Zircon powder processing faces increasing pressure to adopt sustainable practices as environmental regulations tighten and corporate responsibility becomes a competitive advantage. Traditional zircon powder processing methods consume excessive energy, generate substantial waste, and create environmental compliance challenges that threaten long-term business viability. Modern green processing technologies offer proven solutions that reduce environmental impact by 40-60% while often decreasing operational costs through improved efficiency. This analysis examines eight key sustainable processing methods that enable zircon powder manufacturers to meet environmental goals, reduce regulatory risks, and achieve superior financial performance. Leading companies implementing comprehensive green zircon powder processing strategies report 25-35% cost reductions alongside dramatic environmental improvements.
What Environmental Challenges Drive Green Processing?
Traditional zircon powder processing creates multiple environmental challenges that modern manufacturers must address to remain competitive and compliant. The environmental stakes have never been higher. Energy consumption in conventional processing facilities typically ranges from 150-250 kWh per ton of finished product, with thermal processing accounting for 60-70% of total energy use. This high energy demand translates directly to carbon emissions, with traditional facilities generating 0.8-1.2 tons of CO₂ equivalent per ton of zircon powder produced.
Water usage presents another critical challenge, with conventional processing consuming 8-15 cubic meters of water per ton of product. Much of this water becomes contaminated with processing chemicals and suspended solids, requiring expensive treatment before discharge or creating disposal challenges. Regulatory agencies increasingly scrutinize water discharge quality, with many jurisdictions implementing zero liquid discharge requirements that make traditional processing approaches economically unfeasible.
Environmental Challenge | Traditional Impact | Regulatory Trend | Cost Implication |
---|---|---|---|
Carbon emissions | 0.8-1.2 tons CO₂/ton | Stricter limits | $25-100/ton CO₂ |
Water consumption | 8-15 m³/ton | Zero discharge | $5-15/m³ |
Waste generation | 2-4 tons/ton | Reduced limits | $50-200/ton |
Energy consumption | 150-250 kWh/ton | Efficiency mandates | $0.08-0.25/kWh |
Air emissions | Variable | Tighter controls | $10-50/ton |
Waste generation compounds environmental challenges through multiple streams including tailings, chemical waste, and packaging materials. Traditional processing typically generates 2-4 tons of waste per ton of finished product, with disposal costs ranging from $50-200 per ton depending on waste classification and local regulations. These costs add up quickly and impact profitability significantly.
Which Energy-Efficient Technologies Reduce Carbon Footprint?
Renewable energy integration represents the most impactful approach to reducing carbon footprint in zircon powder processing. Solar power installations are transforming facility energy profiles. Modern photovoltaic systems can provide 30-60% of facility energy needs, with payback periods of 4-7 years in most locations. Large processing facilities typically install 2-5 MW solar arrays that generate 3,000-7,500 MWh annually, reducing carbon emissions by 1,500-3,750 tons CO₂ equivalent per year.
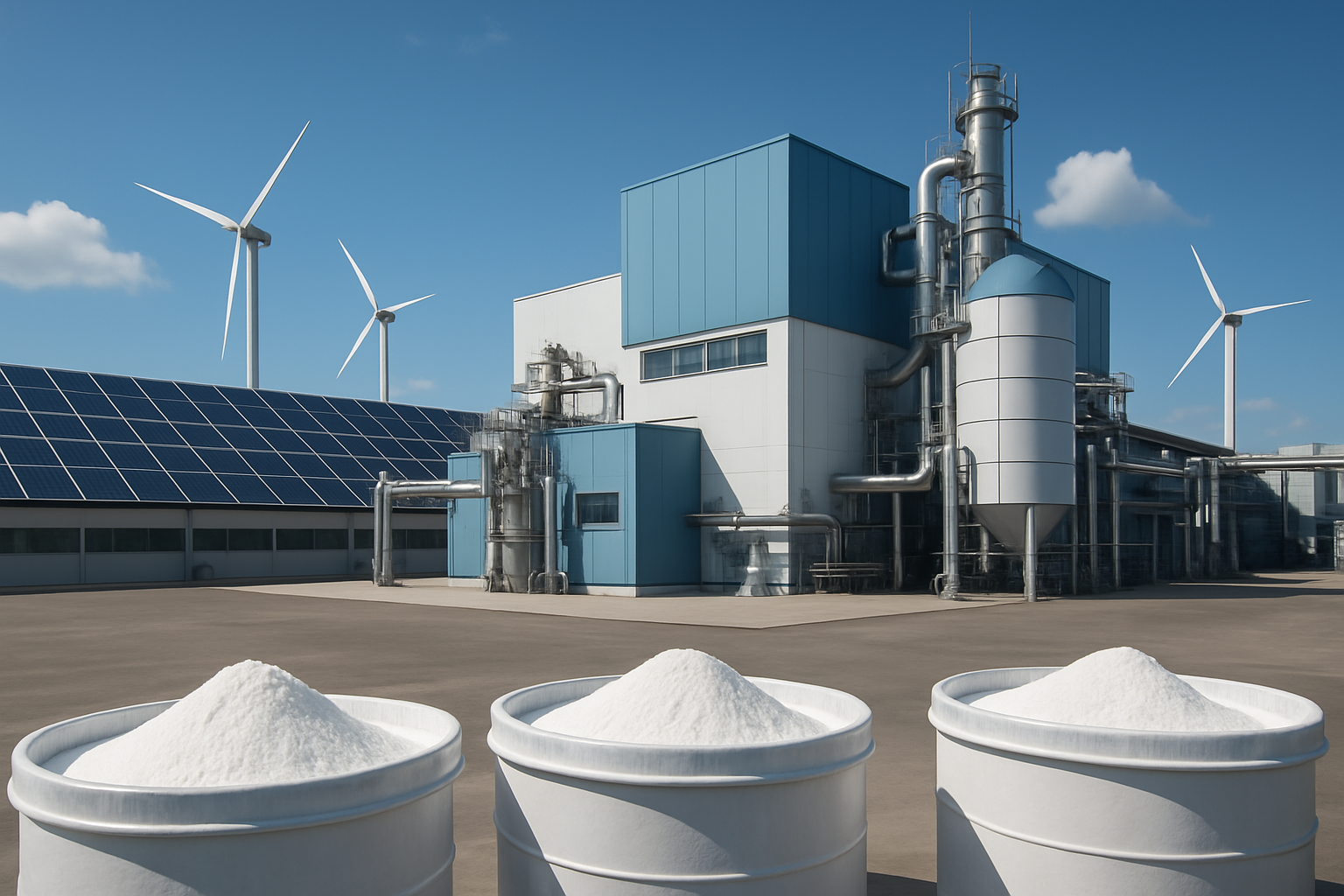
Wind energy applications prove particularly effective for facilities in suitable locations, with modern turbines generating power at costs below grid electricity in many regions. A single 2.5 MW wind turbine can provide 6,000-8,000 MWh annually, sufficient to power significant portions of processing operations. Combined solar and wind installations enable some facilities to achieve 70-90% renewable energy content.
Heat recovery systems capture waste thermal energy from calcination and drying operations, redirecting it to preheat incoming materials or generate steam for other processes. The energy savings are substantial and immediate. Advanced heat exchangers with effectiveness ratings above 85% can recover 40-60% of waste heat, reducing fuel consumption by 25-40%.
Energy Technology | Carbon Reduction | Cost Savings | Payback Period |
---|---|---|---|
Solar PV systems | 40-70% | 20-40% | 4-7 years |
Wind turbines | 50-80% | 25-45% | 5-8 years |
Heat recovery | 25-40% | 15-30% | 1.5-3 years |
Electric equipment | 80-95% | 10-25% | 3-6 years |
Energy storage | 10-20% | 5-15% | 6-10 years |
Electric processing equipment eliminates direct fossil fuel combustion while enabling integration with renewable energy sources. Electric kilns and furnaces offer precise temperature control and can achieve thermal efficiencies 15-25% higher than gas-fired equipment. When powered by renewable electricity, electric processing equipment can reduce carbon emissions by 80-95% compared to fossil fuel alternatives.
How Do Water Conservation Methods Minimize Waste?
Closed-loop water recycling systems eliminate liquid discharge while reducing fresh water consumption by 80-95%. Water recycling transforms operational economics. These systems incorporate multiple treatment stages including clarification, filtration, and chemical treatment to remove contaminants and enable water reuse throughout processing operations. Advanced membrane filtration systems can achieve water recovery rates above 95% while producing water quality suitable for most processing applications.
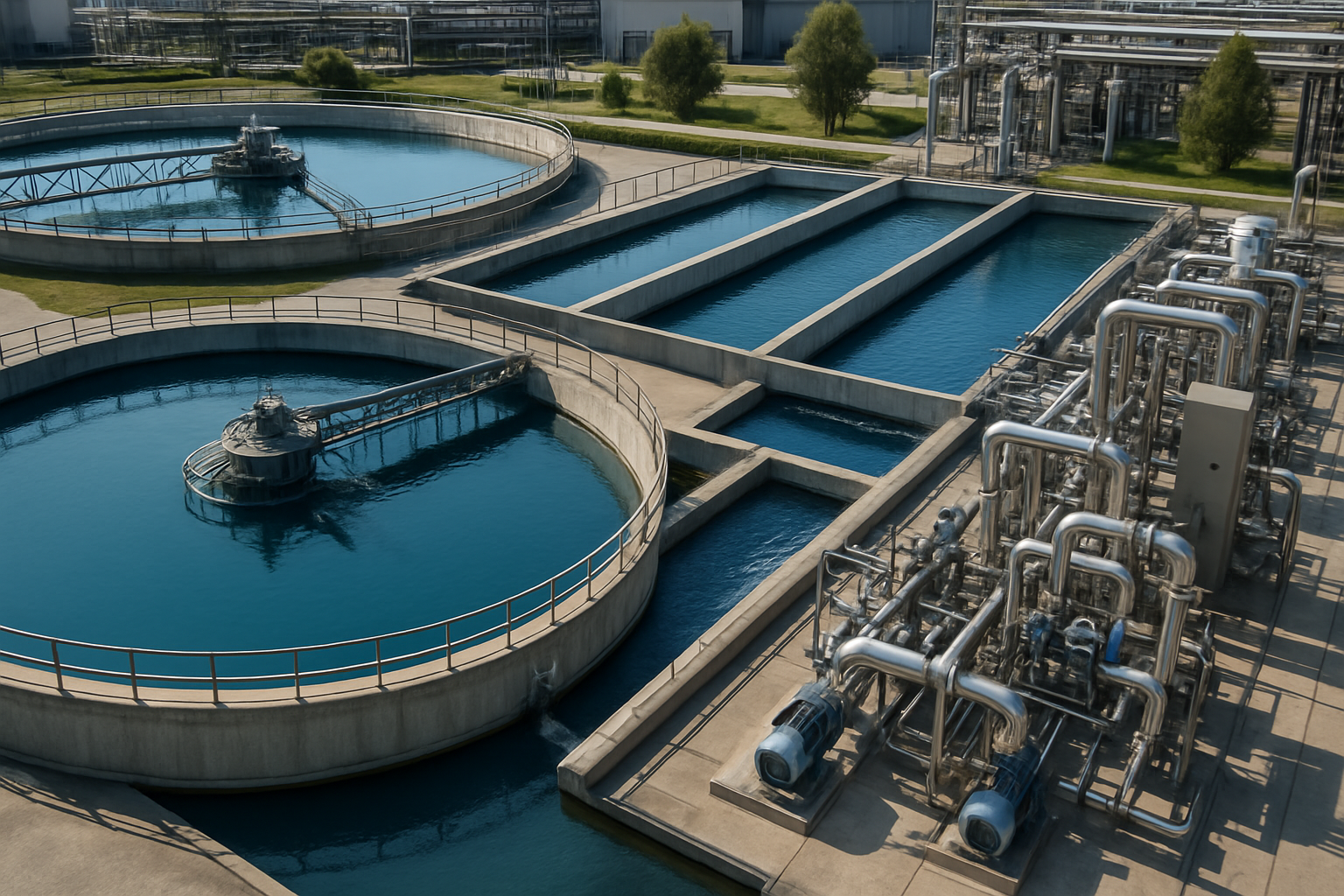
Zero liquid discharge processing approaches represent the ultimate in water conservation, eliminating all liquid waste streams through advanced treatment and recovery technologies. These systems combine reverse osmosis, evaporation, and crystallization to recover all water for reuse while producing solid waste streams that can often be recycled or safely disposed.
Rainwater harvesting systems capture precipitation for use in processing operations, reducing dependence on municipal or groundwater sources. Every drop counts in sustainable operations. Properly designed rainwater collection systems can provide 20-40% of facility water needs in moderate rainfall regions.
Water Technology | Water Savings | Cost Reduction | Implementation Cost |
---|---|---|---|
Closed-loop recycling | 80-95% | 60-80% | $2-8M |
Zero liquid discharge | 100% | 70-90% | $5-15M |
Rainwater harvesting | 20-40% | 15-30% | $200K-1M |
Advanced filtration | 60-85% | 40-60% | $1-5M |
Smart monitoring | 10-25% | 10-20% | $100K-500K |
Smart water monitoring systems use IoT sensors and analytics to optimize water use and detect leaks or inefficiencies in real-time. These systems can identify water waste sources, optimize recycling system performance, and predict maintenance needs before problems occur. Facilities typically achieve 10-25% additional water savings through improved monitoring and control.
What Waste Reduction Strategies Improve Sustainability?
Circular economy principles transform waste streams into valuable resources through systematic identification and utilization of byproducts. Waste becomes a resource in circular processing. Modern zircon powder processing facilities can achieve 60-80% waste reduction by implementing comprehensive byproduct recovery programs. Tailings materials often contain valuable minerals that can be recovered through additional processing.
Byproduct utilization strategies focus on finding commercial applications for materials that would otherwise require disposal. Zircon powder processing generates several byproduct streams including ilmenite, rutile, and garnet that have commercial value in other industries. Establishing markets for these materials can generate $50-200 per ton in additional revenue while eliminating disposal costs.
Waste Strategy | Waste Reduction | Cost Savings | Revenue Potential |
---|---|---|---|
Byproduct recovery | 40-70% | $100-300/ton | $50-200/ton |
Tailings utilization | 60-90% | $150-400/ton | $20-100/ton |
Chemical optimization | 20-40% | $50-150/ton | N/A |
Packaging reduction | 30-60% | $25-75/ton | N/A |
Equipment lifecycle | 15-30% | $10-50/ton | N/A |
Chemical waste reduction focuses on process optimization and chemical substitution to minimize hazardous waste generation. Advanced process control can reduce chemical consumption by 20-40% while maintaining product quality. Biodegradable chemical alternatives eliminate hazardous waste classification for many process streams.
Which Bio-Based Processing Innovations Show Promise?
Biotechnology applications in mineral separation offer environmentally friendly alternatives to traditional chemical processes. Biological processes are revolutionizing mineral processing. Bioflotation techniques use naturally occurring or engineered microorganisms to selectively attach to specific minerals, enabling separation without synthetic chemicals.
Enzyme-assisted processing techniques use specific enzymes to modify mineral surfaces or break down unwanted materials. Enzymes offer high specificity and operate under mild conditions, reducing energy requirements and eliminating harsh chemicals. Some enzyme processes can operate at ambient temperature and neutral pH.
Bio-Technology | Environmental Benefit | Performance | Development Stage |
---|---|---|---|
Bioflotation | 90% chemical reduction | Comparable | Commercial |
Enzyme processing | 60% energy reduction | Superior | Pilot scale |
Microbial separation | 95% waste reduction | Enhanced | Research |
Bio-reagents | 80% toxicity reduction | Equivalent | Commercial |
Biohydrometallurgy | 70% emission reduction | Variable | Development |
Biodegradable reagent alternatives replace synthetic chemicals with naturally derived or biodegradable compounds that provide similar processing performance without environmental persistence. Plant-based surfactants, organic acids, and bio-derived polymers can substitute for many traditional processing chemicals.
How Does Digital Technology Enable Sustainable Operations?
Internet of Things sensors provide real-time monitoring of environmental parameters throughout processing operations, enabling immediate response to efficiency opportunities or environmental concerns. Digital monitoring transforms environmental management. Smart sensor networks can track energy consumption, water usage, emissions, and waste generation at the equipment level, providing detailed data for optimization.
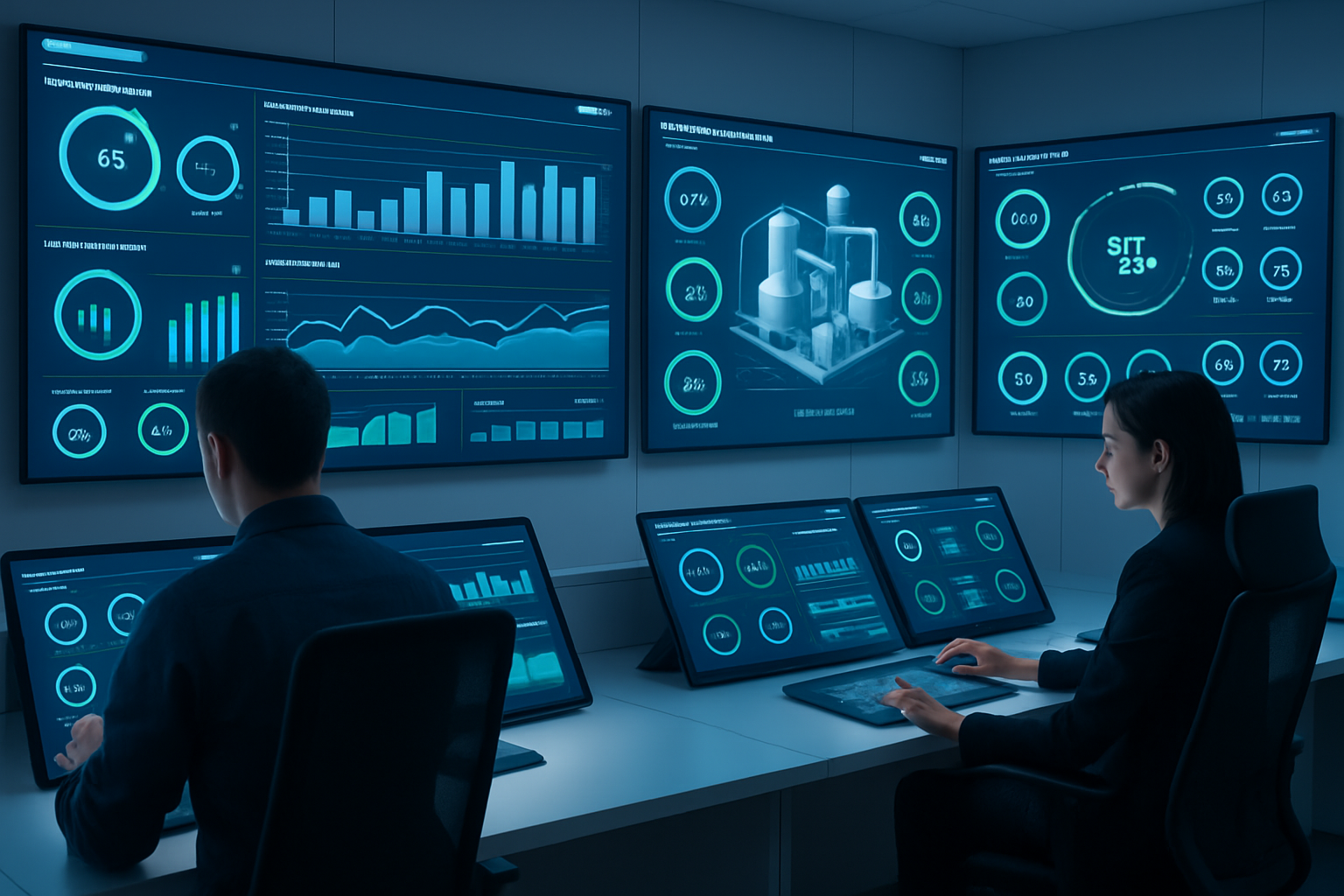
Artificial intelligence-powered process optimization analyzes multiple variables simultaneously to identify optimal operating conditions that minimize environmental impact while maintaining product quality. Machine learning algorithms can process thousands of data points to find efficiency improvements that human operators might miss.
Predictive maintenance technologies use sensor data and analytics to predict equipment failures before they occur, preventing environmental incidents and reducing waste from emergency repairs. Predictive maintenance prevents environmental problems. These systems can predict bearing failures, seal leaks, and other problems that could cause environmental releases.
Digital Technology | Efficiency Gain | Environmental Benefit | Implementation Cost |
---|---|---|---|
IoT monitoring | 15-25% | Real-time optimization | $500K-2M |
AI optimization | 10-20% | Automated efficiency | $1-5M |
Predictive maintenance | 40-60% | Incident prevention | $200K-1M |
Digital twins | 20-35% | Risk-free optimization | $1-3M |
Blockchain tracking | 5-15% | Supply chain transparency | $100K-500K |
Digital twin technology creates virtual replicas of processing operations that enable testing of operational changes without disrupting production. These models can simulate the environmental impact of process modifications, enabling optimization of sustainability metrics before implementation.
What Certification Standards Guide Green Processing?
ISO 14001 environmental management system certification provides a framework for systematic environmental management and continuous improvement. Certification demonstrates environmental commitment. This standard requires facilities to identify environmental aspects, set improvement objectives, and implement management systems to achieve environmental goals.
LEED certification for industrial facilities recognizes sustainable building design and operation practices that reduce environmental impact. LEED-certified processing facilities typically consume 25-40% less energy and 30-50% less water than conventional facilities while providing healthier work environments.
Certification Standard | Environmental Focus | Business Benefit | Implementation Cost |
---|---|---|---|
ISO 14001 | Comprehensive EMS | Risk reduction | $100K-500K |
LEED | Building efficiency | Marketing advantage | $200K-1M |
Carbon verification | GHG emissions | Customer requirements | $50K-200K |
Water stewardship | Water management | Community relations | $100K-300K |
Sustainable mining | Mining practices | Supply chain access | $200K-800K |
Carbon footprint verification standards enable accurate measurement and reporting of greenhouse gas emissions throughout processing operations. Accurate measurement enables effective management. Third-party verification provides credibility for carbon reduction claims while identifying opportunities for improvement.
Which Implementation Strategies Ensure Success?
Phased sustainability transformation approaches reduce implementation risk while enabling learning from early phases to improve later implementations. Systematic implementation ensures success. Typical phases include assessment and planning (3-6 months), pilot testing (6-12 months), limited deployment (12-18 months), and full implementation (18-36 months).
Cost-benefit analysis for green technology adoption must consider both direct cost savings and indirect benefits including risk reduction, regulatory compliance, and market advantages. Comprehensive financial analysis typically shows positive returns within 3-7 years for most green technologies.
Staff training and change management programs address the human factors that determine implementation success. People make technology successful. Comprehensive training programs must cover new equipment operation, environmental procedures, and sustainability principles.
Implementation Phase | Duration | Success Factors | Investment Level |
---|---|---|---|
Assessment | 3-6 months | Thorough analysis | $200K-500K |
Pilot testing | 6-12 months | Realistic conditions | $1-5M |
Limited deployment | 12-18 months | Gradual scaling | $5-20M |
Full implementation | 18-36 months | Change management | $10-50M |
Optimization | Ongoing | Continuous improvement | $500K-2M/year |
Performance measurement and KPI tracking systems monitor progress toward sustainability goals while identifying areas needing attention. Key performance indicators should include energy consumption, water usage, waste generation, carbon emissions, and cost metrics.
Modern green processing methods transform zircon powder operations into environmentally sustainable and economically superior enterprises. These technologies reduce environmental impact by 40-60% while often decreasing operational costs through improved efficiency and waste reduction. Companies implementing comprehensive sustainability programs position themselves for long-term competitive advantage in increasingly environmentally conscious markets. Global Industry’s expertise in sustainable zircon powder processing technology helps clients navigate complex implementation challenges while achieving maximum environmental and financial returns from green technology investments.
What Future Trends Shape Sustainable Processing?
Sustainable zircon powder processing represents a fundamental shift in how the industry approaches environmental responsibility while maintaining operational excellence. The integration of multiple green technologies creates synergistic effects that amplify environmental benefits beyond what individual technologies can achieve. Facilities implementing comprehensive sustainability programs typically see environmental improvements of 50-70% compared to traditional operations.
The economic case for sustainable zircon powder processing continues to strengthen as environmental regulations tighten and carbon pricing mechanisms expand globally. Companies that delay sustainability investments face increasing regulatory risks and potential market access restrictions. Early adopters of green processing technologies position themselves advantageously for future market conditions while capturing immediate operational benefits.
Technology integration challenges require careful planning and phased implementation to ensure successful outcomes. The most successful sustainability transformations combine proven technologies with innovative approaches tailored to specific facility conditions. Zircon powder processors must evaluate their unique circumstances including feedstock characteristics, local regulations, energy costs, and market requirements when selecting optimal technology combinations.
Future developments in sustainable zircon powder processing will likely focus on further automation, artificial intelligence integration, and closed-loop processing systems that eliminate all waste streams. Emerging technologies including advanced materials, biotechnology applications, and quantum computing may enable processing approaches that are currently impossible or economically unfeasible.
The competitive landscape increasingly favors companies with strong environmental performance records. Customers, investors, and regulatory agencies evaluate suppliers based on sustainability metrics, making environmental performance a business necessity rather than an optional consideration. Zircon powder manufacturers implementing comprehensive green processing strategies report improved customer relationships, easier access to capital, and reduced regulatory scrutiny.
Risk management benefits of sustainable processing extend beyond environmental compliance to include operational resilience and supply chain security. Facilities with diversified energy sources, water recycling capabilities, and waste reduction systems prove more resilient to external disruptions including utility outages, water restrictions, and waste disposal limitations.
Conclusion
Investment in sustainable zircon powder processing technology requires long-term perspective and commitment to continuous improvement. The most successful implementations involve ongoing optimization, technology upgrades, and expansion of sustainability initiatives based on operational experience and technological advances. Companies viewing sustainability as a journey rather than a destination achieve superior results and maintain competitive advantages over time.
FAQ Section
Q1: What are the main environmental benefits of sustainable zircon powder processing?
Sustainable zircon powder processing methods reduce carbon emissions by 30-50%, decrease water consumption by 60-80%, and minimize waste generation by 40-70%. These improvements also reduce regulatory compliance costs and improve corporate reputation while often providing long-term cost savings through improved efficiency.
Q2: How much does it cost to implement green zircon powder processing technologies?
Initial investment typically ranges from $2-15 million depending on facility size and technology selection. However, operational savings through reduced energy, water, and waste costs usually provide ROI within 3-7 years. Government incentives and carbon credits can improve financial returns.
Q3: Which sustainable technologies offer the fastest payback period for zircon powder facilities?
Energy efficiency improvements and waste heat recovery systems typically provide the fastest ROI (1-3 years), followed by water recycling systems (2-4 years). Digital optimization technologies also deliver quick returns through improved operational efficiency and reduced resource consumption.
Q4: How do sustainable methods affect zircon powder quality and consistency?
Modern sustainable processing technologies often improve product quality through better process control and reduced contamination. Advanced monitoring systems enable more precise control of processing parameters, resulting in more consistent product specifications and reduced batch variation.
Q5: What regulatory requirements drive sustainable zircon powder processing adoption?
Key drivers include carbon emission reduction mandates, water discharge regulations, waste management requirements, and environmental impact assessment obligations. Many regions now require sustainability reporting and offer incentives for companies adopting green technologies, making sustainable processing both a compliance necessity and competitive advantage.