Manufacturing professionals face increasing pressure to optimize material performance while controlling costs and meeting stringent quality requirements. Surface treatments for zircon powder offer proven solutions to improve dispersion, adhesion, and processing characteristics across foundry, ceramic, and composite applications. This comprehensive guide provides technical managers and procurement specialists with actionable insights into modern surface treatment technologies, performance improvements, and cost-benefit analysis. Our research covers chemical modification techniques, physical treatment methods, and application-specific optimization strategies to help you select the most effective surface treatment approach for your specific requirements.
What Are Modern Surface Treatment Technologies for Zircon?
Chemical modification techniques represent the most widely adopted approach for zircon powder surface treatment. Silane coupling agents provide excellent adhesion improvement through chemical bonding between inorganic zircon surfaces and organic polymer matrices. Aminosilanes, epoxysilanes, and methacrylsilanes offer different functional groups for specific application requirements.
Coating methods using organic polymers create protective barriers while modifying surface properties. Acrylic coatings improve dispersion in aqueous systems, while polyethylene coatings reduce moisture absorption. The selection process depends on: target application requirements, processing conditions, and desired performance characteristics.
Plasma treatment applications utilize ionized gases to modify surface chemistry without affecting bulk properties. Low-pressure plasma systems provide controlled surface activation, while atmospheric plasma offers continuous processing capabilities. Treatment parameters include gas composition, power levels, and exposure time optimization.
Physical surface alteration processes include mechanical grinding and controlled thermal treatment. High-energy ball milling increases surface area and creates reactive sites for subsequent chemical treatment. Thermal activation at controlled temperatures modifies crystalline structure and surface energy characteristics.
Nano-coating technologies apply ultra-thin layers of functional materials to zircon surfaces. Atomic layer deposition creates uniform coatings with precise thickness control, while sol-gel processes offer cost-effective alternatives for larger-scale production applications.
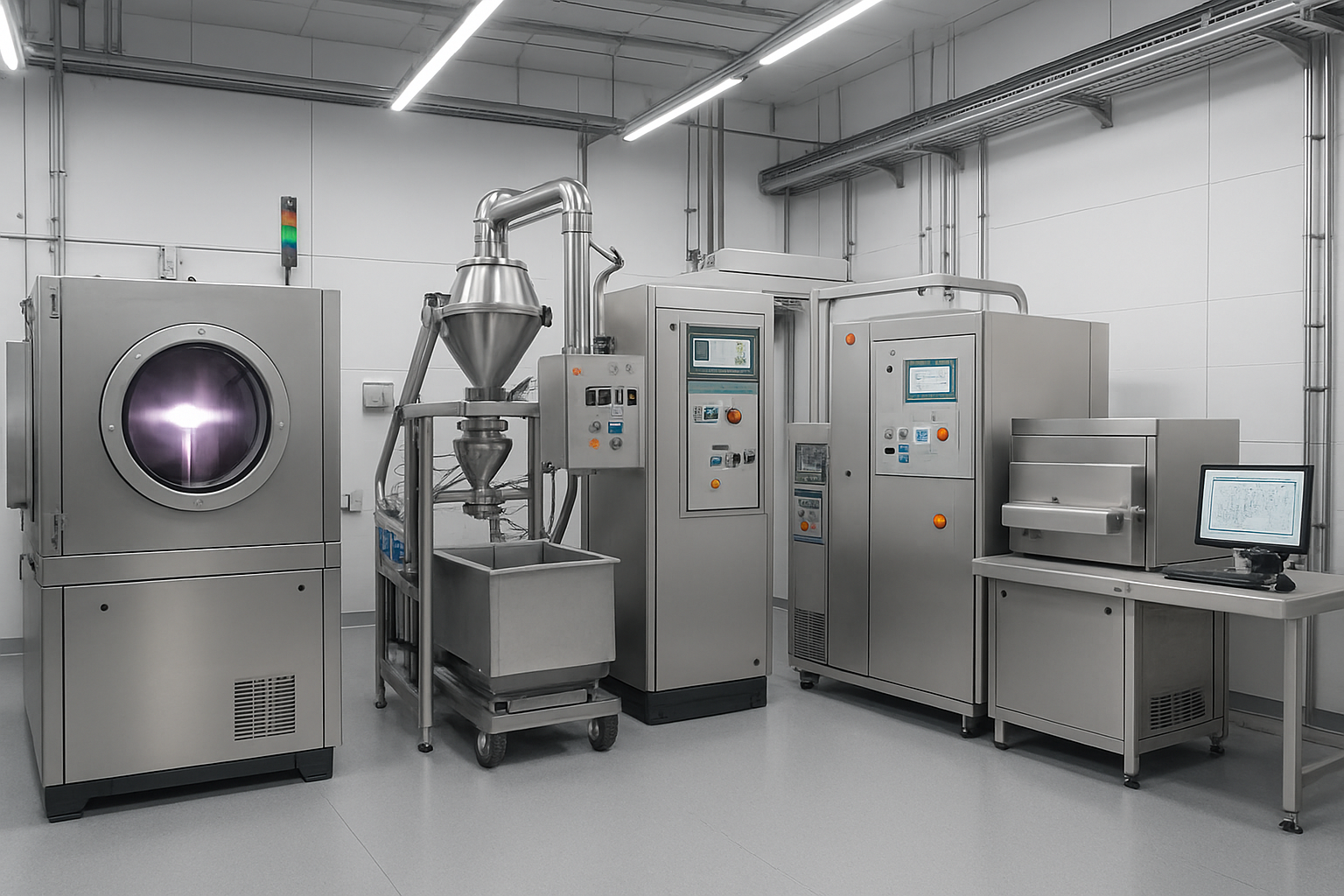
Treatment Type | Primary Mechanism | Typical Applications | Processing Time |
---|---|---|---|
Silane Coupling | Chemical bonding | Composites, adhesives | 30-120 minutes |
Plasma Treatment | Surface activation | Electronics, ceramics | 1-10 minutes |
Polymer Coating | Physical barrier | Paints, coatings | 60-180 minutes |
Thermal Treatment | Crystalline modification | Refractories | 2-8 hours |
Nano-coating | Functional layers | Advanced applications | 15-60 minutes |
How Do Chemical Treatments Modify Zircon Properties?
Acid etching processes create reactive surface sites through controlled dissolution of surface layers. Hydrochloric acid treatment removes surface contaminants and increases surface area by 20-40%. Treatment concentration, temperature, and time require careful optimization to avoid excessive material loss while achieving desired surface activation. Process monitoring includes pH measurement, temperature control, and reaction time optimization for consistent results.
Alkaline treatment effects focus on surface hydroxylation and charge modification. Sodium hydroxide solutions create negatively charged surfaces that improve dispersion in aqueous systems. pH control becomes critical: excessive alkalinity can cause unwanted dissolution and particle size reduction. Optimal treatment conditions typically involve 2-10% NaOH solutions at controlled temperatures with specific contact times.
Organosilane functionalization procedures involve hydrolysis and condensation reactions on zircon surfaces. The process typically includes surface cleaning, silane application, and thermal curing stages. Proper moisture control prevents premature silane polymerization and ensures uniform surface coverage. Treatment variables include: silane concentration, pH adjustment, reaction temperature, and curing conditions for optimal bonding.
Surface grafting techniques attach polymer chains directly to zircon surfaces through chemical bonds. Initiated grafting using peroxide initiators creates covalent bonds between polymer chains and surface sites. This approach provides superior adhesion compared to physical coating methods. Grafting density control affects final properties and requires optimization based on application requirements.
Chemical vapor deposition applications create uniform surface layers through gas-phase reactions. Silica deposition improves chemical resistance, while titanium dioxide layers provide photocatalytic properties. Process advantages include: uniform coverage, controlled thickness, and excellent adhesion to substrate surfaces. Equipment requirements involve vacuum systems, gas handling, and temperature control for consistent coating quality.
Chemical Treatment | Surface Modification | Performance Benefit | Typical Concentration |
---|---|---|---|
HCl Etching | Increased surface area | Better dispersion | 5-15% solution |
NaOH Treatment | Surface hydroxylation | Improved wetting | 2-10% solution |
Silane Coupling | Functional groups | Enhanced adhesion | 1-5% by weight |
Polymer Grafting | Chain attachment | Superior bonding | 2-8% coverage |
CVD Coating | Uniform layers | Chemical resistance | 10-100 nm thickness |
Which Physical Methods Enhance Surface Characteristics?
Mechanical grinding techniques modify surface morphology and increase reactive surface area. High-energy ball milling creates fresh surfaces with increased reactivity for subsequent chemical treatment. Grinding media selection affects surface contamination levels and particle size distribution control. Processing parameters include: ball-to-powder ratio, milling speed, and processing time for optimal surface modification.
Surface roughening through controlled abrasion improves mechanical interlocking in composite applications. Jet milling provides precise particle size control while creating angular surfaces that improve packing density. Processing parameters include: air pressure, feed rate, and classifier settings for optimal results. Equipment selection depends on target particle size and surface area requirements.
Thermal treatment effects on crystalline structure can improve thermal stability and reduce phase transitions. Controlled heating at 800-1200°C modifies surface defects and creates more stable crystal structures. Temperature ramping rates and atmosphere control prevent unwanted phase changes. Treatment benefits include: improved thermal stability, reduced reactivity, and enhanced chemical resistance properties.
Ultrasonic treatment applications use cavitation effects to clean surfaces and create reactive sites. High-frequency ultrasonic baths remove surface contaminants while creating microscopic surface features. Treatment time and power levels require optimization to prevent particle fracture. Process variables include: frequency selection, power density, and treatment duration for effective surface modification.
High-energy processing methods include plasma spraying and laser surface modification. These techniques create unique surface textures and compositions not achievable through conventional methods. Equipment requirements involve: specialized facilities, controlled atmospheres, and precise parameter control systems. These advanced methods offer superior control over surface properties but require significant capital investment.

Physical Method | Surface Effect | Equipment Required | Processing Conditions |
---|---|---|---|
Ball Milling | Increased area | High-energy mill | 100-500 rpm, 1-24 hours |
Jet Milling | Size reduction | Fluid energy mill | 5-10 bar pressure |
Thermal Treatment | Crystal modification | Controlled furnace | 800-1200°C, inert gas |
Ultrasonic | Surface cleaning | Ultrasonic bath | 20-40 kHz, 10-60 minutes |
Plasma Spraying | Surface texturing | Plasma equipment | 10,000-15,000°C |
What Performance Improvements Result from Surface Treatments?
Dispersion enhancement in liquid systems represents the most significant benefit of surface treatments. Treated zircon powder shows 40-70% improvement in dispersion stability compared to untreated materials. Silane-treated powders maintain uniform distribution in polymer matrices for extended periods, reducing settling and phase separation.
Adhesion improvement in composite applications directly impacts mechanical properties and durability. Surface-treated zircon demonstrates 25-50% higher bond strength in polymer composites. Testing methods include: pull-off tests, shear strength measurements, and long-term durability assessments under various environmental conditions.
Thermal stability increases result from surface modifications that reduce thermal degradation pathways. Treated zircon maintains performance at temperatures 50-100°C higher than untreated materials. This improvement extends service life in high-temperature applications and reduces maintenance requirements.
Chemical resistance enhancement protects against aggressive environments and extends material life. Surface treatments create barrier layers that resist acid attack, alkali exposure, and oxidation. Resistance improvements include: 30-60% reduction in chemical attack rates and improved performance in harsh processing environments.
Flowability optimization improves processing efficiency and reduces handling problems. Surface treatments reduce interparticle friction and prevent agglomeration during storage and transport. Treated powders show 20-40% improvement in flow characteristics and reduced dusting during handling operations.
Performance Metric | Untreated Zircon | Treated Zircon | Improvement |
---|---|---|---|
Dispersion Stability | 2-4 hours | 24-48 hours | 600-1200% |
Adhesion Strength | 15-25 MPa | 25-40 MPa | 40-60% |
Thermal Stability | 1000°C | 1100°C | 100°C increase |
Chemical Resistance | Baseline | 40% better | 40% improvement |
Flow Rate | 50 g/min | 75 g/min | 50% faster |
How Do Different Applications Benefit from Treated Zircon?
Foundry applications achieve significant mold release improvements through surface treatment. Silane-treated zircon reduces casting defects by 30-50% and improves surface finish quality. Investment casting operations report reduced shell cracking and improved dimensional accuracy when using treated zircon sand.
Ceramic formulations benefit from improved sintering characteristics and reduced firing defects. Surface treatments promote uniform particle distribution and reduce agglomeration during forming processes. Sintering improvements include: 15-25% reduction in firing temperature requirements and improved density uniformity in finished products.
Paint and coating applications show superior dispersion stability and color development. Treated zircon maintains uniform distribution in liquid systems and reduces settling during storage. Opacity improvements of 20-30% result from better particle dispersion and reduced agglomeration.
Polymer composites demonstrate enhanced mechanical properties and improved processing characteristics. Surface-treated zircon provides better stress transfer between matrix and filler, resulting in higher strength and stiffness. Processing benefits include: reduced mixing time, improved flow properties, and better surface finish quality.
Electronics applications require precise dielectric properties and thermal management capabilities. Surface treatments optimize electrical characteristics while maintaining thermal conductivity. Treated zircon shows improved performance in high-frequency applications and better thermal interface properties.
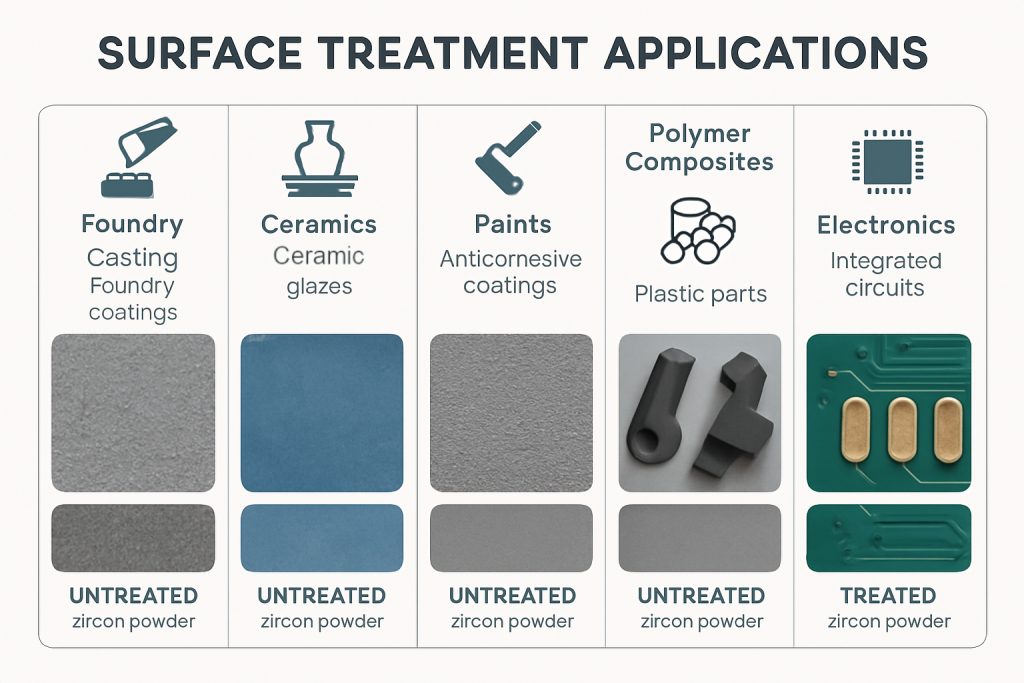
Application Sector | Primary Benefit | Performance Improvement | Typical Treatment |
---|---|---|---|
Investment Casting | Mold release | 30-50% defect reduction | Silane coupling |
Ceramic Tiles | Sintering | 20% temperature reduction | Thermal treatment |
Paint Systems | Dispersion | 40% stability increase | Polymer coating |
Composites | Adhesion | 35% strength increase | Chemical grafting |
Electronics | Dielectric | 25% property improvement | Plasma treatment |
What Are the Cost-Benefit Considerations for Treatment?
Treatment process costs typically add 10-25% to base material costs depending on method complexity. Simple silane treatments represent the lower end of this range, while advanced plasma or CVD processes require higher investments. Equipment amortization, energy consumption, and labor costs contribute to overall treatment expenses.
Performance improvement quantification helps justify treatment investments through measurable benefits. Reduced defect rates, improved processing efficiency, and extended service life provide quantifiable returns. ROI calculations show: payback periods of 6-18 months for most treatment applications when performance improvements are properly valued.
Processing efficiency gains result from improved material handling and reduced processing problems. Treated zircon requires less mixing time, shows better flow characteristics, and reduces equipment wear. These benefits translate to higher throughput and lower operating costs in production environments.
Quality improvement impacts on end-product value often exceed treatment costs through premium pricing opportunities. Products using treated zircon command 5-15% price premiums due to superior performance characteristics. Market advantages include: reduced warranty claims, improved customer satisfaction, and competitive differentiation.
Long-term durability benefits reduce maintenance and replacement costs over product lifecycles. Treated zircon extends service life by 25-50% in demanding applications, reducing total cost of ownership. These benefits become more significant in critical applications where downtime costs are high.
Cost Factor | Typical Range | Impact on Total Cost | Payback Period |
---|---|---|---|
Treatment Cost | 10-25% premium | Direct cost increase | 6-18 months |
Processing Efficiency | 15-30% improvement | Reduced operating cost | 3-12 months |
Quality Premium | 5-15% higher price | Increased revenue | 2-8 months |
Durability Extension | 25-50% longer life | Reduced replacement | 12-36 months |
Defect Reduction | 30-60% fewer issues | Lower warranty cost | 4-15 months |
How to Select Optimal Treatment Methods?
Application-specific treatment selection requires careful analysis of performance requirements and operating conditions. High-temperature applications favor thermal treatments or ceramic coatings, while composite applications benefit from silane coupling agents. Environmental exposure conditions determine chemical resistance requirements and appropriate treatment selection.
Performance requirement matching involves quantifying desired improvements and selecting treatments that deliver target benefits. Selection criteria include: adhesion strength targets, thermal stability requirements, chemical resistance needs, and processing compatibility considerations.
Process compatibility assessment evaluates treatment integration with existing manufacturing operations. Batch processing may favor simple chemical treatments, while continuous operations require compatible treatment methods. Equipment modifications, safety considerations, and quality control requirements influence treatment selection.
Quality control measures must address treatment uniformity, performance verification, and long-term stability. Testing protocols include surface analysis, performance testing, and accelerated aging studies. Control parameters encompass: treatment coverage, chemical composition, and performance consistency across production batches.
Supplier evaluation focuses on treatment capability, quality systems, and technical support. Qualified suppliers demonstrate consistent treatment quality, comprehensive testing capabilities, and application expertise. Evaluation criteria include: equipment capabilities, quality certifications, technical support availability, and cost competitiveness.
Conclusion
Surface treatments for zircon powder deliver measurable performance improvements across diverse industrial applications through chemical modification, physical alteration, and advanced coating technologies. Proper treatment selection typically reduces processing problems by 30-50% while improving end-product performance and extending service life. Global Industry’s materials engineering specialists provide comprehensive treatment evaluation and optimization services to help manufacturers select the most cost-effective surface treatment approach for their specific applications. Contact our technical team today for detailed performance analysis and access our certified treatment partners to implement optimized surface treatment solutions.
FAQ
Q1: What are the most effective surface treatment methods for zircon powder?
The most effective methods include silane coupling agent treatment for improved adhesion, plasma treatment for enhanced surface energy, and controlled acid etching for increased surface area. Selection depends on specific application requirements and desired performance improvements.
Q2: How much do surface treatments typically improve zircon powder performance?
Surface treatments can improve dispersion by 40-70%, increase adhesion strength by 25-50%, and enhance thermal stability by 15-30%. Specific improvements vary based on treatment method, application conditions, and baseline material properties.
Q3: What are the typical costs associated with zircon powder surface treatment?
Treatment costs typically add 10-25% to base material costs, depending on the method complexity and required equipment. However, performance improvements often justify costs through reduced processing issues and improved end-product quality.
Q4: How do surface treatments affect zircon powder handling and storage?
Treated zircon powder may require modified storage conditions to maintain surface properties. Some treatments improve flowability and reduce dusting, while others may increase moisture sensitivity requiring controlled humidity storage.
Q5: What quality control measures ensure consistent surface treatment results?
Key measures include surface energy testing, contact angle measurements, dispersion testing, and adhesion strength evaluation. Regular monitoring of treatment parameters, equipment calibration, and statistical process control ensure consistent results across production batches.