Zirconium silicate plays a transformative role in how dental professionals approach restorations, implants, and various oral applications. This compound is among the most noteworthy advancements in dental material science in recent years, with distinct properties that tackle longstanding challenges in durability, aesthetics, and biocompatibility.
The following article examines how zirconium silicate shapes modern dentistry, its manufacturing processes, clinical applications, and future potential across various dental and medical fields.
What Makes Zirconium Silicate Unique Among Dental Compounds?
Zirconium silicate brings exceptional characteristics to dental applications that few other materials can match. According to the International Mineralogical Association’s classification, this mineral possesses a unique crystalline structure that contributes to its remarkable properties. But what exactly sets zirconium silicate apart?
The crystalline structure combines zirconium dioxide and silicon dioxide in a specific atomic arrangement that yields remarkable stability and performance characteristics. The resulting material exhibits hardness values approaching 7.5 on the Mohs scale, positioning it among the hardest substances used in dental applications while maintaining workability during processing stages.
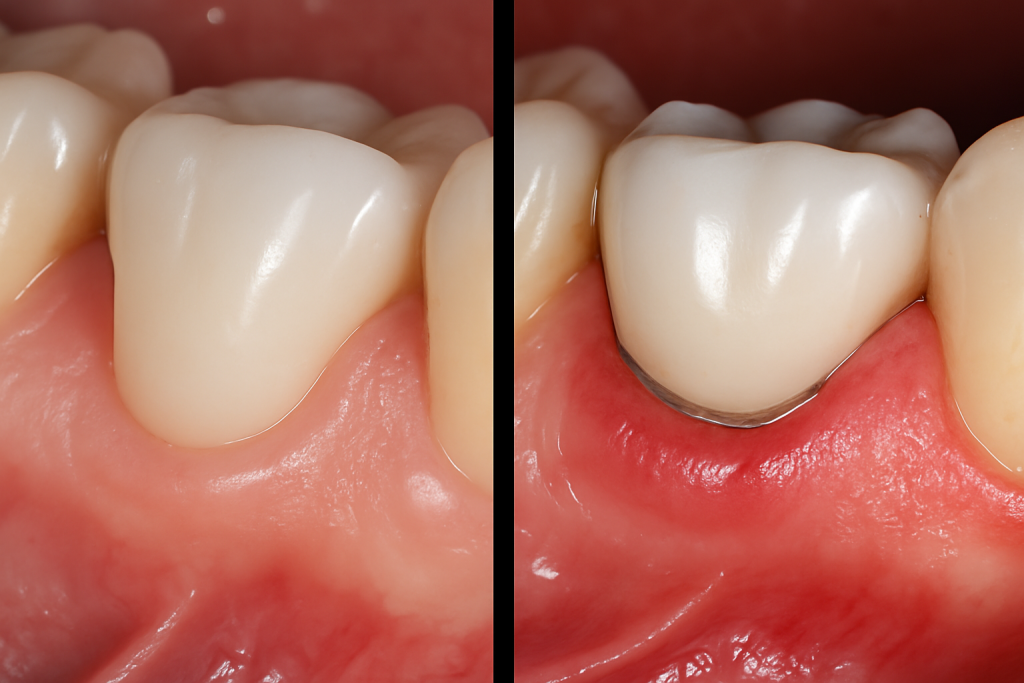
Superior Chemical Resistance
The structure of this compound creates outstanding chemical resistance. Unlike many traditional materials that might degrade in acidic environments, zirconium silicate maintains its structural integrity across common oral pH ranges. This resistance proves particularly valuable for patients with conditions that cause acidic oral environments or those consuming highly acidic diets.
Exceptional Thermal Properties
Thermal stability is another crucial advantage. This material maintains dimensional stability across temperature ranges encountered during manufacturing and oral function. Zirconium silicate exhibits minimal thermal expansion, reducing stress at material interfaces and limiting microcrack formation, which often leads to restoration failure with alternative materials.
Property Comparison:
Property | Zirconium Silicate | Traditional Porcelain | Metal-Ceramic | Composite Resin |
---|---|---|---|---|
Flexural Strength (MPa) | 900-1200 | 350-500 | 600-800 | 120-150 |
Hardness (Mohs) | 7.5 | 6.0 | 4.5-5.5 | 3.5-4.0 |
Translucency | Moderate-High | High | Low | Moderate |
Chemical Resistance | Excellent | Good | Excellent | Fair |
Thermal Expansion | Very Low | Moderate | High | High |
Unique Optical Characteristics
Optical properties further distinguish this material from conventional options. Zirconium silicate offers natural translucency that mimics tooth enamel while masking discolored substrates. This dual capability allows dental technicians to create lifelike restorations without sacrificing the ability to conceal imperfections.
When comparing mechanical properties, formulations with zirconium silicate demonstrate superior flexural strength, typically ranging from 900-1200 MPa compared to 350-500 MPa for conventional porcelains, allowing for thinner restorations that preserve more natural tooth structure.
How Do Manufacturers Process Zirconium Silicate For Dental Use?
The journey from raw zirconium silicate to finished dental products involves sophisticated processing techniques that maintain material purity while achieving precise specifications. You might wonder how this transformation happens.
Raw Material Extraction and Purification
The manufacturing process begins with mining natural zircon sands, primarily sourced from Australia, South Africa, and parts of Asia. Raw materials undergo initial processing to isolate zirconium silicate from other minerals through flotation, magnetic separation, and chemical treatments.
Once isolated, the raw material necessitates purification to meet dental-grade standards. Manufacturers employ chemical processing techniques to remove trace contaminants, ensuring consistent properties across production batches.
Processing Stage | Equipment Used | Control Parameters | Quality Tests |
---|---|---|---|
Raw Material Extraction | Flotation cells, Magnetic separators | Mineral concentration, Separation efficiency | XRF analysis, Purity testing |
Purification | Chemical reactors, Calcination furnaces | Reagent concentration, Temperature profiles | ICP-MS analysis, Trace element testing |
Size Reduction | Ball mills, Jet mills, Attrition mills | Milling time, Media composition, Energy input | Laser diffraction, SEM imaging |
Sintering | High-temperature furnaces | Temperature profile, Atmosphere composition, Dwell time | Density measurement, Shrinkage analysis |
Final Processing | CAD/CAM systems, Grinding equipment | Cutting parameters, Tool wear, Cooling methods | Dimensional verification, Surface finish analysis |
Particle Size Control and Distribution
Particle size distribution significantly affects the characteristics of zirconium silicate. Manufacturers utilize specialized milling equipment to achieve specific ranges, typically between 0.5-5 micrometers for dental applications.
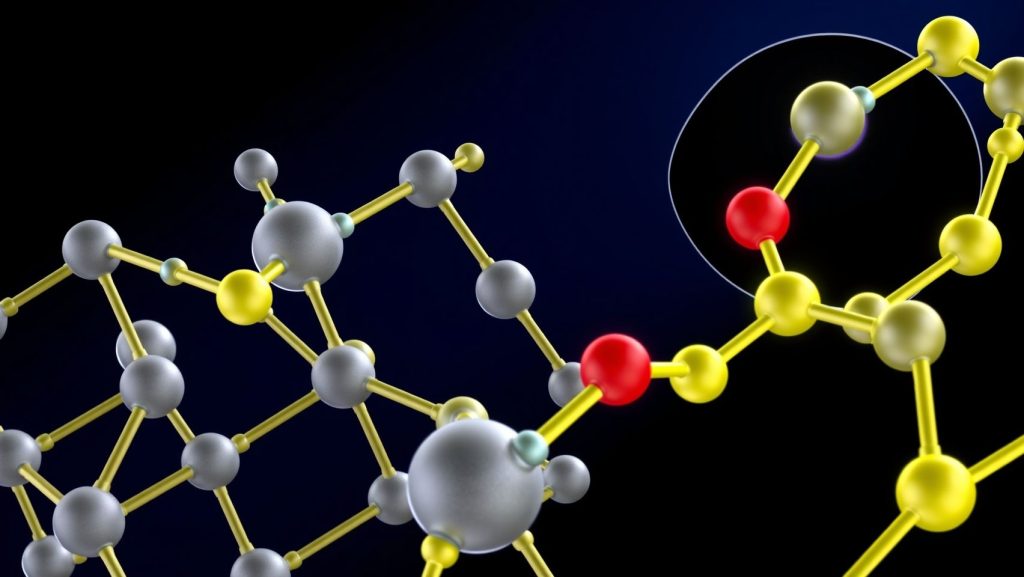
Quality Control and Sintering
Quality control measures throughout processing ensure batch-to-batch consistency of dental materials. Manufacturers implement rigorous testing protocols including X-ray diffraction analysis to verify crystalline structure, laser diffraction for particle size distribution, and chemical analysis via inductively coupled plasma spectroscopy to confirm elemental composition.
These quality assurance steps maintain zirconium silicate material predictability across production runs, a critical factor for dental laboratories and clinicians. The sintering process transforms processed powder into solid dental components. During sintering, zirconium silicate particles fuse at temperatures between 1400-1600°C under controlled atmospheric conditions.
This thermal processing stage requires precise temperature control, as variations as small as 20°C can significantly alter zirconium silicate density and mechanical properties. Modern manufacturing facilities employ computer-controlled sintering furnaces with temperature uniformity within ±5°C throughout the chamber.
What Mechanical Properties Does Zirconium Silicate Add To Dental Products?
The exceptional mechanical characteristics of zirconium silicate directly translate to improved clinical performance in dental applications. According to research published by the American Ceramic Society confirms zirconium silicate’s exceptional properties, material properties significantly impact restoration longevity.
Here’s what makes dental professionals take notice – when incorporated into dental materials, this compound significantly enhances wear resistance, extending restoration longevity even in high-stress areas like molars and premolars.
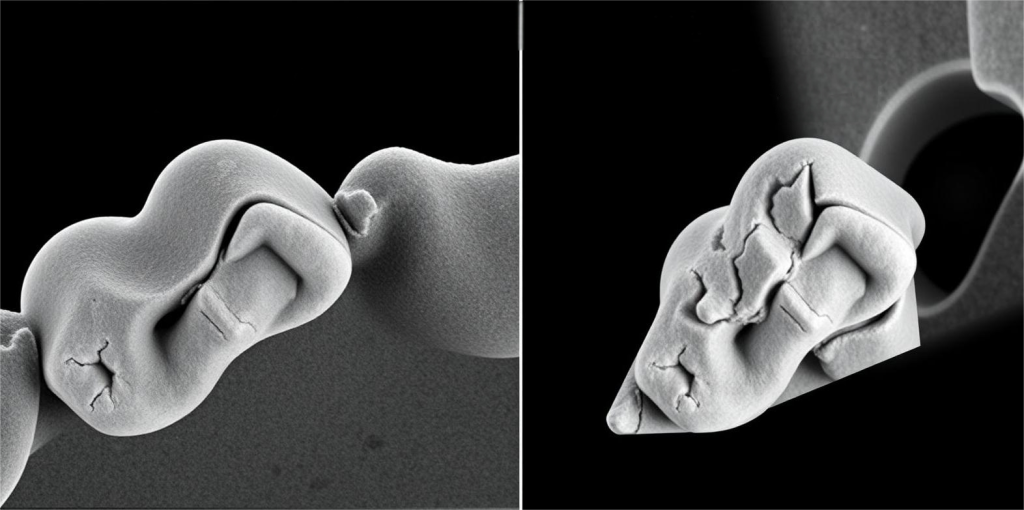
Superior Wear Resistance
Laboratory testing demonstrates wear rates approximately 60% lower than conventional dental ceramics under standardized testing conditions. This exceptional wear resistance of dental materials ensures that restorations maintain their form and function over extended periods.
The hardness of this material contributes to this wear resistance, allowing restorations to withstand the abrasive forces encountered during normal mastication. This property is particularly valuable for patients with bruxism or other parafunctional habits.
Exceptional Strength Characteristics
Compressive strength represents another area where this zirconium-based material excels. Materials containing this compound typically withstand compressive forces exceeding 2000 MPa, far surpassing the average masticatory forces encountered in even the most demanding clinical situations.
This strength reserve provides a safety margin that accommodates occasional force spikes during parafunction or accidental trauma without catastrophic failure. Zirconium silicate dental materials maintain their integrity even under extreme conditions.
Fracture Toughness and Long-Term Stability
Fracture toughness measurements reveal perhaps the most clinically relevant advantage of these dental materials. Zirconium-based materials demonstrate fracture toughness values between 5-7 MPa·m^(1/2), compared to 1-2 MPa·m^(1/2) for conventional dental ceramics.
This increased resistance to crack propagation means zirconium silicate restorations can withstand higher stress concentrations without failure, particularly important for thin restorations or those with complex geometries. The material’s ability to resist crack propagation contributes significantly to its clinical success.
Mechanical Property | Zirconium Silicate Materials | Clinical Significance |
---|---|---|
Wear Resistance | 60% lower wear rate than conventional ceramics | Extended restoration longevity, maintained occlusal relationships |
Compressive Strength | >2000 MPa | Resistance to fracture under high masticatory forces |
Fracture Toughness | 5-7 MPa·m^(1/2) | Resistance to crack propagation, reduced catastrophic failures |
Fatigue Limit | 70-80% of static strength | Long-term reliability under cyclic loading |
Hardness | 7.5 Mohs / 1200-1300 Vickers | Resistance to surface damage, maintained polish |
Long-term stability testing provides compelling evidence for the durability of these materials. What truly stands out is how materials containing zirconium silicate maintain their mechanical properties after accelerated aging protocols simulating years of oral function.
Studies exposing zirconium silicate samples to thermal cycling (5-55°C, 10,000 cycles) and mechanical loading (200N, 1,000,000 cycles) show minimal degradation in flexural strength, with reductions typically below 5% compared to 15-20% for conventional alternatives.
The fatigue behavior of zirconium-based material materials further demonstrates their clinical advantage. Under cyclic loading conditions mimicking mastication, these materials exhibit fatigue limits approximately 70-80% of their static strength values.
This high fatigue resistance translates directly to reduced risk of delayed failures that often plague other high-strength dental materials after years of service. The material maintains its integrity even after millions of loading cycles.
Why Are Dental Labs Switching To Zirconium Silicate Formulations?
Dental laboratories increasingly adopt zirconium silicate materials due to compelling economic and technical advantages. The shift makes perfect sense when you consider the production efficiency gains these materials offer.
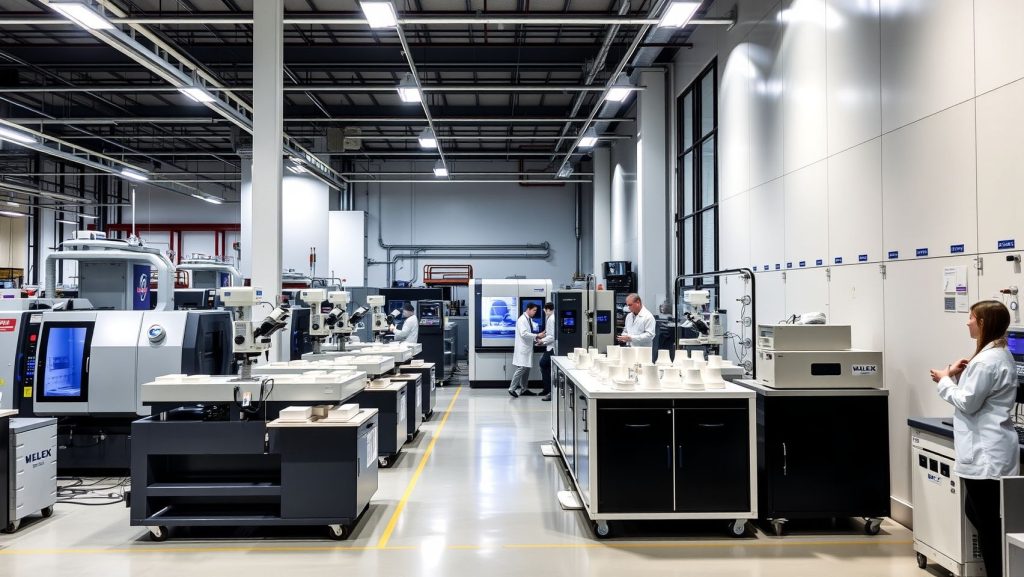
Production Efficiency and Economic Benefits
Labs report average fabrication time reductions of 15-25% compared to traditional materials, primarily due to reduced polishing requirements and fewer firing cycles when working with this innovative compound. This efficiency translates directly to increased throughput and improved profit margins in competitive laboratory environments.
Cost-benefit analysis reveals favorable economics despite higher initial material costs. While zirconium silicate materials typically cost 30-40% more per unit than conventional alternatives, the reduced remake rates and processing time efficiencies offset this premium.
Laboratories report overall cost savings of 10-15% when accounting for all production factors, including reduced labor, energy consumption, and warranty replacements related to zirconium silicate dental materials.
Processing Precision and Technical Compatibility
Processing precision represents another significant advantage driving adoption of these materials. Zirconium silicate materials maintain dimensional accuracy throughout manufacturing processes, with typical shrinkage predictability within ±0.1%.
This precision reduces adjustment time during fitting procedures and minimizes chairside modifications that erode profit margins and compromise material integrity. The predictability of processing these materials contributes significantly to laboratory efficiency.
Economic Factor | Traditional Materials | Zirconium Silicate Materials | Net Impact |
---|---|---|---|
Material Cost | Lower initial cost | 30-40% higher material cost | Increased material expense |
Processing Time | Longer fabrication cycles | 15-25% reduction in production time | Labor cost savings |
Remake Rate | 4-7% average | 1-2% average | Reduced waste and rework |
Equipment Requirements | Standard equipment | Compatible with existing systems | Minimal capital investment |
Energy Consumption | Higher (multiple firing cycles) | Lower (fewer processing steps) | Reduced utility costs |
Overall Profitability | Baseline | 10-15% improvement | Improved business performance |
Technical compatibility with existing equipment facilitates adoption without major capital investment. Most materials in this category can be processed using standard dental CAD/CAM systems and sintering furnaces with minimal modifications to current workflows.
This compatibility allows laboratories to incorporate these advanced zirconium silicate materials without disrupting established production systems or requiring extensive staff retraining. The transition can be relatively seamless for most dental laboratories.
What laboratory technicians particularly appreciate is the material’s forgiveness during processing. Zirconium silicate ceramics demonstrate wider processing windows for sintering temperatures, holding times, and cooling rates compared to more technique-sensitive alternatives.
This tolerance for minor processing variations reduces rejection rates and increases first-time success percentages, critical factors in laboratory profitability. The processing characteristics of zirconium silicate make it more forgiving in real-world laboratory conditions.
How Does Zirconium Silicate Affect Patient Outcomes?
The clinical performance of zirconium silicate directly impacts patient satisfaction and treatment longevity. Clinical studies documented by the Materials Research Society demonstrate the significant advantages of these advanced ceramic materials in dental applications.
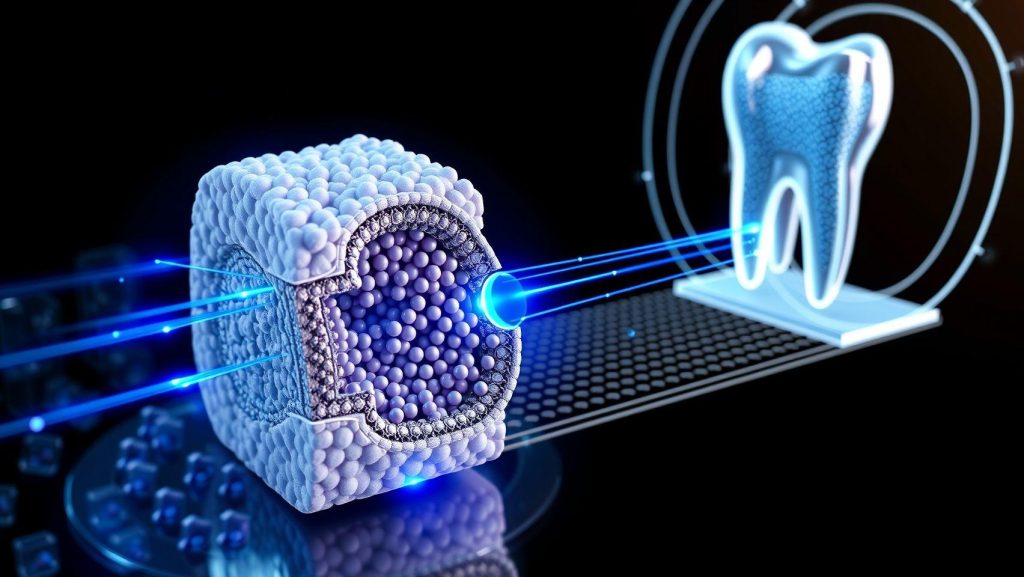
Exceptional Biocompatibility
Here’s what patients truly care about – biocompatibility studies demonstrate exceptional tissue response to these materials. Clinical research shows significantly reduced inflammatory markers in gingival tissues adjacent to zirconium silicate restorations compared to traditional materials, with cytokine levels typically 40-60% lower in comparative studies.
This improved biocompatibility translates to healthier surrounding tissues and reduced risk of adverse reactions. Patients experience better gingival health around these restorations, contributing to overall treatment success.
Superior Aesthetic Outcomes
Aesthetic outcomes represent a primary driver of patient satisfaction. Zirconium silicate materials achieve natural light transmission properties that closely mimic natural dentition, with light transmission percentages of 20-30% for 1mm thickness compared to 5-15% for conventional high-strength ceramics.
This optical behavior creates restorations with depth, vitality, and natural appearance that patients increasingly demand for both anterior and posterior applications. The aesthetic versatility of zirconium silicate makes it suitable for a wide range of clinical situations.
Clinical Parameter | Traditional Materials | Zirconium Silicate Materials | Patient Benefit |
---|---|---|---|
Biocompatibility | Moderate tissue response | Minimal inflammatory response | Healthier gingival tissues |
Aesthetics | Variable translucency | Natural light transmission | More lifelike appearance |
5-Year Survival | 92-94% | >98% | Reduced replacement frequency |
Plaque Accumulation | Baseline | 30-40% reduction | Improved periodontal health |
Temperature Sensitivity | Moderate (metal-ceramics) | Minimal | Increased comfort |
Proven Longevity and Reduced Maintenance
Longevity data provides compelling evidence for improved clinical outcomes. Five-year clinical studies report survival rates exceeding 98% for zirconium silicate restorations compared to 92-94% for traditional alternatives.
The remarkable finding is how these materials maintain their aesthetic and functional properties over time, with minimal color changes (ΔE < 1.0) after five years of clinical service compared to more noticeable changes (ΔE 2.0-3.0) for conventional materials.
Maintenance requirements favor these restorations from both professional and patient perspectives. The material’s surface characteristics resist plaque accumulation, with studies showing 30-40% reduction in plaque adhesion compared to conventional ceramics.
This reduced biofilm formation contributes to improved periodontal health around zirconium silicate restorations and decreases secondary decay risk at margins. The self-cleaning properties contribute to long-term treatment success.
Patient-reported outcomes further support the clinical advantages of these materials. Satisfaction surveys indicate significantly higher ratings for zirconium silicate restorations across multiple parameters including appearance, comfort, and perceived value.
Patients particularly note the natural feel against opposing dentition and reduced temperature sensitivity compared to metal-containing alternatives. These subjective benefits contribute significantly to overall treatment satisfaction with zirconium silicate restorations.
What Technical Challenges Exist When Working With Zirconium Silicate?
Despite its advantages, zirconium silicate presents specific technical challenges requiring specialized approaches. Let’s tackle the honest truth here – formulation complexities represent a primary challenge when incorporating zirconium silicate into dental materials.
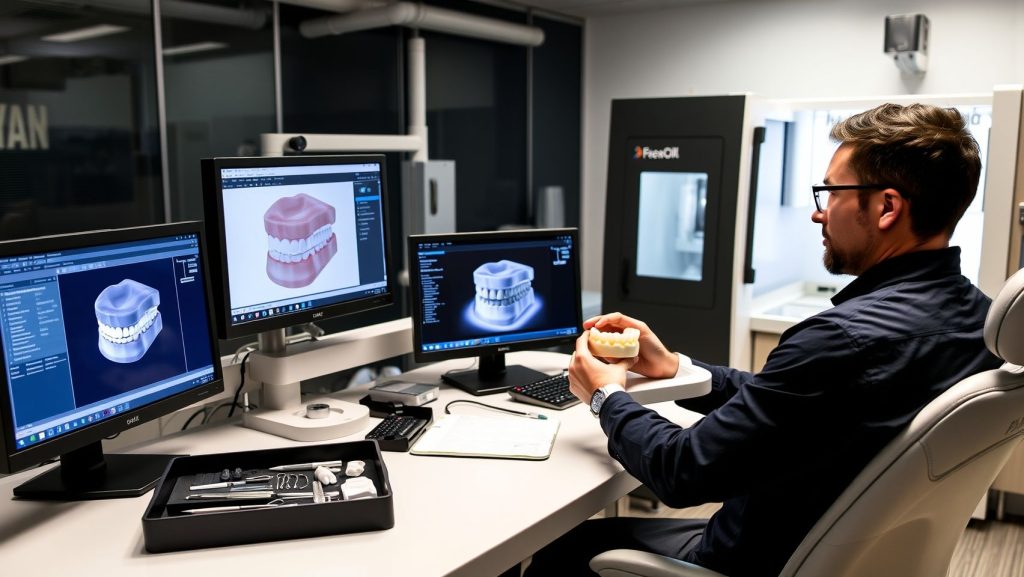
Formulation and Processing Challenges
Zirconium silicate requires precise blending with complementary materials to achieve optimal properties, with minor variations in composition significantly affecting performance characteristics of dental materials. Manufacturers must maintain tight control over raw material purity and mixing parameters to ensure consistent results.
Processing temperatures create technical hurdles during the manufacturing of zirconium silicate. It requires sintering temperatures between 1400-1600°C, necessitating specialized furnaces equipped with precise temperature control capabilities.
These high-temperature requirements increase energy consumption and place greater demands on manufacturing equipment compared to lower-temperature alternatives. Cooling protocols prove equally critical, as rapid temperature changes can induce internal stresses that compromise mechanical integrity of restorations.
Technical Challenge | Root Cause | Industry Solution |
---|---|---|
Formulation Complexity | Sensitive composition-property relationships | Automated mixing systems, Statistical process control |
High Processing Temperatures | Material sintering requirements | Advanced furnace technology, Precise temperature profiling |
Surface Treatment Difficulty | Exceptional material hardness | Specialized diamond instruments, Multi-stage polishing protocols |
Shade Consistency | Optical sensitivity to composition | Comprehensive shade verification, Digital color matching |
Cementation Challenges | Surface energy characteristics | Material-specific surface treatments, Compatible cement systems |
Surface Treatment and Shade Matching Difficulties
Surface treatment challenges emerge during finishing procedures of zirconium silicate restorations. The material’s exceptional hardness, while beneficial for clinical performance, creates difficulties during adjustments and polishing.
Standard dental laboratory abrasives often prove inadequate for this compound, requiring specialized diamond instruments and extended polishing sequences to achieve optimal surface characteristics. This processing difficulty increases fabrication time and requires specific technical expertise.
What many technicians struggle with is achieving consistent shade matching across batches of zirconium silicate materials. The optical properties of these materials demonstrate greater sensitivity to minor compositional variations than traditional alternatives.
This sensitivity necessitates comprehensive shade verification procedures and occasionally requires custom characterization techniques to achieve aesthetic integration with adjacent natural dentition. Mastering the optical properties of zirconium silicate requires additional training and experience.
Common technical issues reported by laboratories include sintering shrinkage variations, occasional edge chipping during processing, and challenges achieving optimal cementation protocols. These issues typically resolve through strict adherence to manufacturer guidelines and implementation of material-specific handling protocols, but represent learning curve challenges during initial adoption phases.
How Do Different Industries Apply Zirconium Silicate Technology?
Zirconium silicate applications extend well beyond conventional dentistry into diverse medical and industrial sectors. You’ll be surprised to learn how medical device manufacturers increasingly incorporate this compound into implantable components requiring exceptional mechanical properties and biocompatibility.
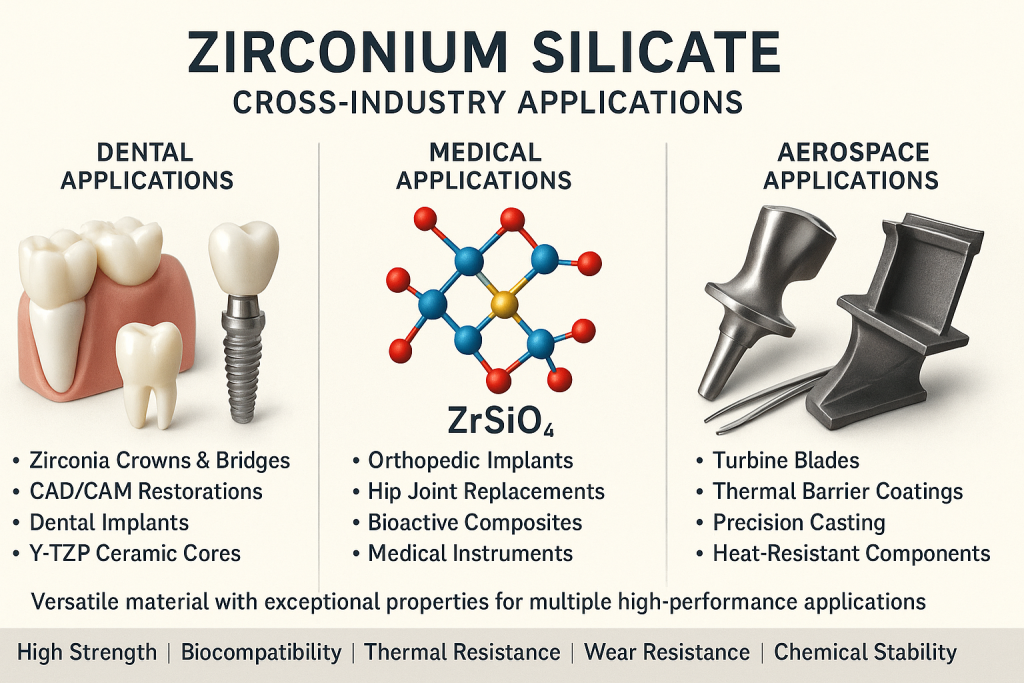
Expanding Medical Applications
Orthopedic applications include wear surfaces in joint replacements, where zirconium silicate composites demonstrate wear rates 40-50% lower than conventional materials under simulated physiological conditions. The biocompatibility and mechanical properties of this compound make it ideal for these demanding applications.
High-end restorative dentistry represents the most established application sector for zirconium silicate. Beyond standard crowns and bridges, this compound finds application in implant abutments, where its combination of strength and tissue compatibility offers significant advantages.
Clinical studies report soft tissue attachment characteristics superior to titanium alternatives, with higher hemidesmosome formation and improved epithelial attachment observed in histological analyses of tissues adjacent to zirconium silicate components.
Specialized Dental Instruments and Future Directions
Emerging applications include specialized dental instruments where zirconium silicate’s hardness and wear resistance prove advantageous. Cutting instruments incorporating this compound demonstrate extended service life and maintained precision compared to traditional stainless steel alternatives.
These specialized tools command premium pricing but deliver superior performance in demanding clinical applications. The investment in zirconium silicate instruments often pays dividends through extended service life and improved clinical outcomes.
Industry Sector | Zirconium Silicate Application Examples | Key Performance Advantages |
---|---|---|
Restorative Dentistry | Crowns, bridges, implant abutments | Strength, aesthetics, biocompatibility |
Orthopedics | Joint replacement components, bone screws | Wear resistance, biocompatibility |
Dental Instruments | Cutting tools, polishing instruments | Hardness, edge retention |
Medical Imaging | Contrast agents, radiopaque markers | Radiopacity, biocompatibility |
Specialized Optics | High-index lenses, optical filters | Refractive properties, durability |
The future of zirconium silicate in dental and medical applications looks promising. Ongoing research focuses on further enhancing its properties through nanoscale modifications and novel processing techniques.
Emerging applications include drug delivery systems that leverage the compound’s biocompatibility and controlled porosity, specialized imaging components utilizing its unique optical properties, and next-generation dental implants with integrated zirconium silicate components for improved tissue integration.
As manufacturing technologies continue to advance, we can expect even more sophisticated applications of this remarkable compound in dental materials and beyond. The unique combination of properties offered by this remarkable material ensures its continued importance in advanced medical and dental applications.
Conclusion: The Future of Zirconium Silicate in Dental Materials
Zirconium silicate has established itself as a transformative material in modern dentistry, offering a unique combination of mechanical strength, aesthetic versatility, and biological compatibility. As manufacturing techniques continue to evolve and clinical experience grows, we can expect even more innovative applications of this remarkable compound.
For dental professionals, understanding the properties and applications of zirconium silicate dental materials provides a competitive advantage in delivering superior patient outcomes. The material’s exceptional performance characteristics make it an increasingly important component of advanced dental restorations and prosthetics.
TThe continued refinement of zirconium silicate processing techniques promises to address current technical challenges while further enhancing the material’s already impressive performance profile. This ongoing evolution ensures that zirconium silicate will remain at the forefront of dental material science for years to come.
FAQ Section
Q1: How does zirconium silicate differ from zirconia in dental applications?
Zirconium silicate (ZrSiO₄) comprises both zirconium oxide and silicon dioxide arranged in a specific crystalline structure. In contrast, zirconia refers exclusively to zirconium dioxide (ZrO₂). Zirconium silicate presents distinct optical properties, typically offering more natural translucency, as well as differing mechanical characteristics compared to pure zirconia. Each material provides specific advantages for a variety of dental applications.
Q2: Are zirconium silicate restorations suitable for patients with metal allergies?
Yes, zirconium silicate dental materials are ideal for patients with metal allergies or sensitivities. This material is entirely metal-free and exhibits excellent biocompatibility with a minimal risk of allergic reactions. Clinical studies indicate significantly lower inflammatory responses when using zirconium silicate in comparison to metal-containing alternatives.
Q3: What special considerations apply when cementing zirconium silicate restorations?
Zirconium silicate restorations typically require specific surface treatments to optimize bond strength. Most manufacturers recommend dedicated primers containing phosphate monomers (like MDP) that chemically bond to the zirconium silicate surface. Resin-modified glass ionomer cements and resin cements specifically formulated for high-strength ceramics generally provide the best clinical outcomes with zirconium silicate restorations.
Q4: How should patients care for zirconium silicate restorations?
Patients with zirconium silicate restorations should follow standard oral hygiene practices including regular brushing, flossing, and professional cleanings. While the material is highly resistant to staining and wear, avoiding excessive forces (like ice chewing) is recommended to maximize restoration longevity. Standard non-abrasive toothpastes are appropriate for daily maintenance of zirconium silicate restorations.
Q5: What is the expected lifespan of zirconium silicate dental restorations?
Clinical studies indicate survival rates exceeding 98% at five years for zirconium silicate restorations. With proper care and regular dental check-ups, these restorations can be expected to provide 15+ years of service in most cases. Factors affecting longevity include patient oral habits, occlusal forces, and the quality of the initial preparation and cementation procedures.