When it comes to selecting materials for specific applications, understanding the technical properties of zirconia powder is vital for professionals in various industries. Many decision-makers face challenges such as identifying quality standards and understanding their implications for performance. This article addresses these concerns directly by detailing the essential technical properties that define high-quality zirconia powder. By doing so, we provide clear insights that allow you to make informed sourcing decisions. Trust that this comprehensive guide, backed by industry expertise, will equip you with the knowledge necessary to select the best materials for your needs.
What Are the Key Technical Properties of Zirconia Powder?
Zirconia powder, also known as zirconium dioxide, is renowned for its unique physical and chemical attributes. To start, it is crucial to understand the fundamentals of this substance. Zirconia is a white crystalline oxide, prized for its robust characteristics, making it suitable for a wide array of applications. Its unique properties stem from its tetragonal and cubic phases, allowing it to excel in both mechanical and thermal capacities.
Understanding the technical properties of zirconia powder helps gauge its quality and performance potential. Key features include:
- Strength: Zirconia exhibits high fracture toughness and strength, surpassing that of many conventional materials. Such attributes are essential for applications requiring durability under stress, such as in cutting tools and dental restorations.
- Thermal Stability: Zirconia boasts a high melting point of around 2700 degrees Celsius. This exceptional thermal stability means it can maintain its integrity in environments with extreme temperature fluctuations, making it ideal for furnace linings and thermal barrier coatings.
- Chemical Resistance: Zirconia is inert to many acids and bases. This characteristic ensures longevity in demanding environments, particularly in chemical processing and industrial applications, where other materials may degrade.
- Biocompatibility: In medical applications, zirconia is non-toxic and well-tolerated by the human body, which has led to its widespread use in dental implants and prosthetics.
To measure these properties, standard testing techniques apply. Test results can indicate purity, grain size, and crystal structure, all of which contribute to the zirconia’s functionality in specific applications.
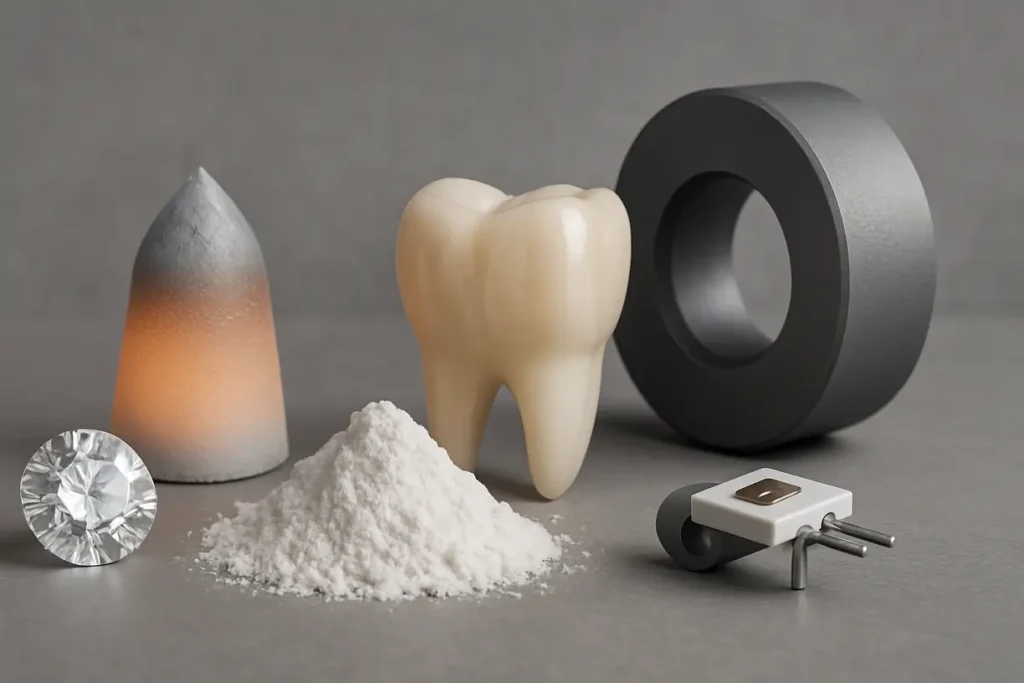
This image illustrates the important attributes of zirconia powder and its applications.
How Does Particle Size Affect Zirconia Quality?
When sourcing zirconia powder, the size of the particles plays a significant role in defining quality. Particle size impacts several crucial attributes that ultimately influence performance and manufacturing processes.
- Physical Properties: Smaller particles typically provide a larger surface area, which can enhance reactivity. This characteristic is essential for processes like sintering, where a larger surface area allows for better interparticle bonding and reduced pores in the final product.
- Mechanical Strength: The overall strength of zirconia can be heightened with finer particle sizes. In finer powders, stress can redistribute more evenly across particles, leading to enhanced fracture toughness. This means that products made from fine zirconia powder are less likely to crack or break under stress.
- Processing Behavior: The size of the particles also influences how easily the powder can be processed and shaped. Smaller and finer particles tend to compact better, leading to denser final products with uniform properties. This consistency is critical in industries like dental ceramics, where the precision of the finished product directly impacts performance and aesthetics.
Furthermore, applying techniques like laser diffraction can accurately measure particle size distribution, and thus manage the quality of zirconia powders used in specific applications effectively.
Important note: Always ensure you obtain accurate particle size measurements to avoid quality discrepancies in your final applications. Maintaining the desired particle size range allows for consistency in performance, making it easier to meet the specific requirements of various industries.
Property | Fine Particles | Coarse Particles |
---|---|---|
Surface Area | Higher | Lower |
Reactivity | Improved | Reduced |
Mechanical Strength | Enhanced | Weaker |
In summary, particle size is a critical parameter when selecting zirconia powder. Opting for the right particle size can lead to improvements in product performance, mechanical resilience, and processing efficiency, which are essential for high-quality end products.
Why Is Purity Critical in Zirconia Powder?
Purity is a significant parameter to consider when evaluating zirconia powders. It directly influences the material’s performance and reliability. High purity levels ensure that the material performs as expected in critical applications. Contaminated zirconia can lead to failures in products that rely on the material’s integrity.
When assessing purity, consider the following factors:
- Impurities: Contaminants can adversely affect mechanical properties, resulting in failure under stress. For instance, even small levels of impurities such as silica or metallic oxides can significantly reduce the strength and toughness of zirconia, rendering it unsuitable for high-performance applications like dental implants or engineering components.
- Effects on Processes: Impurities can also interfere with processing methods, leading to inconsistencies. During sintering, for instance, contaminants can cause unwanted phase transformations, affecting the final product’s density and microstructure.
- Testing Methods: Techniques such as X-ray fluorescence (XRF) and inductively coupled plasma (ICP) spectrometry can determine purity levels accurately. Conducting these tests pre- and post-production ensures that the material meets stringent quality standards.
- Applications and Consequences: In sectors such as dental ceramics, where biocompatibility is critical, high purity is not just advantageous—it is essential. Impurities could lead to adverse biological reactions, prompting product recalls and liability issues.
Maintaining high purity levels contributes not only to product performance but also to longevity through enhanced corrosion resistance. High-purity zirconia can exhibit long-term stability in harsh environments, making it suitable for applications where durability is key.
In summary, sourcing high-purity zirconia powder is pivotal for industries like dental ceramics and high-performance coatings. The ultimate goal is to ensure the material can withstand real-world challenges, providing peace of mind in critical applications.y zirconia powder is pivotal for industries like dental ceramics and high-performance coatings.
Purity Level | Mechanical Properties | Application Suitability |
---|---|---|
> 99.5% | Excellent | High-performance fields |
98.0% – 99.5% | Good | General usage |
< 98.0% | Poor | Limited applications |
What Role Do Crystal Structure and Phase Play?
The crystal structure and phases of zirconia significantly influence its property profile. Zirconia exhibits three major phases: monoclinic, tetragonal, and cubic. Each phase offers distinct properties that are crucial for its performance in various applications.
- Monoclinic Phase: This is the stable form at room temperature. While it has good mechanical properties, it tends to be less stable under high temperatures, undergoing a phase transformation that can lead to expansions and cracks.
- Phase Stability: The tetragonal and cubic phases provide excellent toughness and stability at high temperatures. However, they can convert to monoclinic under certain conditions, which can cause expansion and cracking.
- Identification Techniques: X-ray diffraction is a common method used to determine the phase composition of zirconia powder. This analysis can help predict performance based on the anticipated external conditions.
In applications requiring high thermal and mechanical performance, selecting zirconia with the appropriate phase composition is paramount. The right choice can lead to improved functionality in high-temperature settings, such as turbines or furnace linings.
Phase Type | Temperature Stability | Applications |
---|---|---|
Monoclinic | Low | Ceramics |
Tetragonal | Medium | Bearings, Dental |
Cubic | High | Oxygen sensors |
How Does Density Influence Performance?
The density of zirconia powder is another significant factor in defining its quality. Higher density generally signifies better performance characteristics.
- Mechanical Strength: Higher density powders typically exhibit enhanced mechanical properties. They resist deformation and provide better cushioning in high-stress applications.
- Processing Efficiency: The density affects how well the powder can be processed. Denser powders can lead to stronger sintered products.
To measure density, techniques like Archimedes’ principle or gas pycnometry can provide insights into the material’s compactness. When sourcing zirconia, checking the density can offer valuable hints about its usability in demanding applications.
Density Range | Mechanical Strength | Use Suitability |
---|---|---|
> 6.0 g/cm³ | Excellent | High-performance uses |
5.5 – 6.0 g/cm³ | Good | General applications |
< 5.5 g/cm³ | Weak | Limited use cases |
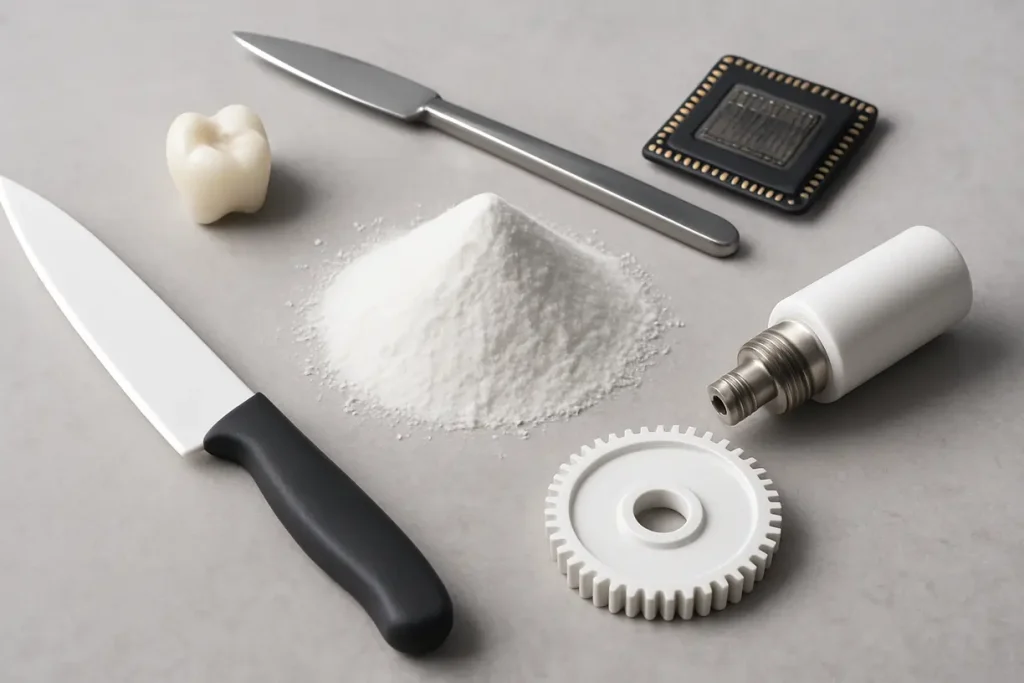
This image displays common applications of zirconia powder across various industries.
What Is the Significance of Mechanical Strength?
Mechanical strength stands out as a prime attribute of zirconia powder. It encompasses several aspects including tensile strength, compressive strength, and toughness.
- Tensile Strength: This property measures how well a material can withstand pulling forces. For zirconia, high tensile strength correlates with greater longevity in load-bearing applications.
- Compressive Strength: This indicates the resistance to crushing forces. Zirconia is known for its impressive compressive strength, making it suitable for heavy-duty applications.
- Toughness: The ability to absorb energy before fracturing is crucial. Zirconia’s toughness makes it a preferred choice in applications subjected to repeated loading.
Evaluating mechanical strength typically involves standard testing methods such as bending tests. The results allow manufacturers to ascertain the material’s durability in real-world applications. Understanding these strength parameters not only helps in material selection but also influences design choices for components exposed to various types of stresses.
Property | Strength Level | Application Example |
---|---|---|
High Tensile Strength | > 800 MPa | Dental implants |
High Compressive Strength | > 1000 MPa | Industrial components |
High Toughness | > 10 MPa·m^1/2 | Wear-resistant coatings |
How Do Thermal Properties Impact Application?
Zirconia’s thermal properties are essential for its application in high-temperature environments. The material’s thermal stability and conductivity determine its functionality in specific scenarios.
- Thermal Conductivity: Zirconia typically has low thermal conductivity, making it an excellent insulator. This property is especially vital in applications such as thermal barriers in gas turbines.
- Thermal Shock Resistance: Zirconia can withstand rapid temperature changes without cracking. This capability is crucial for operations in environments subject to extreme temperature variations.
Testing for thermal properties often involves thermal conductivity measurements and thermal cycling tests. Understanding these properties helps industries make informed choices for applications needing high thermal resistance.
Thermal Property | Value | Application Suitability |
---|---|---|
Thermal Conductivity | Low (~2.5 W/m·K) | Insulating layers |
Maximum Temperature Tolerance | Up to 2000°C | Aerospace components |
Why Should You Consider Surface Area and Morphology?
Surface area and morphology directly affect the reactivity and overall performance of zirconia powder.
- Surface Area: A larger surface area can enhance reactivity and improve bonding in composite applications. This is particularly important in advanced ceramics and catalytic applications.
- Morphology: The shape and arrangement of particles influence how powders flow, pack, and interact chemically. Irregular shapes may provide better sintering behavior compared to spherical particles.
Evaluating these characteristics involves methods like BET surface area analysis. Such tests help assess how particle shapes and sizes impact end-user applications.
Morphology Type | Surface Area Influence | Use Applications |
---|---|---|
Irregular Particles | High Reactivity | Catalytic applications |
Spherical Particles | Moderate Reactivity | Dental ceramics |
What Effects Do Additives Have on Performance?
Using additives in zirconia powder can enhance its performance attributes significantly. Understanding these effects can help in optimizing product quality.
- Types of Additives: Common additives include stabilizers, which help maintain desired phases during processing, and dopants that enhance certain properties.
- Benefits: Additives can improve properties such as sintering behavior and mechanical strength. They can also mitigate phase transformation issues.
While they can provide valuable enhancements, it is critical to understand the potential downsides, such as increased costs or changes in the material properties. Always assess the trade-offs before introducing additives into your zirconia powder formulations.
Additive Type | Purpose | Effect on Zirconia |
---|---|---|
Stabilizers | Maintain phases | Reduce cracking |
Dopants | Improve properties | Enhance toughness |
How Do You Ensure Quality Control in Production?
Quality control is essential for maintaining high standards in zirconia powder manufacturing. Implementing robust quality assurance processes guarantees reliable performance across all applications.
- Quality Assurance Processes: Establishing strict protocols during production, including monitoring temperature and pressure conditions, is vital.
- Testing Protocols: Routine testing must be performed to assess mechanical, thermal, and chemical properties. Such measures ensure products meet or exceed industry standards.
- Certification: Obtaining certifications from recognized industry bodies adds credibility and reassures customers about the product’s quality.
Maintaining an emphasis on quality control not only fosters trust but also enhances customer satisfaction, ultimately leading to repeat business.
Quality Control Aspect | Importance | Implementation Method |
---|---|---|
Process Monitoring | Consistency | Automated controls |
Routine Testing | Compliance | Laboratory assessments |
Certification | Market Credibility | Third-party evaluations |
What Are Real-World Applications of High-Quality Zirconia Powder?
High-quality zirconia powder is versatile, finding a place in various industries. Its exceptional properties make it suitable for multiple applications, from industrial to medical uses.
- Ceramics: In dental applications, zirconia provides strong, aesthetically pleasing materials for crowns and bridges.
- Biotechnology: Zirconia is used as a material for implants and dental prosthetics. Its biocompatibility and mechanical strength make it ideal for these sensitive applications.
- Aerospace and Energy: The powder serves as a plasma-sprayed thermal barrier coating in turbines, protecting components against extreme temperatures.
Considering these applications helps industries assess the value of investing in high-quality zirconia powder.
Application Area | Example Products | Key Benefits |
---|---|---|
Dental Industry | Dental crowns | Aesthetically pleasing, durable |
Automotive | Engine components | High strength under load |
Aerospace | Thermal barriers | Heat resistance |
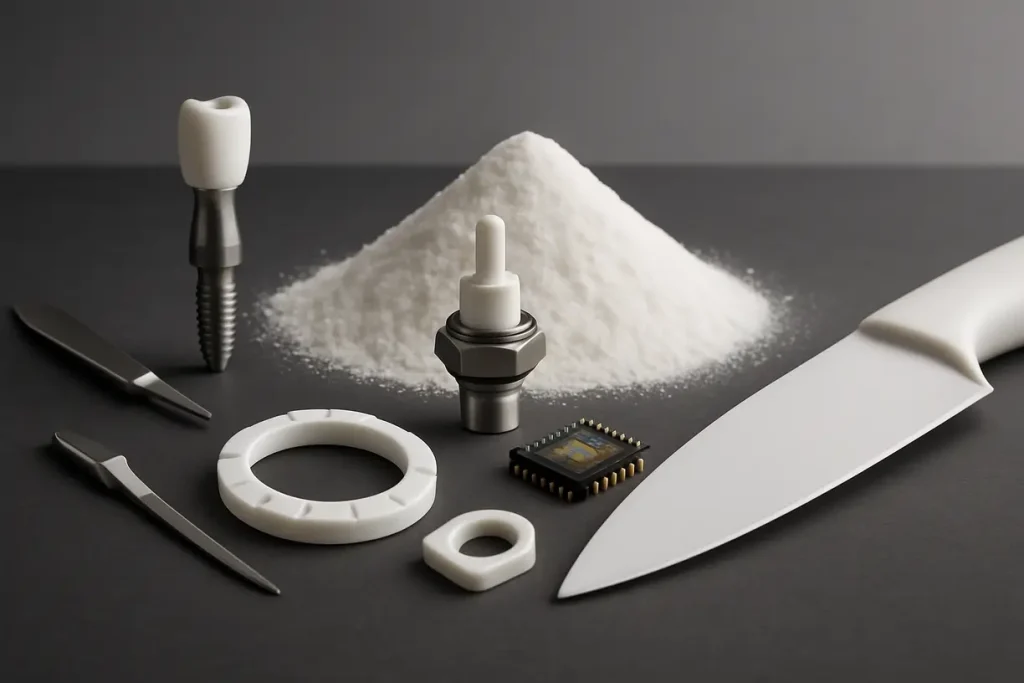
This image highlights the diverse applications of zirconia powder in various industries.
What Should Buyers Look for When Sourcing Zirconia Powder?
When sourcing zirconia powder, buyers must be diligent in assessing supplier quality. Several factors come into play:
- Supplier Qualifications: Look for suppliers with extensive experience and a proven track record in providing high-quality materials.
- Quality Assurance Certifications: Ensure the supplier holds certifications that reflect compliance with international standards.
- Product Specifications: Always request detailed specifications including purity levels, sintering outcomes, and performance metrics.
Doing thorough due diligence guarantees that you receive a product that meets your expectations and performs consistently in your applications.
Sourcing Consideration | Key Questions | Desired Outcomes |
---|---|---|
Supplier Experience | How long have they been in business? | Established credibility |
Certification | What quality standards do they meet? | Assured product quality |
Product Specifications | Can you provide properties data? | Informed purchasing decisions |
Conclusion
In this article, we explored the key technical properties that define high-quality zirconia powder. Insights into particle size, purity, crystal structure, density, and strength highlight the importance of these attributes for optimal performance. Regular assessment of these qualities ensures that you can select materials tailored to your specific needs. By choosing Global Industry as your supplier, you gain access to top-tier zirconia powder tailored for your applications. To take the next step, contact us today and find out how we can meet your material needs effectively.
FAQ Section
Q1: What industries use zirconia powder?
Zirconia powder is utilized across various industries, including ceramics, where it serves as a vital component in making high-performance ceramic tiles and tableware. In the dental industry, zirconia is employed for producing strong and aesthetically pleasing crowns, bridges, and orthodontic products. Additionally, it finds applications in electronics as a dielectric material, in automotive components for wear resistance, and in aerospace for thermal barrier coatings due to its high-temperature stability. This versatility makes it a valuable material in fields that demand both strength and durability.
Q2: How do purity levels affect zirconia performance?
Purity levels are critical in determining the mechanical and chemical performance of zirconia powder. Higher purity means fewer contaminants, which can compromise mechanical strength, fracture toughness, and corrosion resistance. For example, in dental applications, the presence of impurities can lead to higher rates of failure in implants and prosthetics. Additionally, high-purity zirconia is essential in industrial environments where harsh chemicals are present, as impurities can lead to faster material degradation. Thus, investing in high-purity zirconia not only enhances performance but also extends the lifespan of end products.
Q3: What are the most common testing methods for zirconia powder?
Common testing methods for assessing zirconia powder include X-ray diffraction (XRD) for phase analysis, which identifies the crystal structure and stability of the material under varying conditions. Additionally, the Brunauer-Emmett-Teller (BET) method is frequently used to determine the surface area, providing insights into the reactivity of the powder. Density measurements can be performed using methods like Archimedes’ principle or gas pycnometry to ensure consistency and performance in applications. Routine mechanical testing, such as tensile and compressive strength tests, further validates the material’s suitability for specific industrial uses.
Q4: Why is crystal structure variation important in zirconia?
Different crystal structures, such as monoclinic, tetragonal, and cubic, significantly influence the thermal and mechanical properties of zirconia. For example, the tetragonal and cubic phases typically offer higher toughness and strength at elevated temperatures, making them ideal for applications in high-performance environments like gas turbines. Understanding these variations allows manufacturers to tailor zirconia formulations for specific uses, ensuring that the material behaves predictably under the intended operating conditions. For instance, selecting the correct crystal structure can prevent undesirable phase transformations that may lead to component failure.
Q5: What should I ask a supplier about their zirconia powder?
When sourcing zirconia powder, it’s essential to ask suppliers about several key aspects to ensure quality and suitability. Inquire about the purity levels of their zirconia powder and any testing methods used to verify them, as high purity is crucial for performance. Request detailed product specifications that include mechanical, thermal, and chemical properties, as well as information on the packaging sizes and storage conditions. Additionally, ask about their quality assurance processes and certifications to confirm that they comply with industry standards. Inquiring about sample availability for testing before making a large purchase can also be beneficial in ensuring the material meets your needs.