Understanding the unique properties of zirconia powder is essential for professionals in sensor technology. As industries increasingly rely on accurate readings for oxygen levels in various applications, identifying materials that excel in this domain becomes crucial. Zirconia powder stands out due to its impressive thermal stability, ion conductivity, and chemical resilience. This article will clarify how these properties not only enhance sensor performance but also contribute to more efficient and reliable operations in different environments. With insights drawn from industry standards and practices, this discussion aims to establish the credibility of zirconia’s effectiveness in oxygen sensor applications.
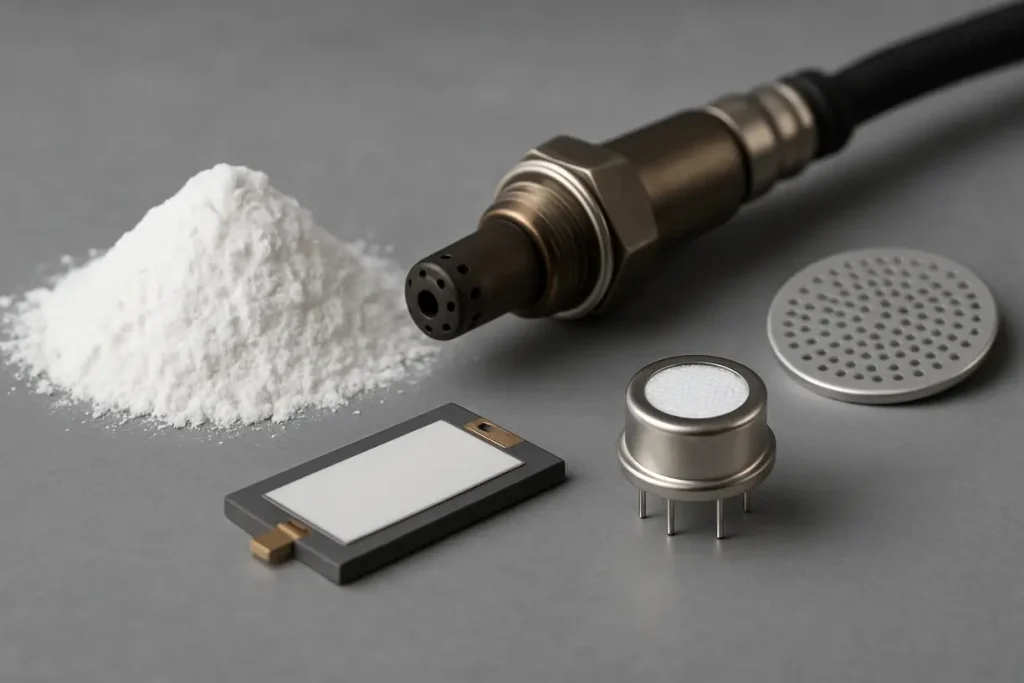
Image shows zirconia powder, highlighting its unique properties vital for sensor technology applications.
What Are the Key Properties of Zirconia Powder?
Zirconia powder, or zirconium dioxide (ZrO₂), is recognized for its exceptional properties that make it suitable for various industrial applications. First and foremost, it has high thermal stability, which allows it to maintain its characteristics even at elevated temperatures. This trait is essential for sensors exposed to harsh environments.
The chemical makeup of zirconia provides it with excellent mechanical properties, including high strength and fracture toughness. Moreover, its resistance to degradation and chemical corrosion makes it an ideal candidate for environments that may compromise other materials. For example, in applications involving combustion engines or industrial processes that emit pollutants, zirconia’s durability ensures longevity and reliability.
A significant property of zirconia powder is its ionic conductivity. In fact, this characteristic is vital for oxygen sensors since it allows the material to facilitate the movement of ions, which is necessary for accurate measurements. Understanding these properties not only highlights why zirconia is favored in sensor technology but also helps decision-makers make informed choices regarding material selection.
Property | Description | Importance |
---|---|---|
Thermal Stability | Retains properties at high temperatures | Ensures functionality in extreme conditions |
Mechanical Strength | High strength and toughness | Increases durability and reliability |
Chemical Resistance | Resistant to corrosion | Suitable for harsh industrial environments |
Ionic Conductivity | Facilitates ion movement | Crucial for accurate oxygen sensing |
Key Benefits of Zirconia Powder
- High Wear Resistance: Ideal for applications involving friction or abrasion.
- Low Thermal Conductivity: Minimizes heat transfer, useful in sensor applications.
- Biocompatibility: Safe for use in medical applications where sensors may contact biological materials.
- Versatility: Can be adapted for various applications across multiple industries.
- Stability in Humid Environments: Performs well in moisture-laden conditions without degradation.
How Does Zirconia Powder Perform in High Temperatures?
The performance of zirconia powder at high temperatures is one of its standout properties. So, how does it handle extreme conditions? Zirconia maintains its integrity under heat, making it an exemplary choice for oxygen sensors used in high-temperature environments such as automotive exhaust systems.
When exposed to temperatures that can impact sensor accuracy, zirconia exhibits minimal degradation. This ability to withstand heat is particularly significant for industries such as aerospace and automotive, where sensors frequently operate in extreme climates. In these scenarios, maintaining accuracy and reliability is paramount.
Research shows that zirconia can perform effectively up to temperatures of approximately 1,000 degrees Celsius. Furthermore, its thermal stability helps in maintaining consistent sensor responses, thus improving overall measurement accuracy. This characteristic is particularly beneficial in applications where precise oxygen readings are critical for optimizing performance and reducing emissions.
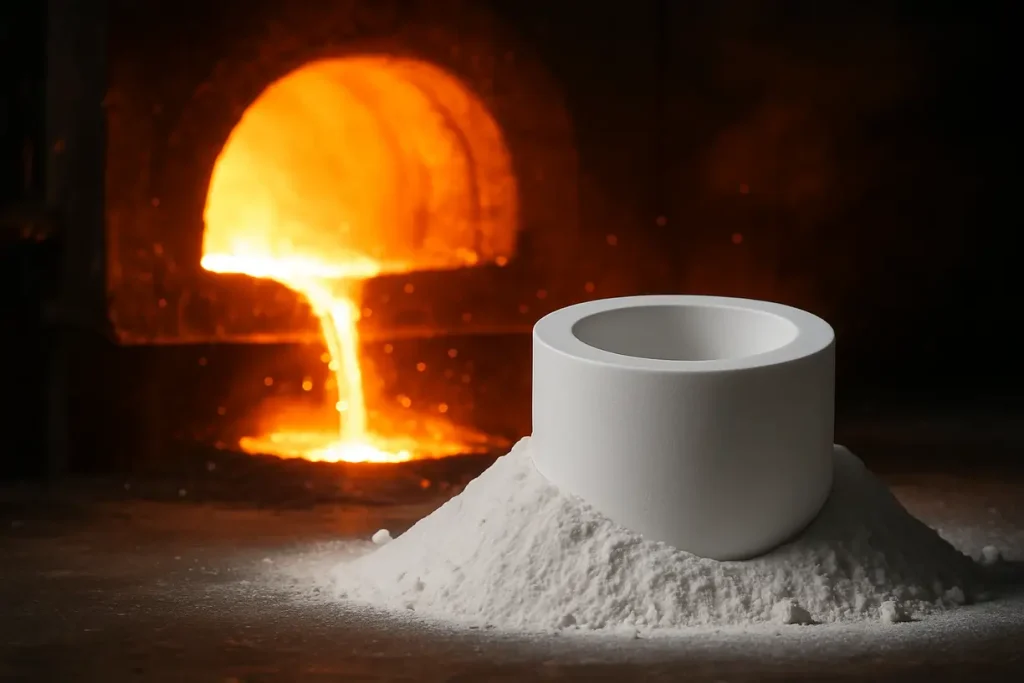
Illustration depicts zirconia powder’s ability to perform well in high-temperature environments, demonstrating its durability.
Temperature Range | Performance Characteristics |
---|---|
Up to 600 °C | Maintains physical properties and stability |
600 °C – 1,000 °C | Exhibits consistent performance for sensors |
Over 1,000 °C | Excellent durability, minimal degradation |
Applications in High-Temperature Environments
- Automotive Exhaust Sensors: Monitors oxygen levels to optimize combustion and reduce emissions.
- Industrial Kilns: Maintains accuracy in environments with fluctuating temperatures.
- Combustive Processes: Essential for accurate measurements in refining and energy production.
Why Is Ion Conductivity Important for Oxygen Sensors?
Ion conductivity is essential for the performance of oxygen sensors because it directly influences measurement efficiency and accuracy. But what exactly does ion conductivity entail? It refers to the material’s ability to transport ions, which is crucial for the sensor’s function.
Zirconia powder is known for its high ionic conductivity, especially when doped with certain oxides like yttria. This enhancement significantly improves its ability to serve as an ion conductor, which is vital for sensing applications. Essentially, sensors rely on the movement of oxygen ions through the zirconia electrolyte to produce accurate readings.
The relationship between ionic conductivity and sensor accuracy cannot be overstated. For example, in automotive and industrial applications, even slight variations in oxygen levels can lead to inefficient combustion and increased emissions. Therefore, using zirconia with optimal ionic conductivity ensures that the sensors can detect these levels promptly and accurately, leading to improved performance and compliance with environmental regulations.
Factor | Effect on Sensor Accuracy |
---|---|
High Ionic Conductivity | Enables rapid response to oxygen levels |
Low Ionic Conductivity | Slower readings can lead to inaccuracies |
Importance of Ionic Conductivity in Sensors
- Fast Response Times: Critical for dynamic systems needing real-time data.
- Energy Efficiency: Reduces power consumption in sensor operation.
- Enhanced Detection Range: Allows sensors to operate effectively over a broader range of oxygen concentrations.
What Role Does Zirconia’s Chemical Stability Play?
Chemical stability is another critical property of zirconia powder that enhances its application in oxygen sensors. Why is this so vital? Because the environments in which these sensors operate can be corrosive, any degradation of the sensor material can compromise its effectiveness.
Zirconia demonstrates exceptional resistance to various chemicals, including acids and bases. In industrial settings, this resistance helps maintain device integrity over time, reducing the need for frequent replacements. When exposed to chemicals, zirconia’s stability ensures that the properties that make it suitable for sensing applications remain intact, ultimately contributing to longer service life and better reliability.
Furthermore, this chemical stability allows oxygen sensors to provide consistent and accurate readings without interference from corrosive agents. In practice, this means that manufacturers can trust that the sensors will operate effectively without degrading over time through exposure to harsh environmental elements.
Chemical Exposure | Zirconia’s Response |
---|---|
Acidic Solutions | Minimal degradation |
Basic Conditions | High resistance to wear |
Organic Solvents | Maintains integrity |
Types of Corrosive Environments
- Automotive Exhaust: Contains harmful gases that can degrade sensor materials.
- Chemical Manufacturing: Acids and bases prevalent in production processes can degrade sensitive materials.
- Marine Applications: Exposure to saltwater and other corrosive elements necessitates high chemical stability.
How Does Zirconia Powder’s Mechanical Strength Affect Sensors?
The mechanical strength of zirconia powder is a defining attribute that impacts the effectiveness of oxygen sensors. But why is mechanical strength so critical? Sensors often encounter stress and potential impact during operation, especially in industrial or automotive settings.
Zirconia’s high strength and toughness help it withstand physical shocks without cracking or breaking. This robustness translates into reliable performance, even when sensors are subjected to vibrations or mechanical strain. For example, in automotive applications, where engines can generate significant vibrations, a strong sensor body means ongoing accurate readings.
Moreover, the mechanical properties of zirconia allow it to perform well under varying pressure conditions. This is particularly important in handling gases, where sensor integrity must remain uncompromised to measure accurately. A strong and durable structure not only enhances performance but also extends the lifespan of the sensor, reducing maintenance costs for businesses.
Aspect | Benefit |
---|---|
High Toughness | Withstands physical impact |
Resistance to Deformation | Maintains measurement accuracy |
Longevity | Reduces replacement costs |
Factors Affecting Mechanical Strength
- Particle Size: Smaller particles may provide enhanced density and toughness.
- Composite Formulations: Combining zirconia with other materials can improve strength and performance.
- Processing Conditions: Temperature and pressure during manufacturing can influence the final strength of zirconia components.
Why Is Zirconia Powder a Preferred Material for Oxygen Sensors?
Considering the properties discussed, it’s clear why zirconia powder is a popular choice in sensor technology. What sets it apart from other materials? A combination of high thermal stability, excellent ionic conductivity, and remarkable chemical resistance makes zirconia an ideal candidate.
Unlike traditional materials such as alumina, zirconia provides superior performance in harsh environments. In practical terms, this translates to better sensor accuracy and longevity, leading to more efficient operations in various industries. Furthermore, the reduced maintenance needs associated with zirconia-based sensors result in lower total ownership costs.
Additionally, zirconia’s versatility allows manufacturers to innovate continuously. They can adapt the chemical composition of zirconia for specific applications or performance levels, tailoring sensors to meet particular operational requirements. This adaptability ensures that industries can achieve optimal sensor solutions while maintaining compliance with relevant standards.
Material | Advantages of Zirconia |
---|---|
Zirconia Powder | Best thermal and ionic properties |
Alumina | Lower thermal stability, less accurate |
Traditional Metals | Susceptible to corrosion and wear |
Expected Industry Applications for Zirconia Sensors
- Automotive Industry: Emission control and management systems.
- Power Generation: Monitoring and optimization of combustion efficiency in turbines.
- Aerospace Engineering: Oxygen sensors for in-flight monitoring systems.
How Do Particle Size and Morphology Influence Performance?
The particle size and morphology of zirconia powder play a significant role in its performance as a sensor material. So, why does this matter? Smaller particle sizes can enhance the surface area available for reactions and ion movement, which is particularly crucial for sensors.
Zirconia with a fine particle size typically shows improved ionic conductivity. This means that sensors made from finely milled zirconia can respond more quickly and accurately to changes in oxygen concentrations. Manufacturers often optimize the particle size during production to achieve the desired performance characteristics.
Morphology, or the shape of the zirconia particles, also influences how the material interacts in practical applications. For instance, spherical particles might pack more efficiently than irregularly shaped ones, leading to enhanced performance characteristics. Industries need to consider both factors carefully to achieve the best outcomes for oxygen sensing applications.
Particle Size | Influence on Performance |
---|---|
Smaller Particles | Improved ionic conductivity |
Irregular Shapes | Potentially less efficient packing |
Effects of Particle Morphology on Performance
- Surface Area: Larger surface areas enhance reaction rates and sensor responsiveness.
- Inter-Particle Bonding: Proper bonding among particles can increase overall strength and durability.
- Grain Structure: Impacts how effectively zirconia can manage mechanical stresses.
What Are the Manufacturing Techniques for Zirconia Powder?
The production of zirconia powder is a sophisticated process that influences its final characteristics. So, what methods are typically used? Common techniques include precipitation, sol-gel processes, and mechanical milling.
The precipitation method involves creating zirconia from a soluble zirconium salt. This process leads to high purity which is critical for sensor applications where contamination could impact performance. On the other hand, the sol-gel process allows for control over particle size and morphology, enabling customization for specific needs.
Mechanical milling is another approach that can further refine particle size and distribution. Ultimately, each technique has unique benefits that cater to different applications in sensor technology, ensuring that manufacturers can produce zirconia powders tailored to precise specifications.
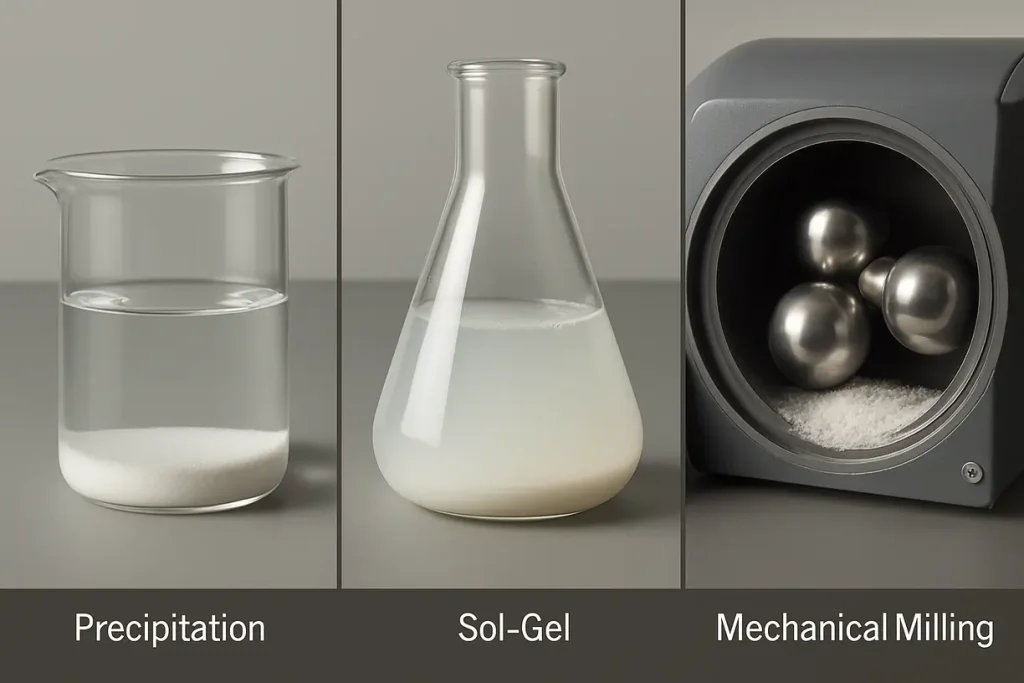
Image illustrates various techniques used in the manufacturing of zirconia powder, highlighting their unique contributions.
Manufacturing Technique | Key Characteristics |
---|---|
Precipitation | High purity, consistent quality |
Sol-Gel Process | Customizable particle properties |
Mechanical Milling | Refines particle size efficiently |
Considerations in Manufacturing Processes
- The purity of Raw Materials: Influences the quality of the final product.
- Process Control: Maintaining specific conditions throughout production is vital for consistent results.
- Post-Processing Treatments: Can enhance properties such as strength and conductivity.
How Does Zirconia Powder Contribute to Environmental Sustainability?
As industries focus more on sustainability, the role of materials like zirconia powder becomes increasingly significant. What makes it environmentally friendly? Zirconia can enhance the efficiency of processes that reduce emissions and improve energy use.
In applications such as exhaust gas monitoring, accurate oxygen sensing is crucial for optimizing combustion processes. This, in turn, leads to reduced fuel consumption and lower emissions of harmful gases. Using zirconia sensors can thus contribute to more environmentally friendly industrial practices and compliance with regulations.
Moreover, the durability of zirconia reduces the frequency of replacements, which can further decrease the ecological footprint associated with manufacturing and waste. By opting for zirconia-based sensors, companies can align their operations with environmental sustainability goals while simultaneously increasing efficiency.
Aspect | Environmental Benefit |
---|---|
Accurate Measurements | Reduces emissions |
Long Lifespan | Decreases waste and resources required |
Sustainability Factors with Zirconia
- Reduced Waste: Longer life spans of sensors lead to less frequent replacements.
- Energy Efficiency: Accurate readings help optimize processes, reducing resource waste.
- Recyclability: Potential for recovery and reuse of zirconia materials after sensor life concludes.
What Are the Future Trends for Zirconia in Sensor Technology?
The future of zirconia in sensor technology looks promising. So, what trends should industries watch for? Ongoing research and advancements are likely to enhance the existing properties of zirconia further, making it even more effective for sensor applications.
Emerging technologies may involve developing new dopants for zirconia, enhancing its ionic conductivity and stability. Furthermore, innovations in manufacturing techniques can lead to even finer control over particle size and morphology, resulting in sensors with improved speed and accuracy.
Beyond technical improvements, the growing focus on sustainability will drive demand for materials like zirconia that support more efficient industrial practices. Companies that invest in upgrading their sensing technologies with high-performance materials are poised to gain a competitive advantage in the market.
Trend | Expected Impact |
---|---|
Advanced Dopants | Improved sensor performance |
Enhanced Manufacturing | Finer control over material properties |
Increased Demand | Alignment with sustainability goals |
Conclusion
In summary, zirconia powder stands out as a superior material for oxygen sensors due to its combination of properties that ensure reliability and efficiency. Its thermal stability, mechanical strength, ionic conductivity, and chemical resistance position it as the material of choice for diverse applications. As industries evolve, the adaptability of zirconia will continue to meet and surpass the demands of modern sensor technology, paving the way for sustainable practices and enhanced performance.
FAQ Section
Q1: What makes zirconia powder suitable for sensors?
Zirconia powder is ideal for sensors primarily due to its high thermal stability, which allows it to function effectively at elevated temperatures without degrading. Its high ionic conductivity facilitates quick and accurate ion transport, essential for measuring oxygen levels. Additionally, its excellent mechanical strength and chemical resistance ensure durability in harsh environments, making it a reliable choice for a variety of applications.
Q2: How does temperature affect zirconia powder performance?
Temperature plays a crucial role in the performance of zirconia powder. At high temperatures, zirconia maintains its crystalline structure and properties, enabling it to perform reliably in extreme conditions, such as those found in automotive exhaust systems and industrial furnaces. This thermal stability helps prevent the material from deteriorating, which is vital for ensuring the accuracy of oxygen measurements over prolonged use.
Q3: What is the significance of ion conductivity in oxygen sensors?
Ion conductivity is critical in oxygen sensors as it directly affects their response time and accuracy. High ionic conductivity in zirconia allows for efficient movement of oxygen ions through the material, which is necessary for real-time monitoring of oxygen levels. This property ensures that sensors can quickly adjust to changes in oxygen concentration, thereby improving sensitivity and overall measurement precision—key factors in applications that demand stringent accuracy.
Q4: How does zirconia’s mechanical strength enhance sensor durability?
Zirconia’s high mechanical strength contributes to its durability by enabling it to withstand physical stress and shock. In many industrial and automotive applications, sensors are subjected to vibrations and impacts that could compromise weaker materials. The toughness of zirconia ensures that sensors remain intact and operational under such pressures, thus extending their lifespan and reducing the frequency and cost of replacements.
Q5: What are the future prospects for zirconia in the sensor industry?
The future of zirconia in the sensor industry looks promising due to ongoing research and technological advancements. Innovations in dopants and manufacturing techniques are expected to enhance the material’s properties, such as its ionic conductivity and responsiveness, making sensors even more efficient. Additionally, as industries increasingly prioritize sustainability, zirconia’s durability and low environmental impact position it favorably for continued use in various applications, aligning with global efforts towards greener technologies.