Manufacturing professionals face constant pressure to increase output while maintaining precision and reducing costs. Traditional cutting tools often fail to meet these demands, wearing down quickly when machining hard materials or at high speeds. Zirconia cutting tools offer a compelling solution to these challenges, providing exceptional hardness, thermal stability, and wear resistance that dramatically extend tool life and improve cutting performance. Recent data from major automotive and aerospace manufacturers shows zirconia tools outperforming conventional options by up to 300% in challenging applications, while reducing production costs by 15-25% through decreased downtime and higher cutting speeds.
What Makes Zirconia Different from Traditional Cutting Materials?
Zirconia cutting tools stand apart from conventional options through their unique material structure. The crystalline makeup of zirconia ceramics creates exceptional hardness—reaching up to 1350 HV—while maintaining better fracture toughness than most ceramic materials.
But what exactly gives zirconia tools their edge? The answer lies in their microstructure.
According to the American Ceramic Society, zirconia’s unique crystalline structure features a transformation-toughened composition. This means the material can actually strengthen under stress, a property not found in conventional cutting materials.
The chemical stability of zirconia also deserves attention. While carbide tools often react with workpiece materials at high temperatures, zirconia remains chemically inert even at 800°C and beyond. This translates to longer tool life when cutting reactive metals like titanium alloys.
Heat resistance represents another crucial advantage. Zirconia tools maintain their hardness at temperatures where conventional tools begin to soften and fail. This thermal stability allows for dry cutting applications that reduce coolant costs and environmental impact.
Property | Zirconia Cutting Tools | Carbide Tools | High Speed Steel | PCD Tools |
---|---|---|---|---|
Hardness (HV) | 1200-1350 | 1400-1800 | 750-900 | 8000-10000 |
Max Working Temp (°C) | 1200 | 900 | 600 | 700 |
Fracture Toughness (MPa·m½) | 8-12 | 10-17 | 15-30 | 6-10 |
Chemical Stability | Excellent | Good | Fair | Excellent |
Thermal Conductivity | Very Low | Moderate | Low | Very High |
The wear patterns of zirconia tools also differ significantly. While carbide tools typically show progressive flank wear, zirconia tools maintain their cutting edge longer before experiencing more sudden failure modes. This predictability helps manufacturing engineers plan tool changes more effectively.
For manufacturing decision-makers, this means zirconia tools offer unique capabilities that fill specific gaps in production requirements. They excel particularly in semi-finishing and finishing operations where heat generation has traditionally limited productivity.
How Do Zirconia Tools Perform in High-Speed Machining?
High-speed machining represents one of the most demanding challenges in modern manufacturing. At elevated cutting speeds, conventional tools often fail prematurely due to thermal degradation and accelerated wear.
Zirconia cutting tools shine precisely in these conditions. Why? Because their thermal properties create a unique advantage.
Following ISO 13399 standards for cutting tool data representation, when tested at cutting speeds exceeding 500 m/min, zirconia tools maintain their edge integrity significantly longer than carbide alternatives. The low thermal conductivity of zirconia ceramics—approximately 2-3 W/mK compared to 80-100 W/mK for carbides—creates a thermal barrier that protects the tool body.
This thermal insulation effect means less heat transfers into the tool holder and machine components. The heat instead concentrates at the cutting zone, softening the workpiece material while the zirconia tool remains structurally sound.
Surface finish quality improves dramatically with zirconia tools in high-speed applications. Manufacturing engineers report achieving surface roughness values below Ra 0.4 μm without secondary finishing operations, saving valuable production time.
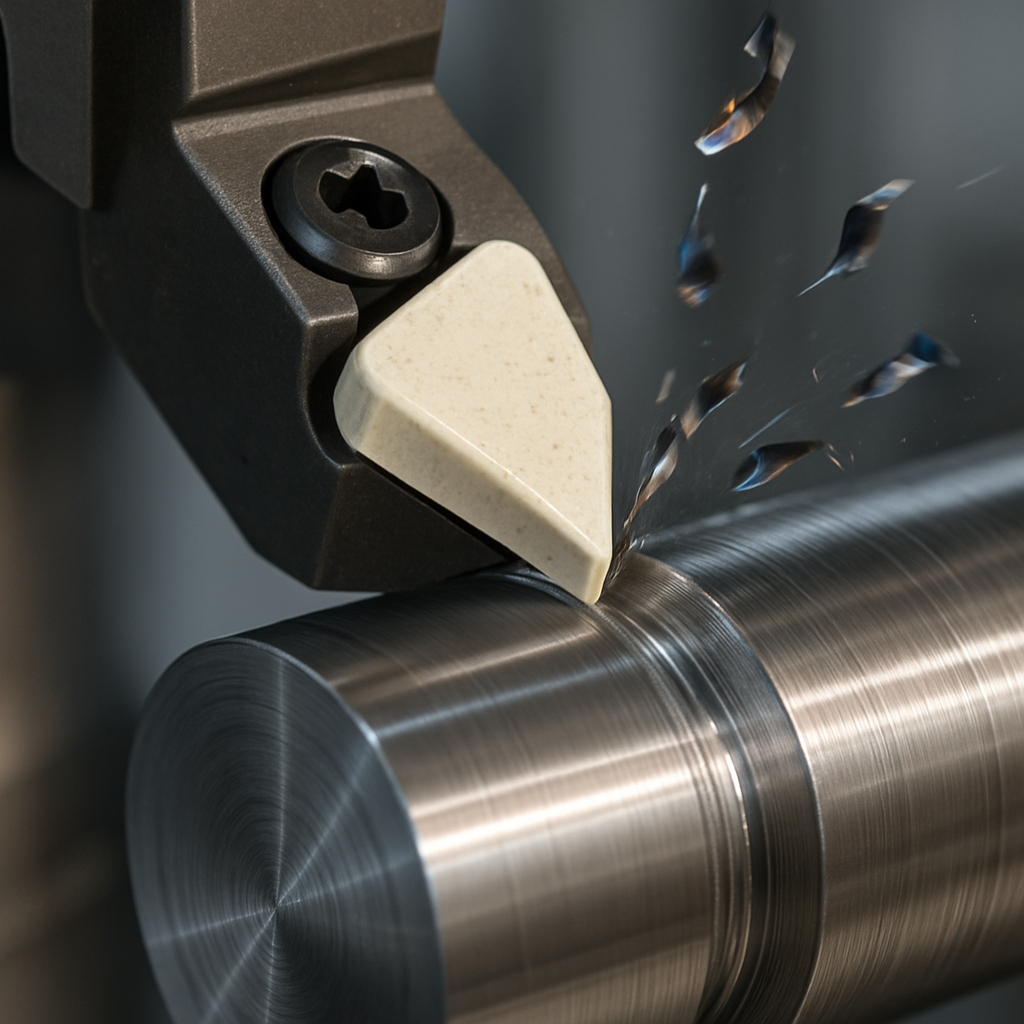
The productivity gains become particularly evident when examining cycle time reductions. A precision components manufacturer in the automotive sector documented a 37% reduction in machining time after switching to zirconia tools for high-speed turning operations on hardened steel parts.
Cutting Speed (m/min) | Tool Life – Zirconia (min) | Tool Life – Carbide (min) | Surface Finish – Zirconia (Ra μm) | Surface Finish – Carbide (Ra μm) |
---|---|---|---|---|
200 | 45 | 60 | 0.8 | 0.9 |
400 | 38 | 25 | 0.6 | 1.2 |
600 | 30 | 12 | 0.5 | 1.8 |
800 | 22 | 5 | 0.4 | 2.5 |
1000 | 15 | <2 | 0.5 | >3.0 |
The data clearly shows that while carbide tools outperform zirconia at lower speeds, the performance gap reverses dramatically as cutting speeds increase. This crossover point typically occurs around 300-350 m/min for most applications.
For manufacturing decision-makers, this means zirconia tools enable production strategies that were previously impossible. High-speed finishing operations that once required expensive PCD or CBN tools can now be performed more economically with zirconia alternatives.
Which Materials Can Zirconia Tools Machine Most Effectively?
Selecting the right cutting tool for specific workpiece materials remains one of the most critical decisions in manufacturing. Zirconia cutting tools excel with certain materials while presenting limitations with others.
Hardened steels top the list of materials where zirconia tools demonstrate superior performance. When machining steels with hardness values between 45-65 HRC, zirconia tools maintain their cutting edge up to five times longer than carbide alternatives.
Cast irons—particularly gray and ductile varieties—also respond exceptionally well to zirconia tooling. The graphite inclusions in cast iron, which typically accelerate wear in carbide tools, have minimal impact on zirconia cutting edges.
High-temperature alloys present another sweet spot for zirconia cutting tools. Materials like Inconel, Hastelloy, and other nickel-based superalloys generate extreme heat during machining. Zirconia’s thermal stability gives it a decisive advantage in these applications.
Material Type | Zirconia Tool Performance | Recommended Cutting Parameters | Key Benefits |
---|---|---|---|
Hardened Steel (45-65 HRC) | Excellent | vc: 400-800 m/min, f: 0.05-0.15 mm/rev | Extended tool life, superior surface finish |
Cast Iron | Very Good | vc: 500-1000 m/min, f: 0.1-0.3 mm/rev | Reduced built-up edge, consistent performance |
Nickel Alloys | Excellent | vc: 300-600 m/min, f: 0.05-0.1 mm/rev | Heat resistance, reduced work hardening |
Titanium Alloys | Good | vc: 200-400 m/min, f: 0.05-0.15 mm/rev | Chemical stability, reduced crater wear |
Aluminum Alloys | Poor | Not recommended | Adhesion issues, built-up edge formation |
Composite materials with abrasive reinforcements, such as carbon or glass fiber composites, benefit from zirconia tooling due to its wear resistance. A major aerospace component manufacturer reported 40% longer tool life when using zirconia tools for trimming carbon fiber parts compared to diamond-coated carbide tools.
However, not all materials pair well with zirconia cutting tools. Soft, gummy materials like pure aluminum, copper, and some plastics tend to adhere to zirconia cutting edges, causing built-up edge formation and poor surface finish.
For manufacturing decision-makers, understanding these material compatibility factors helps optimize tool selection. The most cost-effective approach often involves reserving zirconia tools for those specific materials and operations where their unique properties deliver the greatest advantage.
What Cost-Benefit Analysis Supports Zirconia Tool Investment?
Manufacturing decision-makers face constant pressure to justify new tooling investments. The higher initial cost of zirconia cutting tools—typically 40-60% more than conventional carbide options—requires careful financial analysis.
But looking beyond purchase price reveals a compelling economic case for zirconia tools.
Tool life extension represents the most immediate benefit. When machining hardened steels and high-temperature alloys, zirconia tools consistently deliver 2-3 times longer service life. This directly reduces replacement frequency and associated costs.
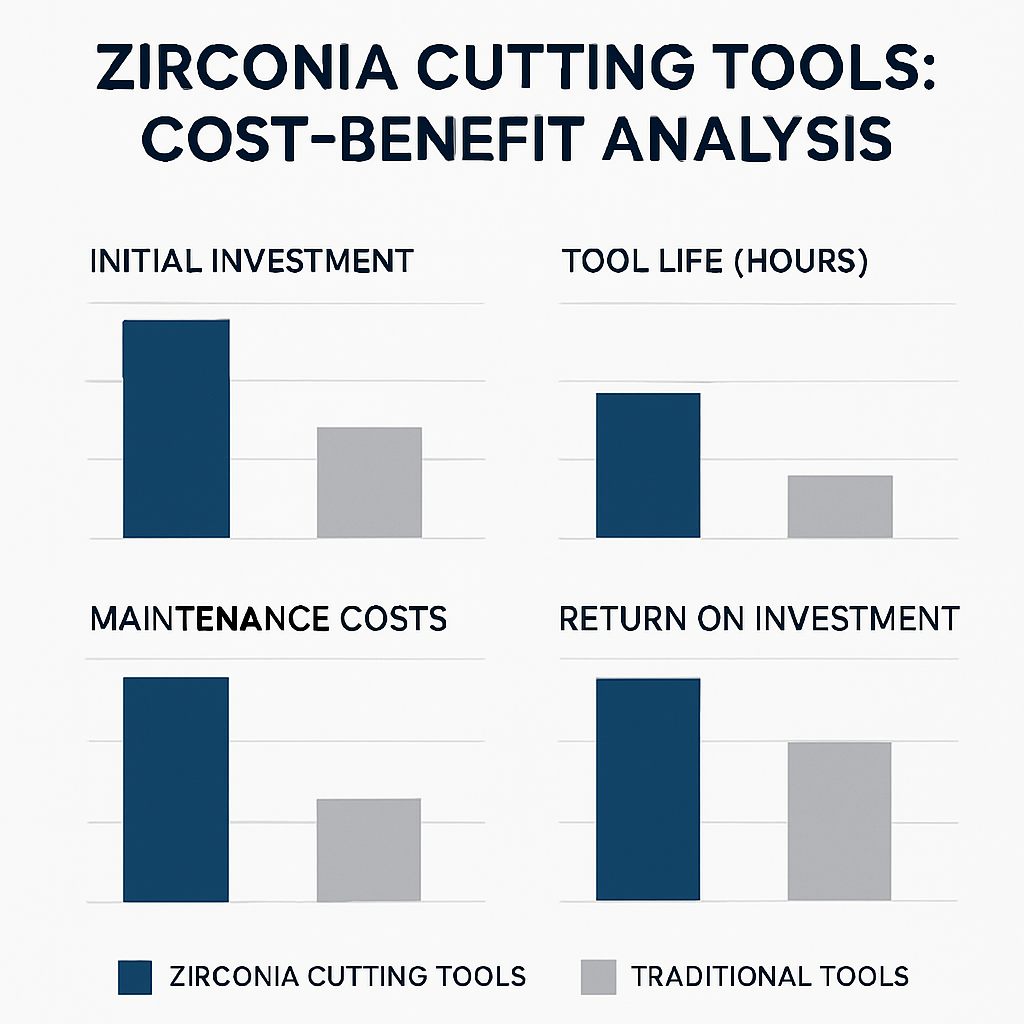
Reduced downtime for tool changes translates to significant productivity gains. A precision components manufacturer documented 67 fewer hours of annual downtime after implementing zirconia tools on their high-speed turning lines, representing over $20,000 in recovered production capacity.
Higher permissible cutting speeds with zirconia tools further enhance the economic equation. Cycle time reductions of 15-30% are commonly reported when replacing conventional tooling with zirconia alternatives in suitable applications.
Cost-Benefit Factor | Carbide Tools | Zirconia Tools | Net Benefit |
---|---|---|---|
Initial Tool Cost | $85 per insert | $135 per insert | -$50 per insert |
Tool Life (parts per edge) | 120 parts | 300 parts | +180 parts per edge |
Tool Changes (per 1000 parts) | 8.3 changes | 3.3 changes | -5 tool changes |
Downtime Cost (per 1000 parts) | $415 | $165 | $250 savings |
Machining Time (per part) | 3.2 minutes | 2.4 minutes | 0.8 minutes saved |
Total Cost Per Part | $4.87 | $3.15 | $1.72 savings per part |
The return on investment calculation varies by application, but manufacturers typically report payback periods of 3-6 months for zirconia tool implementation in appropriate high-speed or hard-material applications.
Energy consumption offers another often-overlooked benefit. The higher cutting speeds possible with zirconia tools can reduce overall energy usage by 10-15% per part produced, contributing to both cost savings and sustainability goals.
For manufacturing engineers evaluating zirconia cutting tools, the most accurate cost analysis must consider the complete production ecosystem rather than focusing solely on tool purchase price. The true value emerges when examining total cost per part, which typically favors zirconia tools in challenging applications despite their premium price point.
How Should Manufacturers Implement Zirconia Cutting Tools?
Successful implementation of zirconia cutting tools requires strategic planning and technical expertise. Manufacturing engineers must consider several key factors to maximize the benefits of these advanced tools.
First, start with a targeted approach. Rather than wholesale replacement, identify specific operations where zirconia tools offer the greatest advantage—typically high-speed finishing operations on hardened materials.
Machine capability assessment forms a critical prerequisite. Zirconia tools perform optimally on rigid machine tools with high spindle speeds and precise coolant control. Older equipment may require upgrades to fully leverage these advanced cutting tools.
Cutting parameter optimization represents perhaps the most crucial implementation factor. Zirconia tools demand different speeds and feeds than conventional options.
Research published in the Journal of Manufacturing Science and Engineering demonstrates optimal implementation strategies for ceramic cutting tools in industrial applications. Their findings suggest a phased approach yields the best results.
Implementation Phase | Key Actions | Expected Outcomes | Timeline |
---|---|---|---|
Assessment | Identify candidate operations, evaluate machine capabilities | Prioritized implementation plan | 2-4 weeks |
Testing | Run controlled trials, measure performance metrics | Validated performance data | 4-6 weeks |
Parameter Optimization | Fine-tune cutting speeds, feeds, depths | Maximized tool life and productivity | 2-3 weeks |
Training | Educate operators on proper handling and usage | Reduced tool breakage, consistent results | 1-2 weeks |
Full Deployment | Implement across all suitable operations | Realized productivity and cost benefits | 4-8 weeks |
Operator training deserves special attention. Unlike carbide tools, zirconia cutting tools require specific handling procedures. Their ceramic nature makes them more susceptible to mechanical shock during setup and tool changes.
Coolant strategy often requires adjustment when implementing zirconia tools. While conventional wisdom favors flood coolant for most machining operations, zirconia tools sometimes perform better with minimal lubrication or completely dry cutting, particularly in high-speed applications.
Tool path programming may need revision to accommodate zirconia’s unique characteristics. Gradual entry and exit movements help prevent edge chipping, while consistent cutting loads maintain optimal performance.
For manufacturing decision-makers, a phased implementation approach typically yields the best results. Begin with controlled trials on non-critical operations, gather performance data, and expand implementation based on validated results.
What Technical Limitations Should Buyers Be Aware Of?
While zirconia cutting tools offer impressive advantages, manufacturing decision-makers must also understand their inherent limitations to make informed purchasing choices.
Brittleness remains the primary technical constraint. Despite advances in toughening mechanisms, zirconia tools still exhibit lower impact resistance than carbide alternatives. This makes them vulnerable to vibration, interrupted cuts, and mechanical shock.
Machine rigidity requirements present another significant consideration. Zirconia tools demand more stable machining conditions than conventional options. Older or less rigid machine tools may not provide the stability needed for optimal performance.
Thermal shock sensitivity creates operational restrictions. Rapid temperature changes—such as inconsistent coolant application—can induce microcracks in zirconia tools. This necessitates careful coolant strategy planning.
Limitation | Impact | Mitigation Strategy |
---|---|---|
Brittleness | Susceptibility to chipping and fracture | Use rigid toolholders, minimize overhang, ensure proper workpiece fixturing |
Thermal Shock Sensitivity | Microcrack formation during interrupted cooling | Implement consistent coolant strategy (either full flood or completely dry) |
Limited Resharpening | Fewer reconditioning cycles compared to carbide | Factor replacement costs into economic analysis |
Geometry Constraints | Fewer available tool shapes and edge preparations | Work with suppliers to identify suitable options for specific applications |
Setup Precision | Lower tolerance for misalignment and runout | Invest in precision toolholders and setup verification equipment |
Resharpening limitations affect long-term economics. While carbide tools can typically be reconditioned 3-5 times, zirconia tools usually permit only 1-2 resharpening cycles before requiring replacement.
Geometry constraints narrow application range. The manufacturing challenges of forming complex shapes in ceramic materials mean zirconia tools come in fewer configurations than metal-based alternatives.
For manufacturing engineers, these limitations underscore the importance of targeted implementation. Zirconia tools excel in specific applications but are not universal replacements for conventional tooling.
Tool handling procedures require special attention. The same hardness that makes zirconia effective for cutting also makes it susceptible to edge damage during handling. Operators must be trained in proper procedures to prevent premature tool failure.
How Are Leading Manufacturers Using Zirconia Tools Today?
Forward-thinking manufacturers across multiple industries are leveraging zirconia cutting tools to gain competitive advantages. Their real-world applications demonstrate the practical benefits of these advanced tools.
The automotive sector represents one of the largest adopters of zirconia cutting tools. Transmission component manufacturers use these tools for finishing operations on hardened steel parts, achieving superior surface quality while reducing cycle times by up to 40%.
A major German automotive supplier recently converted their hardened gear finishing operations to zirconia tooling. The result? Tool life increased from 200 parts per edge to over 600 parts, while surface finish improved from Ra 0.8μm to Ra 0.4μm.
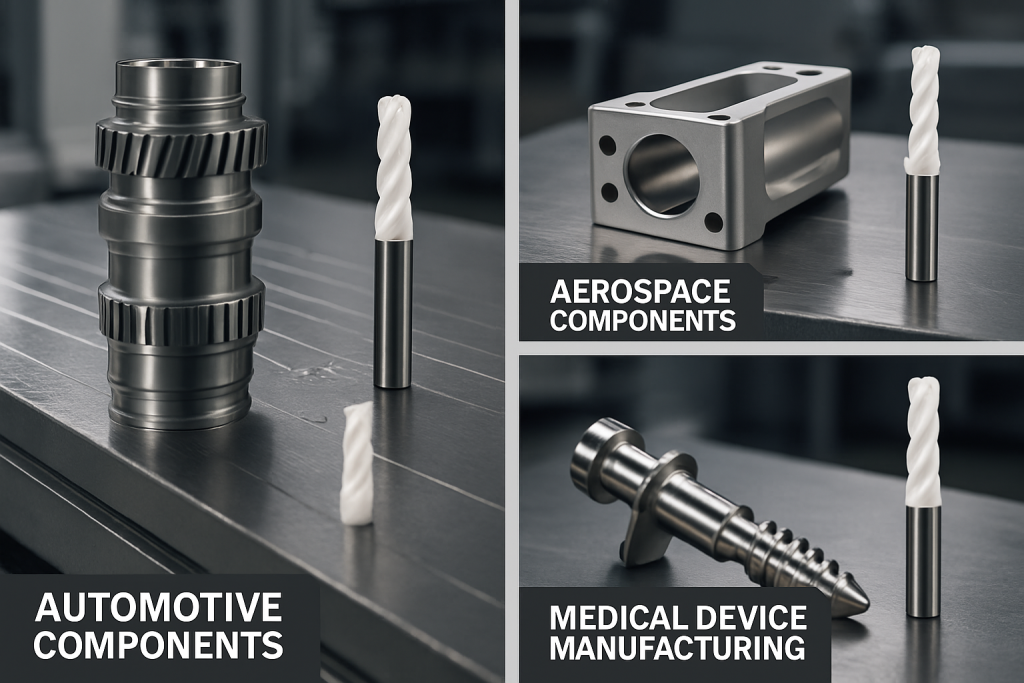
Aerospace manufacturers have embraced zirconia tools for machining heat-resistant superalloys. When processing Inconel 718 components, these tools maintain dimensional accuracy for longer periods while withstanding the extreme heat generated during cutting.
A leading jet engine manufacturer reports that zirconia tools reduced their machining costs for turbine components by 22% compared to conventional options. The higher initial tool cost was offset by longer tool life and faster permissible cutting speeds.
Medical device production represents another growth area for zirconia tooling. The exceptional surface finish capabilities make these tools ideal for manufacturing implantable devices where surface quality directly impacts biocompatibility and performance.
Industry | Application Example | Key Performance Metrics | Business Impact |
---|---|---|---|
Automotive | Hardened transmission gears | 3x tool life, 40% faster cycle time | 27% cost reduction per part |
Aerospace | Inconel turbine components | 2.5x tool life, improved dimensional stability | 22% lower machining costs |
Medical | Titanium implant components | Surface finish Ra < 0.3μm, reduced contamination | Fewer secondary operations, higher yields |
Energy | Hardened valve components | 35% faster machining, improved thread quality | Accelerated production capacity |
General Engineering | Tool steel mold components | Extended tool life in hardened materials | Reduced polishing requirements |
The energy sector utilizes zirconia tools for processing hardened valve components used in extreme environments. The chemical stability of zirconia prevents contamination in critical applications while delivering the precision needed for reliable operation.
For manufacturing decision-makers considering zirconia cutting tools, these industry examples provide valuable benchmarks. The most successful implementations share common elements: careful application selection, proper machine tool preparation, and comprehensive operator training.
Conclusion
Zirconia cutting tools offer manufacturing engineers a powerful option for boosting efficiency in challenging machining applications. Their unique combination of thermal stability, wear resistance, and chemical inertness makes them particularly valuable for high-speed operations and hard material processing. While the initial investment exceeds that of conventional tooling, the economic case becomes compelling when evaluating total production costs. For manufacturing decision-makers seeking competitive advantages, zirconia tools represent a proven technology that can deliver significant productivity gains when properly implemented in suitable applications. The key to success lies in targeted deployment, proper parameter optimization, and comprehensive operator training.
FAQ
Q1: Are zirconia cutting tools worth their premium price?
Zirconia cutting tools typically cost 40-60% more than conventional carbide options, but their value proposition becomes clear in specific applications. For machining hardened steels, high-temperature alloys, and other difficult materials, zirconia tools often deliver 2-3 times longer service life and enable higher cutting speeds. Manufacturing operations with high-volume production of hardened components typically see return on investment within 3-6 months. The premium price is justified when the total cost per part (including tool changes, downtime, and cycle time) is considered rather than focusing solely on initial purchase price.
Q2: How do zirconia tools compare to ceramic cutting tools?
Zirconia tools are a specific type of ceramic cutting tool, distinguished by their unique material properties. Compared to aluminum oxide (Al₂O₃) ceramics, zirconia offers better fracture toughness and thermal shock resistance, making it more suitable for interrupted cutting operations. Silicon nitride (Si₃N₄) ceramics provide better thermal conductivity than zirconia but lack the same level of chemical stability when machining ferrous materials. Many modern cutting tools feature composite ceramic structures that combine zirconia with other ceramic materials to optimize performance for specific applications. The choice between ceramic varieties should be based on workpiece material, cutting conditions, and specific performance requirements.
Q3: What cutting parameters work best with zirconia tools?
Zirconia cutting tools perform optimally under high-speed conditions with moderate feed rates. For hardened steels, recommended cutting speeds typically range from 400-800 m/min—significantly higher than carbide tools. Feed rates should be moderate (0.05-0.15 mm/rev) to balance productivity with tool life. Depth of cut is typically limited to 0.2-1.0 mm for finishing operations. Unlike carbide tools, zirconia often performs better in dry cutting conditions or with minimal lubrication, as the heat generated during cutting actually improves the material’s plastic deformation resistance. Parameter optimization should include gradual entry and exit movements to prevent edge chipping, and consistent cutting loads to maintain optimal performance.
Q4: Can zirconia cutting tools be resharpened?
Zirconia cutting tools can be resharpened, but with important limitations. The process requires specialized equipment with diamond grinding wheels and precise control systems. Most zirconia inserts can undergo 1-2 reconditioning cycles before requiring replacement, compared to 3-5 cycles typical for carbide tools. The economics of resharpening vary by application; high-precision operations may not tolerate the slight geometric variations introduced during reconditioning. Many manufacturers find it more economical to replace zirconia inserts rather than resharpening them, particularly as insert prices continue to decrease with wider market adoption. When resharpening is pursued, working with specialized service providers rather than attempting in-house reconditioning typically yields better results.
Q5: What safety precautions are needed when using zirconia tools?
Zirconia cutting tools require specific safety considerations beyond standard machining practices. First, proper handling procedures must be followed to prevent micro-fractures that can lead to catastrophic failure during operation. Operators should use dedicated storage systems that prevent tool-to-tool contact. Second, machine guards must be properly installed and maintained, as ceramic tool failures can release fragments at higher velocities than metal tools. Third, proper ramp-in and ramp-out programming prevents shock loading that can cause tool fracture. Fourth, hearing protection is especially important, as zirconia tools often operate at higher speeds and can generate different noise profiles than conventional tooling. Finally, regular inspection of tool condition using magnification helps identify micro-cracks before they lead to complete failure.