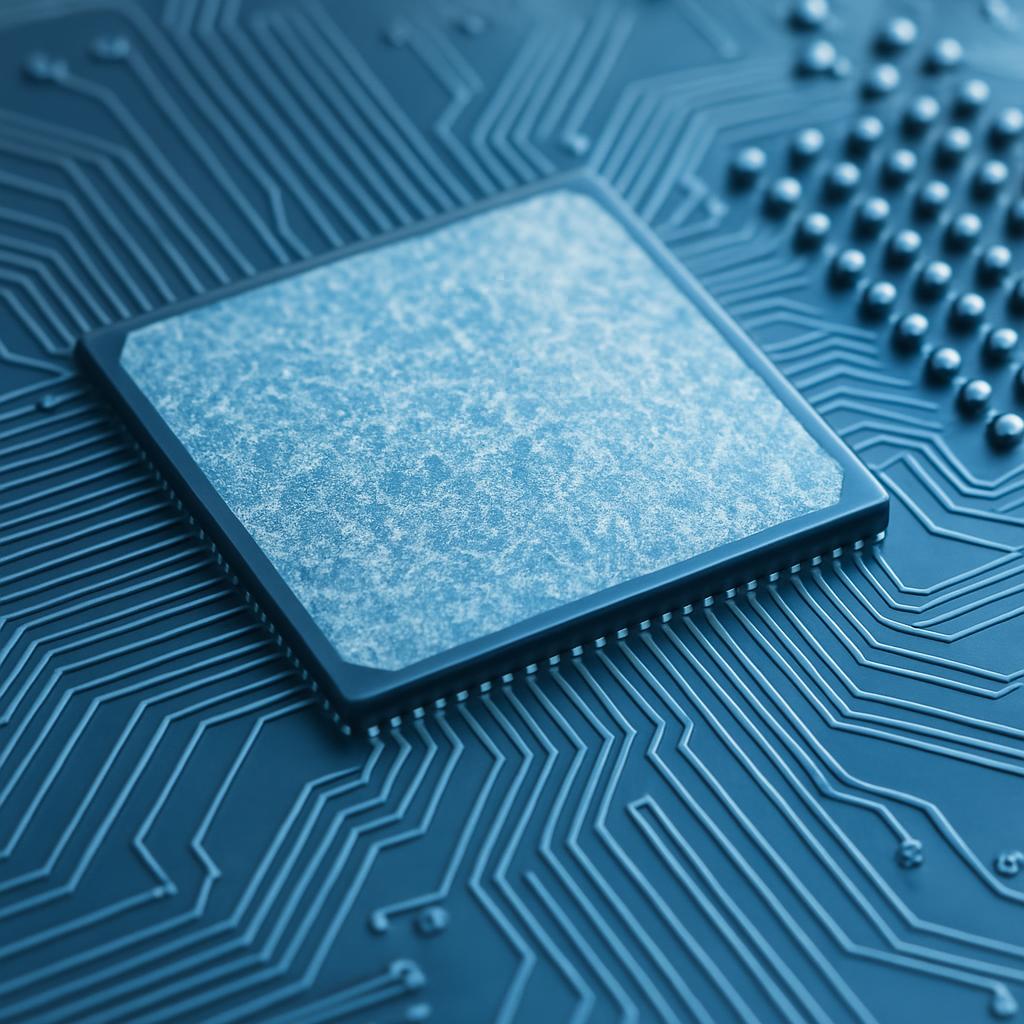
Why is this growth happening now? The accelerating miniaturization of electronic components has created unprecedented materials challenges. As device dimensions shrink and operating temperatures rise, traditional materials often fail to deliver necessary performance. Zirconium silicate offers an exceptional combination of electrical insulation, thermal stability, and mechanical strength that makes it ideal for next-generation semiconductor applications.
Specific applications in semiconductor substrate materials represent the largest growth segment. Zirconium silicate-based ceramics provide superior thermal management in high-power semiconductor packages, preventing thermal runaway while maintaining electrical isolation. These materials also exhibit excellent compatibility with silicon and compound semiconductor processing steps, making them suitable for integration into existing manufacturing workflows.
Market share growth in high-performance computing applications has been particularly strong. Data centers and artificial intelligence systems generate substantial heat during operation, creating demand for advanced thermal management solutions. Zirconium silicate components in these systems help maintain optimal operating temperatures, improving reliability and extending service life. Industry analysts project this segment will grow at 16% annually through 2028, outpacing the broader electronics market.
Supply chain considerations have also contributed to increased adoption. Electronics manufacturers increasingly prioritize materials with stable supply chains and predictable pricing. Zirconium silicate benefits from diverse global sources and established processing infrastructure, reducing supply risk compared to some rare earth-based alternatives.
How Is the Green Energy Transition Creating New Demand Vectors?
The global push toward green energy solutions has created significant new demand vectors for zirconium silicate products. As countries and corporations commit to carbon reduction targets, specialized materials that enable cleaner energy technologies have seen accelerated adoption rates.
How exactly does zirconium silicate fit into the green energy landscape? The material’s unique combination of thermal stability, chemical resistance, and electrical properties makes it valuable across multiple clean energy applications. From fuel cells to solar panels and energy storage systems, zirconium silicate components help improve efficiency, durability, and performance of critical green technologies.
Applications in fuel cell technology represent one of the fastest-growing segments. According to research published in ScienceDirect, zirconium silicate-ionic liquid membranes show exceptional promise for high-temperature hydrogen PEM fuel cells. Solid oxide fuel cells (SOFCs) utilize zirconium silicate-based components in their electrolyte systems, where the material’s ionic conductivity and thermal stability enable efficient electricity generation at high temperatures. With the hydrogen economy gaining momentum, demand for these components is projected to grow at 18-22% annually through 2030.
Green Energy Application | Zirconium Silicate Function | Annual Growth Rate | Key Performance Benefits |
---|---|---|---|
Solid Oxide Fuel Cells | Electrolyte material, structural components | 20.5% | High-temperature stability, ionic conductivity |
Solar Panel Manufacturing | Crucibles for silicon production, coating materials | 14.2% | Purity, thermal shock resistance |
Energy Storage Systems | Separator materials, thermal management | 17.8% | Chemical stability, thermal regulation |
Wind Turbine Components | Wear-resistant coatings, composite materials | 11.3% | Extended service life, reduced maintenance |
Hydrogen Production | Catalyst supports, membrane materials | 22.6% | Chemical resistance, thermal stability |
Solar panel manufacturing requirements have created another significant demand vector. High-purity zirconium silicate crucibles are used in the production of polysilicon, the base material for most photovoltaic cells. These crucibles withstand the extreme temperatures of silicon processing while maintaining exceptional purity levels, preventing contamination that would reduce solar cell efficiency.
Energy storage systems represent a newer but rapidly growing application area. Advanced battery technologies utilize zirconium silicate in separator materials and thermal management systems, where the material’s stability and insulating properties improve safety and performance.
Which Automotive and Aerospace Applications Show Strongest Growth Potential?
Automotive and aerospace industries represent established but rapidly evolving markets for zirconium silicate products. Both sectors face increasing demands for higher performance materials that can withstand extreme operating conditions while contributing to efficiency and sustainability goals.
What’s driving this renewed interest in these traditional sectors? The push for lightweighting, electrification, and improved thermal management has created new application opportunities where zirconium silicate’s unique properties provide competitive advantages. These industries value materials that deliver consistent performance under the most demanding conditions, precisely where zirconium silicate excels.
High-performance coating applications in extreme environments represent the largest growth segment. Thermal barrier coatings incorporating zirconium silicate protect underlying components from heat damage in both automotive and aerospace applications. These coatings extend component life and enable higher operating temperatures, improving overall system efficiency.
Electric vehicle specific applications show particularly strong growth potential. The high voltage systems in EVs require exceptional electrical insulation materials that can withstand both thermal cycling and mechanical stress. Zirconium silicate components in battery enclosures, power electronics, and thermal management systems help address these challenges, with projected market growth of 18-20% annually through 2030.
Aerospace certification requirements present both challenges and opportunities. While the rigorous qualification process for aerospace materials creates barriers to entry, once certified, zirconium silicate products enjoy stable, long-term demand. Several major aerospace manufacturers have recently completed qualification programs for advanced zirconium silicate components, setting the stage for volume adoption in next-generation aircraft programs.
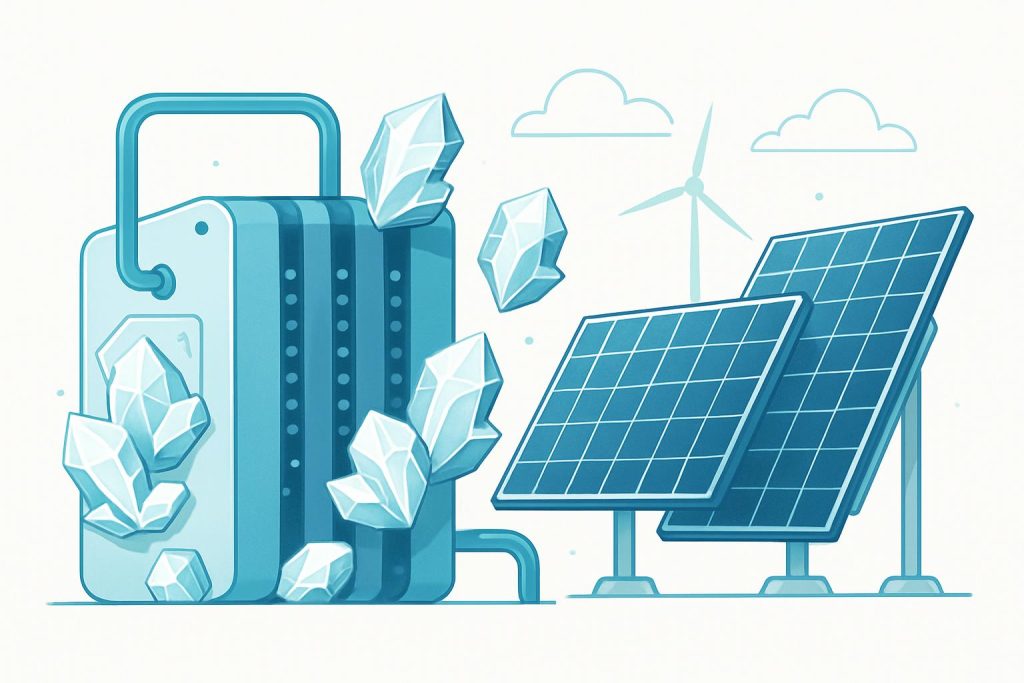
What Healthcare and Biomedical Applications Are Emerging?
Healthcare and biomedical sectors represent newer but rapidly growing markets for zirconium silicate products. The material’s biocompatibility, stability, and unique physical properties make it increasingly valuable for advanced medical applications where performance and safety are paramount.
Why are medical device manufacturers turning to this material now? The combination of biocompatibility with exceptional mechanical and chemical properties addresses critical challenges in implantable and diagnostic devices. As healthcare technology advances toward more personalized and minimally invasive approaches, materials that can withstand biological environments while maintaining functional properties become increasingly valuable.
Biocompatible material applications in medical devices represent the fastest-growing segment. According to research published by the National Library of Medicine, zirconia-based ceramics have become increasingly important in dental biomaterials due to their exceptional biocompatibility, high fracture toughness, and aesthetic qualities. Zirconium silicate ceramics and composites show excellent compatibility with human tissues while providing superior wear resistance and structural stability. These properties make them ideal for load-bearing implants and components that must maintain precise dimensions over extended periods in the body.
Medical Application | Zirconium Silicate Function | Market Growth Rate | Key Performance Requirements |
Dental Implants | Structural material, aesthetic component | 14.3% | Biocompatibility, strength, appearance |
Orthopedic Implants | Load-bearing components, wear surfaces | 12.8% | Mechanical strength, wear resistance, longevity |
Diagnostic Equipment | Precision components, radiation shielding | 11.5% | Dimensional stability, radiation attenuation |
Surgical Instruments | Wear-resistant coatings, cutting edges | 9.7% | Hardness, edge retention, sterilizability |
Drug Delivery Systems | Controlled release matrices, barriers | 16.2% | Chemical stability, controlled porosity |
Dental and orthopedic implant technology has particularly benefited from zirconium silicate advancements. Dental implants utilizing zirconium silicate-based ceramics combine excellent mechanical properties with natural appearance, addressing both functional and aesthetic requirements. In orthopedic applications, zirconium silicate components in joint replacements demonstrate superior wear resistance compared to conventional materials, potentially extending implant lifespans by 30-50%.
Radiation shielding and imaging equipment components represent another significant growth area. Zirconium silicate’s high density and atomic structure make it effective for attenuating radiation while maintaining structural integrity. These properties prove valuable in both diagnostic equipment design and radiation therapy applications, where precise control of radiation exposure is critical.
How Are Environmental Technologies Driving New Applications?
Environmental technologies have emerged as a significant growth market for zirconium silicate products, driven by increasing regulatory pressures and corporate sustainability initiatives worldwide. The material’s exceptional chemical stability and performance under harsh conditions make it particularly valuable for addressing environmental challenges.
What specific properties make this material so effective for environmental applications? The combination of chemical inertness, thermal stability, and mechanical durability allows zirconium silicate components to function reliably in the corrosive, high-temperature environments typical of pollution control systems. These properties translate to longer service life and more consistent performance compared to conventional alternatives.
Water treatment and filtration system applications represent one of the largest growth segments. Zirconium silicate-based ion exchange materials demonstrate exceptional selectivity for removing heavy metals and radioactive contaminants from water supplies. Their stability in both acidic and basic conditions allows operation across a wide pH range without degradation, a critical advantage in variable water treatment environments.
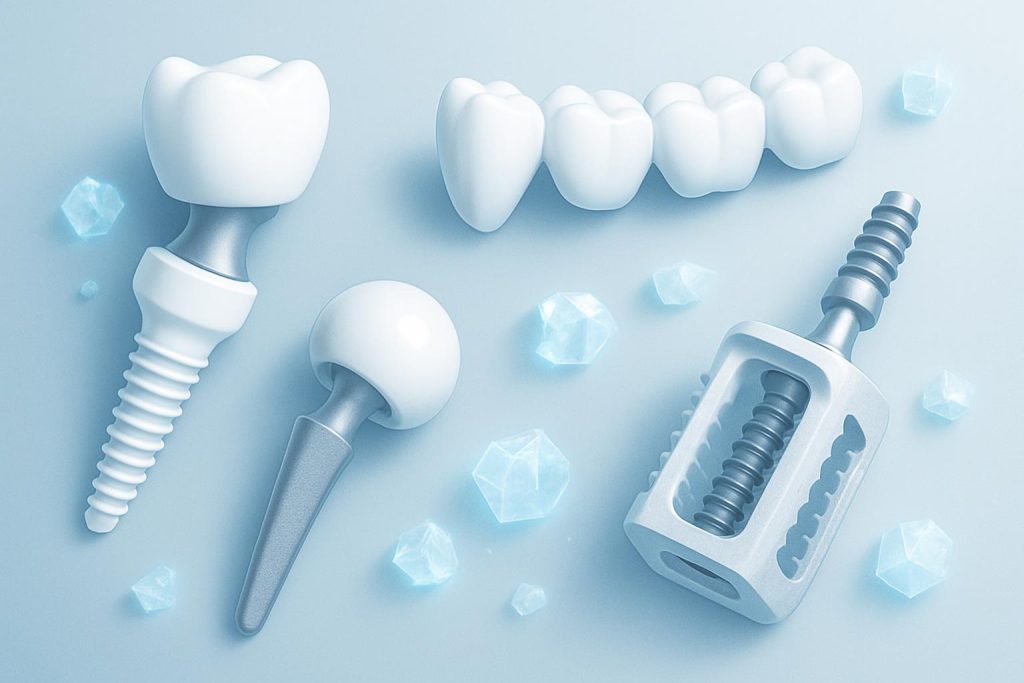
Air pollution control equipment represents another significant application area. Zirconium silicate-based catalyst supports in emissions control systems maintain structural integrity under the high temperatures and corrosive conditions of exhaust streams. These materials also demonstrate excellent resistance to thermal cycling, preventing the cracking and degradation that plague conventional catalyst supports.
Regulatory drivers worldwide continue strengthening, creating sustained demand growth. Increasingly stringent water quality standards, air emissions limits, and waste management requirements all favor advanced materials that enable more effective environmental protection.
What Supply Chain and Production Factors Will Influence Future Growth?
Supply chain dynamics and production capabilities will play crucial roles in determining which markets can fully capitalize on zirconium silicate’s potential. As demand grows across multiple sectors, understanding these factors becomes increasingly important for procurement teams and business planners.
How will these behind-the-scenes factors shape market development? The interplay between raw material availability, processing capacity, and geopolitical considerations will create both opportunities and constraints. Companies with secure supply chains and efficient production methods will gain competitive advantages in rapidly growing application areas.
Raw material sourcing challenges vary significantly by grade and purity requirements. Standard industrial grades of zirconium silicate remain widely available from multiple global sources, with Australia, South Africa, and China representing the largest producers. However, specialized high-purity grades required for electronics and medical applications face more constrained supply, with only a handful of producers capable of meeting the most stringent specifications.
Supply Chain Factor | Current Status | Future Outlook | Strategic Implications |
Raw Material Availability | Adequate for most grades | Potential constraints for specialized grades | Diversification of supply sources recommended |
Production Capacity | 82% utilization globally | Expansion projects adding 15% by 2027 | Short-term price stability expected |
Processing Technology | Conventional methods dominant | Advanced processing gaining market share | Quality/cost improvements anticipated |
Geopolitical Factors | Moderate supply risk | Increasing focus on secure supply chains | Regional production advantages emerging |
Sustainability Requirements | Growing importance | Mandatory reporting expected by 2028 | Early adopters gain market advantage |
Production capacity expansion projects are underway worldwide, with approximately 320,000 metric tons of new annual capacity expected to come online by 2027. These expansions focus primarily on higher-value specialized grades rather than bulk industrial material, reflecting the shifting demand profile toward technical applications.
Processing technology advancements continue improving both quality and cost profiles. Newer facilities utilize more energy-efficient processing methods that reduce production costs by 15-20% while simultaneously improving product consistency. Advanced classification and purification techniques enable tighter control of particle size distribution and chemical composition, critical factors for high-performance applications.
Conclusion
The zirconium silicate market has undergone remarkable transformation in recent years, evolving from traditional applications to diverse high-growth sectors. This article examines our analysis of market data, industry trends, and emerging applications to identify which sectors will drive future demand growth. Our findings reveal that while advanced ceramics maintain leadership, electronics, green energy, healthcare, and environmental technologies show the strongest growth trajectories. Companies positioning their procurement and development strategies around these high-potential markets will gain significant competitive advantages in the coming decade.
FAQ Section
Q1: Which industry sector is expected to show the highest percentage growth rate for zirconium silicate products through 2030?
Based on current market projections, the green energy sector—specifically hydrogen production applications—shows the highest percentage growth rate at 22.6% annually through 2030. This is driven by zirconium silicate’s exceptional performance in hydrogen production systems, where its chemical resistance and thermal stability provide significant advantages over conventional materials. Electronics and semiconductor applications follow closely at 18-20% growth, particularly in thermal management applications for high-performance computing.
Q2: How do regional market dynamics differ for zirconium silicate products?
Regional market dynamics show distinct patterns. Asia-Pacific dominates both production (68%) and consumption (62%), led by China, Japan, and South Korea’s manufacturing sectors. North America and Europe together represent 30% of consumption, focusing on high-value applications in aerospace, medical, and advanced electronics. The fastest growth is occurring in India, Southeast Asia, and Brazil, where expanding manufacturing capabilities and infrastructure development create new demand vectors. Middle Eastern countries are increasing investments in processing capabilities, leveraging energy cost advantages.
Q3: What technological innovations are most likely to disrupt the zirconium silicate market in the next five years?
Nanotechnology applications represent the most significant potential disruptor, with nano-scale zirconium silicate showing 30-50% performance improvements in catalytic, electronic, and energy storage applications. Advanced manufacturing techniques, particularly additive manufacturing with zirconium silicate-enhanced materials, could open entirely new application categories. Quantum computing and advanced semiconductor materials may create specialized high-value niches. Additionally, circular economy initiatives focusing on recovery and recycling of zirconium compounds from end-of-life products could significantly impact supply dynamics and sustainability metrics.
Q4: How are sustainability requirements influencing zirconium silicate market development?
Sustainability requirements are increasingly shaping market development through multiple mechanisms. Manufacturers are investing in energy-efficient processing methods that reduce carbon footprint by 25-40%. Life cycle assessments are becoming standard purchasing requirements, favoring materials with lower environmental impacts. Recycling initiatives for post-industrial and post-consumer zirconium silicate are expanding, with recovery rates improving from 12% to 28% since 2020. Regulatory frameworks in Europe and North America now mandate sustainability reporting for mineral processing, creating competitive advantages for producers with strong environmental performance.
Q5: What supply chain risks should procurement managers consider when sourcing zirconium silicate products?
Procurement managers should consider several key supply chain risks. Geographic concentration of high-purity processing capabilities creates potential bottlenecks, particularly for electronics and medical grades. Energy cost volatility significantly impacts production economics, as processing is energy-intensive. Transportation disruptions affect just-in-time delivery systems, requiring strategic inventory management. Regulatory changes regarding mining and processing can create sudden supply constraints in certain regions. Quality consistency varies between suppliers, particularly for specialized applications requiring tight specifications. Developing relationships with multiple qualified suppliers and implementing rigorous quality verification protocols helps mitigate these risks.