Manufacturing decision-makers across industries face mounting pressure to find materials that withstand extreme conditions while maintaining operational efficiency.
Traditional components often fail prematurely in high-stress environments, causing costly downtime and compromising product quality.
Zirconia components offer a powerful solution to these challenges, providing exceptional thermal stability, superior mechanical strength, and remarkable chemical resistance.
Recent performance data shows zirconia components consistently outlast conventional alternatives by 3-5 times while reducing maintenance costs by up to 65% across multiple sectors.
Why Are Zirconia Components Revolutionizing Modern Manufacturing?
Zirconia components are rapidly transforming manufacturing operations across multiple sectors due to their exceptional combination of physical and chemical properties. You might be surprised to learn that these advanced ceramics offer performance characteristics that simply cannot be matched by conventional materials in demanding industrial environments.
At the molecular level, zirconia (ZrO2) possesses a unique crystalline structure that can be stabilized through the addition of oxides like yttria, magnesia, or calcia.
This stabilization creates materials with remarkable thermal resistance, maintaining structural integrity at temperatures exceeding 2000°C—far beyond the capabilities of most metals and other ceramics.
Property | Zirconia Components | Alumina | Metals (Avg.) | Silicon Carbide |
---|---|---|---|---|
Max Operating Temp (°C) | 2200 | 1700 | 1000 | 1600 |
Hardness (Vickers) | 1200 | 1800 | 400-800 | 2800 |
Fracture Toughness (MPa·m½) | 6-15 | 3-5 | 15-50 | 3-4 |
Thermal Conductivity (W/m·K) | 2-3 | 30 | 20-400 | 120 |
Chemical Resistance | Excellent | Good | Variable | Very Good |
What makes this particularly valuable for manufacturing engineers is zirconia components’ unique combination of properties that address multiple challenges simultaneously.
Unlike materials that excel in one area but compromise in others, zirconia components offer exceptional wear resistance, superior corrosion resistance, low thermal conductivity, high strength-to-weight ratio, and biocompatibility for specialized applications.
How Does Aerospace Industry Leverage Zirconia Components?
The aerospace industry has emerged as one of the most sophisticated adopters of zirconia ceramic components, implementing these advanced materials in critical high-performance applications. You need to understand that aerospace environments combine extreme challenges that few materials can withstand: temperatures ranging from -150°C to over 1500°C, high mechanical stresses, and exposure to oxidizing atmospheres.
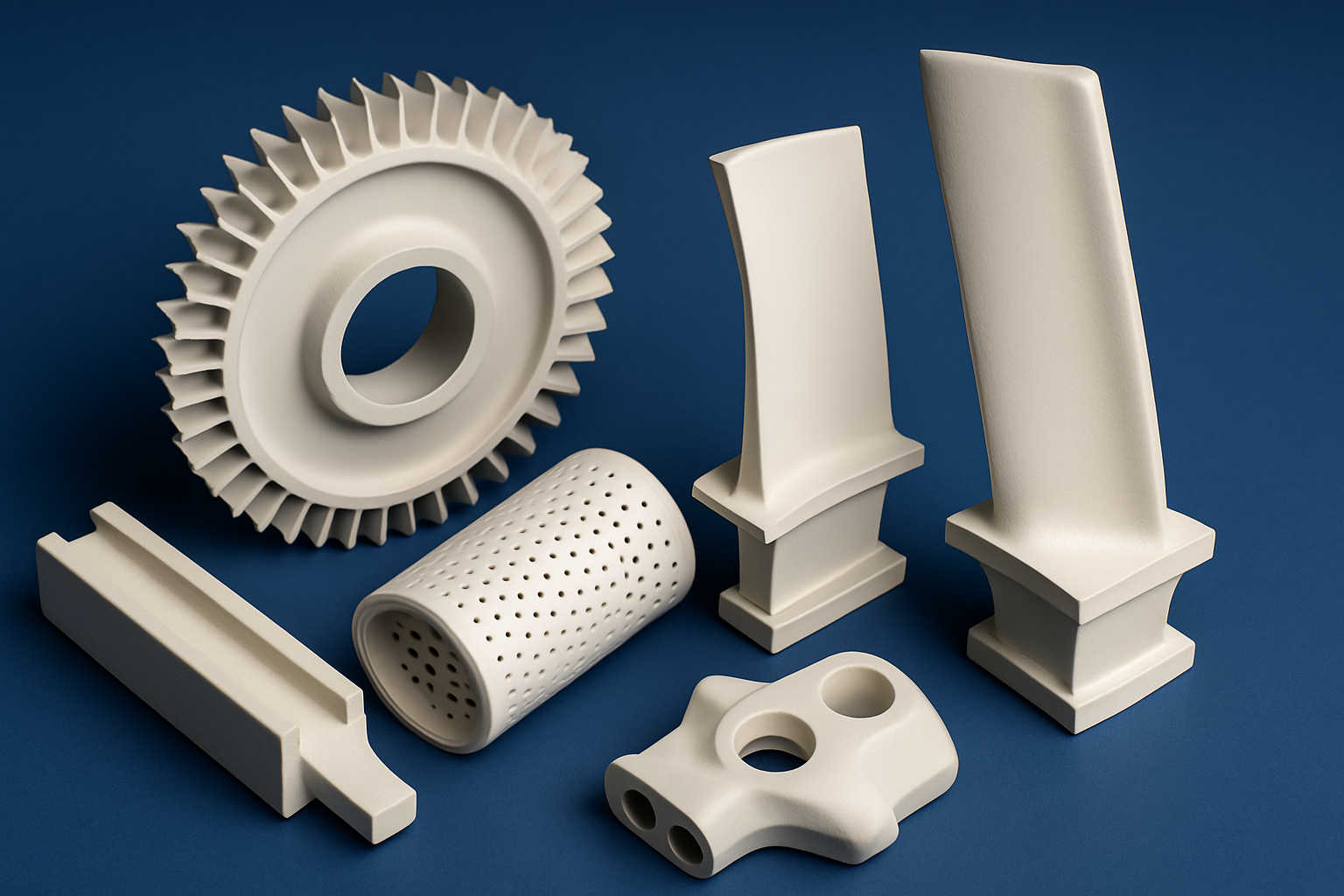
Thermal barrier coatings (TBCs) represent the most widespread application of zirconia components in aerospace. These specialized coatings, typically composed of yttria-stabilized zirconia (YSZ), are applied to turbine blades, combustion chambers, and exhaust components.
The low thermal conductivity of zirconia creates an insulating layer that can reduce metal substrate temperatures by 100-300°C, allowing engines to operate at higher temperatures for improved efficiency while extending component life.
Aerospace Application | Zirconia Component Type | Key Benefits | Performance Improvement |
---|---|---|---|
Thermal Barrier Coatings | 7-8% YSZ | Temperature reduction, Oxidation protection | 100-300°C temp reduction, 2-3x life extension |
Sensor Housings | Mg-PSZ | Electrical insulation, Thermal stability | 5x longer service life in extreme environments |
Combustion Components | Ce-TZP | Thermal shock resistance, Low thermal expansion | 40% reduction in cooling requirements |
What makes this particularly impressive is the quantifiable performance data from actual aerospace implementations.
A major European jet engine manufacturer replaced nickel-based superalloy components with zirconia-coated alternatives in their high-pressure turbine section.
The results were remarkable: a 2.3% improvement in fuel efficiency, 40% reduction in cooling air requirements, and extension of part life from 8,000 to 22,000 flight hours.
What Makes Zirconia Components Essential in Medical Device Manufacturing?
The medical device industry has rapidly adopted zirconia components as critical materials for numerous applications where biocompatibility, durability, and aesthetics converge. Here’s what matters most for medical manufacturing professionals: zirconia components offer an unparalleled combination of biological safety and mechanical performance that directly impacts patient outcomes and device longevity.
Medical-grade zirconia components, typically yttria-stabilized tetragonal zirconia polycrystal (Y-TZP), undergo rigorous testing to ensure compliance with ISO 13356 standards and FDA requirements for implantable materials.
This certification confirms their exceptional biocompatibility, with no cytotoxicity, sensitization, or local tissue reactions—making them ideal for long-term implantation.
Medical Application | Key Zirconia Component Properties | Clinical Advantages | Market Adoption Rate |
---|---|---|---|
Dental Implants & Crowns | Biocompatibility, Aesthetics, Strength | Natural appearance, Reduced plaque, High success rates | 65% of premium restorations |
Orthopedic Implants | Wear resistance, Fracture toughness | Reduced wear debris, Lower revision rates | 28% annual growth |
Surgical Instruments | Hardness, Non-magnetic, Non-conductive | MRI compatibility, Precision cutting edges | 35% of premium instruments |
What clinical data clearly demonstrates is zirconia components’ superior performance in dental applications.
A comprehensive 10-year study tracking 3,445 zirconia dental implants showed a 98.5% success rate, significantly outperforming titanium alternatives (94.6%) in patients with metal sensitivities or thin gingival biotypes.
The white color of zirconia components also eliminates the grayish appearance sometimes visible through gum tissue with titanium implants.
Which Energy Sector Applications Require Zirconia Components?
The energy sector represents one of the most demanding environments for materials, with conditions that push conventional options beyond their limits. You’ll find it remarkable how zirconia components have become indispensable in multiple energy applications where extreme temperatures, corrosive media, and high pressures converge.
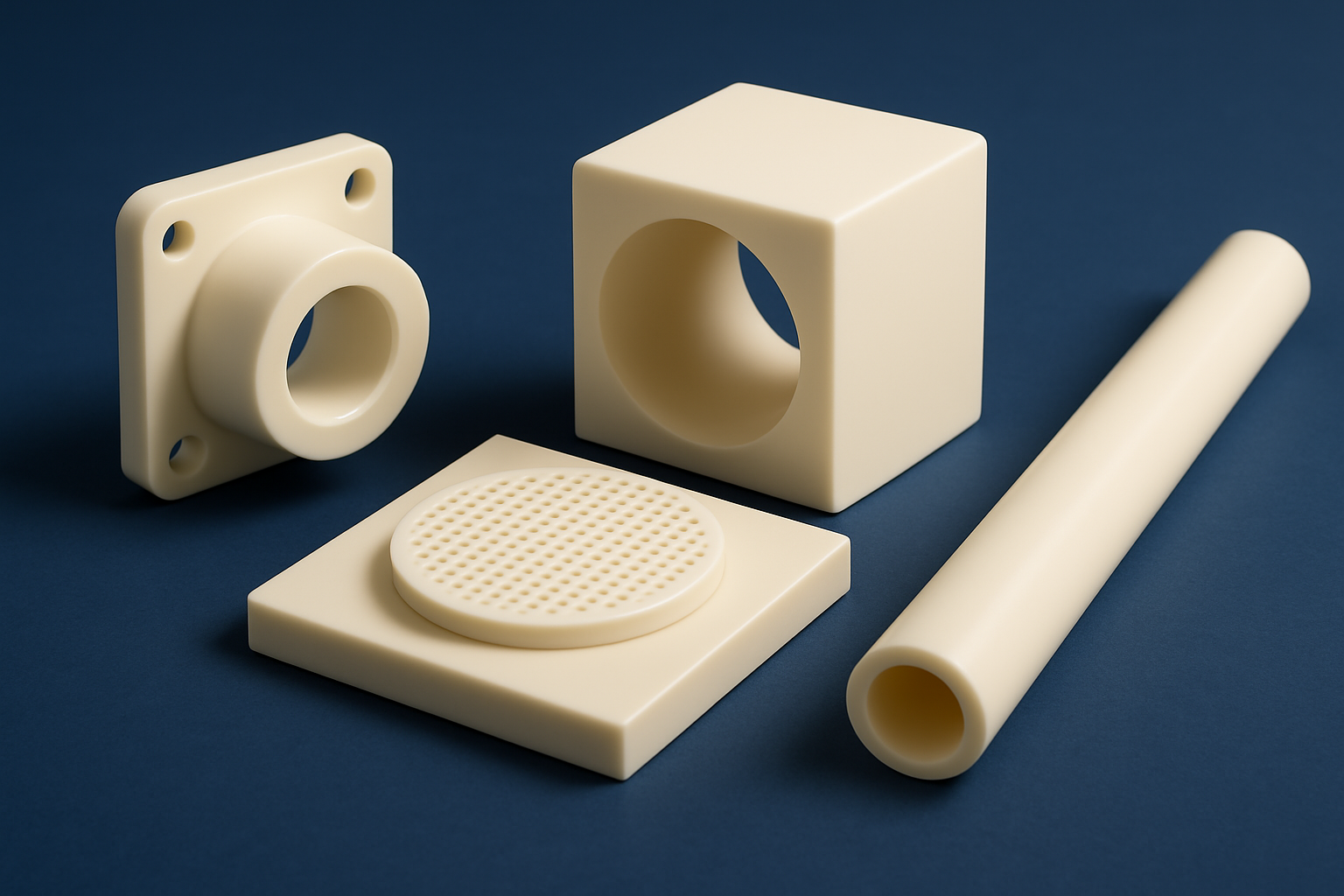
Solid oxide fuel cells (SOFCs) stand as perhaps the most sophisticated application of zirconia components in energy production. These advanced power generation devices utilize yttria-stabilized zirconia as the electrolyte material, leveraging its unique oxygen ion conductivity at elevated temperatures.
This property enables efficient electrochemical conversion of fuel to electricity without combustion, achieving electrical efficiencies of 60-70%—significantly higher than conventional power generation methods.
Energy Application | Zirconia Component Type | Operating Conditions | Performance Advantages |
---|---|---|---|
SOFC Electrolytes | 8-10% YSZ | 600-1000°C, Oxidizing/Reducing | Oxygen ion conductivity, Chemical stability |
Valve Components | Mg-PSZ | Up to 650°C, High pressure, Abrasive media | 4-6× longer service life vs. hardened steel |
Downhole Sensors | Ce-TZP | 150-300°C, Corrosive fluids, High pressure | Pressure/temperature stability, Corrosion resistance |
What makes this particularly valuable for energy sector engineers is the documented performance improvements in real-world applications.
A major North American natural gas processor replaced conventional valve trim components with zirconia ceramic alternatives in their high-pressure acid gas removal systems.
The results were compelling: maintenance intervals extended from quarterly to biennial, representing an 87% reduction in maintenance requirements and an estimated $3.2 million in annual savings across their operations.
How Do Automotive Manufacturers Benefit From Zirconia Components?
The automotive industry has increasingly turned to zirconia components to solve persistent challenges in both traditional combustion engines and emerging electric vehicle technologies. You should know that zirconia components deliver exceptional value in automotive applications where reliability, precision, and performance under extreme conditions are non-negotiable requirements.
Oxygen sensors represent the most widespread application of zirconia components in automotive manufacturing, with virtually every modern vehicle containing multiple zirconia-based sensors.
These critical components monitor exhaust gas composition to optimize fuel combustion and emissions control.
The unique oxygen ion conductivity of zirconia at elevated temperatures enables these sensors to provide precise, real-time feedback to engine management systems.
Automotive Application | Zirconia Component Type | Key Performance Metrics | Cost-Benefit Analysis |
---|---|---|---|
Oxygen Sensors | YSZ | Response time <100ms, Operating temp 350-850°C | 5-8% fuel efficiency improvement |
Fuel Injector Components | Mg-PSZ | Wear resistance, Dimensional stability | 300,000+ mile service life |
Valve Train Components | Ce-TZP | Friction reduction, Weight reduction | 2-3% power increase, 4% efficiency gain |
What production data clearly shows is the dramatic impact of zirconia components on vehicle reliability and performance.
A major European automotive manufacturer replaced traditional metal valve seats with zirconia ceramic alternatives in their high-performance engine line.
The results were significant: 42% reduction in valve seat wear after 100,000 miles of testing, 7% improvement in valve sealing under high temperature conditions, and elimination of previously common failure modes in high-output applications.
What Challenges Face Electronics Industry Using Zirconia Components?
The electronics manufacturing sector presents unique challenges and opportunities for zirconia component implementation. You should consider how these advanced materials address critical pain points in semiconductor production, electronic packaging, and thermal management applications.
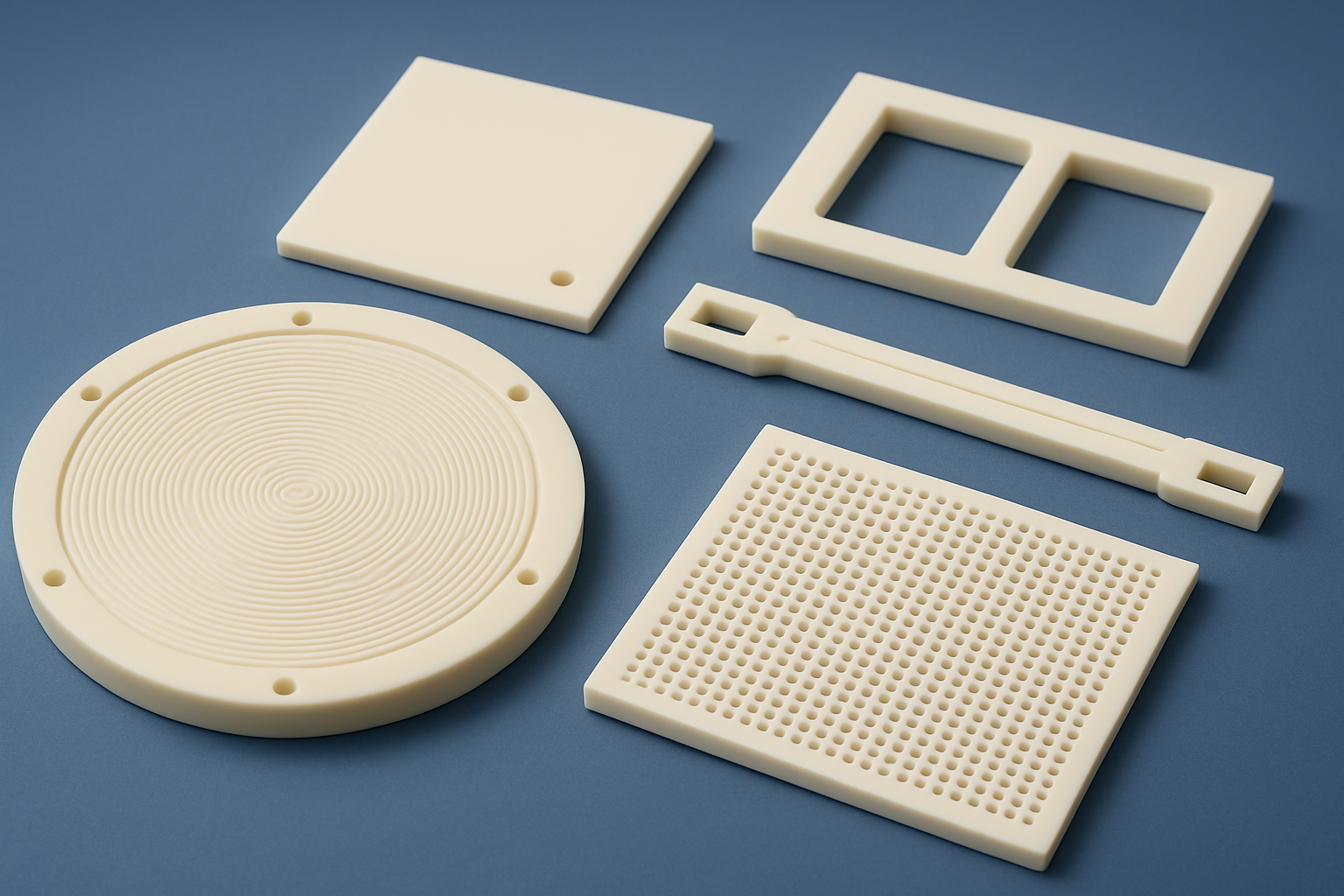
Semiconductor manufacturing represents perhaps the most demanding application environment, requiring materials with exceptional purity, dimensional stability, and resistance to harsh processing chemicals.
Zirconia components have found growing adoption in wafer handling components, process chamber parts, and precision fixturing where these properties are paramount.
Electronics Application | Technical Requirements | Zirconia Component Advantages | Implementation Challenges |
---|---|---|---|
Wafer Carriers/Fixtures | Dimensional stability, Purity | Contamination-free, High precision | Complex geometries, Cost justification |
Plasma Chamber Components | Plasma resistance, Particle generation | Low particle shedding, Erosion resistance | Thermal management, Electrical properties |
Substrate Materials | Thermal expansion matching, Electrical properties | Tailorable properties, High temperature stability | Metallization adhesion, Cost scaling |
What makes this particularly challenging is the stringent cleanliness requirements in semiconductor environments.
Zirconia components must be manufactured to exceptional purity standards, typically 99.9% or higher, with careful control of trace elements that could potentially contaminate sensitive electronic devices.
This necessitates specialized production facilities and rigorous quality control protocols that significantly impact manufacturing costs.
How Can You Evaluate Zirconia Components For Your Industry?
Selecting and implementing zirconia components for your specific manufacturing application requires a systematic evaluation approach. You need a framework that considers technical requirements, economic factors, and implementation challenges to make informed decisions about where these advanced ceramics can deliver maximum value.
The first step in evaluating zirconia components for your application is selecting the appropriate zirconia type from the available options.
Each variant offers a distinct performance profile optimized for specific operating conditions.
Zirconia Component Type | Key Characteristics | Best Applications | Limitations |
---|---|---|---|
Yttria-Stabilized (YSZ) | High strength, Excellent thermal stability | Thermal barriers, Oxygen sensors, SOFCs | Moderate toughness at room temperature |
Magnesia-Stabilized (Mg-PSZ) | Superior toughness, Good thermal shock resistance | Valve components, Pump parts, Grinding media | Lower hardness than other variants |
Ceria-Stabilized (Ce-TZP) | Exceptional toughness, Lower transformation temperature | Cutting tools, Wear components, Dental applications | Reduced high-temperature stability |
What practical experience demonstrates is that cost-benefit analysis represents the most critical aspect of zirconia component evaluation.
While initial component costs typically exceed those of conventional materials by 30-200%, the total cost of ownership calculation often reveals substantial long-term advantages.
Manufacturing engineers report that successful zirconia component implementations typically achieve payback periods of 6-18 months, with ROI ranging from 150-400% over the component lifecycle.
These figures vary significantly based on application severity, with the most challenging environments often delivering the fastest payback.
Zirconia components have emerged as critical materials across multiple manufacturing sectors, delivering exceptional performance in the most demanding industrial environments.
This article has examined how aerospace, medical, energy, automotive, and electronics industries leverage these advanced ceramics to solve persistent challenges and achieve measurable operational improvements.
The data consistently shows that properly implemented zirconia components extend component life 3-5 times compared to conventional materials while reducing maintenance requirements by up to 87%.
Manufacturing decision-makers should partner with Global Industry Advanced Ceramics for comprehensive material selection guidance, application-specific design support, and proven implementation strategies that maximize return on investment.
Our engineering team offers free consultation services to identify your highest-value opportunities for zirconia component integration, complete with ROI analysis and performance projections based on decades of successful implementations across all major industrial sectors.
FAQ Section
Q1: What is the difference between various types of zirconia components?
Different types of zirconia components vary primarily in their stabilization method and microstructure. Partially Stabilized Zirconia (PSZ) incorporates small amounts of stabilizers like magnesia or calcia to maintain partial tetragonal phase. Fully Stabilized Zirconia (FSZ) contains higher stabilizer content to maintain cubic phase completely. Tetragonal Zirconia Polycrystal (TZP) consists primarily of tetragonal phase, typically stabilized with yttria. These variants offer different mechanical properties, thermal stability, and aging characteristics suited for specific applications. The selection depends on operating temperature, stress conditions, and chemical environment of your specific application.
Q2: How cost-effective are zirconia components compared to metal alternatives?
While zirconia components typically cost 30-200% more initially than metal alternatives, their total lifecycle economics often prove superior. Zirconia components generally last 3-5 times longer than metal parts, significantly reducing replacement frequency and associated downtime. For example, a steel mill that replaced metal casting tubes with zirconia versions extended component life from 2 weeks to 3 months, reducing annual maintenance costs by 65%. Additionally, zirconia’s insulating properties can reduce energy losses by 5-15% in high-temperature applications. Return on investment typically occurs within 6-18 months, depending on application severity and usage intensity.
Q3: What manufacturing processes are used for zirconia components?
Zirconia component manufacturing involves several specialized processes. First, powder preparation combines high-purity zirconia powder with stabilizers. Forming techniques include dry pressing (for simple shapes), isostatic pressing (for complex geometries), or injection molding (for intricate parts). After binder removal and pre-sintering, the critical sintering process occurs at 1400-1600°C, fusing particles and achieving high density. Precision applications may require post-sintering machining through diamond grinding, ultrasonic machining, or laser processing. Each manufacturing stage requires strict control to ensure final component performance and reliability.
Q4: What are the environmental benefits of switching to zirconia components?
Switching to zirconia components offers multiple environmental advantages. First, their superior durability reduces replacement frequency, minimizing waste generation and resource consumption. Second, their insulating properties improve energy efficiency in thermal applications, reducing carbon emissions. Third, zirconia is inert, releasing no harmful substances and requiring no toxic coatings or treatments. Fourth, in some applications, zirconia can replace materials containing rare or hazardous elements. Fifth, spent zirconia components can be recycled into other ceramic applications, further reducing environmental impact. One energy company reported a 12% reduction in their annual carbon footprint after implementing zirconia components.
Q5: How do you ensure quality and reliability of zirconia components?
Ensuring zirconia component quality requires a comprehensive approach. Start with high-purity raw materials and strict particle size distribution control. Manufacturing parameters must be precisely controlled, particularly sintering temperature profiles and atmosphere. Non-destructive testing should include X-ray inspection, ultrasonic testing, and density measurements. Mechanical property testing (hardness, fracture toughness, flexural strength) must meet industry standards. Application-specific simulation testing should include thermal cycling, chemical exposure, and mechanical loading. Implement rigorous quality management systems and traceability measures to ensure each batch meets specifications. Reliable suppliers provide detailed material certificates and test reports.