Zircon sand is used worldwide in ceramics, refractories, and casting operations. But for many procurement managers and industrial safety officers, one question keeps surfacing—is zircon sand safe to use? This concern doesn’t come from nowhere. Zircon can naturally contain radioactive elements like uranium and thorium. These raise real issues for workplace safety, regulatory compliance, and even waste handling. So, what’s the solution? The good news is that with the right information and controls, using zircon can be safe and compliant.
This article outlines every key detail B2B buyers and decision-makers need to know about zircon sand and radiological safety. Here’s why you can trust this resource: It’s based on industry best practices, international standards, and real use-case insights across sectors like ceramics, metal casting, and industrial manufacturing.
What is zircon sand and how is it used?
Zircon sand is a naturally occurring mineral primarily composed of zirconium silicate. It’s extracted from heavy mineral sands and refined for industrial use. One of its key strengths is thermal stability, making it ideal for high-temperature applications.
Let’s break this down. Zircon sand is typically found in Australia, South Africa, and parts of Asia. It is separated from other minerals using techniques like electrostatic and magnetic processing. From there, it’s packaged and shipped globally.
Industrially, zircon sand is commonly used in:
- Foundry casting, where it forms part of molds for steel and iron
- Ceramic glazes and opacifiers, especially in tiles and sanitaryware
- Refractories, such as furnace linings and kiln bricks
Its high melting point and low reactivity make it versatile. However, not all zircon is the same. Natural zircon contains small amounts of radioactive elements. These are naturally embedded during the mineral’s formation.
Here’s the catch. While its industrial value is undeniable, the presence of radioactivity—however minimal—brings safety and regulatory issues into the spotlight.
Industrial Application | Purpose | Temperature Resistance |
---|---|---|
Casting molds | Shape retention during pours | Up to 2,200°C |
Ceramic glazes | Opacity and smooth finish | 1,200–1,400°C |
Refractories | Insulation and lining | 1,800–2,000°C |
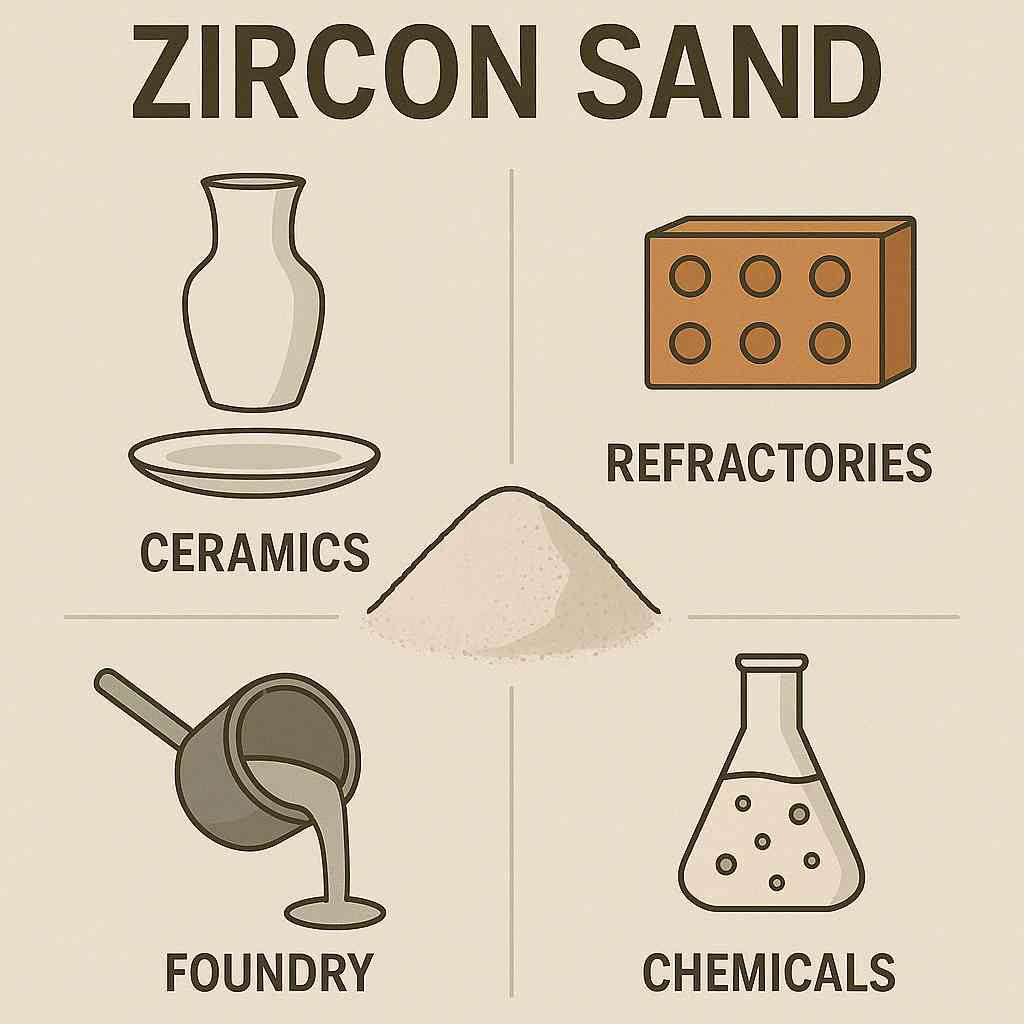
This image shows where zircon sand is applied across multiple industries including ceramics and metallurgy.
How does zircon sand become a radiological concern?
The issue stems from trace amounts of uranium and thorium found in natural zircon. These elements are alpha emitters, meaning they release radiation that can be harmful if ingested or inhaled.
Here’s what makes this tricky. While zircon itself is stable, processing it—especially crushing or grinding—can release fine dust particles. These particles can carry radioactive isotopes into the air. If inhaled, they may settle in the lungs, increasing long-term exposure.
Some countries set threshold values for natural radioactivity in industrial materials. If zircon exceeds these limits, it’s classified under naturally occurring radioactive material (NORM) regulations. That affects how it’s handled, stored, and disposed of.
In low-volume or tightly controlled use cases, the radiological risk may be minimal. But in heavy-use environments like zircon flour production or sandblasting, the exposure could exceed recommended limits.
To make matters worse, repeated handling or storage in unventilated areas can allow radioactive dust to build up, increasing cumulative exposure for workers and nearby personnel.
Element | Radioactivity Type | Potential Hazard |
---|---|---|
Uranium | Alpha emission | Lung and bone exposure |
Thorium | Alpha emission | Internal radiation dose |
What are the typical exposure pathways for workers?
Radiological safety isn’t just about measuring radiation in raw materials. It’s also about understanding how that radiation can reach people.
So, how does exposure happen? There are three main ways:
- Inhalation of airborne dust: This is the biggest concern, especially during grinding, cutting, or handling of dry zircon sand.
- Skin contact: Less risky, but still worth noting. Handling zircon without gloves may allow fine particles to settle on the skin.
- Surface contamination: Over time, zircon particles can settle on floors, tools, and work surfaces. Without proper cleaning, this builds up.
Secondary exposure is also a threat. Workers may carry contaminated dust on clothing or equipment, unintentionally bringing it into break rooms or homes.
Here’s the good news. Most of these risks are manageable with clear procedures and protective gear. But without them, daily contact—even if small—can accumulate over time.
Exposure Path | Risk Level | Common Scenario |
---|---|---|
Inhalation | High | Grinding zircon flour |
Skin Contact | Low | Manual handling |
Equipment | Medium | Contaminated surfaces |
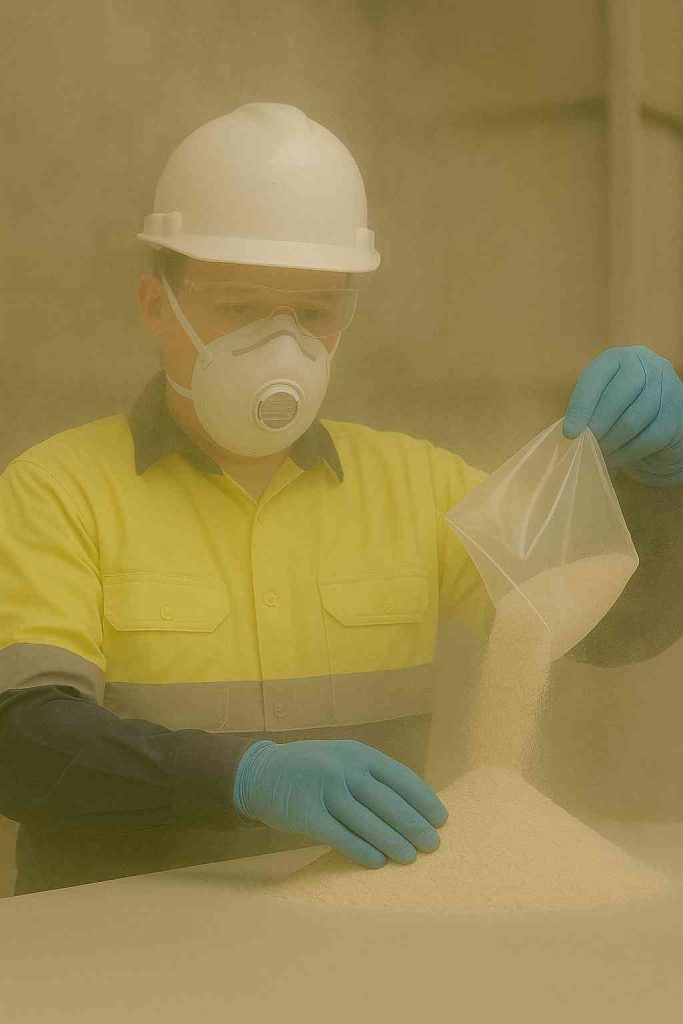
This image illustrates airborne dust risk during zircon sand handling operations.
Which industries face the highest radiological exposure?
Not all users of zircon sand are equally affected. Some industries rely heavily on bulk material use and manual processing, raising exposure levels.
Let’s look at the highest-risk sectors:
- Foundries: Zircon is widely used for casting molds. Workers often handle large volumes and are exposed during mold preparation.
- Ceramics: Zircon is crushed into flour to be used in tile glazes. The crushing process increases dust generation.
- Zircon flour plants: Facilities that mill zircon to micron levels face the highest airborne dust risks.
The risk increases when ventilation is poor or when dust controls are missing. Even the storage of large zircon bags can release dust when handled carelessly.
Industry | Zircon Use Type | Exposure Source |
---|---|---|
Foundry | Mold casting | Sand pouring and removal |
Ceramics | Tile glaze | Flour grinding and spraying |
Milling | Fine powder | Crushing and packing |
What regulations govern zircon sand safety?
If you work with zircon, you’re subject to several rules—some global, some regional. These are in place to control radiation exposure and protect workers.
Here’s what you need to know. International standards like IAEA’s NORM guidelines set broad limits. For example, the exemption level for materials with natural radioactivity is typically around 1 Bq/g.
In the EU, REACH regulations may require documentation on zircon’s radioactive content. In the US, OSHA requires hazard communication under HAZCOM if zircon exceeds threshold levels.
Labels, transport documents, and safety data sheets (SDS) must all include this information when applicable. Failing to comply can lead to shipment rejections, fines, or worse.
The rules are clear: Know your source, test your batch, and document everything.
Regulatory Body | Region | Primary Concern |
---|---|---|
IAEA | Global | Radiation thresholds |
OSHA | USA | Workplace exposure |
REACH | EU | Chemical safety and labeling |
How can companies monitor radiation from zircon?
You can’t control what you don’t measure. Radiation monitoring is the first step in keeping workplaces safe.
Let’s go through the tools.
- Geiger counters: Used for general ambient radiation checks.
- Dosimeters: Worn by workers to track personal exposure over time.
- Dust samplers: Collect airborne particles for lab analysis.
Monitoring frequency depends on volume of use and local regulations. High-volume users may need weekly checks. Lower volume may only require quarterly or annual testing.
Want to avoid surprises? Start with a baseline test, document all readings, and establish a control plan if levels exceed guidance.
Tool | Purpose | Frequency |
---|---|---|
Geiger Counter | Check ambient levels | Weekly |
Dosimeter | Track personal dose | Continuous |
Dust Sampler | Analyze airborne particles | Monthly |
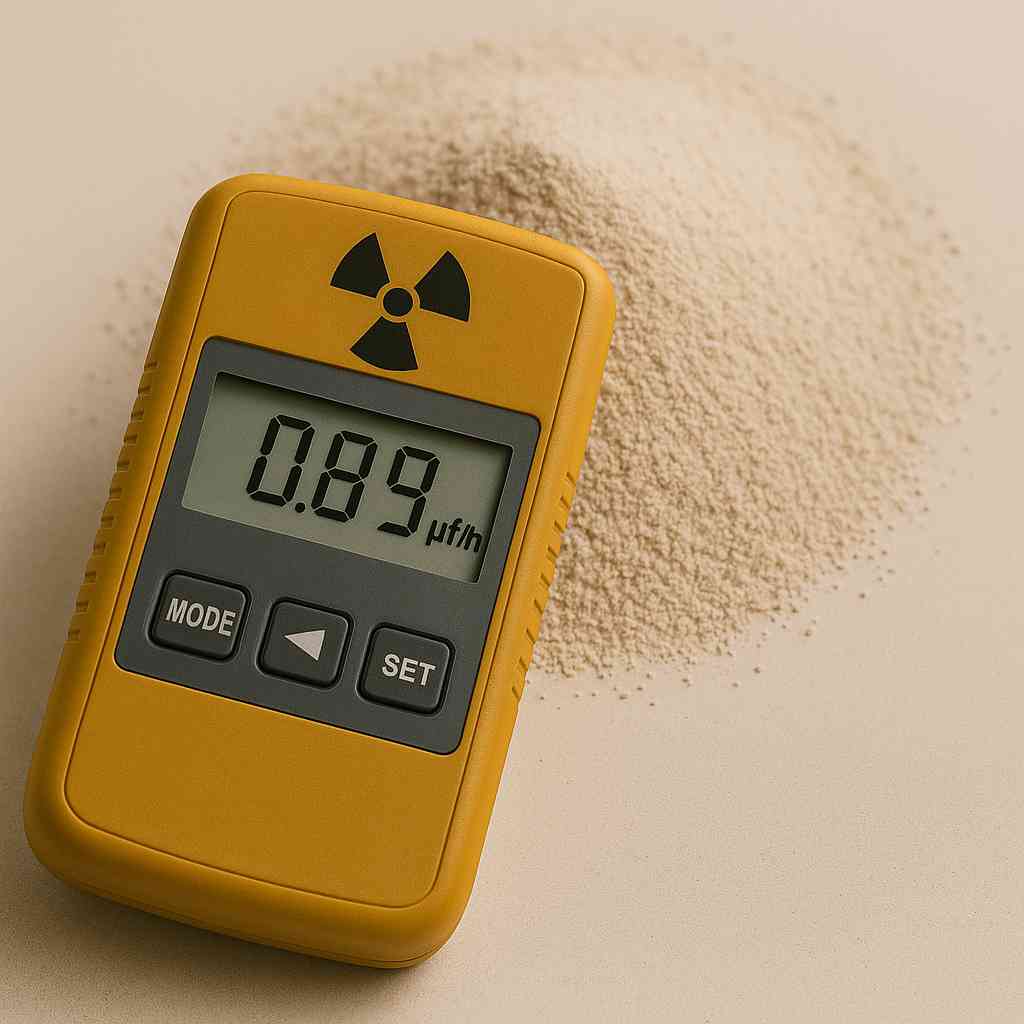
This image shows common instruments for radiation measurement in zircon handling.
What are the best practices for minimizing exposure?
Here’s where prevention comes in. By applying smart controls, companies can significantly reduce worker exposure to zircon’s radiological risks.
Start with:
- Engineering controls: Local exhaust ventilation, enclosed handling systems, and HEPA filters.
- PPE: Gloves, masks (preferably P100 or N100), and protective suits when needed.
- Training: Workers must understand the materials they’re handling and how to protect themselves.
Routine cleaning is also key. Dry sweeping should be avoided since it spreads dust. Instead, use vacuum systems or wet methods.
Even simple changes—like sealing storage bags—can reduce dust release.
Control Type | Example | Benefit |
---|---|---|
Engineering | Ventilation | Reduces airborne dust |
Administrative | Training | Improves compliance |
PPE | Respirator | Lowers inhalation risk |
How should zircon sand waste be handled?
Waste zircon can’t just be tossed in the trash. Depending on the radioactivity level, it may need special disposal.
Here’s how to handle it safely:
- Classify the waste: Test for radioactivity. If above threshold, label it as hazardous.
- Use approved containers: Waste should be sealed in dust-tight packaging.
- Arrange for disposal: Work with licensed waste handlers experienced in NORM material.
You may also need to report the waste volume and disposal method to authorities, depending on your location.
Improper disposal can lead to environmental violations or community health complaints.
Waste Type | Disposal Method | Handling Notes |
---|---|---|
Low-level dust | Landfill (approved) | With protective liner |
High-level waste | Licensed NORM facility | Requires permit |
Contaminated PPE | Hazardous waste stream | Must be tracked |
What are the alternatives to zircon sand in sensitive applications?
For some industries, switching to non-radioactive substitutes is the safest option. While no material is a perfect match, several can replace zircon in certain contexts.
Here are a few options:
- Alumina: High-temperature stability but may lack zircon’s casting precision.
- Silica: Widely available, but less stable at extreme heat.
- Mullite: Used in ceramics, similar thermal resistance but costlier.
Switching may affect product performance or cost structure, so it’s important to test thoroughly before changing.
Substitute | Use Case | Limitation |
---|---|---|
Alumina | Refractory bricks | High cost |
Silica | Mold backing | Lower heat resistance |
Mullite | Ceramic tiles | Limited supply |
Conclusion
So, what’s the takeaway for zircon users?
Zircon sand brings strong industrial value, but radiological safety must be taken seriously. With the right tools and controls, risks can be minimized. Businesses gain from better compliance, safer workspaces, and more informed decision-making.
FAQ Section
Q1: Does all zircon sand contain radioactive material?
Yes, nearly all natural zircon sand includes trace levels of radioactive elements like uranium and thorium. These elements are embedded within the mineral structure during its natural formation in the earth’s crust. The actual concentration depends on the geographical source of the zircon, with sands from some regions containing higher levels than others. While these levels are usually low, they can become a regulatory concern when used in bulk quantities or processed into finer particles. For this reason, many industrial buyers require material safety data and source-specific testing before purchase.
Q2: Is zircon sand dangerous to work with daily?
It can be, but only under certain conditions. The primary danger comes from prolonged inhalation of fine zircon dust, which may carry radioactive particles. If workers are consistently exposed to airborne dust without protection, especially during tasks like grinding or pouring, they could accumulate a measurable radiation dose over time. However, with standard workplace controls—like dust extraction systems, sealed handling equipment, and proper PPE—the risk can be kept well below occupational exposure limits. Routine training and monitoring are key to safe daily use.
Q3: What industries are most affected by zircon radiation?
Industries that handle large volumes of zircon or process it into fine powders tend to face the highest radiological exposure. These include metal casting facilities using zircon molds, ceramics manufacturers applying zircon-based glazes, and milling operations producing zircon flour. In these settings, workers are more likely to encounter airborne particles, which carry the greatest risk. Proper ventilation, industrial hygiene controls, and compliance with NORM regulations are especially critical in these industries to protect personnel and maintain legal compliance.
Q4: Are there exposure limits for workers handling zircon?
Yes, both international and regional bodies set exposure limits. For example, the IAEA recommends that occupational exposure should not exceed 20 millisieverts (mSv) per year, averaged over five years, with no single year exceeding 50 mSv. In the United States, OSHA and NRC (Nuclear Regulatory Commission) also provide standards for permissible exposure, often focused on airborne particulate concentration and surface contamination. Companies must monitor exposure using personal dosimeters, air sampling, and other tracking tools to ensure workers remain within legal thresholds.
Q5: Can zircon sand be safely transported internationally?
Yes, but it must meet regulatory transport labeling and documentation standards if radiation levels exceed defined limits.