In modern industry, materials enduring extreme conditions are indispensable. Zircon powder is a critical component in high-temperature applications, maintaining integrity under intense thermal stress, which is crucial for operational efficiency and product quality. This article explores zircon powder’s thermal endurance, its fundamental properties, influencing factors, and its pivotal role across high-temperature industrial processes. For B2B buyers, understanding these nuances is key to optimizing material selection, enhancing reliability, and driving innovation.
What is zircon powder’s basic thermal stability?
Zircon (ZrSiO4) is a natural mineral known for exceptional thermal stability, making it highly sought after in industrial applications. Its ability to withstand high temperatures comes from its unique tetragonal crystalline structure, which resists decomposition and phase changes under intense heat. The strong covalent and ionic bonds within the zircon lattice contribute to its high melting point, typically around 2550°C (4622°F).
Key intrinsic factors influencing zircon powder’s thermal behavior include its low thermal expansion coefficient and high thermal conductivity. Low thermal expansion minimizes expansion/contraction with temperature fluctuations, reducing thermal shock and cracking. High thermal conductivity efficiently dissipates heat, preventing localized hot spots. Compared to other refractory materials, zircon powder often excels in high-temperature environments, especially where chemical inertness and resistance to molten metals are crucial. Its thermal stability makes it ideal for consistent performance over prolonged periods at elevated temperatures, typically 1600°C to 2000°C (2912°F to 3632°F), and even higher for short durations or in specialized compositions.
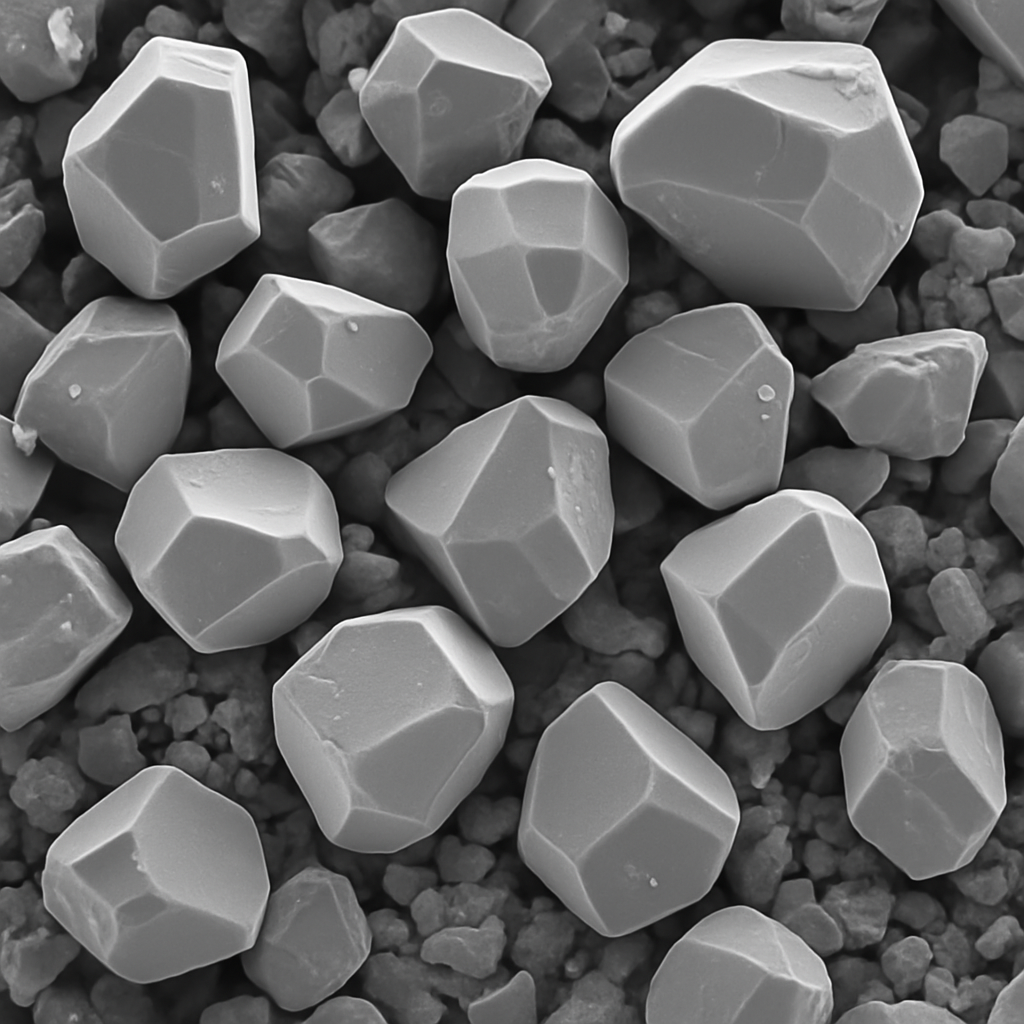
How does purity affect thermal limits?
The purity of zircon powder directly influences its thermal limits and performance. Even minute impurities can significantly alter its thermal behavior, leading to premature degradation and compromised integrity. Trace elements play a crucial role in how zircon powder withstands extreme heat.
Common impurities like iron oxides, titanium oxides, alumina, and alkali/alkaline earth metals can act as fluxing agents, lowering zircon’s melting point and promoting undesirable phase transformations. For example, iron oxides can catalyze zircon decomposition at lower temperatures, while alkali metals can form low-melting eutectics, causing softening and deformation. Impurities also increase susceptibility to chemical attack and corrosion in aggressive high-temperature environments.
Different zircon powder grades exist, with thermal characteristics dictated by purity. Standard grades, while cost-effective, have higher impurity levels and lower thermal limits. High-purity grades, through extensive beneficiation, offer superior thermal stability, higher melting points, and enhanced chemical degradation resistance. The chosen grade must align with the application’s thermal demands and chemical environment. Stringent quality control is essential to ensure consistent thermal performance and prevent failures.
Case studies from glass manufacturing and metallurgy show consequences of purity-related thermal failures. Impure zircon refractory bricks can spall or wear prematurely in glass furnaces, causing downtime. In steel casting, impurities in zircon-based molds can react with molten metal, causing product defects. These examples highlight the economic and operational importance of high-purity zircon powder for maximum thermal limits.
What industrial applications use high temperatures?
Zircon powder‘s exceptional thermal endurance makes it indispensable across high-temperature industrial applications. Its resistance to extreme heat, chemical attack, and thermal shock makes it a preferred choice for performance and longevity.
Refractory linings are a significant application. Zircon powder is used in furnaces, kilns, and crucibles, especially those with very high temperatures or corrosive molten materials. In the glass industry, zircon-based refractories line melting tanks due to their resistance to molten glass corrosion and high thermal stability. In steel and non-ferrous metal industries, zircon refractories are used in ladles, tundishes, and continuous casting systems, resisting molten metal penetration and erosion, ensuring cleaner metal and longer equipment life.
In foundry processes, zircon powder is crucial for high-quality metal castings. It’s used as facing sand in molds and cores for ferrous and non-ferrous castings. Its high refractoriness, low thermal expansion, and excellent thermal conductivity prevent metal penetration and ensure a smooth surface finish. Zircon washes and coatings enhance mold/core resistance to heat and chemical reactions, reducing casting defects and improving efficiency. This is vital for precision castings requiring dimensional accuracy and surface quality.
Zircon powder is also key in advanced ceramics, glazes, and opacifiers. Its high melting point and chemical inertness make it ideal for specialized ceramic products needing high thermal stability and wear resistance. As an opacifier, it imparts whiteness and opacity to glazes and enamels on tiles, sanitaryware, and other ceramic products, contributing to aesthetic appeal and durability.
Investment casting heavily relies on zircon powder. In this precision method, zircon flour and sand are primary components of slurries and stucco for ceramic shells. Their superior refractoriness and low thermal expansion ensure mold dimensional stability and integrity during high-temperature pouring of molten alloys, leading to accurate components for aerospace, automotive, and medical industries.
Beyond these, zircon powder is used in other critical high-temperature industrial processes, such as metallurgy (resistance to extreme heat and chemical aggression) and in specialty chemicals and high-performance coatings protecting substrates from thermal degradation. Zircon powder’s versatility and robust thermal performance underscore its irreplaceable position where high-temperature endurance is non-negotiable.
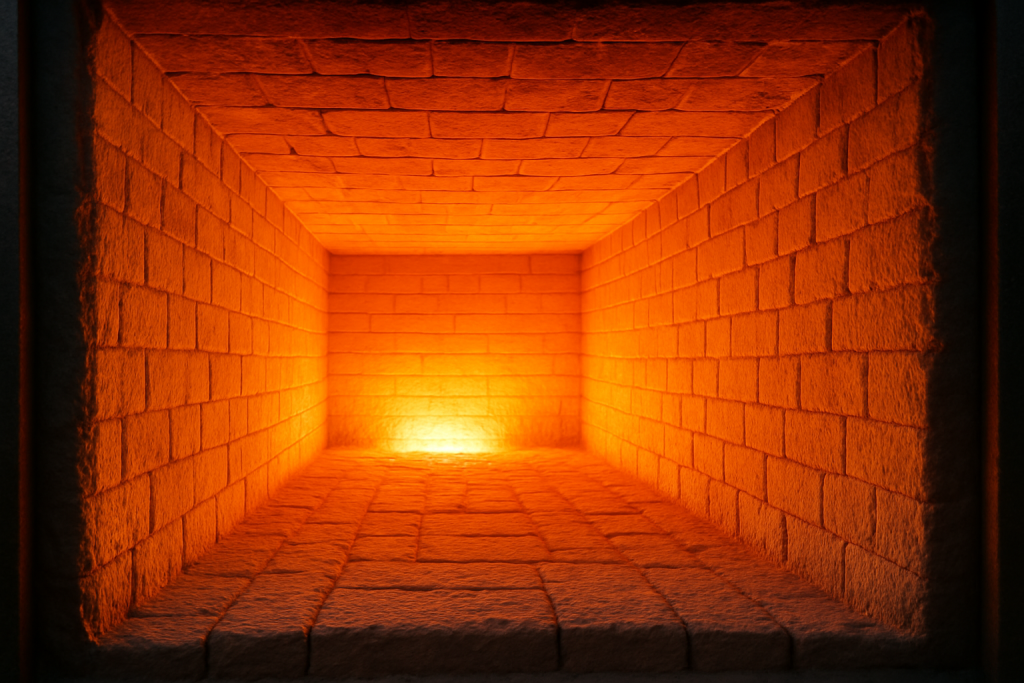
How do processing methods influence performance?
Zircon powder’s thermal performance is influenced by processing methods, not just inherent properties or purity. Particle size distribution, morphology, and thermal/mechanical treatments optimize it for high-temperature demands.
Particle size distribution and morphology are fundamental. Finer particles offer larger surface area, influencing reactivity and sintering. A well-controlled distribution (blend of coarse and fine) is crucial for optimal packing density in refractory applications. Higher packing density means lower porosity, improving thermal shock resistance and reducing permeability. Particle morphology (shape) also matters; spherical particles flow and pack more efficiently, contributing to a uniform, stable structure under thermal stress.
Various milling and grinding techniques (wet, dry, jet) produce different particle sizes and shapes, impacting thermal performance. Ultra-fine grinding can enhance reactivity for ceramics but may increase susceptibility to chemical attack in some high-temperature environments.
Thermal treatments like calcination and sintering profoundly affect zircon powder’s thermal stability and density. Calcination removes volatile impurities and induces partial sintering, improving stability. Sintering fuses powder particles, increasing density and strength. The degree of sintering directly impacts refractoriness, thermal conductivity, and resistance to creep/deformation at elevated temperatures.
Binder systems and additives in formulations are also crucial. Zircon powder mixed with binders (organic polymers, inorganic silicates) and additives forms slurries or green bodies. These additives affect rheological properties, green body strength, and critically, high-temperature performance. Some act as sintering aids, while others may form new phases that enhance or detract from thermal stability. Careful selection and optimization are essential for expected performance.
Optimizing processing parameters is key to tailoring zircon powder for specific thermal demands. This requires understanding the interplay between raw material properties, milling techniques, thermal treatments, and formulation additives. Controlling these variables allows manufacturers to produce zircon powder and zircon-based products with superior thermal endurance, mechanical strength, and chemical resistance, meeting stringent industrial requirements.
What are common failure modes at high heat?
Despite its thermal endurance, zircon powder and zircon-based materials can fail under extreme, prolonged high-temperature conditions. Understanding these failure modes is crucial for robust system design, lifespan prediction, and effective mitigation.
Thermal shock is a prevalent failure mode, occurring from rapid temperature changes causing differential thermal expansion/contraction. Zircon, though having low thermal expansion, is susceptible to thermal shock, especially with rapid heating/cooling cycles. Resulting internal stresses cause micro-cracks, leading to macroscopic cracking and spalling, compromising integrity.
Creep and deformation are critical failure mechanisms under sustained high temperatures and mechanical loads. Creep is slow, permanent deformation under stress. At elevated temperatures, increased atomic mobility in zircon leads to viscous flow or grain boundary sliding, causing gradual shape/dimension changes. This is a significant concern for refractory linings where precise dimensions and load-bearing capacity are essential.
Chemical reactions, oxidation, and corrosion also contribute to high-temperature failure. While zircon is chemically inert, it can react with aggressive environments at elevated temperatures (e.g., strong alkalis, molten metals), leading to degradation or dissolution. Oxidation can alter surface properties or cause internal structural changes. Corrosion, exacerbated by molten slags/glasses, erodes the surface, reducing thickness and protective capabilities.
Phase transformations can also degrade materials. Zircon (ZrSiO4) can decompose into zirconia (ZrO2) and silica (SiO2) under extreme conditions. Zirconia exhibits polymorphic transformations (e.g., monoclinic to tetragonal) with significant volume changes. If these occur in a zircon-based material, induced internal stresses can cause cracking and mechanical failure. Controlling these transformations through material design and processing is vital for long-term stability.
How is thermal performance tested and verified?
Rigorous testing and verification methods ensure zircon powder and zircon-based materials meet industrial thermal demands. These methods provide critical data on high-temperature behavior, enabling performance prediction, quality assurance, and material optimization.
Standardized testing methods are fundamental for evaluating thermal properties, with protocols from organizations like ASTM International and ISO ensuring consistency. Key thermal properties measured include:
- Thermal Expansion: Measures material expansion/contraction with temperature changes using dilatometry. Low thermal expansion is desirable to minimize thermal stress.
- Thermal Conductivity: Quantifies heat conduction using methods like hot wire or laser flash analysis. High conductivity dissipates heat, while low conductivity is for insulation.
- Specific Heat Capacity: Measures heat required to raise unit mass temperature by one degree using DSC or calorimetry.
For high-temperature mechanical strength, the hot modulus of rupture (HMOR) test is crucial. It measures flexural strength at elevated temperatures, indicating load-bearing capability and deformation resistance. High HMOR means significant strength retention when hot, vital for refractory linings.
Advanced analytical techniques offer deeper insights:
- Thermogravimetric Analysis (TGA): Measures mass changes with temperature/time in controlled atmosphere, studying decomposition, oxidation, and phase transformations.
- Differential Thermal Analysis (DTA) and Differential Scanning Calorimetry (DSC): Detects thermal events (phase transitions, melting) by measuring temperature difference or heat flow.
Real-world performance validation is essential, often involving simulating service conditions via pilot-scale tests or industrial trials. Case studies provide invaluable feedback on zircon powder’s performance under actual operating stresses (thermal cycling, chemical attack, mechanical loads). This comprehensive approach ensures reliable and predictable performance in demanding high-temperature industrial environments.
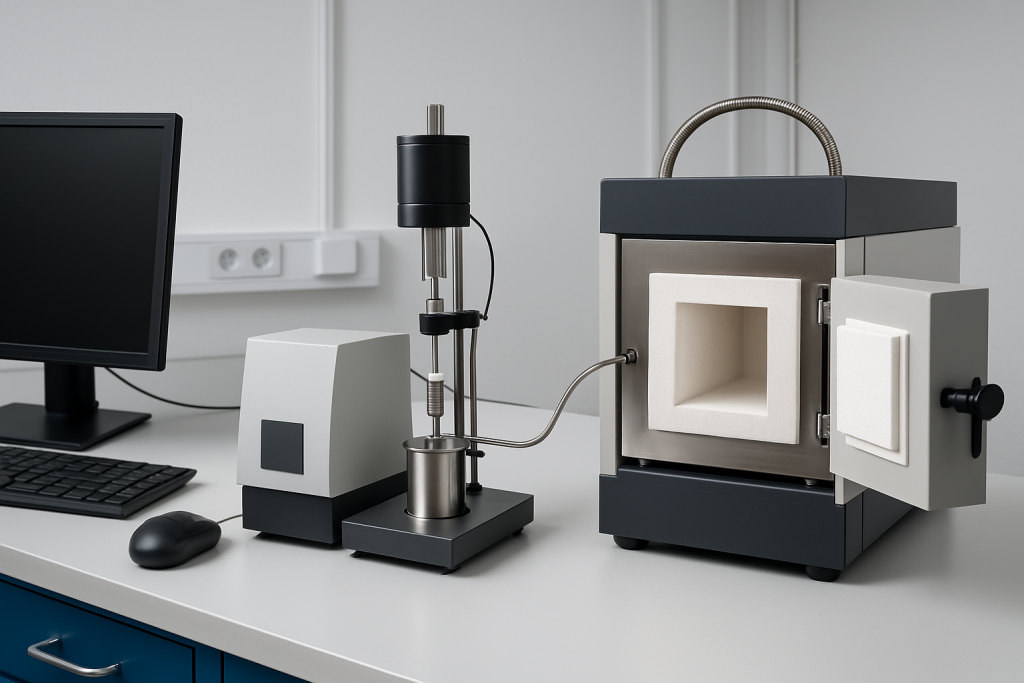
What future innovations enhance thermal resistance?
The quest for materials enduring higher temperatures and aggressive environments is continuous, with zircon powder at the forefront. Future innovations focus on pushing its thermal resistance boundaries, expanding application scope, and enhancing performance.
Advanced surface treatments and protective coatings are promising. Modifying zircon powder particle surfaces or applying thin, refractory coatings improves resistance to chemical attack, oxidation, and erosion at elevated temperatures. Techniques like ALD, CVD, and plasma spraying create durable, inert layers, extending service life.
Novel composite materials incorporating zircon powder are another trend. Combining zircon with other high-performance ceramics, metals, or polymers creates hybrid materials leveraging each component’s best properties. Zircon-reinforced composites can show enhanced fracture toughness, thermal shock resistance, and mechanical strength at high temperatures, suitable where traditional zircon falls short. These are used in aerospace, advanced energy, and next-generation refractory solutions.
Applications of nanotechnology and nanomaterials revolutionize zircon powder technology. Incorporating nano-sized zircon particles or other nanoparticles improves properties. Nanoparticles inhibit grain growth, leading to finer microstructures and enhanced mechanical properties. They also improve sintering, allowing denser, more stable materials at lower processing temperatures. Research explores nanostructured zircon for ultra-high temperature ceramics and thermal barrier coatings.
Emerging processing techniques aim for ultra-high temperature stability and new functionalities. Advanced sintering methods (SPS, FAST) allow rapid densification at lower temperatures, preserving fine microstructures. Additive manufacturing (3D printing) for zircon-based materials enables complex geometries with tailored thermal properties, reducing waste and increasing design flexibility.
Overall, research trends in enhancing zircon powder’s thermal endurance are multidisciplinary. Focus is on increasing maximum temperature, improving long-term stability, resistance to degradation, and overall performance in complex industrial environments. These innovations will solidify zircon powder’s critical position for future demanding high-temperature applications.
Conclusion
Zircon powder, with its unparalleled thermal endurance, is critical for diverse industrial applications. Its inherent stability, from robust crystalline structure and high melting point, makes it a cornerstone in extreme temperature environments, enabling processes otherwise impossible or inefficient.
Performance depends not just on intrinsic properties, but also on purity, meticulous processing (particle size, morphology, thermal treatments), and careful additive selection. Understanding common failure modes—thermal shock, creep, chemical reactions, phase transformations—is vital for designing resilient systems and predicting material behavior.
Rigorous testing and verification, including standardized lab methods and real-world validation, are indispensable for ensuring zircon-based materials’ reliability and quality. These evaluations provide data for informed material selection and process optimization.
Future innovations in surface treatments, composites, nanotechnology, and advanced processing promise to further enhance zircon powder’s thermal resistance, pushing boundaries and expanding applications into even more demanding high-temperature environments. For B2B buyers, investing in and understanding zircon powder is about securing operational efficiency, ensuring product quality, and maintaining a competitive edge where thermal performance is paramount.
FAQ Section
Q1: What is the maximum continuous operating temperature for standard zircon powder?
Standard zircon powder typically withstands continuous operating temperatures up to 1600°C to 2000°C (2912°F to 3632°F), depending on purity and application. Higher temperatures are possible for short durations or in specialized compositions.
Q2: How does the presence of silica affect zircon powder’s thermal stability?
Zircon (ZrSiO4) contains zirconia and silica. While silica is a component, excessive free silica or impurities can lower overall refractoriness and thermal stability, especially if they form low-melting eutectics. High-purity zircon ensures silica is chemically bound within the stable zircon structure.
Q3: Can zircon powder be used in oxidizing and reducing atmospheres?
Zircon powder generally shows good stability in both oxidizing and reducing atmospheres. Performance can be influenced by other reactive elements at very high temperatures. In most industrial applications, it maintains integrity.
Q4: What are the primary advantages of zircon powder over alumina in high-temperature applications?
Compared to alumina, zircon powder offers superior resistance to molten metal/glass corrosion, lower thermal expansion, and excellent thermal shock resistance. It also has a higher melting point than most alumina grades, suiting more extreme thermal environments.
Q5: How do particle size and shape influence zircon powder’s thermal shock resistance?
Particle size and shape significantly influence thermal shock resistance. A well-controlled distribution (mix of coarse and fine) allows optimal packing density, reducing porosity and improving thermal conductivity, which dissipates thermal stresses. More spherical particles pack better, contributing to a uniform structure, further enhancing thermal shock resistance.