Zircon powder processing faces mounting pressure to improve efficiency, reduce costs, and meet stricter quality standards. Traditional zircon powder processing methods struggle with energy consumption, inconsistent product quality, and environmental compliance challenges. Modern technological advances offer solutions that transform these limitations into competitive advantages. This analysis examines breakthrough innovations in separation, milling, thermal processing, and automation that enable zircon powder manufacturers to achieve superior product quality while reducing operational costs by up to 35%. Leading zircon powder processors who adopt these technologies gain significant market advantages through improved efficiency and product consistency.
Zircon powder quality improvements through advanced processing technologies enable manufacturers to meet demanding specifications while reducing waste and improving profitability. Modern zircon powder facilities that implement comprehensive technology upgrades typically see dramatic improvements in both operational efficiency and product quality metrics.
What Advanced Separation Technologies Improve Purity?
Modern separation technologies represent the most significant advancement in zircon powder processing, with magnetic separation systems achieving unprecedented purity levels. High-intensity magnetic separators now deliver results that were impossible just five years ago. These systems utilize rare earth permanent magnets generating fields up to 20,000 gauss, enabling separation of weakly magnetic minerals that conventional systems cannot handle.
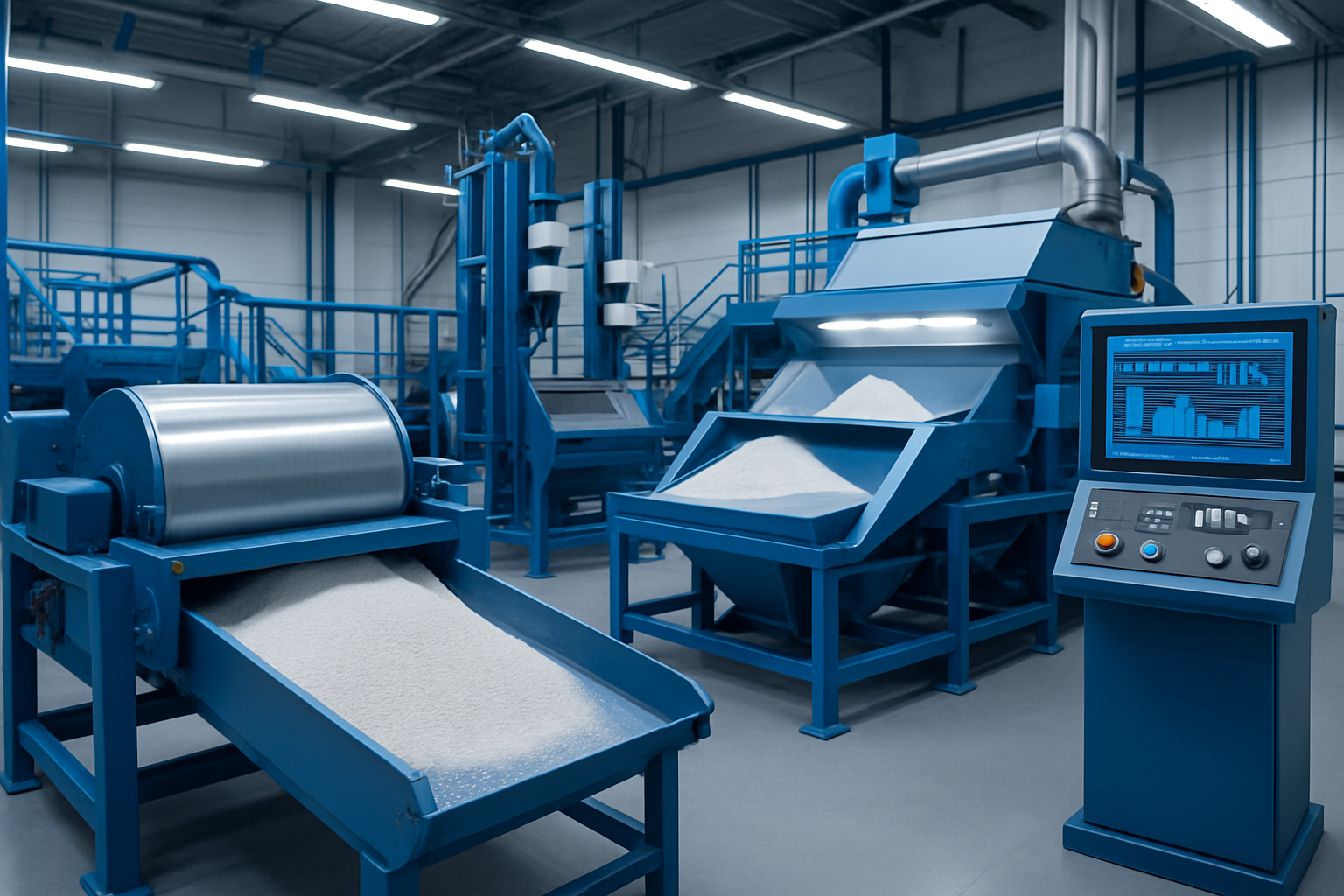
Electrostatic separation has evolved beyond traditional corona discharge methods to include triboelectric and electrodynamic techniques. These advanced systems can process materials with moisture content up to 8% while maintaining separation efficiency above 95%. The integration of multiple electrostatic stages allows for precise grade control, producing zircon concentrates with ZrO₂ content exceeding 66% consistently.
Automated sorting systems using artificial intelligence and machine learning algorithms represent the cutting edge of separation technology. These systems analyze individual particles using X-ray transmission, near-infrared spectroscopy, and color recognition to make sorting decisions in milliseconds. The precision of these systems is truly remarkable. They can identify and separate particles as small as 1mm with accuracy rates exceeding 99.5%.
Separation Technology | Purity Achievement | Recovery Rate | Energy Consumption |
---|---|---|---|
High-intensity magnetic | 99.2% | 94-96% | 15-25 kWh/ton |
Advanced electrostatic | 98.8% | 92-95% | 8-12 kWh/ton |
Multi-stage gravity | 97.5% | 88-92% | 5-8 kWh/ton |
Hybrid systems | 99.5% | 96-98% | 20-30 kWh/ton |
Sensor-based sorting | 99.8% | 85-90% | 3-5 kWh/ton |
How Do Modern Milling Techniques Enhance Efficiency?
High-energy ball milling innovations focus on optimizing grinding media design and mill configuration to achieve superior particle size distribution. These improvements change everything about grinding efficiency. Advanced ceramic grinding media with engineered surface textures reduce contamination while increasing grinding efficiency by 20-30%. Variable speed drives allow real-time adjustment of mill rotation speed based on material characteristics and desired product specifications.
Zircon powder particle size control becomes critical for many applications, requiring precise milling techniques that maintain consistent size distributions. Modern zircon powder milling systems incorporate advanced monitoring and control technologies to ensure optimal particle characteristics for specific end-use applications.
Jet milling technology has advanced significantly with the development of spiral jet mills and opposed jet systems that achieve ultra-fine particle sizes with narrow size distributions. These systems operate at pressures up to 10 bar and can produce particles with d50 values below 5 microns while maintaining coefficient of variation under 1.5.
Stirred media mills represent a major advancement in fine grinding technology, offering superior energy efficiency compared to traditional ball mills. These systems use small grinding media (0.5-3mm) in a stirred chamber, achieving specific energy consumption 30-50% lower than conventional mills for equivalent product fineness.
Milling Technology | Particle Size Range | Energy Efficiency | Contamination Risk |
---|---|---|---|
High-energy ball mill | 10-100 microns | Standard baseline | Medium |
Spiral jet mill | 1-20 microns | 40% more efficient | Very low |
Stirred media mill | 5-50 microns | 50% more efficient | Low |
Cryogenic mill | 1-10 microns | 60% more efficient | Very low |
Continuous systems | Variable | 35% more efficient | Low |
Which Thermal Processing Innovations Reduce Costs?
Advanced calcination furnace designs incorporate multi-zone temperature control and enhanced heat transfer mechanisms to improve energy efficiency and product quality. The cost savings are substantial and immediate. Modern rotary kilns with preheater systems reduce fuel consumption by 40-50% compared to conventional designs while achieving more uniform temperature distribution throughout the material bed.
Energy recovery systems capture waste heat from calcination processes and redirect it to preheat incoming materials or generate steam for other plant operations. Heat exchangers with effectiveness ratings above 85% recover thermal energy that would otherwise be lost, reducing overall energy costs by 20-30%. These systems typically pay for themselves within 18-24 months through energy savings alone.
Microwave-assisted heating technologies offer precise temperature control and rapid heating rates for specialized applications. These systems heat materials volumetrically rather than through surface conduction, resulting in more uniform temperature distribution and reduced processing time.
Thermal Technology | Energy Reduction | Temperature Control | Processing Time |
---|---|---|---|
Advanced rotary kiln | 40-50% | ±5°C | Standard |
Microwave heating | 30-40% | ±2°C | 60% faster |
Fluidized bed | 25-35% | ±3°C | 30% faster |
Plasma processing | 20-30% | ±1°C | 80% faster |
Heat recovery systems | 20-30% | Variable | No change |
What Digital Technologies Transform Quality Control?
Real-time chemical composition monitoring systems use X-ray fluorescence and laser-induced breakdown spectroscopy to analyze material composition continuously during processing. This technology transforms quality assurance from reactive to proactive. These systems provide composition data within seconds, enabling immediate process adjustments to maintain product specifications and reduce off-specification material production.
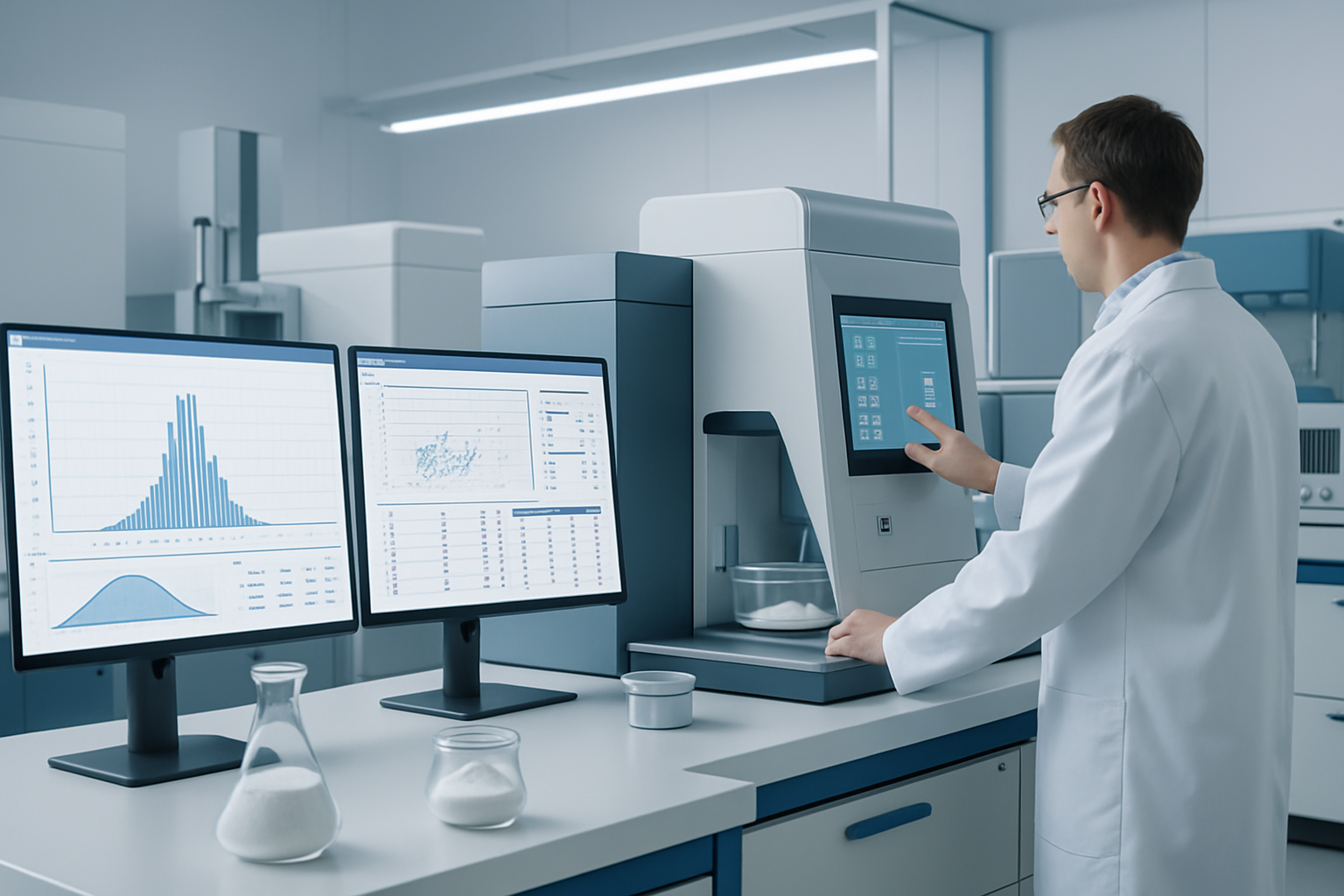
Automated particle size analysis systems integrate laser diffraction and dynamic image analysis to monitor particle size distribution continuously. These systems can detect changes in particle size distribution within minutes and automatically adjust milling parameters to maintain target specifications. The elimination of manual sampling and laboratory analysis reduces quality control costs by 40-60%.
Artificial intelligence-powered quality prediction models analyze multiple process variables simultaneously to predict product quality before final testing. These models use machine learning algorithms trained on historical data to identify patterns and correlations that human operators might miss. Prediction accuracy typically exceeds 95%, enabling proactive process adjustments that prevent quality issues.
Digital Technology | Response Time | Accuracy | Cost Reduction |
---|---|---|---|
Real-time XRF | 10-30 seconds | ±0.2% | 30-40% |
Automated sizing | 1-5 minutes | ±2% | 40-60% |
AI prediction | Real-time | 95%+ | 20-30% |
Digital twin | Variable | 90-95% | 15-25% |
IoT monitoring | Continuous | Variable | 25-35% |
How Does Automation Improve Processing Efficiency?
Robotic material handling systems eliminate manual labor in hazardous or repetitive tasks while improving consistency and reducing contamination risks. Automation transforms the entire operational landscape. Modern robotic systems can handle materials ranging from bulk powders to individual containers with precision and reliability that exceeds human capabilities. These systems operate continuously without breaks, increasing effective production time by 15-20%.
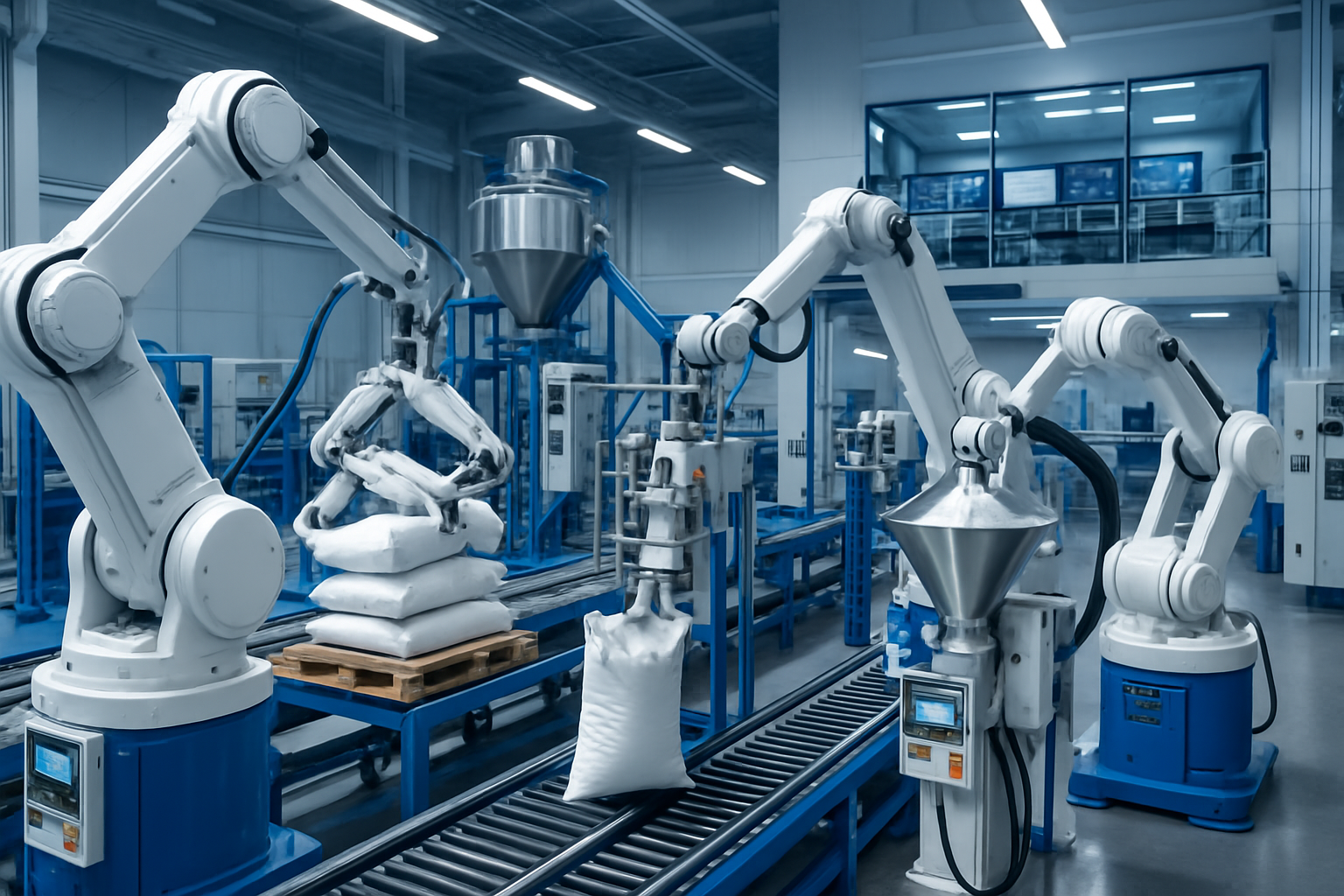
Automated packaging and bagging solutions integrate weighing, filling, and sealing operations into seamless production lines. These systems achieve filling accuracy within ±0.1% while operating at speeds up to 1200 bags per hour. Quality control systems built into packaging lines automatically reject packages that do not meet weight or seal integrity specifications.
Process control automation systems coordinate multiple processing units to optimize overall plant efficiency. These systems use advanced algorithms to balance production rates, energy consumption, and product quality across all operations. Integrated control systems typically improve overall equipment effectiveness by 20-30% while reducing operator workload.
Predictive maintenance technologies use vibration analysis, thermal imaging, and oil analysis to monitor equipment condition continuously. Machine learning algorithms analyze this data to predict when maintenance will be required, allowing scheduled maintenance during planned downtime. The impact on operational efficiency is dramatic. Predictive maintenance reduces unplanned downtime by 40-60% while extending equipment life by 20-30%.
Automation Technology | Efficiency Gain | Labor Reduction | Payback Period |
---|---|---|---|
Robotic handling | 15-20% | 60-80% | 2-3 years |
Automated packaging | 25-30% | 70-90% | 1.5-2 years |
Process control | 20-30% | 40-60% | 2-4 years |
Predictive maintenance | 40-60% | 30-50% | 1-2 years |
Remote monitoring | 10-15% | 20-30% | 3-5 years |
Which Environmental Technologies Enhance Sustainability?
Dust collection and emission control systems utilize advanced filtration technologies including pulse-jet baghouses and electrostatic precipitators to achieve emission levels well below regulatory requirements. Environmental compliance becomes a competitive advantage. Modern dust collection systems achieve collection efficiencies exceeding 99.9% while reducing energy consumption through optimized airflow design and variable speed fans.
Water recycling and treatment innovations enable closed-loop water systems that eliminate discharge while reducing fresh water consumption by 80-90%. Advanced treatment technologies including membrane filtration, ion exchange, and biological treatment remove contaminants and enable water reuse throughout processing operations.
Renewable energy integration includes solar panels, wind turbines, and biomass systems that reduce dependence on fossil fuels. Many processing facilities achieve 30-50% renewable energy content through on-site generation and power purchase agreements.
Environmental Technology | Emission Reduction | Cost Savings | Implementation Cost |
---|---|---|---|
Advanced dust collection | 99.9% | 10-15% | $500K-2M |
Water recycling | 90-95% | 20-30% | $1M-5M |
Waste heat recovery | 15-25% | 15-20% | $2M-8M |
Renewable integration | 30-50% | 25-40% | $3M-15M |
Carbon capture | 80-95% | Variable | $5M-20M |
What Implementation Strategies Ensure Success?
Technology assessment and selection criteria must balance performance benefits, implementation complexity, and financial returns to identify optimal solutions for specific facilities. Success depends on systematic evaluation and planning. Comprehensive assessments evaluate current operations, identify improvement opportunities, and prioritize technologies based on potential impact and implementation feasibility.
Phased implementation approaches reduce risk and enable learning from early phases to improve later implementations. Typical phases include pilot testing, limited production trials, and full-scale deployment. This approach allows refinement of operating procedures and training programs while demonstrating benefits to stakeholders.
Staff training and skill development requirements increase significantly with advanced technologies, requiring comprehensive programs that address both technical skills and change management. Training programs must cover equipment operation, maintenance procedures, troubleshooting, and safety protocols.
Implementation Phase | Duration | Success Factors | Risk Level |
---|---|---|---|
Assessment | 3-6 months | Thorough analysis | Low |
Pilot testing | 6-12 months | Realistic conditions | Medium |
Limited deployment | 12-18 months | Gradual scaling | Medium |
Full implementation | 18-36 months | Change management | High |
Optimization | Ongoing | Continuous improvement | Low |
How Do These Innovations Impact Cost Structure?
Capital investment requirements for comprehensive technology upgrades typically range from $5-20 million depending on facility size and technology selection. The financial impact extends far beyond initial costs. While substantial, these investments generate returns through improved efficiency, reduced operating costs, and enhanced product quality that commands premium pricing. Most facilities achieve positive cash flow within 2-4 years of implementation.
Operating cost reductions through efficiency gains affect multiple cost categories including energy, labor, maintenance, and raw materials. Energy costs typically decrease by 25-40% through improved efficiency and waste heat recovery. Labor costs reduce by 30-60% through automation, while maintenance costs decrease by 20-40% through predictive maintenance and improved equipment reliability.
Zircon powder market positioning improves significantly when manufacturers can guarantee consistent quality and meet demanding specifications. Premium zircon powder grades command 15-25% higher prices than standard products, making quality improvements highly profitable for manufacturers who invest in advanced processing technologies.
Cost Category | Typical Reduction | Investment Required | Payback Period |
---|---|---|---|
Energy costs | 40-60% | $2M-8M | 2-4 years |
Labor costs | 20-40% | $3M-12M | 3-5 years |
Maintenance costs | 20-40% | $1M-3M | 1-3 years |
Quality costs | 50-70% | $2M-6M | 1-2 years |
Environmental costs | 30-50% | $2M-10M | 3-7 years |
Return on investment analysis for technology adoption must consider both direct cost savings and indirect benefits including improved market position, regulatory compliance, and risk reduction. Comprehensive ROI calculations typically show returns of 15-25% annually for well-planned technology implementations. The competitive advantages gained often prove more valuable than direct cost savings.
What Emerging Technologies Shape Future Processing?
Nanotechnology applications in zircon powder processing focus on surface modification and particle engineering to create products with enhanced properties. These technologies open entirely new market opportunities. Nanocoating technologies can modify zircon particle surfaces to improve dispersion, reduce agglomeration, and enhance compatibility with various matrix materials. These modifications enable zircon powder use in applications previously dominated by other materials.
Three-dimensional printing for equipment manufacturing enables rapid prototyping and production of custom processing equipment components. Additive manufacturing allows creation of complex geometries impossible with traditional manufacturing methods, enabling optimized designs for specific applications. 3D printing reduces equipment lead times from months to weeks while enabling cost-effective customization.
Advanced materials for processing equipment include ceramic composites, superalloys, and engineered coatings that extend equipment life and improve performance. These materials resist wear, corrosion, and high temperatures better than conventional materials, reducing maintenance costs and improving product quality. Equipment life extensions of 50-100% are common with advanced materials.
Quantum computing applications in process optimization solve complex optimization problems that are intractable with conventional computers. The computational power is beyond current imagination. Quantum algorithms can optimize multiple variables simultaneously to find optimal operating conditions for complex processing systems. While still in early development, quantum computing promises to transform process optimization capabilities.
Emerging Technology | Development Stage | Potential Impact | Timeline |
---|---|---|---|
Nanotechnology | Commercial | High | Current |
3D printing | Early commercial | Medium | 2-5 years |
Advanced materials | Commercial | High | Current |
Quantum computing | Research | Very high | 10-20 years |
Biotechnology | Pilot scale | Medium | 5-10 years |
Hybrid processing technologies combine multiple processing methods to achieve results impossible with individual technologies. Examples include microwave-assisted grinding, plasma-enhanced separation, and bio-assisted flotation. These hybrid approaches often achieve superior performance while reducing energy consumption and environmental impact.
Next-generation automation incorporates artificial intelligence, machine learning, and advanced robotics to create fully autonomous processing systems. These systems can adapt to changing conditions, optimize performance continuously, and make decisions without human intervention. Autonomous systems promise to reduce operating costs while improving safety and consistency.
Conclusion
Modern zircon powder processing technologies transform traditional operations into highly efficient, environmentally sustainable, and profitable enterprises. These innovations reduce operating costs by 25-35% while improving zircon powder quality and environmental performance significantly. Companies that adopt comprehensive technology upgrade programs position themselves for long-term competitive advantage in increasingly demanding zircon powder markets. Global Industry’s expertise in technology integration and process optimization helps clients navigate complex implementation challenges and achieve maximum returns from their zircon powder technology investments.
FAQ Section
Q1: What is the most impactful innovation in zircon powder processing?
Advanced separation technologies, particularly AI-powered automated sorting systems, represent the most significant breakthrough. These systems can achieve 99%+ purity levels while reducing processing time by 40-60% compared to traditional methods, directly impacting both quality and cost efficiency.
Q2: How much can modern processing technologies reduce operational costs?
Comprehensive technology upgrades typically reduce operational costs by 25-35% through energy efficiency improvements, automation-driven labor savings, and improved yield optimization. Energy costs alone can decrease by 30-50% with advanced thermal processing and heat recovery systems.
Q3: What are the main barriers to adopting new processing technologies?
Primary barriers include high capital investment requirements ($2-10 million for comprehensive upgrades), technical complexity requiring specialized expertise, integration challenges with existing systems, and staff training needs. However, ROI typically occurs within 2-4 years for most implementations.
Q4: Which technologies offer the fastest return on investment?
Digital quality control systems and process automation typically provide the fastest ROI (12-18 months) due to immediate improvements in yield, quality consistency, and labor efficiency. These technologies require lower capital investment while delivering measurable operational benefits.
Q5: How do these innovations affect product quality and consistency?
Modern processing technologies dramatically improve product consistency, with coefficient of variation in particle size distribution reduced from ±15% to ±3%. Chemical purity levels increase from 95-97% to 99%+, while batch-to-batch variation decreases by 70-80%, enabling premium pricing and expanded market opportunities.