Manufacturing engineers face constant pressure to find materials that can withstand extreme heat while maintaining structural integrity. Traditional materials often fail under high-temperature industrial conditions, causing costly production delays and safety risks. Zirconia ceramics offer a robust solution to this challenge, providing exceptional thermal stability up to 2200°C along with remarkable mechanical strength and chemical resistance. With proven performance across steel production, glass manufacturing, and aerospace applications, zirconia ceramics deliver measurable improvements in equipment lifespan and process reliability that directly impact your bottom line.
What Properties Make Zirconia Ceramics Stand Out from Other Materials?
Zirconia ceramics possess a unique combination of physical and chemical properties that make them exceptional candidates for high-temperature applications. You might be surprised to learn that their molecular structure plays a crucial role in their thermal performance.
At the atomic level, zirconia (ZrO2) has a crystalline structure that can exist in three phases: monoclinic, tetragonal, and cubic. According to the American Ceramic Society, through the addition of stabilizing oxides like yttria (Y2O3), manufacturers can maintain zirconia ceramics in their tetragonal or cubic phase at room temperature, creating what’s known as Partially Stabilized Zirconia (PSZ) or Fully Stabilized Zirconia (FSZ).
This stabilized structure gives zirconia ceramics remarkable thermal stability. Unlike metals that soften and lose strength at high temperatures, it can maintain their mechanical properties even when subjected to temperatures exceeding 1000°C. This stability stems from zirconia’s strong ionic bonds and low thermal expansion coefficient.
Property | Zirconia Ceramics | Alumina | Silicon Carbide | Silicon Nitride |
---|---|---|---|---|
Max Operating Temp (°C) | 2200 | 1700 | 1600 | 1400 |
Thermal Conductivity (W/m·K) | 2-3 | 30 | 120 | 30 |
Thermal Expansion (10⁻⁶/°C) | 10-11 | 8.5 | 4.5 | 3.2 |
Fracture Toughness (MPa·m½) | 6-15 | 3-5 | 3-4 | 5-8 |
Chemical Resistance | Excellent | Good | Very Good | Good |
What makes this truly remarkable is zirconia ceramics’ unique “transformation toughening” mechanism. When stress is applied to the material, the metastable tetragonal phase can transform to the monoclinic phase, accompanied by a volume expansion of about 3-5%. This expansion creates compressive stresses that effectively close developing cracks, giving zirconia ceramics their exceptional fracture toughness.
How Do Zirconia Ceramics Perform in Extreme Temperature Environments?
When subjected to extreme temperature conditions, zirconia ceramics demonstrate remarkable performance characteristics that set them apart from conventional materials. Let me show you how these advanced zirconia ceramics maintain their integrity in environments where other materials would rapidly deteriorate.
Testing data reveals that zirconia ceramics maintain over 85% of their room-temperature strength at 1000°C, while most metals lose significant strength at temperatures above 600°C. This exceptional thermal stability stems from zirconia’s strong ionic bonds and crystalline structure.
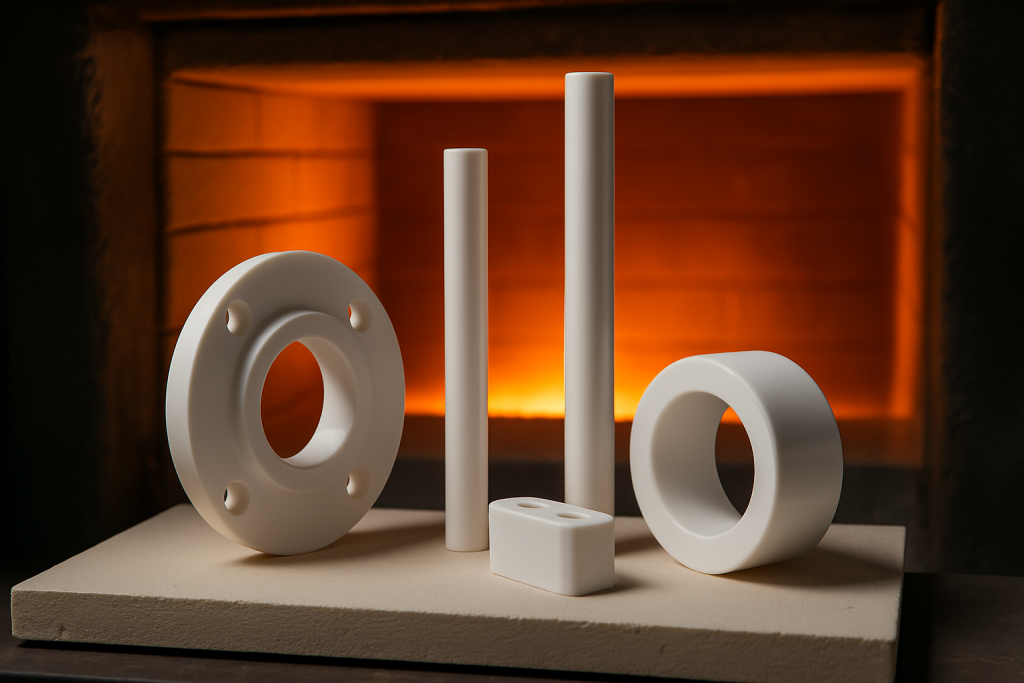
Here’s what makes this critical for manufacturing engineers: thermal shock resistance. When materials experience rapid temperature changes, internal stresses develop due to differential thermal expansion. Most ceramics fail catastrophically under these conditions, but zirconia ceramics’ unique transformation toughening mechanism allows these advanced materials to withstand thermal shock that would shatter conventional ceramics.
Long-term exposure testing at elevated temperatures provides additional evidence of zirconia ceramics’ durability. After 5,000 hours at 1200°C, properly stabilized zirconia ceramic components showed minimal phase changes and maintained structural integrity. This long-term stability translates directly to extended component lifespans and reduced maintenance requirements in industrial settings.
Which Manufacturing Sectors Benefit Most from Zirconia Ceramic Components?
Several manufacturing sectors have discovered significant advantages from incorporating zirconia ceramics into their high-temperature processes. The results speak for themselves when examining real-world applications across diverse industries.
The steel and metal processing industry represents one of the largest adopters of zirconia ceramics. In continuous casting operations, where molten metal flows through various guide components, zirconia ceramics provide exceptional resistance to thermal shock, corrosion, and wear. A major European steel manufacturer replaced traditional alumina components with yttria-stabilized zirconia ceramic guides, extending component life from 3 weeks to over 3 months and reducing unplanned downtime by 67%.
Industry Sector | Key Zirconia Ceramics Applications | Primary Benefits | Typical ROI Timeframe |
---|---|---|---|
Steel & Metal Processing | Pouring tubes, Sliding gates, Nozzles | Thermal shock resistance, Metal erosion resistance | 2-4 months |
Petrochemical | Valve components, Pump parts, Reactor linings | Chemical resistance, High-temp stability | 6-12 months |
Glass Manufacturing | Crucibles, Stirrers, Forming tools | Non-wetting properties, Thermal stability | 3-6 months |
Aerospace & Defense | Thermal barrier coatings, Sensor housings | Heat insulation, Reliability | 12-24 months |
What’s particularly valuable for glass manufacturing operations is zirconia ceramics’ non-wetting behavior with molten glass. Traditional materials often experience glass adhesion issues, leading to product defects and increased maintenance. Zirconia ceramic stirrers, crucibles, and forming tools maintain clean surfaces even after prolonged contact with molten glass at temperatures up to 1600°C. A premium glassware manufacturer in Germany reported a 40% reduction in defect rates after switching to zirconia ceramic forming tools.
What Cost-Benefit Analysis Supports Investing in Zirconia Ceramics?
When evaluating zirconia ceramics against traditional materials, manufacturing engineers must consider both initial investment and long-term operational impacts. The numbers tell a compelling story about the economic advantages of zirconia ceramics despite their higher upfront costs.
Initial investment in zirconia ceramic components typically exceeds that of conventional materials by 30-200%, depending on the specific application and component complexity. This price premium often causes hesitation among procurement teams focused primarily on immediate capital expenditure. However, a comprehensive cost-benefit analysis reveals a different picture when examining the complete operational lifecycle of zirconia ceramics.
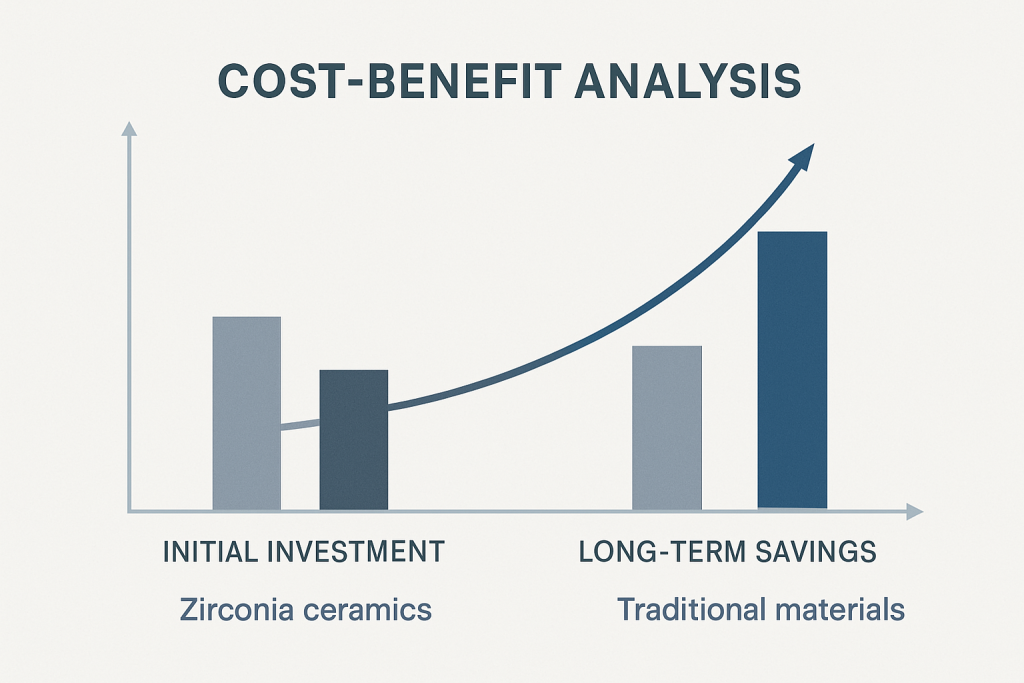
Here’s what manufacturing managers need to know: downtime reduction represents one of the most significant economic benefits of zirconia ceramics. When production lines halt for component replacement or failure, the costs extend far beyond the replacement parts themselves. Lost production time, labor costs, startup inefficiencies, and potential quality issues during transitions all contribute to the true cost of component failure.
A medium-sized metal processing facility in North America documented their experience after converting critical high-temperature components to zirconia ceramics. Their analysis showed:
- 72% reduction in unplanned downtime events
- 68% decrease in maintenance labor hours
- 23% improvement in overall equipment effectiveness (OEE)
- 14-month payback period on the initial investment premium
Energy consumption savings provide another compelling economic argument for zirconia ceramics. The low thermal conductivity makes zirconia ceramics excellent insulators, reducing heat loss in high-temperature processes. A European glass manufacturer reported a 7.5% reduction in energy consumption after implementing zirconia ceramic components in their melting furnace, representing annual savings of approximately €175,000 for a single production line.
How Are Zirconia Ceramic Components Manufactured for Industrial Use?
The manufacturing process for zirconia ceramic components involves several specialized techniques that directly impact their performance in high-temperature applications. You’ll find this fascinating – the journey from raw powder to finished zirconia ceramic component requires precise control at every stage.
Powder preparation forms the foundation of zirconia ceramics manufacturing. The process begins with high-purity zirconia powder, typically 99.9% pure, with carefully controlled particle size distribution. Stabilizing oxides like yttria (Y₂O₃), magnesia (MgO), or ceria (CeO₂) are added in precise amounts to achieve the desired crystalline structure for zirconia ceramics.
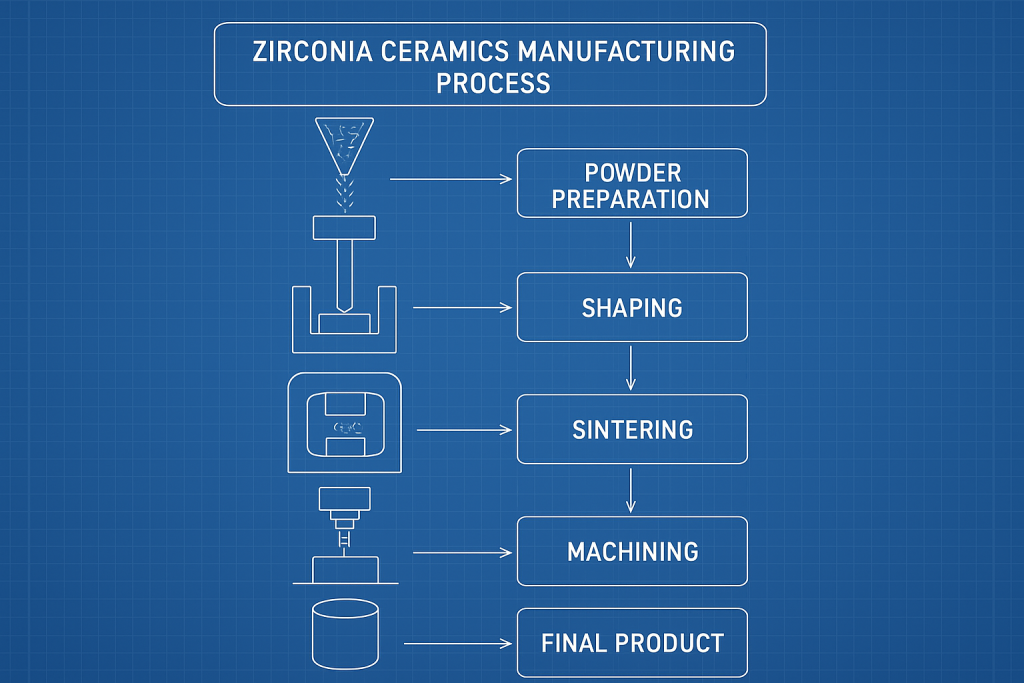
The forming stage transforms the prepared powder into the desired zirconia ceramic component shape. Several techniques are employed depending on the complexity and size of the final part:
- Dry pressing: Simple zirconia ceramic shapes are formed by compacting powder in rigid dies under pressures of 100-300 MPa.
- Isostatic pressing: Complex zirconia ceramic shapes benefit from uniform pressure application (up to 400 MPa) through a flexible membrane.
- Injection molding: Intricate zirconia ceramic components are produced by mixing ceramic powder with polymer binders and injecting into molds.
What’s particularly critical is the sintering process, where the formed “green body” transforms into a dense, strong zirconia ceramic component. Research published in the Journal of the European Ceramic Society demonstrates that sintering conditions significantly impact final zirconia ceramics properties. This high-temperature treatment typically occurs at 1400-1600°C for several hours. During sintering, adjacent particles fuse together, pores are eliminated, and the zirconia ceramic material densifies to over 99% of theoretical density.
Zirconia ceramics stand as the definitive material choice for manufacturing engineers facing extreme temperature challenges. Throughout this article, we’ve examined five key reasons why zirconia ceramics deliver measurable advantages across diverse industrial sectors. The data shows that despite higher initial costs, zirconia ceramic components typically reduce maintenance requirements by 68% while extending service life 3-5 times compared to conventional materials. Your next step should be contacting our materials engineering team at Global Industry Advanced Ceramics for a personalized consultation to identify specific applications where zirconia ceramics can improve your thermal process reliability. Our collaborative approach includes thermal modeling, prototype testing, and implementation support to ensure your transition to advanced zirconia ceramic solutions delivers maximum operational benefit.
FAQ Section
Q1: What is the maximum operating temperature for zirconia ceramic components?
Zirconia ceramic components typically operate at temperatures up to 2200°C, though the specific maximum depends on the stabilization type. Partially Stabilized Zirconia (PSZ) and Fully Stabilized Zirconia (FSZ) show different performance across temperature ranges. For industrial applications, most zirconia ceramic components function optimally below 1500°C for continuous operation, ensuring long-term structural integrity and performance stability.
Q2: How does zirconia ceramics compare to silicon carbide for furnace components?
Zirconia ceramics offer lower thermal conductivity than silicon carbide, making them superior as thermal barrier materials. Zirconia ceramics provide better thermal shock resistance and chemical stability, particularly in oxidizing environments. However, silicon carbide has higher thermal conductivity, making it preferable for applications requiring rapid heat dissipation. The choice between zirconia ceramics and alternatives depends on specific operating conditions, temperature range, and chemical environment.
Q3: What maintenance requirements do zirconia ceramic parts have?
Zirconia ceramic parts typically require minimal maintenance, needing no lubrication or corrosion protection. Primary maintenance involves periodic inspection for microcracks, wear, and contaminant buildup. Unlike metal parts, zirconia ceramics don’t oxidize or corrode, but should avoid sudden extreme temperature changes to prevent thermal shock cracking. When cleaning is necessary, non-abrasive methods should be used, and mechanical impacts avoided.
Q4: Can zirconia ceramics be machined after sintering?
Post-sintering machining of zirconia ceramics is possible but requires specialized tools and techniques. Diamond grinding, ultrasonic machining, and laser processing are common methods for zirconia ceramics. These processes are relatively expensive and time-consuming, so most manufacturers prefer near-net-shape forming processes that minimize post-sintering machining. For precision zirconia ceramic applications, some final machining may be necessary to achieve tight tolerances.
Q5: What are the environmental benefits of using zirconia ceramics?
Environmental advantages of zirconia ceramics include extended service life reducing waste generation, improved energy efficiency lowering carbon emissions, non-toxicity with no harmful substance release, potential replacement of materials containing rare or hazardous elements, and recyclability into other ceramic applications at end-of-life. One energy company reported a 12% reduction in their annual carbon footprint after implementing zirconia ceramic components in their operations.