Zircon sand plays a pivotal role across multiple sectors. Whether you’re sourcing materials for precision casting, ceramic tiles, or nuclear reactors, chances are zircon sand is already on your radar. But with so many options and technical standards out there, knowing exactly how zircon sand fits into your operations can be confusing.
This article solves that problem. It outlines how zircon sand is applied in real-world industry, not just in theory. From manufacturing foundry molds to protecting reactors, we’ll break down each use case clearly.
Here’s why you can trust this information—our insights are built on industrial standards, real-world applications, and sourcing knowledge used by decision-makers at companies like yours. If you’re considering zircon sand for procurement, engineering, or quality assurance, this guide gives you a direct understanding of what matters.
What Is Zircon Sand and Where Does It Come From?
Zircon sand is a natural mineral extracted from heavy mineral sands. Its core ingredient is zirconium silicate (ZrSiO₄), known for its thermal stability and chemical inertness. It often contains minor traces of titanium, iron, or hafnium. These features make it reliable for high-performance industrial use.
So, where does it come from? The largest producers include Australia, South Africa, and Indonesia. These countries supply over 80% of the world’s zircon sand through open-pit mining or beach dredging operations. Once mined, the material undergoes several refining steps such as electrostatic separation, magnetic separation, and milling to meet industrial purity standards.
There are different grades available, depending on purity and particle size. High-purity zircon (>66% ZrO₂+HfO₂) is preferred for ceramics and nuclear applications. Lower grades may serve casting or abrasive markets.
Why does this matter? Because the origin and grade of the zircon sand influence not just cost, but performance and compliance in regulated industries.
Grade Type | ZrO₂ + HfO₂ (%) | Typical Uses |
---|---|---|
Standard Foundry | 65–66% | Casting, refractory bricks |
Ceramic Grade | >66% | Tiles, sanitaryware |
Nuclear Grade | >99% (as zirconium metal) | Fuel rods, cladding |
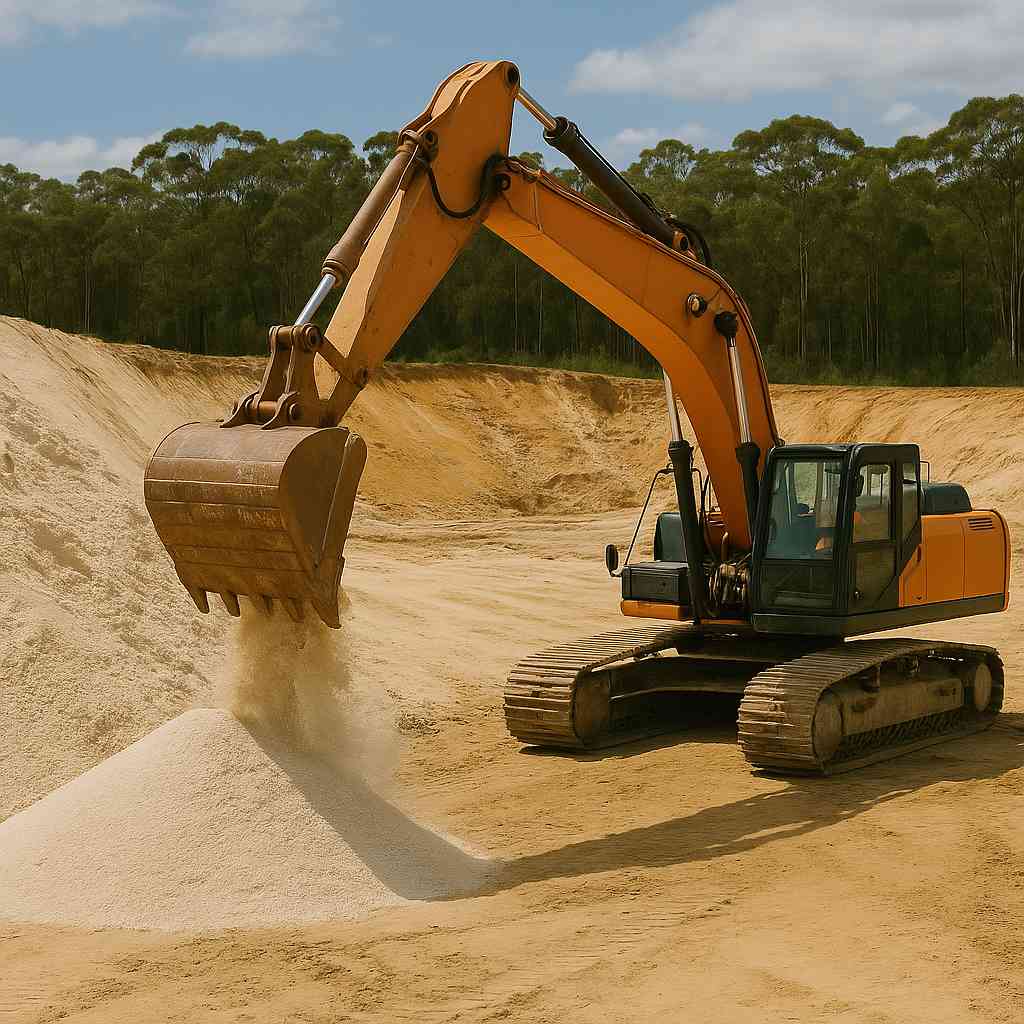
This image shows a zircon mining site where raw materials are extracted using large-scale equipment.
How Is Zircon Sand Used in Foundry Applications?
Foundries depend heavily on zircon sand. Its thermal stability, high melting point (over 2,200°C), and low thermal expansion make it ideal for metal casting molds.
Here’s the deal—casting with metals like steel or aluminum requires molds that won’t crack or deform. Zircon holds its shape and cools uniformly, reducing warpage in the final part. It’s used for both shell mold and core production, especially where dimensional precision is a priority.
Zircon’s consistent grain size ensures smoother surface finishes. It also helps limit metal penetration and reaction with the mold, reducing defects.
A major advantage? Reusability. With proper reconditioning, zircon sand can go through multiple casting cycles, making it cost-effective despite a higher upfront price.
Foundry Requirement | Why Zircon Works Well |
---|---|
High thermal stability | Withstands molten metal temperatures |
Low thermal expansion | Maintains dimensional accuracy |
Chemical inertness | Prevents mold-metal reactions |
Reusability | Lower total lifecycle cost |
Why Is Zircon Sand Critical in the Ceramics Sector?
Zircon is widely used in the ceramics industry, particularly in tiles, sanitaryware, and tableware.
Let’s break it down—zircon improves whiteness, opacity, and mechanical strength in ceramic glazes. It helps prevent transparency and discoloration at high firing temperatures. This is especially valuable in polished porcelain tiles and other visible surfaces where appearance matters.
The fine, uniform particles help manufacturers achieve consistent texture and surface quality. Its stability means it withstands multiple firings without degradation.
In many ceramic plants, zircon is applied in two key steps:
- Added to body composition for structural strength
- Applied as an opacifier in glazes for finish aesthetics
Ceramic Function | Role of Zircon |
---|---|
Body Strength | Improves hardness and thermal resistance |
Surface Finish | Increases whiteness and smoothness |
Opacification | Masks background patterns/colors |
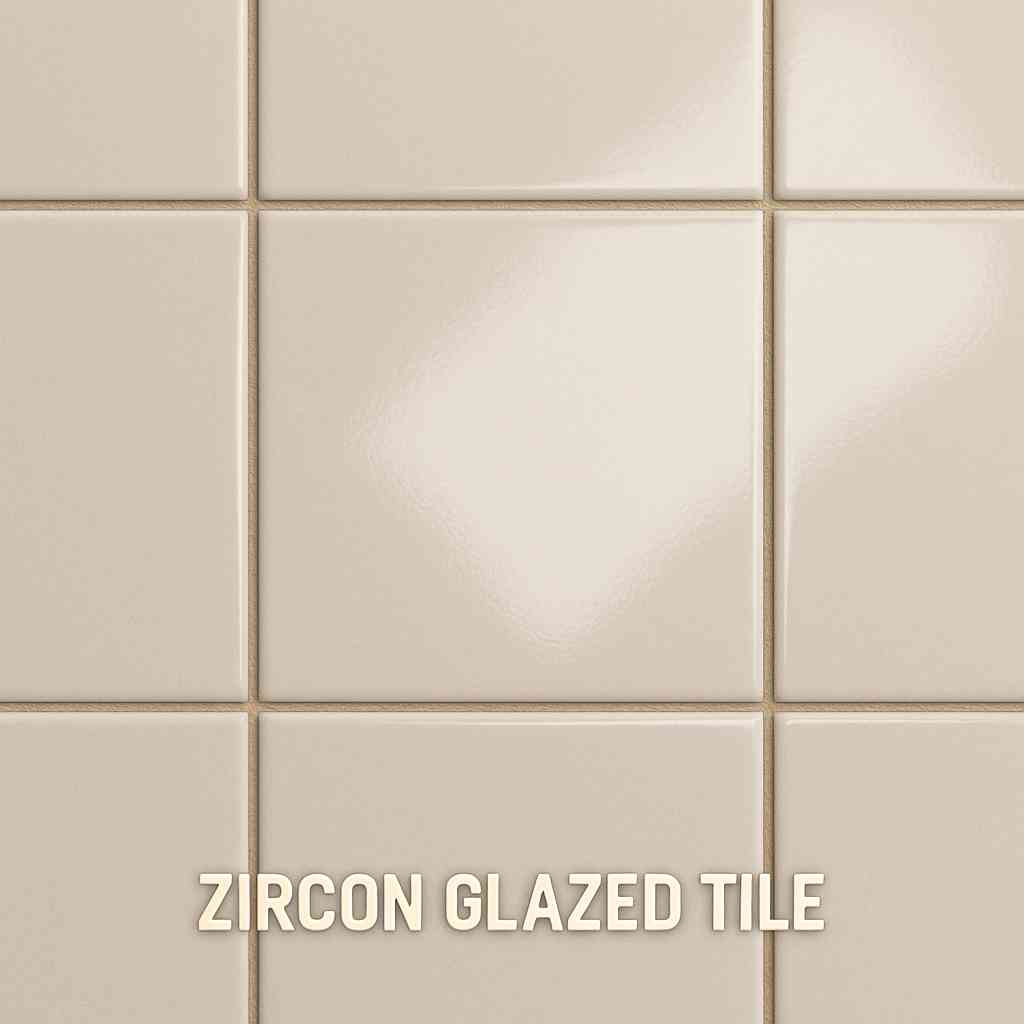
This image illustrates how zircon sand is used to enhance tile brightness and durability.
How Does Zircon Sand Benefit Refractories Manufacturing?
Industrial furnaces, kilns, and reactors operate under extreme heat. That’s where zircon-based refractories come in.
Zircon sand forms the base material for firebricks and castables that line these structures. Its thermal shock resistance keeps it from cracking during rapid temperature changes.
Why does this matter to manufacturers? Because the failure of a refractory lining can shut down operations for days, if not weeks.
Zircon’s natural resistance to chemical attack makes it suitable for glass, steel, and cement manufacturing plants. In environments with molten slag or corrosive vapors, it stays intact far longer than other materials.
You’ll find zircon refractories in:
- Steel ladles
- Glass melting tanks
- Cement kilns
- Petrochemical reactors
Refractory Property | Performance Contribution from Zircon |
---|---|
Thermal Shock Resistance | Withstands sudden temperature changes |
Chemical Resistance | Resists corrosion and erosion |
High Melting Point | Suitable for severe service environments |
What Is the Role of Zircon Sand in Nuclear Energy?
The nuclear sector values zircon for a different reason—it’s used to extract zirconium metal, essential in reactor technology.
Zirconium has a very low neutron absorption cross-section. That means it won’t interfere with the nuclear fission process. It’s mainly used in fuel rod cladding for light water reactors.
But there’s a catch—zirconium must be separated from hafnium, which has a high neutron absorption rate. This requires additional refining steps, making nuclear-grade zirconium expensive and highly regulated.
Countries with advanced nuclear industries have specific standards for sourcing and processing zircon. Long-term supply contracts, quality control, and traceability are standard.
Application | Zircon-Based Contribution |
---|---|
Fuel Rod Cladding | Corrosion-resistant, low neutron capture |
Core Components | Stability under radiation |
Safety Systems | High structural reliability |
Can Zircon Sand Improve Additive Manufacturing?
3D printing in metals and ceramics is rising fast. Zircon sand is now finding its way into these modern production lines.
In particular, zircon is used in binder jetting and selective laser sintering (SLS) to produce molds or even final components. It offers high print resolution and smooth surface textures, which are critical in aerospace and medical prototyping.
You might be surprised—zircon-based powders offer finer print quality than silica or alumina in many tests.
Applications include:
- Precision casting molds
- Aerospace tooling
- Functional ceramic prototypes
Additive Process | Why Use Zircon Sand |
---|---|
Binder Jetting | Accurate layering and high resolution |
SLS | High temperature resistance |
Hybrid Composites | Enhanced stiffness and durability |

This image shows a precision mold printed using zircon-based material in a binder jetting process.
What Industrial Coatings Use Zircon-Based Materials?
Some of the toughest environments—jet engines, turbines, reactors—demand extreme surface protection.
Zircon-based coatings act as thermal barriers and corrosion shields. They are often sprayed on metal components in aerospace and energy industries. The coatings protect against oxidation, thermal fatigue, and material wear.
Zirconium oxide (ZrO₂), derived from zircon sand, is used in:
- Turbine blades
- Combustion chamber liners
- High-temperature bearings
Why is this significant? Because without this protection, parts degrade quickly, increasing replacement costs and downtime.
Application Area | Coating Function |
---|---|
Aerospace Turbines | Thermal insulation |
Power Generation | Oxidation resistance |
Industrial Machinery | Wear protection |
How Does Zircon Sand Impact Environmental Sustainability?
Zircon sand supports cleaner manufacturing in a few indirect but measurable ways.
Foundries and ceramics plants recycle zircon sand across several production cycles. That reduces both material waste and energy consumption per unit produced.
Newer facilities now use closed-loop systems to capture and reclaim sand after casting. Also, zircon’s stability allows it to be used at thinner coating layers or lower loadings, which saves on raw materials.
Let’s pause here—zircon mining does pose some challenges, especially in coastal regions. But responsible sourcing programs and ISO certifications are improving traceability and sustainability reporting.
Sustainability Factor | Zircon Impact |
---|---|
Recyclability | High reuse rate in foundries |
Energy Savings | Fewer reprocessing cycles required |
Sourcing Transparency | Improving through traceability tools |
What Should Buyers Look for When Sourcing Zircon Sand?
Procurement isn’t just about price—it’s about performance and reliability.
Buyers should evaluate zircon sand based on:
- Purity and particle size
- Thermal behavior
- Supplier certification and quality systems
- Delivery timelines and storage requirements
Here’s what you should check—ask suppliers for technical datasheets, including ZrO₂ percentage, grain size distribution, and impurity profile. It’s also worth inspecting packaging and how moisture control is handled during shipping.
Buyer Checklist | Why It Matters |
---|---|
Grade and Composition | Impacts application performance |
Supplier Reliability | Prevents production delays |
Moisture Control | Affects storage and usability |
Technical Support | Helps with process integration |
What Are the Emerging Trends in Zircon Sand Applications?
New sectors are adopting zircon due to its performance profile.
Sectors like defense, aerospace composites, and technical glass are testing zircon-based formulations for next-gen materials. There’s also R\&D around hybrid materials using zircon with carbon fibers or silicon carbide.
Supply chains are tightening, so buyers are entering long-term contracts to lock in pricing and availability.
Let’s wrap this up—zircon sand is no longer just for foundries or tiles. Its usage is expanding into specialized high-stakes environments.
Sector | Future Use of Zircon |
---|---|
Aerospace | Hybrid ceramic composites |
Electronics | Heat-dissipating substrates |
Defense | Radiation shielding materials |
Conclusion
Zircon sand supports industries that demand reliability—from casting shops to nuclear plants. It delivers stability, durability, and chemical resistance under stress. That’s a hard combination to find.
Companies using zircon benefit from reduced waste, better part quality, and higher thermal performance. That translates into fewer shutdowns and tighter tolerances.
If your operation needs high-purity zircon sand, contact us for a technical consultation and pricing. We help procurement teams match grades to applications and streamline your supply chain.
Let’s build a reliable partnership that supports your production goals.
FAQ Section
Q1: Is zircon sand safe to use in industrial settings?
Yes, zircon sand is generally considered safe when handled properly. In industrial settings, it is important to use appropriate protective equipment, such as dust masks and gloves, to manage exposure to fine particulates. Proper ventilation and dust control measures should also be implemented to minimize inhalation risks.
Q2: How does zircon sand compare to silica in casting applications?
Zircon sand offers several advantages over silica in casting applications. It has superior thermal stability, which allows it to withstand higher temperatures without breaking down. Additionally, zircon sand has a finer grain structure, which leads to more precise casting results, improved surface finish, and longer mold life. This makes it a preferred choice for high-quality casting in demanding applications.
Q3: What industries are the largest consumers of zircon sand?
The largest consumers of zircon sand include the ceramics, foundry, refractories, and nuclear energy industries. In ceramics, zircon is used for making tiles and sanitary ware. In foundries, it is essential for casting molds. Refractories use zircon sand for high-temperature applications, while the nuclear energy sector relies on its unique properties for various safety and structural applications.
Q4: Can zircon sand be reused after casting or processing?
Yes, zircon sand can often be reused multiple times in foundry operations. With proper reconditioning and screening processes to remove contaminants, zircon sand maintains its effectiveness for subsequent castings. This reuse reduces material costs and waste, making it an economical choice for foundry applications. However, careful monitoring is essential to ensure its performance does not degrade over time.
Q5: Is the global supply of zircon sand stable?
The global supply of zircon sand is somewhat stable, but it is concentrated in a few key regions, such as Australia, South Africa, and Brazil. Consequently, availability can be affected by geopolitical factors, regulatory changes, and environmental concerns. Manufacturers should develop robust sourcing strategies that include diverse suppliers and consider stockpiling to mitigate potential disruptions in the supply chain.