In the rapidly evolving world of advanced materials, composites stand as a cornerstone of innovation, offering unparalleled combinations of strength, lightness, and functionality. At the heart of many high-performance composites lies a critical component: filler materials. Among these, zircon powder has emerged as a material of significant interest, particularly for applications demanding enhanced mechanical, thermal, and chemical properties.
However, the mere inclusion of zircon powder is not enough to guarantee optimal composite performance. The true determinant of its functionality lies in its surface characteristics—the intricate details at the interface between the powder particles and the surrounding matrix. For B2B buyers and decision-makers in industries ranging from aerospace to medical devices, understanding these surface features is paramount. It enables informed material selection, precise formulation, and ultimately, the development of composites that meet stringent performance requirements and drive market success.
This article will delve into the specific surface characteristics of zircon powder that dictate its efficacy in composite applications, exploring how these features influence overall composite properties and the methods used to optimize them for superior performance.
What defines zircon powder surface characteristics?
The functionality of zircon powder in composite materials is intrinsically linked to its surface characteristics. These features, often microscopic, play a pivotal role in determining how the powder interacts with the polymer or ceramic matrix, influencing everything from dispersion and processing to the final mechanical and thermal properties of the composite. Understanding these defining attributes is the first step toward optimizing composite formulations.
Particle size and distribution are fundamental. Finer particles offer a larger surface area, leading to increased reactivity and better interfacial adhesion if properly managed. However, excessively fine particles can also lead to agglomeration, making uniform dispersion challenging. A well-controlled particle size distribution is crucial for achieving optimal packing density and reducing porosity within the composite, enhancing its mechanical integrity.
Characteristic | Description | Impact on Composites | Typical Range/Value |
---|---|---|---|
Particle Size | Average diameter. | Affects surface area, packing, mechanicals. | 0.1 µm – 50 µm |
PSD | Range of sizes. | Influences viscosity, packing, homogeneity. | Narrow to Broad |
SSA | Surface area per mass. | More sites for interaction, adhesion. | 1 – 20 m²/g |
Porosity | Voids within/on particles. | Affects density, strength, conductivity. | Low to Moderate |
Surface area and porosity are closely related. High surface area provides more sites for chemical bonding. Porosity influences density and thermal properties. A dense, non-porous surface is preferred for strength and minimal moisture absorption.
Surface chemistry and functional groups are critical. Outermost atomic layers have specific chemical groups (e.g., hydroxyl) that react or bond. Modifying these alters wettability and reactivity, improving compatibility.
Surface Aspect | Description | Influence on Interaction | Common Groups |
---|---|---|---|
Hydroxyl (-OH) | Reactive sites. | Key for coupling agents, chemical bonding. | -OH |
Acidity/Basicity | Lewis/Brønsted character. | Affects adsorption, interaction. | Zr-O sites |
Surface Charge | Electrical charge. | Influences agglomeration/dispersion. | Negative |
Impurities | Trace elements/phases. | Can cause defects, alter reactivity. | Fe₂O₃, TiO₂ |
Surface energy and wettability describe liquid spreading. High surface energy means better wettability, leading to stronger interfacial adhesion. Surface treatments tailor energy for optimal wetting and bonding.
Finally, morphology and roughness refer to shape and texture. Spherical particles disperse and pack better. Roughness influences mechanical interlocking. Optimizing these balances processability and final composite properties.
How do surface features impact composite properties?
The intrinsic surface characteristics of zircon powder profoundly influence the macroscopic properties of composites. The interface is where stresses transfer and interactions occur.
Interfacial adhesion and bonding are direct impacts. Strong adhesion is crucial for efficient stress transfer. Good bonding, often via modification, ensures filler reinforces the matrix, distributing stress evenly and preventing crack propagation, improving mechanical properties.
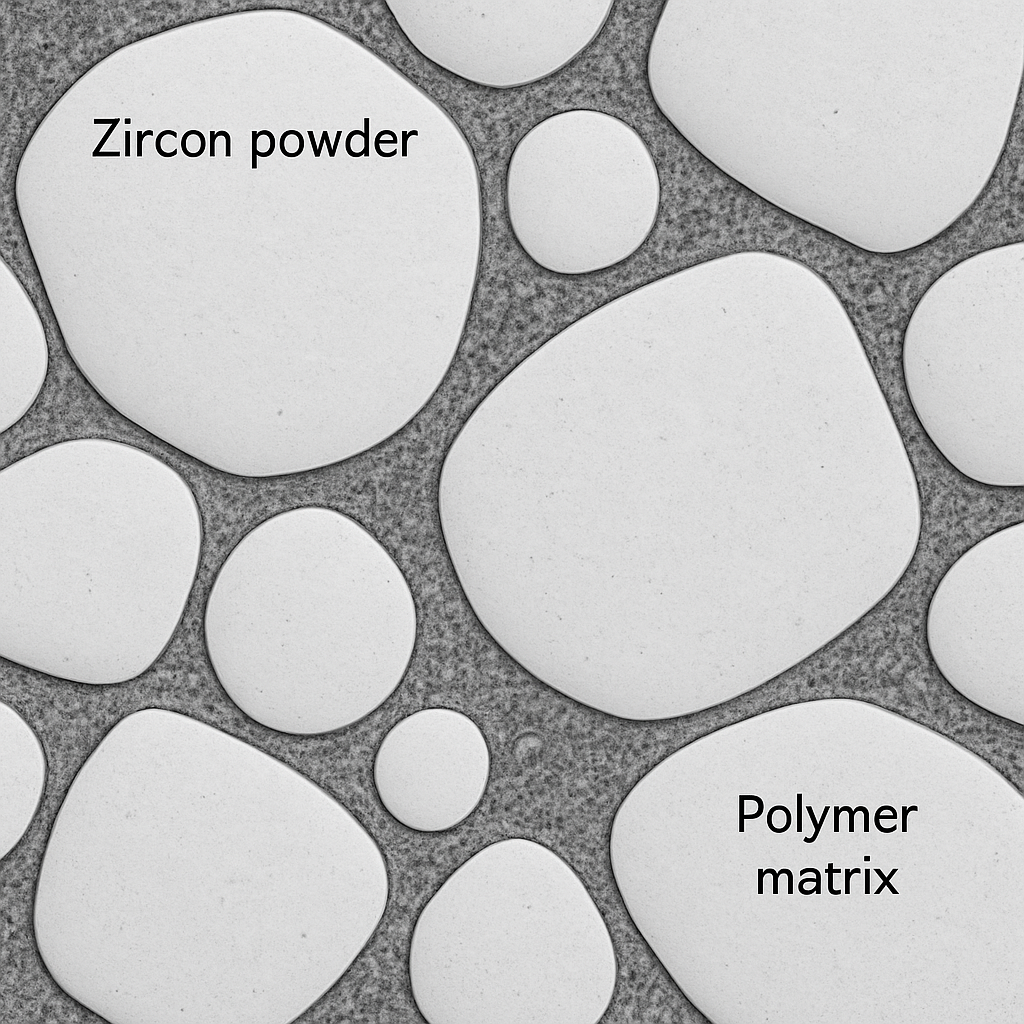
Mechanical strength and toughness are significantly affected by the filler-matrix interface quality. Zircon powder enhances tensile strength and impact toughness. Strong bonding leads to higher strength by transferring load. Improved adhesion enhances toughness by promoting energy dissipation. Optimal dispersion reduces stress concentration.
Composite Property | Impact of Zircon Surface | Desired Surface Feature |
---|---|---|
Strength | Efficient load transfer. | High surface energy, reactive groups. |
Toughness | Energy dissipation. | Controlled interfacial strength. |
Thermal Stability | Zircon’s inherent stability. | Chemically stable surface. |
Thermal Conductivity | Efficient heat transfer. | Good physical contact. |
Electrical Insulation | Influences dielectric. | Clean surface, no impurities. |
Chemical Resistance | Inert zircon protects matrix. | Chemically inert surface. |
Wear Resistance | Hard zircon particles. | Strong adhesion, optimal size. |
Thermal stability and conductivity can be tailored. Zircon has excellent thermal stability. Proper integration enhances thermal performance. Good interfacial contact allows efficient heat transfer. Surface properties can also help achieve lower thermal conductivity for insulation. Optimized treatments mitigate thermal expansion mismatch.
Electrical properties and dielectric constant are influenced by surface characteristics. Zircon is a dielectric. Surface chemistry and treatments affect dielectric constant, loss tangent, and breakdown strength. Precise control is essential for electronic applications, with modification achieving desired insulation or specific dielectric behaviors.
Chemical resistance and durability are enhanced when zircon powder is effectively integrated. Zircon is chemically inert. Proper bonding protects the composite from aggressive chemical environments. Surface modifications create a barrier, improving long-term durability.
What methods modify zircon powder surfaces?
Various surface modification methods tailor zircon powder characteristics, improving interfacial adhesion, dispersion, and overall composite performance.
Silane coupling agents are widely used. Silanes are bifunctional molecules that react with zircon surface hydroxyl groups and are compatible with the polymer matrix, creating a molecular bridge. This significantly improves interfacial adhesion, stress transfer, and mechanical properties.
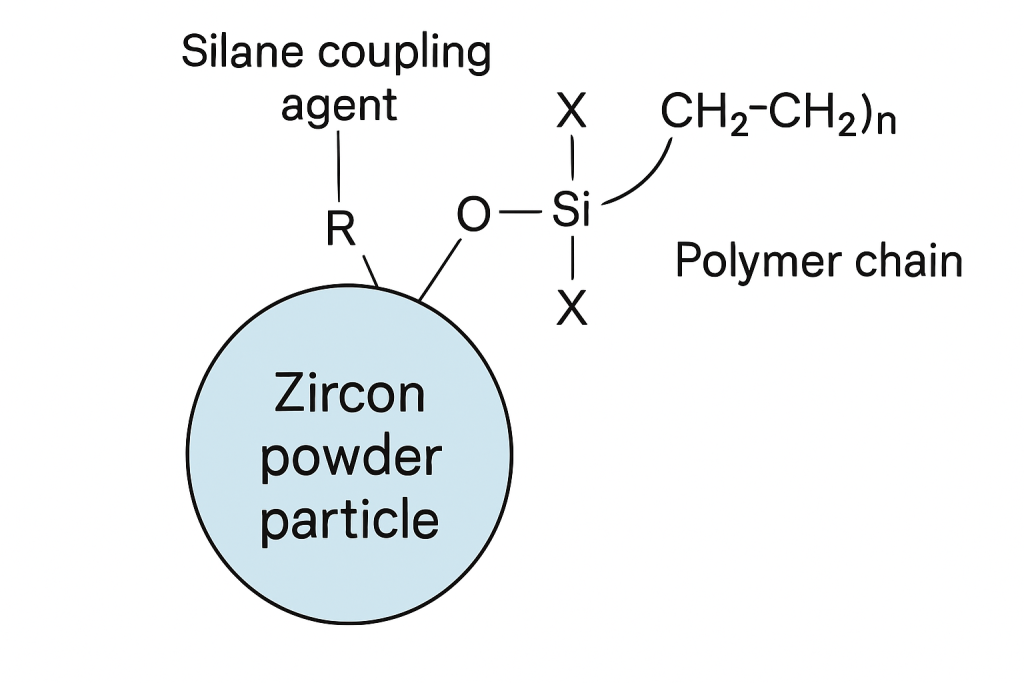
Method | Principle | Advantages | Disadvantages | Example |
---|---|---|---|---|
Silane Coupling | Chemical bridge. | Improved adhesion, versatile. | Moisture sensitive, agglomeration. | Dental/structural composites. |
Polymer Grafting | Coating with polymer. | Enhanced compatibility, dispersion. | Complex, costly. | Thermoplastic matrices. |
Inorganic Coatings | Thin layer deposition. | Altered chemistry, barrier. | Increased size, delamination. | Silica coating for bonding. |
Plasma Treatment | Ionized gases. | Dry process, reactive surfaces. | Equipment intensive, damage. | Activating surfaces for PEEK. |
Mechanochemical | Mechanical energy. | Increased reactivity, new groups. | Defects, altered morphology. | Co-milling with additives. |
Polymer grafting and encapsulation involve chemically attaching or physically coating particles with polymer. Grafting creates a brush-like layer for better compatibility. Encapsulation forms a polymer shell, protecting the filler and enhancing interaction.
Inorganic coatings deposit thin layers of alumina, silica, or titania. These alter surface chemistry, improve wettability, or provide a barrier. Applied via sol-gel or chemical precipitation.
Plasma treatment and surface etching are physical techniques. Plasma uses ionized gases to clean, introduce functional groups, or cross-link. Etching increases surface roughness for mechanical interlocking.
High-energy milling and mechanochemical activation are mechanical methods. Milling reduces particle size and increases surface area. Mechanochemical activation induces chemical reactions on the surface. These are often combined with chemical treatments.
Each method bridges the gap between inorganic zircon and organic polymer matrices, ensuring homogeneous dispersion and strong interfacial bonding. Selection depends on the specific system, desired properties, and economics.
How are modified zircon powders evaluated?
Rigorous evaluation of modified zircon powder surfaces and their impact on composite properties is crucial, using surface characterization and composite performance testing.
Surface characterization techniques understand chemical and physical changes. SEM and TEM provide visual information. XPS analyzes elemental composition. FTIR spectroscopy identifies functional groups. BET surface area analysis measures changes in surface area and porosity.
Technique | Information Provided | Purpose in Development |
---|---|---|
SEM | Morphology, dispersion. | Visualize modification effectiveness. |
XPS | Elemental composition. | Confirm grafting, chemical changes. |
FTIR | Chemical bonds. | Verify bonding, surface chemistry. |
Contact Angle | Surface energy, wettability. | Assess compatibility, optimize wetting. |
Mechanical Testing | Strength, toughness. | Quantify modification impact. |
Thermal Analysis | Thermal stability. | Evaluate degradation, interaction. |
Rheological | Viscosity, flow. | Understand processability. |
Wettability and contact angle measurements directly assess compatibility. Lower contact angle indicates better wettability, leading to improved interfacial adhesion.
Mechanical testing of composites is paramount. Tensile strength, flexural strength, and impact toughness tests demonstrate reinforcement and stress transfer efficiency. Improved properties indicate successful surface treatment.
Thermal analysis techniques like TGA and DSC evaluate thermal stability and phase transitions. TGA determines organic modifier amount. DSC identifies changes in glass transition temperature.
Dispersion analysis ensures uniform distribution. Optical microscopy, SEM, and X-ray microtomography visualize dispersion and identify agglomerates. Poor dispersion compromises performance.
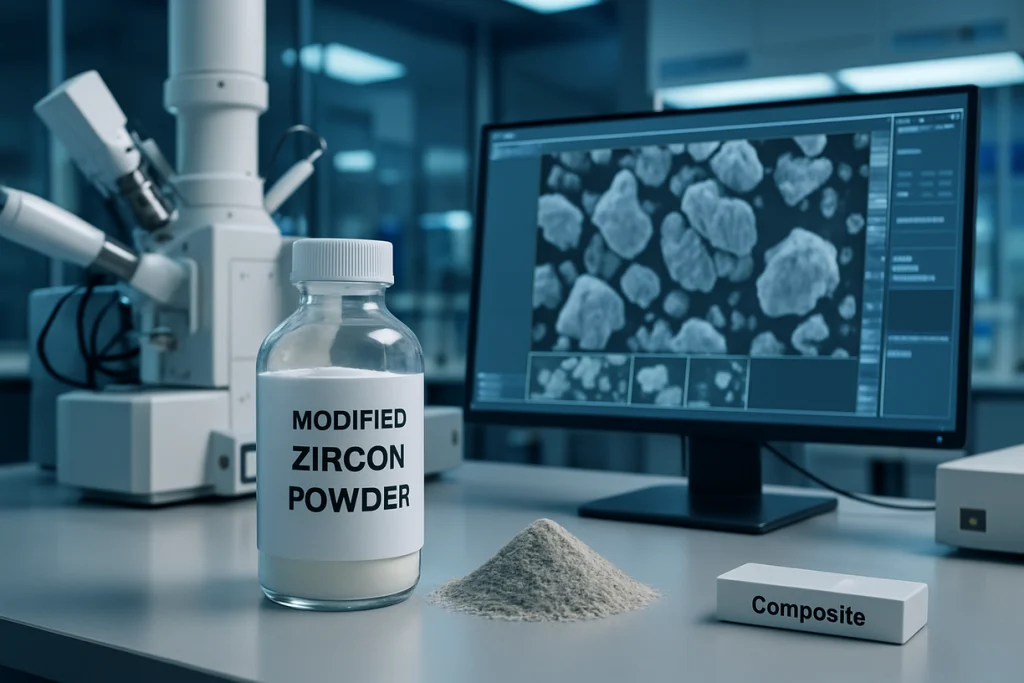
What challenges arise in optimizing zircon powder surfaces?
Optimizing zircon powder surfaces presents challenges from inherent properties, modification complexities, and diverse composite requirements.
Achieving uniform and stable surface coverage is primary. Factors like particle size and agglomerates make uniform coverage difficult. The modified layer must remain intact under processing and long-term use.
Challenge | Description | Mitigation Strategies |
---|---|---|
Uniform Coverage | Consistent coating difficult. | Optimized conditions, multi-step processes. |
Agglomeration | Particles tend to clump. | Pre-dispersion, in-situ modification. |
Cost-Effectiveness | Expensive modifications. | Cost-efficient modifiers, optimized loading. |
Long-Term Stability | Must withstand harsh conditions. | Robust agents, thorough testing. |
Scalability | Lab to industrial scale. | Continuous methods, QC protocols. |
Compatibility | Not optimal for all matrices. | Versatile agents, tailored treatments. |
Controlling agglomeration and dispersion is significant. Zircon powder tends to agglomerate, acting as defects. While modification aims to improve dispersion, the process itself can induce agglomeration if not controlled. Effective dispersion requires optimized treatment and processing.
Balancing cost-effectiveness with performance is practical. Advanced modification techniques can be expensive. Benefits must outweigh increased costs. Manufacturers seek cost-effective methods delivering significant enhancements.
Ensuring long-term stability and durability in various service environments is crucial. Composites are exposed to harsh conditions. The modified interface must maintain integrity. Accelerated aging tests and environmental exposure studies validate durability.
Scaling up laboratory-scale processes to industrial production presents engineering challenges. Consistency and quality control require robust process design and significant investment.
What future trends enhance zircon powder functionality?
The field is evolving, driven by demand for higher performance and new technologies.
Nanotechnology and nanocoatings are at the forefront. Nano-sized particles or ultrathin nanocoatings (e.g., graphene) enhance interfacial properties, provide barrier properties, or introduce new functionalities. Challenges include uniform nanocoating and preventing agglomeration.
Future Trend | Description | Potential Impact |
---|---|---|
Nanotechnology | Nano-sized zircon/coatings. | Enhanced interfacial properties. |
Bio-inspired | Mimicking natural mechanisms. | Superior adhesion, self-repair. |
Sustainable Methods | Green solvents, less waste. | Reduced environmental footprint. |
Advanced Characterization | In-situ, atomic microscopy. | Precise design, faster development. |
Multi-functional | Single modification, multiple properties. | Versatile composites. |
Smart Composites | Responsive to stimuli. | Built-in monitoring, adaptive. |
Bio-inspired surface modifications draw inspiration from natural systems for enhanced adhesion, self-healing, or biocompatibility. This interdisciplinary approach combines materials science with biology and chemistry.
Sustainable and eco-friendly modification methods are increasingly important. There is a drive to reduce hazardous chemicals, minimize waste, and consume less energy, exploring green solvents and enzymatic approaches.
Advanced characterization techniques provide deeper insights into the filler-matrix interface. In-situ spectroscopy, advanced electron microscopy, and computational modeling precisely understand bonding and degradation mechanisms, crucial for designing effective modifications.
Multi-functional surface treatments are an emerging trend, imparting multiple properties simultaneously (e.g., adhesion, thermal conductivity, antimicrobial). This reduces manufacturing complexity and leads to versatile composites. Design requires sophisticated understanding of surface chemistry.
These trends highlight a shift towards more precise, sustainable, and multi-functional approaches, promising next-generation composites with unprecedented performance.
Conclusion
The functionality of zircon powder in composite materials is inextricably linked to its surface characteristics. These attributes dictate how effectively zircon powder interacts with the matrix, influencing critical composite properties. Through various modification methods, manufacturers can tailor these surface properties to optimize interfacial adhesion and dispersion. Rigorous evaluation ensures efficacy. While challenges persist, ongoing research promises to unlock even greater potential. For B2B buyers, understanding these characteristics and their optimization is key to selecting the right materials, driving innovation and success.
FAQ
Q1: Why are zircon powder surface characteristics important in composites?
Zircon powder surface characteristics are crucial because they dictate how well the powder interacts and bonds with the composite matrix. Proper surface properties ensure uniform dispersion, strong interfacial adhesion, and efficient stress transfer, essential for achieving optimal mechanical, thermal, and chemical performance in the final composite material.
Q2: What is the role of silane coupling agents in modifying zircon powder?
Silane coupling agents act as molecular bridges between the inorganic zircon powder and the organic polymer matrix. They create a robust chemical link that significantly improves interfacial adhesion, enhances stress transfer, and boosts the mechanical properties of the composite, preventing delamination and improving durability.
Q3: How does particle size and distribution affect zircon powder functionality in composites?
Particle size and distribution significantly impact functionality. Finer particles offer larger surface area for interaction, but can cause agglomeration. A well-controlled distribution is vital for optimal packing density, reduced porosity, and homogeneous dispersion, contributing to enhanced mechanical integrity.
Q4: What are some common challenges in optimizing zircon powder surfaces for composites?
Key challenges include achieving uniform and stable surface coverage, controlling agglomeration and ensuring proper dispersion, balancing cost-effectiveness with performance, and ensuring long-term stability and durability of the modified interface. Scaling up laboratory processes to industrial production is also complex.
Q5: What future trends are expected to enhance zircon powder functionality in composites?
Future trends include nanotechnology and nanocoatings, bio-inspired modifications, sustainable methods, advanced characterization techniques, and multi-functional surface treatments. These promise significant advancements in zircon powder composite technology.