In today’s demanding industrial environments, component wear remains one of the most persistent challenges facing engineers and procurement specialists. The search for materials that can withstand extreme abrasion, friction, and surface degradation while maintaining dimensional stability has led many industries to zirconia ceramics. This article examines why zirconia offers exceptional wear resistance compared to other engineering materials, how its unique properties translate to superior performance in critical applications, and which industries benefit most from these capabilities. Understanding zirconia’s wear resistance advantages enables better material selection decisions that can dramatically extend component lifespans, reduce maintenance costs, and improve operational reliability.
What Makes Wear Resistance Critical In Modern Engineering?
Wear-related failures represent a massive economic burden across virtually all industrial sectors. When critical components degrade through surface wear, the consequences extend far beyond simple replacement costs.
Here’s the stark reality: a single unexpected wear-related failure in a critical industrial component can cost between $100,000 and $1 million in direct replacement expenses, while associated production losses often exceed $50,000 per hour in high-volume manufacturing environments.
Four primary wear mechanisms dominate industrial applications:
- Abrasive wear: Hard particles cut or plow through softer surfaces
- Adhesive wear: Surface asperities weld together and tear during relative motion
- Fatigue wear: Repeated stress cycles cause surface cracking and material removal
- Corrosive wear: Combined chemical attack and mechanical wear accelerate material loss
Wear Mechanism | Primary Damage Mode | Common Industrial Environments | Traditional Material Limitations |
---|---|---|---|
Abrasive | Cutting, plowing, gouging | Mining, cement, ceramics processing | Rapid material removal, gouging |
Adhesive | Galling, seizing, scuffing | Metal forming, bearings, gears | Surface welding, catastrophic seizure |
Fatigue | Cracking, pitting, spalling | Rolling contacts, cyclical loading | Progressive surface degradation |
Corrosive | Chemical-mechanical synergy | Chemical processing, marine | Accelerated material loss |
Traditional materials face significant limitations in extreme wear environments. Metals may offer good toughness but limited hardness, while conventional ceramics provide hardness but poor impact resistance. These limitations have driven the search for advanced materials like zirconia that offer superior wear resistance without compromising other critical properties.
How Does Zirconia’s Microstructure Enable Superior Wear Resistance?
Zirconia’s exceptional wear resistance begins at the atomic level with its unique crystalline structure. Unlike most ceramics, zirconia possesses a remarkable combination of hardness and toughness that stems directly from its microstructural characteristics.
What makes this truly special is zirconia’s phase transformation toughening mechanism. When stress is applied to the material—such as during abrasive contact—metastable tetragonal zirconia particles can transform to the monoclinic phase. This transformation involves a volume expansion of approximately 3-5%, which creates compressive stresses that effectively inhibit crack propagation.
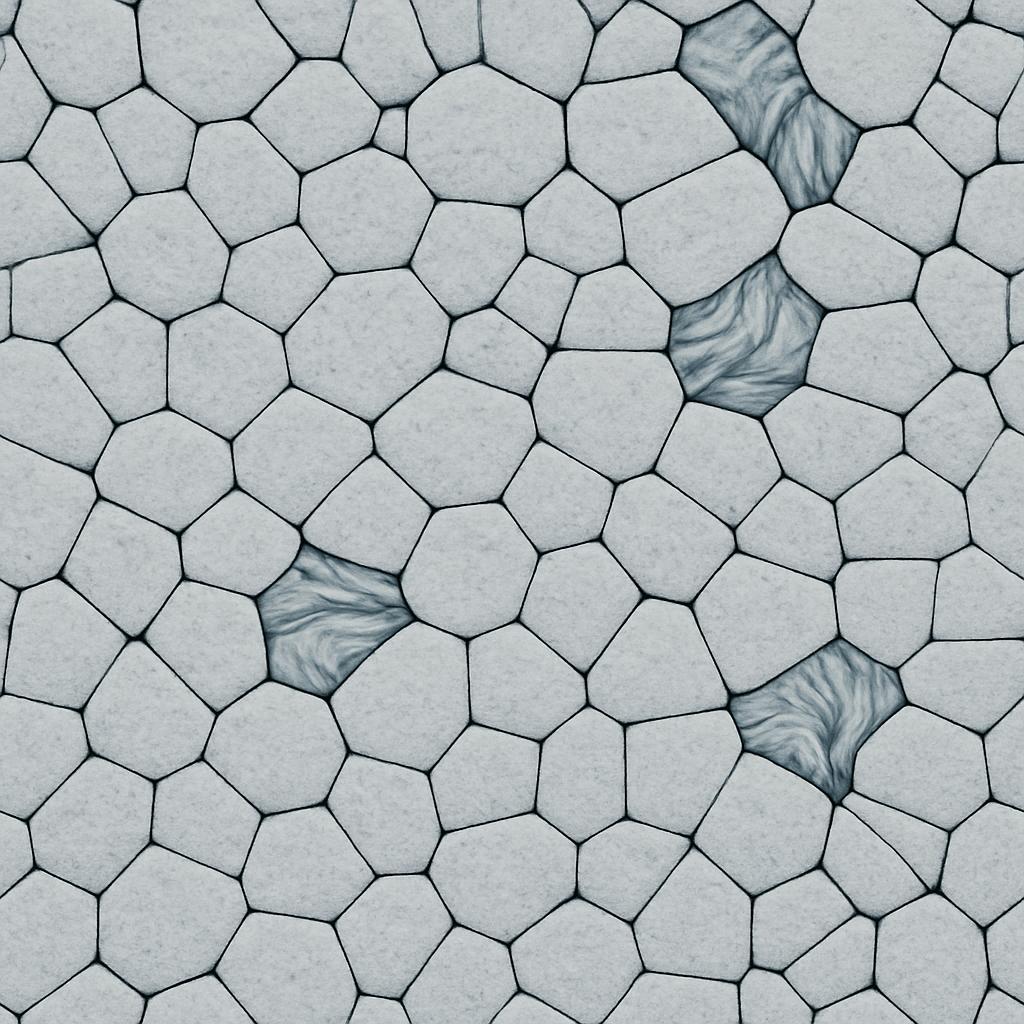
Stabilizing oxides fundamentally alter zirconia’s wear behavior. The most common stabilizers include:
- Yttria (Y₂O₃): Creates a partially stabilized structure with excellent mechanical properties
- Magnesia (MgO): Provides good thermal stability and moderate wear resistance
- Ceria (CeO₂): Offers enhanced resistance to hydrothermal degradation and aging
Stabilizer | Optimal Content | Effect on Wear Resistance | Best Applications |
---|---|---|---|
Yttria (Y₂O₃) | 3 mol% | Highest overall wear resistance | Precision components, bearings |
Magnesia (MgO) | 8-10 mol% | Good thermal stability, moderate wear | High-temperature applications |
Ceria (CeO₂) | 12 mol% | Excellent aging resistance, good wear | Medical devices, humid environments |
Calcia (CaO) | 7-8 mol% | Lower cost, moderate wear resistance | General industrial components |
Surface characteristics significantly impact zirconia’s tribological performance. Highly polished zirconia surfaces (Ra < 0.02 μm) typically exhibit lower friction coefficients (0.2-0.4) than rougher finishes.
What Mechanical Properties Give Zirconia Its Wear Advantage?
Zirconia’s superior wear resistance stems from an exceptional combination of mechanical properties that few other engineering materials can match.
But here’s what you need to know: hardness alone doesn’t tell the complete story of wear resistance. Zirconia’s true advantage comes from its balanced property profile. With Vickers hardness values typically ranging from 12-14 GPa, zirconia is significantly harder than most metals (0.2-4 GPa) while remaining machinable with specialized tools.
Fracture toughness represents zirconia’s most distinctive advantage over other ceramics. While conventional ceramics like alumina typically exhibit fracture toughness values of 3-4 MPa·m½, zirconia can achieve 6-10 MPa·m½ thanks to its transformation toughening mechanism. This exceptional toughness prevents the brittle fracture and microcracking that often limit the wear life of other ceramic materials.
Material | Hardness (GPa) | Fracture Toughness (MPa·m½) | Elastic Modulus (GPa) | Relative Wear Resistance* |
---|---|---|---|---|
Yttria-Stabilized Zirconia | 12-14 | 6-10 | 200-210 | 100 |
Alumina | 15-19 | 3-4 | 380-400 | 40-60 |
Silicon Carbide | 24-28 | 2.5-4 | 380-430 | 70-90 |
Stainless Steel | 2-4 | 50-200 | 190-210 | 5-15 |
Tungsten Carbide | 18-22 | 8-20 | 550-650 | 80-120 |
*Normalized to zirconia = 100 under abrasive wear conditions |
The elastic modulus of zirconia (200-210 GPa) provides an optimal balance for wear applications. This relatively low modulus (compared to other ceramics) allows for better stress distribution at contact points, reducing the peak stresses that can initiate wear damage.
Flexural strength is particularly important for components subjected to bending loads during service. Zirconia’s exceptional flexural strength (800-1500 MPa) far exceeds that of conventional ceramics (300-500 MPa) and approaches the values of high-strength metals.
How Does Zirconia Perform Under Different Wear Conditions?
Zirconia’s wear performance varies significantly across different operating environments, with certain conditions showcasing its advantages most dramatically.
You might be surprised to learn that in dry sliding wear tests against hardened steel counterfaces, zirconia typically shows wear rates 5-10 times lower than alumina and 20-50 times lower than engineering metals. This exceptional performance stems from zirconia’s unique combination of hardness and transformation toughening.
In wet and lubricated conditions, zirconia maintains its advantages while exhibiting some unique behaviors. The material’s relatively low surface energy creates a hydrophilic surface that retains fluid films effectively. In water-lubricated applications, wear rates typically decrease by 30-60% compared to dry conditions. Oil lubrication provides even greater benefits, with wear rates often reduced by 80-95%.
Wear Condition | Zirconia Wear Rate | Comparative Performance | Key Performance Factors |
---|---|---|---|
Dry sliding | 10⁻⁶-10⁻⁷ mm³/Nm | 5-10× better than alumina | Transformation toughening, hardness |
Water lubricated | 10⁻⁷-10⁻⁸ mm³/Nm | 3-8× better than silicon nitride | Surface energy, crack resistance |
Oil lubricated | 10⁻⁸-10⁻⁹ mm³/Nm | 2-5× better than tungsten carbide | Film formation, surface finish |
Particle erosion | 10⁻⁵-10⁻⁶ mm³/g | 3-7× better than stellite alloys | Hardness, impact resistance |
Slurry erosion | 10⁻⁵-10⁻⁶ mm³/g | 10-30× better than hardened steels | Chemical stability, hardness |
High-temperature environments present both challenges and opportunities for zirconia wear applications. Up to approximately 500°C, wear resistance typically improves due to oxide film formation. Between 500-800°C, performance remains stable for properly stabilized grades. Above 800°C, some zirconia formulations may experience accelerated wear due to phase stability issues.
Which Industries Benefit Most From Zirconia’s Wear Resistance?
Zirconia’s exceptional wear resistance creates substantial value across numerous industries, with certain sectors gaining particularly significant advantages from this unique material property.
The results speak for themselves: in the aerospace industry, zirconia components have demonstrated service life improvements of 300-500% compared to traditional materials in applications like bearing elements, valve components, and turbine parts. The material’s combination of wear resistance, temperature capability, and light weight makes it particularly valuable in this weight-sensitive sector.
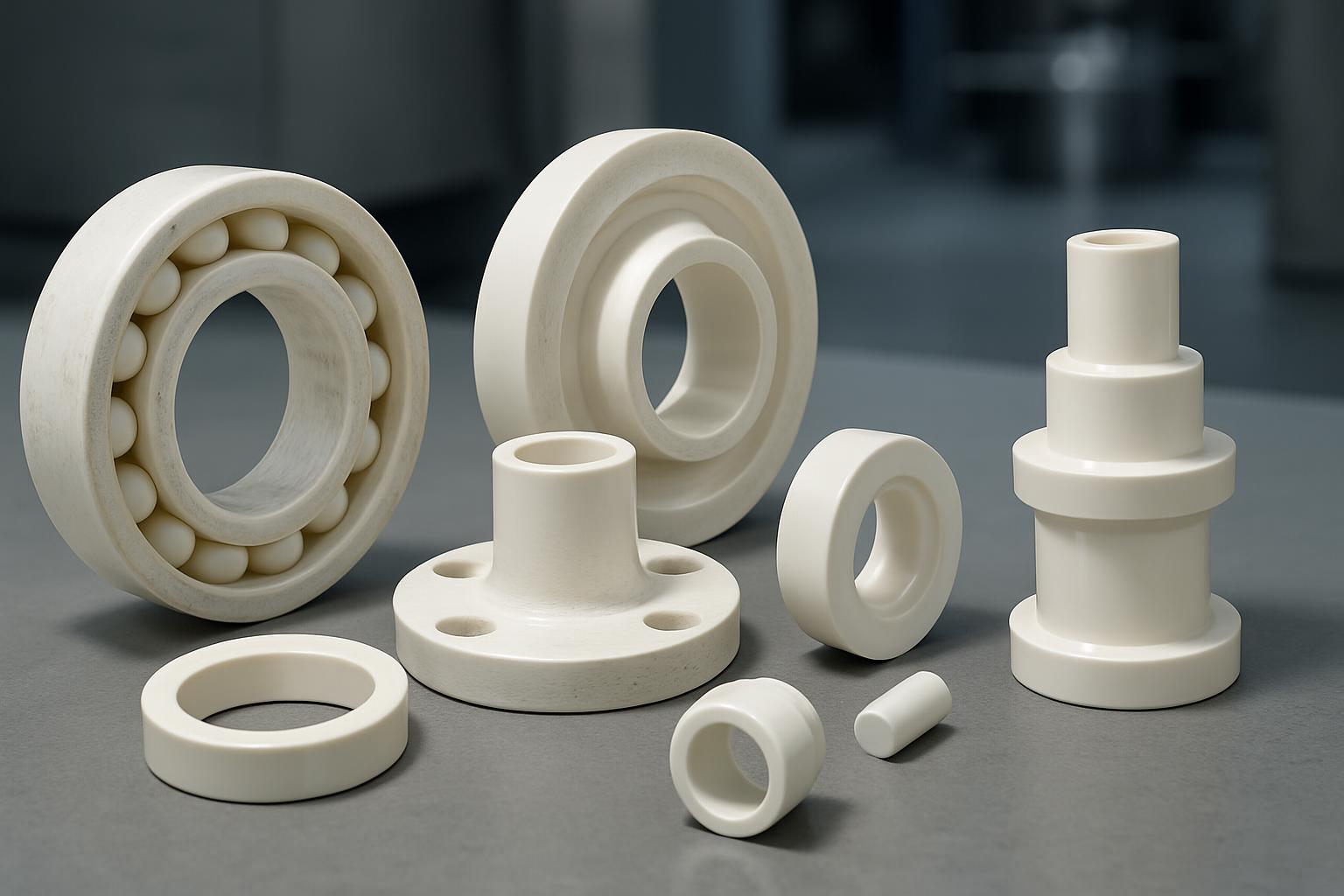
The oil and gas industry relies on zirconia components in some of the most severe wear environments imaginable. Downhole tools, valve trim, and pump components face combinations of abrasive slurries, high pressures, and corrosive chemicals. Zirconia parts in these applications routinely deliver 3-5 times longer service life than tungsten carbide alternatives and up to 10 times longer than hardened steel.
Industry | Key Applications | Primary Wear Challenge | Value Proposition |
---|---|---|---|
Aerospace | Bearings, bushings, valve seats | High loads, temperature extremes | 300-500% longer service life |
Medical | Joint replacements, dental implants | Biocompatibility, lifetime durability | 100-1000× lower volumetric wear |
Oil & Gas | Valve trim, pump components, seals | Abrasive slurries, high pressure | 3-10× longer component life |
Textile | Thread guides, yarn tensioners | Continuous abrasion, minimal lubrication | 5-8× longer service intervals |
Precision Manufacturing | Gauges, fixtures, positioning elements | Dimensional stability, cleanliness | Submicron precision maintenance |
Medical device manufacturers have embraced zirconia for wear-critical applications, particularly in orthopedic implants. Hip and knee joint components made from zirconia-based ceramics show dramatically reduced wear rates compared to metal alternatives, with volumetric wear rates often 100-1000 times lower.
How Do Different Zirconia Grades Compare In Wear Applications?
Not all zirconia ceramics offer identical wear performance. Various grades and formulations provide optimized properties for specific operating conditions, making proper selection critical for maximizing component lifespan.
This is important to understand: Partially Stabilized Zirconia (PSZ) containing 3-4 mol% yttria typically offers the best overall wear resistance for most industrial applications. This composition provides an optimal balance of hardness (12-13 GPa) and fracture toughness (6-10 MPa·m½), allowing it to resist both abrasive wear and impact damage.
Zirconia Grade | Composition | Hardness (GPa) | Toughness (MPa·m½) | Best Wear Applications | Limitations |
---|---|---|---|---|---|
Partially Stabilized (PSZ) | 3-4 mol% Y₂O₃ | 12-13 | 6-10 | General industrial, bearings | Moderate thermal stability |
Fully Stabilized (FSZ) | 8 mol% Y₂O₃ | 10-11 | 2-3 | High temperature, corrosive | Lower wear resistance |
Tetragonal (TZP) | 2-3 mol% Y₂O₃ | 13-14 | 5-7 | High-stress mechanical | Aging in humid environments |
Magnesia Stabilized | 8-10 mol% MgO | 11-12 | 4-6 | Thermal cycling | Lower chemical resistance |
Ceria Stabilized | 12 mol% CeO₂ | 10-11 | 8-12 | Medical, humid environments | Higher cost |
Zirconia-based composites represent an important category for specialized wear applications. Zirconia-toughened alumina (ZTA) combines alumina’s excellent hardness with improved toughness from dispersed zirconia particles. Alumina-toughened zirconia (ATZ) maintains most of zirconia’s toughness while gaining hardness and chemical stability from the alumina phase.
What Testing Methods Accurately Predict Zirconia’s Wear Performance?
Selecting the right zirconia grade for a specific wear application requires reliable testing methods that accurately predict real-world performance.
The key insight here is: no single test method can fully characterize wear behavior. A comprehensive testing approach combining multiple methods provides the most reliable prediction of field performance. The selection of test methods should reflect the dominant wear mechanisms expected in the actual application.
Standard pin-on-disk and ball-on-disk tests (ASTM G99, DIN 50324) remain the foundation of comparative wear testing. These methods provide controlled evaluation of sliding wear behavior under various loads, speeds, and lubrication conditions.
Component-level testing represents the most reliable but also most expensive approach to performance prediction. By testing actual components under simulated service conditions, these methods capture the complex interactions between material properties, component geometry, and operating parameters.
How Can Engineers Optimize Zirconia Components For Wear Resistance?
Maximizing the wear performance of zirconia components requires attention to design details, manufacturing processes, and system-level considerations that go beyond simple material selection.
What really matters is this: design considerations fundamentally impact wear performance. Contact stress distribution represents perhaps the most critical factor—even the best zirconia grade will fail prematurely if subjected to stress concentrations that exceed material limits. Finite element analysis should be employed to identify and eliminate stress hot spots through geometry optimization.
Surface finish quality dramatically impacts wear behavior. For optimal results, zirconia components should be polished to a surface roughness (Ra) below 0.02 μm. This ultra-smooth finish reduces asperity contact, lowers friction coefficients, and improves lubricant film formation. While achieving this finish requires specialized polishing techniques, the investment typically delivers 20-40% improvements in wear life.
Lubrication strategy optimization can extend zirconia component life by 5-10 times compared to unlubricated conditions. Beyond basic lubricant selection, engineers should consider delivery methods, filtration requirements, and condition monitoring approaches.
What Future Innovations Will Enhance Zirconia’s Wear Performance?
The field of zirconia wear materials continues to evolve rapidly, with several promising research directions poised to deliver significant performance improvements in coming years.
The future looks promising: novel stabilizer combinations represent one of the most active research areas. By moving beyond traditional single-oxide stabilizers to carefully engineered multi-oxide systems, researchers have demonstrated zirconia materials with 30-50% higher fracture toughness while maintaining excellent hardness.
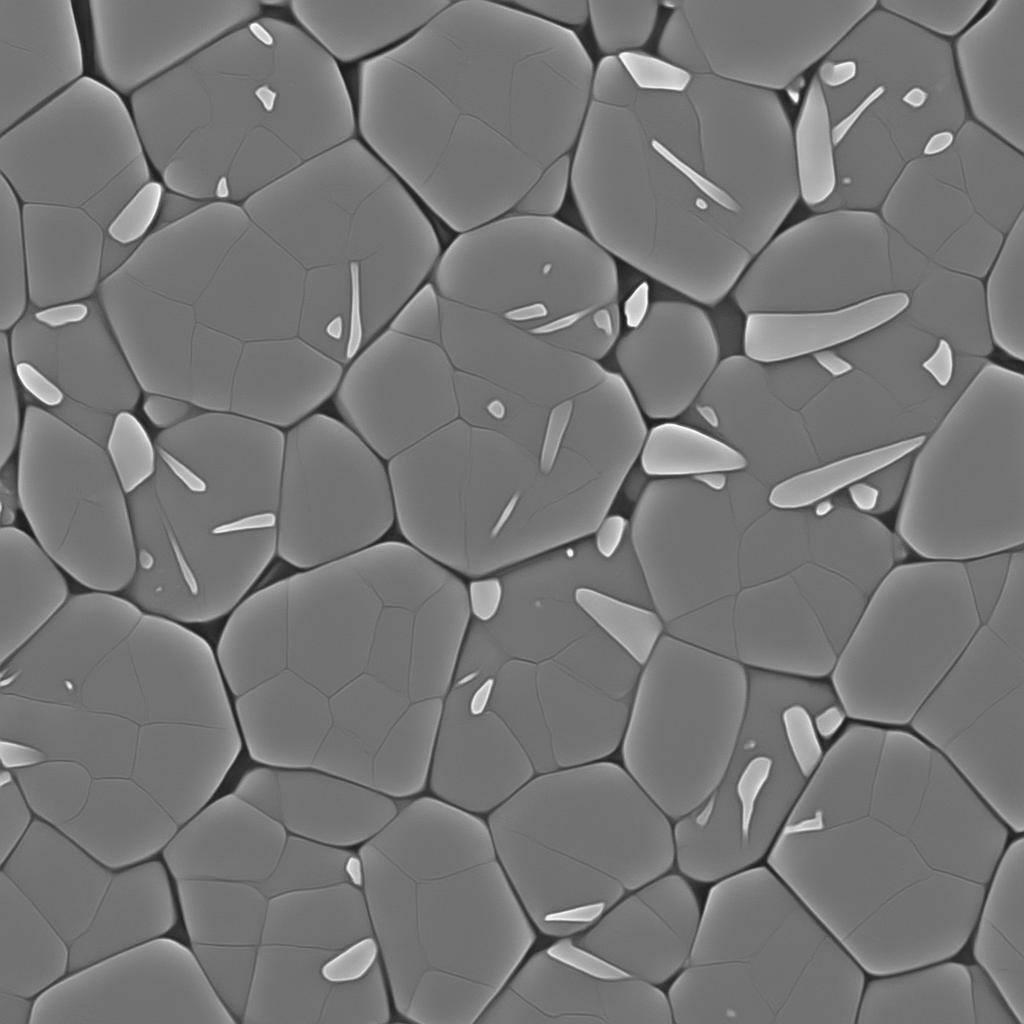
Nanocomposite zirconia materials incorporate secondary phases at the nanoscale to enhance specific properties. Zirconia-carbon nanotube composites have shown friction reductions of 40-60% while maintaining the base material’s excellent wear resistance. Zirconia-graphene nanocomposites demonstrate similar friction improvements plus enhanced thermal conductivity that helps dissipate frictional heating.
Innovation Area | Performance Improvement | Technology Readiness | Key Applications |
---|---|---|---|
Multi-oxide stabilizers | 30-50% higher toughness | Commercial availability: 1-3 years | Extreme mechanical environments |
Nanocomposites | 40-60% lower friction | Commercial availability: 2-5 years | High-speed bearings, dry running |
Surface engineering | Application-specific enhancements | Commercial availability: 1-3 years | Specialized tribological systems |
Computational design | 20-30% optimized properties | Ongoing implementation | Complex mechanical systems |
Bioinspired structures | Potential 2-5× lifetime improvements | Research stage | Next-generation wear solutions |
Computational materials science is accelerating the development of optimized zirconia formulations. Machine learning algorithms can now predict wear behavior based on composition and processing parameters, allowing researchers to explore vast design spaces efficiently.
Conclusion
Zirconia’s exceptional wear resistance stems from its unique combination of hardness, fracture toughness, and phase transformation capabilities that few other engineering materials can match. From its distinctive microstructure to its balanced mechanical properties, zirconia offers a compelling solution for components facing severe wear challenges across diverse industries.
The data clearly demonstrates that properly selected and implemented zirconia components typically deliver 3-10 times longer service life than conventional materials in demanding wear applications, translating to lifecycle cost reductions of 40-70% despite higher initial investment.
For your next wear-critical application, partner with Global Industry to identify the optimal zirconia grade and component design. Our engineering team specializes in tribological system optimization, ensuring you receive the maximum performance benefit from zirconia’s unique properties.
Contact our technical support team today to discuss your specific wear challenges and discover how our advanced zirconia solutions can transform your most demanding applications.
FAQ Section
Q1: How does zirconia’s wear resistance compare to alumina ceramics?
Zirconia and alumina show significant differences in wear performance. While alumina offers slightly higher hardness (18-23 GPa vs. zirconia’s 12-15 GPa), zirconia’s fracture toughness is 2-3 times higher (6-10 MPa·m½ vs. alumina’s 3-4 MPa·m½). This toughness advantage makes zirconia superior in applications with impact loads and stress concentrations. In dry sliding wear tests, zirconia typically shows 30-50% lower volume loss rates than alumina, particularly under conditions involving vibration and impact.
Q2: Can zirconia withstand abrasive slurry environments?
Zirconia performs exceptionally well in abrasive slurry environments, though performance depends on specific conditions. In water or oil-based slurries containing hard particles (like silica or alumina), zirconia’s wear rate is typically 1-2 orders of magnitude lower than metals and 2-3 orders lower than engineering plastics. In chemically variable slurries, zirconia’s combined chemical stability and wear resistance provide particular advantages.
Q3: Does stabilizer content affect zirconia’s wear resistance?
Stabilizer content significantly impacts zirconia’s wear performance. TZP zirconia with low stabilizer content (around 3mol% Y₂O₃) typically offers optimal wear resistance by balancing high fracture toughness (6-10 MPa·m½) with moderate hardness (12-13 GPa). As stabilizer content increases to 8mol% in FSZ, both hardness and toughness decrease slightly, reducing wear performance by 15-30% in certain environments.
Q4: How does temperature affect zirconia’s wear performance?
Temperature has complex effects on zirconia’s wear behavior. From room temperature to approximately 400°C, zirconia maintains stable wear resistance with rate variations under 10-15%. Between 400-800°C, many zirconia materials experience wear behavior transitions related to oxide film formation, lubricant film stability changes, and material softening. Above 800°C, particularly for Y-TZP zirconia, accelerated wear may occur as reverse phase transformation from tetragonal to monoclinic causes volume expansion and microcracking.
Q5: What surface treatments can enhance zirconia’s wear resistance?
Multiple surface treatment technologies can effectively enhance zirconia’s wear performance. Laser surface modification can create nanostructured surface layers with 15-25% higher hardness while maintaining bulk toughness. Ion implantation (particularly nitrogen) can form hard nitride surface layers that reduce friction coefficients by 30-40%. Plasma spray techniques can apply composite coatings like ZrO₂-Al₂O₃ or ZrO₂-TiO₂ that provide gradient property transitions.