The global zircon powder market presents diverse opportunities for suppliers seeking strategic growth. With increasing demand across multiple industries and evolving technical requirements, identifying the most promising market segments has become crucial for sustainable business development. This article examines the key growth areas for zircon powder suppliers, analyzing current consumption patterns, emerging applications, and regional market dynamics to help suppliers optimize their market positioning and product development strategies.
Which Industries Currently Drive Zircon Powder Demand?
The zircon powder market continues to be shaped by several core industries that form its traditional demand base while new applications emerge.
But here’s what you need to know: The ceramics industry remains the dominant consumer of zircon materials, accounting for approximately 54% of global consumption. This sector utilizes zircon primarily as an opacifier and as a key component in glazes, frits, and specialized ceramic bodies. The demand from this sector shows steady growth of 3-4% annually, driven by construction activity and consumer product development.
Foundry and precision casting applications represent the second-largest consumption category at approximately 14% of the market. These applications value zircon’s high temperature resistance, low thermal expansion, and non-reactivity with molten metals.
Industry Sector | Global Consumption Share | Annual Growth Rate | Key Applications |
---|---|---|---|
Ceramics | 54% | 3-4% | Tiles, sanitaryware, tableware, technical ceramics |
Foundry/Casting | 14% | 2-3% | Investment casting, sand casting, refractory coatings |
Refractories | 13% | 1-2% | Glass furnace components, steel production linings |
Electronics | 8% | 7-8% | Capacitors, piezoelectrics, sensors, substrates |
Chemical/Catalysts | 6% | 5-6% | Catalysts, fuel cells, environmental applications |
Others | 5% | 4-5% | Medical devices, nuclear applications, coatings |
The refractory industry consumes approximately 13% of global zircon production, primarily for high-temperature applications in glass and steel manufacturing. This sector values zircon’s exceptional thermal stability and chemical inertness in aggressive environments.
Electronics and semiconductor applications, while currently representing only about 8% of consumption, show the strongest growth trajectory at 7-8% annually. This sector demands ultra-high purity grades and specialized particle characteristics for applications in capacitors, piezoelectric components, and advanced substrates.
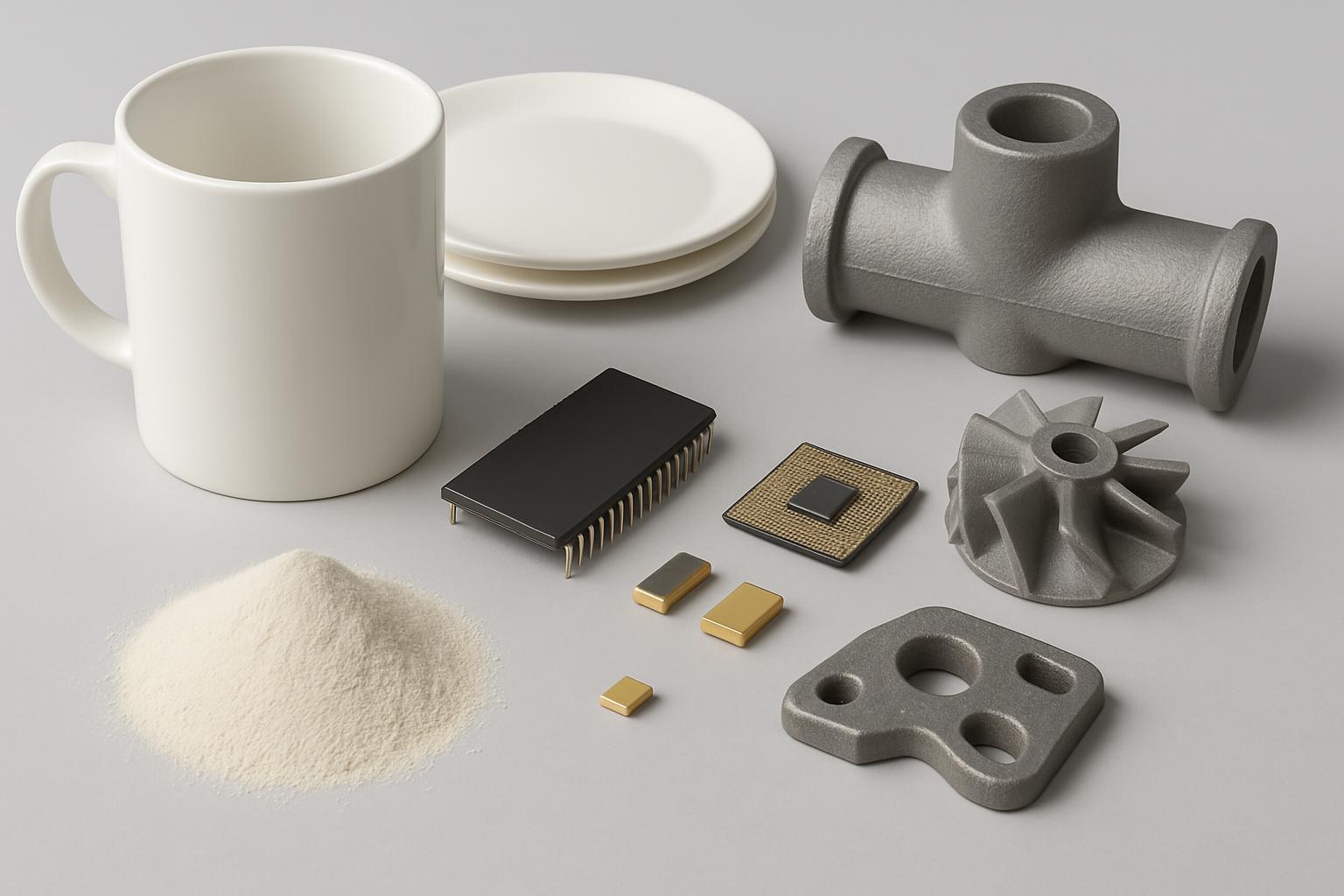
Why Is The High-Tech Ceramics Segment Expanding Rapidly?
The high-tech ceramics segment represents one of the most promising growth opportunities for zircon powder suppliers, with demand increasing significantly faster than traditional ceramic applications.
The data confirms this trend: Advanced ceramic applications are growing at 8-10% annually compared to 3-4% for traditional ceramics. This growth is driven by expanding applications in electronics, medical devices, and industrial components where performance requirements continue to increase.
Electronic devices represent a major growth driver, with zirconia ceramics used in components requiring exceptional mechanical properties, electrical insulation, and thermal stability. The miniaturization trend in electronics creates demand for increasingly precise ceramic components with tightly controlled specifications.
High-Tech Ceramic Application | Market Growth Rate | Zircon Grade Requirements | Key Performance Attributes |
---|---|---|---|
Electronic Components | 9-11% | Ultra-high purity (99.9%+) | Electrical insulation, thermal stability |
Medical Implants | 10-12% | Medical grade (low radioactivity) | Biocompatibility, mechanical strength |
Automotive Sensors | 8-10% | High purity (99.5%+) | Thermal shock resistance, dimensional stability |
Cutting Tools | 6-8% | Transformation-toughened | Wear resistance, fracture toughness |
Solid Oxide Fuel Cells | 15-18% | Yttria-stabilized | Ionic conductivity, thermal cycling resistance |
Medical and dental applications show particularly strong growth, with zirconia becoming the material of choice for implants, prosthetics, and specialized surgical tools. These applications demand medical-grade zircon with extremely low radioactivity levels and exceptional biocompatibility.
Here’s why this matters: The high-tech ceramics segment not only offers higher growth rates but also commands premium pricing. While standard ceramic-grade zircon typically sells for $1,200-1,500 per ton, specialized grades for advanced ceramics can command $3,000-5,000 per ton, with ultra-high purity electronic grades reaching $8,000-12,000 per ton.
How Is The Electronics Market Transforming Zircon Demand?
The electronics industry is rapidly emerging as a transformative force in the zircon powder market, creating demand for specialized grades with unique properties and processing requirements.
Consider these facts: Electronic applications currently account for approximately 8% of global zircon consumption but are growing at 7-8% annually—nearly twice the market average. This growth is driven by expanding applications in capacitors, piezoelectric components, sensors, and advanced substrates.
The most significant demand comes from multilayer ceramic capacitor (MLCC) manufacturers, who require zircon-derived materials with exceptional purity and precisely controlled particle characteristics. With the average smartphone containing 800-1,000 MLCCs and electric vehicles using up to 10,000, this application alone drives substantial growth.
Electronic Application | Purity Requirements | Particle Size Requirements | Key Contaminant Limits |
---|---|---|---|
Multilayer Ceramic Capacitors | 99.9%+ | 0.1-0.5 μm, narrow distribution | Fe < 50 ppm, Na < 20 ppm |
Piezoelectric Components | 99.95%+ | 0.2-0.8 μm, controlled morphology | Fe < 30 ppm, Al < 50 ppm |
Semiconductor Substrates | 99.99%+ | 0.5-2.0 μm, spherical particles | Total metals < 50 ppm |
Optical Components | 99.9%+ | 1.0-5.0 μm, uniform distribution | Fe < 20 ppm, Ti < 50 ppm |
Sensor Elements | 99.9%+ | Application-specific | Application-specific |
This creates a clear opportunity: Suppliers who can consistently deliver electronic-grade zircon with the required purity levels and particle characteristics can command premium prices and establish long-term supply relationships with major electronic component manufacturers.
The technical requirements for electronic applications differ significantly from traditional ceramic uses. While standard ceramic applications focus primarily on whiteness and opacity, electronic applications demand precise control of chemical composition, crystal structure, particle size distribution, and surface characteristics.
What Opportunities Exist In Emerging Green Technologies?
Emerging green technologies represent a rapidly expanding market segment for specialized zircon powder applications, driven by global sustainability initiatives and environmental regulations.
The potential is substantial: While currently accounting for only about 6% of global zircon consumption, green technology applications are growing at 12-15% annually—more than triple the overall market growth rate. This exceptional growth creates significant opportunities for suppliers who can develop specialized products for these applications.
Clean energy systems represent a major growth area, with zircon-derived materials playing critical roles in solid oxide fuel cells, hydrogen production systems, and advanced battery technologies. These applications leverage zirconia’s unique combination of ionic conductivity, thermal stability, and chemical resistance.
Green Technology Application | Annual Growth Rate | Zircon Material Form | Key Performance Requirements |
---|---|---|---|
Solid Oxide Fuel Cells | 15-18% | Yttria-stabilized zirconia | Ionic conductivity, thermal cycling resistance |
Environmental Catalysts | 10-12% | Surface-modified zirconia | Surface area, thermal stability, selectivity |
Water Purification | 12-14% | Functionalized zirconia | Adsorption capacity, regeneration capability |
Photocatalytic Materials | 14-16% | Doped zirconia | Band gap engineering, surface reactivity |
Sustainable Building Materials | 8-10% | Zircon-based additives | Thermal insulation, fire resistance |
What makes this particularly interesting: Green technology applications typically require specialized zircon derivatives rather than standard grades. This creates opportunities for suppliers to develop proprietary processing techniques and formulations that can command significant price premiums and create barriers to competition.
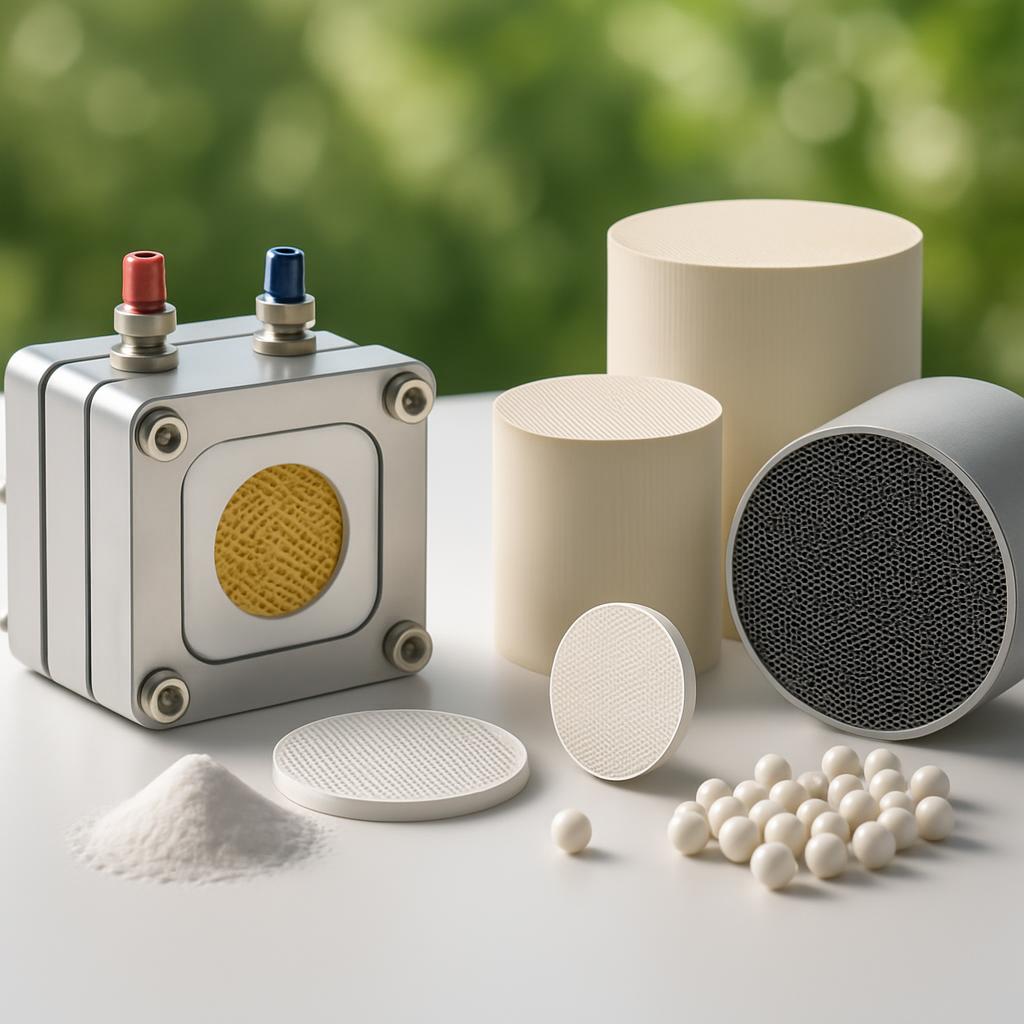
Which Geographic Markets Show Highest Growth Potential?
Regional market dynamics play a crucial role in identifying growth opportunities for zircon powder suppliers, with significant variations in consumption patterns, growth rates, and technical requirements across different geographic regions.
Here’s the regional breakdown: Asia-Pacific remains the dominant market region, accounting for approximately 65% of global zircon consumption. Within this region, China represents the largest single market at approximately 45% of global demand, driven primarily by its massive ceramic manufacturing base.
However, the most rapid growth is occurring in emerging Asian markets, particularly India, Vietnam, and Indonesia. These markets are expanding at 8-12% annually compared to 4-5% for China and 2-3% for developed markets in North America and Europe.
Region | Market Share | Annual Growth Rate | Primary Applications | Key Market Characteristics |
---|---|---|---|---|
China | 45% | 4-5% | Ceramics, Refractories | Volume-driven, increasing technical requirements |
Other Asia | 20% | 8-12% | Ceramics, Electronics | Rapid industrialization, growing high-tech sectors |
Europe | 15% | 2-3% | Technical Ceramics, Electronics | High-specification applications, sustainability focus |
North America | 12% | 2-3% | Electronics, Medical, Aerospace | High-value applications, technical performance focus |
Rest of World | 8% | 4-6% | Varied by country | Diverse requirements, often price-sensitive |
The strategic implication is clear: Suppliers should develop region-specific strategies that align with local market characteristics and requirements. For high-volume standard grades, establishing strong positions in Asian markets—particularly emerging economies—offers the greatest growth potential.
India deserves special attention as its consumption is growing at 10-12% annually, driven by rapid expansion in ceramic manufacturing and growing electronic component production. The country’s “Make in India” initiative is accelerating industrial development and creating new opportunities for material suppliers.
How Are Value-Added Processing Opportunities Evolving?
Value-added processing represents one of the most significant opportunities for zircon powder suppliers to increase margins, differentiate their offerings, and establish stronger customer relationships.
The economics are compelling: While standard zircon sand typically sells for $1,000-1,500 per ton, micronized zircon powder commands $1,800-2,500 per ton, and specialized grades for technical applications can reach $5,000-12,000 per ton. This value multiplication creates strong incentives for suppliers to move downstream in the processing chain.
Nano-scale zircon powder processing represents a particularly promising opportunity. Materials with particle sizes below 100 nanometers show unique properties and performance characteristics that enable new applications in catalysts, sensors, and advanced ceramics.
Processing Technology | Value Multiplication Factor | Technical Complexity | Key Applications | Investment Requirements |
---|---|---|---|---|
Micronization | 1.5-2.0x | Medium | Ceramics, Coatings | $2-5 million |
Chemical Processing | 2.0-3.0x | High | Electronics, Catalysts | $5-15 million |
Surface Modification | 2.5-4.0x | Medium-High | Composites, Catalysts | $3-8 million |
Nano-Processing | 4.0-8.0x | Very High | Advanced Electronics, Medical | $10-20 million |
Custom Formulation | 3.0-5.0x | Medium-High | Application-Specific | $4-10 million |
This creates a strategic decision point: Suppliers must evaluate whether to invest in developing their own value-added processing capabilities or partner with specialized processors. The decision depends on technical capabilities, capital resources, and market access considerations.
Custom formulations and blends represent another value-added opportunity. By developing application-specific formulations that combine zircon with complementary materials, suppliers can provide enhanced performance and simplified processing for customers.
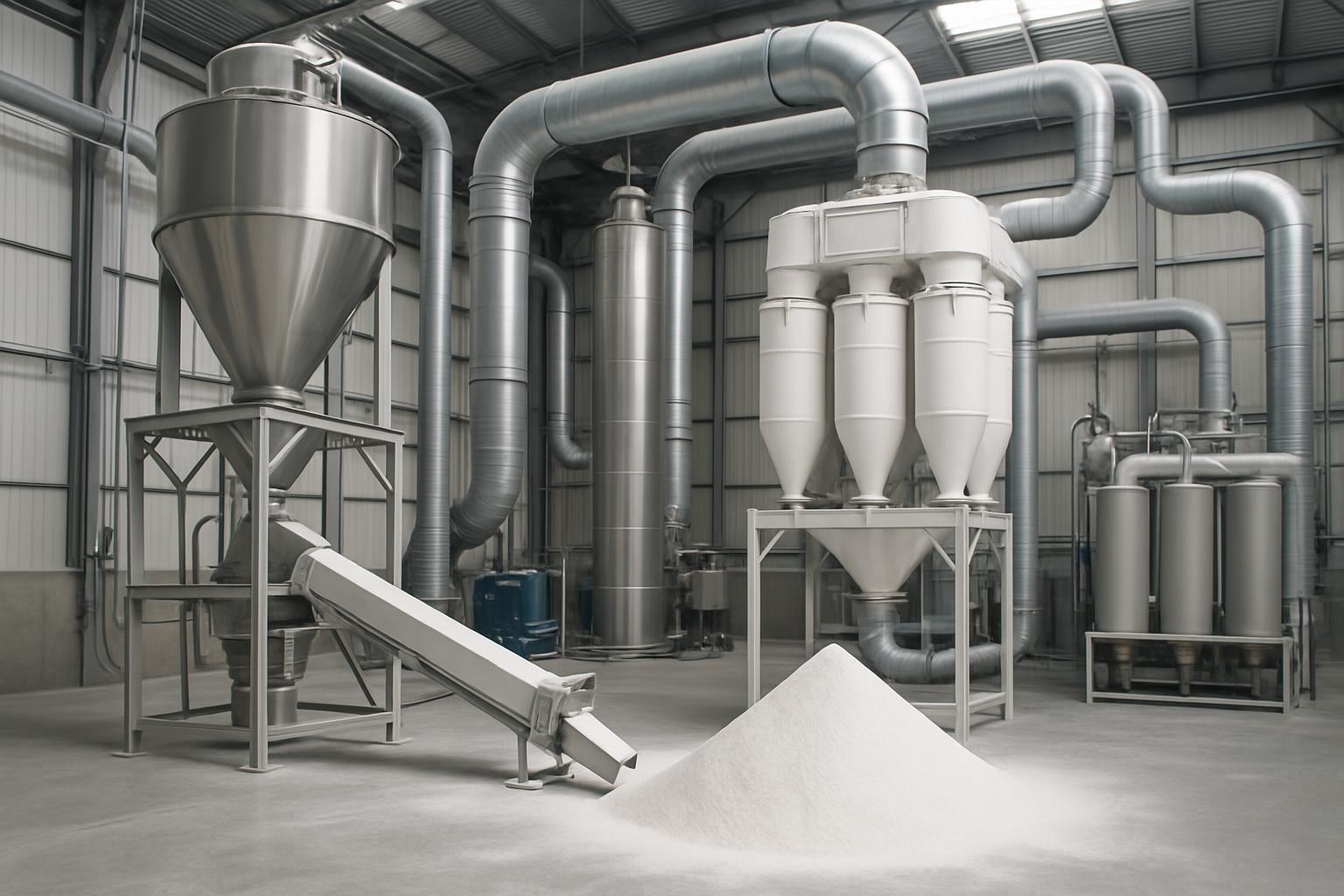
Conclusion
The global zircon powder market presents diverse growth opportunities for suppliers who can strategically target high-potential segments and adapt their offerings to evolving requirements. The most promising opportunities exist in high-tech ceramics, electronic applications, and emerging green technologies, where technical performance requirements and growth rates significantly exceed traditional applications. Regional strategies should recognize the continued dominance of Asian markets while addressing the specialized requirements of developed markets and the rapid growth in emerging economies.
Companies that invest in value-added processing capabilities can multiply product value by 2-8 times compared to standard grades, creating substantial margin improvement opportunities. Effective supply chain strategies and proactive approaches to sustainability requirements further enhance competitive positioning and market access.
Partner with Global Industry for comprehensive zircon solutions tailored to your specific application requirements. Our technical expertise, global supply network, and application development capabilities can help you optimize performance while managing total cost of ownership.
Contact our zircon specialists today to discuss how our market insights and material solutions can support your specific growth objectives in this dynamic market.
FAQ Section
Q1: What are the key differences between standard and premium zircon powder grades?
Standard and premium zircon powder grades differ in several critical aspects: chemical purity (premium grades typically contain 99.0-99.9% ZrSiO₄ compared to 96-98% for standard grades); particle size distribution (premium grades offer tighter control, typically ±5% vs. ±15-20% for standard grades); impurity levels (premium grades contain significantly lower levels of coloring oxides like Fe₂O₃ and TiO₂, typically <0.1% vs. 0.2-0.4% in standard grades); consistency (premium grades maintain stricter batch-to-batch consistency with comprehensive statistical process control); and traceability (premium grades typically offer complete documentation from raw material to finished product).
Q2: How can suppliers effectively balance inventory costs against supply security in volatile markets?
Suppliers can balance inventory costs against supply security through several strategic approaches: segmented inventory strategies (maintaining higher safety stocks for critical grades and customers while minimizing inventory for standard products); geographic diversification of both supply sources and inventory locations to mitigate regional disruption risks; risk-based pricing models that incorporate supply security costs into customer pricing structures; strategic partnerships with key customers involving shared forecasting, capacity commitments, and inventory management; and advanced analytics and digital tools to optimize inventory levels based on demand patterns, lead times, and risk factors.
Q3: What processing technologies offer the best return on investment for suppliers entering value-added markets?
The processing technologies offering the best return on investment depend on target market segments and existing capabilities, but several approaches stand out: micronization and classification systems typically provide the most accessible entry point with investment requirements of $2-5 million and payback periods of 2-3 years; chemical processing technologies (particularly those producing zirconium chemicals for electronic and catalyst applications) offer higher margins but require investments of $5-15 million with longer payback periods; and surface modification technologies present an attractive middle ground, requiring moderate investment ($3-8 million) while enabling access to specialized composite and catalyst markets.
Q4: How are customer technical support requirements evolving across different market segments?
Customer technical support requirements are evolving significantly across market segments: traditional ceramic customers increasingly seek assistance with formulation optimization and process efficiency rather than basic material selection; electronic component manufacturers require comprehensive technical data packages, often including statistical process control data and performance testing in specific applications; medical device manufacturers need regulatory compliance support and documentation in addition to technical performance data; and green technology companies frequently seek collaborative development partnerships rather than simple supplier relationships.
Q5: What sustainability metrics are most important to track and report for different customer segments?
The most important sustainability metrics vary significantly by customer segment: European customers typically prioritize comprehensive carbon footprint data (Scope 1, 2, and increasingly Scope 3 emissions), with many now requiring data at the product level rather than company level; North American customers focus heavily on responsible sourcing certification and compliance with specific frameworks like the Responsible Minerals Initiative; Japanese electronic manufacturers emphasize detailed data on specific contaminants and hazardous substances beyond regulatory requirements; and automotive industry customers require sustainability data formatted to industry-specific standards like the Automotive Industry Action Group protocols.