In today’s demanding industrial landscape, finding materials that can withstand aggressive chemical environments isn’t just a technical challenge—it’s a business imperative. Zirconia ceramics have emerged as exceptional performers where other materials fail, offering unprecedented chemical resistance across diverse applications. This article examines how zirconia outperforms competing ceramics in harsh chemical environments, what makes its resistance properties unique, and which industries benefit most from these capabilities. By understanding this material’s superior chemical performance, engineers and procurement specialists can make informed decisions that extend component lifespans, reduce maintenance costs, and improve operational safety in corrosive settings.
Why Is Chemical Resistance Critical In Modern Industries?
Chemical attack represents one of the most destructive forces in industrial operations, silently degrading equipment and components until catastrophic failure occurs. The economic impact is staggering—a single corrosion-related failure in chemical processing equipment can cost between $500,000 and $10 million in direct replacement costs alone, not counting production losses.
But here’s the reality: chemical environments in modern manufacturing have become increasingly aggressive as processes push temperature and concentration boundaries to improve efficiency. Components face complex mixtures of acids, bases, salts, and organic compounds, often at elevated temperatures that accelerate degradation. This unique ceramic offers a solution to these challenges.
Industry | Common Chemical Challenges | Annual Cost of Corrosion |
---|---|---|
Chemical Processing | H₂SO₄, HCl, NaOH, organic solvents | $6-8 billion |
Oil & Gas | H₂S, CO₂, organic acids | $7-9 billion |
Pulp & Paper | NaOH, Cl₂, H₂O₂ | $3-5 billion |
Semiconductor | HF, H₂O₂, NH₄OH mixtures | $2-4 billion |
Material selection directly impacts both operational efficiency and safety. Inadequate chemical resistance leads to contamination, production downtime, increased maintenance, and potential catastrophic failures that can release hazardous substances. The weight given to chemical resistance in material selection decisions has grown significantly, now ranking among the top three criteria in industries handling corrosive media. This ceramic consistently ranks as a top performer in these evaluations.
What Makes Zirconia’s Chemical Structure Uniquely Resistant?
Exceptional chemical resistance stems from its fundamental atomic and crystalline structure. At the heart of this ceramic’s durability is a remarkably stable arrangement of zirconium and oxygen atoms that creates strong ionic-covalent bonds with high dissociation energy.
The science is clear: its crystal structure provides inherent stability against chemical attack. In its most common forms—tetragonal, monoclinic, and cubic—this material maintains strong Zr-O bonds that resist breaking even in aggressive chemical environments. This stability contrasts sharply with other ceramics like alumina, which can undergo preferential dissolution of grain boundary phases.
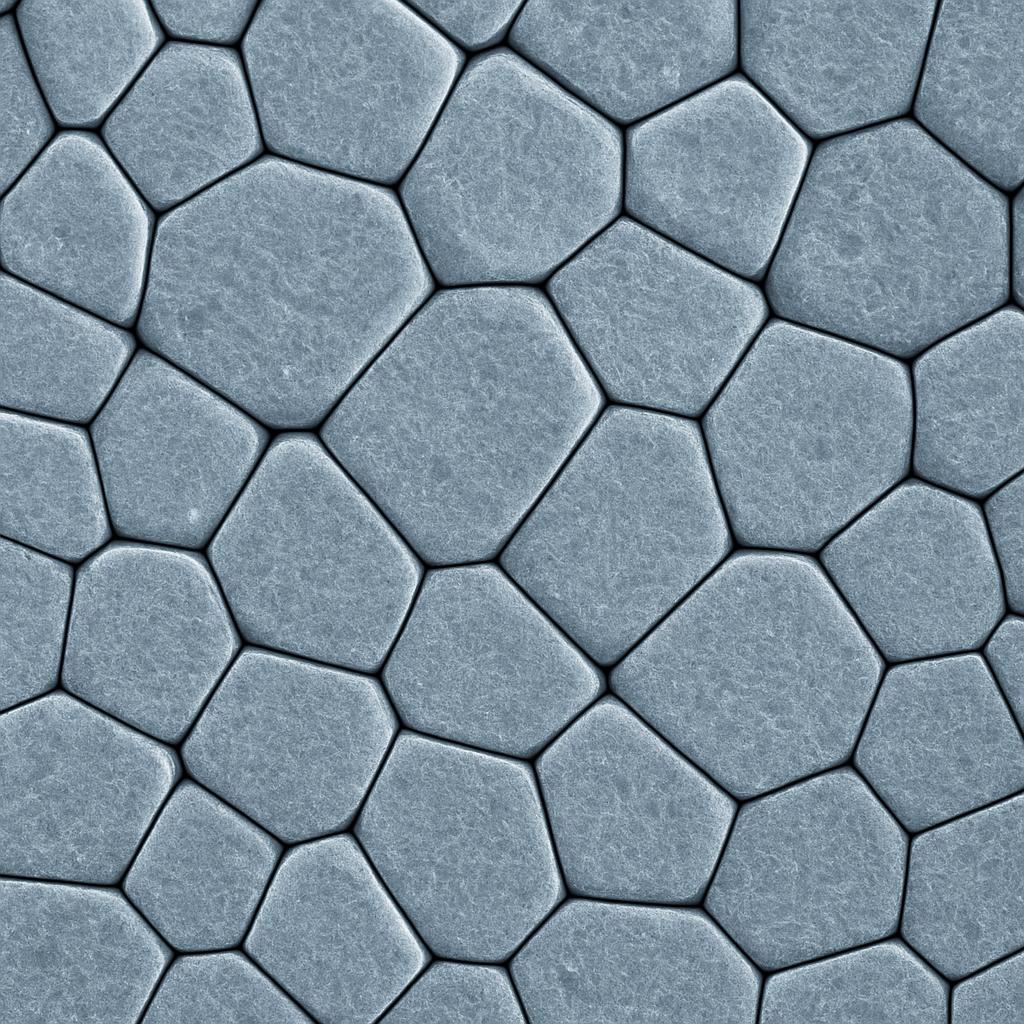
Stabilizing oxides play a crucial role in this ceramic’s chemical performance. Yttria (Y₂O₃) creates oxygen vacancies that actually enhance chemical stability in acidic environments. Magnesia (MgO) stabilization provides superior performance in alkaline conditions. Ceria (CeO₂) offers excellent resistance in both oxidizing and reducing atmospheres. These additives make it adaptable to various chemical challenges.
Stabilizer Type | Optimal Content | Best Chemical Resistance In | Limitations |
---|---|---|---|
Yttria (Y₂O₃) | 3-8 mol% | Strong acids, oxidizing environments | Moderate alkaline resistance |
Magnesia (MgO) | 8-10 mol% | Strong bases, alkaline slurries | Lower acid resistance |
Ceria (CeO₂) | 12-15 mol% | Reducing atmospheres, sulfur compounds | Higher cost |
Microstructural features significantly impact this material’s chemical resistance. Smaller grain sizes (0.2-0.5 μm) typically offer better chemical durability by reducing grain boundary area susceptible to preferential attack. Porosity must be minimized, as each 1% increase in open porosity can reduce chemical resistance by 5-15%.
How Does Zirconia Perform In Strong Acidic Environments?
Zirconia demonstrates remarkable stability in most acidic environments, maintaining structural integrity and surface properties where other ceramics rapidly degrade. Comprehensive testing across various acid types reveals an exceptional performance profile.
Consider these impressive results: In concentrated sulfuric acid (98% H₂SO₄) at 100°C, high-purity yttria-stabilized materials shows corrosion rates below 0.001 mm/year—over 50 times better than alumina and 10 times better than silicon nitride. In hydrochloric acid (37% HCl), it maintains similar superiority, with negligible mass loss after 1000-hour exposure tests.
Acid Type | Concentration | Temperature | Zirconia Corrosion Rate | Alumina Corrosion Rate |
---|---|---|---|---|
Sulfuric (H₂SO₄) | 98% | 100°C | 0.001 mm/year | 0.05-0.1 mm/year |
Hydrochloric (HCl) | 37% | 80°C | <0.002 mm/year | 0.1-0.2 mm/year |
Nitric (HNO₃) | 70% | 120°C | <0.001 mm/year | 0.01-0.03 mm/year |
Hydrofluoric acid (HF) represents the primary limitation to the acid resistance of this material. HF attacks the oxygen bonds, forming soluble zirconium fluoride complexes. Even at concentrations as low as 5%, significant degradation occurs. For HF applications, alternative materials like certain polymers or platinum group metals are recommended instead.
Long-term immersion testing confirms durability in acidic media. After 5-year exposure tests in industrial acid environments, yttria-stabilized components retained over 95% of their original mechanical strength and dimensional stability. This translates to practical service lifespans exceeding 15 years in many acid handling applications.
When Does Zirconia Excel In Alkaline Conditions?
Alkaline environments present distinct challenges that zirconia handles with remarkable effectiveness. From caustic processing solutions to molten salts, it demonstrates stability that distinguishes it from competing materials.
What makes this truly remarkable is zirconia’s resistance to concentrated sodium hydroxide (NaOH) and potassium hydroxide (KOH)—chemicals that rapidly degrade silicon-based ceramics. In 50% NaOH at 90°C, the material shows corrosion rates below 0.003 mm/year, while silicon carbide experiences rates 20-30 times higher due to hydroxide attack on Si-C bonds.
Alkaline Environment | Temperature | Zirconia Performance | Silicon Carbide Performance |
---|---|---|---|
50% NaOH solution | 90°C | Excellent (<0.003 mm/yr) | Poor (0.06-0.09 mm/yr) |
Molten glass (20% alkaline) | 1500°C | Excellent (2+ year life) | Poor (rapid failure) |
Cement slurry (pH 12-13) | 85°C | Excellent (<0.001 mm/yr) | Fair (0.02-0.04 mm/yr) |
High-temperature alkaline melts represent particularly challenging environments where zirconia truly shines. In glass melting operations, where molten glass contains up to 20% alkaline oxides at temperatures exceeding 1500°C, magnesia-stabilized components can operate continuously for years. This performance far surpasses alumina, which typically fails within months under identical conditions.
The alkaline corrosion mechanism differs fundamentally from other ceramics. While silicon-based ceramics undergo hydroxide ion attack that breaks Si-O bonds, zirconia’s structure resists hydroxyl penetration. The few reactions that do occur tend to form stable surface compounds rather than soluble species that would accelerate material loss.
Which Specialized Chemical Environments Showcase Zirconia’s Superiority?
Beyond conventional acids and bases, numerous specialized chemical environments highlight zirconia’s exceptional performance advantages. These challenging conditions often represent the true test of a material’s chemical durability.
You might be surprised to learn that it exhibits remarkable stability in both oxidizing and reducing atmospheres—a rare combination among engineering ceramics. In oxygen-rich environments at 1000°C, the material maintains its structure and properties indefinitely. Equally impressive, in hydrogen atmospheres that reduce most oxide ceramics, properly stabilized components show minimal degradation.
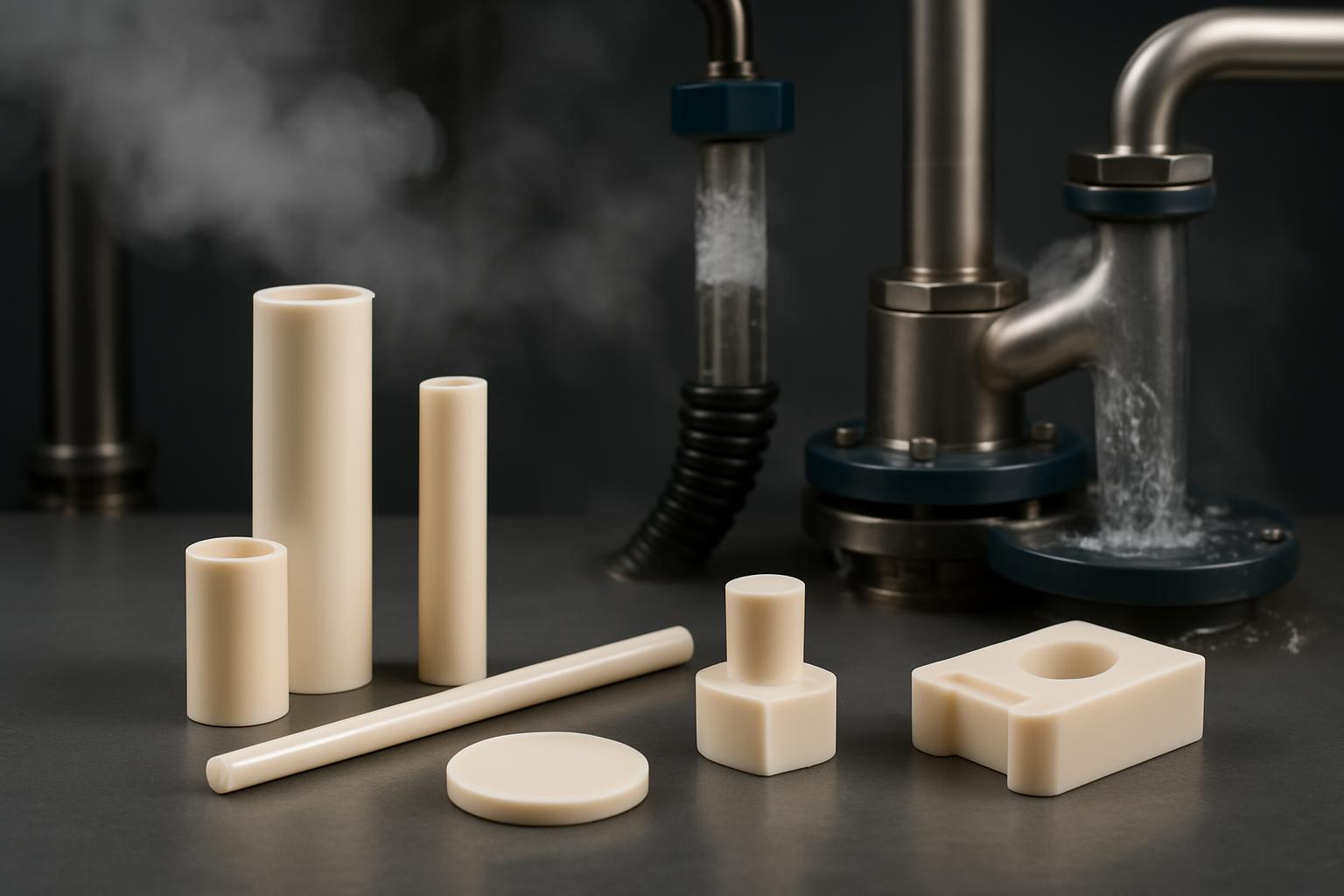
Halogen environments represent particularly aggressive conditions where this material demonstrates clear superiority. In chlorine gas at 800°C, corrosion rates remain below 0.01 mm/year, while alumina experiences rates 5-8 times higher. Even in fluorine-containing atmospheres (excluding HF), this ceramic outperforms most alternatives.
Specialized Environment | Key Challenge | Zirconia Performance | Best Alternative Material |
---|---|---|---|
Chlorine gas (800°C) | Oxidation, chloride formation | Excellent (<0.01 mm/yr) | Nickel alloys (0.05 mm/yr) |
Hydrogen atmosphere (1200°C) | Reduction of oxide structure | Very good (minimal reduction) | Platinum (excellent but costly) |
Molten nitrate salts (565°C) | Dissolution, thermal cycling | Excellent (negligible loss) | Inconel (good but higher cost) |
Organic solvents and petrochemical fluids pose minimal threat to zirconia ceramics. From aggressive industrial cleaning agents to process solvents like dimethylformamide (DMF) and dimethyl sulfoxide (DMSO), this material remains chemically inert. This property makes it ideal for precision components in pharmaceutical manufacturing where product purity is paramount.
How Do Different Zirconia Grades Compare In Chemical Resistance?
Not all zirconia ceramics offer identical chemical resistance. Various grades and formulations provide optimized performance for specific environments, making proper selection critical for maximizing component lifespan.
Here’s what you need to know: Fully stabilized zirconia (FSZ), containing 8 mol% Y₂O₃, offers the best overall chemical stability across diverse environments. Its cubic crystal structure eliminates phase transformation concerns and provides consistent performance in fluctuating conditions. owever, this comes at the cost of reduced mechanical properties compared to partially stabilized variants.
Zirconia Grade | Composition | Acid Resistance (1-10) | Alkali Resistance (1-10) | Best Applications |
---|---|---|---|---|
Fully Stabilized (FSZ) | 8 mol% Y₂O₃ | 9 | 8 | Chemical processing, sensors |
Partially Stabilized (PSZ) | 3-4 mol% Y₂O₃ | 8 | 7 | Pump components, valves |
Tetragonal (TZP) | 2-3 mol% Y₂O₃ | 7 | 6 | Structural components |
Magnesia Stabilized | 8-10 mol% MgO | 6 | 9 | Alkali processing, glass contact |
Partially stabilized zirconia (PSZ), typically containing 3-4 mol% Y₂O₃, balances chemical resistance with superior mechanical properties. This makes it ideal for applications requiring both chemical durability and structural strength. PSZ performs particularly well in acidic environments but may show slightly reduced resistance in strong bases compared to FSZ.
Zirconia-based composites offer tailored performance profiles. Zirconia-toughened alumina (ZTA) combines alumina’s excellent wear resistance with improved chemical durability from the zirconia phase. Alumina-toughened zirconia (ATZ) maintains most of the material’s chemical resistance while enhancing mechanical reliability. These composite materials expand the application range considerably.
What Testing Methods Verify Zirconia’s Chemical Resistance Claims?
Rigorous testing protocols are essential for validating zirconia’s chemical resistance claims and ensuring appropriate material selection for specific applications. Standard and advanced methods provide complementary insights into performance expectations.
The bottom line is this: Static immersion testing remains the foundation of chemical resistance evaluation. Following standards like ASTM C1161 and ISO 10545-13, these tests involve exposing samples to target chemicals under controlled conditions for extended periods. Weight change, dimensional stability, and surface appearance provide primary performance indicators.
Testing Method | Key Parameters Measured | Test Duration | Best For Predicting |
---|---|---|---|
Static Immersion (ASTM C1161) | Weight change, visual changes | 1000+ hours | Long-term stability |
Electrochemical (ASTM G5) | Corrosion current, polarization | 24-48 hours | Reaction mechanisms |
High-Pressure Autoclave | Combined T/P effects | 100-500 hours | Extreme environments |
Surface Analysis (XPS/SEM) | Chemical composition changes | N/A (analysis) | Reaction mechanisms |
Electrochemical testing techniques provide deeper insights into zirconia’s corrosion mechanisms. Potentiodynamic polarization and electrochemical impedance spectroscopy reveal reaction kinetics and identify potential passivation behaviors. These methods are particularly valuable for environments where electrical conductivity plays a role in degradation processes.
Surface analysis techniques complement bulk testing by revealing chemical interaction mechanisms. X-ray photoelectron spectroscopy (XPS) identifies surface chemical changes with depth resolution to 5-10 nm. Scanning electron microscopy with energy dispersive spectroscopy (SEM-EDS) maps elemental distribution changes resulting from chemical exposure. These techniques help optimize zirconia formulations for specific applications.
Which Industries Benefit Most From Zirconia’s Chemical Durability?
Zirconia’s exceptional chemical resistance creates substantial value across diverse industries, with some sectors gaining particularly significant advantages from this unique material property.
What this means for you: The chemical processing industry represents perhaps the largest beneficiary of zirconia’s durability. Pump components, valve seats, flow liners, and agitator bearings made from this material routinely deliver 3-5 times longer service life than metal alternatives in corrosive media. The resulting reduction in maintenance downtime and replacement costs typically delivers ROI within 12-18 months despite higher initial costs.
Industry | Key Applications | Primary Chemical Challenges | Value Proposition |
---|---|---|---|
Chemical Processing | Pumps, valves, seals | Acids, bases, chlorides | 3-5× component life |
Semiconductor | Wafer handling, gas distribution | HF, plasma, cleaning chemicals | Contamination reduction |
Medical | Implants, surgical tools | Body fluids, sterilization chemicals | Biocompatibility |
Energy | Fuel cells, electrolyzers | High-temperature electrolytes | Efficiency, durability |
Semiconductor manufacturing relies on zirconia components for ultrapure processing environments. Wafer handling tools, gas distribution components, and plasma-resistant parts benefit from zirconia’s combination of chemical inertness, high purity, and minimal particle generation. As process chemicals become increasingly aggressive to enable smaller feature sizes, this material’s importance continues to grow.
Medical applications leverage zirconia’s biocompatibility alongside its chemical stability. Dental implants, orthopedic components, and surgical instruments resist both bodily fluids and aggressive sterilization chemicals. The material’s chemical inertness prevents ion leaching that could trigger adverse patient reactions, while its durability ensures long-term functional performance.
Conclusion
Zirconia’s exceptional chemical resistance across diverse environments makes it a standout material choice for the most demanding industrial applications. From concentrated acids to caustic bases, halogens to organic solvents, properly selected zirconia grades deliver performance that other ceramics simply cannot match. This translates directly to longer component lifespans, reduced maintenance requirements, and improved operational reliability.
The data clearly shows that zirconia components in chemically aggressive environments typically deliver 300-500% longer service life than conventional alternatives, resulting in lifetime cost reductions of 40-60% despite higher initial investment.
For your next project involving harsh chemical environments, partner with Global Industry to identify the optimal zirconia grade and component design. Our engineering team specializes in material selection for extreme chemical conditions, ensuring you receive the maximum performance benefit from this unique material property.
Contact our technical support team today to discuss your specific chemical resistance requirements and discover how our advanced zirconia solutions can transform your most challenging applications.
FAQ Section
Q1: Can zirconia withstand hydrofluoric acid exposure?
Zirconia shows excellent resistance to most acids, but hydrofluoric acid (HF) is a significant exception. HF attacks zirconia’s oxygen bonds, forming soluble zirconium fluoride complexes that cause material degradation. At room temperature in concentrations below 5%, zirconia may show limited short-term resistance but is not recommended for prolonged use. Certain specially formulated zirconia composites with rare earth additions (like cerium) offer slightly improved HF resistance but remain unsuitable for continuous exposure. For HF applications, carbon-based materials, specific polymers (like PTFE), or platinum metals are typically more appropriate choices.
Q2: How does zirconia’s chemical resistance compare to silicon carbide?
Zirconia and silicon carbide offer complementary chemical resistance profiles depending on the specific environment. In strong alkaline conditions, zirconia significantly outperforms silicon carbide, withstanding up to 50% NaOH solutions while silicon carbide undergoes gradual hydrolysis in strong bases. Zirconia also excels in oxidizing acids like nitric and sulfuric acid. However, silicon carbide performs better in hydrofluoric acid and offers advantages in reducing environments and high-temperature hydrocarbon settings. Silicon carbide’s thermal conductivity (120-170 W/m·K) far exceeds zirconia’s (2-3 W/m·K), making it preferable for corrosive environments requiring rapid heat dissipation.
Q3: Does the stabilizer type affect zirconia’s chemical resistance?
Yes, stabilizer type significantly impacts chemical resistance. Yttria-stabilized zirconia (YSZ) performs best in most acidic environments, particularly sulfuric and hydrochloric acids. Magnesia-stabilized zirconia offers superior performance in alkaline environments but may experience stabilizer leaching under acidic conditions. Ceria-stabilized zirconia shows excellent stability in reducing environments, making it suitable for sulfur-containing applications. Calcia-stabilized zirconia costs less but offers generally inferior chemical stability for harsh environments. Stabilizer content also matters—fully stabilized zirconia (8-10 mol% stabilizer) typically provides optimal chemical stability, while partially stabilized variants prioritize mechanical performance.
Q4: Can zirconia survive in molten metal environments?
Zirconia performs exceptionally well in many molten metal environments, making it ideal for metallurgical applications. It withstands non-ferrous molten metals like aluminum, copper, zinc, and lead with minimal reaction or dissolution. In molten iron, cobalt, or nickel, zirconia experiences limited dissolution, particularly at temperatures above 1600°C. Contact with molten metals under reducing atmospheres may cause partial reduction of zirconia to substoichiometric oxides or metallic zirconium, affecting structural integrity. Performance can be enhanced through special coatings or composite designs, such as zirconia-iridium composites that show significantly improved stability in molten platinum group metals.
Q5: How does porosity affect zirconia’s chemical resistance?
Porosity has a profound impact on chemical resistance. High-density zirconia (>99% theoretical density) provides optimal chemical protection by minimizing surface area exposed to corrosive media and eliminating interconnected pathways for chemical penetration into the material interior. Each 1% increase in open porosity can increase corrosion rates by 5-15%, depending on the chemical environment. Pores in the microstructure not only increase surface area, but can act as stress concentration points, accelerating crack formation under chemical attack. However, in certain applications like catalyst supports or biomedical implants, controlled porosity (typically 10-25%) may be necessary, requiring a balance between functionality and chemical durability.