Zirconium carbonate markets face unprecedented growth opportunities as global demand surges across multiple industries. Manufacturing companies struggle to secure reliable supplies while navigating complex market dynamics and regulatory requirements. This article analyzes the key factors driving the projected 6.5% CAGR through 2030, providing actionable insights for procurement teams and strategic planners. Recent market analysis from leading chemical industry researchers confirms zirconium carbonate’s expanding applications and supply chain evolution will create both challenges and opportunities for businesses across the value chain.
What Is Driving Global Demand for Zirconium Carbonate?
The global zirconium carbonate market is experiencing robust growth driven by multiple factors across diverse industries. Raw material demands continue to evolve as manufacturers seek higher performance and more sustainable options.
Here’s what you need to know about the primary demand drivers reshaping this market. Ceramic and glass manufacturing industries represent the largest consumption segment, with zirconium carbonate serving as a critical opacifier and whitening agent. The compound creates the characteristic white, opaque appearance in high-end ceramics and specialty glass products. Market data shows this application segment alone accounts for approximately 35-40% of global zirconium carbonate consumption.
Nuclear power generation presents another significant growth vector. Zirconium compounds, including zirconium carbonate as a precursor material, are essential in nuclear fuel rod cladding due to their low neutron absorption properties and excellent corrosion resistance at high temperatures. With over 50 nuclear reactors currently under construction globally and many countries recommitting to nuclear energy as part of their carbon reduction strategies, this sector will drive substantial demand growth through 2030.
Industry Sector | Current Market Share (%) | Projected Growth Rate (%) | Key Applications |
---|---|---|---|
Ceramics & Glass | 38 | 5.8 | Opacifiers, glazes, whitening agents |
Nuclear | 22 | 7.2 | Fuel rod cladding precursors |
Water Treatment | 18 | 8.5 | Fluoride removal, heavy metal adsorption |
Pharmaceuticals | 12 | 6.0 | Antacids, excipients |
Electronics | 6 | 9.3 | Specialty coatings, semiconductors |
Others | 4 | 4.5 | Various applications |
Water treatment applications show the fastest growth trajectory, with zirconium carbonate increasingly used for fluoride and heavy metal removal from drinking water and industrial wastewater. This segment is projected to grow at 8.5% annually, driven by stricter water quality regulations and growing water scarcity concerns globally.
Pharmaceutical formulations represent another expanding application area. Zirconium carbonate serves as an effective antacid ingredient and excipient in various drug formulations. Its low toxicity and high stability make it particularly valuable for controlled-release medications and specialized drug delivery systems.
The electronics and semiconductor industries have begun adopting zirconium carbonate in advanced manufacturing processes. The compound’s unique properties enable the creation of high-performance ceramic substrates and specialty coatings essential for next-generation electronic components. This emerging application segment, while currently small, shows the highest growth potential at 9.3% annually.
How Are Industrial Applications Expanding Market Reach?
Industrial applications of zirconium carbonate continue to diversify, creating new market opportunities beyond traditional uses. The compound’s unique chemical and physical properties enable performance advantages across multiple sectors.
Catalytic converters and industrial catalysts represent a growing application segment. Zirconium compounds derived from zirconium carbonate serve as structural promoters and oxygen storage components in automotive catalytic converters. The numbers tell the story – a single modern catalytic converter can contain up to 15-20 grams of zirconium compounds, with global automotive production exceeding 80 million vehicles annually. This application alone creates substantial demand that will continue growing as emission standards tighten worldwide.
Refractory materials and high-temperature applications leverage zirconium carbonate’s exceptional thermal stability. When processed into zirconia (ZrO₂), these materials withstand temperatures exceeding 2,000°C while maintaining structural integrity. This makes them invaluable in industrial furnaces, glass melting tanks, and other high-temperature processing equipment.
Application | Technical Advantages | Market Growth Drivers | Key Industries |
---|---|---|---|
Catalytic Systems | Oxygen storage capacity, thermal stability | Stricter emission regulations, growing automotive production | Automotive, petrochemical |
Refractory Materials | Temperature resistance (>2,000°C), chemical inertness | Industrial expansion in developing economies, energy efficiency requirements | Steel, glass, cement |
Specialty Glass | Optical clarity, UV resistance, controlled refractive index | Growing demand for high-performance displays, optical devices | Electronics, telecommunications |
Ceramic Pigments | Color stability, non-toxicity, weather resistance | Expanding construction sector, consumer preference for durable products | Building materials, consumer goods |
Advanced Coatings | Corrosion resistance, thermal barrier properties | Infrastructure development, extended service life requirements | Oil & gas, aerospace, marine |
Specialty glass production increasingly relies on zirconium compounds for creating products with specific optical properties. Zirconium-containing glasses offer enhanced durability, controlled refractive indices, and superior UV resistance compared to conventional formulations. These properties are particularly valuable in optical coatings, display technologies, and specialty lenses.
Ceramic pigments and glazes benefit from zirconium carbonate’s ability to create stable, non-toxic colorants. Zirconium-based pigments maintain their appearance even under harsh environmental conditions, making them ideal for exterior architectural applications and products exposed to weathering. The construction boom in developing economies drives significant demand growth in this segment.
Research and development investments continue to yield novel industrial applications. Recent innovations include zirconium-based solid oxide fuel cells, advanced sensors for extreme environments, and specialized catalysts for green chemistry applications. These emerging technologies, while currently representing small market segments, demonstrate significant growth potential as they transition from research to commercial deployment.
Which Regional Markets Show Highest Growth Potential?
Regional market dynamics for zirconium carbonate reveal significant variations in growth trajectories and application priorities. Understanding these geographic differences is essential for strategic market positioning.
The Asia-Pacific region dominates global zirconium carbonate consumption, accounting for approximately 45% of worldwide demand. China leads this regional market, driven by its massive manufacturing base and continued industrial expansion. What makes this particularly significant is China’s dual role as both the largest consumer and producer of zirconium compounds globally. The country’s “Made in China 2025” initiative specifically targets high-performance materials, including zirconium compounds, as strategic priorities for domestic development.
Region | Market Share (%) | CAGR Through 2030 (%) | Primary Growth Drivers | Key Challenges |
---|---|---|---|---|
Asia-Pacific | 45 | 7.8 | Industrial expansion, infrastructure development, electronics manufacturing | Raw material access, environmental regulations |
North America | 22 | 5.2 | Technological innovation, healthcare applications, water treatment | High labor costs, competitive alternatives |
Europe | 20 | 4.5 | Sustainable applications, specialty ceramics, nuclear power | Strict environmental regulations, slow economic growth |
Middle East & Africa | 8 | 6.9 | Industrial diversification, water treatment, construction | Political instability, infrastructure limitations |
Latin America | 5 | 5.8 | Mining operations, manufacturing growth, water purification | Economic volatility, regulatory uncertainty |
North American markets, representing approximately 22% of global consumption, focus primarily on high-value applications in healthcare, advanced electronics, and water treatment. The region’s growth, projected at 5.2% annually through 2030, is driven by technological innovation rather than volume expansion. United States and Canada maintain leadership positions in research and development of novel zirconium applications, particularly in medical devices and advanced materials.
European markets emphasize sustainable applications and specialty products. The region’s strict environmental regulations have accelerated the adoption of zirconium compounds in clean technologies, including water purification systems and emissions control. European manufacturers particularly value zirconium carbonate’s non-toxic profile and compatibility with circular economy initiatives.
Middle East and Africa represent smaller but rapidly growing markets, with 6.9% projected annual growth through 2030. Industrial diversification efforts in Gulf Cooperation Council countries create new demand for specialty chemicals, including zirconium compounds. Water treatment applications are particularly important in this water-scarce region, with zirconium-based adsorbents increasingly deployed in desalination plants and municipal water systems.
Latin American markets center around the region’s significant mining operations and growing manufacturing base. Countries like Brazil and Mexico are developing domestic production capabilities for zirconium compounds to reduce import dependence and capture more value from their mineral resources. Water purification applications show strong growth potential throughout the region.
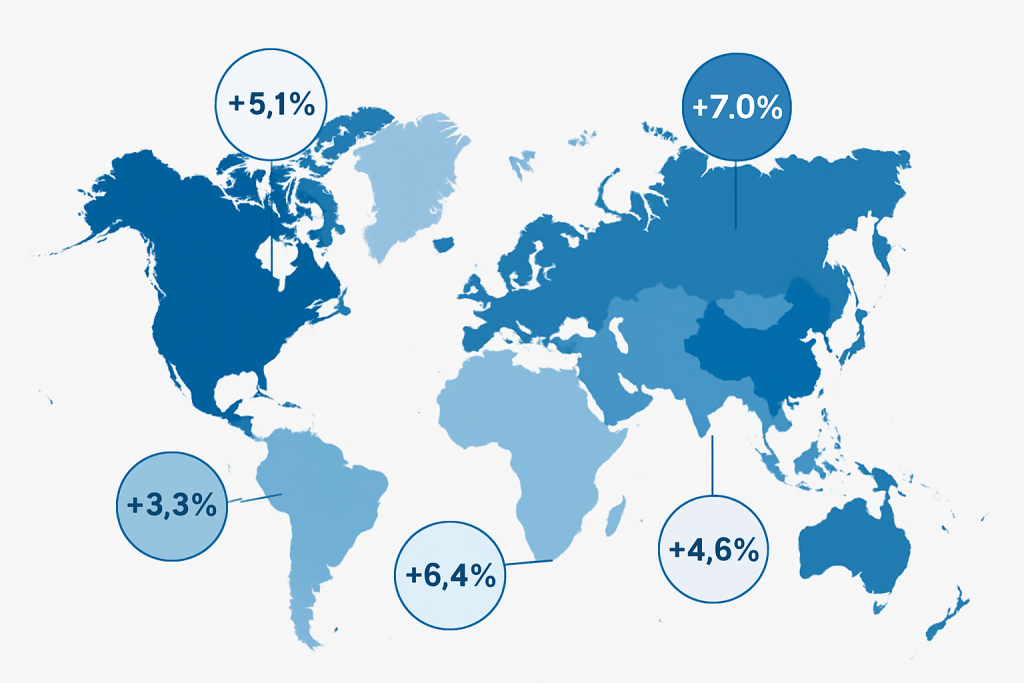
What Supply Chain Factors Influence Market Dynamics?
Supply chain considerations significantly impact zirconium carbonate market dynamics, creating both constraints and opportunities for market participants. Raw material availability represents the foundation of the entire value chain.
Zircon sand (ZrSiO₄) serves as the primary feedstock for zirconium chemicals, including zirconium carbonate. Global zircon resources are geographically concentrated, with Australia, South Africa, and China controlling approximately 70% of production. This concentration matters because supply disruptions in any major producing region can trigger significant price volatility. Recent years have seen zircon prices fluctuate between $900 and $1,800 per metric ton, creating challenges for downstream manufacturers.
Geopolitical tensions increasingly affect global supply chains for critical minerals, including zirconium. Trade disputes, export restrictions, and strategic mineral policies create uncertainty for international buyers. Companies are responding by diversifying supply sources, developing strategic stockpiles, and investing in recycling technologies to recover zirconium from manufacturing waste and end-of-life products.
Supply Chain Factor | Impact on Market | Risk Level | Mitigation Strategies |
---|---|---|---|
Raw Material Availability | Price volatility, supply uncertainty | High | Long-term contracts, diversified sourcing, strategic reserves |
Geopolitical Tensions | Trade disruptions, regulatory changes | Medium-High | Regional production facilities, alternative suppliers, political risk insurance |
Production Capacity | Supply constraints during demand spikes | Medium | Capacity expansion planning, inventory management, flexible manufacturing |
Technological Innovation | Process efficiency, product quality | Medium | R&D investments, technology licensing, industry partnerships |
Vertical Integration | Market concentration, pricing power | Medium-Low | Strategic alliances, long-term agreements, specialty product focus |
Production capacity expansions by key manufacturers will reshape competitive dynamics through 2030. Major producers including Alkane Resources, Tosoh Corporation, and Iluka Resources have announced significant investments in new production facilities and process improvements. These expansions will increase global capacity by an estimated 25-30% over the next five years, potentially alleviating supply constraints in high-growth application segments.
Technological innovations in extraction and processing methods continue to improve efficiency and reduce environmental impacts. Advanced solvent extraction techniques, microwave-assisted processing, and continuous flow reactors represent significant improvements over traditional batch processing methods. These innovations reduce energy consumption by 15-25% while increasing product purity and consistency.
Strategic partnerships and vertical integration strategies are becoming increasingly common throughout the zirconium value chain. Mining companies are expanding into chemical processing, while specialty chemical manufacturers secure dedicated mineral supplies through long-term agreements or direct investments in mining operations. This vertical integration helps companies maintain supply security while capturing additional value across the production chain.
Production Stage | Key Challenges | Recent Innovations | Environmental Considerations |
---|---|---|---|
Mining & Mineral Processing | Resource depletion, water usage | Sensor-based sorting, dry processing | Reduced water consumption, tailings management |
Chemical Conversion | Energy intensity, waste generation | Continuous flow processing, catalytic methods | Lower emissions, reduced chemical usage |
Purification | Product consistency, impurity removal | Membrane technologies, selective precipitation | Closed-loop water systems, reagent recovery |
Final Processing | Quality control, specialized grades | Automated monitoring, particle engineering | Energy efficiency, waste minimization |
Logistics & Distribution | Transportation costs, packaging | Regional processing hubs, bulk handling systems | Optimized shipping, reusable containers |
How Are Sustainability Trends Reshaping the Market?
Sustainability considerations are fundamentally transforming the zirconium carbonate market, creating both challenges and opportunities for industry participants. Environmental regulations increasingly shape production practices and market access.
Cleaner production processes represent a primary focus area for manufacturers. Traditional zirconium carbonate production generates significant waste streams and requires substantial energy inputs. You’ll find that leading producers have invested heavily in process improvements, reducing waste generation by 30-40% and energy consumption by 20-25% compared to conventional methods. These improvements not only reduce environmental impacts but also lower production costs, creating competitive advantages for early adopters.
Circular economy initiatives are gaining traction throughout the value chain. Recycling of zirconium compounds from manufacturing waste and end-of-life products provides an alternative source of raw materials while reducing disposal requirements. Current recovery rates remain relatively low at 15-20%, but technological improvements and regulatory incentives are expected to increase recycling to 30-35% by 2030.
Sustainability Factor | Current Industry Status | 2030 Targets | Business Impact |
---|---|---|---|
Waste Reduction | 30-40% improvement in leading facilities | 50-60% reduction industry-wide | Lower disposal costs, improved community relations |
Energy Efficiency | 20-25% reduction in best practices | 35-40% reduction through new technologies | Reduced operating costs, lower carbon footprint |
Water Conservation | Closed-loop systems in modern plants | Zero liquid discharge in 60% of facilities | Regulatory compliance, operation in water-stressed regions |
Carbon Emissions | Limited measurement and reporting | 30% reduction, comprehensive reporting | Carbon pricing readiness, investor requirements |
Recycled Content | 15-20% in select applications | 30-35% across major product categories | Supply security, marketing advantages |
Eco-friendly applications in water purification highlight zirconium carbonate’s positive environmental contributions. The compound’s exceptional efficiency in removing fluoride, arsenic, and heavy metals from water supplies makes it valuable for addressing critical contamination issues. A single kilogram of zirconium-based adsorbent can treat approximately 1,000-1,500 liters of contaminated water, providing cost-effective solutions for communities facing water quality challenges.
Process optimization continues to reduce the environmental footprint of zirconium carbonate production. Advanced reactor designs, improved separation technologies, and energy recovery systems significantly improve resource efficiency. These technological improvements align with both regulatory requirements and corporate sustainability commitments, accelerating their adoption throughout the industry.
Sustainable sourcing practices are becoming increasingly important for market access. End users, particularly in consumer-facing industries, demand transparency regarding raw material origins and production methods. Leading zirconium carbonate producers have implemented responsible sourcing programs, including third-party audits, traceability systems, and supplier sustainability assessments. These programs help secure preferential supplier status with environmentally conscious customers.
Application | Environmental Benefit | Market Opportunity | Implementation Challenges |
---|---|---|---|
Water Purification | Contaminant removal, reduced chemical usage | Growing municipal and industrial markets | System integration, competition from alternatives |
Catalytic Systems | Reduced emissions, improved energy efficiency | Expanding regulatory requirements | Technical complexity, performance validation |
Sustainable Ceramics | Lower firing temperatures, reduced energy use | Green building certifications, consumer preference | Cost considerations, performance trade-offs |
Recycled Content Products | Resource conservation, waste reduction | Public procurement requirements, corporate sustainability goals | Collection infrastructure, quality consistency |
Low-Impact Mining | Habitat protection, reduced water usage | Social license to operate, regulatory compliance | Capital investment, technology limitations |
What Technological Innovations Are Fueling Growth?
Technological innovations across the zirconium carbonate value chain are creating new market opportunities and addressing traditional limitations. These advances span production methods, product characteristics, and application technologies.
Advanced manufacturing techniques have significantly improved product quality and consistency. Computer-controlled continuous flow reactors replace traditional batch processes, enabling precise control of reaction parameters and resulting in more uniform products. The impact is substantial – these systems reduce quality variations by 40-50% while increasing production throughput by 25-30%. This consistency is particularly valuable for high-specification applications in electronics and healthcare.
Nanotechnology applications enhance zirconium carbonate performance characteristics. Nano-structured zirconium compounds demonstrate superior catalytic activity, adsorption capacity, and optical properties compared to conventional materials. These enhanced properties enable new applications in areas including photocatalysis, selective chemical sensing, and advanced optical coatings. The market for nano-zirconium compounds, while currently small, is projected to grow at over 12% annually through 2030.
Technology | Development Stage | Market Impact | Key Applications |
---|---|---|---|
Continuous Flow Processing | Commercial | Higher quality, lower costs | All major product categories |
Nano-structured Materials | Early Commercial | Enhanced performance, new applications | Electronics, catalysts, sensors |
High-purity Grades | Commercial | Expanded application range | Semiconductors, medical devices |
Process Automation | Commercial | Efficiency improvements, labor savings | Large-scale production |
Novel Synthesis Routes | Research/Pilot | Reduced environmental impact, cost reduction | Next-generation products |
High-purity grades development addresses the needs of specialized applications. Advanced purification techniques now enable the production of zirconium carbonate with impurity levels below 10 parts per million, meeting the stringent requirements of semiconductor manufacturing and medical applications. These ultra-pure grades command premium prices, often 3-5 times higher than standard industrial grades, creating attractive high-margin market segments for producers with advanced technical capabilities.
Process automation and efficiency improvements reduce production costs while enhancing safety and reliability. Modern zirconium carbonate production facilities incorporate extensive automation, real-time monitoring systems, and predictive maintenance capabilities. These technologies reduce labor requirements by 30-40% compared to conventional plants while minimizing unplanned downtime and process upsets.
Research and development breakthroughs continue to expand zirconium carbonate applications. Recent innovations include zirconium-based solid electrolytes for next-generation batteries, bioactive zirconium compounds for medical implants, and specialized catalysts for carbon capture technologies. While many of these applications remain in development stages, they represent significant future growth opportunities as they transition to commercial deployment.
R&D Focus Area | Potential Market Impact | Commercialization Timeline | Technical Challenges |
---|---|---|---|
Energy Storage | High – battery market exceeds $100B | 3-5 years | Performance consistency, cost reduction |
Biomedical Applications | Medium – specialized but high-value | 5-7 years | Regulatory approval, biocompatibility |
Carbon Capture | High – growing with climate initiatives | 3-6 years | Scalability, regeneration efficiency |
Quantum Materials | Medium – specialized electronics | 7-10 years | Manufacturing complexity, quality control |
Smart Coatings | Medium – premium performance segment | 2-4 years | Durability, application methods |
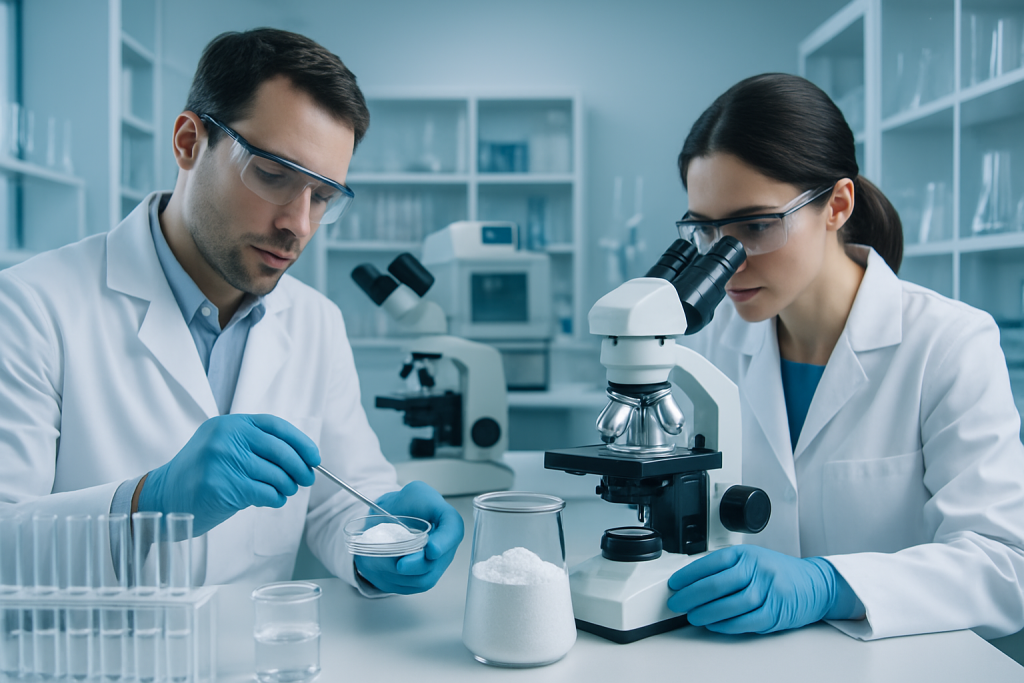
How Will Competitive Landscape Evolve Through 2030?
The competitive landscape for zirconium carbonate will undergo significant transformation through 2030, driven by market consolidation, new entrants, and changing customer requirements. Strategic positioning will determine which companies capture the highest-value opportunities.
Market concentration analysis reveals moderate but increasing consolidation. The top five producers currently control approximately 65% of global capacity, with this share projected to reach 70-75% by 2030. This trend creates both risks and opportunities for market participants. Larger producers benefit from economies of scale, integrated supply chains, and broader product portfolios. However, specialized producers can thrive by focusing on high-value niches and providing customized solutions for specific applications.
Merger and acquisition activities continue to reshape industry structure. Recent years have seen several significant transactions, including Tronox’s acquisition of Cristal’s titanium dioxide business (which included zirconium operations) and Alkane Resources’ expansion of its rare earths and zirconium processing capabilities. These consolidations create larger, more vertically integrated companies with enhanced market power and broader geographic reach.
Company Type | Market Position | Competitive Advantages | Challenges |
---|---|---|---|
Global Integrated Producers | Market leaders, 15-20% share each | Scale economies, vertical integration, broad portfolios | Innovation agility, cost structures |
Regional Specialists | 5-10% share in specific regions | Local market knowledge, customer relationships | Scale limitations, technology access |
Application Specialists | 3-8% share in specific segments | Technical expertise, customized solutions | Portfolio breadth, raw material access |
New Entrants | <2% share, growing | Innovative technologies, agility | Scale, customer relationships, market access |
Emerging Market Producers | 5-15% combined share, growing | Cost advantages, local market access | Quality consistency, international standards |
Emerging players from developing economies increasingly challenge established manufacturers. Chinese and Indian chemical companies have made substantial investments in zirconium production capabilities, leveraging cost advantages and growing domestic markets. These companies initially focused on standard grades for mass-market applications but are progressively moving into higher-value segments as their technical capabilities advance.
Differentiation strategies through product innovation and specialization represent key competitive approaches. Leading companies invest 4-6% of revenue in research and development, focusing on proprietary technologies and specialized formulations. This innovation focus helps maintain margins and market position despite increasing competition from lower-cost producers. Successful differentiation strategies typically target specific high-value applications rather than competing directly in commodity segments.
Alternative materials and potential substitutes pose competitive threats in certain applications. Advanced aluminum compounds can replace zirconium in some catalytic applications, while synthetic materials offer alternatives for certain ceramic applications. However, zirconium’s unique combination of properties – including exceptional heat resistance, chemical stability, and biocompatibility – makes direct substitution difficult in many high-value applications.
Strategic Approach | Companies Pursuing | Success Factors | Market Examples |
---|---|---|---|
Vertical Integration | Alkane Resources, Iluka, Tronox | Raw material access, value chain control | Mine-to-market zirconium products |
Technical Leadership | Tosoh, AREVA, Luxfer | R&D investment, patent portfolio | High-purity grades, specialized formulations |
Application Specialization | Guangdong Orient Zirconic, Chemours | Deep application knowledge, customer collaboration | Industry-specific product lines |
Geographic Focus | Regional producers | Local relationships, market understanding | Customized solutions for regional needs |
Cost Leadership | Emerging market producers | Process efficiency, scale, input costs | Standard grades, high-volume applications |
Conclusion
Zirconium carbonate markets will experience robust growth through 2030, driven by expanding applications across multiple industries and supported by technological innovations throughout the value chain. The projected 6.5% CAGR represents significant opportunities for both producers and end-users who understand the market dynamics. Companies can gain competitive advantage by securing stable raw material supplies, investing in sustainable production technologies, and developing specialized formulations for high-value applications. Partnering with Global Industry’s material science experts provides access to industry-leading insights and customized solutions that address your specific zirconium carbonate requirements. Contact our technical team today to discuss how our advanced zirconium products can enhance your manufacturing processes and end-product performance.
FAQ
Q1: What is zirconium carbonate and what are its primary applications?
Zirconium carbonate is an inorganic compound with the formula ZrCO₃ or its hydrated forms, serving as a key intermediate in zirconium chemistry. Its primary applications include use in ceramics and glass manufacturing as an opacifier and whitening agent, in water treatment for removing contaminants like fluoride, in catalysts for various chemical processes, and in pharmaceutical formulations as an antacid ingredient. The compound’s unique properties, including chemical stability and low toxicity, make it valuable across diverse industries.
Q2: Why is the zirconium carbonate market projected to grow at 6.5% CAGR through 2030?
The projected 6.5% CAGR through 2030 stems from multiple converging factors: expanding industrial applications in ceramics, glass, and water treatment; growing demand from emerging economies, particularly in Asia-Pacific; technological innovations creating new high-value applications; increasing use in pharmaceutical and cosmetic products; and rising investments in nuclear power generation where zirconium compounds play a critical role. Additionally, environmental regulations favoring effective water treatment solutions are creating substantial new market opportunities.
Q3: Which companies are the key players in the global zirconium carbonate market?
Key players in the global zirconium carbonate market include established chemical manufacturers like Alkane Resources Ltd., Tosoh Corporation, AREVA, Iluka Resources Limited, Tronox Limited, Exxaro Resources Limited, and Luxfer Group. These companies maintain significant market share through vertical integration, technological expertise, and global distribution networks. Additionally, specialized producers like Guangdong Orient Zirconic Ind Sci & Tech Co. Ltd. and Chemours Company are gaining prominence through product innovation and focus on high-purity grades for specialized applications.
Q4: How do raw material supply challenges affect zirconium carbonate pricing?
Raw material supply challenges significantly impact zirconium carbonate pricing through several mechanisms. Zirconium minerals like zircon sand are geographically concentrated, making the supply chain vulnerable to disruptions in key mining regions. Price volatility in zircon feedstock directly affects production costs, while energy price fluctuations impact extraction and processing expenses. Additionally, geopolitical tensions affecting major producing countries can create supply uncertainties, and increasing environmental regulations on mining operations add compliance costs. These factors collectively contribute to price fluctuations and can temporarily constrain market growth despite strong demand.
Q5: What environmental benefits does zirconium carbonate offer in industrial applications?
Zirconium carbonate offers several environmental benefits in industrial applications. In water treatment, it effectively removes fluoride, arsenic, and heavy metals from drinking water and industrial wastewater without introducing harmful byproducts. As a catalyst component, it enhances reaction efficiency, reducing energy consumption and waste generation. In ceramic production, it enables lower firing temperatures, decreasing energy usage and associated carbon emissions. Its durability in applications extends product lifecycles, reducing replacement frequency and waste. Additionally, when used in nuclear applications, zirconium compounds contribute to cleaner energy generation with lower greenhouse gas emissions compared to fossil fuels.