The use of zirconia powder in ceramic manufacturing has garnered attention for its potential to enhance performance significantly. Many professionals in the ceramics industry face challenges related to strength, durability, and thermal stability. This article aims to address these concerns by examining the benefits of zirconia powder, which can ultimately transform the manufacturing process and product quality. We will explore how zirconia powder improves performance and offer practical insights based on industry expertise. With well-researched information and real-world examples, this article serves as a reliable resource for decision-makers in the ceramics field.
How Does Zirconia Powder Enhance Ceramic Manufacturing?
Zirconia powder is widely recognized for its role in improving the characteristics of ceramics. First, it is essential to understand what zirconia is. Zirconia, or zirconium dioxide, is a ceramic material renowned for its hardness and resistance to wear. When added to ceramic formulations, zirconia powder contributes to superior mechanical properties.
Over time, zirconia has evolved in its applications within the ceramics industry. Initially used in dental ceramics, its advantages have been recognized and extended to various sectors. For example, zirconia’s ability to sustain high temperatures makes it suitable for manufacturing thermal barriers in aerospace components.
The key characteristics of zirconia powder include:
- High mechanical strength: Zirconia exhibits remarkable toughness, making it less prone to fracture.
- Wear resistance: This powder resists abrasion, prolonging the lifespan of ceramic products.
- Thermal stability: Zirconia maintains its properties even at elevated temperatures, making it ideal for extreme environments.
These capabilities position zirconia powder as an essential ingredient in modern ceramic manufacturing processes, meeting increasingly demanding performance standards.
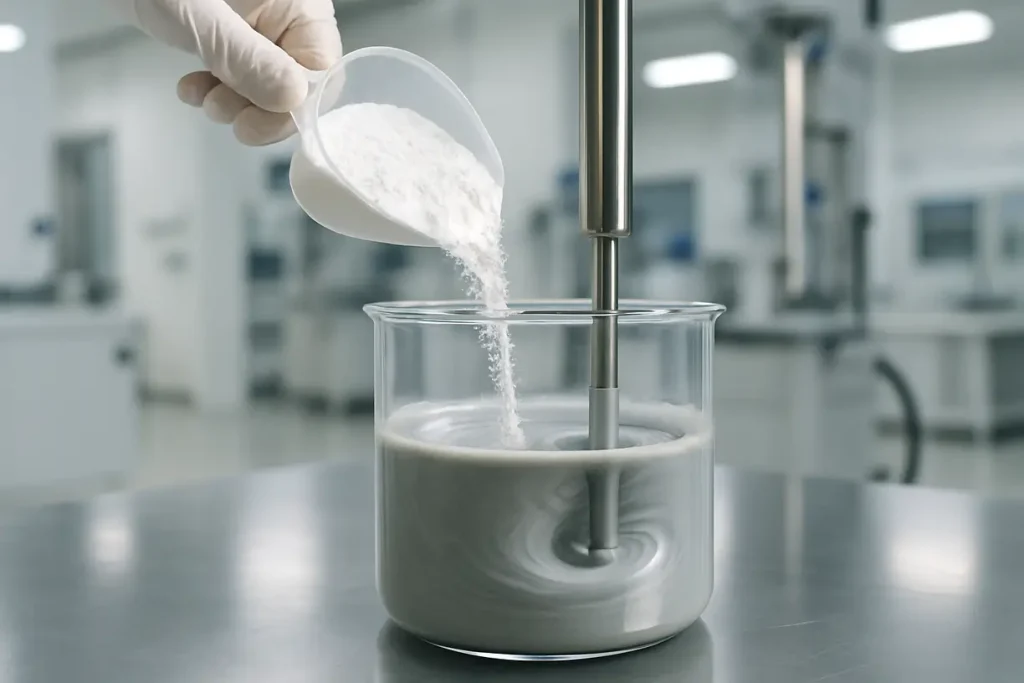
Zirconia powder being integrated into ceramic mixtures for improved properties.
What Performance Benefits Does Zirconia Powder Offer?
The incorporation of zirconia powder into ceramic materials yields numerous performance benefits that are crucial for industries where ceramic products must withstand harsh conditions.
First and foremost, mechanical strength is one of the most significant improvements that zirconia provides. Zirconia enhances the hardness of ceramics, making them ideal for applications that require impact resistance. For instance, in the automotive sector, components like brake pads and engine parts benefit from zirconia’s ability to resist deformation and fracture. This is particularly beneficial in high-stress environments where materials are subject to rapid changes and forces.
Moreover, zirconia’s wear resistance is another standout feature. In practical terms, this means that tools and components treated with zirconia powder exhibit significantly less wear over time than those without it. For example, ceramic cutting tools that incorporate zirconia maintain their sharpness and effectiveness longer, leading to fewer replacements and reduced downtime in manufacturing processes. This property translates into lower maintenance costs, as businesses can rely on longer-lasting tools and equipment.
Another critical performance aspect is thermal stability. Zirconia can endure intense heat, ensuring that ceramic products retain their integrity in environments exposed to fluctuations in temperature. This is especially essential in applications such as furnace linings or cutting tools used in high-heat scenarios. The ability to withstand elevated temperatures without degrading adds an extra layer of reliability to products used in such demanding conditions.
In addition, zirconia contributes to improved resistance to chemical corrosion. For industries that involve exposure to aggressive chemicals, having materials that retain their properties without being compromised is vital. Zirconia’s chemical inertness helps maintain the performance and lifespan of ceramic products, further enhancing their usability in various applications.
To put it simply, zirconia powder offers profound benefits that address specific performance challenges faced by manufacturers. By utilizing zirconia in their product formulations, businesses can produce stronger, more durable, and thermally stable ceramic products. Not only do these enhancements improve functional performance, but they also help meet increasingly demanding standards in various industries, ultimately leading to greater customer satisfaction and market success.
How Does Zirconia Powder Affect Processing Techniques?
Integrating zirconia powder into ceramic manufacturing processes necessitates adjustments in processing techniques.
To begin with, zirconia affects sintering, a critical stage in ceramic production. During this process, zirconia powder requires specific temperature profiles to optimize bonding between particles. Typical firing temperatures for zirconia-containing ceramics can range from 1,400°C to 1,600°C.
Furthermore, zirconia impacts shaping methods. Traditional ceramic forming techniques such as slip casting or extrusion may need specific modifications to accommodate the properties of zirconia. Incorporating the right additives can help achieve the desired flowability and moldability, ensuring uniform parts.
When it comes to glazing applications, zirconia has a role to play as well. It can be included in glazes to increase their durability and aesthetic appeal. Here, manufacturers have reported improved resistance to scratches and stains, enhancing the product’s overall quality.
Here is a table summarizing key processing adjustments needed with zirconia powder integration:
Processing Technique | Adjustment Needed | Impact |
---|---|---|
Sintering | Higher firing temperatures for optimal bonding | Improved strength and integrity |
Shaping | Modifications to additives for flowability | Uniform parts with fewer defects |
Glazing | Inclusion in glazes for added durability | Enhanced resistance to scratches and stains |
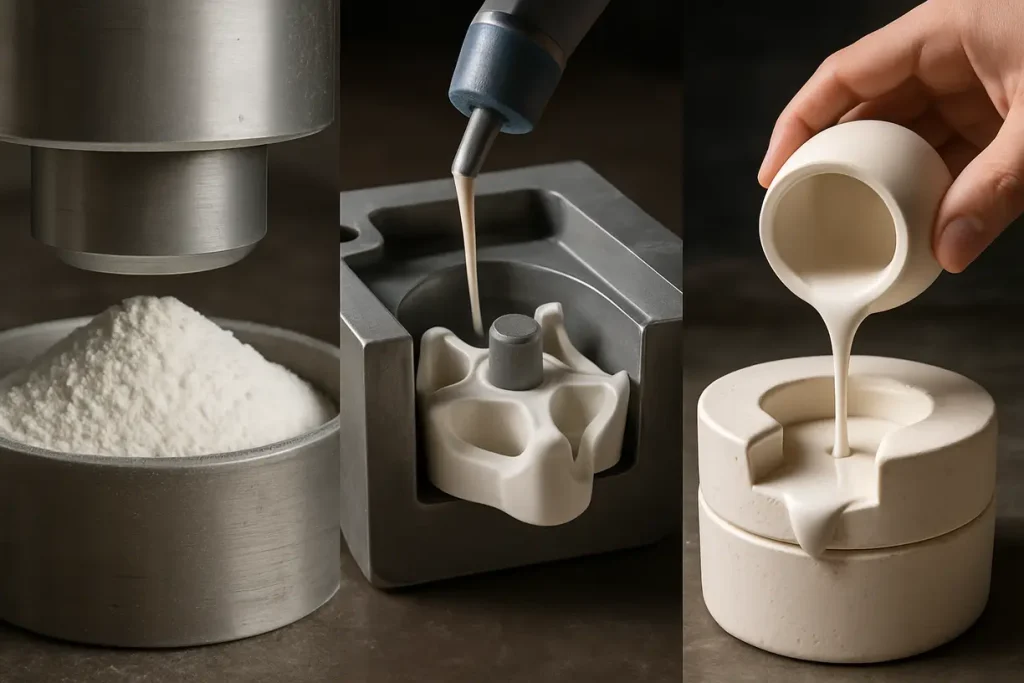
Different ceramic shaping techniques affected by zirconia’s properties.
These adjustments underscore the necessity for manufacturers to develop tailored strategies when incorporating zirconia powder into their processes.
What Industries Benefit from Zirconia-Enhanced Ceramics?
Zirconia-enhanced ceramics are making waves across various industries due to their unique properties. The medical field, for example, benefits significantly from zirconia’s biocompatibility and strength. Dental applications use zirconia in crowns and bridges, providing both aesthetic and functional value.
In the aerospace sector, zirconia’s thermal stability is invaluable. It is often utilized in turbine engines where materials must withstand extreme temperatures while maintaining structural integrity.
Additionally, the consumer electronics industry leverages zirconia in manufacturing components that require high durability. For instance, zirconia parts can be found in smartphone casings and wearables, where they deliver both safety and performance.
In summary, several industries reap the rewards of zirconia-enhanced ceramics, confirming their versatility and crucial role in modern applications.
How Do Performance Improvements Translate to Cost Savings?
The performance enhancements provided by zirconia powder extend beyond product quality; they also lead to significant cost savings over time.
To illustrate, when buildings use zirconia-enhanced tiles, the durability leads to lower replacement frequency. There are reduced maintenance costs, contributing to a favorable return on investment.
Performance efficiency plays a crucial role, too. With tools and components exhibiting greater wear resistance, manufacturing processes become more streamlined. For example, ceramic cutting tools that incorporate zirconia maintain sharpness longer, allowing for extended operational periods without interruptions.
Moreover, the overall durability of products translates to fewer warranty claims. Companies spend less on post-sale support and can allocate resources to other areas, thus improving their bottom line.
A table below summarizes the impact of zirconia on cost savings:
Benefit | Cost Implication |
---|---|
Reduced maintenance | Lower frequency of replacements leads to savings |
Increased operational efficiency | Fewer disruptions in production save time |
Decreased warranty claims | Less spending on product support lowers expenses |
These tangible cost-saving benefits highlight the financial wisdom of integrating zirconia powder into manufacturing practices.
What Are the Challenges of Using Zirconia Powder?
Despite the clear advantages of zirconia powder, there are notable challenges that manufacturers should consider.
One primary concern is cost. Raw zirconia materials can be relatively expensive compared to other materials. For budget-conscious manufacturers, this can pose a barrier to entry when considering zirconia for production.
Processing difficulties also present challenges. Zirconia can be tricky to work with due to its specific requirements regarding sintering temperatures and environmental conditions. Proper calibration of equipment and adaptations to current manufacturing processes are often necessary, adding time and complexity to the operations.
Furthermore, quality control is vital. Variability in zirconia sources can lead to inconsistencies in material properties. That means manufacturers must implement stringent quality assessments to ensure a steady supply of high-quality zirconia.
The table below outlines the challenges and potential solutions for manufacturers integrating zirconia powder:
Challenge | Description | Solution |
---|---|---|
High material costs | Raw zirconia can be expensive | Explore alternative sources or bulk purchasing |
Processing complexity | Specific conditions required for optimal results | Invest in equipment and training |
Quality variability | Inconsistent properties among suppliers | Establish quality checks and trusted suppliers |
Addressing these challenges head-on allows for effective integration of zirconia powder while minimizing potential setbacks.
How Can Companies Source Quality Zirconia Powder?
Finding reliable sources of quality zirconia powder is crucial for manufacturers seeking to maintain high standards.
When selecting suppliers, companies should prioritize those with established reputations in the ceramics industry. Researching supplier backgrounds and client testimonials can provide insight into their reliability.
Additionally, certifications play a significant role. Suppliers who meet specific quality assurance standards, such as ISO certifications, demonstrate a commitment to product quality. Companies should inquire about a supplier’s certifications before making purchasing decisions.
Logistics is another critical aspect. Timely delivery and proper handling of zirconia powder ensure that manufacturing disruptions are minimized. Evaluating a supplier’s logistics processes can aid in selecting the right partner.
Here’s a table summarizing key considerations when sourcing zirconia powder:
Consideration | Description |
---|---|
Supplier reputation | Research background and client reviews |
Quality certifications | Verify ISO or similar industry certifications |
Logistics | Assess delivery times and handling protocols |
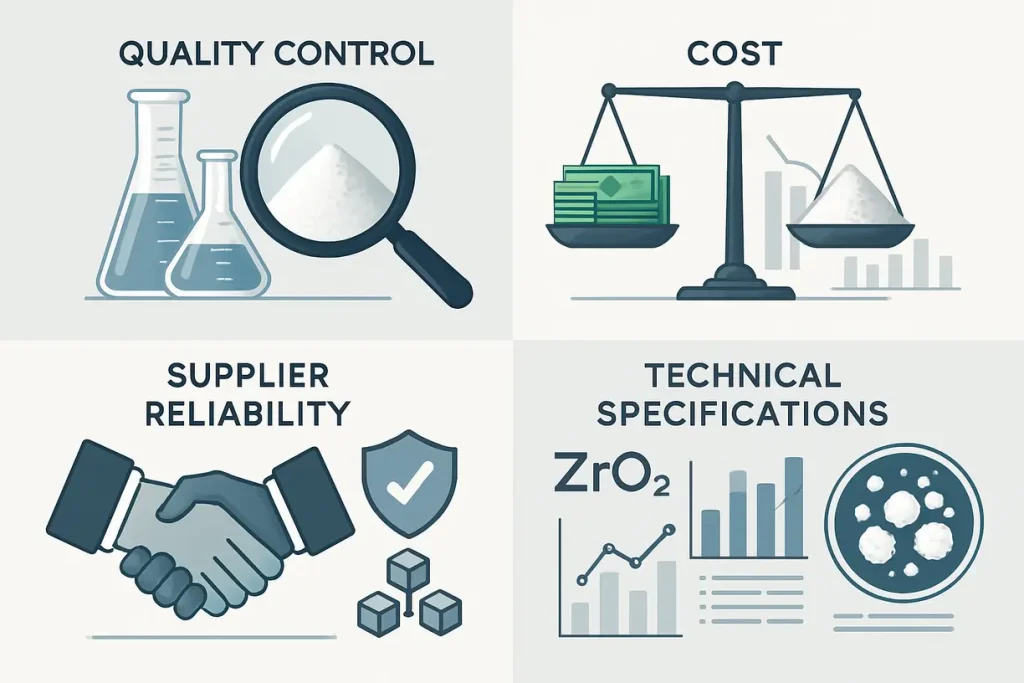
Key factors to consider when sourcing zirconia powder for manufacturing.
These sourcing strategies can significantly impact the effectiveness of zirconia integration into manufacturing processes.
What Innovations Are Emerging in Zirconia Powder Applications?
Research and technology are driving exciting innovations in the use of zirconia powder. Ongoing studies explore new formulations that can enhance the properties of zirconia further.
One emerging area is the hybridization of zirconia with other ceramic materials, aiming to improve functionality further. These hybrid materials may offer enhanced thermal and mechanical properties, expanding their applications even further.
Another area of innovation is in 3D printing, where zirconia powder is being explored for additive manufacturing processes. Companies are developing new techniques to utilize zirconia effectively in 3D-printed components, reducing waste and potentially lowering production costs.
Lastly, advancements in nanotechnology allow for more refined applications of zirconia powder, potentially leading to even better material properties and functions.
The following table outlines significant innovations within the zirconia landscape:
Innovation | Description |
---|---|
Hybrid materials | Combining zirconia with other ceramics for better performance |
Additive manufacturing | Exploring zirconia for 3D printing applications |
Nanotechnology | Utilizing nanostructured zirconia for advanced properties |
These innovations highlight the ongoing evolution of zirconia powder in ceramics and provide opportunities for manufacturers to stay at the forefront of technology.
How Can Companies Implement Zirconia Powder Effectively?
To effectively integrate zirconia powder, companies must follow specific steps that streamline the transition while maximizing benefits.
First, companies should conduct a thorough assessment of their current processes. This assessment will identify areas where zirconia can add value, ensuring targeted improvements.
Training staff is also crucial. Employees need to understand the unique properties and handling requirements of zirconia powder. Regular workshops can keep staff updated on best practices for processing and quality checks.
Building partnerships with reliable suppliers can also make a significant difference. Collaborative relationships with lookout suppliers can help streamline procurement and ensure quality materials.
Here’s a table summarizing implementation steps for zirconia powder integration:
Step | Description |
---|---|
Process assessment | Identify areas for zirconia application |
Staff training | Educate employees on handling and performance |
Supplier partnerships | Collaborate for consistent quality and reliability |
These implementation strategies help organizations transition smoothly and start reaping the benefits of zirconia powder.
What Feedback Do Industry Experts Offer on Zirconia Use?
Industry experts provide valuable insights based on their experience with zirconia powder in ceramics.
Many practitioners emphasize the importance of comprehensive testing before scaling up production. Small-scale tests can identify potential issues, validating performance claims against real-world use.
Experts also recommend regularly revisiting supplier relationships. Consistent quality checks and modifications can lead to improved outcomes and cost efficiencies.
Case studies from companies utilizing zirconia effectively further illustrate the benefits. For instance, a prominent medical device manufacturer reported a significant reduction in product failures after switching to zirconia-enhanced materials.
The following table showcases expert feedback on utilizing zirconia powder:
Feedback Point | Description |
---|---|
Comprehensive testing | Essential for validating material performance |
Supplier relationship reviews | Continually assess suppliers for consistent quality |
Case studies | Document successes and challenges for improved practices |
These insights affirm the strategic value of implementing zirconia powder in manufacturing while emphasizing ongoing evaluation and adjustment.
In summary, the integration of zirconia powder offers numerous benefits to ceramic manufacturing. From enhancing performance characteristics to achieving substantial cost savings, zirconia plays a vital role in various industries. Notably, companies can realize significant improvements in product quality, durability, and operational efficiency.
For businesses looking to implement these advantages, Global Industry recommends taking a strategic approach, focusing on quality sourcing, staff training, and effective supplier partnerships. By building these competencies, companies can remain leaders in the ceramics field.
FAQ Section
Q1: What is zirconia powder used for in ceramics?
Zirconia powder is primarily used as an additive in ceramic formulations to improve their physical properties. Its incorporation significantly enhances the mechanical strength, toughness, wear resistance, and thermal stability of ceramics. This makes zirconia powder particularly valuable in applications ranging from dental ceramics, where aesthetic qualities and durability are essential, to industrial applications such as cutting tools and furnace linings that require materials capable of withstanding harsh conditions.
Q2: Are there specific industries that benefit most from zirconia powder?
Absolutely! Several industries significantly benefit from zirconia-enhanced ceramics. The medical field frequently employs zirconia in dental applications for crowns and bridges due to its biocompatibility and strength. The aerospace sector utilizes zirconia in turbine engines, where materials must endure extreme temperatures without fail. Additionally, the electronics industry adopts zirconia for manufacturing durable components used in smartphones and wearables, benefiting from its resistance to wear and aesthetic appeal. These examples illustrate how zirconia’s unique properties cater to various high-performance requirements.
Q3: What are the main challenges when using zirconia powder?
While zirconia powder offers numerous advantages, there are challenges that manufacturers must consider. One of the primary challenges is sourcing high-quality zirconia, as variations in material purity can affect the final properties of the ceramic products. Additionally, processing zirconia can present difficulties, as it requires specific sintering conditions and adjustments in shaping techniques to achieve optimal results. Furthermore, ensuring rigorous quality control throughout the manufacturing process is essential, as inconsistencies in material properties can lead to performance issues. Addressing these challenges is vital for maximizing the benefits of zirconia in production.
Q4: How does zirconia powder translate to cost savings for manufacturers?
The incorporation of zirconia powder can lead to significant cost savings in multiple ways. Firstly, the enhanced durability and wear resistance of zirconia-enabled products reduce the frequency of replacements and maintenance, lowering long-term costs for manufacturers. Additionally, the improved efficiency of tools and components can streamline production processes, resulting in greater productivity and reduced downtime. Finally, the longevity of zirconia-enhanced products often leads to lower warranty claims and customer service costs, as these products are less likely to fail under normal operating conditions. Overall, zirconia contributes to a favorable return on investment.
Q5: What trends are emerging in the use of zirconia powder?
Emerging trends in the use of zirconia powder include the exploration of hybrid materials that combine zirconia with other ceramics to achieve even greater performance enhancements. Researchers are also investigating the application of zirconia in additive manufacturing and 3D printing, which opens new possibilities for customized components and reduction of material waste. Additionally, advancements in nanotechnology are paving the way for refined zirconia applications, potentially leading to improved properties such as higher strength and lighter weights, further broadening its utility across industries.