Precision casting demands materials that withstand extreme conditions while delivering exceptional surface finish and dimensional accuracy. Among various materials in this specialized field, zircon powder stands out with unique properties that make it indispensable for high-quality casting operations. This article explores the characteristics that enable zircon powder to excel in precision casting applications.
What Makes Zircon Powder Essential for Precision Casting?
Zircon powder (zirconium silicate, ZrSiO₄) possesses a crystalline structure providing exceptional stability under extreme conditions. This naturally occurring mineral contains approximately 67% zirconia (ZrO₂) and 33% silica (SiO₂) in a tetragonal crystal system, creating a material with remarkable thermal and chemical resistance. Zircon’s strong covalent bonds resist breakdown even at temperatures approaching 2,200°C, making it ideal for containing molten metals during casting.
The historical development of zircon in foundry applications dates back to the mid-20th century. By the 1970s, it had established itself as the premium material for precision casting, particularly in aerospace and medical applications. Today, global consumption of zircon in precision casting exceeds 380,000 tons annually, representing approximately 15% of total zircon production.
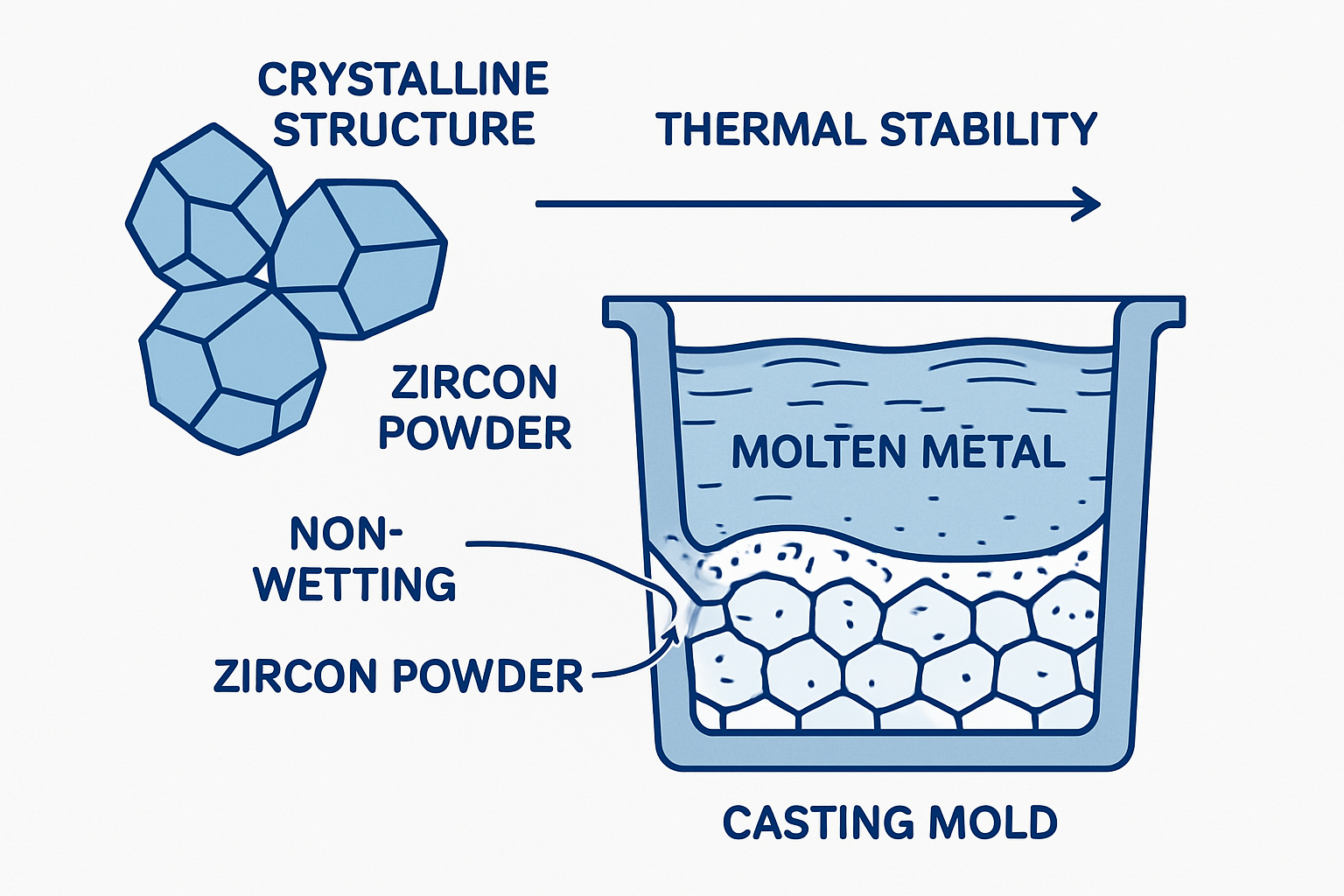
When compared to alternative materials such as silica, chromite, or olivine sands, zircon demonstrates superior performance across multiple parameters:
Property | Zircon | Silica | Chromite | Olivine |
---|---|---|---|---|
Melting Point (°C) | 2,200 | 1,710 | 2,150 | 1,890 |
Thermal Expansion (10⁻⁶/°C) | 4.5 | 15.0 | 7.6 | 10.2 |
Thermal Conductivity (W/m·K) | 5.1 | 1.7 | 12.5 | 3.2 |
Typical Cost ($/ton) | 1,800-2,200 | 120-180 | 380-450 | 220-280 |
While zircon’s initial cost is significantly higher than alternatives, foundries report 30-40% reductions in finishing operations, 15-25% lower rejection rates, and 40-60% longer mold life when using zircon-based systems for high-value components.
How Does Thermal Stability Impact Casting Quality?
The exceptional thermal stability of zircon powder plays a pivotal role in precision casting quality. With a melting point of approximately 2,200°C, zircon remains solid and stable even when exposed to molten superalloys, titanium, and high-temperature steels, preventing mold breakdown during pouring.
Zircon’s remarkably low coefficient of thermal expansion (4.5×10⁻⁶/°C—approximately one-third that of silica sand) minimizes dimensional changes during heating and cooling cycles. This exceptional stability enables the production of components with tolerances as tight as ±0.1mm even in complex geometries.
Thermal shock resistance represents another critical advantage. When molten metal at temperatures exceeding 1,500°C contacts the mold surface, zircon’s unique combination of thermal properties allows it to withstand these extreme temperature gradients without failure. Laboratory testing demonstrates that zircon can withstand over 30 thermal shock cycles from room temperature to 1,000°C without significant degradation, compared to 3-5 cycles for typical silica-based materials.
With a thermal conductivity of approximately 5.1 W/m·K, zircon offers moderate heat extraction that promotes directional solidification in complex castings. This controlled cooling prevents the formation of shrinkage porosity and hot tears, particularly in components with varying section thicknesses.
What Surface Properties Enhance Metal-Mold Interactions?
The non-wetting characteristics of zircon powder with molten metals represent one of its most valuable attributes. Unlike many refractory materials that can be partially wetted by molten alloys, zircon maintains a high contact angle (typically >120°) with most metals, preventing penetration into the mold surface. This property creates a clear boundary between mold and metal that translates to exceptional surface finish on the final casting.
When metal wets the mold surface, it can penetrate between sand grains, creating rough surfaces known as metal penetration defects. Zircon’s resistance to wetting reduces these defects by approximately 85% compared to silica-based systems—particularly valuable when casting reactive alloys such as titanium and aluminum.
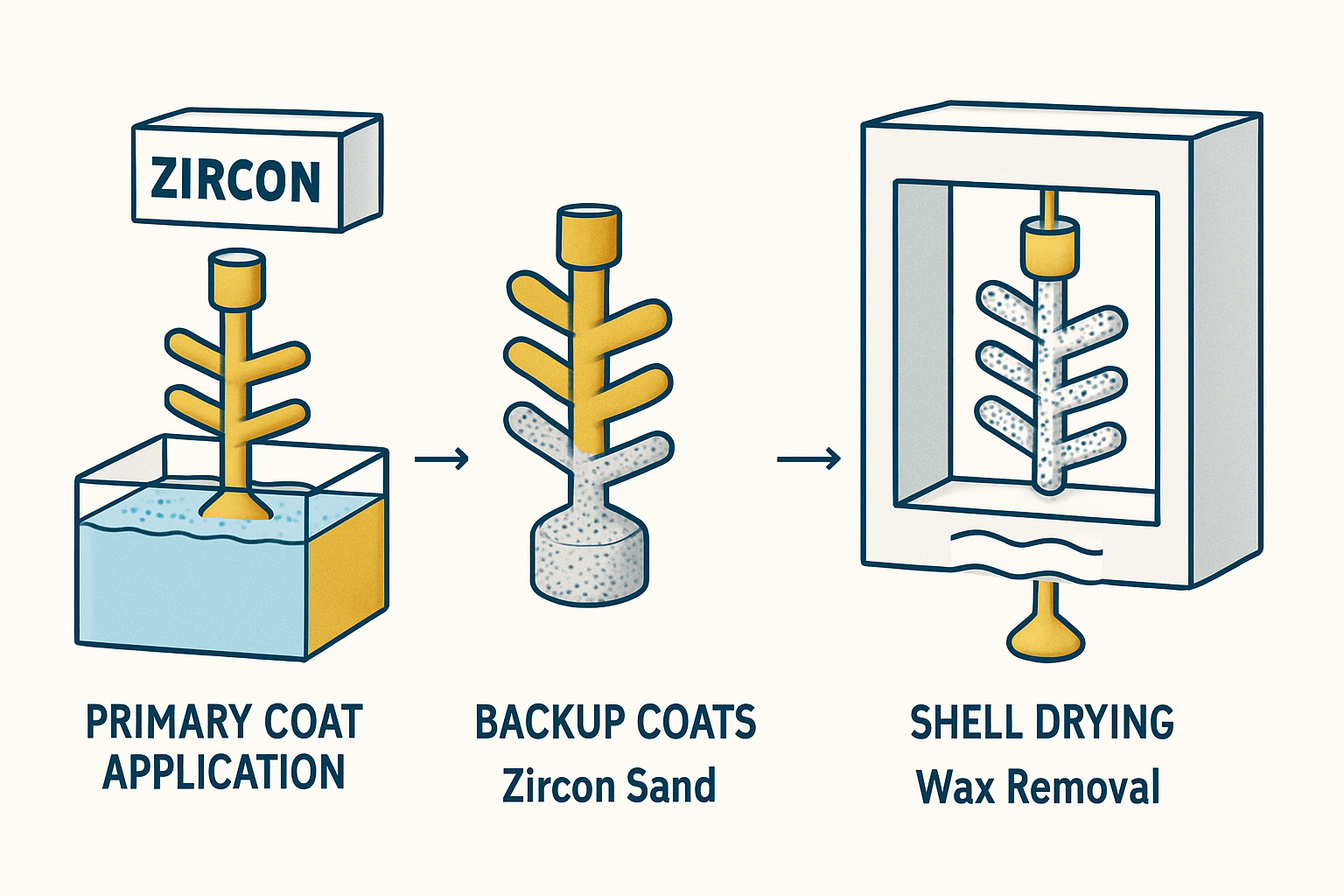
Grain morphology and particle size distribution significantly influence zircon’s performance in precision casting. Investment casting primary slurries typically utilize fine zircon flour with D50 (median particle size) of 10-15μm to capture intricate surface details, while backup coats employ coarser 80-120 mesh (125-177μm) material for strength and permeability.
Components cast using zircon-based molds typically achieve surface roughness values of Ra 1.6-3.2μm without additional finishing, compared to Ra 6.3-12.5μm for silica-based systems. This superior finish reduces or eliminates secondary operations such as grinding and polishing, providing significant cost savings while improving component performance.
Why Is Chemical Inertness Critical for Precision Results?
Zircon’s chemical inertness plays a crucial role in precision casting, particularly with reactive alloys. It demonstrates exceptional resistance to reaction with various alloy systems, including stainless steels, superalloys, and reactive metals like titanium and zirconium. This stability stems from zircon’s thermodynamically stable crystal structure and strong Si-O-Zr bonds that resist chemical attack even at elevated temperatures.
The pH stability of zircon in different binder systems provides versatility across various casting processes. Zircon remains stable in both acidic environments (pH 3-7) used in ethyl silicate binder systems and alkaline conditions (pH 9-11) common in colloidal silica investment casting shells. This broad pH tolerance allows foundries to select optimal binder chemistry without concerns about adverse reactions.
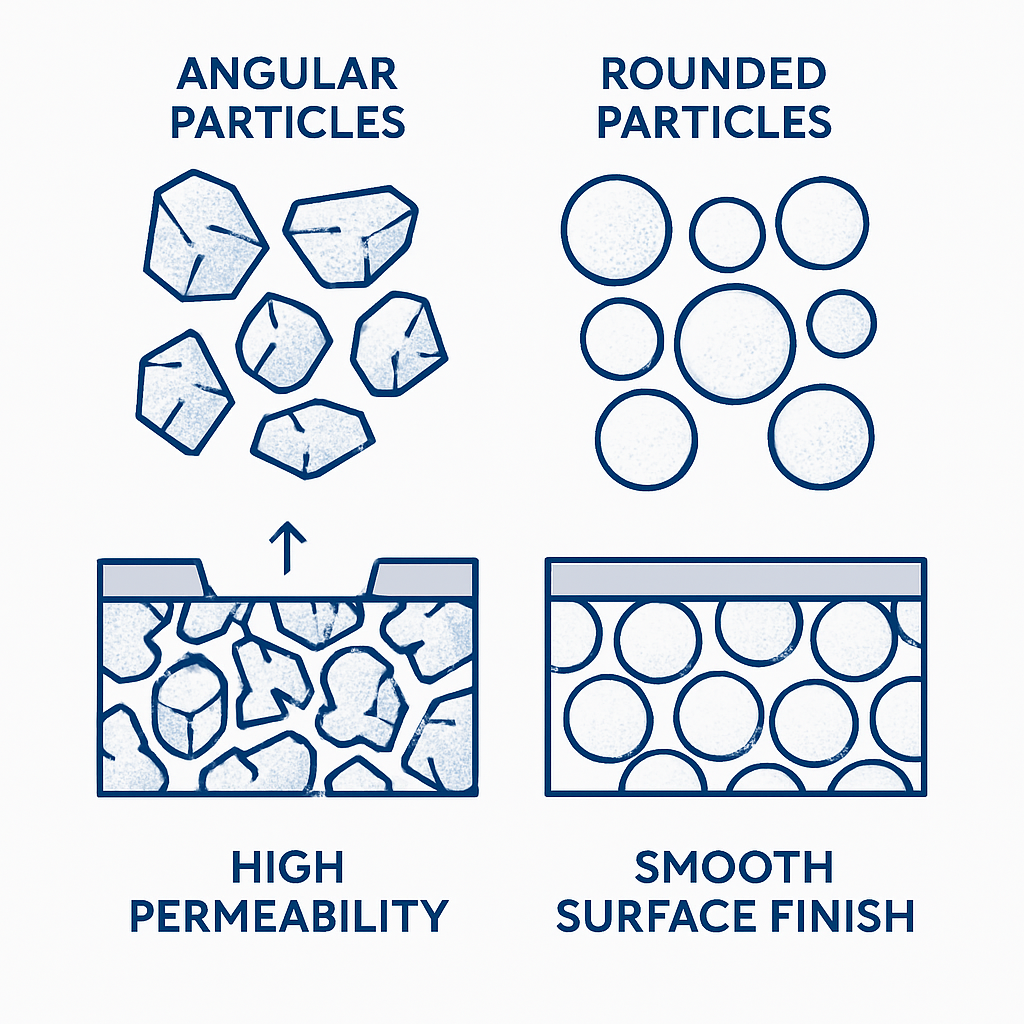
Minimal gas evolution during casting represents another significant advantage of zircon-based systems. Zircon’s thermal stability results in gas evolution rates approximately 85% lower than organic-bonded silica systems and 60% lower than phosphate-bonded alternatives. This reduced gas generation is particularly valuable when casting gas-sensitive alloys such as aluminum and magnesium.
When mold materials react with molten metal, they can introduce non-metallic inclusions that serve as stress concentration points and reduce mechanical properties. Zircon’s stability prevents such reactions, resulting in cleaner castings with superior mechanical performance. Metallurgical analysis of components cast in zircon molds typically shows inclusion content 65-75% lower than those produced in conventional sand systems.
How Are Zircon Coatings Applied in Sand Casting?
In sand casting applications, zircon is often applied as a coating or wash to conventional sand molds and cores. Water-based formulations typically contain 60-70% zircon flour suspended in colloidal silica or clay binders, while alcohol-based versions utilize isopropanol or ethanol carriers with resin binders for faster drying.
Application methods include dipping, spraying, and brushing, with most applications targeting 0.3-0.5mm dry film thickness. This thickness is achieved by controlling slurry viscosity (typically 18-22 seconds in a #4 Zahn cup) and application technique. Modern foundries employ ultrasonic thickness gauges to verify coating consistency before casting.
Zircon coatings provide a barrier between metal and sand, improving surface finish by 60-70% compared to uncoated molds. In chemically bonded sand systems (no-bake and cold box), zircon coatings can reduce cleaning operations by 40-50% while improving dimensional accuracy.
What Advancements Are Improving Zircon Performance?
Recent technological advancements continue to enhance zircon’s performance in precision casting:
- Advanced Beneficiation: Modern techniques incorporate flotation, magnetic separation, and chemical leaching to produce grades exceeding 66.5% ZrO₂ with controlled impurity profiles, delivering superior performance in reactive alloy casting.
- Surface Treatments: Silane coupling agents and specialized surfactants can modify zircon’s surface chemistry to improve binder interactions and reduce water demand in slurries, increasing green strength by 15-30% while reducing binder requirements by 10-15%.
- Nano-Zircon: Processing techniques including attrition milling and chemical precipitation can produce zircon particles in the 50-500nm range, enabling the casting of micro-featured components for medical devices and advanced electronics.
- Hybrid Systems: Strategic combinations such as zircon-alumina for improved hot strength, zircon-chromite for enhanced thermal conductivity, and zircon-mullite for thermal shock resistance allow foundries to optimize performance-to-cost ratios for specific applications.
- Recycling Technologies: Advanced thermal and mechanical processes can recover 70-80% of zircon from used investment casting shells and core materials, reducing virgin zircon consumption by 25-35% while maintaining quality standards.
Conclusion
Zircon powder’s exceptional performance in precision casting stems from a unique combination of properties that address the most critical challenges in the casting process. Its remarkable thermal stability, with high melting point and low thermal expansion, ensures dimensional accuracy and resistance to thermal shock. The non-wetting characteristics and chemical inertness provide superior surface finish and prevent defects, while its versatility across different particle sizes and morphologies allows optimization for specific applications.
Despite its premium cost compared to alternative materials, zircon delivers compelling economic benefits through reduced rejection rates, decreased finishing operations, and extended mold life. As manufacturing industries continue to demand higher precision components with complex geometries and tighter tolerances, zircon’s role in precision casting will likely expand further.
Ongoing technological advancements in beneficiation, surface treatments, and recycling are addressing sustainability concerns while enhancing performance. For foundries seeking to produce high-value, critical components where quality cannot be compromised, zircon powder remains the gold standard in precision casting materials, offering unmatched reliability and performance that justifies its premium position in the market.
FAQ Section
Q1: How does zircon powder compare to chromite sand for steel castings?
Zircon offers superior performance for steel castings compared to chromite in several key areas. While chromite provides good chilling properties with higher thermal conductivity, zircon excels in thermal stability with a higher melting point (2,200°C vs. 2,150°C) and significantly better resistance to thermal expansion (4.5×10⁻⁶/°C vs. 7.6×10⁻⁶/°C). This translates to superior dimensional stability and reduced veining defects. Zircon also demonstrates better chemical inertness with molten steel, resulting in cleaner casting surfaces.
Q2: What particle size distribution is optimal for investment casting primary slurries?
The optimal distribution for zircon flour in investment casting primary slurries typically centers around a -325 mesh (44μm) specification with D10 of 1-3μm, D50 of 10-15μm, and D90 of 30-40μm. This distribution provides the ideal balance between surface finish quality and slurry stability. Finer particles (below 5μm) constitute approximately 25-30% of the mix for excellent surface reproduction, while mid-range particles (5-20μm) at 40-45% ensure proper shell building and strength development.
Q3: Can zircon powder be effectively recycled from used casting shells?
Zircon powder can be effectively recycled from used casting shells through thermal reclamation at 800-900°C to remove organic binder residues and mechanical attrition to separate zircon from other refractory layers. The recovered material typically retains 85-90% of virgin zircon’s performance characteristics. Most foundries implement a blending strategy, incorporating 20-30% reclaimed material with virgin zircon to maintain quality standards while reducing material costs by 15-25%.
Q4: How does zircon powder affect the environmental footprint of casting operations?
Zircon powder impacts the environmental footprint in several ways. Positively, its exceptional properties extend mold life by 30-50% compared to alternatives, reducing overall material consumption. Its superior performance also decreases casting rejection rates by 15-25%, lowering energy and material waste. However, zircon mining and processing carry environmental considerations, including higher energy intensity than silica sand processing and naturally occurring radioactive materials (NORM) that require monitoring.
Q5: What binder systems are most compatible with zircon powder in precision casting?
For investment casting, colloidal silica binders (3-10% by weight) demonstrate optimal compatibility due to their similar pH stability range (9.5-10.5) and excellent particle wetting characteristics. For sand casting applications, phenolic urethane cold-box systems (1.0-1.4% binder level) offer excellent flowability while maintaining 85-95% of tensile strength achieved with silica sand. Notably incompatible systems include phosphate-bonded binders, which can react with trace impurities in lower-grade zircon.