Zircon powder is a vital industrial material. It is essential for ceramics, refractories, electronics, and nuclear industries. This is due to its high melting point, chemical inertness, and thermal stability.
For B2B buyers, understanding the technical properties that define commercial-grade zircon powder quality is not just about specifications. It is about securing consistent performance, optimizing production processes, and mitigating risks in critical applications.
This article will guide purchasing managers through the key quality parameters, testing methods, and selection criteria for zircon powder. It aims to provide a clear path to informed procurement decisions.
What is Zircon Powder and Its Uses?
Zircon powder is derived from the mineral zircon (zirconium silicate, ZrSiO4). It is a finely ground material with unique properties that make it indispensable across various industrial sectors.
Its composition primarily consists of zirconium, silicon, and oxygen, often with trace amounts of other elements. The purity and crystalline structure of zircon powder directly influence its performance in end-use applications. What does this mean for you? It means that the fundamental makeup of the powder dictates its suitability for your specific needs.
In ceramics, zircon powder is a key ingredient for glazes, opacifiers, and structural ceramics. This is due to its high refractive index and thermal shock resistance. In refractories, it is valued for its ability to withstand extreme temperatures and corrosive environments, making it ideal for furnace linings and crucibles.
The electronics industry uses it in specialized components. Its neutron absorption properties make it suitable for certain nuclear applications. The quality requirements vary significantly across these uses.
For example, high-purity, fine-grained zircon powder is essential for dental ceramics where aesthetic and mechanical properties are critical. In contrast, coarser grades might be acceptable for some refractory applications. This highlights why understanding the specific quality parameters is so important; it directly impacts the final product’s integrity and performance.
For instance, in the production of ceramic tiles, the particle size distribution of zircon powder directly influences the opacity and whiteness of the glaze. A consistent particle size ensures uniform application and a smooth finish, preventing defects that could lead to costly rejections.
Similarly, in the investment casting industry, zircon flour is used to create molds for high-temperature alloys. The thermal stability and low thermal expansion of the zircon are critical to prevent mold cracking and ensure dimensional accuracy of the cast parts. Any deviation in quality can lead to significant material waste and production delays. This is why a clear understanding of the technical properties is not just academic, but directly impacts your bottom line.
Why Particle Size Matters in Zircon?
Particle size distribution (PSD) is a fundamental property of zircon powder. It profoundly affects its behavior during processing and the final properties of the end product. PSD refers to the range of particle sizes present in a sample and their relative proportions. It is typically measured using techniques such as laser diffraction or sieve analysis. Why should you care about PSD? Because it directly influences how the powder packs, flows, and reacts.
For example, in ceramic applications, a finer particle size generally leads to better sintering behavior. This allows for denser and stronger final products at lower firing temperatures. This is because smaller particles have a higher surface area-to-volume ratio, promoting more efficient diffusion and bonding during the sintering process. Conversely, an overly fine powder can lead to excessive shrinkage and cracking.
In dental ceramics, a narrow and consistent PSD is crucial for achieving high translucency and mechanical strength. Variations can lead to aesthetic flaws or structural weaknesses. For refractories, a broader PSD might be preferred to achieve optimal packing density, which improves thermal insulation and resistance to slag penetration.
Consider a case where a manufacturer of high-end ceramic glazes switched to a zircon powder with a slightly different PSD. They observed a noticeable change in glaze opacity and surface finish, requiring costly adjustments to their firing cycles. This illustrates how even subtle changes in PSD can have significant downstream effects.
Another example is in the production of specialized technical ceramics for electronic components. Here, precise control over particle size is paramount to achieve the required dielectric properties and prevent defects that could cause component failure. Manufacturers often specify sub-micron particle sizes with tight distribution ranges to meet these demanding requirements. This level of precision underscores the importance of PSD in high-value applications.
Table 1: Impact of Particle Size Distribution on Zircon Powder Applications
Application Type | Desired PSD Characteristics | Impact on Product Performance | Example |
---|---|---|---|
Dental Ceramics | Fine, narrow distribution | High translucency, strength, smooth finish | Reduced polishing time, fewer aesthetic defects |
Refractories | Broad distribution | Optimal packing density, thermal insulation | Improved resistance to thermal shock, longer service life |
Glazes & Opacifiers | Consistent, controlled range | Uniform opacity, whiteness, surface quality | Prevention of mottling, consistent color |
Investment Casting | Specific mesh sizes | Mold strength, surface finish of castings | Reduced mold breakage, finer cast details |
Technical Ceramics | Ultra-fine, narrow distribution | Precise dielectric properties, high density | Enhanced electronic component reliability |
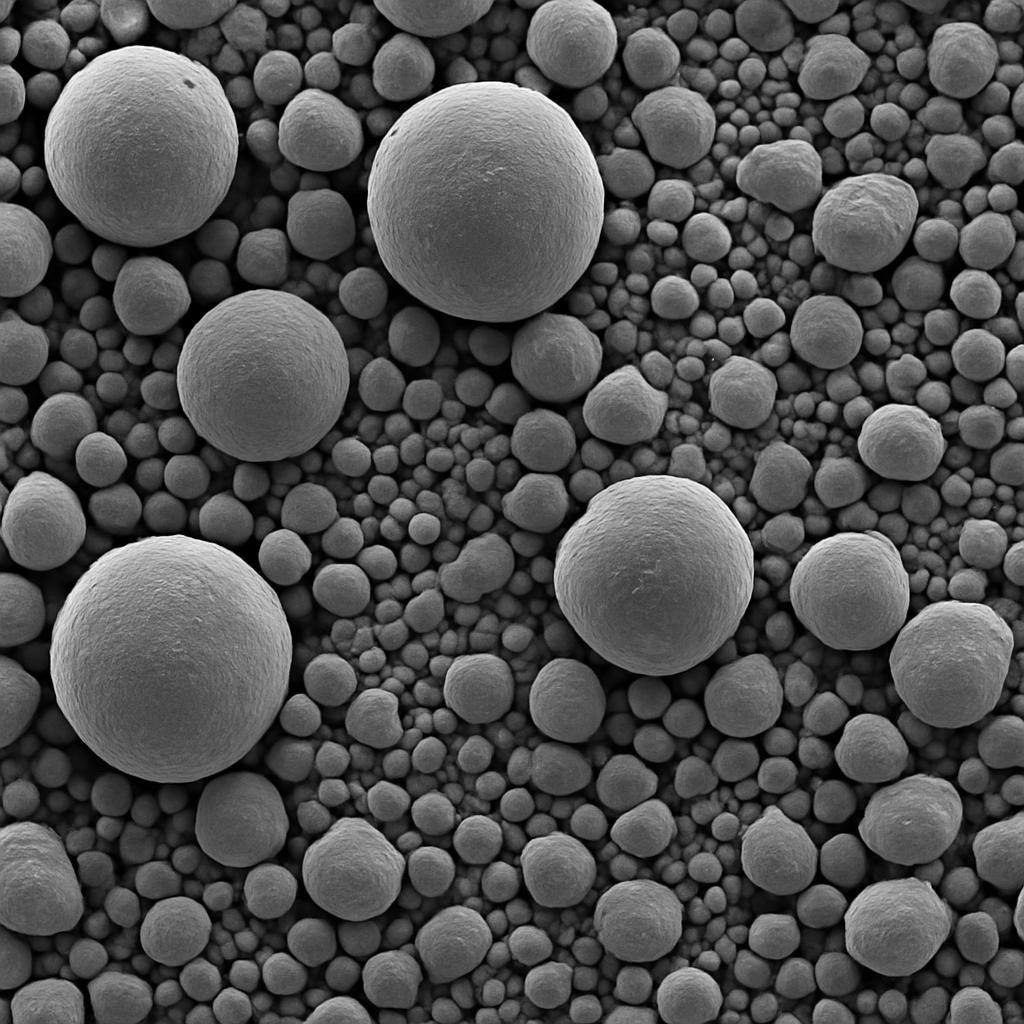
How Does Chemical Purity Affect Zircon?
Chemical purity is another defining characteristic of commercial-grade zircon powder. It refers to the absence of undesirable elements that can negatively impact its performance. The most common impurities include iron oxide (Fe2O3), titanium dioxide (TiO2), aluminum oxide (Al2O3), and silica (SiO2) beyond the stoichiometric amount. Why is purity so important? Because even small concentrations of impurities can alter the material’s properties.
For instance, iron oxide can cause discoloration in white ceramics, leading to undesirable yellow or brown tints. Titanium dioxide can affect the opacity and thermal stability. Aluminum oxide can influence the sintering behavior and mechanical strength.
For high-tech applications, such as those in the nuclear or electronics industries, even trace amounts of certain elements can be detrimental. Nuclear applications require extremely low levels of neutron-absorbing elements like boron and cadmium. In electronics, impurities can alter electrical conductivity or dielectric properties.
Analytical methods like X-ray fluorescence (XRF) and inductively coupled plasma-optical emission spectrometry (ICP-OES) are used to precisely determine the chemical composition and impurity levels. A manufacturer of high-purity ceramic crucibles, for example, found that a slight increase in Fe2O3 content in their zircon powder led to premature failure of the crucibles at high temperatures due to altered thermal expansion characteristics. This necessitated a costly recall and process adjustment.
Another example is in the production of piezoelectric ceramics, where specific electrical properties are critical. Impurities can act as charge carriers or disrupt the crystal lattice, significantly degrading the piezoelectric response. Suppliers often provide certificates of analysis (CoAs) detailing the chemical composition, allowing buyers to verify purity against their specifications. This rigorous approach to chemical purity ensures that the zircon powder performs as expected in demanding applications, preventing costly failures and maintaining product integrity.
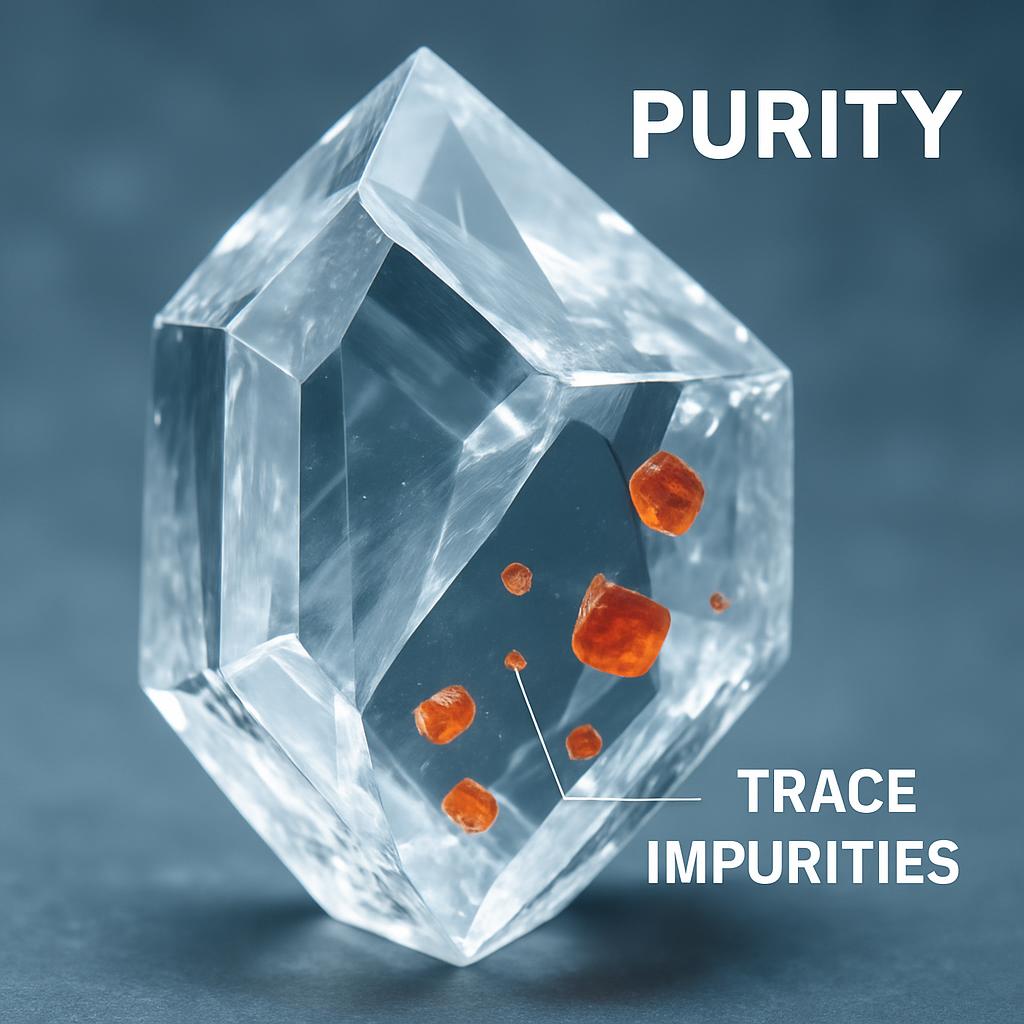
Understanding Radioactivity in Zircon Powder
Zircon, being a naturally occurring mineral, often contains trace amounts of naturally occurring radioactive materials (NORM). These are primarily uranium (U) and thorium (Th), and their decay products. What does this mean for your safety and compliance? It means that understanding and managing radioactivity levels is critical, especially for certain applications and regions.
Regulatory limits for radioactivity in zircon powder vary by country and application. For example, in some regions, there are strict limits for zircon used in consumer products or building materials. For nuclear applications, the focus is on neutron-absorbing elements, but overall radioactivity is also a consideration for handling and disposal.
Measurement techniques include gamma spectrometry, which can identify and quantify specific radionuclides. While the levels are generally low and pose minimal risk in most industrial uses, it is important for B2B buyers to be aware of these regulations and ensure their suppliers comply.
For instance, a company importing zircon powder for use in dental prosthetics must ensure that the radioactivity levels meet the stringent health and safety standards of their target market. Failure to do so could result in product rejection, legal penalties, and severe reputational damage.
Another example is in the production of specialized refractories for high-temperature furnaces, where long-term exposure to materials might be a concern. While not directly impacting the refractory performance, the NORM content could influence waste disposal classifications and handling procedures. Therefore, requesting a certificate of analysis that includes radioactivity data is a prudent step for buyers, allowing them to assess compliance and manage any associated risks. This proactive approach helps maintain regulatory compliance and ensures the safety of both products and personnel.
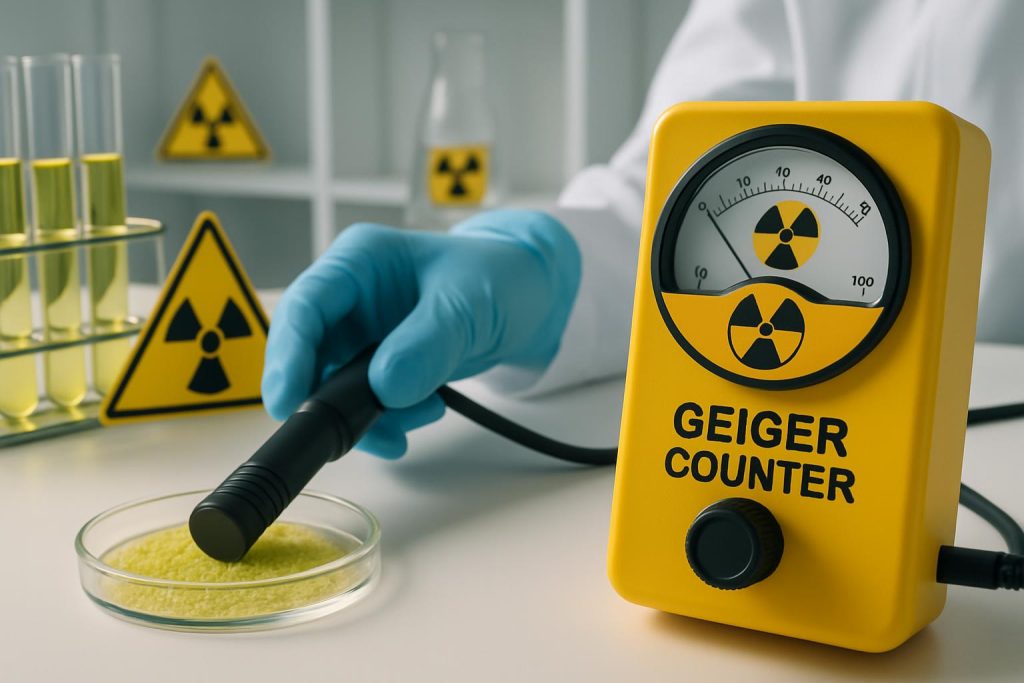
What are Key Physical Properties of Zircon?
Beyond chemical composition and particle size, several physical properties of zircon powder play a significant role in its commercial application and performance. These properties dictate how the powder behaves during processing and how the final product performs under various conditions. Why should you pay attention to these? Because they directly influence the material’s workability and end-use characteristics.
Density, specifically bulk density and true density, affects packing behavior and the final density of sintered products. A higher packing density often leads to less shrinkage during firing and a denser final product.
Specific surface area (SSA), measured by techniques like the BET method, relates to the total surface area per unit mass of the powder. A higher SSA generally indicates finer particles and can influence reactivity, adsorption, and binder requirements.
Morphology, or the shape of the zircon particles (e.g., angular, rounded, irregular), can impact flowability, packing density, and green strength of compacted parts. For example, spherical particles tend to flow better and pack more uniformly than irregular ones.
Thermal properties, such as thermal expansion and thermal conductivity, are critical for high-temperature applications. Zircon’s low thermal expansion and good thermal conductivity make it ideal for thermal shock resistance.
Mechanical properties, including hardness and fracture toughness, are important for wear-resistant applications. For instance, in the production of grinding media, a high hardness is essential for effective material removal and long service life.
Consider a manufacturer of precision ceramic components who experienced issues with inconsistent green strength and cracking during compaction. Upon investigation, they found that variations in the morphology of the incoming zircon powder were causing poor packing and uneven stress distribution. By working with their supplier to ensure a more consistent particle shape, they significantly reduced defects and improved production yield. This illustrates how seemingly subtle physical properties can have a substantial impact on manufacturing processes and product quality.
Another example is in the development of advanced refractory materials for specialized industrial furnaces. Here, the thermal expansion characteristics of the zircon powder are precisely matched with other components to prevent spalling and ensure structural integrity at extreme temperatures. Understanding these physical properties allows buyers to select zircon powder that is optimized for their specific manufacturing processes and desired product performance.
Table 2: Key Physical Properties of Zircon Powder and Their Relevance
Property | Description | Relevance to Application | Measurement Method |
---|---|---|---|
Density | Mass per unit volume (bulk, true) | Packing behavior, final product density | Pycnometry, Tap Density Tester |
Specific Surface Area (SSA) | Total surface area per unit mass | Reactivity, adsorption, binder demand | BET (Brunauer-Emmett-Teller) method |
Morphology | Particle shape (angular, rounded) | Flowability, packing, green strength | Scanning Electron Microscopy (SEM) |
Thermal Expansion | Change in volume with temperature | Thermal shock resistance, dimensional stability | Dilatometry |
Thermal Conductivity | Ability to conduct heat | Heat transfer, insulation properties | Laser Flash Analysis (LFA) |
Hardness | Resistance to indentation | Wear resistance, abrasive performance | Vickers, Knoop Hardness Tests |
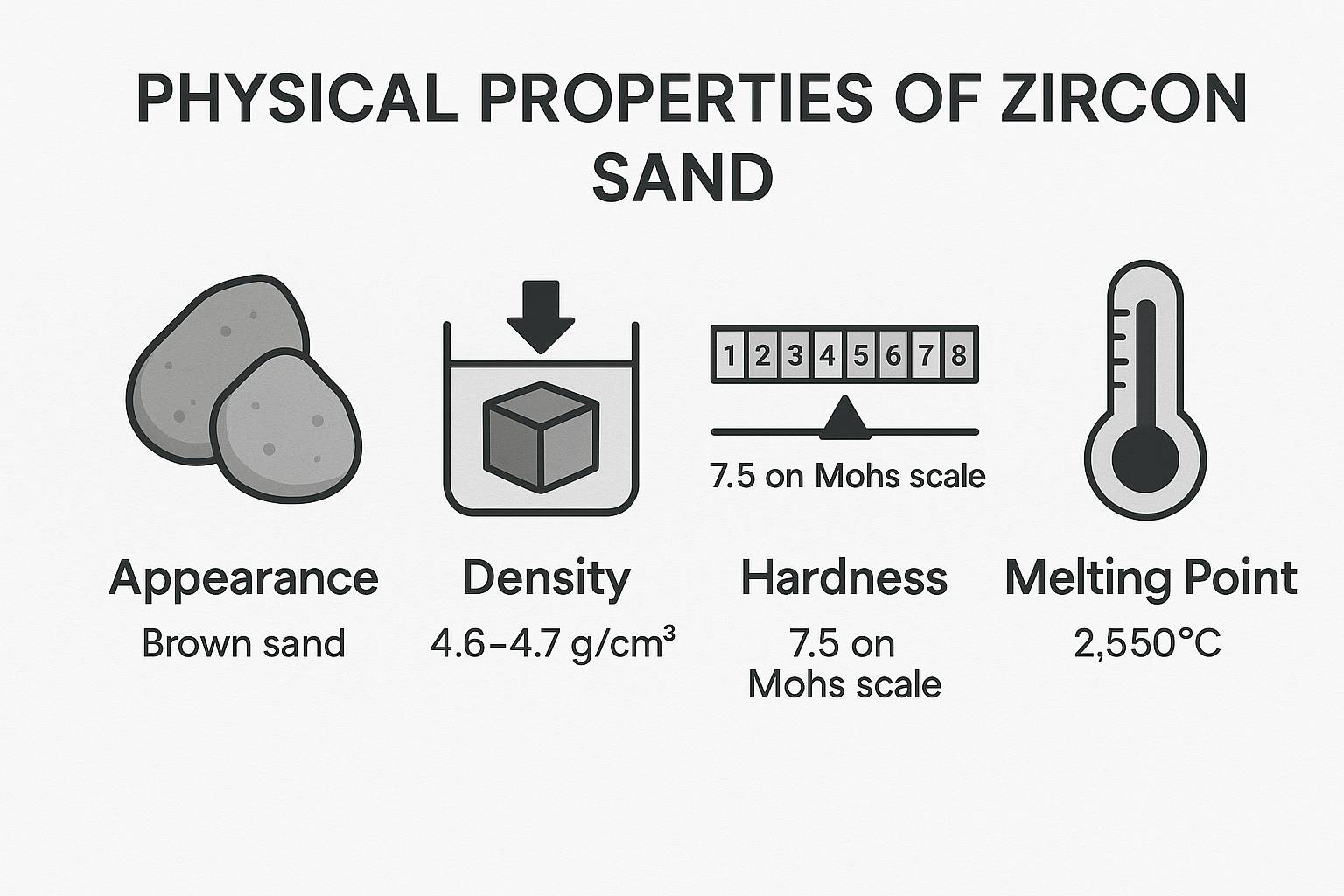
How is Zircon Powder Quality Tested?
To ensure that commercial-grade zircon powder meets the required specifications, a range of standardized testing methods are employed. These tests provide objective data on the powder’s properties, allowing both suppliers and buyers to verify quality and consistency. How can you be sure of what you are buying? By understanding the testing protocols.
Standardized testing methods, such as those established by ISO (International Organization for Standardization) and ASTM (American Society for Testing and Materials), provide a common framework for evaluating zircon powder. For example, ISO 13320 specifies particle size analysis by laser diffraction, while ASTM C373 covers water absorption, bulk density, apparent porosity, and true porosity of fired ceramic materials.
Laboratory equipment for quality assessment includes laser diffraction analyzers for PSD, XRF and ICP-OES for chemical composition, BET surface area analyzers, and dilatometers for thermal expansion. The importance of batch consistency cannot be overstated; even if a supplier’s product meets specifications, variations between batches can lead to production issues. Therefore, robust quality control (QC) procedures are essential, involving regular sampling and testing.
Many reputable suppliers also implement comprehensive quality assurance (QA) programs and hold certifications like ISO 9001, which indicates a commitment to quality management systems. For instance, a major electronics manufacturer sources zircon powder from a supplier that provides a Certificate of Analysis (CoA) with every batch, detailing PSD, chemical purity, and radioactivity levels, all verified by third-party labs. This rigorous testing and documentation process minimizes the risk of receiving off-spec material and ensures smooth production.
Another example is in the production of high-performance abrasives, where the consistency of zircon powder’s hardness and particle shape is critical for abrasive efficiency. Regular testing of these parameters ensures that the abrasive products maintain their cutting performance and durability. By insisting on comprehensive testing and working with certified suppliers, B2B buyers can significantly reduce their risk exposure and ensure the reliability of their end products.
Choosing the Right Commercial Zircon Powder
Selecting the appropriate commercial-grade zircon powder is a strategic decision. It directly impacts product quality, manufacturing efficiency, and cost-effectiveness. It requires a systematic approach that aligns material specifications with application requirements. What should guide your selection process? A clear understanding of your needs and supplier capabilities.
First, precisely match zircon powder specifications to your application requirements. This involves defining the critical parameters for your end product, such as desired mechanical strength, thermal resistance, or optical properties. Then, translate these into specific zircon powder characteristics (e.g., particle size range, purity levels, specific physical properties).
For example, if you are producing dental crowns, you will need ultra-fine, high-purity zircon powder with controlled radioactivity. Whereas for refractory bricks, a coarser, less pure grade might be sufficient.
Second, consider factors when selecting a supplier. Look for suppliers with a proven track record, robust quality control processes, transparent documentation (e.g., Certificates of Analysis), and the ability to provide consistent supply. Their technical support and willingness to collaborate on custom specifications can also be valuable.
Third, the importance of technical data sheets and samples cannot be overemphasized. Always request and thoroughly review technical data sheets. Whenever possible, obtain samples for in-house testing to validate performance in your specific process.
Finally, conduct a cost-benefit analysis of different quality grades. While higher purity or finer particle sizes often come at a premium, the long-term benefits of reduced defects, improved product performance, and increased manufacturing efficiency can outweigh the initial cost difference.
For instance, a company manufacturing ceramic components for aerospace applications initially opted for a lower-cost zircon powder. However, they soon faced high rejection rates due to inconsistent sintering and poor mechanical properties. By switching to a higher-grade zircon powder, despite the increased material cost, they reduced their rejection rate by 15%, leading to significant overall savings and improved product reliability. This demonstrates that the cheapest option is not always the most economical in the long run.
Another example is in the production of specialized coatings where the specific surface area of the zircon powder directly impacts the coating’s adhesion and durability. A supplier offering a range of SSA options allows the buyer to fine-tune their formulation for optimal performance. By following these guidelines, B2B buyers can make informed decisions that secure a stable supply of high-quality zircon powder, contributing to their operational success and competitive advantage.
Conclusion
Defining commercial-grade zircon powder quality is a multi-faceted process that goes beyond basic specifications. It involves a deep understanding of particle size, chemical purity, radioactivity, and physical properties. All of these directly impact performance in diverse industrial applications.
For B2B buyers, making informed procurement decisions means prioritizing suppliers who adhere to rigorous testing standards and provide transparent data. By aligning material properties with specific application needs, companies can secure consistent product quality, optimize manufacturing processes, and mitigate supply chain risks. This strategic approach to zircon powder procurement ensures operational excellence and a sustained competitive edge in the market.
FAQ Section
Q1: What is the most critical property for high-performance zircon powder?
For high-performance zircon powder, particle size distribution (PSD) is often considered the most critical property. It directly influences sintering behavior, final density, mechanical strength, and optical properties in many advanced applications.
Q2: How do impurities affect the color of zircon-based ceramics?
Impurities, particularly iron oxide (Fe2O3), are the primary cause of discoloration in zircon-based ceramics. Even trace amounts of Fe2O3 can lead to undesirable yellow, brown, or grayish tints, compromising the whiteness and brightness of the final product.
Q3: What is the typical shelf life of commercial-grade zircon powder?
The typical shelf life of commercial-grade zircon powder, when stored in dry conditions and sealed containers, is generally several years (e.g., 2-5 years). However, prolonged exposure to humidity can lead to agglomeration or contamination, affecting its performance.
Q4: Can zircon powder be recycled from industrial waste?
Yes, zircon powder can be recycled from certain industrial wastes, particularly from spent refractories or ceramic production scraps. Recycling processes involve crushing, grinding, and sometimes chemical treatment to recover usable zircon, contributing to circular economy initiatives.
Q5: What are the common packaging options for bulk zircon powder shipments?
Common packaging options for bulk zircon powder shipments include 25 kg multi-ply paper bags, 1-ton or 1.5-ton bulk bags (FIBCs – Flexible Intermediate Bulk Containers), and sometimes drums or specialized containers for very high-purity grades. The choice depends on quantity, transport method, and customer requirements.