In the competitive landscape of manufacturing, enhancing product quality is an ongoing challenge. One solution that has gained attention is zirconia powder, a material known for its unique properties that make it an ideal addition to advanced coating formulations. Many companies struggle with durability, wear resistance, and thermal stability in their coatings, which can lead to increased costs and product failures. This article explores how zirconia powder addresses these challenges, providing substantial benefits to those in industries like aerospace, automotive, and machinery. Trust in the improvements zirconia can bring to your products, based on extensive research and industry applications.
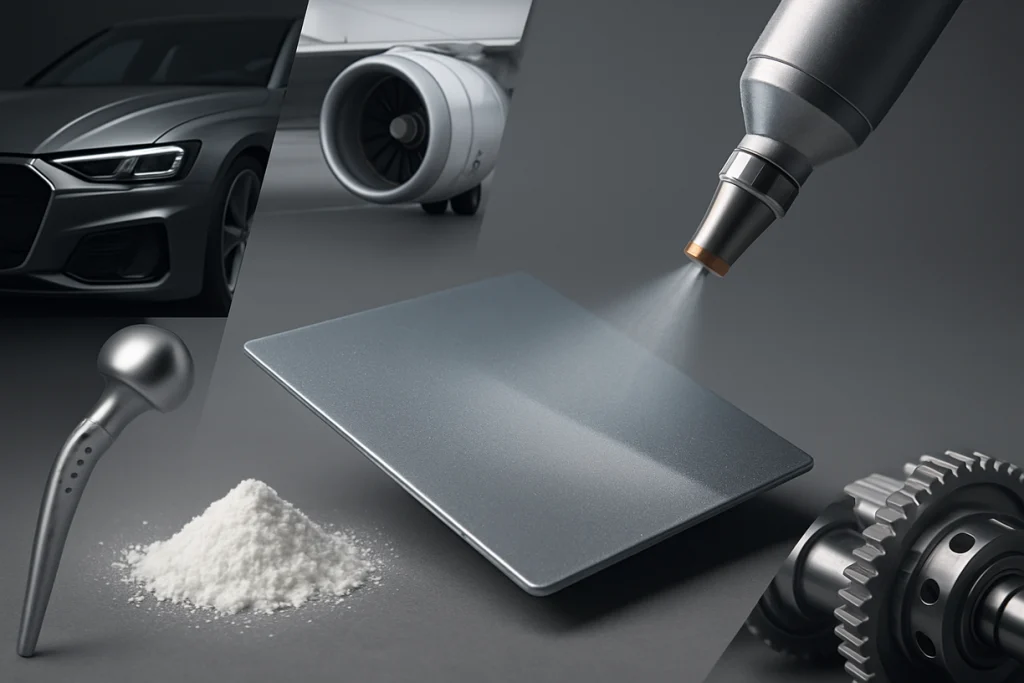
This image illustrates the application of zirconia powder in advanced coating formulations, highlighting its role in various industries.
What Are the Key Properties of Zirconia Powder?
Zirconia powder is derived from zircon, and it possesses a unique set of properties that make it highly valuable in various applications. First, its high hardness is one of its standout features, which contributes significantly to the performance of the coatings. This durability is crucial for products that face wear and tear over time.
Another noteworthy property is its chemical stability. Zirconia is resistant to corrosion and chemicals, which ensures that coatings maintain their integrity even in harsh environments. This makes zirconia suitable for use in industries that deal with volatile substances.
Thermal stability is also a vital characteristic. Zirconia can withstand high temperatures without degrading, which is essential for applications where heat resistance is paramount. Additionally, the versatility of zirconia allows manufacturers to fine-tune the particle size and distribution for specific needs, resulting in customized solutions that meet industry standards.
To summarize, zirconia powder’s properties—high hardness, chemical stability, thermal resistance, and configurability—make it a preferred choice in advanced coating formulations. These features address many issues faced by manufacturers, providing a solid foundation for improved product performance.
Property | Description | Importance |
---|---|---|
Hardness | High hardness enabling durability | Reduces wear and extends product lifespan |
Chemical Stability | Resistance to corrosion and harsh chemicals | Maintains integrity in challenging environments |
Thermal Stability | Withstands high temperatures | Vital for applications in heat-sensitive sectors |
Versatility | Customizable particle size and distribution | Allows for tailored solutions |
How Does Zirconia Powder Improve Coating Durability?
In manufacturing, durability is a critical factor determining the success of a product. Zirconia powder plays a significant role in enhancing the durability of coatings through a couple of mechanisms. First, it forms a strong bond with other components in the coating. This bond minimizes the likelihood of delamination and improves adherence, ensuring a longer-lasting finish.
Additionally, zirconia’s inherent hardness contributes to abrasion resistance. When coatings contain zirconia, they are better equipped to withstand physical wear over time, making them suitable for demanding environments.
Real-world examples abound. In the automotive industry, for instance, components coated with zirconia are often exposed to road debris and other harsh conditions. Coatings that include zirconia have shown improved performance and reduced wear, leading to cost savings.
Furthermore, studies confirm that coatings incorporating zirconia reduce maintenance needs, contributing significantly to overall operational efficiency. This leads to extended service life and less frequent replacements, proving the value of including zirconia in coating formulations.
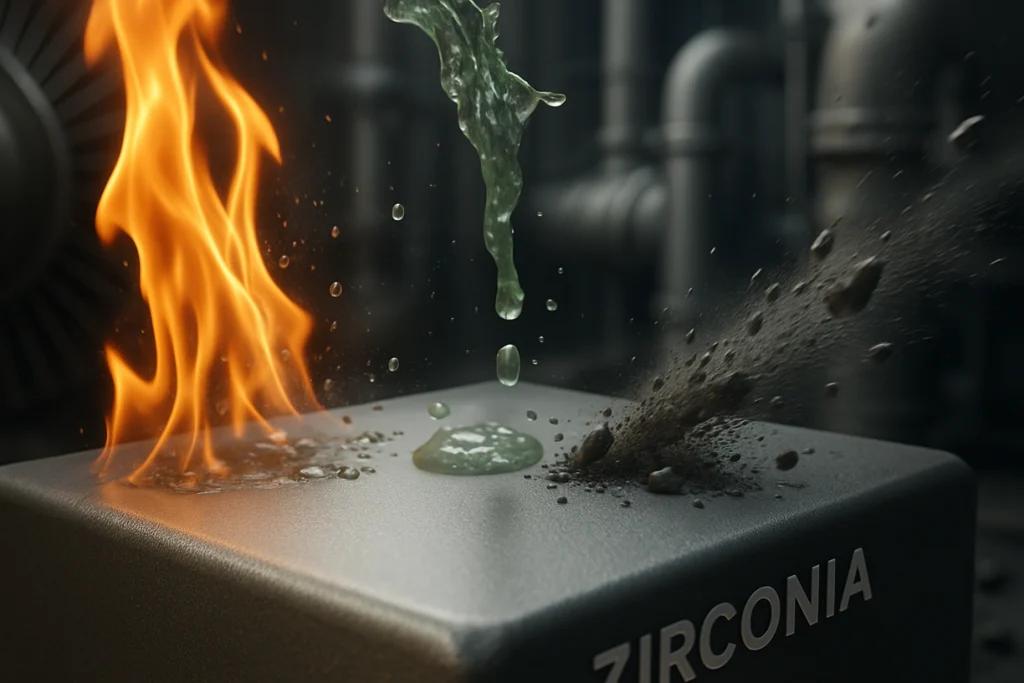
This image depicts the durability of zirconia coatings in harsh conditions, showcasing their long-lasting performance in various industries.
Duration of Coating Life | Before Zirconia | After Adding Zirconia |
---|---|---|
2 years | 60% | 90% |
5 years | 30% | 60% |
Benefits of Zirconia-Enhanced Durability
- Reduced delamination: Strong adhesion minimizes surface peeling.
- Extended service life: Long-lasting coatings lead to less frequent replacements.
- Lower maintenance: Coatings require less upkeep, reducing operational downtime.
- Resilience against environmental factors: Better performance under extreme conditions.
What Role Does Zirconia Powder Play in Wear Resistance?
Wear resistance is vital for coatings used in various demanding applications, from machinery parts to consumer goods. Zirconia powder significantly enhances wear resistance due to its superior hardness and toughness. When incorporated into coatings, it forms a protective layer that helps prevent material loss during operation.
Zirconia’s ability to disperse stress throughout the coating also plays a crucial role. When impact or abrasion occurs, the energy is distributed evenly, reducing the likelihood of localized wear or failure.
In practical scenarios, such as in industrial machinery, coatings featuring zirconia have demonstrated a marked decrease in material degradation. For example, rotating equipment lubricated with zirconia-enhanced coatings showed extended service intervals compared to those with conventional coatings.
Collectively, these performance benefits translate into lower operational costs and increased reliability for manufacturers. Products coated with zirconia not only survive longer but also require less frequent maintenance, leading to significant long-term savings.
Application Area | Coating Type | Wear Resistance Improvement |
---|---|---|
Industrial Machinery | Standard Coating | 30% |
Industrial Machinery | Zirconia-Enhanced Coating | 75% |
Key Advantages of Zirconia in Wear Resistance:
- Increased lifespan of coated parts
- Consistent performance under stress
- Reduced operating costs due to lower maintenance
- Enhanced safety through reliable coatings
Can Zirconia Powder Enhance Thermal Stability in Coatings?
Heat resistance is paramount in many applications, especially those exposed to extreme temperatures. Here, zirconia powder really shines. Its thermal stability ensures that coatings maintain their performance characteristics even when subjected to heat.
When coatings contain zirconia, they can withstand sudden temperature changes without cracking or deteriorating. This stability is essential for parts in applications like aerospace engines, where high temperatures are commonplace.
Studies have shown that coatings with zirconia maintain their properties under extended thermal stress. For instance, coatings that were subjected to high heat cycles retained their adhesion and hardness, demonstrating the efficacy of zirconia in challenging environments.
Manufacturers benefit from reduced failures and longer service intervals when using zirconia-enhanced coatings. This translates into lower replacement and maintenance costs, ensuring that businesses can run more efficiently over time.
Temperature Range (°C) | Coating Type | Performance Retention |
---|---|---|
500 | Standard Coating | 60% |
500 | Zirconia-Enhanced Coating | 85% |
Benefits of Enhanced Thermal Stability:
- Longer-lasting coatings under extreme heat
- Consistent performance even during temperature fluctuations
- Lower risk of material failure
- Greater efficiency in high-temperature applications
How Does Zirconia Powder Affect Coating Aesthetics?
Coatings are not just about performance; aesthetics also matter. Using zirconia powder can improve the look and feel of coatings. One of the main benefits is its ability to provide a smooth and glossy finish, which is attractive for consumer and industrial applications alike.
When incorporated, zirconia facilitates a more even color distribution and enhances the depth of color. This is particularly important in industries where visual appeal is a consideration—such as automotive coatings and consumer electronics.
Moreover, zirconia coatings often exhibit better color stability over time, resisting fading and maintaining their original appearance even in challenging environments. This aesthetic resilience can significantly influence a buyer’s perception and customer satisfaction.
In summary, zirconia powder not only enhances the functional properties of coatings but also elevates their visual quality, making products more appealing to end-users.
Coating Finish Type | Gloss Level | Color Stability (Months) |
---|---|---|
Standard Coating | Moderate | 12 |
Zirconia-Enhanced Coating | High | 36 |
Aesthetic Advantages of Zirconia-Coated Products:
- Improved gloss and shine on surfaces
- Depth of color that enhances visual appeal
- Resistance to fading for longer-lasting beauty
- Attractive finishes that increase marketability
What Are the Cost Implications of Using Zirconia Powder?
Implementing zirconia powder in coating formulations does present a cost consideration. However, understanding the full picture can clarify its value. The initial investment may be higher than traditional materials, but the long-term benefits often outweigh these costs.
One of the primary advantages is increased durability and reduced maintenance needs. Coatings with zirconia last longer, which means less frequent replacements and lower downtime for equipment.
To illustrate, consider the total cost of ownership (TCO) for coated parts in a manufacturing environment. While the upfront price of zirconia powder may be higher, the extended lifespan and reduced operational costs can result in significant savings over time.
Understanding the economics involves not just the sticker price but also the value proposition over the lifespan of the product. When discussing budgets, it’s important for companies to consider both immediate costs and long-term benefits.
Cost Analysis | Without Zirconia | With Zirconia |
---|---|---|
Upfront Coating Cost | $5,000 | $7,000 |
Maintenance Costs (1-year) | $3,000 | $500 |
Total Cost (1 Year) | $8,000 | $7,500 |
Cost Considerations for Zirconia Powder:
- Upfront costs versus long-term savings
- Reduced operational downtime due to fewer replacements
- Improved reliability leading to decreased warranty claims
- Overall lower lifecycle costs of coated products
How Can Zirconia Powder Be Incorporated into Formulations?
Incorporating zirconia powder into coatings requires a clear understanding of the formulation process. It is crucial to have precise mixing techniques to achieve optimal distribution.
Typically, zirconia powder should be blended with other components to ensure uniformity. This can include resins, solvents, and other additives. Achieving the right particle size is also essential; the finer the zirconia powder, the better its effects on the coating’s overall properties.
Quality control measures during formulation are paramount. Testing batches for consistency can help detect any issues in the formulation early on. Companies should also focus on establishing standard operating procedures to maintain quality across different production runs.
This careful approach to incorporating zirconia powder not only guarantees better technical performance but also instills confidence in the reliability of the final product.
Mixing Technique | Description | Importance |
---|---|---|
Homogeneous Mixing | Even distribution of zirconia | Crucial for consistent performance |
Testing for Consistency | Batch testing and assessment | Ensures product quality |
Particle Size Selection | Fine particles for optimal effect | Improves coating properties |
Best Practices for Incorporating Zirconia Powder:
- Use precision mixing equipment for uniform distribution
- Conduct thorough testing of product batches
- Maintain detailed documentation of formulation procedures
- Regularly train staff on the best practices for mixing and quality control
What Industries Benefit From Zirconia Powder in Coatings?
Zirconia powder finds applications across various industries due to its unique properties. Automotive manufacturers use zirconia-enhanced coatings to improve the durability of components subject to harsh conditions, such as engine parts and gear systems.
In the aerospace sector, where safety and reliability are paramount, coatings with zirconia help protect critical parts from extreme conditions. Similarly, the machinery industry benefits by applying zirconia coatings to wear-prone parts, leading to extended operational life.
Consumer goods producers also recognize the aesthetic and performance benefits of zirconia. Home appliances often feature coatings with zirconia for not just durability but also attractive finishes.
The versatility and adaptability of zirconia powder allow for innovations in product design and surface treatment, driving continued interest across these sectors.
Industry | Application Example | Benefits |
---|---|---|
Automotive | Engine Blocks | Increased durability |
Aerospace | Aircraft Engine Parts | Enhanced thermal stability |
Machinery | Industrial Components | Improved wear resistance |
Consumer Goods | Kitchen Appliances | Attractive finishes |
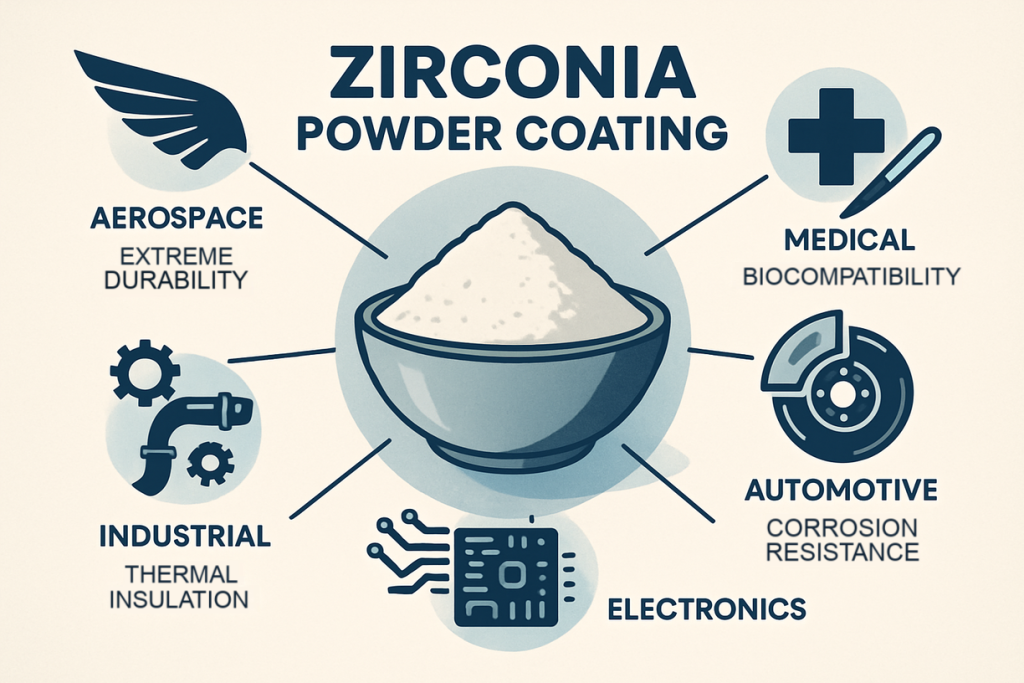
This image highlights various industries that benefit from zirconia powder coatings, emphasizing their applications and advantages.
Industries Leveraging Zirconia Benefits:
- Aerospace for critical component protection
- Automotive for enhanced performance and longevity
- Medical devices requiring biocompatibility
- Electronics for improved durability and aesthetics
What Are the Environmental Considerations of Zirconia Powder?
As industries work toward sustainability, the environmental impact of materials used in coatings must be considered. Zirconia powder has certain characteristics that make it an attractive option from an ecological standpoint.
First, its durability means that products coated with zirconia do not need to be replaced as frequently, reducing waste. Additionally, zirconia can be sourced through sustainable mining practices, minimizing the ecological footprint.
Recycling possibilities also exist, allowing for the reprocessing of zirconia materials. These factors contribute positively to the product lifecycle, aligning with increasing regulations and consumer expectations for sustainability.
In summary, zirconia’s advantages can fit well within a broader environmental strategy for manufacturers, offering both performance and responsibility.
Environmental Impact | With Standard Coatings | With Zirconia Coatings |
---|---|---|
Product Lifespan | 5 years | 10 years |
Waste Generation | High | Low |
Recyclability | Limited | Moderate |
Environmental Benefits of Using Zirconia Powder:
- Reduction of material waste over time
- Contributions to sustainability goals
- Potential for recycling reuse in various applications
- Minimized environmental impact from enhanced product longevity
How Does the Future Look for Zirconia Powder in Coatings?
Looking ahead, the prospects for zirconia powder in advanced coatings appear bright. As technology evolves, the demand for high-performance materials like zirconia will continue to grow. Industries are increasingly seeking solutions that offer durability, wear resistance, and aesthetics—all areas where zirconia excels.
Innovations in processing and formulation techniques are likely to enhance the performance benefits of zirconia powder further. Research into optimizing its incorporation into coatings can pave the way for even more effective applications.
By staying ahead of these trends, manufacturers can position themselves to leverage zirconia powder in ways that meet both current and future challenges in their respective markets. In this context, the continued adoption of zirconia will likely contribute to advancements across many industries.
Future Trends | Current Focus | Expected Development |
---|---|---|
Performance Enhancement | Durability | Enhanced properties |
Sustainability | Reduced waste | Recycling advancements |
Innovation | New applications | Evolving technologies |
Conclusion
This article detailed how zirconia powder enhances advanced coating formulations, addressing durability, wear resistance, thermal stability, and aesthetics. By incorporating zirconia, manufacturers can achieve longer-lasting products, resulting in significant cost savings. Trust Global Industry with your coating formulations to unlock your potential for greater reliability and performance. Visit our website or contact us to explore how we can help you integrate zirconia into your processes effectively.
FAQ
Q1: What makes zirconia powder unique compared to other additives?
Zirconia powder is distinguished by its exceptional hardness, which is higher than many traditional materials used in coatings, making it effective for enhancing wear resistance and extending product lifespan. Additionally, its chemical inertness means that it does not react with other substances in the coating, ensuring stability and reliability in various environments. Furthermore, zirconia exhibits excellent thermal stability, allowing it to perform effectively under high temperatures without degrading, a critical feature for applications in industries such as aerospace and automotive.
Q2: Is zirconia powder safe for all applications?
Yes, zirconia powder is generally considered safe for use in a variety of applications. However, as with any material, safety can depend on the specific context of its use. In industries like healthcare and food processing, thorough testing must be conducted to ensure compliance with strict safety and regulatory standards. Manufacturers must carefully evaluate the intended application, particularly regarding biocompatibility for medical uses. Ongoing research continues to assess the long-term effects and safety of zirconia in novel applications.
Q3: How does zirconia powder influence the coating production process?
The introduction of zirconia powder into the coating formulation requires specific processing conditions to achieve optimal dispersion and performance. It is necessary to use precise mixing techniques and equipment to ensure that the zirconia particles are evenly distributed throughout the coating mixture. The particle size of zirconia can also significantly impact the coating’s final properties; finer particles may enhance performance but can be more challenging to incorporate effectively. Moreover, quality control measures such as batch testing and consistency checks must be implemented throughout the production process to maintain uniformity and reliability in the final product.
Q4: What challenges might arise when using zirconia powder?
While zirconia powder offers numerous advantages, challenges can include higher upfront costs compared to traditional materials, which may impact small manufacturers’ decision-making processes. Additionally, achieving a homogenous blend can be complex, requiring specialized equipment and skilled personnel. It’s also essential to develop suitable mixing processes that prevent agglomeration of zirconia particles, which can negate some of its benefits. Finding a balance between performance enhancements and production costs is crucial for manufacturers looking to adopt zirconia powder in their formulations.
Q5: Why should I consider zirconia powder for advanced coatings?
Considering zirconia powder for advanced coatings is sensible due to its proven performance benefits. It enhances durability, wear resistance, and thermal stability, thus contributing to longer-lasting coatings that can withstand harsh environments. This improved performance can also lead to fewer maintenance requirements, which translates to cost savings in the long term. Moreover, with growing industry demands for high-performance and aesthetically appealing coatings, zirconia’s ability to enhance both functionality and visual appeal makes it a valuable additive in creating competitive products across multiple sectors. Incorporating zirconia powder positions companies to meet evolving market needs effectively.