Moisture in zircon sand is a headache for many buyers in ceramics, foundries, and refractory production. Without reliable zircon sand drying, water clogs feeders, damages molds, and weakens final products. This guide explains each practical step to keep zircon sand dry before it enters production lines. You’ll find real methods, proven tools, and smart controls that guarantee your zircon sand stays dry, cost-efficient, and on spec. Trust this approach — it works for small batch kilns and global high-volume plants alike.
Why Dry Zircon Sand Before Production?
Listen closely: Unchecked moisture makes good zircon sand useless in high-heat processes. It adds weight, raises shipping fees, and breeds mold if stored too long. Inside factories, wet grains lump together. Operators then stop machines to break clogs. Lost time means lost money.
Drying fixes this mess. Loose, dry grains slide easily down chutes. Mixers spin freely without lumps jamming blades. Kilns and foundry molds work better when sand stays at the right moisture level.
For ceramic tile producers, dry sand locks in firing strength. Tiles resist cracking and shrink evenly. For foundries, molds shape metal parts precisely. Any leftover water bubbles metal, leaving pits that cost money to repair.
Buyers demand verified low moisture because it cuts headaches later. Sellers who dry sand well earn repeat orders and build long-term supply deals.
Risk of Wet Sand | Production Damage |
---|---|
Clumping in hoppers | Costly downtime |
Weight spikes | Higher freight bills |
Mold risk in storage | Scrap loss |
Porosity in fired tiles | Returns and complaints |
One example: a ceramic factory in Malaysia switched from raw sand to kiln-dried zircon sand. They cut mold breakage by 28% and saved $12,000 on repair clay per quarter. A small zircon sand drying change paid off fast.
How Does Moisture Impact Processing?
Stay sharp here: Processing steps depend on stable, predictable sand. When water levels vary, milling torque jumps. Grinding wheels wear down faster. Operators must stop to re-balance loads.
In foundries, moist zircon sand hides steam pockets. When hot metal hits, sudden pressure cracks molds. Engine blocks and alloy parts end up pitted. Fixing cast defects costs more than proper zircon sand drying upfront.
Glazing lines face another problem: wet zircon sand absorbs glaze unevenly. Tiles show dull patches or surface flaws after firing, which means rework or waste.
Routine checks help avoid all these faults. Many plants run inline sensors on dried zircon sand and verify moisture hourly. If levels rise, they adjust dryers quickly to protect product flow.
Process Phase | Moisture Trouble |
---|---|
Milling | Uneven torque, blade wear |
Casting | Blowholes in molds |
Glazing | Inconsistent surface finish |
Final firing | Cracks or weak tiles |
Keep in mind that buyers often want test certificates with each shipment. Showing consistent moisture results builds trust and defends your pricing.
What Methods Dry Zircon Sand Effectively?
Let’s get straight to it: Choosing the right drying method is the backbone of any zircon sand preparation plan. Drying wrong eats up fuel, slows production, and delivers inconsistent quality — a nightmare for any production manager. Three tried-and-true systems lead the industry: kilns, rotary drum dryers, and fluid bed dryers.
Kiln drying is the classic method. Think of it as the slow cooker for zircon sand. Heat moves through sand beds at controlled rates. It’s perfect for small or specialty batches where high precision matters more than speed. Many custom tile or fine ceramic producers love kilns because they can tweak settings for each order.
Rotary drum dryers are the workhorses in big operations. Inside these giant cylinders, sand tumbles continuously while hot air flows through. This moving mix dries sand fast and in large volumes. Foundries and large refractory plants favor rotary dryers because they handle steady, round-the-clock demand without frequent stops.
Fluid bed dryers are the modern champions of even heat. In these, sand sits on a perforated plate while hot air pushes upward, making grains float slightly — like popcorn bouncing in a hot pan. This ensures every surface dries uniformly, cutting the risk of overcooked spots or damp centers. Specialty glass sand makers and premium ceramics suppliers often choose fluid beds when quality specs leave zero room for error.
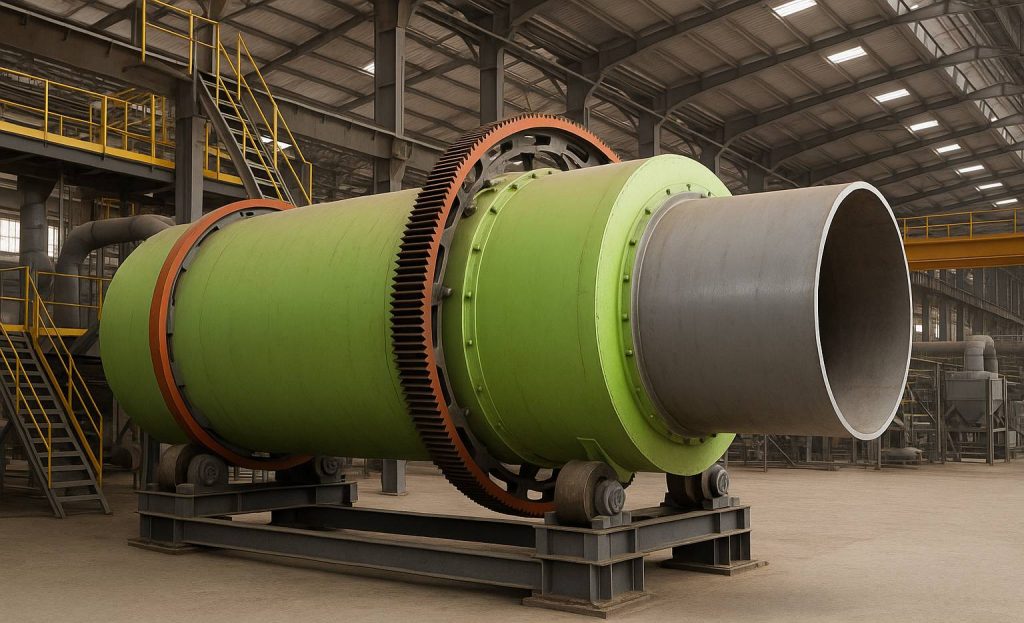
This image shows a large industrial rotary drum dryer in operation for high-volume zircon sand drying.
Here’s a pro tip: Many plants combine systems. For instance, a rotary drum may handle bulk drying first, followed by a brief fluid bed pass to polish moisture levels for high-spec buyers. This hybrid setup balances speed and uniformity.
Operating costs matter too. Kilns need less complex upkeep but run longer. Rotary drums burn more fuel but deliver volume. Fluid beds require upfront investment but can lower energy costs with heat recovery and finer control.
Check this fresh comparison:
Method | Batch Size | Drying Speed | Uniformity | Energy Use | Typical User |
---|---|---|---|---|---|
Kiln | Small to medium | Slow | High | Low-medium | Boutique ceramics, R&D labs |
Rotary drum | Large | Fast | Medium | High | Foundries, bulk suppliers |
Fluid bed | Medium-large | Fast | Highest | Medium | High-spec glass or ceramics |
Example from the field: A mid-sized European tile maker upgraded from old box kilns to a fluid bed plus rotary combo. Their throughput rose by 35% and scrap rate dropped by 15% in just six months — proof that the right mix saves both time and product waste.
One last insight: Always factor in local fuel costs and available staff skills. A sophisticated fluid bed is wasted if operators can’t run controls well. Reliable drying hinges on matching equipment capability with real-world conditions.
Key Decision Factors | Kiln | Rotary Drum | Fluid Bed |
---|---|---|---|
Upfront cost | Low | Medium | High |
Skill needed | Basic | Moderate | High |
Space required | Small footprint | Large footprint | Medium |
Maintenance | Simple | Regular cleaning | More sensors |
Choosing well sets the stage for everything else: lower moisture, stronger products, and fewer production headaches down the line.
A large rotary drum handles bulk zircon sand in continuous drying operations.
How To Control Drying Temperature Correctly?
Focus on this: Keeping drying heat in the safe range protects product quality and fuel costs. Many factories lose profit when heat drifts without clear checks.
Too much heat scorches grains or changes chemical phases. Too little leaves hidden moisture inside lumps — a sure way to cause cracks or blowholes later.
How do top operators manage it?
They set up three basic controls:
- Multiple temperature probes:
- One near the burner to track inlet heat
- One mid-way to catch drifting air loss
- One near the exit to confirm final sand temperature
- Linked airflow and drum speed:
- Faster drums move more sand but need more heat
- Slower drums allow longer drying time at lower temps
- Fan speed must match to avoid cold spots
- Regular burner tune-ups:
- Clean jets mean stable flames
- Inspect seals to avoid leaks
- Repair insulation before winter to stop heat waste
Quick point: Operators also train new staff to read heat logs and spot unusual patterns fast. This practice stops small drifts from turning into huge fuel bills.
Key Checkpoint | Good Range | If Too High | If Too Low |
---|---|---|---|
Burner inlet | 250–300°C | Grain burn risk | Slow drying |
Mid drum | 220–270°C | Uneven moisture | Damp lumps |
Exit sand | 80–120°C | Over-dried surface | Hidden moisture |
One ceramics line in Turkey linked these checks with a smart PLC. Within six months, gas use dropped 20% while drying stayed within spec. That’s a profit boost without new machines.
How Long Should Drying Take For Best Results?
Note this well: Timing depends on dryer type, sand grade, and moisture at the start.
Kilns handle smaller runs, taking 4–8 hours per batch. Artisanal tile makers often prefer this method for precision.
Rotary drums process more tons in less time — typically 30–120 minutes per pass, depending on grain size and drum length.
Fluid beds dry batches fastest. Sand floats on hot air, drying in 20–60 minutes.
Plants often stagger drying and packing shifts. Dryers run overnight. Workers pack sand at dawn, shipping same day.
Quality managers spot-check moisture every cycle. If it drifts above 0.5%, they tweak drum speed or add a second pass.
Dryer Type | Average Time | Use Case |
---|---|---|
Kiln | 4–8 hours | High-precision batches |
Rotary | 30–120 minutes | Bulk production |
Fluid bed | 20–60 minutes | Clean, even drying |
A South African mine uses rotary drying plus inline moisture sensors. Downtime from re-drying dropped by half in one year.
Which Equipment Works Best For Drying?
Check this out: not every dryer suits every zircon sand job. Smart buyers match equipment to output, fuel type, and staff skills.
Kilns fit small shops producing special batches. Technicians adjust time and heat carefully to get premium zircon sand quality.
Rotary drum dryers work best for bulk zircon sand drying. They run all day, pushing tons through with steady airflow. Maintenance is simple — just clean buildup and check seals.
Fluid bed dryers lead where top-grade zircon sand specs leave no margin for error. They cost more to set up but deliver very even heat and fine moisture control.
Other gear matters too. Steady conveyors feed the drum evenly. Dust collectors stop fine zircon sand particles from escaping. Modern plants link burners, fans, and belts with smart controls.
System | Good For | Not Ideal |
---|---|---|
Kiln | Small runs | High volume |
Rotary drum | Large batches | Tiny shops |
Fluid bed | Spec-heavy buyers | Tight budgets |
One ceramics exporter in Australia added a baghouse to a rotary drum line. Dust around their zircon sand dryer dropped 60%, improving air quality and worker safety.
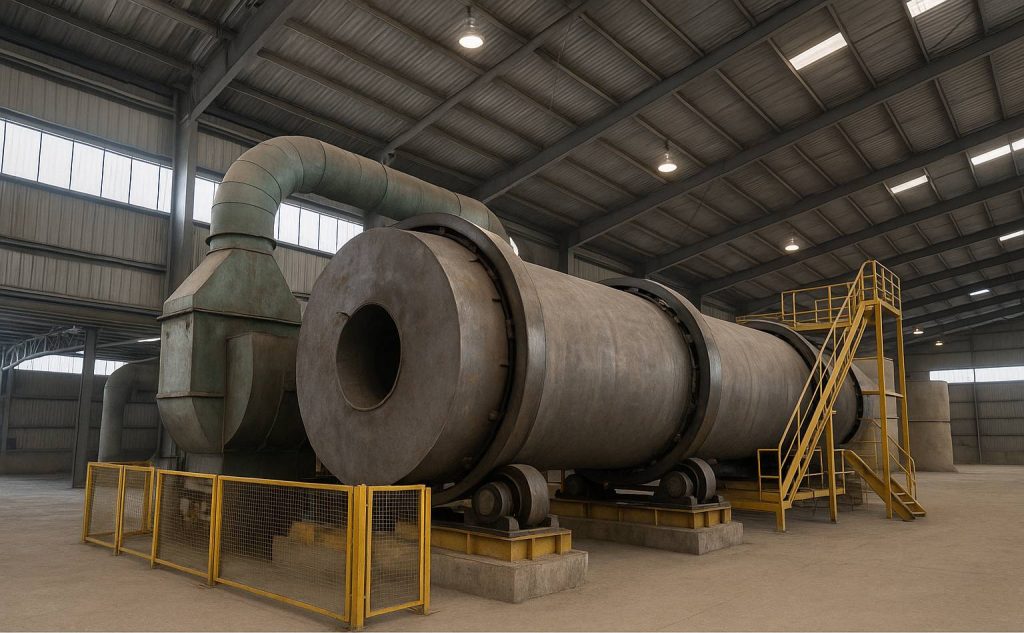
A controlled kiln handles delicate zircon sand batches for premium ceramics.
How To Ensure Consistent Moisture Removal?
Pay close attention: Drying once isn’t hard. Keeping it steady for every shift, every truckload, every season? That’s what sets strong suppliers apart from weak ones.
Moisture drift makes buyers angry. Unexpected lumps block feeders. Damp sand causes sudden kiln cracks. Every missed check means risk.
What’s the routine for consistency? Most reliable plants stick to these basics:
- Live inline sensors: Check every ton leaving the dryer
- Hourly lab samples: Back up sensor accuracy
- Operator logs: Write down inlet levels, exit moisture, burner loads
- Daily trend checks: Spot unusual spikes early
- Weekly drum clean-up: Remove stuck fines that hold water
A smart practice many managers follow: Keep a short checklist next to the dryer control panel. Anyone can tick off tasks before changing shifts. No guesswork, no hidden faults.
Control Tool | Job | How Often |
---|---|---|
Inline probe | Instant moisture check | Always on |
Lab oven | Validate probe | Hourly or per lot |
Operator record | Trends over time | Per shift |
Maintenance | Clean for airflow | Weekly |
One helpful tip: Many plants train two staff as ‘moisture champions’. They get extra practice reading logs and fixing small issues before they spread. This simple system keeps drying steady and customer claims low.
A global foundry chain did this and cut rejected batches by 70% in one year — just by sticking to these small, repeatable steps.
What Quality Checks Are Needed Post Drying?
Stay on top: Final checks prove the work paid off.
Measure residual moisture. Aim for less than 0.5%. Some high-grade applications want even drier sand.
Check grain size. If lumps formed inside drums, crush or sieve again. Also test for unwanted trace minerals.
Label each bag with date, batch ID, and moisture result. Many buyers scan these records before unloading trucks.
Some firms add barcodes for full traceability from mine to mold.
Test | Target | Action if Fails |
---|---|---|
Moisture | < 0.5% | Redry or recheck |
Size | Buyer spec | Re-sieve |
Purity | Zero foreign particles | Inspect source |
How To Minimize Energy Use When Drying?
Big cost saver: Drying costs money. Wasting heat burns profit.
Use heat exchangers. Hot exhaust air can pre-warm fresh air entering the drum.
Wrap pipes and ducts in good insulation. Fix leaks fast.
Some plants feed leftover heat from kilns back into rotary dryers. Smart recycling cuts fuel bills.
Variable fans match airflow to sand weight. No waste.
Compare utility bills each month. Small tweaks add up over a year.
Tactic | Payoff |
---|---|
Heat exchanger | Cut gas cost |
Pipe insulation | Hold more heat |
Recycled hot air | Use less fuel |
A Thai zircon mill cut gas spend by 22% after adding an exhaust heat recovery loop.
How To Store Dried Zircon Sand Properly?
Keep dry means keep safe: Dry sand attracts water fast if stored wrong.
Dry it — then protect it. Dried zircon sand attracts air moisture fast if left open.
Seal bags tight. For export, use liners with moisture barriers. Keep dried zircon sand indoors, away from big temperature swings.
Rotate stock FIFO — first in, first out. This keeps your oldest zircon sand moving before new batches pile up. Train drivers to handle bags gently. Holes let air sneak in overnight.
Storage Rule | Why |
---|---|
Seal bags | Block air moisture |
Control room humidity | Stop re-wetting |
Rotate stock | Keep sand fresh |
A Vietnamese supplier switched to lined bags and shaded silos. Zircon sand moisture complaints fell by 80% in six months.
Conclusion
Dry zircon sand means zero surprises in your molds, tiles, or castings. You now have clear steps, smart controls, and top gear choices to keep moisture away. Well-dried sand cuts faults and raises profit. Ready to level up your drying line? Talk to Global Industry today. We’ll help set up or refine your sand process, so you stay ahead. Start your quality boost with us now.
FAQ
Q1: Why must zircon sand be dried before use?
Drying stops lumps, clogs, and defects. It keeps zircon sand flowing smoothly in kilns and molds.
Q2: What drying method uses the least energy?
Rotary drums with heat recovery or fluid beds with smart control are efficient for zircon sand drying.
Q3: How do I test if zircon sand is dry enough?
Combine inline sensors with random lab checks for reliable results.
Q4: Can poor drying weaken final products?
Yes — wet zircon sand cracks ceramics, bubbles molds, and weakens casting strength.
Q5: How should I store dried zircon sand?
Use sealed, lined bags in stable rooms. Rotate stock and check for leaks.