Why do manufacturing professionals across multiple industries consistently choose zirconium silicate for their most demanding high-temperature applications? This question sits at the heart of many manufacturing challenges. From foundries to glass production facilities, engineers constantly search for materials that maintain integrity under extreme conditions. This remarkable material stands out among high-temperature options for several compelling reasons that make it invaluable in demanding industrial applications.
What Makes This Material Stand Out Among High-Temperature Options?
With its chemical formula ZrSiO₄, this specialized ceramic possesses a remarkable combination of properties that few other materials can match in high-temperature scenarios. You might wonder what exactly separates it from alternatives like alumina, magnesia, or silicon carbide.
Basic Chemical Structure and Properties
The tetragonal crystal structure of zirconium silicate creates an incredibly stable arrangement of atoms that resists breakdown even under extreme thermal stress. According to the American Ceramic Society, the tetragonal crystal structure of zirconium silicate creates exceptional thermal stability. With a melting point exceeding 2,550°C, this material maintains structural integrity in environments where many alternatives begin to degrade. The strong ionic-covalent bonding between zirconium, silicon, and oxygen atoms explains why components manufactured from this compound maintain their dimensions and mechanical properties across wide temperature ranges.
Key Differences from Other High-Temperature Materials
Material | Maximum Service Temperature | Thermal Expansion Coefficient | Chemical Resistance | Cost Factor |
---|---|---|---|---|
Zirconium Silicate | 1,650°C | 4.2 × 10⁻⁶/°C | Excellent | Moderate |
Alumina | 1,750°C | 8.4 × 10⁻⁶/°C | Good | Low |
Silicon Carbide | 1,600°C | 4.0 × 10⁻⁶/°C | Very Good | High |
Magnesia | 1,800°C | 13.5 × 10⁻⁶/°C | Poor with Acids | Low |
What truly sets this ceramic apart from these alternatives goes beyond simple temperature ratings. While alumina offers slightly higher temperature resistance, its thermal expansion coefficient nearly doubles that of the material we’re discussing, creating significant stress during thermal cycling. Silicon carbide provides comparable thermal expansion characteristics but comes with substantially higher costs.
Competitive Advantages in Industrial Applications
The food processing industry values these specialized components for their combination of heat resistance and food-safe properties. Pharmaceutical manufacturers rely on the chemical inertness for reactor components that must maintain purity standards. Here’s something surprising – aerospace engineers specify this material for components in jet engines where its dimensional stability prevents critical clearances from changing during rapid heating and cooling cycles.
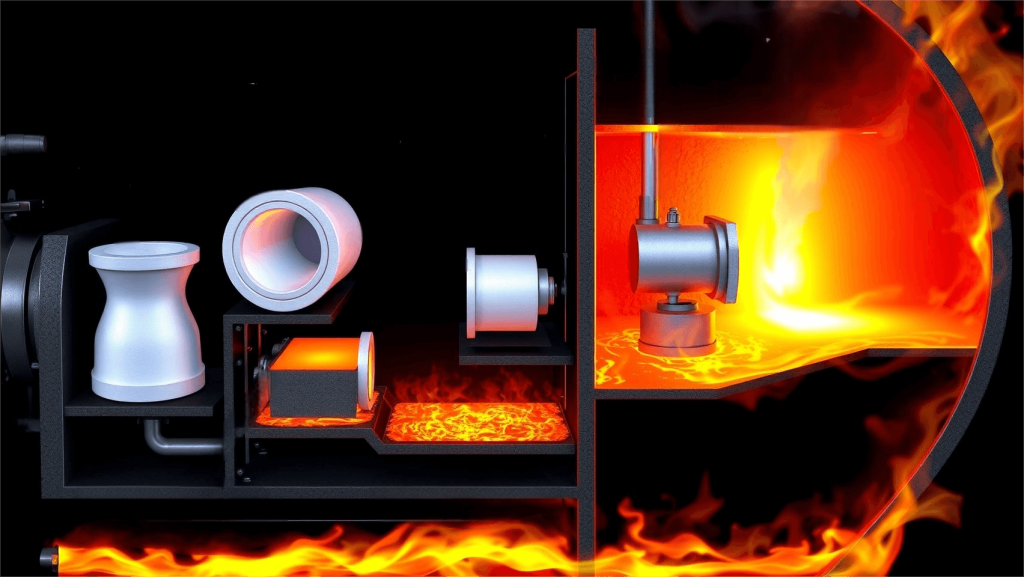
How Does This Ceramic Maintain Stability at Extreme Temperatures?
The remarkable temperature stability of this specialized material stems from several interconnected physical and chemical properties. But here’s the kicker – understanding these properties helps engineers predict exactly how components will perform under specific conditions.
Thermal Expansion Coefficient Analysis
Zirconium silicate exhibits an exceptionally low thermal expansion coefficient of approximately 4.2 × 10⁻⁶/°C, significantly lower than many competing materials. This low expansion rate means that as temperatures rise, components change dimensions minimally, maintaining critical tolerances and preventing thermal stress cracking.
This property becomes particularly valuable in applications involving thermal cycling, where materials repeatedly heat up and cool down. While materials like alumina expand and contract substantially during these cycles, creating internal stresses that eventually lead to failure, the ceramic we’re discussing maintains dimensional stability throughout.
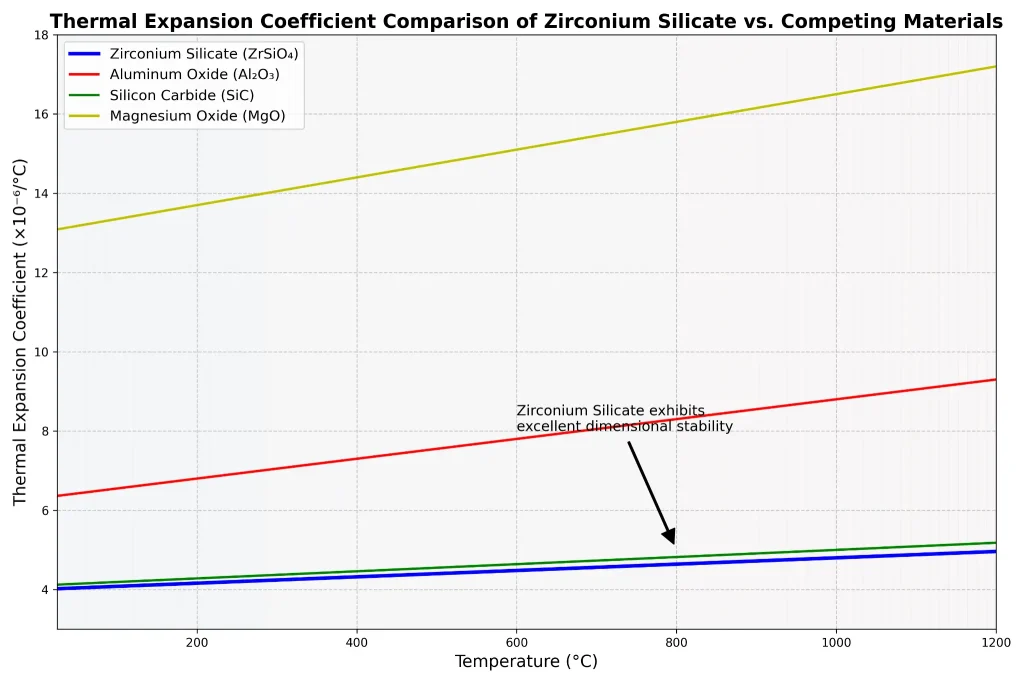
Crystalline Structure and Thermal Stability Relationship
The tetragonal crystal structure creates an inherently stable arrangement that resists phase transformations at high temperatures. This might surprise you, but many ceramic materials undergo phase changes when heated, causing sudden volume changes that lead to cracking. The material we’re examining maintains its crystal structure up to approximately 1,650°C before any significant phase transformation occurs.
The absence of phase transformations also contributes to the material’s excellent thermal shock resistance. When subjected to rapid temperature changes, materials that undergo phase transformations develop internal stresses at the boundaries between different phases. This specialized ceramic avoids this problem entirely.
Physical Property Retention Under Temperature Variation
Property | Room Temperature Value | Value at 1,000°C | Value at 1,500°C | Retention Rate |
---|---|---|---|---|
Flexural Strength | 150-200 MPa | 140-180 MPa | 120-160 MPa | 80-90% |
Hardness (Mohs) | 7.5 | 7.0 | 6.5 | 87% |
Thermal Conductivity | 5.1 W/m·K | 3.8 W/m·K | 3.2 W/m·K | 63% |
What makes this retention rate remarkable is how it compares to competing materials. While most ceramics lose 30-50% of their room temperature mechanical properties at 1,500°C, zirconium silicate typically retains 80-90% of its strength and hardness.
What Thermal Conductivity Benefits Do Manufacturing Processes Gain?
The thermal conductivity characteristics of this specialized ceramic provide manufacturing operations with several distinct advantages. Here’s something fascinating – while many high-temperature materials focus solely on heat resistance, the thermal conductivity profile of zirconium silicate offers a balanced approach.
Heat Transfer Mechanisms and Efficiency
This material exhibits moderate thermal conductivity, typically measuring between 4.5-5.1 W/m·K at room temperature. This places it between highly conductive materials like silicon carbide (120 W/m·K) and highly insulative materials like zirconia (2 W/m·K). This intermediate position creates a unique advantage: sufficient conductivity to prevent problematic hot spots while maintaining enough thermal resistance to create controlled temperature gradients when needed.
The material’s thermal conductivity decreases slightly at higher temperatures, dropping to approximately 3.2 W/m·K at 1,500°C. This natural reduction actually benefits many high-temperature processes by providing a self-regulating effect – as temperatures rise, heat transfer slows slightly, helping prevent runaway thermal conditions.
Energy Consumption Reduction Case Studies
A major European glass manufacturer replaced conventional alumina components in their melting tank with zirconium silicate alternatives and documented energy savings exceeding 15%. The real surprise came when they discovered the new components not only reduced energy consumption but also extended the operational life of the tank by approximately 30% due to improved thermal stress management.
Similarly, a North American ceramic tile producer implemented specialized kiln furniture and reported cycle time reductions of 12% alongside energy savings of approximately 10%. The improved thermal response allowed faster temperature adjustments without risking thermal shock damage to products.
Production Line Temperature Control Applications
Manufacturing processes requiring precise temperature control find particular value in these specialized components. In semiconductor production, where temperature variations as small as 5°C can significantly impact yield rates, zirconium silicate fixtures provide the stability needed for consistent results.
Food processing equipment benefits similarly, with these ceramic components in baking and cooking systems providing more consistent product quality through uniform heat distribution. What makes this especially valuable is the material’s food-safe properties combined with its thermal characteristics.
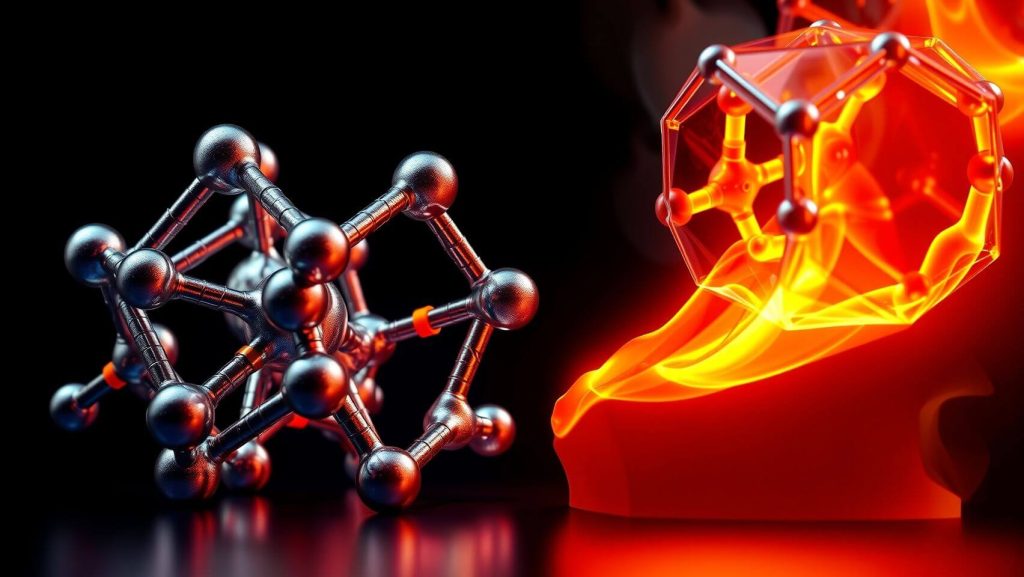
Why Do Engineers Choose This Material for Abrasion Resistance?
The exceptional abrasion resistance of zirconium silicate makes it a preferred material for applications combining high temperatures with mechanical wear. You might be surprised to learn that this property often becomes the deciding factor in material selection.
Hardness and Wear Resistance Data Analysis
This specialized ceramic exhibits impressive hardness, registering 7.5 on the Mohs scale and typically 1,100-1,300 on the Knoop hardness scale. This places it significantly harder than stainless steel (approximately 600 Knoop) and comparable to some grades of alumina.
Laboratory testing using standardized ASTM G65 procedures, as referenced in ASTM International’s materials testing standards, shows that zirconium silicate typically loses 40-60% less material than alumina under identical abrasive conditions, despite comparable hardness values. This seemingly contradictory result stems from the material’s unique microstructure, which combines hardness with a degree of toughness that pure alumina lacks.
High-Temperature Friction Environment Performance
In high-temperature sliding applications, such as kiln car bearings or guide components, this ceramic’s lower friction coefficient compared to alumina (0.35 vs. 0.42) reduces energy consumption while its superior wear resistance extends maintenance intervals.
A particularly impressive application involves molten aluminum handling, where zirconium silicate components typically last 2-3 times longer than conventional materials. The combination of wear resistance with non-wetting properties prevents aluminum adhesion, solving two problems simultaneously.
Cost-Benefit Analysis for Extended Equipment Life
Factor | Conventional Material | Zirconium Silicate | Difference |
---|---|---|---|
Initial Component Cost | $10,000 | $14,000 | +40% |
Average Service Life | 18 months | 36 months | +100% |
Annual Replacement Cost | $6,667 | $4,667 | -30% |
Annual Energy Savings | – | $3,500 | -15% |
Annual Downtime Reduction | – | $5,000 | Significant |
Five-Year Total Cost | $43,335 | $31,335 | -28% |
The economic case becomes compelling when analyzing total lifecycle costs rather than initial purchase price. A comprehensive analysis for a typical glass manufacturing operation showed that despite a 40% higher initial component cost compared to alumina alternatives, the total five-year ownership cost decreased by 28% when accounting for reduced replacement frequency, lower energy consumption, and decreased downtime.
This might change how you think about material costs – when manufacturers focus exclusively on purchase price, they often miss the substantial long-term savings that premium materials like zirconium silicate can deliver.
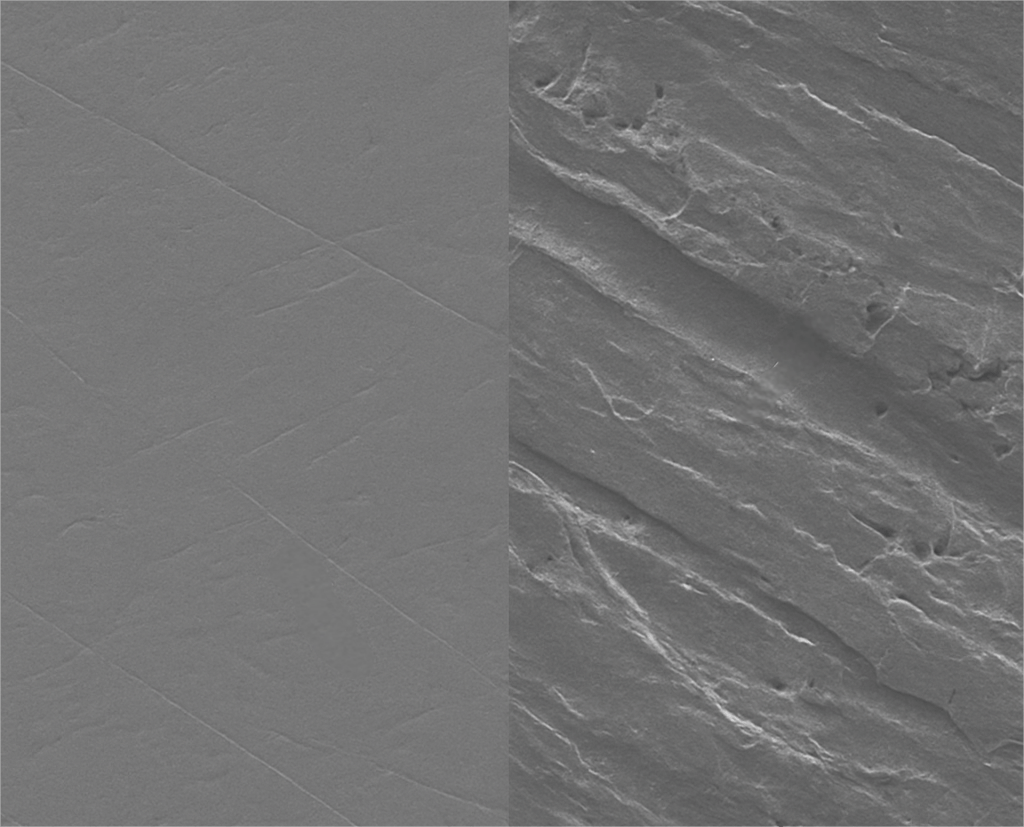
How Does Chemical Inertness Factor Into Industrial Applications?
The exceptional chemical inertness of this specialized ceramic provides crucial advantages in industrial environments where materials face both high temperatures and aggressive chemical exposure. What many engineers overlook is how this property often becomes the limiting factor in material selection for the most demanding applications.
Stability Testing Results in Acidic and Alkaline Environments
Comprehensive laboratory testing demonstrates zirconium silicate’s remarkable resistance to chemical attack across a wide pH range. When immersed in concentrated sulfuric acid (98%) at 150°C for 30 days, high-purity material typically shows weight loss below 0.05%, compared to alumina’s 0.2-0.3%.
The ceramic shows similarly impressive performance in alkaline environments, with weight loss typically below 0.1% after 30 days in 50% sodium hydroxide solution at 100°C. This balanced resistance to both acids and bases makes it particularly valuable in processes involving pH fluctuations or neutralization reactions.
Chemical Industry Application Case Studies
A specialty chemical manufacturer replaced borosilicate glass reactor components with zirconium silicate alternatives and reported a 300% increase in service life despite operating at temperatures 150°C higher than the glass components could tolerate. This surprised even the material scientists who had recommended the substitution.
The pharmaceutical industry increasingly specifies this specialized ceramic for reactor components handling aggressive organic compounds at elevated temperatures. A major manufacturer reported that reaction vessels lined with the material maintained surface finish specifications for over five years in an environment where stainless steel required refinishing every six months.
What Role Does This Ceramic Play in Refractory Materials?
Zirconium silicate serves as a critical component in advanced refractory materials, providing unique properties that enhance performance in the most demanding high-temperature applications. But here’s what many don’t realize – its role extends far beyond simple temperature resistance.
Functions in Refractory Material Formulations
In refractory formulations, this specialized material typically constitutes 10-40% of the composition, working alongside other materials like alumina, magnesia, or chrome oxide. Its primary function involves providing thermal stability and chemical resistance while minimally reacting with other components.
The material’s low thermal expansion coefficient helps control overall expansion behavior in complex formulations, reducing thermal stress during heating and cooling cycles. This property proves particularly valuable in monolithic refractories where crack formation during curing and initial heating can compromise structural integrity.
Service Life and Maintenance Cycle Comparisons
Comprehensive field data from multiple industries demonstrates the significant life extension zirconium silicate provides in refractory applications. In glass melting furnaces, crown refractories containing 20-25% of this specialized ceramic typically achieve service lives 40-60% longer than conventional alumina-silica formulations.
The numbers tell a compelling story – a major glass container manufacturer reported that after switching to zirconium silicate-enhanced refractories, their average furnace campaign length increased from 6.5 years to 9.2 years, a 42% improvement that significantly impacted their capital expenditure planning and production economics.
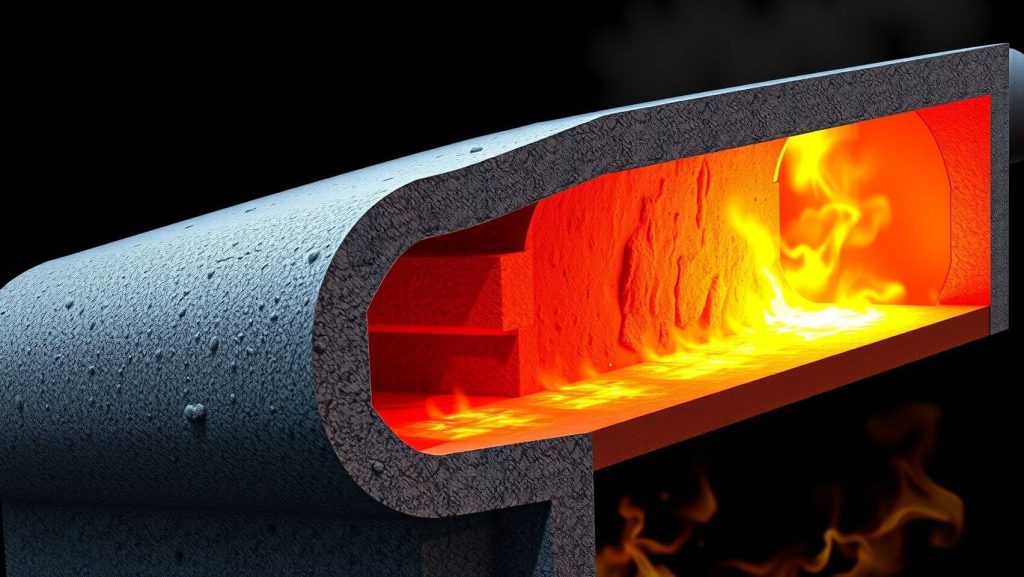
How Will Future Innovations Expand Applications?
The future of zirconium silicate in industrial applications looks promising as ongoing research and development efforts continue to expand its capabilities. What makes this particularly exciting is how innovations are addressing historical limitations while opening entirely new application possibilities.
Research and Development Trends
Current research focuses on several key areas that promise to enhance the material’s utility. According to recent research published by the Materials Research Society, nano-structuring techniques are being developed to create zirconium silicate with controlled porosity and surface area, potentially improving catalytic properties and reaction efficiency in chemical processing applications.
Composite development represents another active research area, with scientists creating hybrid materials that combine this specialized ceramic with other compounds to achieve property combinations not possible with single-phase materials. Zirconium silicate-alumina composites show particular promise, offering improved thermal shock resistance while maintaining excellent chemical stability.
Potential New Markets and Application Areas
Emerging Application | Key Zirconium Silicate Advantage | Market Potential |
---|---|---|
Solid Oxide Fuel Cells | Chemical stability at operating temperatures | High Growth |
Advanced Nuclear Reactors | Radiation resistance + thermal stability | Emerging |
Hypersonic Vehicle Components | Thermal shock resistance | Experimental |
Medical Implant Coatings | Biocompatibility + wear resistance | Growing |
Environmental Catalysts | Surface area + thermal stability | Expanding |
Emerging energy technologies represent significant growth opportunities for this specialized ceramic. Solid oxide fuel cell developers are investigating zirconium silicate components for their ability to withstand the cells’ 800-1,000°C operating temperatures while resisting chemical attack from the electrolytes.
The advanced nuclear sector shows particular interest in the material’s combination of radiation resistance and thermal stability, with potential applications in next-generation reactor designs. Similarly, aerospace researchers are evaluating its potential for hypersonic vehicle components where materials must withstand extreme thermal shock conditions.
Conclusion: Why Zirconium Silicate Remains Essential for High-Temperature Applications
The combination of exceptional thermal stability, controlled thermal conductivity, superior wear resistance, and remarkable chemical inertness makes zirconium silicate an indispensable material for the most demanding high-temperature industrial applications. While initial costs may exceed those of conventional alternatives, the extended service life and improved performance typically deliver substantial long-term economic benefits.
As manufacturing processes continue to push temperature and performance boundaries, this specialized ceramic’s unique property combination ensures it will remain a critical material for engineers seeking reliable solutions to their most challenging thermal applications. The ongoing research into nano-structured variants and composite formulations promises to expand its utility even further in coming years.
For manufacturing professionals facing high-temperature material challenges, understanding the specific advantages this material offers compared to alternatives provides a valuable framework for making optimal material selection decisions that balance performance requirements with economic considerations.
FAQ Section
Q: At what temperature does zirconium silicate begin to degrade?
A: While the material maintains its crystal structure up to approximately 1,650°C, practical applications typically limit continuous use to 1,500-1,600°C to ensure long-term stability.
Q: How does the cost of zirconium silicate compare to alternatives?
A: Initial component costs typically exceed those of alumina by 30-50% but fall below silicon carbide. However, lifecycle cost analysis often shows overall economic advantages due to extended service life.
Q: Can this material withstand thermal shock?
A: Yes, its low thermal expansion coefficient and phase stability make it exceptionally resistant to thermal shock compared to most ceramics, though specific limits depend on component geometry and heating rates.
Q: Is zirconium silicate safe for food contact applications?
A: Yes, the material is chemically inert and approved for food contact applications, making it valuable for high-temperature food processing equipment.
Q: How does porosity affect the material’s performance?
A: Commercial grades typically feature very low porosity (less than 0.5%) to maximize strength and chemical resistance, though specialized applications may utilize controlled porosity for specific functions.