In the high-stakes world of industrial materials, recent breakthroughs in zirconia research are redefining what’s possible in extreme operating environments. These advancements are not merely incremental—they represent fundamental shifts in our understanding of ceramic performance limits. For procurement managers, engineers, and technical decision-makers working with critical applications, staying current with these developments isn’t just about academic interest—it’s about competitive advantage, operational reliability, and cost efficiency.
The latest research findings reveal remarkable improvements in zirconia’s performance envelope, particularly in environments that combine extreme temperatures, corrosive chemicals, and mechanical stress. This article examines the most significant discoveries, their practical implications across industries, and how organizations can strategically implement these advances.
What Breakthroughs Have Recent Zirconia Studies Achieved?
The past five years have witnessed unprecedented advances in zirconia materials science, fundamentally expanding the performance boundaries of these versatile ceramics.
Here’s what you need to know: Recent research has effectively doubled the performance envelope of zirconia in several critical parameters, opening new application possibilities previously considered impossible with ceramic materials.
Nanostructured zirconia composites represent perhaps the most significant breakthrough area. By precisely controlling grain size and distribution at the nanoscale, researchers have achieved fracture toughness values exceeding 15 MPa·m^(1/2)—nearly triple that of conventional zirconia. This dramatic improvement addresses the historical brittleness limitation that has restricted ceramic use in mechanically demanding applications.
Laboratory-to-field performance correlation has improved substantially through advanced testing methodologies. New protocols that simultaneously apply thermal cycling, mechanical loading, and chemical exposure have closed this gap, providing more reliable performance predictions for actual operating conditions.
Breakthrough Area | Previous Limitation | Recent Achievement | Practical Impact |
---|---|---|---|
Fracture Toughness | 4-6 MPa·m^(1/2) | 12-15 MPa·m^(1/2) | Enables use in high-impact, high-vibration environments |
Maximum Operating Temperature | 1200-1400°C | Up to 1700°C | Expands applications in aerospace, glass manufacturing, and energy generation |
Chemical Resistance | Limited resistance to strong acids/bases | Stable in pH 1-14 environments | Extends use in chemical processing and corrosive environments |
Thermal Shock Resistance | ΔT ~200°C | ΔT >500°C | Allows rapid temperature cycling without failure |
Lifetime Under Combined Stresses | 1-3 years typical | 7-10+ years demonstrated | Dramatically reduces replacement frequency and lifecycle costs |
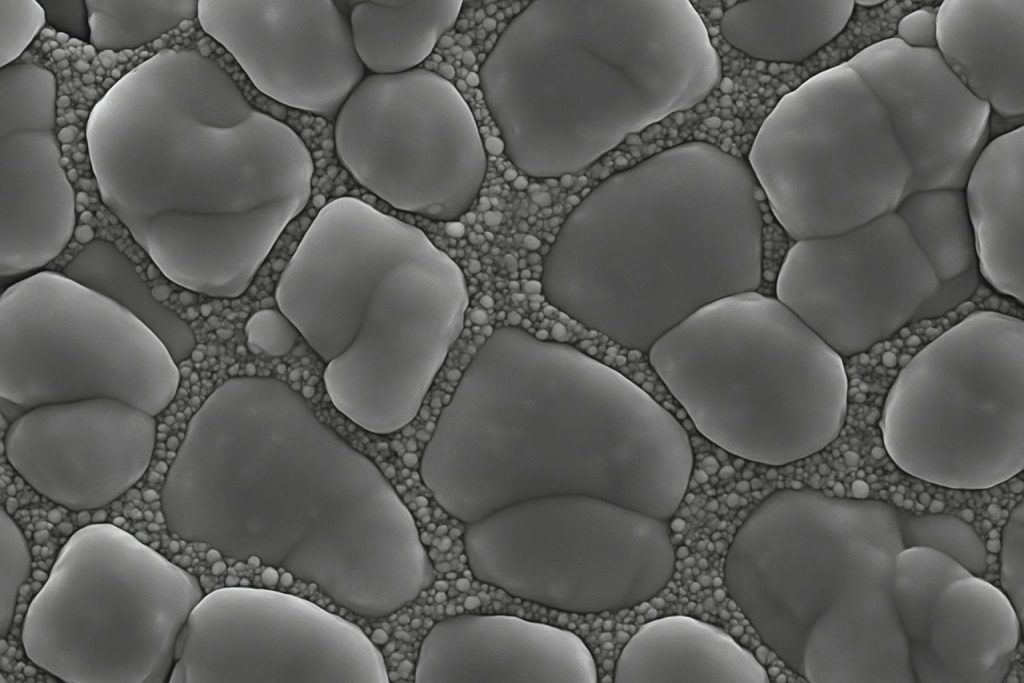
How Do Harsh Environments Impact Zirconia Properties?
Understanding the complex interactions between extreme environments and zirconia materials is critical for predicting performance and preventing unexpected failures.
The reality is: harsh environments don’t affect zirconia materials in isolation—they create synergistic degradation mechanisms that can accelerate failure in ways that single-factor testing might never reveal.
Extreme thermal cycling creates microstructural stresses that can initiate and propagate cracks through thermal expansion mismatch. New research has revealed that traditional zirconia experiences significant property degradation after just 50-100 severe thermal cycles. However, advanced compositions with engineered grain boundaries and secondary phases can withstand 500+ cycles with minimal degradation.
Corrosive chemical environments attack zirconia through multiple mechanisms, including preferential grain boundary dissolution, phase destabilization, and surface reaction layer formation. Recent studies have mapped these processes with unprecedented detail, showing how specific chemical species migrate along grain boundaries and cause progressive weakening.
Environmental Factor | Degradation Mechanism | Traditional Zirconia Response | Advanced Zirconia Response |
---|---|---|---|
Thermal Cycling | Microcrack formation and propagation | Progressive strength loss after 50-100 cycles | Maintains >85% of properties after 500+ cycles |
Corrosive Chemicals | Grain boundary attack and phase destabilization | Surface-to-core degradation within months | Surface passivation with minimal penetration |
Combined Mechanical/Thermal Stress | Accelerated creep and stress-assisted corrosion | Rapid failure under combined loading | Engineered microstructure distributes stress and prevents critical crack formation |
Radiation Damage | Atomic displacement and defect accumulation | Progressive embrittlement and swelling | Nanostructured defect sinks trap and neutralize radiation damage |
Which Industries Benefit Most From These New Findings?
While zirconia research advances offer potential benefits across many sectors, certain industries stand to gain transformative advantages from implementing these new materials.
What matters most: industries with the most extreme operating conditions—where traditional materials consistently fail to deliver adequate performance or lifetime—will see the most dramatic return on investment from adopting these advanced zirconia solutions.
The aerospace sector is experiencing perhaps the most significant impact from these research advances. New zirconia composites are enabling critical components in aircraft engines to operate at higher temperatures, directly translating to improved fuel efficiency and reduced emissions. Specifically, turbine shrouds and combustor liners manufactured from advanced zirconia composites allow operating temperatures 150-200°C higher than previous generation materials.
Chemical processing industries are implementing these materials to solve longstanding corrosion challenges. Pumps, valves, and reactor components made from new zirconia formulations are demonstrating 5-7 year lifespans in environments that previously required annual replacement of metal or conventional ceramic parts.
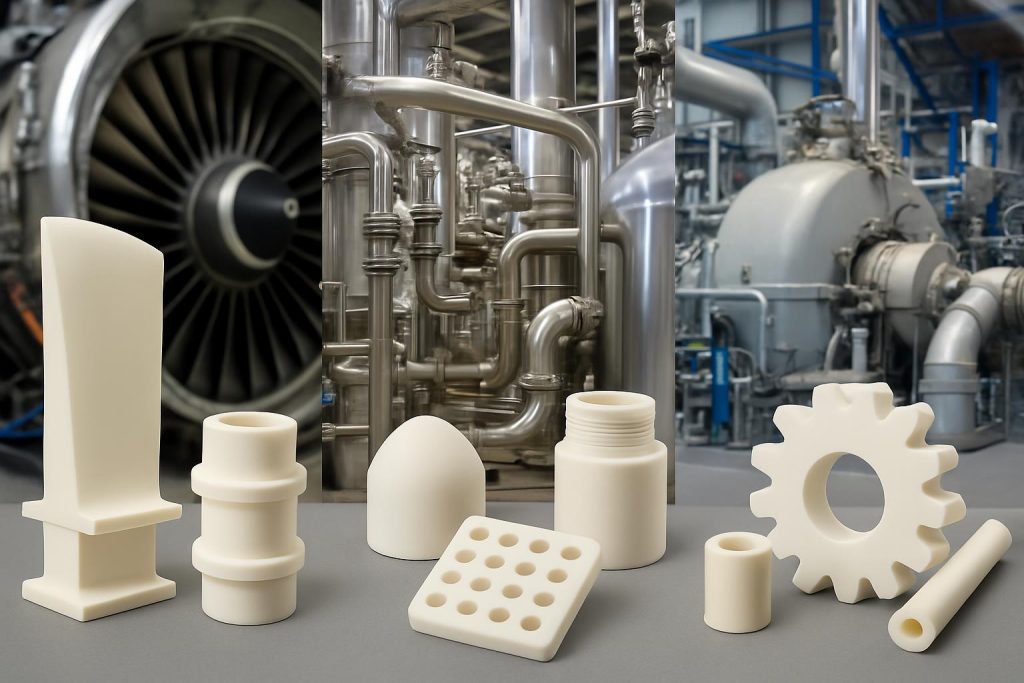
What Performance Metrics Matter Most In Critical Applications?
When evaluating advanced zirconia materials for extreme environment applications, focusing on the right performance metrics is essential for making sound technical and business decisions.
The key insight: while traditional metrics like room-temperature strength and hardness remain important, they’re poor predictors of performance in extreme environments. A new generation of application-specific performance indicators provides much better guidance.
High-temperature mechanical properties have emerged as the most critical performance metrics for many applications. Recent research shows that conventional strength testing at room temperature has almost no correlation with performance above 1200°C. New testing protocols measuring creep resistance, slow crack growth thresholds, and strength retention after thermal cycling provide much more reliable performance predictions.
Thermal shock resistance quantified through standardized thermal quenching tests has proven to be a crucial metric for applications involving rapid temperature changes. Advanced zirconia materials now demonstrate resistance to temperature differentials exceeding 500°C without failure—more than double the capability of conventional ceramics.
Performance Metric | Traditional Testing Approach | Advanced Evaluation Method | Correlation with Field Performance |
---|---|---|---|
Mechanical Integrity | Room-temperature strength testing | High-temperature testing under combined stresses | High correlation with actual service life |
Thermal Stability | Single-point maximum temperature | Cyclic exposure with property measurement | Excellent predictor of thermal cycling performance |
Corrosion Resistance | Simple weight loss measurement | Microstructural analysis after exposure | Strong correlation with long-term stability |
Lifetime Prediction | Accelerated single-factor testing | Multi-factor testing with statistical modeling | 80-90% accuracy in predicting service life |
System Compatibility | Material-specific properties | Interface stability and interaction testing | Critical for preventing unexpected failures |
How Are Testing Methodologies Evolving For Zirconia?
The gap between laboratory testing and real-world performance has historically been a major challenge for ceramic materials. Recent advances in testing methodologies are closing this gap, providing much more reliable predictions.
What’s changing: testing is moving from simplified, single-parameter evaluations to sophisticated multi-factor protocols that more accurately simulate the complex conditions materials face in extreme environments.
Integrated multi-parameter testing represents perhaps the most significant advancement in evaluation methodologies. Traditional approaches tested properties like strength, temperature resistance, and chemical stability separately, missing critical interaction effects. New protocols simultaneously apply mechanical stress, thermal cycling, and chemical exposure—revealing synergistic failure mechanisms that single-factor testing would never detect.
In-situ characterization techniques now allow researchers to observe microstructural changes in real-time as materials are exposed to extreme conditions. Advanced imaging and spectroscopy methods performed while materials are under stress, at high temperature, or exposed to corrosive media provide unprecedented insights into degradation mechanisms.
Testing Innovation | Key Capabilities | Benefits Over Traditional Methods | Implementation Status |
---|---|---|---|
Multi-Parameter Simultaneous Testing | Combined mechanical, thermal, chemical stresses | Reveals interaction effects missed by single-factor testing | Increasingly standard in R&D, growing in quality control |
In-Situ Characterization | Real-time observation of microstructural changes | Identifies actual degradation mechanisms rather than just end results | Advanced research facilities, specialized testing services |
Accelerated Lifetime Testing | Statistically valid predictions from shorter tests | Reduces testing time from years to months while maintaining accuracy | Established protocols for specific industries |
Digital Twin Simulation | Virtual testing of material responses | Screens candidates before physical testing, reducing development time and cost | Growing adoption in advanced materials development |
Standardized Application-Specific Protocols | Industry-consensus test methods | Enables direct comparison between different suppliers and formulations | Varies by industry, most advanced in aerospace and medical |
What Design Considerations Emerge From New Research?
The expanded performance envelope of advanced zirconia materials enables—and often requires—new approaches to component and system design.
The design paradigm shift: rather than designing around ceramic limitations, engineers can now design for ceramic advantages, but this requires rethinking traditional approaches to material selection and component design.
Microstructure-based design principles have emerged as a fundamental consideration for advanced ceramics. Unlike metals, where composition largely determines properties, ceramic performance depends heavily on microstructural features like grain size, porosity, and phase distribution. New design approaches incorporate these factors explicitly, specifying not just material composition but also critical microstructural parameters.
Functionally graded materials (FGMs) represent a powerful design strategy enabled by recent manufacturing advances. Rather than using homogeneous materials, FGMs feature composition and microstructure that vary continuously through the component, optimizing different regions for specific requirements.
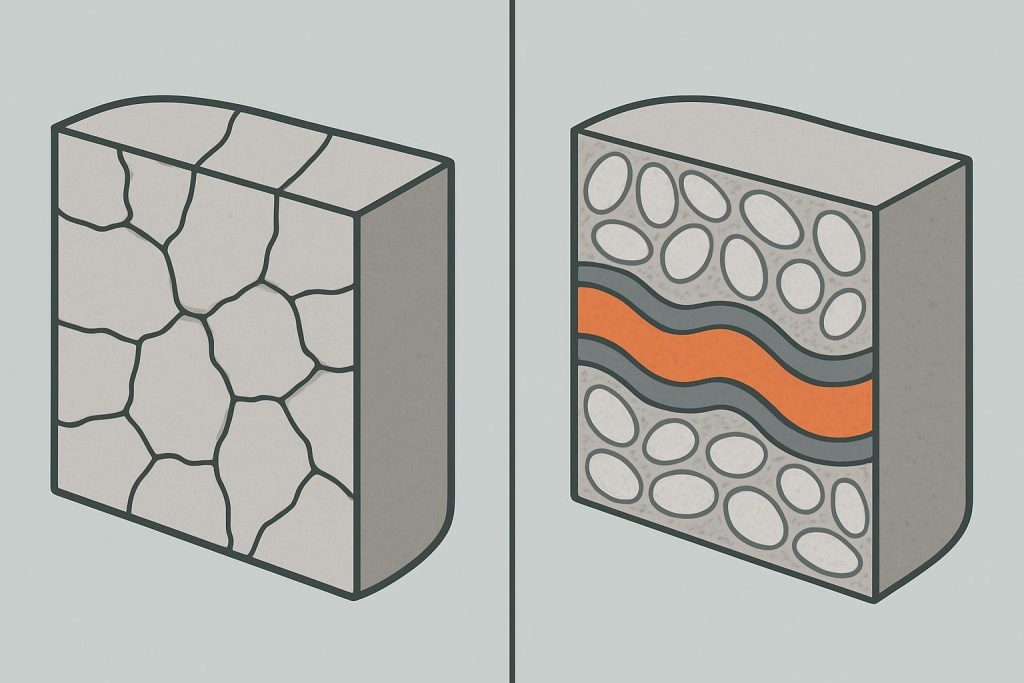
How Will Future Research Directions Shape Applications?
Current research trajectories point to several emerging technologies that will likely transform zirconia applications within the next decade.
Looking ahead: while today’s advanced zirconia materials represent significant improvements over previous generations, ongoing research suggests we’re still in the early stages of what’s ultimately possible with these versatile ceramics.
Self-healing zirconia composites represent one of the most promising research directions. These materials incorporate phases that react with oxygen at high temperatures to fill cracks as they form, preventing catastrophic failure. Early prototypes have demonstrated the ability to recover up to 80% of original strength after damage.
Multifunctional zirconia materials that combine structural, thermal, electrical, and even sensing capabilities are advancing rapidly. Rather than using ceramics solely for their mechanical and thermal properties, researchers are developing compositions that simultaneously provide multiple functions.
Research Direction | Current Development Stage | Potential Impact | Expected Commercialization |
---|---|---|---|
Self-Healing Ceramics | Advanced laboratory demonstration | Eliminate catastrophic failure modes | 3-5 years for initial applications |
Multifunctional Composites | Early commercial implementation | Reduce system complexity, enable new capabilities | Available now for specific applications, broader adoption in 2-4 years |
AI-Designed Materials | Active research and early implementation | Accelerate development cycles by 3-5× | Already impacting R&D, commercial products within 1-3 years |
Sustainable Manufacturing | Growing research focus | Reduce energy requirements by 30-50%, enable recycling | Gradual implementation over 2-7 years |
Extreme Environment Sensing | Proof-of-concept demonstration | Enable real-time monitoring in previously impossible environments | 3-6 years depending on application |
What Implementation Strategies Maximize New Research Benefits?
Translating research advances into practical business advantages requires thoughtful implementation strategies.
The implementation reality: despite their impressive capabilities, advanced zirconia materials aren’t simply drop-in replacements for existing solutions—they require thoughtful integration strategies to deliver their full potential.
Technology transfer pathways from research to application have been refined based on implementation experiences across multiple industries. Successful organizations typically employ a staged approach, beginning with non-critical applications to build experience and confidence before deploying advanced materials in mission-critical roles.
Cost-benefit analysis frameworks have evolved to capture the full value proposition of advanced materials. Traditional procurement approaches focusing primarily on acquisition cost often miss the substantial lifecycle benefits these materials provide. Comprehensive evaluation models now incorporate factors like extended service life, reduced maintenance requirements, improved system efficiency, and avoided downtime.
Implementation Strategy | Key Elements | Benefits | Typical Timeline |
---|---|---|---|
Staged Adoption | Begin with non-critical applications, expand based on performance data | Builds experience while minimizing risk | 6-18 months for initial evaluation to full implementation |
Comprehensive Cost-Benefit Analysis | Include lifecycle costs, efficiency improvements, and avoided downtime | Justifies higher initial investment | 1-3 months analysis before implementation decision |
Supplier Partnership | Collaborative development, performance guarantees, technical support | Reduces implementation risk, accelerates problem-solving | Ongoing relationship with defined milestones |
Personnel Training | Technical education on material properties, handling, and maintenance | Prevents implementation failures due to knowledge gaps | 1-3 months before implementation |
Performance Monitoring | Systematic data collection and analysis from initial applications | Validates benefits, guides expansion to additional applications | Continuous through implementation lifecycle |
Conclusion
Recent zirconia research has fundamentally expanded what’s possible in extreme environment applications, offering unprecedented combinations of properties that solve longstanding materials challenges. These advances aren’t merely incremental improvements—they represent step-changes in performance that enable new capabilities and efficiencies across multiple industries.
For technical decision-makers, these materials offer compelling advantages: operating temperature capabilities extended by 200-300°C, service lifetimes increased 3-5×, and resistance to combined stresses that would rapidly degrade conventional materials. Organizations implementing these advanced ceramics report significant competitive advantages, including reduced maintenance costs, improved system efficiency, and access to operating conditions previously considered impossible.
FAQ Section
Q1: How does the cost of advanced zirconia materials compare to conventional options?
Advanced zirconia materials typically cost 3-5 times more than conventional ceramics and 7-10 times more than high-performance metals on a per-unit basis. However, lifecycle cost analysis often shows favorable economics due to extended service life (typically 3-5 times longer), reduced maintenance requirements, and system-level efficiency improvements. Several case studies document payback periods of 12-24 months for these materials in extreme environment applications, with substantial ongoing savings thereafter.
Q2: What are the most effective supplier qualification processes for advanced zirconia materials?
Effective supplier qualification should include comprehensive technical assessment and business evaluation. Technical qualification should examine material property documentation, statistical process control data, and quality management systems. Request sample components for independent testing, focusing on properties critical to your application. Business qualification should assess production capacity, financial stability, and technical support capabilities.
Q3: How can companies balance cost efficiency with performance in zirconia applications?
Companies can optimize the cost-performance balance by implementing application-specific material selection and design approaches. First, clearly define the critical performance requirements and operating conditions to avoid over-engineering. Consider hybrid designs that use advanced zirconia materials only where their unique properties are essential, combined with conventional materials elsewhere.
Q4: What testing protocols best predict real-world performance of these materials?
The most effective testing protocols combine standardized mechanical and thermal testing with application-specific simulations of actual operating conditions. Standard tests should include fracture toughness (ASTM C1421), flexural strength (ASTM C1161), thermal shock resistance (ASTM C1525), and relevant environmental exposure tests. Supplement them with application-specific protocols that simultaneously apply relevant combinations of mechanical stress, temperature cycling, and chemical exposure.
Q5: How are sustainability requirements changing zirconia material development?
Sustainability considerations are increasingly influencing zirconia material development in several ways. Manufacturing processes are evolving to reduce energy consumption and waste generation, with innovations like lower-temperature sintering and near-net-shape forming. Material compositions are being reformulated to eliminate or reduce environmentally problematic elements while maintaining performance. Design approaches increasingly consider end-of-life scenarios, with some newer composites incorporating features that facilitate recycling or reuse of valuable components.