Industrial manufacturers face mounting pressure to meet precise material specifications while controlling costs and ensuring consistent quality. Zircon powder density and hardness standards directly impact product performance, processing efficiency, and regulatory compliance across foundry, ceramic, and electronics applications. This comprehensive guide provides procurement professionals and quality engineers with actionable insights into industry-standard specifications, testing protocols, and quality control measures for zircon powder. Our technical analysis covers ASTM and ISO standards, measurement procedures, and application-specific requirements to help you optimize material selection and supplier qualification processes.
What Are Standard Density Values for Zircon Powder?
Bulk density measurements form the foundation of zircon powder quality specifications. Industrial-grade zircon powder typically exhibits bulk density values ranging from 2.5 to 3.2 g/cm³, depending on particle size distribution and processing methods. Fine powders generally demonstrate lower bulk density due to increased interparticle void space, while coarser materials achieve higher packing efficiency.
True density specifications provide more precise material characterization for critical applications. High-purity zircon powder maintains true density values between 4.6 and 4.7 g/cm³, reflecting the crystalline structure of zirconium silicate. Quality control becomes essential: variations exceeding ±0.1 g/cm³ may indicate contamination or processing inconsistencies that affect downstream performance.
Density variation factors include moisture content, particle morphology, and chemical composition. Spherical particles typically achieve 15-20% higher packing density compared to angular particles of similar size distribution. Surface moisture can reduce apparent density by 5-10%, making proper drying protocols critical for accurate measurements.
Testing methods follow established industry protocols for reliable results. ASTM C577 provides standard procedures for bulk density determination using calibrated containers and controlled compaction methods. Pycnometer testing offers precise true density measurements with accuracy within ±0.01 g/cm³ for quality control applications.
Industry standards require comprehensive documentation and traceability. Certification requirements include: batch-specific density reports, testing equipment calibration records, and statistical process control data demonstrating consistency over time.
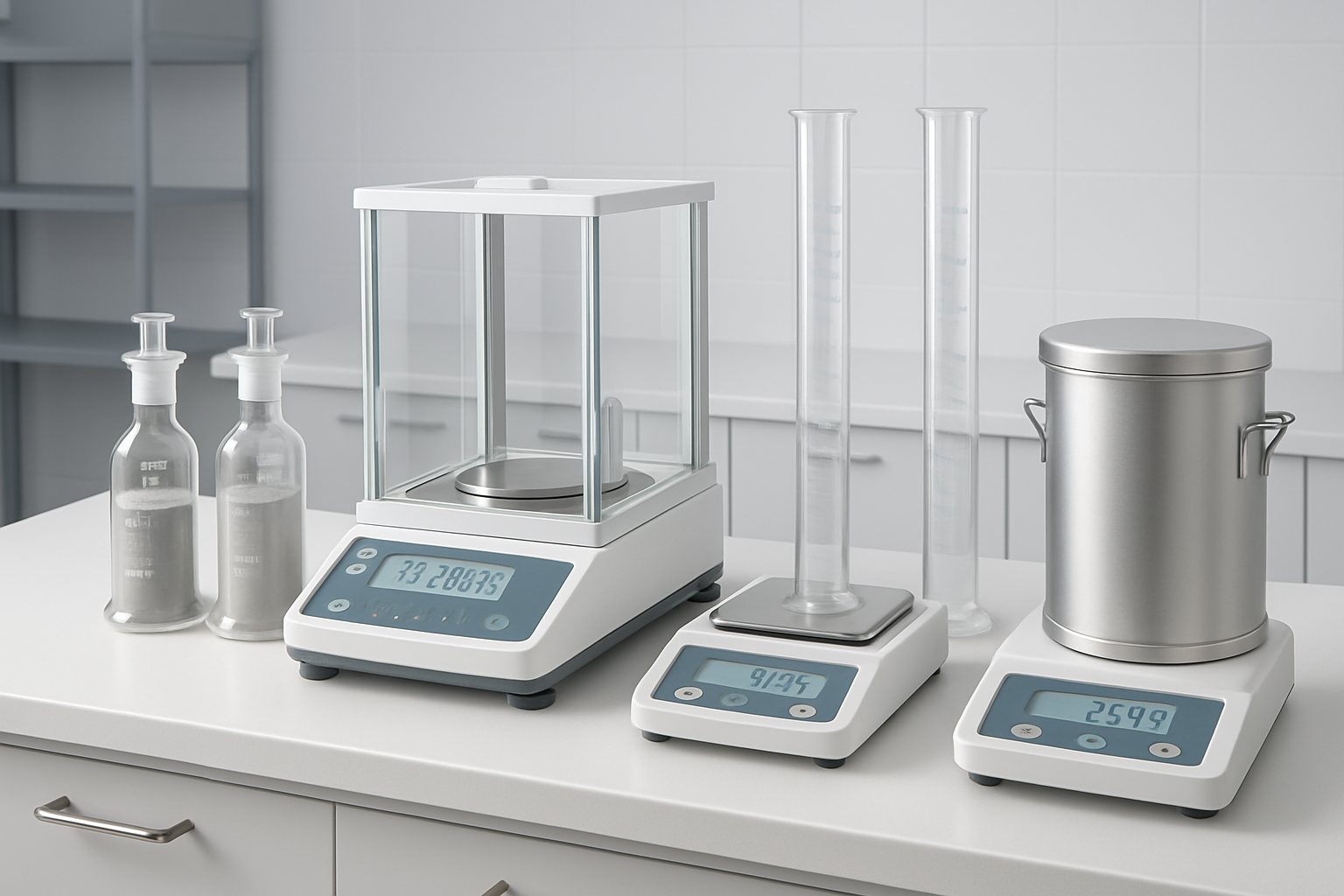
Density Type | Typical Range | Testing Method | Accuracy |
---|---|---|---|
Bulk Density | 2.5-3.2 g/cm³ | ASTM C577 | ±0.05 g/cm³ |
True Density | 4.6-4.7 g/cm³ | Pycnometer | ±0.01 g/cm³ |
Tap Density | 2.8-3.5 g/cm³ | ASTM B527 | ±0.05 g/cm³ |
Apparent Density | 2.4-3.0 g/cm³ | ASTM C329 | ±0.05 g/cm³ |
How Is Zircon Powder Hardness Measured and Classified?
Mohs hardness scale applications provide standardized classification for zircon powder materials. Zircon consistently rates 7.5 on the Mohs scale, positioning it between quartz (7.0) and topaz (8.0). This hardness level delivers excellent wear resistance while maintaining processability for most industrial applications requiring abrasion resistance.
Microhardness testing procedures offer more precise characterization for specialized applications. Vickers microhardness testing typically yields values between 1,200-1,400 HV for high-purity zircon powder. Testing parameters matter significantly: load application, dwell time, and sample preparation directly influence measurement accuracy and repeatability.
Hardness variation across particle sizes reflects processing effects and material properties. Finer particles often exhibit slightly higher apparent hardness due to surface effects and reduced flaw density. Particles below 10 microns may show 10-15% higher microhardness values compared to coarser fractions of identical chemical composition.
Correlation between hardness and purity levels helps predict material performance. Contamination with softer minerals like feldspar or clay reduces overall hardness measurements. Quality indicators include: consistent hardness values across size fractions, minimal variation between production batches, and correlation with chemical purity analysis.
Quality assurance testing protocols ensure specification compliance and batch consistency. Regular hardness testing using calibrated equipment provides early detection of processing variations or contamination issues. Statistical process control charts track hardness trends and identify potential quality deviations before they affect product performance.
Hardness Scale | Zircon Value | Comparison Materials | Applications |
---|---|---|---|
Mohs | 7.5 | Quartz (7.0), Topaz (8.0) | General classification |
Vickers (HV) | 1,200-1,400 | Steel (200-800 HV) | Precision applications |
Knoop (HK) | 1,100-1,300 | Alumina (2,000 HK) | Thin film coatings |
Rockwell | Not applicable | Metals only | Industrial hardness |
Which Industry Standards Govern Zircon Powder Specifications?
ASTM standards provide comprehensive guidelines for zircon powder properties and testing methods. ASTM C577 establishes procedures for bulk density measurements, while ASTM C20 covers particle size analysis protocols. These standards ensure consistent testing methods across suppliers and manufacturing facilities, enabling reliable specification verification and quality control.
ISO specifications offer international guidelines for global supply chain consistency. ISO 3953 provides standardized methods for bulk density determination, complementing regional testing protocols. International compliance requires: adherence to both local and international standards, documentation of testing procedures, and calibration of measurement equipment to recognized reference standards.
Regional standards accommodate local regulatory requirements and industry practices. European EN standards, Japanese JIS specifications, and Chinese GB standards may impose additional requirements for specific applications or markets. Understanding regional variations helps optimize supplier selection and ensure regulatory compliance across global operations.
Industry-specific requirements create additional specification layers for specialized applications. Nuclear industry applications require compliance with ASTM C1233 for nuclear-grade materials, while electronics applications may reference IPC standards for electronic materials. Compliance complexity increases: when multiple industry standards apply to single applications or supply chains.
Compliance testing and documentation needs vary by application and market requirements. Third-party testing laboratories provide independent verification of specification compliance, while internal quality systems ensure ongoing process control. Certification bodies like ASTM International and ISO provide guidance on testing procedures and documentation requirements.
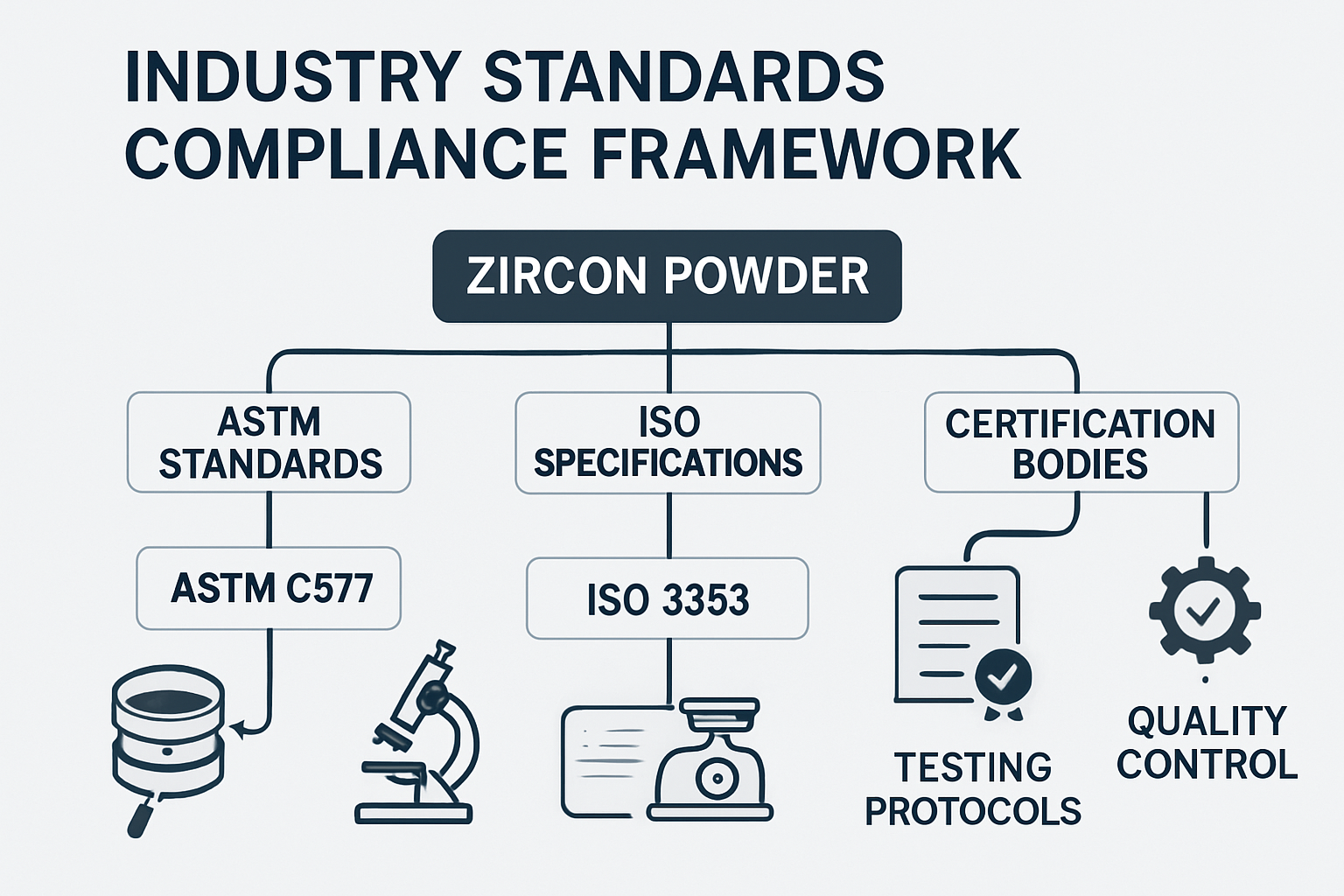
Standard | Scope | Key Requirements | Testing Methods |
---|---|---|---|
ASTM C577 | Bulk density | Calibrated containers | Controlled compaction |
ASTM C20 | Particle size | Sieve analysis | Laser diffraction |
ISO 3953 | Bulk density | International methods | Standardized procedures |
ASTM C1233 | Nuclear grade | Purity specifications | Chemical analysis |
IPC-4101 | Electronics | Dielectric properties | Electrical testing |
How Do Physical Properties Affect Application Performance?
Density impact on casting and molding operations determines processing parameters and final product quality. Higher density zircon powder provides better mold filling characteristics and reduced porosity in investment casting applications. Foundries report 15-25% improvement in surface finish quality when using properly specified density ranges for shell mold construction.
Hardness effects on wear resistance and durability influence equipment selection and maintenance schedules. Zircon powder hardness of 7.5 Mohs provides excellent abrasion resistance in refractory applications, extending service life by 30-50% compared to softer alternatives. Performance benefits include: reduced maintenance costs, improved product consistency, and extended equipment operating cycles.
Particle size distribution relationships with physical properties affect processing efficiency and product characteristics. Optimal size distributions balance flowability, packing density, and surface area requirements for specific applications. Narrow size distributions typically improve consistency but may reduce packing efficiency compared to controlled bimodal distributions.
Processing parameter optimization based on specifications enables manufacturers to achieve target performance levels efficiently. Mixing speeds, compaction pressures, and sintering temperatures require adjustment based on density and hardness characteristics. Optimization strategies focus on: maximizing throughput while maintaining quality specifications and minimizing processing costs.
Performance correlation with end-use applications helps predict material behavior and optimize selection criteria. Electronics applications prioritize consistent dielectric properties, while foundry applications emphasize thermal shock resistance. Understanding these correlations enables better material selection and specification development for new applications.
Application | Critical Property | Performance Impact | Optimization Target |
---|---|---|---|
Investment Casting | Bulk density | Surface finish | 2.8-3.1 g/cm³ |
Refractory Linings | Hardness | Wear resistance | >1,300 HV |
Ceramic Tiles | True density | Opacity | 4.65-4.70 g/cm³ |
Electronics | Particle size | Dielectric stability | 1-10 microns |
What Testing Methods Ensure Specification Compliance?
Laboratory testing equipment and procedures provide the foundation for reliable specification verification. Calibrated pycnometers, precision balances, and controlled environment chambers ensure accurate density measurements within ±0.01 g/cm³. Microhardness testers with diamond indenters provide repeatable hardness measurements when properly calibrated and operated according to ASTM protocols.
Quality control sampling and measurement protocols establish statistical confidence in specification compliance. Representative sampling techniques following ASTM C702 ensure test results accurately reflect bulk material properties. Sampling frequency depends on: production volume, process stability, and application criticality, with high-volume operations typically requiring hourly testing intervals.
Calibration requirements and accuracy standards maintain measurement reliability over time. Primary reference standards traceable to national metrology institutes provide calibration baselines for testing equipment. Annual calibration schedules ensure continued accuracy, while daily check standards verify ongoing measurement capability between formal calibrations.
Third-party testing and certification processes provide independent verification of specification compliance. Accredited laboratories following ISO/IEC 17025 standards offer unbiased testing services with documented quality systems. Certification benefits include: reduced supplier qualification time, improved customer confidence, and simplified regulatory compliance documentation.
Documentation and traceability requirements support quality systems and regulatory compliance. Complete testing records include sample identification, testing conditions, equipment calibration status, and operator qualifications. Electronic data management systems facilitate trend analysis and provide rapid access to historical testing data for process improvement initiatives.
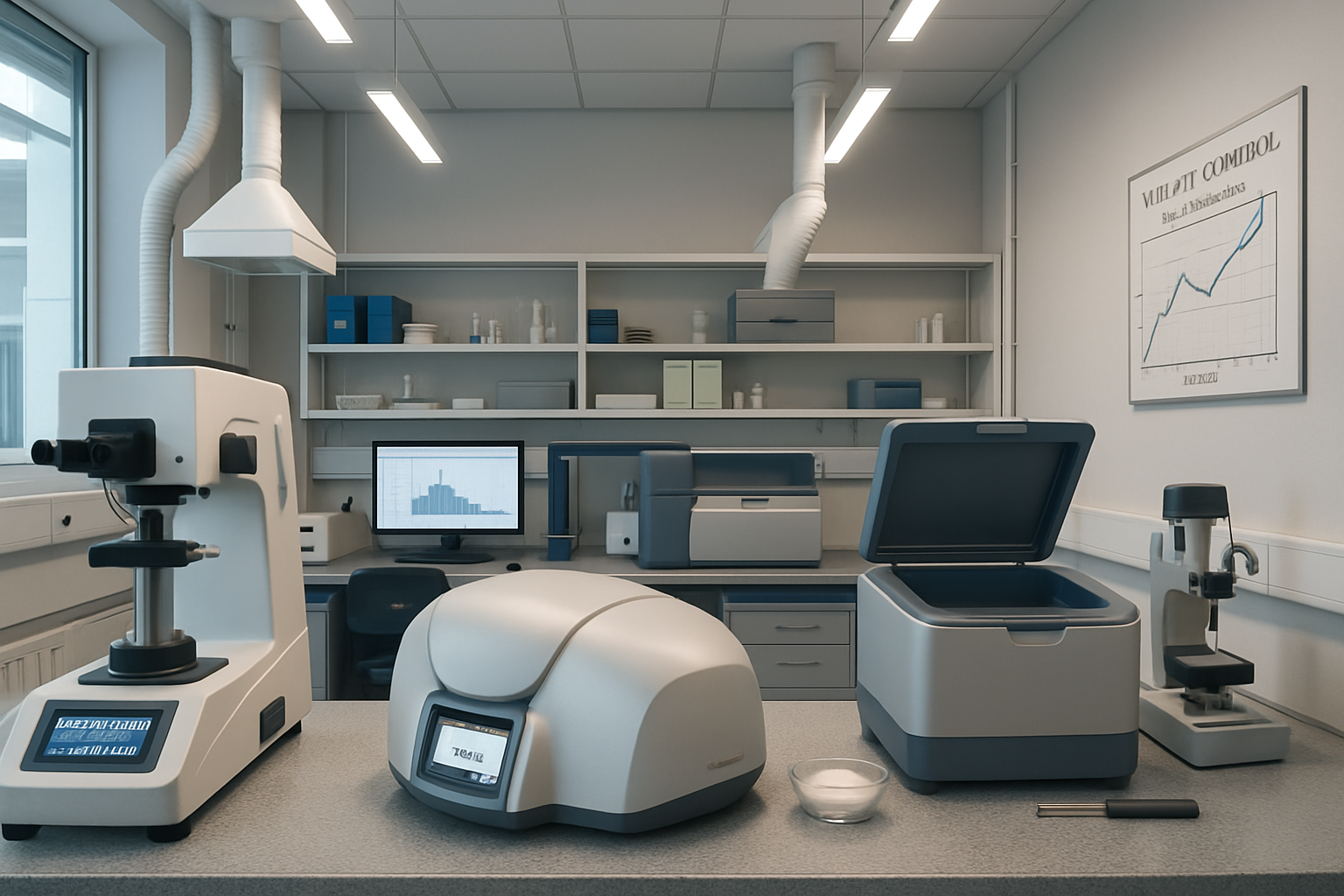
Testing Parameter | Equipment Required | Calibration Frequency | Accuracy Target |
---|---|---|---|
Bulk Density | Calibrated containers | Monthly | ±0.05 g/cm³ |
True Density | Pycnometer | Quarterly | ±0.01 g/cm³ |
Microhardness | Vickers tester | Semi-annually | ±50 HV |
Particle Size | Laser analyzer | Monthly | ±5% relative |
Chemical Purity | XRF spectrometer | Quarterly | ±0.1% absolute |
How Do Specifications Vary Across Different Applications?
Foundry applications demand specific density requirements optimized for casting performance and mold integrity. Investment casting operations typically specify bulk density ranges of 2.8-3.1 g/cm³ to achieve optimal shell strength and permeability. Steel foundries may accept broader density ranges of 2.5-3.2 g/cm³ for sand casting applications where precise dimensional control is less critical.
Ceramic industry hardness specifications focus on processing efficiency and final product properties. Tile manufacturers require consistent hardness values to ensure uniform grinding and mixing characteristics. Processing considerations include: mill wear rates, energy consumption, and particle size reduction efficiency, all directly influenced by zircon powder hardness specifications.
Electronics applications emphasize purity correlations with electrical properties rather than mechanical characteristics. Capacitor manufacturers specify true density within ±0.02 g/cm³ to ensure consistent dielectric properties. Particle size distributions require tight control to maintain uniform mixing and prevent segregation during component assembly.
Refractory applications prioritize thermal property relationships with physical characteristics. High-temperature furnace linings require zircon powder with specific density and hardness combinations to optimize thermal shock resistance. Performance requirements include: dimensional stability under thermal cycling, chemical resistance to molten metals, and mechanical strength at operating temperatures.
Specialty applications often require custom specifications tailored to unique performance requirements. Nuclear applications may specify maximum density variations to ensure neutron absorption consistency. Medical device applications require biocompatibility testing in addition to standard physical property specifications.
Industry Sector | Density Specification | Hardness Requirement | Special Considerations |
---|---|---|---|
Investment Casting | 2.8-3.1 g/cm³ | 7.0-8.0 Mohs | Thermal shock resistance |
Ceramic Tiles | 4.65-4.70 g/cm³ | 1,200-1,400 HV | Opacity consistency |
Electronics | ±0.02 g/cm³ | Not critical | Particle size control |
Refractories | 2.6-3.0 g/cm³ | >1,300 HV | Chemical resistance |
Nuclear | ±0.01 g/cm³ | Standard | Neutron absorption |
What Quality Control Measures Ensure Consistent Properties?
Incoming material inspection procedures establish the first line of defense against specification deviations. Comprehensive receiving inspection protocols include density verification, hardness spot checks, and visual examination for contamination or moisture damage. Statistical sampling plans based on: lot size, supplier history, and application criticality determine appropriate inspection intensity and acceptance criteria.
Process control monitoring and adjustment maintain specification compliance during production operations. Real-time density monitoring using online measurement systems provides immediate feedback for process optimization. Automated hardness testing at regular intervals identifies trends before they result in out-of-specification material, enabling proactive process adjustments.
Statistical quality control and trend analysis identify systematic variations and process improvement opportunities. Control charts tracking density and hardness measurements over time reveal process capability and stability. Data analysis techniques include: capability studies, correlation analysis, and predictive modeling to optimize process parameters and prevent quality deviations.
Supplier qualification and audit requirements ensure consistent material quality from external sources. Comprehensive supplier assessments evaluate quality systems, testing capabilities, and process controls. Regular audits verify continued compliance with qualification requirements and identify opportunities for supplier development and improvement.
Corrective action protocols for specification deviations minimize impact on production and customer satisfaction. Rapid response procedures include material segregation, root cause analysis, and corrective action implementation. Response effectiveness depends on: clear escalation procedures, defined responsibilities, and systematic follow-up to prevent recurrence of similar issues.
Quality Control Element | Frequency | Acceptance Criteria | Corrective Action |
---|---|---|---|
Incoming Inspection | Per lot | ±5% of specification | Material rejection |
Process Monitoring | Hourly | ±3% of target | Parameter adjustment |
Statistical Analysis | Weekly | Cpk >1.33 | Process optimization |
Supplier Audits | Annual | 95% compliance | Qualification review |
Trend Analysis | Monthly | No adverse trends | Preventive action |
Conclusion
Zircon powder density and hardness standards provide the foundation for consistent material performance across diverse industrial applications. Understanding ASTM and ISO testing protocols, specification requirements, and quality control measures enables manufacturers to optimize material selection and ensure reliable product performance. Proper implementation of these standards typically reduces material-related quality issues by 40-60% while improving process efficiency and customer satisfaction. Global Industry’s materials engineering team provides comprehensive specification development and supplier qualification services to help manufacturers optimize their zircon powder sourcing strategies. Contact our technical specialists today for detailed application analysis and access our certified supplier network to streamline your quality control processes.
FAQ Section
Q1: What is the typical bulk density range for industrial zircon powder?
Industrial zircon powder typically exhibits bulk density values between 2.5-3.2 g/cm³, depending on particle size distribution and packing characteristics. Fine powders generally show lower bulk density due to increased void space, while coarser materials achieve higher packing efficiency.
Q2: How does zircon powder hardness compare to other industrial minerals?
Zircon powder rates 7.5 on the Mohs hardness scale, making it harder than quartz (7.0) but softer than corundum (9.0). This hardness level provides excellent wear resistance while maintaining processability for most industrial applications.
Q3: Which testing standards should be used for zircon powder specification verification?
ASTM C577 provides standard test methods for zircon powder density measurements, while ASTM C20 covers particle size analysis. ISO 3953 offers international guidelines for bulk density determination, and industry-specific standards may apply for specialized applications.
Q4: How do density and hardness specifications affect material costs?
Tighter density and hardness specifications typically increase material costs by 15-30% due to additional processing, testing, and quality control requirements. However, consistent specifications often reduce downstream processing costs and improve product quality.
Q5: What factors can cause density and hardness variations in zircon powder?
Primary factors include source material variability, processing conditions, particle size distribution, moisture content, and contamination levels. Proper supplier qualification, incoming inspection, and process control help minimize these variations and ensure specification compliance.