Commercial-grade zircon powder is an essential raw material used extensively across various industries, including ceramics, refractories, electronics, and nuclear applications. The functionality and effectiveness of zircon powder in these fields heavily depend on its specific technical properties. This article explores the critical characteristics that define the quality of commercial-grade zircon powder, ensuring that B2B buyers can make informed choices when sourcing this versatile material. We delve into composition, particle size, surface area, purity levels, density, moisture content, phase composition, and the role of rigorous quality control in maintaining high standards.
The Foundations of Commercial Zircon Powder Quality
Commercial-grade zircon powder quality is not merely a single measurement; rather, it encompasses a variety of technical specifications. The quality assessment begins with the fundamental composition of zirconium silicate (ZrSiO₄), extending through a range of other factors that can influence performance across numerous applications.
Key Components of Zircon Powder Composition:
- Zirconium Dioxide (ZrO₂): Forms the bulk of the composition, impacting thermal and mechanical properties.
- Silicon Dioxide (SiO₂): Works in conjunction with ZrO₂, influencing sintering behavior and reactivity.
- Impurities: Trace elements such as iron (Fe), titanium (Ti), and aluminum (Al) that can affect quality.
Zirconium silicate, composed of zirconium dioxide (ZrO₂) and silicon dioxide (SiO₂), serves as the backbone of zircon powder. The intricacies of processing this mineral yield various grades, each suited for particular applications. A critical metric is the ratio of ZrO₂ to SiO₂. Typically, high-quality zircon contains approximately 65-67% ZrO₂ and 32-34% SiO₂. Deviations from these values can indicate the presence of impurities or incomplete processing, which may adversely affect performance in applications like glazes and precision casting.
Purity is another paramount factor in determining quality. Even minor impurities can dramatically alter the physical and chemical behavior of zircon powder. For example, the presence of iron oxides can lead to discoloration in ceramic materials, while the presence of titanium can affect thermal expansion properties. In sectors where the highest performance is demanded, such as in electronic components or high-end ceramics, high-purity zircon grades are essential.
Key Impurities Affecting Quality:
- Iron (Fe₂O₃): Can cause discoloration.
- Titanium (TiO₂): Affects thermal and electrical properties.
- Aluminum (Al₂O₃): Influences viscosity and casting quality.
Established industry standards and specifications play a significant role in defining zircon powder quality. Reputable organizations such as ASTM and ISO provide detailed guidelines, setting acceptable ranges for parameters spanning chemical composition, particle size, and bulk density. Adhering to these standards is integral to ensuring baseline quality and consistency in products across different industries.
Property | Standard Grade | High Purity Grade | Nuclear Grade |
---|---|---|---|
ZrO₂ Content (%) | 65-66 | 66-67 | >99.5 (post-processing) |
SiO₂ Content (%) | 32-33 | 33-34 | <0.5 (post-processing) |
Fe₂O₃ (max %) | 0.1 | 0.02 | <0.005 |
TiO₂ (max %) | 0.2 | 0.05 | <0.001 |
Al₂O₃ (max %) | 0.5 | 0.1 | <0.005 |
Quality can fluctuate significantly among suppliers, influenced by factors such as raw material sources, processing techniques, and quality control measures. Some manufacturers may specialize in high-purity grades by employing advanced processing technologies, while others may focus on producing cost-effective standard grades. Therefore, thorough supplier evaluation, alongside requests for detailed technical data sheets and third-party testing results, is necessary to ensure that you receive high-quality materials that meet your needs.
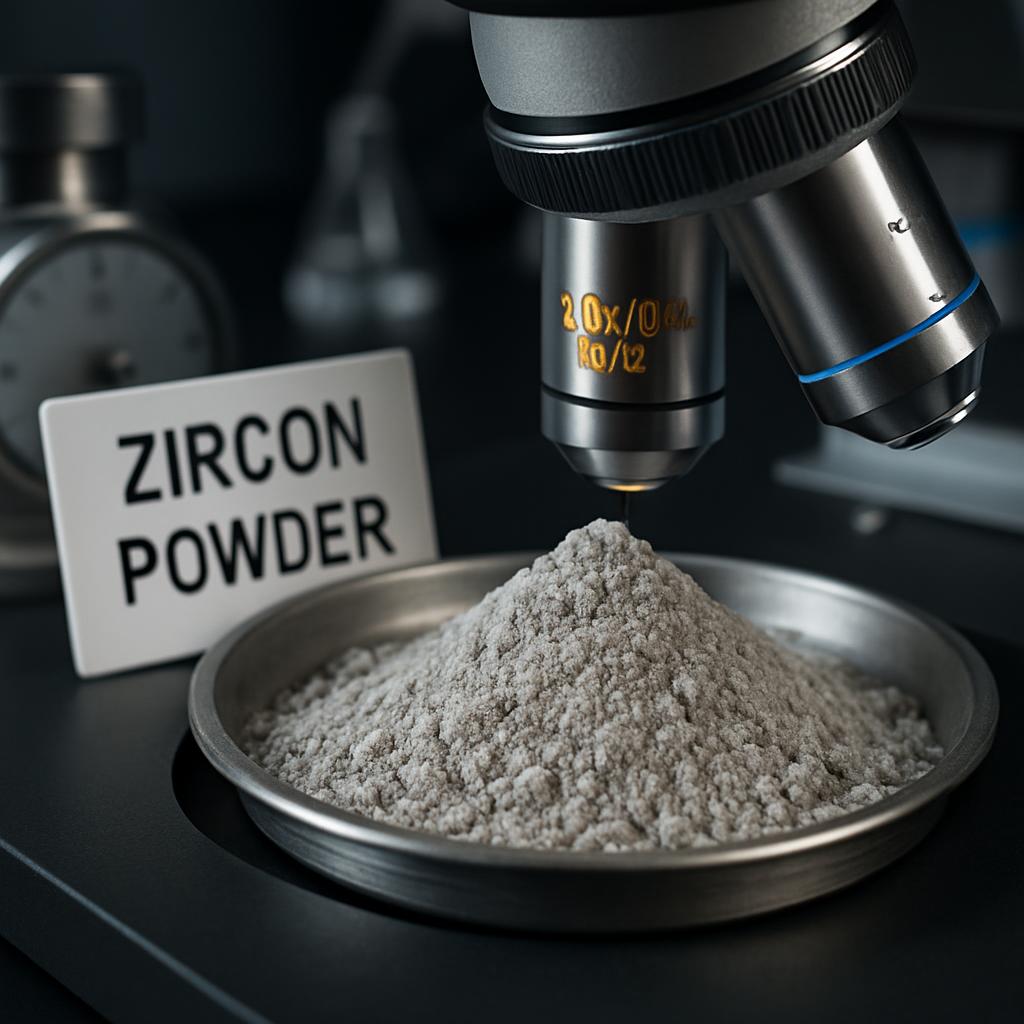
The Importance of Particle Size Distribution in Zircon Powder
Another essential aspect of zircon powder quality is the particle size distribution (PSD). This characteristic significantly impacts how the powder behaves during various processing stages and affects the properties of the final product. A well-defined particle size distribution is crucial for achieving stable suspensions and ensuring consistent mold filling. When particle size is too large, it can lead to settlement issues, causing uneven densities and defects in the final product.
Factors Influencing Particle Size Distribution:
- Processing methods: Milling and classification techniques can affect the final PSD.
- Feedstock quality: The quality of raw materials can influence particle size consistency.
- Environmental conditions: Humidity and temperature can affect particle aggregation.
Particle size is strongly linked to sintering—a process crucial for many zircon applications. Finer particles have a higher surface area-to-volume ratio, which facilitates faster sintering at lower temperatures, leading to denser final products. Conversely, coarser particles can cause defects like porosity and cracking during the sintering process.
Mean Particle Size (D50) denotes the median diameter of the particles within the distribution. Additionally, understanding D10 and D90 values offers a comprehensive view of the distribution breadth. A narrow span, defined as the difference between D90 and D10 divided by D50, signals a meticulously controlled distribution, which is highly desirable for ensuring consistent product quality.
Particle Size Metric | Description | Importance |
---|---|---|
D10 | 10% smaller than the median | Essential for understanding fine particle effects on viscosity |
D50 (Mean) | Median particle size | Indicative of the overall fineness of the powder |
D90 | 90% smaller than median | Highlights presence of coarse particles that may affect defects |
Span ((D90-D10)/D50) | Measures distribution breadth | A lower span indicates uniformity and predictability in processing |
Employing advanced characterization techniques such as laser diffraction guarantees accuracy in measuring particle size distribution. Regular analysis of this parameter ensures batch consistency and aids in troubleshooting processing challenges.
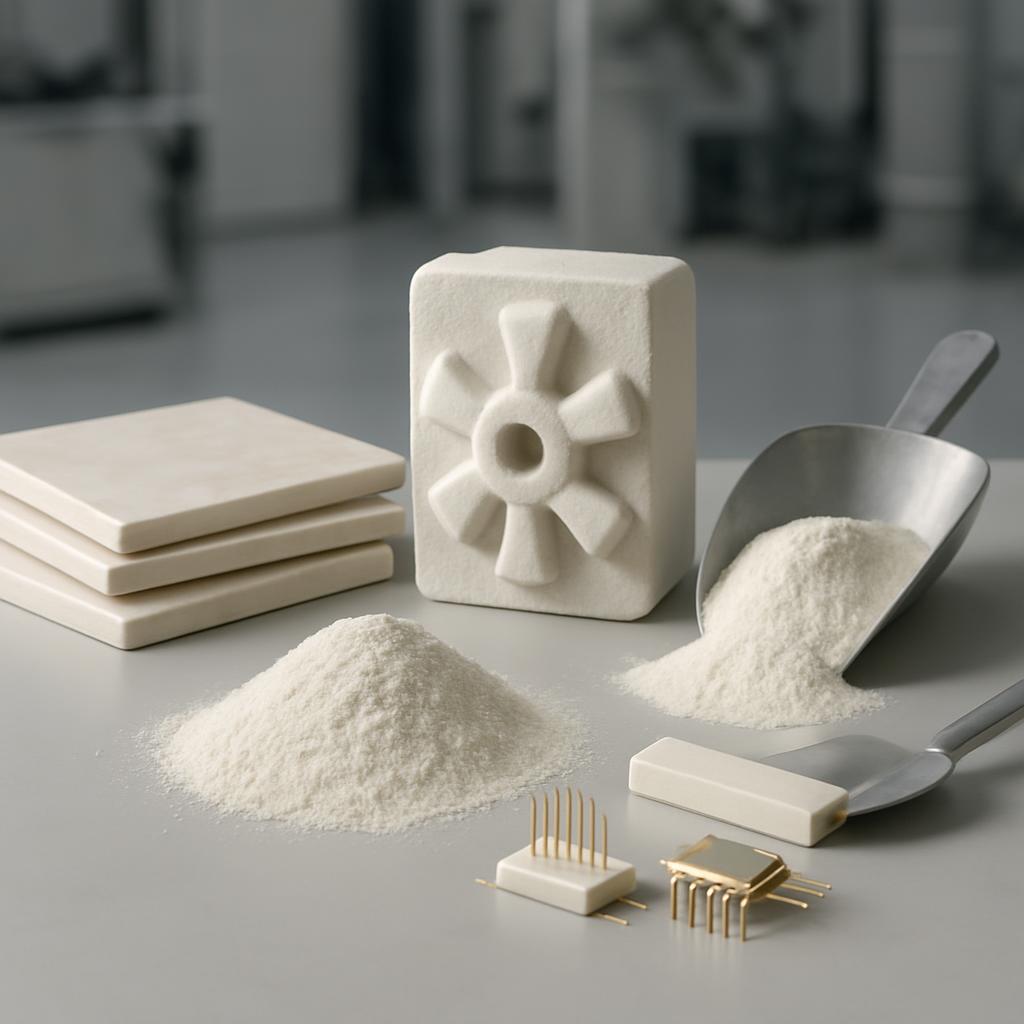
Specific Surface Area and Its Influence on Performance
Specific surface area (SSA) is another critical parameter in evaluating the quality of zircon powder. SSA affects various properties, including reactivity, sintering kinetics, and slurry behavior. Higher SSA correlates with increased reactivity, making the powder more amenable for chemical reactions, which is particularly relevant in advanced ceramic formulations.
Key Influences of Specific Surface Area:
- Reactivity: Higher SSA improves chemical interaction in formulations.
- Sintering kinetics: Finer particles densify at lower temperatures, enhancing mechanical properties.
- Slurry behavior: Increased SSA can lead to higher liquid absorption, affecting viscosity.
The impact of SSA on sintering kinetics cannot be overstated. Finer particles possess higher specific surface areas, allowing for densification to occur at lower temperatures. This feature is essential for improving mechanical properties and achieving tight tolerances in the final product. Moreover, SSA influences the behavior of slurries; powders with elevated SSA can absorb more liquid, which may alter viscosity and affect processing.
The most common method for measuring SSA involves the Brunauer-Emmett-Teller (BET) technique, which quantifies the surface area based on nitrogen adsorption. Optimizing the SSA for specific applications contributes directly to achieving desired material properties and application efficiencies.
Key Chemical Purity Requirements for Zircon Powder
Chemical purity remains a cornerstone in defining commercial-grade zircon powder quality. The level of purity directly impacts performance, color, and overall stability of the material. High ZrO₂ content generally indicates a purer form of zircon powder, which is critical in refractories and other high-performance applications.
Major Impurities to Monitor:
- Iron (Fe₂O₃): Can lead to aesthetic issues in ceramics.
- Titanium (TiO₂): Affects material characteristics like thermal expansion.
- Aluminum (Al₂O₃): Influences processing viscosity.
Contaminants and trace impurities, such as iron, titanium, and aluminum, present significant concerns for manufacturers. For instance, iron can lead to undesirable discoloration in ceramics, while titanium can influence the refractive index and thermal expansion characteristics of products. Therefore, monitoring and controlling the levels of these impurities is an essential aspect of maintaining high quality.
Impurity | Typical Max Limit (High Purity Grade) | Impact |
---|---|---|
Fe₂O₃ | 0.02% | Can cause discoloration and affect aesthetics |
TiO₂ | 0.05% | Affects thermal and refractive properties |
Al₂O₃ | 0.1% | Influences viscosity and processing behavior |
U/Th (Radioactivity) | <100 ppm | Compliance with safety regulations |
P₂O₅ | 0.01% | Can create low-melting phases affecting stability |
Analytical techniques such as X-ray fluorescence (XRF) and inductively coupled plasma (ICP) mass spectrometry are commonly employed to ensure regular chemical analysis of the zircon powder. Regular testing of key impurity levels helps in verifying quality compliance.
Bulk Density and Its Effects on Applications
Bulk density is a measurement that significantly influences the handling, storage, and overall processing of zircon powder. The apparent density reflects the loosely packed powder density, while tap density measures the density of the powder when it is subjected to tapping or compaction. The relationship between the two densities—the bulk density and the tap density—can provide critical insights into the flowability and compressibility of the powder.
Factors Influencing Bulk Density:
- Moisture content: Dampness can lower bulk density.
- Particle size: Finer particles may have different bulk properties.
- Processing method: Different processing conditions can yield varying bulk densities.
The bulk density directly affects material handling efficiency and also plays a crucial role in processes like dry pressing, which directly correlates to the final quality of the product. Variations in bulk density can lead to inconsistent compaction in forming processes, potentially resulting in variations in mechanical properties.
Density Metric | Description | Importance |
---|---|---|
Apparent Density | Density of loosely packed powder | Affects storage and logistics |
Tap Density | Density when powder is compacted | Important for compaction processes |
Hausner Ratio | Ratio of tap to apparent density | Indicates flowability of the powder |
Standard measurement methods, such as the ASTM D1895 or ISO 787-11, ensure accurate determination of bulk density. Regular assessment of this property is critical for predicting powder behavior during processing.
Moisture Content: A Critical Factor for Quality
Moisture content is an often-overlooked aspect that can dramatically impact the quality and performance of zircon powder. Even minimal moisture levels can cause agglomeration, leading to compromised flowability and creating problems like blockages in processing equipment.
Effects of Moisture on Zircon Powder:
- Agglomeration: Increased moisture can cause powder to clump.
- Reactivity: Excess moisture can alter chemical behavior.
- Defects in Finished Products: Poor moisture control can lead to cracks or weak points.
Moisture not only affects storage stability but also plays a significant role in chemical reactions that can occur during processing. Excessive moisture content can lead to defects during the drying or firing phases of production. Therefore, accurate moisture measurements are critical, typically carried out using methods such as loss on drying (LOD) or Karl Fischer titration.
Proper moisture control during storage and handling is vital; maintaining dry conditions can prevent moisture absorption, ensuring consistent quality from batch to batch.
The Role of Phase Composition in Zircon Powder Quality
The phase composition of zircon powder, particularly the crystalline forms of zirconia, can greatly influence its performance under high-temperature conditions. Zirconia predominantly exists in monoclinic and tetragonal phases, both of which exhibit different thermal shock resistance and mechanical properties.
Important Phase Characteristics:
- Monoclinic Zirconia: Stable at room temperature, lower strength at high temperatures.
- Tetragonal Zirconia: Higher stability at elevated temperatures, improves toughness.
- Stabilizers: Commonly added to zirconia to maintain desired phases during thermal cycling.
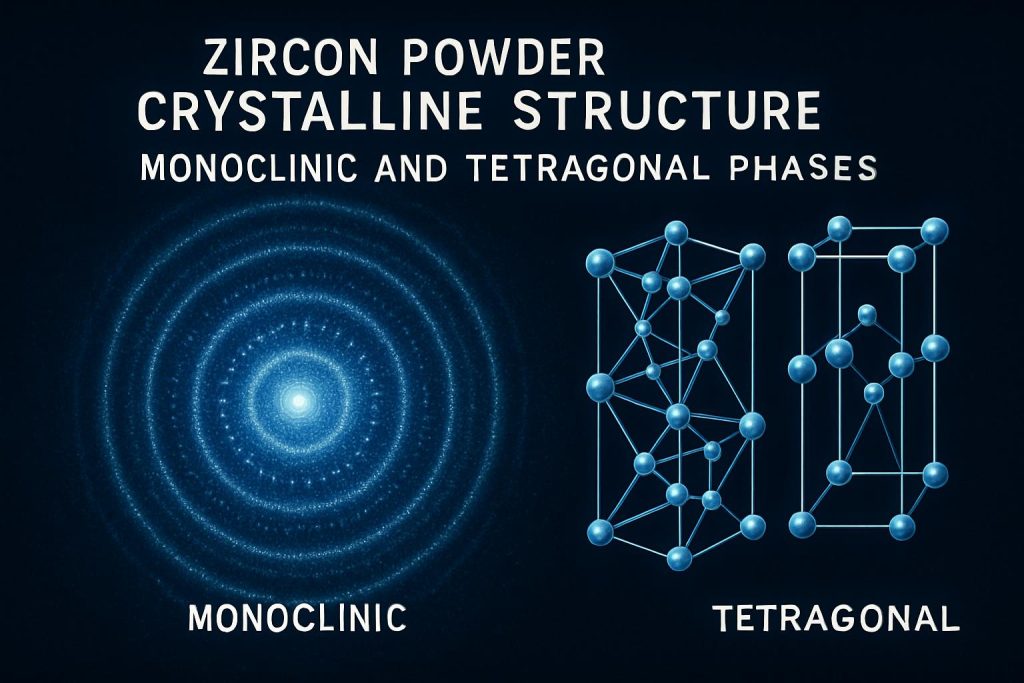
Additionally, stabilizers used in processing can significantly impact phase behavior. Stabilized zirconia can improve durability by preventing adverse volume changes occurring due to phase transformations during heating or cooling. This aspect is critical in industries where materials are subjected to extreme thermal environments.
Analyzing phase composition can be effectively achieved through techniques like X-ray diffraction (XRD), which provides valuable insights into the structural integrity of the zircon powder and can help predict performance characteristics under various conditions.ity of the zircon powder and can help predict performance characteristics under various conditions.
Quality Control and Testing of Zircon Powder
An effective quality control (QC) system is essential for ensuring consistency and reliability in the production of zircon powder. A stringent QC system must cover every stage, from raw material sourcing to final product packaging, tackling variability and ensuring adherence to specifications.
Key Quality Control Steps:
- Incoming Material Inspection: Ensure raw materials meet specified standards.
- In-Process Testing: Regular checks during production to monitor key parameters.
- Final Product Inspection: Comprehensive testing to verify compliance with specifications.
In-process testing and final inspections are crucial components of maintaining high standards. Suppliers often provide Certificates of Analysis (CoAs) to verify that materials meet specified requirements. Engaging independent third-party laboratories for testing can offer additional validation, ensuring trust and transparency in the quality of zircon powder.
Continuous improvement through feedback mechanisms plays an integral role in fostering supplier partnerships and enabling innovation in product development.
Conclusion
In conclusion, the quality of commercial-grade zircon powder is governed by a multifaceted array of technical properties that are crucial for its performance across various industrial applications. These properties include chemical composition, particle size distribution, specific surface area, purity levels, bulk density, moisture content, phase composition, and robust quality control mechanisms. Understanding the significance of each characteristic not only empowers B2B buyers to make informed purchasing decisions but also aids manufacturers in optimizing their processes to achieve superior product quality.
As industries increasingly demand higher performance materials, the need for high-purity and precisely characterized zircon powder will continue to rise. By adhering to established standards and conducting thorough quality assessments, companies can ensure the reliability and consistency of their products. This not only enhances their market competitiveness but also fosters innovation in applications ranging from ceramics and refractories to advanced electronics and nuclear technologies.
Ultimately, investing in quality zircon powder translates to improved outcomes in production efficiency, material properties, and product longevity. Therefore, stakeholders at every level—from raw material suppliers to end-users—must prioritize quality considerations in their procurement strategies to leverage the full potential of zircon in their respective fields.
FAQ Section
Q1: What are the primary differences between standard and high-purity zircon powder?
Standard grades typically contain higher levels of impurities, while high-purity grades are processed to minimize contaminants, making them essential for sensitive applications where performance and aesthetics are crucial.
Q2: How does particle size distribution affect zircon powder performance?
A controlled particle size distribution ensures stable slurry viscosity and predictable sintering behavior, which directly impacts final product density and mechanical strength. A narrow distribution is generally favorable for achieving consistent results.
Q3: Why is specific surface area important for zircon powder, and how is it measured?
Higher SSA indicates greater reactivity and is measured via the BET method. This property affects chemical interactions and the behavior of slurries, which are vital for processes where precise formulation is required.
Q4: What are the main concerns regarding radioactivity in zircon powder?
Trace elements such as uranium and thorium can pose regulatory compliance challenges. Monitoring and controlling radioactivity levels are necessary to ensure safety in applications, especially in nuclear and high-tech industries.
Q5: How do suppliers ensure commercial-grade zircon powder quality?
Suppliers implement robust QC systems featuring in-process testing, thorough inspections, and may provide CoAs. Engaging third-party verification and adhering to international standards are common practices to maintain high quality.