The use of zirconia powder in high-temperature sensors is growing, driven by its remarkable properties. Many decision-makers face challenges when selecting materials that can withstand extreme conditions while ensuring reliable performance. This article will address those concerns by detailing the benefits of zirconia powder as the material of choice for high-temperature sensors. You will learn about its unique characteristics, applications, and the value it brings to various industries. With insights backed by research and practical examples, this article will build your understanding and confidence in choosing zirconia powder for your high-temperature needs.
Why Is Zirconia Powder Preferred in High-Temperature Applications?
Zirconia powder stands out as a material in high-temperature applications due to its unique properties. Its impressive thermal stability enables sensors to maintain accuracy and reliability, even in extreme temperature environments. This characteristic is particularly crucial in industries where sensor performance directly impacts safety and operational efficiency.
Historically, zirconia has proven its worth in applications that demand high-performance materials. Unlike conventional materials that may warp, crack, or deteriorate under heat, zirconia can endure intense conditions, making it a go-to choice for engineers and manufacturers alike.
When it comes to comparisons, zirconia powder consistently outperforms alternatives such as alumina and silicon carbide. For instance, while alumina might work well in moderate temperatures, it lacks the thermal shock resistance that zirconia offers. Similarly, silicon carbide, although robust, can become less effective when subjected to rapid temperature fluctuations.
One of zirconia’s defining features is its ability to operate effectively in temperatures exceeding 1,000 degrees Celsius. This makes it not only suitable but ideal for applications in various sectors, including aerospace, automotive, and energy. Moreover, the versatility of zirconia powder allows its integration into diverse applications, ranging from high-performance engine components to advanced thermal sensors.
Ultimately, choosing zirconia powder ensures long-term reliability and performance. By minimizing the frequency of replacements and maintenance needs, businesses can significantly reduce operational costs while maximizing the efficiency of their high-temperature sensor systems. This combination of durability, performance, and cost-effectiveness underscores zirconia’s critical role in modern engineering.
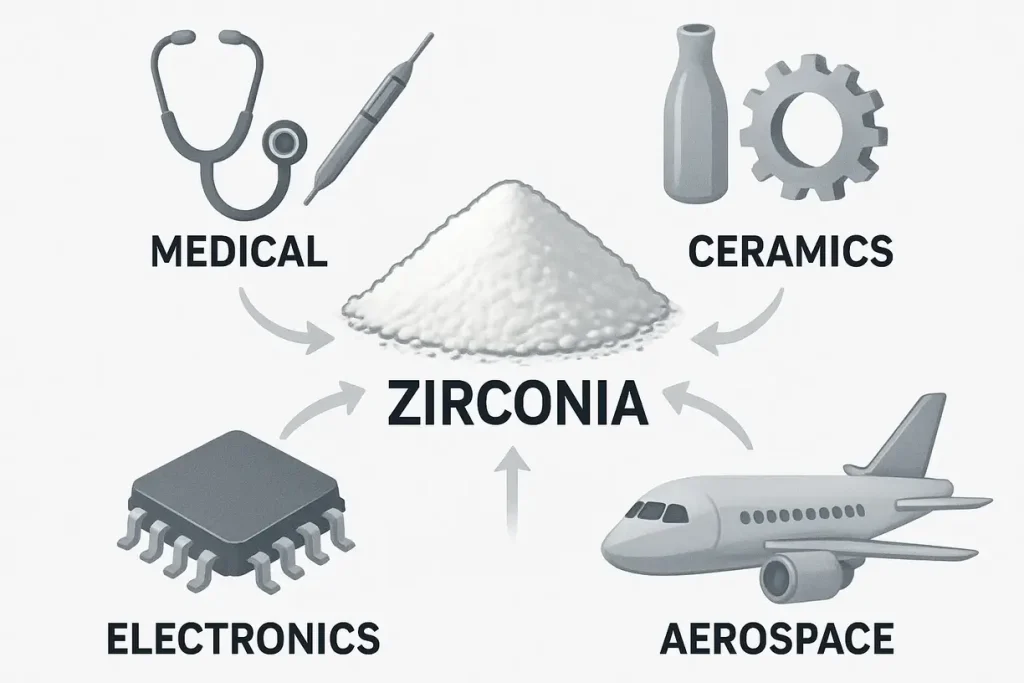
This image displays the diverse applications of zirconia powder in various industries.
What Are the Key Properties of Zirconia Powder?
Zirconia powder possesses several key properties, making it an ideal choice for high-temperature sensors.
Firstly, thermal stability is one of its standout attributes. Zirconia remains stable at elevated temperatures, ensuring that sensors provide accurate readings without degradation. This characteristic is particularly important in environments where temperature fluctuations are frequent and can have a significant impact on sensor performance. Due to its high melting point, zirconia can function effectively in extreme conditions, often exceeding 1,000 degrees Celsius.
Secondly, it has exceptional mechanical strength. This robust property allows sensors to withstand the physical stresses encountered in harsh conditions, such as vibrations or shocks that can occur in industrial machinery and automotive applications. The high tensile strength of zirconia contributes to its durability, ensuring that sensors maintain their structural integrity over time.
Furthermore, zirconia’s chemical inertness means it does not react with most substances, making it suitable for diverse applications, including those involving corrosive environments. This resistance to chemical interactions helps prevent sensor degradation and maintains long-term accuracy, especially in industries like chemical manufacturing or energy production.
Additional Key Characteristics of Zirconia Powder:
- High Density: This contributes to durability and thermal conductivity stability, which are crucial for sensor applications.
- Low Thermal Conductivity: This property aids in maintaining temperature gradients, allowing for precise measurements in sensor technology.
- Toughness: Zirconia’s ability to resist fracture under stress further enhances its suitability for demanding applications.
Table 1 below summarizes these key properties:
Property | Description | Importance |
---|---|---|
Thermal Stability | Maintains performance at high temperatures | Ensures accurate sensor readings |
Mechanical Strength | High resistance to physical stress | Increases sensor durability |
Chemical Inertness | Non-reactive with most substances | Suitable for various applications |
High Density | Provides enhanced durability | Supports reliability in challenging environments |
Low Thermal Conductivity | Aids in accurate temperature measurements | Essential for sensor response precision |
Understanding these properties can help companies determine the best materials for their high-temperature sensor applications, ensuring optimal performance and longevity.
How Does Zirconia Powder Perform in Extreme Conditions?
Understanding zirconia powder’s behavior in extreme conditions is essential for making informed material choices.
In terms of temperature resilience, zirconia can handle fluctuations without losing integrity, which is key in applications where sudden temperature changes are common.
Additionally, pressure can affect the performance of materials, but zirconia maintains its properties even under high pressure, which is often the case in industrial settings.
Corrosion resistance is another significant factor. Zirconia is not susceptible to many corrosive agents, ensuring it remains reliable in harsh chemical environments.
This performance capability can be analyzed further in Table 2:
Condition | Zirconia Powder Performance |
---|---|
High Temperature | Remains stable and effective |
High Pressure | Retains mechanical properties |
Corrosive Environments | Minimal degradation and reliable function |
With these advantages, zirconia powder ensures that sensors function optimally in extreme conditions, making them a smart option for manufacturers looking to enhance their products.
Performance in Various Conditions:
- Thermal Shock: Quick shifts in temperature do not adversely affect zirconia.
- Impact Resistance: The material withstands fluctuations in physical stress without cracking.
- Chemical Exposure: Zirconia’s inert nature protects against degradation from aggressive chemicals.
What Industries Rely on Zirconia Powder for High-Temperature Sensors?
Zirconia powder finds applications across several vital industries due to its unique properties and reliability.
In aerospace engineering, high-temperature sensors are critical for monitoring engine performance. Here, zirconia powder is vital in ensuring safety and efficiency.
The automotive industry also utilizes zirconia-based sensors. They are crucial for exhaust gas temperature monitoring, helping to optimize engine performance and reduce emissions.
In the energy sector, companies rely on zirconia powder sensors in turbines and other equipment where high temperatures are prevalent. These sensors help ensure efficient operation and safety in power generation.
Table 3 highlights industry applications:
Industry | Application | Importance |
---|---|---|
Aerospace | Engine performance monitoring | Safety and efficiency |
Automotive | Exhaust gas temperature monitoring | Optimizes performance |
Energy | Turbine operation sensors | Ensures effective energy generation |
The diverse applications of zirconia powder demonstrate its importance across various sectors. Its reliability promotes enhanced performance and safety in critical systems.
How Is Zirconia Powder Made and Processed?
Creating high-quality zirconia powder involves a series of steps that ensure its properties align with application requirements.
The manufacturing process typically begins with zirconium oxide, which is refined to remove impurities. This purity is essential for maintaining performance in high-temperature conditions.
Next, several processing techniques can be applied, including milling and blending, to achieve the desired particle size and distribution. Fine particle size helps enhance the sensor’s response time and accuracy.
Finally, quality control measures are paramount throughout production. Testing for thermal and mechanical properties ensures that the final product meets strict industry standards.
Table 4 summarizes the zirconia production process:
Step | Description | Importance |
---|---|---|
Refinement | Removal of impurities from zirconium oxide | Ensures high purity of zirconia powder |
Processing | Milling and blending for desired size | Improves sensor performance |
Quality Control | Continuous testing for thermal and mechanical properties | Maintains high industry standards |
Key Steps in Zirconia Powder Production:
- Milling: Reducing particle size for better application performance.
- Mixing: Ensuring homogeneity for consistent quality.
- Sintering: Enhances strength and stability of the final product.
- Testing: Rigorous checks to guarantee adherence to specifications.
This careful attention to detail in the production process leads to zirconia powder that consistently performs well in high-temperature applications.
What Applications Benefit from Zirconia Powder Sensors?
The versatility of zirconia powder allows for its use in various applications that demand reliable sensor performance.
For instance, in industrial machinery, zirconia sensors are used for monitoring temperatures in manufacturing processes. They ensure that machines operate within safe limits, lowering the risk of failures and costly downtime.
Zirconia sensors also play a role in monitoring systems within critical infrastructures, like power plants. Here, they keep track of varying temperature conditions, contributing to overall operational safety.
Moreover, their use in safety systems is crucial. In environments where overheating can lead to hazardous situations, zirconia sensors help trigger safety protocols, ensuring prompt action is taken.
Table 5 shows applications of zirconia powder sensors:
Application | Description | Benefits |
---|---|---|
Industrial Machinery | Temperature monitoring in manufacturing processes | Reduces risk of failure and downtime |
Monitoring Systems | Temperature tracking in power plants | Contributes to operational safety |
Safety Systems | Overheating detection in critical environments | Enhances safety protocols |
Understanding these applications demonstrates how zirconia sensors contribute to efficiency and safety across multiple settings.
Specific Applications of Zirconia Powder Sensors:
- Heat Treating Equipment: For monitoring furnace temperatures in metal processing.
- Food Processing: Ensuring proper temperatures are maintained for food safety.
- HVAC Systems: Monitoring air and water temperatures for energy efficiency.
How Do Cost and Value Compare with Other Materials?
Cost considerations influence the choice of materials for high-temperature sensors. Zirconia powder may have a higher initial cost than alternatives like alumina, but it provides significant value over time.
When comparing pricing, it is essential to consider performance versus longevity. Zirconia’s durability and resistance to thermal shock lead to lower replacement costs. A longer lifespan reduces the total cost of ownership for businesses that rely on high-temperature sensors.
Furthermore, the return on investment (ROI) is very favorable with zirconia sensors. With less frequent replacements and consistent performance, companies save considerably over time.
Insights into costs can be highlighted in the following table:
Material | Initial Cost | Lifespan | Estimated Long-Term Cost |
---|---|---|---|
Zirconia Powder | Higher | Longer | Lower total ownership cost |
Alumina | Lower | Shorter | Higher total ownership cost |
This comparison emphasizes the value proposition of zirconia powder sensors. Investing in quality materials today can yield substantial savings down the road.
Cost-Benefit Considerations:
- Initial Investment: Higher for zirconia powder but leads to greater savings over time.
- Performance Longevity: Zirconia’s durability translates to fewer sensor replacements.
- Operational Efficiency: Less maintenance required, allowing for uninterrupted operations.
What Challenges Exist in Using Zirconia Powder?
Despite its advantages, using zirconia powder is not without challenges.
One common issue is the processing difficulty. It may require specialized handling techniques to prevent defects during manufacturing.
Additionally, while zirconia is highly resistant, it can still be susceptible to stress under extreme conditions. Manufacturers must ensure proper design and installation to mitigate this risk.
Lastly, the initial acquisition cost can be a barrier. Some may hesitate to invest in higher-quality materials when cheaper options exist. However, as discussed, the long-term benefits of using zirconia powder can outweigh these initial costs.
These challenges can be divided into a clearer overview:
Challenge | Description | Potential Solutions |
---|---|---|
Processing Difficulty | Requires specialized techniques | Invest in training and equipment |
Stress Under Extreme Conditions | Susceptibility to design flaws | Ensure proper design and installation |
Initial Acquisition Cost | Higher upfront expense | Emphasize long-term savings |
Addressing these challenges proactively helps ensure that zirconia powder remains a viable choice for high-temperature sensors.
What Innovations Are Emerging in Zirconia Powder Technology?
The field of zirconia powder technology is evolving, with ongoing research leading to exciting innovations.
Latest studies focus on enhancing sensor capabilities, such as improved sensitivity and faster response times. These advancements can further solidify zirconia’s position as the material of choice.
Another area of innovation involves developing hybrid materials that combine zirconia’s properties with those of other components. This could lead to enhanced performance in specific applications, driving efficiency and safety.
Lastly, advancements in production methods are continually being integrated, making it easier to produce high-quality zirconia at lower costs. As technology progresses, businesses can expect even more refined products tailored to their needs.
Table 6 can illustrate these innovations:
Innovation | Description | Impact |
---|---|---|
Improved Sensitivity | Enhancements that allow for quicker responses | Increases sensor reliability |
Hybrid Materials | Combination of zirconia with other elements | Potential for specialized applications |
Advanced Production Methods | Streamlined manufacturing processes | Reduced costs and improved quality |
Future Trends in Zirconia Powder Technology:
- Nano-Zirconia: Smaller particles may enhance performance even further.
- Sustainable Production Methods: Focus on green technologies in manufacturing.
- Smart Sensor Integration: Utilizing zirconia in IoT applications for better monitoring.
These innovations highlight the promise of zirconia powder, ensuring it remains at the forefront of sensor technology.
Why Trust Zirconia Powder for Your High-Temperature Needs?
Trust in zirconia powder stems from its proven track record across multiple industries.
Testimonials from industry leaders often cite zirconia’s reliability and performance as key reasons for its continued use. Companies have reported markedly improved sensor performance and lower maintenance costs, further cementing this material’s reputation.
Case studies also support these claims. For instance, an aerospace company reported that switching to zirconia-based sensors improved engine monitoring metrics, allowing for more accurate diagnostics and maintenance alerts.
Recommendations from experts reinforce these insights, emphasizing the importance of selecting the right materials for high-temperature applications. The overall consensus is clear: zirconia powder is a trustworthy choice, backed by research and positive user experiences.
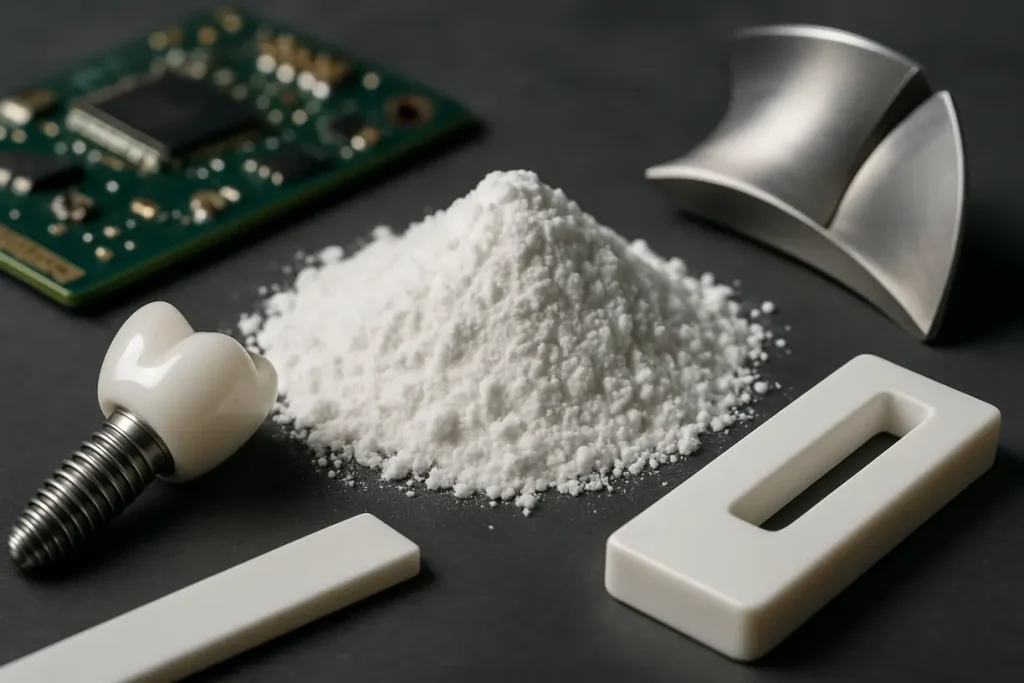
This image represents the trust placed in zirconia powder across various industries due to its proven performance.
In summary, the advantages of zirconia powder in high-temperature sensors include its durability, reliability, and resistance to harsh conditions. Industries that prioritize safety and performance can depend on zirconia to meet their demanding requirements.
Conclusion
In conclusion, zirconia powder emerges as an exceptional material for high-temperature sensors, thanks to its stability, mechanical strength, and chemical inertness. Businesses can achieve reduced maintenance costs and enhanced operational safety by investing in this reliable material. Global Industry stands ready to assist you in sourcing high-quality zirconia powder for your specific needs. Take the next step towards improving your high-temperature sensor applications and partner with us today for dependable solutions.
FAQ Section
Q1: What industries commonly use zirconia powder?
Zirconia powder is extensively utilized in aerospace, automotive, and energy sectors due to its high-temperature resilience and wear resistance. In aerospace, it is prized for components requiring durability and reliability under extreme conditions. The automotive industry employs zirconia for engine parts and fuel cells, while in the energy sector, it plays a crucial role in nuclear applications and thermal barrier coatings for turbines.
Q2: What are the advantages of zirconia powder over other materials?
Zirconia powder offers several advantages, including superior thermal stability, mechanical strength, and chemical inertness. It can withstand high temperatures and harsh environments better than many conventional materials, making it ideal for applications like cutting tools and biomaterials. Its resistance to wear and corrosion further enhances its value in demanding settings, allowing for longer service life and reduced maintenance costs.
Q3: How does the manufacturing process affect zirconia powder quality?
The quality of zirconia powder is greatly influenced by its manufacturing process. Techniques such as sintering, milling, and calcination play critical roles in determining the final properties of the powder. For instance, precise control over sintering temperature and time can enhance the density and mechanical strength of zirconia. Variations in these processes can lead to differences in particle size, distribution, and purity, impacting overall performance in applications.
Q4: What are the potential issues when using zirconia powder?
While zirconia powder has many benefits, there are potential challenges to consider. Processing difficulties can arise during shaping and sintering, especially if not done under optimal conditions. Additionally, zirconia may present limitations in extreme conditions, such as aggressive chemical environments, which can affect its durability. However, these challenges can often be mitigated through careful selection of processing techniques and formulations tailored to specific applications.
Q5: How does zirconia powder contribute to safety in high-temperature applications?
Zirconia powder enhances safety in high-temperature applications by enabling accurate temperature monitoring and control. Sensors made from zirconia materials can function reliably in extreme heat, providing critical data for ensuring equipment safety. This capability reduces the risk of malfunctions or failures in high-temperature environments, ultimately improving operational efficiency and minimizing downtime. As a result, the strategic use of zirconia powder contributes significantly to the safety and reliability of industrial processes.