For purchasing managers and technical directors, sourcing high-quality zircon powder is a constant challenge. Inconsistent material quality directly impacts production efficiency and the performance of your final products. This often leads to costly rework and customer dissatisfaction. The truth is, achieving superior results demands a deep understanding of the processing methods that truly deliver premium zircon powder. This article cuts through the complexity, providing a clear guide to the techniques that ensure purity, consistency, and optimal performance. We will detail the critical steps and considerations, empowering you to make informed procurement decisions that directly benefit your operational excellence and bottom line.
What is zircon powder and its uses?
Zircon powder, derived from zircon sand, is a material with exceptional properties. Zircon sand, a naturally occurring mineral, serves as the raw material. This sand undergoes various processes to become the fine powder used across many industries. Its key characteristics include a very high melting point, excellent chemical inertness, and strong resistance to abrasion.
These attributes make it indispensable in demanding applications. For example, in the ceramics industry, zircon powder is vital for producing glazes and opacifiers, giving products a smooth finish and durability. It also plays a significant role in refractories, where its heat resistance makes it ideal for lining high-temperature furnaces.
The foundry industry uses zircon powder for molds and cores, ensuring precision and a clean surface finish for metal castings. Even in the nuclear sector, specific grades of zircon powder are used due to their low neutron absorption cross-section. So, what does this mean for your business? It means that for any application requiring extreme heat resistance, chemical stability, or precise material properties, zircon powder is often the material of choice. The quality of this powder directly influences the performance and longevity of your end products, making the selection of processing methods a critical decision for B2B buyers.
Why does zircon powder quality matter?
The quality of zircon powder is not merely a preference; it is a fundamental requirement for consistent manufacturing and product reliability. Impurities, even in minute quantities, can severely compromise the performance of the final product. For instance, iron or titanium oxides can cause discoloration in ceramic glazes or reduce the refractoriness of furnace linings.
Particle size distribution is another critical factor. A narrow and consistent particle size range ensures uniform packing density and predictable sintering behavior. This is essential for high-performance ceramics and precision castings. Consider this scenario: if your zircon powder has a wide particle size distribution, it can lead to uneven shrinkage during firing, resulting in cracks or deformities in the finished product.
Crystallinity and phase composition also play a role. Different crystalline phases of zirconia, which can form during processing, have varying thermal expansion coefficients. This can cause internal stresses and micro-cracks in materials subjected to thermal cycling. Ultimately, using low-quality zircon powder can lead to increased scrap rates, higher production costs, and a damaged reputation due to product failures. Understanding these quality parameters is paramount for any purchasing manager seeking to optimize material inputs.
Quality Parameter | Impact on Product Performance |
---|---|
Purity | Prevents discoloration, improves refractoriness |
Particle Size | Affects packing density, sintering, surface finish |
Crystallinity | Influences thermal stability, prevents micro-cracks |
Moisture Content | Impacts flowability, prevents agglomeration |
Specific Surface Area | Affects reactivity, binder demand |
What are common zircon processing methods?
Producing high-quality zircon powder begins with the raw material: zircon sand. This sand, extracted from mineral deposits, contains various impurities that must be removed. The initial steps often involve beneficiation processes. Gravity separation, for example, uses differences in density to separate zircon from lighter minerals. Magnetic separation then removes magnetic impurities like ilmenite.
But that’s just the start. After these initial steps, the zircon concentrate undergoes more advanced treatments. These can be broadly categorized into mechanical, chemical, and thermal methods. Mechanical treatments focus on physical size reduction and classification. Chemical treatments aim to remove specific impurities through reactions. Thermal treatments involve high temperatures to alter the material’s properties or remove volatile compounds.
The choice of method depends on several factors, including the desired purity level, the specific end application, and economic considerations such as processing cost and energy consumption. Each method contributes uniquely to the final powder’s characteristics. A combination is often employed to achieve the highest quality.
How does milling affect powder quality?
Milling is a crucial step in zircon powder production, primarily aimed at reducing particle size. This process transforms coarser zircon particles into a fine powder, which is essential for many applications. Various types of milling equipment are used, each with its own advantages.
Ball mills, for instance, use ceramic or steel balls to grind the material. These are suitable for producing relatively coarse powders. Jet mills, on the other hand, use high-velocity air or steam to cause particles to collide. This results in extremely fine powders with a narrow particle size distribution. Vibratory mills also offer precise control over particle size.
Here’s the critical point: the parameters of milling, such as milling speed, duration, and the type of milling media, directly influence the final particle size, shape, and surface area. Improper milling can lead to excessive fines, broad particle size distribution, or even contamination from the milling media itself.
For example, using steel balls in a ball mill can introduce iron impurities. This is unacceptable for high-purity applications. Achieving a narrow particle size distribution is often a key objective, as it ensures consistent material behavior in subsequent processing steps and in the final product.
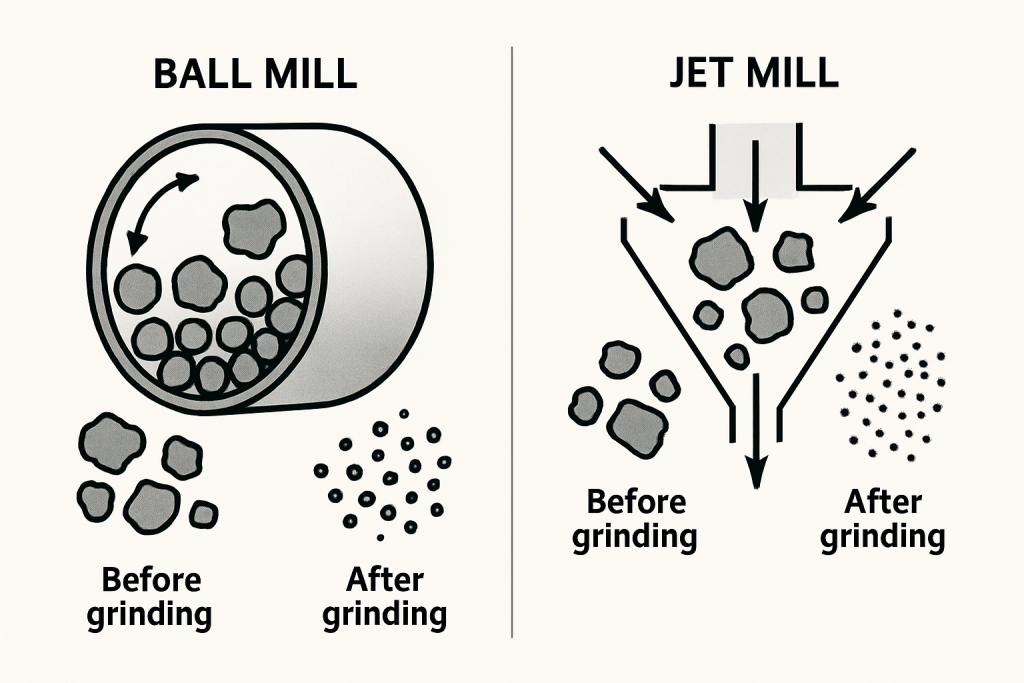
What about chemical purification techniques?
Chemical purification techniques are indispensable for achieving the highest purity levels in zircon powder. While mechanical methods can remove physical impurities, chemical methods target specific elements that are chemically bound or finely dispersed within the zircon structure. Why is this so important? Because even trace amounts of certain elements, like iron, titanium, or aluminum, can negatively impact the optical, electrical, or thermal properties of the final product.
Acid leaching is a common technique, where zircon powder is treated with strong acids such as sulfuric acid or hydrochloric acid. These acids dissolve impurities while leaving the zircon largely unaffected. Alkali fusion methods involve mixing zircon with alkaline compounds and heating to high temperatures, followed by leaching to remove soluble impurities.
Solvent extraction and ion exchange are more advanced techniques used for ultra-high purity applications. These are capable of selectively removing specific metal ions. Each chemical method has its own set of challenges, including managing corrosive reagents and waste disposal. However, their benefits in terms of purity enhancement are undeniable. For instance, in the production of high-performance ceramics for electronics, chemical purification is essential to prevent electrical leakage or short circuits caused by metallic impurities.
Chemical Purification Method | Target Impurities | Advantages | Disadvantages |
---|---|---|---|
Acid Leaching | Fe, Ti, Al | Effective, relatively simple | Corrosive reagents, waste |
Alkali Fusion | Si, some metals | High removal efficiency | High temperature, energy intensive |
Solvent Extraction | Specific metal ions | Ultra-high purity | Complex, costly |
Ion Exchange | Specific metal ions | High selectivity | Regeneration required |
How do drying methods impact final powder?
Drying is a critical post-processing step that significantly influences the final characteristics of zircon powder. The primary goal is to remove moisture. However, the method chosen can affect particle morphology, flowability, and the tendency for agglomeration. Think about it: if the powder retains too much moisture, it can clump together, making it difficult to handle and process in subsequent manufacturing steps.
Spray drying is a widely used method, especially for producing spherical, free-flowing particles. A slurry of zircon is atomized into a hot drying chamber, where water rapidly evaporates, leaving behind uniform particles. Rotary drying involves tumbling the powder in a heated rotating cylinder, suitable for larger volumes. Vacuum drying is used for heat-sensitive materials or when very low moisture content is required.
The choice of drying method, along with parameters like temperature and drying time, directly impacts the powder’s bulk density, specific surface area, and overall consistency. Improper drying can lead to hard agglomerates that are difficult to break down, affecting the final product’s homogeneity. Optimizing the drying process is essential for ensuring the powder is ready for storage, transport, and immediate use in manufacturing without issues.
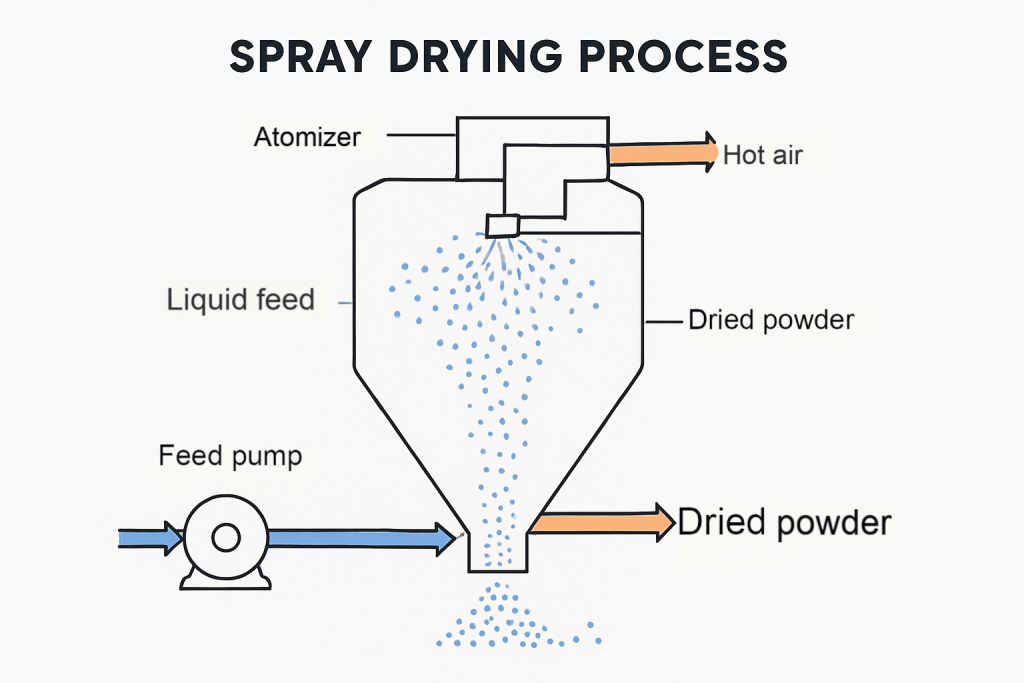
What quality control steps are crucial?
Rigorous quality control is not an option; it is a necessity for any supplier of premium zircon powder. Both in-process and final product testing are vital to ensure consistency and meet stringent customer specifications. How do you know you’re getting what you pay for? Analytical techniques play a key role.
X-ray fluorescence (XRF) is used to determine the elemental composition, ensuring the absence of unwanted impurities. X-ray diffraction (XRD) identifies the crystalline phases present, confirming the desired zirconia structure. Scanning electron microscopy (SEM) provides insights into particle morphology and size distribution. Particle size analysis (PSA) techniques, such as laser diffraction, precisely measure the particle size range.
These tests verify chemical purity, particle size, specific surface area, and other critical parameters. Batch consistency is paramount; each shipment must perform identically to the last. Traceability, from raw material to finished product, provides an audit trail for quality assurance. Adherence to industry standards and certifications, such as ISO 9001, further demonstrates a commitment to quality. For example, a supplier might provide a Certificate of Analysis (CoA) with each batch, detailing all tested parameters and confirming compliance with specifications. This level of scrutiny provides purchasing managers with confidence in their material supply.
Quality Control Test | Purpose | Key Information Provided |
---|---|---|
XRF | Elemental composition | Purity, impurity levels |
XRD | Crystalline phases | Phase purity, structure |
SEM | Particle morphology | Shape, surface features |
PSA | Particle size distribution | Uniformity, flowability |
Moisture Analysis | Water content | Drying effectiveness |
How to select a premium zircon supplier?
Selecting the right zircon powder supplier is a strategic decision that extends beyond mere price comparison. What should you look for? Start by evaluating their commitment to quality and consistency. A premium supplier will have robust quality control processes, as discussed previously, and be transparent about their testing methodologies. Their processing capabilities are also key; a supplier with advanced milling, purification, and drying technologies is more likely to produce superior powder.
Requesting samples and conducting your own trials is an essential step. This allows you to assess how the powder performs in your specific application before committing to large orders. Understanding their supply chain and logistics capabilities is also important to ensure timely and reliable delivery. Ultimately, it’s about partnership. A long-term partnership with a reliable supplier can provide technical support, consistent material, and even custom solutions for your unique needs.
For instance, a supplier might offer technical consultations to help you optimize your processes based on their powder’s characteristics. This collaborative approach ensures that you consistently receive the highest quality zircon powder, directly contributing to your operational success and product innovation.
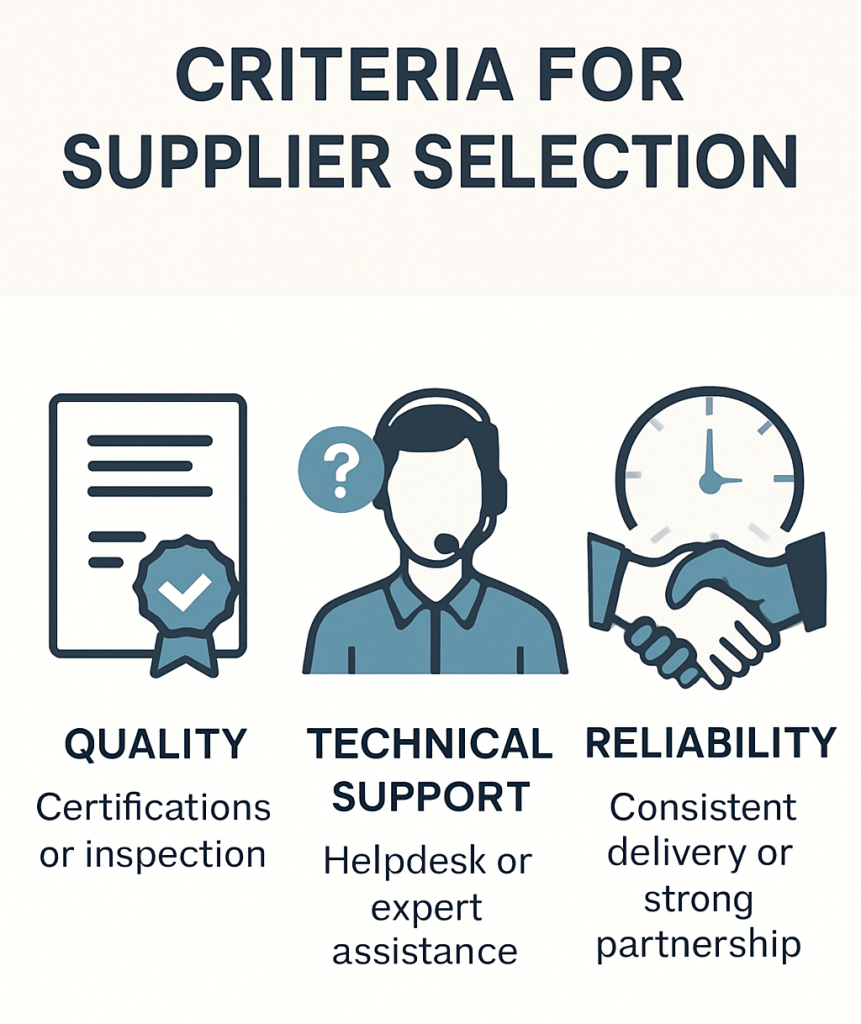
Conclusion
In summary, achieving premium zircon powder quality is not accidental; it results from meticulous processing, rigorous quality control, and strategic supplier selection. Understanding the nuances of milling, chemical purification, and drying ensures a material that consistently meets demanding industrial specifications. By prioritizing these methods, businesses can significantly reduce production defects and extend the lifespan of their end products, directly impacting profitability. Ready to elevate your material standards? Partner with Global Industry for your premium zircon powder needs. Our expertise and commitment to quality ensure you receive materials that drive operational excellence. Visit our website for more resources on advanced material solutions and to begin a partnership built on reliability and innovation.
FAQ Section
Q1: What is the primary benefit of using premium zircon powder? Using premium zircon powder ensures superior performance and reliability in critical applications, reducing defects and extending the lifespan of end products. Its high purity and controlled particle size lead to consistent results and improved material properties.
Q2: Can different processing methods be combined for zircon powder? Yes, often a combination of mechanical, chemical, and thermal processing methods is used to achieve specific purity levels and particle characteristics. This multi-step approach allows for precise control over the final powder’s quality.
Q3: How does particle size distribution affect zircon powder applications? Particle size distribution is crucial as it directly influences properties like packing density, sintering behavior, and surface reactivity. A narrow and consistent distribution is often preferred for high-performance applications to ensure uniform material properties.
Q4: What are common impurities found in raw zircon sand? Common impurities in raw zircon sand include iron oxides, titanium oxides, alumina, and silica. These impurities must be significantly reduced or removed during processing to achieve the high purity required for premium zircon powder.
Q5: Why is quality control important when purchasing zircon powder? Quality control is vital to verify that the zircon powder meets specified purity, particle size, and other performance criteria. Rigorous testing ensures batch consistency, minimizes production issues, and guarantees the material’s suitability for demanding industrial applications.