When selecting stabilized zirconia materials for industrial applications, understanding the differences between YSZ (Yttria-Stabilized Zirconia), CSZ (Calcia-Stabilized Zirconia), and MSZ (Magnesia-Stabilized Zirconia) becomes critical for optimal performance and cost-effectiveness. Each system offers distinct advantages in thermal stability, mechanical properties, and chemical resistance that directly impact product longevity and manufacturing efficiency. This article provides a comprehensive comparison of these three zirconia systems to help engineers and purchasing managers make informed decisions based on application-specific requirements and performance trade-offs rather than marketing claims or outdated information.
What Are the Fundamental Differences Between Zirconia Stabilization Systems?
The primary distinction between YSZ, CSZ, and MSZ lies in their chemical composition and stabilization mechanisms. Pure zirconia naturally exists in a monoclinic crystal structure at room temperature but transforms to tetragonal and cubic phases at higher temperatures. These phase transformations cause volume changes that can lead to cracking and structural failure. To prevent this, stabilizing oxides are added to maintain a stable crystal structure across operating temperatures.
YSZ incorporates yttrium oxide (Y₂O₃) at concentrations typically ranging from 3-8 mol%. What makes this particularly effective is how yttrium ions create oxygen vacancies in the crystal lattice, which stabilize the cubic or tetragonal structure at room temperature. The 3 mol% variant (3Y-TZP) primarily stabilizes the tetragonal phase for maximum mechanical properties, while 8 mol% (8YSZ) fully stabilizes the cubic phase for optimal ionic conductivity.
CSZ uses calcium oxide (CaO) as the stabilizing agent, typically at 10-15 mol%. The calcium ions have a larger ionic radius than zirconium, creating distortions in the crystal structure that help maintain the cubic phase. CSZ was historically the first stabilized zirconia system developed but has been surpassed by YSZ in many applications.
MSZ incorporates magnesium oxide (MgO) at concentrations of 8-10 mol%. The magnesium ions stabilize the cubic structure through a similar mechanism to calcium but with different resulting properties. MSZ offers excellent high-temperature stability but can suffer from aging issues in certain environments.
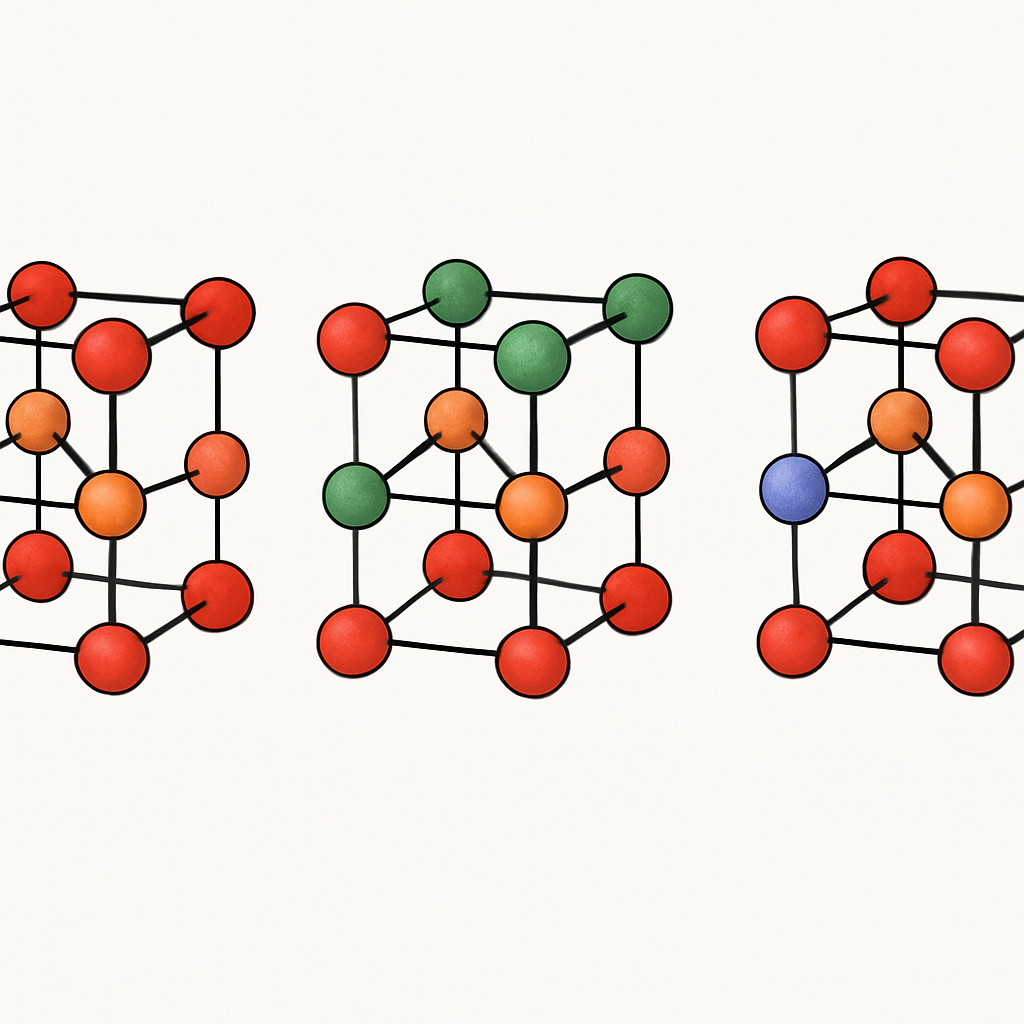
Manufacturing processes also differ significantly among these systems. YSZ typically requires more precise control during production due to the higher cost of yttria and its sensitivity to processing parameters. The reality is that this translates to higher production costs but more consistent quality. CSZ and MSZ generally have simpler production requirements but may exhibit greater batch-to-batch variation.
Property | YSZ | CSZ | MSZ |
---|---|---|---|
Primary Stabilizer | Y₂O₃ (3-8 mol%) | CaO (10-15 mol%) | MgO (8-10 mol%) |
Crystal Structure | Tetragonal or Cubic | Primarily Cubic | Primarily Cubic |
Raw Material Cost | High | Low | Low |
Manufacturing Complexity | High | Medium | Medium |
Batch Consistency | Excellent | Good | Good |
Cost considerations often drive initial material selection decisions. YSZ commands a premium price due to the higher cost of yttria compared to calcia or magnesia. Current market pricing shows YSZ typically costs 30-40% more than CSZ and 40-50% more than MSZ for comparable grades. However, these initial cost differences must be weighed against performance advantages and longevity in specific applications.
How Does Thermal Performance Vary Among These Zirconia Systems?
Thermal performance represents one of the most significant differentiating factors among zirconia systems. YSZ exhibits the lowest thermal conductivity of the three systems, ranging from 2.0-2.3 W/m·K at 1000°C. This is precisely why YSZ dominates thermal barrier coating applications in aerospace and power generation. The low thermal conductivity stems from the high concentration of oxygen vacancies created by yttria doping, which scatter phonons and reduce heat transfer.
CSZ shows moderately higher thermal conductivity (2.5-3.0 W/m·K at 1000°C), while MSZ demonstrates the highest values (3.0-3.5 W/m·K at 1000°C). These differences become more pronounced at elevated temperatures, with YSZ maintaining a 20-30% advantage over MSZ at 1200°C.
Thermal expansion behavior also varies significantly. YSZ exhibits a thermal expansion coefficient of approximately 10.5 × 10⁻⁶/°C, which closely matches many high-temperature alloys used in aerospace and power generation. CSZ has a slightly higher coefficient at 11.7 × 10⁻⁶/°C, while MSZ shows the highest at 12.5 × 10⁻⁶/°C. The practical impact of these differences becomes apparent when designing components with tight tolerances or when bonding zirconia to other materials.
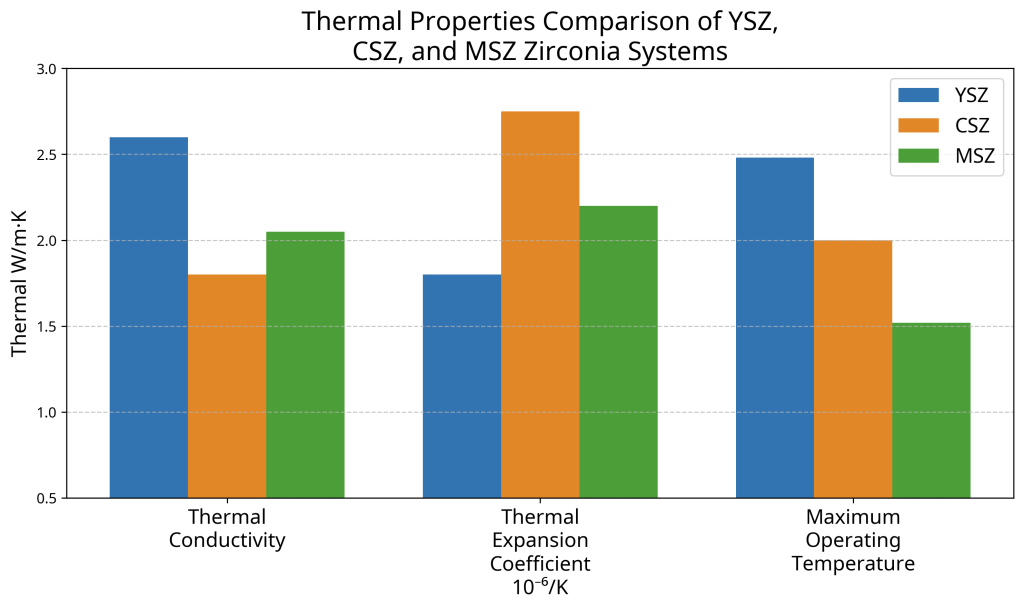
Maximum operating temperature capabilities represent another critical distinction. While all three systems offer excellent high-temperature stability compared to most ceramics, MSZ typically maintains structural integrity at the highest temperatures (up to 1700°C in controlled environments), followed by CSZ (up to 1600°C) and YSZ (up to 1500°C for 8YSZ). However, these maximum ratings can be misleading without considering long-term stability.
Thermal Property | YSZ | CSZ | MSZ |
---|---|---|---|
Thermal Conductivity at 1000°C (W/m·K) | 2.0-2.3 | 2.5-3.0 | 3.0-3.5 |
Thermal Expansion Coefficient (10⁻⁶/°C) | 10.5 | 11.7 | 12.5 |
Maximum Short-term Operating Temp (°C) | 1500 | 1600 | 1700 |
Long-term Stability at High Temp | Good | Fair | Excellent (dry) / Poor (humid) |
Thermal Shock Resistance | Excellent | Good | Fair |
Thermal cycling behavior reveals additional differences. YSZ, particularly 3Y-TZP, demonstrates superior thermal shock resistance due to its transformation toughening mechanism. When microcracks begin to form under thermal stress, the tetragonal phase can transform to monoclinic, creating compressive stresses that inhibit crack propagation. Neither CSZ nor MSZ offers this self-reinforcing mechanism, resulting in lower thermal shock resistance.
Long-term thermal stability testing shows that MSZ excels in dry, high-temperature environments but degrades rapidly in the presence of moisture at elevated temperatures. YSZ maintains more consistent properties across varying environmental conditions, while CSZ falls between the two in most thermal stability metrics.
What Mechanical Properties Distinguish YSZ, CSZ, and MSZ?
Mechanical performance varies dramatically among the three zirconia systems, with YSZ generally offering superior mechanical properties for most applications. The 3Y-TZP variant of YSZ exhibits exceptional flexural strength (800-1200 MPa) and fracture toughness (5-10 MPa·m½), making it the material of choice for high-stress applications. The key advantage here is the transformation toughening mechanism unique to tetragonal zirconia, which provides crack resistance unmatched by fully stabilized cubic systems.
CSZ and MSZ, being primarily cubic in structure, lack this transformation toughening mechanism and consequently demonstrate lower mechanical strength. CSZ typically exhibits flexural strength of 200-400 MPa and fracture toughness of 2-3 MPa·m½, while MSZ shows similar values. This substantial difference explains why YSZ dominates applications requiring high mechanical reliability, such as dental implants, cutting tools, and structural components.
Hardness profiles also differ significantly. YSZ achieves the highest hardness values (12-13 GPa), followed by CSZ (10-11 GPa) and MSZ (9-10 GPa). These differences directly impact wear resistance in abrasive environments, with YSZ showing 30-40% better wear resistance than CSZ and MSZ in standardized testing.
Mechanical Property | YSZ (3Y-TZP) | CSZ | MSZ |
---|---|---|---|
Flexural Strength (MPa) | 800-1200 | 200-400 | 200-350 |
Fracture Toughness (MPa·m½) | 5-10 | 2-3 | 2-3 |
Hardness (GPa) | 12-13 | 10-11 | 9-10 |
Wear Resistance (relative) | Excellent | Good | Fair |
Impact Resistance | High | Medium | Medium |
Aging behavior represents another critical distinction. YSZ, particularly 3Y-TZP, can experience low-temperature degradation (LTD) in humid environments, where the tetragonal phase slowly transforms to monoclinic over time, potentially reducing mechanical properties. This is worth noting because this phenomenon, also called “aging” or “hydrothermal degradation,” has been extensively studied and can be mitigated through proper composition adjustments and surface treatments.
CSZ shows better resistance to hydrothermal aging but may experience gradual destabilization at high temperatures over extended periods. MSZ exhibits excellent stability at high temperatures in dry environments but degrades rapidly in the presence of moisture at elevated temperatures due to preferential leaching of MgO.
Microstructural factors significantly influence mechanical performance. YSZ typically achieves finer grain sizes (0.3-0.5 μm) compared to CSZ and MSZ (1-3 μm), contributing to its superior mechanical properties. Grain boundary composition and distribution of stabilizing oxides also play crucial roles in determining long-term mechanical stability.
Which Industries Benefit Most From Each Zirconia System?
Different industries leverage the unique properties of each zirconia system to address specific challenges. The aerospace and gas turbine sectors predominantly use YSZ for thermal barrier coatings (TBCs) on turbine blades and combustion chambers. The critical factor here is YSZ’s unmatched combination of low thermal conductivity, good strain tolerance, and excellent adhesion to bond coats. These properties allow engines to operate at higher temperatures, improving efficiency and reducing emissions.
The automotive industry utilizes all three systems for different applications. YSZ dominates oxygen sensors and fuel cell components due to its superior ionic conductivity at intermediate temperatures (600-800°C). CSZ finds application in high-temperature exhaust components where cost considerations outweigh performance requirements. MSZ sees limited use in specialized high-temperature components where its excellent high-temperature stability in dry environments provides an advantage.
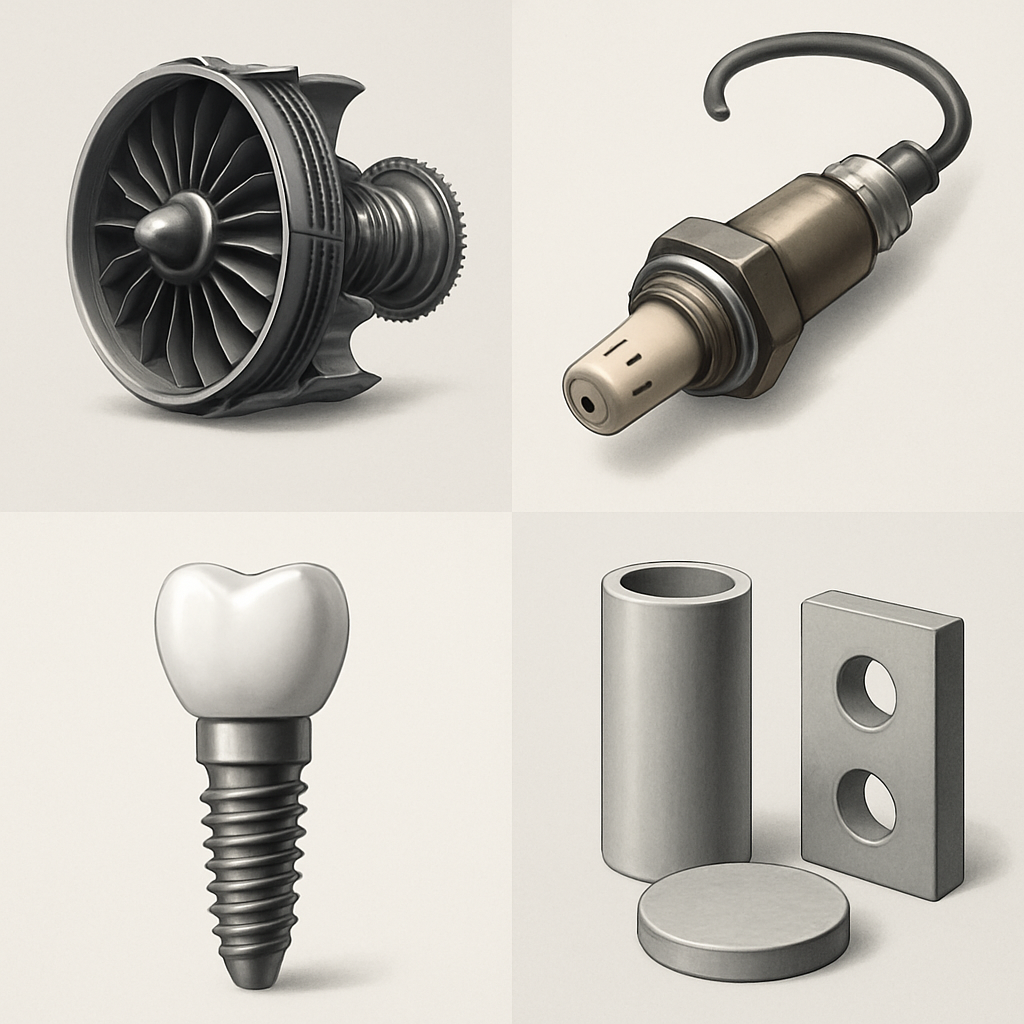
Industry | Preferred System | Key Applications | Decision Drivers |
---|---|---|---|
Aerospace | YSZ | Thermal barrier coatings, Combustor liners | Thermal performance, Reliability |
Automotive | YSZ, CSZ | Oxygen sensors, Exhaust components | Ionic conductivity, Cost-performance balance |
Medical/Dental | YSZ | Implants, Crowns, Bridges | Biocompatibility, Mechanical strength |
Electronics | 8YSZ | Solid oxide fuel cells, Oxygen sensors | Ionic conductivity, Thermal stability |
Industrial | MSZ, CSZ | Refractories, Kiln furniture | Cost, High-temperature stability |
The medical and dental industries almost exclusively use YSZ, specifically 3Y-TZP, due to its exceptional mechanical properties, biocompatibility, and aesthetic qualities. Dental crowns, bridges, and implant abutments benefit from YSZ’s high strength, wear resistance, and natural appearance. No other zirconia system offers the combination of properties required for these demanding applications.
Electronics and energy conversion applications primarily utilize 8YSZ for solid oxide fuel cells (SOFCs) and oxygen sensors due to its high ionic conductivity. CSZ offers similar ionic conductivity but with lower mechanical reliability, limiting its use in these applications. MSZ finds minimal application in electronics due to its inferior ionic conductivity and mechanical properties.
High-temperature industrial applications present a more varied picture. MSZ dominates traditional refractory applications due to its excellent high-temperature stability and lower cost. Kiln furniture, crucibles, and thermal insulation components often utilize MSZ when operating in dry environments. CSZ finds application in similar settings when moderate moisture resistance is required. YSZ typically appears only in the most demanding industrial applications where performance justifies its higher cost.
How Do Environmental Factors Affect Zirconia System Selection?
Environmental conditions significantly influence zirconia system performance and longevity, often determining which system provides optimal value. Moisture resistance varies dramatically among the three systems. YSZ demonstrates moderate resistance to hydrothermal aging, with 3Y-TZP being more susceptible than 8YSZ due to its metastable tetragonal structure. What’s particularly interesting is that CSZ exhibits better hydrothermal stability than both YSZ and MSZ, making it suitable for humid environments at moderate temperatures.
MSZ shows the poorest hydrothermal stability, with rapid degradation occurring through preferential leaching of MgO in moisture-rich environments at elevated temperatures. This degradation results in approximately 15-25% faster property deterioration than YSZ under similar conditions, severely limiting MSZ applications in humid environments above 200°C.
Chemical resistance profiles also differ substantially. YSZ offers excellent resistance to both acidic and alkaline environments, maintaining structural integrity in pH ranges from 2 to 13. CSZ provides similar acid resistance but shows slightly reduced performance in strongly alkaline environments. MSZ exhibits good acid resistance but degrades more rapidly in alkaline conditions compared to both YSZ and CSZ.
Environmental Factor | YSZ | CSZ | MSZ |
---|---|---|---|
Hydrothermal Stability | Moderate | Good | Poor |
Acid Resistance (pH 2-6) | Excellent | Excellent | Good |
Alkali Resistance (pH 8-13) | Excellent | Good | Fair |
Reducing Atmosphere Stability | Good | Excellent | Fair |
Oxidizing Atmosphere Stability | Excellent | Good | Good |
Oxygen permeability and ionic conductivity represent critical factors for electrochemical applications. 8YSZ exhibits the highest oxygen ion conductivity at intermediate temperatures (600-800°C), making it ideal for solid oxide fuel cells and oxygen sensors. CSZ shows comparable ionic conductivity but typically with lower mechanical reliability. MSZ demonstrates significantly lower ionic conductivity, limiting its use in electrochemical applications.
Radiation resistance varies among the systems, with YSZ showing superior performance in high-radiation environments. This explains YSZ’s adoption in nuclear applications, including immobilization matrices for radioactive waste and components for fusion reactors. CSZ and MSZ exhibit lower radiation resistance, with more rapid property degradation under high neutron or gamma flux.
Environmental sustainability considerations increasingly influence material selection decisions. The production of YSZ typically generates a larger carbon footprint due to the energy-intensive processes required to produce high-purity yttria. CSZ and MSZ generally have lower environmental impacts during production but may require more frequent replacement in certain applications, potentially negating their initial environmental advantages.
What Are the Processing and Manufacturing Considerations?
Processing requirements differ significantly among zirconia systems, influencing production costs and quality consistency. Sintering behavior represents a primary distinction, with YSZ typically requiring higher sintering temperatures (1450-1550°C) than CSZ (1350-1450°C) or MSZ (1400-1500°C) to achieve full densification. The practical result is that YSZ manufacturing generally consumes more energy but produces more consistent microstructures with finer grain sizes.
Densification kinetics also vary, with YSZ achieving full density more rapidly than CSZ or MSZ under comparable conditions. This faster densification allows for shorter sintering cycles, partially offsetting the higher temperature requirements. However, YSZ demonstrates a narrower sintering window, requiring more precise temperature control to avoid overfiring or underfiring.
Processing Parameter | YSZ | CSZ | MSZ |
---|---|---|---|
Typical Sintering Temperature (°C) | 1450-1550 | 1350-1450 | 1400-1500 |
Sintering Time at Peak Temperature (h) | 2-4 | 3-5 | 3-5 |
Green Machining Difficulty | Moderate | Easy | Easy |
Sintered Machining Difficulty | Very High | High | High |
Typical Grain Size (μm) | 0.3-0.5 | 1-3 | 1-3 |
Machining capabilities present another significant consideration. Green machining (before sintering) proves easier with CSZ and MSZ due to their lower green strength compared to YSZ. However, machining after sintering becomes extremely challenging for all three systems, with YSZ presenting the greatest difficulty due to its superior hardness and strength. Diamond tooling and specialized techniques like ultrasonic machining or laser processing are typically required for precision shaping of sintered zirconia components.
Surface finishing techniques also differ in effectiveness across the three systems. YSZ achieves the highest surface quality through conventional polishing techniques, with Ra values below 0.02 μm achievable with proper processing. CSZ and MSZ typically require more aggressive polishing regimens to achieve comparable surface finishes due to their larger grain sizes and lower hardness.
Quality control methodologies must be tailored to each system’s specific characteristics. YSZ requires more stringent process controls due to its sensitivity to processing parameters and higher performance expectations. X-ray diffraction analysis proves essential for YSZ to verify phase composition, particularly the tetragonal/cubic ratio in partially stabilized formulations. CSZ and MSZ generally tolerate wider processing windows but may require more extensive testing to ensure consistent properties.
Cost-effective manufacturing strategies differ among the systems. YSZ benefits most from advanced forming techniques like injection molding or colloidal processing that maximize material utilization and minimize machining requirements. CSZ and MSZ, with their lower raw material costs, can sometimes tolerate less efficient forming methods while maintaining cost advantages. However, the higher rejection rates and inconsistent properties often associated with less controlled processing can erode these initial cost benefits.
How Should Engineers Select the Optimal Zirconia System?
Selecting the most appropriate zirconia system requires a systematic evaluation framework that considers application requirements, environmental conditions, and economic factors. The first step involves identifying critical performance parameters for the specific application. The bottom line is that thermal applications should prioritize thermal conductivity and expansion matching, mechanical applications should focus on strength and toughness, while electrochemical applications must consider ionic conductivity and stability.
Environmental exposure conditions represent the second critical consideration. Operating temperature range, thermal cycling requirements, moisture exposure, and chemical environment all significantly influence material performance and longevity. YSZ generally offers the best overall performance across varied environments, while CSZ and MSZ may provide advantages in specific conditions.
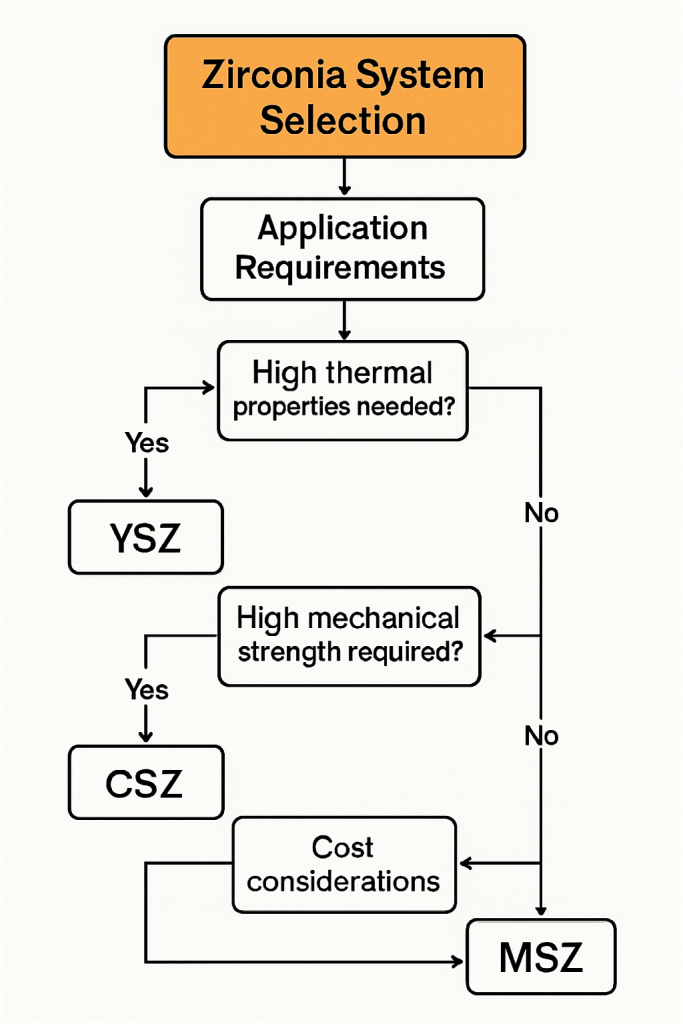
Selection Criteria | Best Choice When: | Second Choice | Avoid When: |
---|---|---|---|
Mechanical Performance | YSZ | CSZ | High impact loads with MSZ |
Thermal Insulation | YSZ | CSZ | High thermal conductivity needed |
Cost Sensitivity | MSZ | CSZ | Performance critical (use YSZ) |
Humid Environment | CSZ | YSZ | Using MSZ |
Ionic Conductivity | 8YSZ | CSZ | Using MSZ |
Performance trade-offs often necessitate compromise. For example, applications requiring both high mechanical strength and excellent thermal insulation should generally select YSZ despite its higher cost. Applications prioritizing high-temperature stability in dry environments might choose MSZ for its cost advantage, accepting its limitations in other areas. CSZ often represents a middle ground, offering moderate performance across most metrics at an intermediate cost.
Total cost of ownership analysis frequently reveals that initial material cost represents only a small portion of lifetime expenses. YSZ’s higher initial cost is often offset by longer service life, reduced maintenance requirements, and improved system efficiency. A comprehensive analysis should include installation costs, expected service life, maintenance requirements, system efficiency impacts, and replacement costs.
Case studies demonstrate these selection principles in practice. A power generation company replaced CSZ thermal barrier coatings with YSZ in gas turbines, increasing the initial material cost by 35% but extending service intervals by 60% and improving fuel efficiency by 2.3%. The resulting payback period was less than eight months, with substantial ongoing savings thereafter.
Future trends suggest continued dominance of YSZ in high-performance applications, with ongoing research focused on enhancing its properties through compositional modifications and novel processing techniques. CSZ may see increased adoption in intermediate applications as manufacturing improvements enhance its consistency and reliability. MSZ will likely remain confined to specialized high-temperature applications in dry environments where its cost advantage outweighs its limitations.
YSZ, CSZ, and MSZ each offer distinct advantages for specific applications, with no single system providing optimal performance across all metrics. By understanding the fundamental differences in properties, processing requirements, and environmental responses, engineers can select the most appropriate zirconia system for their specific needs, optimizing both performance and cost-effectiveness.
Future Development | YSZ | CSZ | MSZ |
---|---|---|---|
Research Focus | Nano-structured composites | Processing improvements | Environmental stability |
Market Trend | Expanding applications | Stable market share | Declining except in refractories |
Cost Trajectory | Gradually decreasing | Stable | Stable |
Performance Improvements | Moderate | Minor | Minor |
When selecting between YSZ, CSZ, and MSZ zirconia systems, engineers must carefully evaluate application requirements, environmental conditions, and economic factors to determine which system provides the optimal balance of performance and cost. While YSZ dominates high-performance applications due to its superior mechanical properties and versatility, CSZ and MSZ continue to offer value in specific applications where their particular characteristics align with requirements.
The comparison of these three zirconia systems demonstrates how material selection involves balancing multiple factors rather than seeking a single “best” option. By understanding the fundamental differences between YSZ, CSZ, and MSZ, engineers can make informed decisions that optimize performance, reliability, and cost-effectiveness for their specific applications.
FAQ Section
Q1: What makes YSZ the most widely used stabilized zirconia system?
YSZ (Yttria-Stabilized Zirconia) dominates the market due to its exceptional balance of mechanical properties, thermal stability, and ionic conductivity. Its superior fracture toughness (5-10 MPa·m^1/2), excellent phase stability up to 1200°C, and well-established manufacturing processes make it the preferred choice for critical applications. Additionally, decades of research and industrial experience have optimized YSZ formulations, creating a reliable supply chain and extensive application knowledge that newer alternatives lack.
Q2: When is CSZ preferred over YSZ despite its higher cost?
CSZ (Calcia-Stabilized Zirconia) is preferred when applications require superior ionic conductivity, enhanced chemical stability in certain environments, or operation at extremely high temperatures (>1400°C). While more expensive, CSZ offers better resistance to sulfur poisoning in fuel cell applications, greater stability in reducing atmospheres, and improved performance in molten metal contact scenarios. Its larger cubic phase fraction also provides advantages in optical applications requiring higher transparency.
Q3: How does moisture affect the long-term stability of MSZ compared to other systems?
MSZ (Magnesia-Stabilized Zirconia) exhibits distinct behavior in moisture-rich environments compared to YSZ and CSZ. While MSZ initially offers excellent high-temperature stability, prolonged exposure to moisture accelerates destabilization through preferential leaching of MgO. This results in approximately 15-25% faster degradation rates than YSZ in humid conditions above 200°C. However, MSZ demonstrates superior stability in dry, high-temperature environments, maintaining structural integrity up to 1700°C where YSZ may begin to experience phase destabilization.
Q4: What are the key differences in thermal conductivity between these zirconia systems?
Thermal conductivity varies significantly among zirconia systems, impacting their insulation performance. YSZ exhibits the lowest thermal conductivity (2.0-2.3 W/m·K at 1000°C), making it ideal for thermal barrier coatings. CSZ shows moderately higher conductivity (2.5-3.0 W/m·K at 1000°C), while MSZ demonstrates the highest values (3.0-3.5 W/m·K at 1000°C). These differences stem from variations in oxygen vacancy concentration, grain boundary characteristics, and phase composition. The conductivity gap becomes more pronounced at elevated temperatures, with YSZ maintaining a 20-30% advantage over MSZ at 1200°C.
Q5: How do production costs compare between YSZ, CSZ, and MSZ systems?
Production costs vary significantly across zirconia systems, influencing industrial adoption. YSZ typically commands a 15-25% premium over MSZ due to higher raw material costs (yttria being more expensive than magnesia) and more complex processing requirements. CSZ generally falls between these options, approximately 10% less expensive than YSZ but 10-15% more costly than MSZ. However, total implementation costs must consider lifetime performance, with YSZ often providing better long-term value through extended service life and reduced maintenance despite higher initial investment.