High-temperature coatings are crucial in industrial applications demanding extreme heat, corrosion, and wear resistance. Zircon powder has emerged as a preferred choice for these challenging environments. This article explores why zircon powder outperforms other materials in high-temperature coating applications, detailing its unique properties, practical industrial uses, and optimization strategies. For companies aiming to enhance component durability and performance in extreme thermal conditions, understanding zircon powder’s advantages offers a path to improved efficiency and extended service life.
What Properties Make Zircon Powder Thermally Superior?
Zircon powder’s exceptional thermal properties distinguish it from competing materials in high-temperature coating applications. Its thermal superiority arises from a combination of physical and chemical characteristics, making it an ideal high-temperature coating material.
Zircon powder boasts a high melting point of approximately 2,550°C (4,622°F), significantly higher than many alternatives. This heat resistance allows zircon-based coatings to maintain structural integrity where other materials would fail. Compared to alumina (2,072°C) or magnesia (2,852°C), zircon offers an optimal balance of thermal stability and practical application properties.
The crystalline structure of zircon powder, a tetragonal crystal system, resists phase transformations during heating and cooling. This stability ensures coating longevity and consistent performance in fluctuating temperature environments.
Property | Zircon Powder | Alumina | Magnesia | Silicon Carbide |
---|---|---|---|---|
Melting Point (°C) | 2,550 | 2,072 | 2,852 | 2,730 |
Thermal Expansion Coefficient (10⁻⁶/K) | 4.5-5.0 | 8.0-8.5 | 13.5-14.0 | 4.0-4.5 |
Thermal Conductivity (W/m·K) | 2.0-2.5 | 30-35 | 38-42 | 120-170 |
Phase Stability | Excellent | Good | Moderate | Good |
Chemical Stability at High Temp | Excellent | Good | Moderate | Excellent |
Zircon powder’s low thermal expansion coefficient (4.5-5.0 × 10⁻⁶/K) minimizes thermal stress between the coating and substrate during temperature fluctuations. This reduces cracks, delamination, and coating failures.
Its relatively low thermal conductivity (2.0-2.5 W/m·K) makes zircon an excellent thermal barrier, protecting underlying substrates. As a coating, it creates an effective thermal shield, slowing heat transfer and safeguarding critical components.
Zircon’s phase stability under thermal cycling is a key attribute. Unlike some ceramics, zircon maintains its crystalline structure across a wide temperature range, preventing volume changes and microcracking that often lead to coating failure.
How Does Zircon Powder Enhance Coating Durability?
Zircon powder coatings exhibit exceptional durability due to synergistic physical and chemical properties. While thermal resistance is often highlighted, zircon’s durability advantages extend beyond temperature resistance.
Zircon powder offers remarkable wear resistance, with hardness typically 7.5 to 8.0 on the Mohs scale. This hardness, combined with excellent abrasion resistance, makes zircon coatings effective against particulate erosion, sliding wear, and abrasive media. The material’s natural hardness provides long-term protection without significant surface degradation.
Chemical stability is another cornerstone of zircon’s durability. It resists both acidic and alkaline environments, maintaining integrity even when exposed to corrosive substances at elevated temperatures. This inertness prevents reactions that could compromise coating integrity.
Durability Factor | Performance Rating | Key Benefit |
---|---|---|
Wear Resistance | Excellent | Maintains surface integrity in abrasive environments |
Chemical Stability | Very Good | Resists both acidic and alkaline corrosion |
Bond Strength | Good to Excellent | Creates strong mechanical and chemical bonds with substrates |
Thermal Shock Resistance | Good | Withstands rapid temperature changes without failure |
Coating Lifespan | 3-5× longer than conventional coatings | Reduces maintenance frequency and replacement costs |
The bonding mechanism between zircon coatings and substrates significantly contributes to durability. Zircon forms both mechanical and chemical bonds with properly prepared surfaces, enhancing adhesion.
Comparative lifespan data demonstrates zircon’s durability. In industrial applications, zircon-based coatings typically last 3-5 times longer than conventional ceramic coatings, reducing maintenance and production interruptions.
Zircon coatings maintain performance in extreme environments. Testing shows they retain over 90% of protective properties after extended exposure to temperatures above 1,200°C, unlike conventional coatings that degrade significantly.
This combination of wear resistance, chemical stability, strong bonding, and performance retention makes zircon powder ideal for applications where coating durability impacts operational efficiency and equipment longevity. These properties enable coatings to withstand harsh industrial environments while maintaining protective functions.
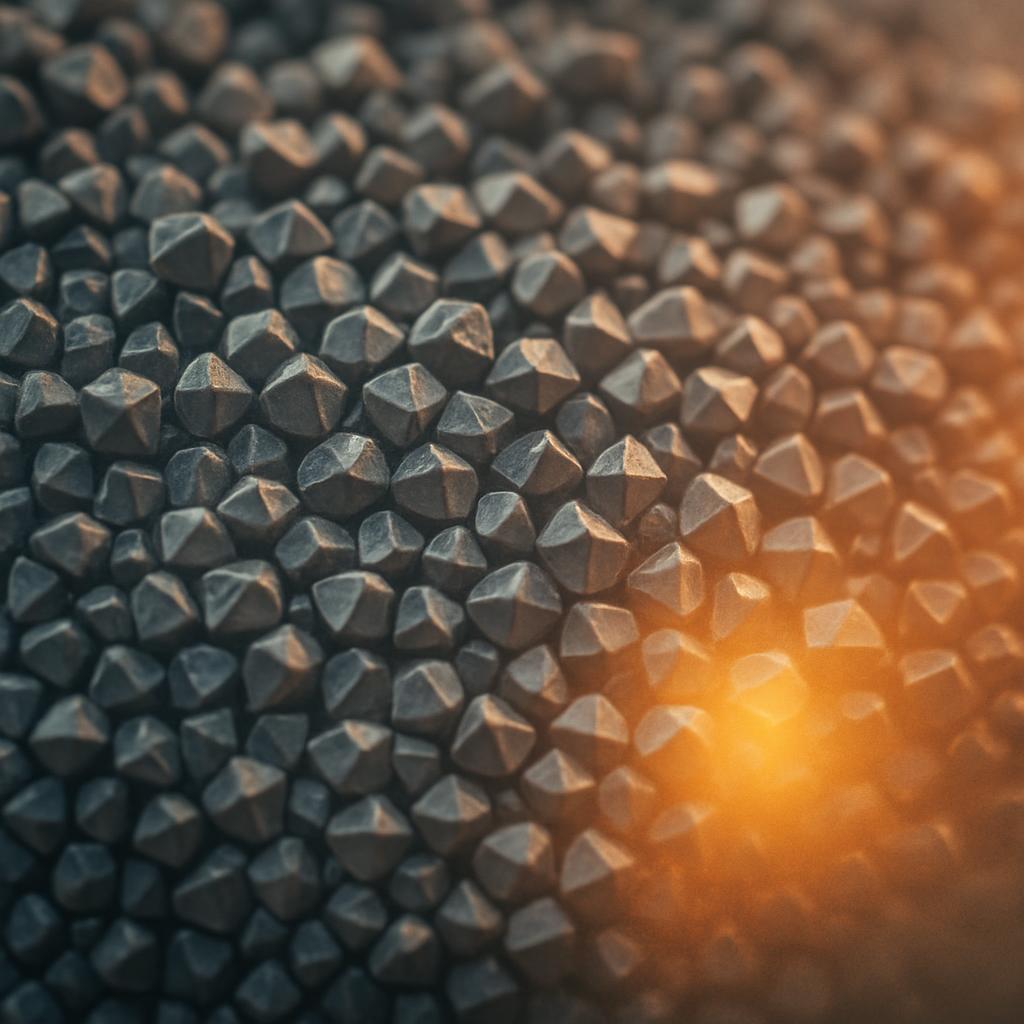
Which Industries Benefit Most From Zircon Coatings?
Zircon powder coatings are vital in industries requiring extreme temperature resistance and durability. Several sectors gain significant competitive advantages from these specialized coatings.
The aerospace industry is a primary beneficiary. Jet engine components like turbine blades and combustion chambers operate under extreme thermal conditions. Zircon-based thermal barrier coatings (TBCs) protect these critical parts, extending lifespan, improving fuel efficiency, and enhancing engine performance.
Energy generation, particularly gas turbines and power plants, is another major application. Combustion chambers and hot gas path components benefit from zircon’s thermal insulation and durability. Power plants report 2-4% efficiency improvements and up to 30% longer maintenance intervals, yielding significant operational and financial benefits.
Industry | Key Applications | Primary Benefits |
---|---|---|
Aerospace | Turbine blades, combustion chambers, exhaust systems | Extended component life, improved thermal efficiency |
Energy Generation | Gas turbine components, boiler tubes, heat exchangers | Increased efficiency, reduced maintenance |
Metallurgy | Furnace linings, ladles, tundishes, casting molds | Extended refractory life, improved metal quality |
Automotive | Exhaust components, turbochargers, engine parts | Enhanced durability, improved emissions control |
Petrochemical | Reactors, process vessels, catalyst supports | Corrosion resistance, extended equipment life |
The metallurgical industry extensively uses zircon coatings for molten metal contact. Furnace linings, ladles, and casting molds benefit from zircon’s high-temperature stability and resistance to molten metal attack. These coatings typically extend refractory life by 50-100% and improve metal quality.
Automotive applications have grown due to demand for higher-efficiency engines and stricter emissions. Exhaust system components, turbochargers, and catalytic converters coated with zircon-based materials show improved durability and performance under cyclic thermal conditions.
The petrochemical industry uses zircon coatings in reactors and process vessels where high temperatures and corrosive environments coexist. Zircon’s chemical stability resists attack from process chemicals and high-temperature reaction products, extending equipment life and reducing process stream contamination.
Across these industries, the common need is for materials that withstand extreme thermal conditions while maintaining structural integrity and performance. Zircon powder coatings meet these demands, extending component life, improving system efficiency, and reducing maintenance in challenging industrial environments.
What Are The Critical Processing Parameters?
Proper processing parameters are crucial for zircon powder coating performance. Understanding these factors helps optimize coating quality for specific applications.
Particle size distribution is highly influential. The optimal range is typically 1-45 μm, varying with application method. Finer particles (1-5 μm) yield denser, smoother coatings but require careful handling. Coarser particles (20-45 μm) allow faster deposition and thicker single-pass coatings but may increase porosity. High-performance applications often use a controlled distribution combining different size fractions for optimal density, adhesion, and efficiency.
Coating thickness must be carefully controlled. Most high-temperature zircon coatings are 150-500 μm. Too thin, they lack thermal protection; too thick, they risk delamination. Optimal thickness depends on operating temperature, thermal cycling, and mechanical stresses.
Processing Parameter | Optimal Range | Effect on Performance |
---|---|---|
Particle Size | 1-45 μm (application dependent) | Controls coating density, surface finish, and deposition rate |
Coating Thickness | 150-500 μm (application dependent) | Balances thermal protection with mechanical stability |
Spray Parameters | Velocity: 200-800 m/s Temperature: 2,500-3,000°C | Determines particle melting, splat formation, and coating adhesion |
Sintering Temperature | 1,100-1,400°C | Affects coating density, crystallinity, and bond strength |
Sintering Time | 1-4 hours | Influences microstructure development and phase stability |
Thermal spray parameters, such as particle velocity (200-800 m/s) and flame/plasma temperature (2,500-3,000°C), significantly impact coating quality. These must be optimized to partially melt particles without excessive decomposition. Spray distance (75-150 mm) balances particle heating and substrate heat transfer. These parameters interact and must be optimized together.
Sintering conditions are crucial for densification and bond formation. Optimal sintering temperatures (1,100-1,400°C) produce denser coatings. Sintering time (1-4 hours) ensures proper densification without excessive grain growth. Controlled heating and cooling rates prevent thermal shock damage.
Surface preparation fundamentally influences coating adhesion. Substrates need cleaning and roughening (e.g., grit blasting to 3-5 μm Ra) for mechanical bonding. Chemical pretreatments or bond coats can further enhance adhesion. Proper preparation can increase bond strength by 50-100%.
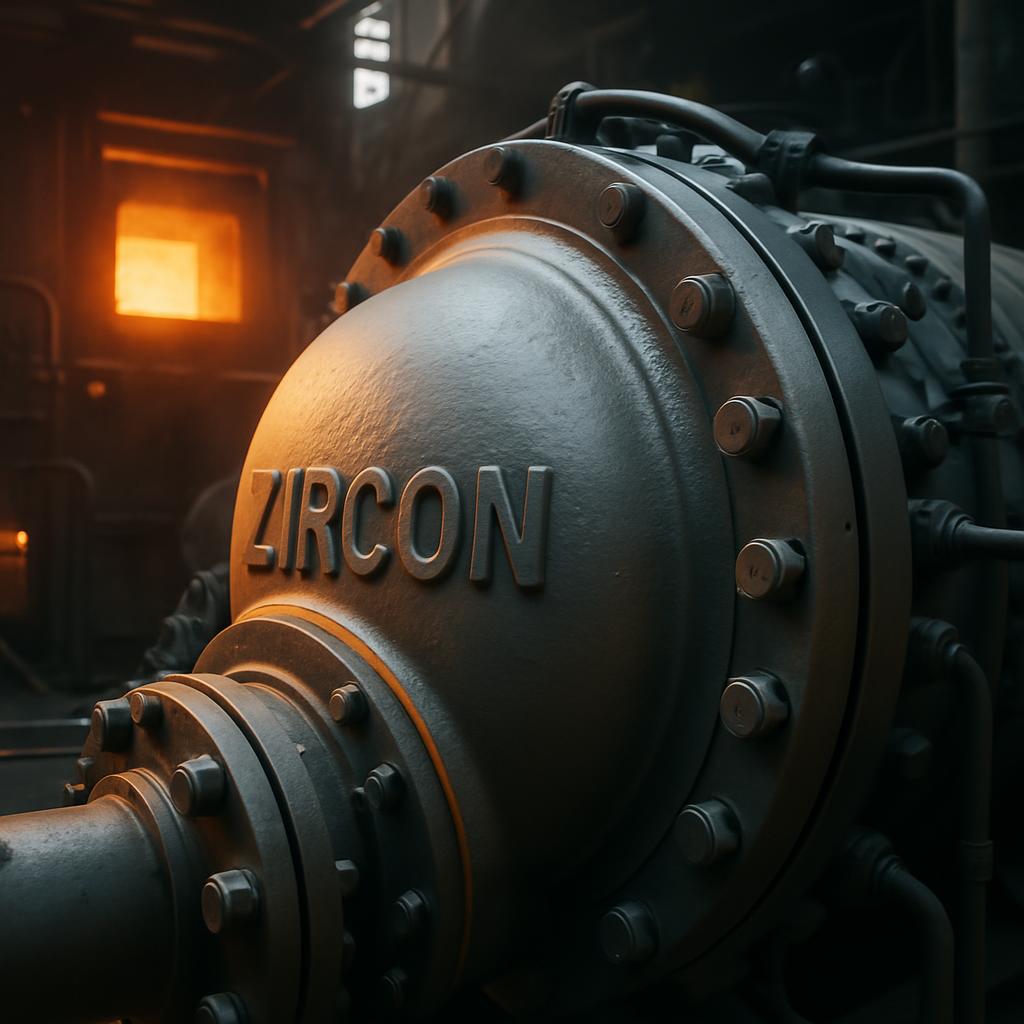
How Do Different Zircon Powder Grades Compare?
Zircon powders vary in performance for high-temperature coating applications. Specific grades offer distinct advantages for particular uses, making proper selection essential.
Standard industrial-grade zircon powder (65-66% ZrO₂, 32-33% SiO₂) offers good thermal resistance and durability at a reasonable cost. It suits general industrial applications where extreme purity isn’t critical, such as foundry coatings and general-purpose thermal barriers.
High-purity zircon powder (66-67% ZrO₂, 33-34% SiO₂, <0.5% impurities) provides superior performance. Reduced impurities lead to consistent thermal properties, better chemical resistance, and improved high-temperature stability. This grade is preferred for aerospace components, precision casting, and advanced TBCs.
Zircon Grade | ZrO₂ Content | SiO₂ Content | Total Impurities | Typical Applications | Relative Cost |
---|---|---|---|---|---|
Standard Industrial | 65-66% | 32-33% | 1-3% | General refractories, foundry coatings | 1× (baseline) |
High-Purity | 66-67% | 33-34% | <0.5% | Aerospace, precision casting, advanced TBCs | 1.5-2× |
Nano-Grade | 66-67% | 33-34% | <0.3% | Advanced electronics, specialized coatings | 3-5× |
Stabilized Zirconia | 90-95% ZrO₂ | N/A | Plus stabilizers (Y₂O₃, CaO, MgO) | High-end TBCs, oxygen sensors | 2-4× |
Composite Grades | Variable | Variable | Plus additives | Application-specific performance | 1.5-3× |
Nano-grade zircon powder (<100 nm particles) offers unique properties: enhanced sintering, improved coating density at lower temperatures, and ultra-thin, uniform coatings. It also shows superior thermal shock resistance. However, it comes with higher costs and more complex processing.
Stabilized zirconia grades (90-95% ZrO₂ with stabilizers) are an alternative for some high-temperature uses. They offer superior thermal insulation but generally less chemical resistance and may be more prone to sintering shrinkage.
Composite zircon grades incorporate additives (e.g., alumina for hardness, titania for thermal shock resistance) to enhance specific properties. These allow performance customization but are typically more expensive than standard grades.
Cost-benefit analysis is crucial. While high-purity and specialized grades are more expensive (1.5-5×), their performance often justifies the investment in critical applications. For example, high-purity zircon coatings can extend aerospace component service life by 30-50%, providing a compelling return.
What Are The Latest Advancements In Application Methods?
Application technology for zircon powder coatings continues to advance, expanding performance capabilities and making zircon coatings viable for new applications.
Thermal spray technology has seen significant improvements. Plasma spraying, enhanced with computer-controlled parameter adjustment, ensures consistent coating properties. High-velocity oxy-fuel (HVOF) spraying is preferred for many zircon applications, producing denser coatings with superior bond strength and wear resistance.
Plasma spraying typically results in 10-15% porosity, while HVOF achieves 2-5% porosity. This density difference improves wear resistance, reduces permeability, and enhances corrosion protection. HVOF zircon coatings typically have bond strengths of 60-80 MPa, compared to 30-50 MPa for plasma-sprayed alternatives.
Application Method | Typical Coating Density | Bond Strength | Thickness Range | Cost Factor | Best Applications |
---|---|---|---|---|---|
Plasma Spray | 85-90% | 30-50 MPa | 100-1,000 μm | 1× (baseline) | General thermal barriers, thick coatings |
HVOF | 95-98% | 60-80 MPa | 50-500 μm | 1.2-1.5× | Wear-resistant applications, dense barriers |
Sol-Gel | 90-95% | 40-60 MPa | 1-50 μm | 1.5-2× | Thin films, complex geometries |
PVD/CVD | 98-99% | 70-90 MPa | 1-20 μm | 2-3× | Precision components, thin high-performance coatings |
Cold Spray | 90-95% | 50-70 MPa | 50-2,000 μm | 1.3-1.8× | Thick coatings, temperature-sensitive substrates |
Sol-gel processing is important for specialized zircon coating applications. This wet-chemical technique produces thin (1-50 μm), highly uniform coatings on complex geometries. Lower processing temperatures make sol-gel suitable for temperature-sensitive substrates.
Physical vapor deposition (PVD) and chemical vapor deposition (CVD) are adapted for specialized zircon coatings. These methods produce exceptionally dense, thin coatings with excellent adhesion and high precision. They are valuable for precision components in electronics, optics, and aerospace.
Cold spray technology is promising for certain zircon coatings. This process uses kinetic energy, preventing thermal decomposition and minimizing residual stresses. It offers advantages for thick coatings on temperature-sensitive substrates and components requiring minimal distortion.
Emerging laser-based techniques combine thermal spray with precise energy delivery, allowing exceptional microstructural control and tailored properties. Though complex and costly, they point to future capabilities in customized zircon coatings.
How Can Performance Be Optimized In Extreme Conditions?
Optimizing zircon powder coatings for extreme conditions requires specialized approaches. Strategic modifications to composition, structure, and application techniques can dramatically extend performance limits.
For ultra-high temperatures (>1,500°C), rare earth oxides (3-5% yttria or ceria) enhance phase stability and reduce sintering. Nanostructured zircon coatings with engineered grain boundaries also accommodate thermal stresses, showing up to 40% improvement in thermal cycling life.
Thermal shock resistance is critical. Controlled porosity (10-15% by volume) in coating designs accommodates rapid temperature changes. Optimized pore structures, with fine, interconnected porosity, improve performance. Gradient structures, transitioning from dense to porous, distribute thermal stresses effectively.
Extreme Condition | Optimization Strategy | Performance Improvement | Implementation Complexity |
---|---|---|---|
Ultra-High Temperature (>1,500°C) | Rare earth oxide additions (3-5%) | 30-40% longer life at extreme temperatures | Moderate |
Thermal Shock | Engineered porosity (10-15%) | 2-3× improvement in thermal cycling resistance | Moderate to High |
Composite Structures | Layered or graded designs | Application-specific improvements of 25-100% | High |
Multi-Layer Systems | Bond coat + zircon + top seal | 3-5× improvement in overall system life | High |
Dopant Additions | Application-specific elements (0.5-3%) | 15-30% improvement in targeted properties | Moderate |
Composite coating structures enhance performance. Layered designs combine zircon with complementary materials for multiple requirements (e.g., wear-resistant outer layer over thermal barrier). Functionally graded coatings eliminate sharp interfaces, preventing failure under stress.
Multi-layer coating systems offer exceptional performance. A typical system includes a metallic bond coat, a primary zircon layer, and a thin top seal layer. These integrated systems extend coating life by 3-5 times in extreme environments.
Strategic dopant additions (0.5-3% titanium, aluminum, or magnesium) can enhance specific properties like thermal conductivity or hardness. These must be carefully controlled as they can affect multiple properties.
Application parameters are even more critical for extreme-condition coatings. Precise control of particle temperature and velocity during thermal spray ensures optimal bonding. Advanced monitoring systems provide real-time feedback for continuous adjustment, especially for multi-layer or graded structures.
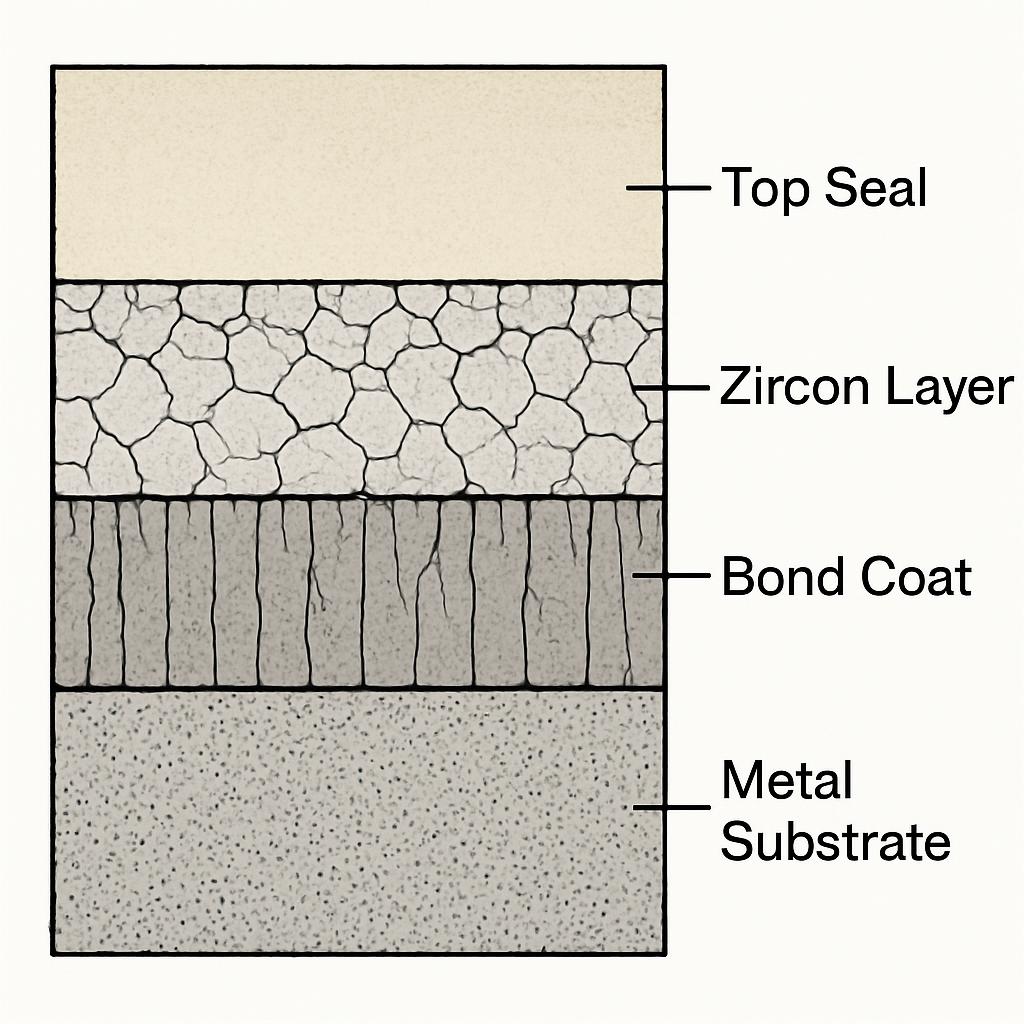
What Are The Cost-Benefit Considerations?
The economic case for zircon powder coatings relies on their value exceeding implementation costs. While initial costs may be higher, total lifecycle economics often favor zircon-based solutions.
Initial investment is typically 20-40% higher than conventional ceramic coatings due to material and application costs. For a typical industrial component, the coating process might be 5-15% of the total cost, with zircon coatings at the higher end.
Extended equipment life provides compelling economic benefits. Zircon coatings typically extend service life by 2-4 times, reducing replacement costs and minimizing costly downtime. For critical equipment in continuous process industries, this benefit alone often justifies the investment.
Economic Factor | Typical Impact | Calculation Approach |
---|---|---|
Initial Investment | 20-40% premium over conventional coatings | Direct material and application costs |
Equipment Life Extension | 2-4× longer component service life | Replacement cost × frequency reduction |
Energy Efficiency | 2-8% reduction in energy consumption | Energy cost × usage × efficiency improvement |
Maintenance Reduction | 30-50% longer intervals between service | Maintenance cost × frequency reduction |
Downtime Avoidance | 50-70% reduction in failure-related downtime | Hourly downtime cost × hours avoided |
Total Lifecycle Savings | Typically 3-5× return on initial premium | Sum of all benefits / additional initial cost |
Energy efficiency improvements are another significant benefit. Zircon coatings’ thermal barrier properties can reduce heat loss by 15-25%, leading to 2-8% energy savings. For energy-intensive processes, these savings accumulate rapidly. A medium-sized industrial furnace might realize annual energy cost savings of tens of thousands of dollars.
Reduced maintenance and downtime further enhance cost-effectiveness. Zircon coatings extend maintenance intervals by 30-50% and reduce failure-related downtime by 50-70%. This translates to substantial savings in labor, parts, and lost production. For example, a single avoided shutdown in a petrochemical plant can save hundreds of thousands of dollars.
The total lifecycle cost analysis consistently favors zircon coatings. Despite higher initial investment, the long-term savings from extended life, improved efficiency, and reduced maintenance typically yield a 3-5 times return on the initial premium. This makes zircon powder coatings a strategic investment for industries operating in high-temperature, demanding environments.
Conclusion
Zircon powder is the premier material for high-temperature coating applications due to its exceptional thermal stability, durability, and cost-effectiveness. Its unique properties create coatings that significantly outperform alternatives in demanding thermal environments. From aerospace to industrial furnaces, zircon coatings extend component life by 200-400%, reduce energy consumption by 2-8%, and minimize costly downtime.
For manufacturers seeking competitive advantage, zircon powder coatings offer a proven solution with quantifiable benefits. One aerospace manufacturer reported $1.2 million in annual savings from extended component life and reduced maintenance after implementing zircon-based thermal barrier coatings.
Contact Global Industry today to discuss how our premium zircon powder formulations and application expertise can address your specific high-temperature challenges. Our technical team provides comprehensive support, ensuring you achieve maximum performance and value from your coating investment.
Partner with us to transform your high-temperature components with coating solutions that deliver measurable improvements in durability, efficiency, and operational reliability—because in extreme environments, material choice makes all the difference.
FAQ
Q1: How does zircon powder compare to yttria-stabilized zirconia for thermal barrier coatings?
Zircon powder (ZrSiO₄) and yttria-stabilized zirconia (YSZ) serve different optimal applications. Zircon offers better chemical stability, especially in corrosive environments, and consistent properties across a wide temperature range. YSZ provides superior thermal insulation (30-40% lower thermal conductivity), making it preferable for pure thermal barrier applications. Zircon is typically 30-50% less expensive than YSZ and offers better erosion resistance. For applications needing both thermal protection and chemical/erosion resistance, zircon often balances properties and cost-effectiveness. YSZ remains superior for extreme thermal insulation.
Q2: What is the optimal particle size distribution for zircon powder in thermal spray applications?
Optimal particle size distribution for zircon powder in thermal spray depends on the method and desired coating. For atmospheric plasma spray (APS), 15-45 μm is typical (D10 ~10 μm, D90 ~50 μm). High-velocity oxy-fuel (HVOF) generally prefers finer distributions, 5-30 μm. A controlled distribution with minimal ultra-fine particles (<5 μm) improves flowability and reduces clogging. For optimal density and adhesion, a moderately tight distribution (span factor <1.5) is best. Testing with specific equipment is essential as optimal size varies.
Q3: How can delamination be prevented in zircon coatings during thermal cycling?
Preventing delamination in zircon coatings during thermal cycling requires addressing thermal expansion mismatch, coating structure, and application parameters. Use a compatible bond coat for a gradual transition. Engineer controlled porosity (10-15%) for strain tolerance. Optimize coating thickness (150-300 μm generally better). Apply segmentation techniques (fine vertical cracks) for strain relief. Use gradual heating/cooling to minimize thermal shock. Ensure thorough surface preparation (Ra 3-5 μm) for maximum mechanical bonding. These strategies can improve thermal cycling resistance by 300-500%.
Q4: What maintenance practices maximize the service life of zircon coatings?
Maximizing zircon coating service life involves systematic maintenance for early detection and prevention. Implement regular visual inspections (borescopes) to identify cracking, erosion, or delamination. Establish baseline thermal imaging and conduct periodic comparisons. Avoid rapid thermal cycling with controlled startup/shutdown. Clean coated surfaces to prevent contaminant accumulation. Promptly repair minor damage. Document performance to optimize maintenance intervals. These practices can help achieve 80-90% of theoretical maximum service life.
Q5: How do environmental regulations affect zircon powder coating processes?
Environmental regulations impact zircon powder coating processes in four areas: air emissions, waste management, worker safety, and material compliance. Thermal spray generates particulates requiring filtration (99%+ efficiency). Waste management classifies spent zircon based on composition. Worker safety mandates respiratory protection. Material compliance requires verifying zircon sources meet thresholds for uranium and thorium content. Compliance costs typically add 5-15% to overall coating costs but are essential for legal operation and environmental responsibility.