Tile manufacturers face daily pressure to deliver flawless, bright products at a steady price. One tiny flaw in glaze can trigger costly rework or scrap. Many procurement teams struggle when cheaper fillers promise savings but cause more defects. Here’s the good news: using zircon sand solves this problem at scale. This article explains what makes zircon sand so dependable, how it compares with other choices, and how smart sourcing protects quality and budget. Backed by industry data, real factory stories, and clear buying tips, this guide equips managers with practical knowledge to make the right call for their tile lines.
What Key Properties Define Zircon Sand?
Zircon sand stands out because it handles heat like a pro and stays stable under tough kiln conditions. This keeps glazes smooth and prevents random flaws that drive up reject rates. Factories love that zircon does not react wildly when fired at high temperatures. Instead, it locks in strength and color.
The grain size matters, too. Fine grains spread more evenly, which means fewer lumps in glaze mixes. Coarser grains might suit rustic or textured finishes. Choosing the right grain size depends on the look your buyers expect.
Another big factor is chemical purity. Top-grade sand has fewer iron traces. Iron can ruin light-colored tiles with stains or streaks. Good zircon means cleaner colors and less stress during inspection.
Here’s a tip worth noting: Always ask for the sand’s moisture content and impurity breakdown. High moisture causes unwanted steam in kilns, leading to bubbles or cracks. Reliable suppliers provide detailed lab results with each shipment.
Zircon’s high melting point keeps it stable even when kilns hit peak heat. This thermal stability keeps the tile body firm and the glaze tight.
For busy purchasing teams, consistency matters most. With zircon sand, production lines run smoother because each lot behaves predictably.
Property | Why It Matters |
---|---|
Chemical Purity | Stops color defects |
Controlled Grain Size | Smooth glaze application |
Thermal Stability | Safe high-temp firing |
Low Moisture | Prevents kiln defects |
Many factories run trial firings with small sand batches first. This step lets them tweak glaze formulas and spot issues before big production runs. Taking time to pick the right zircon type saves money in the long run and keeps customers loyal.
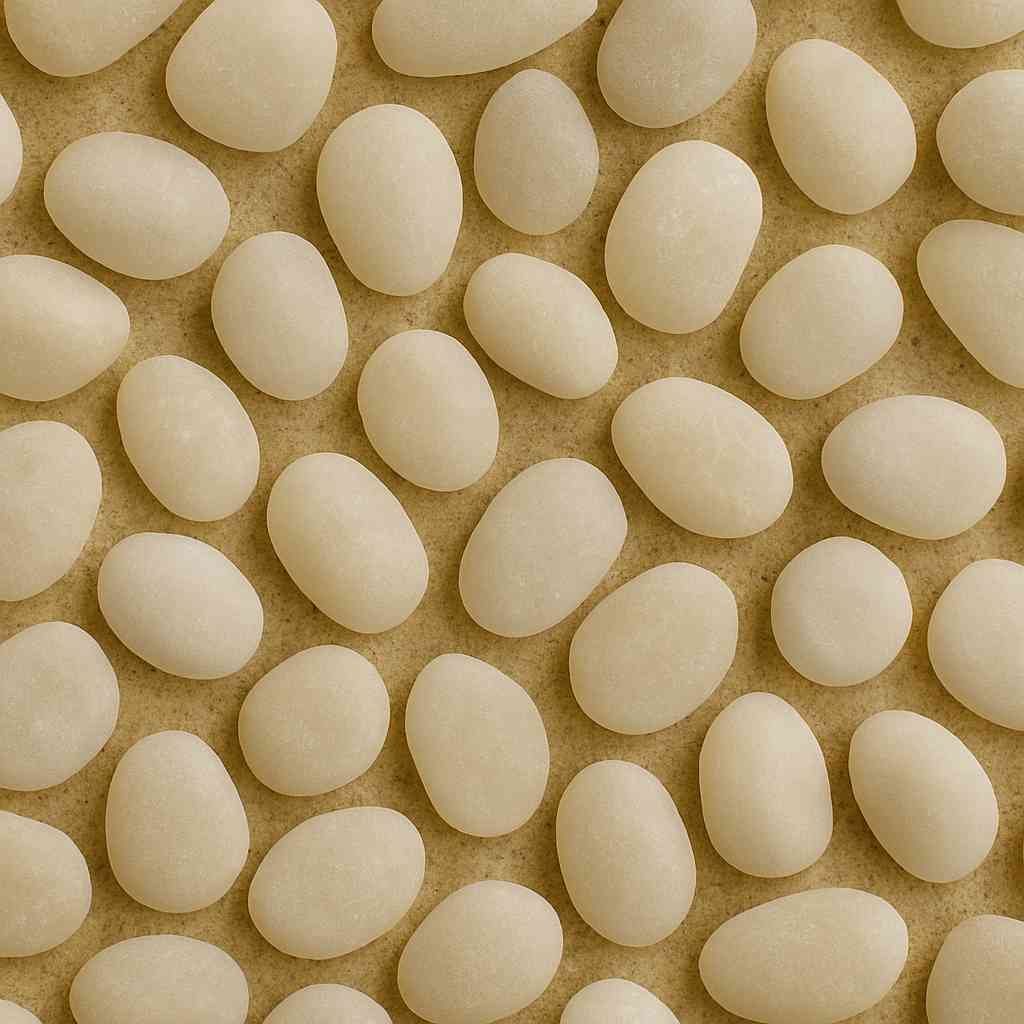
This image shows how uniform zircon grains look under a microscope, which helps ensure even tile coating.
How Does Zircon Sand Improve Tile Opacity?
Tile buyers, especially for high-end bathroom and kitchen projects, expect flawless color. Any patchy spots or faint lines lower the tile’s value fast. Zircon sand plays a big part in solving this headache because it controls how light behaves on the tile’s surface.
In simple terms, zircon grains act like millions of tiny reflectors inside the glaze. They scatter incoming light in many directions. This bounce effect hides small flaws, covers dark spots in the clay body, and keeps the top layer looking clean and bright. Even after years of use, tiles with proper zircon levels resist dulling.
Here’s something smart: Many factories use just enough zircon to hit their target whiteness without overspending. They test different sand grades and mixing ratios. This testing helps balance quality with cost.
Some low-cost fillers can look okay at first glance but fade under bathroom moisture or kitchen heat. When this happens, homeowners complain or ask for replacements. Using zircon protects a tile brand’s reputation and reduces these headaches.
Factor | Effect on Opacity |
---|---|
High reflectance | Bright, clean finish |
Consistent grain size | Smooth, even glaze |
High purity | No dark streaks |
A real case comes from a Spanish tile maker. They switched to a cheaper local opacifier to save money but soon saw customer complaints jump by 30%. Shifting back to premium zircon sand cut complaints overnight and won back big retail orders.
Factories also watch kiln settings carefully. Overheating can burn out zircon’s reflectivity. Technicians adjust firing curves to lock in the sand’s opacity power.
Keep this in mind: Opacity is more than just looks. Strong coverage hides tiny cracks or clay defects that could grow under wear and tear. Zircon builds a hidden safety net, keeping tiles beautiful and tough at the same time.
This balance of good looks and durability explains why procurement managers often refuse to gamble with untested substitutes. They stick with trusted zircon, knowing it keeps product returns low and buyers satisfied for years.turns low and buyers satisfied for years.
Why Is Zircon Sand Favored Over Other Opacifiers?
Many purchasing managers ask the same question: why not switch to a cheaper filler if it seems to do the same job? The answer hides in the details only production runs can reveal. Let’s break this down in plain terms.
Zircon sand keeps delivering steady results under different conditions. Other opacifiers like tin oxide add brightness but at a much higher cost per ton. Some clay-based fillers work for entry-level tiles yet struggle to hold color under daily wear. They might pass lab checks but fail after a few cleaning cycles in a busy kitchen or bathroom.
Think about this: Tiles get exposed to steam, soap, heat, and regular scrubbing. If the opacifier can’t handle these stresses, stains show up or the glaze loses shine. Zircon stands firm against heat and chemicals, which explains its popularity in both luxury and mass-market tiles.
Opacifier | Average Cost per Ton | Performance Consistency | Use Case |
---|---|---|---|
Zircon Sand | Medium | High | Standard and premium tiles |
Tin Oxide | High | Very High | Luxury finishes |
Local Clay Fillers | Low | Low to Medium | Budget tiles |
Another reason buyers stick with zircon is equipment safety. Some substitutes create lumps or react during firing, clogging spray guns and causing downtime. Cleaning clogged equipment or fixing ruined batches costs far more than paying a bit more for zircon up front.
Factories also like how easy it is to source zircon in large, steady quantities. Well-known mines and global shipping networks back up supply security. This helps planning teams avoid production gaps due to missing raw materials.
A real example comes from an Italian ceramics producer. They once tested a low-cost opacifier blend to cut expenses by 10%. But within three months, they lost two major hotel supply contracts because tiles showed blotchy surfaces. Switching back to zircon restored customer trust and locked in new orders.
Here’s what stands out: Reliability saves money in the long run. Procurement heads compare not just raw material cost but also hidden expenses—machine downtime, rework, refunds, and bad reviews. When viewed this way, zircon is often the safer bet for stable profit margins.
In short, zircon sand remains a favorite because it balances reasonable price, predictable performance, and easy processing. Substitutes may look attractive on paper but rarely match zircon’s total value when you run the numbers from mine to showroom floor. Smart buyers see the full picture and budget for consistency over risky shortcuts., not just material price. Factories lose more money handling returns than they gain from cheaper filler.
Where Is High-Quality Zircon Sand Sourced?
Supply chains for zircon sand stretch across continents, and sourcing plays a huge role in quality control. Not every mining region produces sand that meets tight ceramic standards, so procurement teams must stay sharp about where shipments originate.
Australia leads the pack for reliable zircon supply. Mines there produce some of the cleanest sand with low iron and steady grain size. Buyers love Australian zircon because it rarely needs extra refining. This cuts processing time and unexpected costs later.
South Africa also ranks high, with vast deposits and established exporters. However, the purity can vary more between mines compared to Australia. Buyers often request detailed lab tests before placing large orders. This step prevents receiving a batch with too much clay or moisture, which could ruin kilns.
Asian mines—mainly in Vietnam and Indonesia—supply many nearby tile makers. Local sourcing cuts transport time and import fees. But quality may fluctuate more widely. Smart buyers always vet these sources through site visits or trusted agents.
Here’s what experienced buyers do: They sign long-term contracts with well-known miners or brokers. This ensures a steady flow of sand even if global shipping runs into port delays or customs bottlenecks.
Major Source | Key Strength | Buyer Caution |
---|---|---|
Australia | Consistent high purity | Higher base cost |
South Africa | Large volumes | Variable mine grades |
Vietnam & Indonesia | Cost savings for local buyers | More quality checks needed |
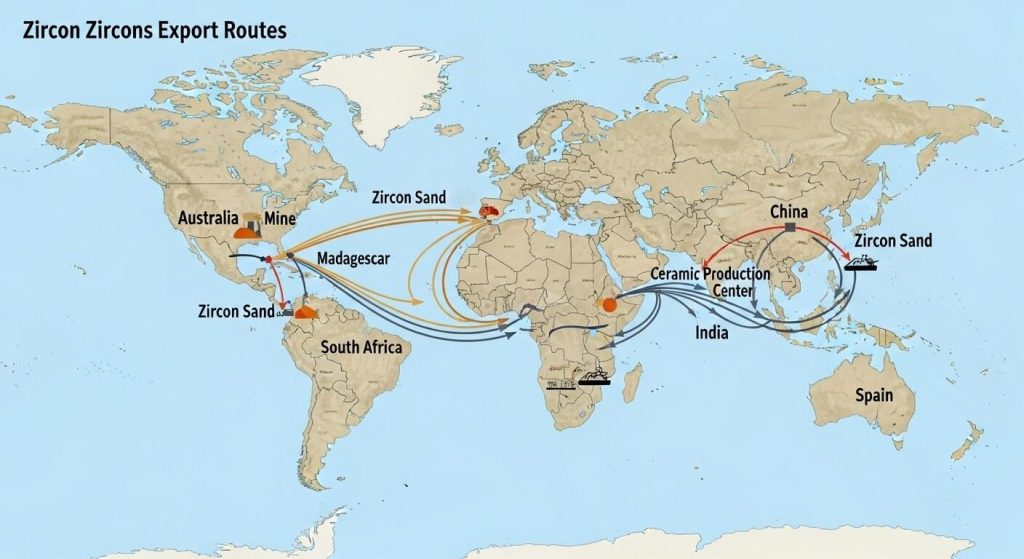
This map visualizes top export routes from leading zircon mining countries to major ceramic production hubs worldwide.
Another factor buyers consider is local regulation. Some countries tighten export rules when domestic industries need more sand. Unexpected bans or quota cuts can disrupt delivery schedules. Keeping backup sources on contract helps prevent sudden factory shutdowns.
Shipping time is another big deal. Zircon travels mostly by sea in bulk containers. A shipment from Australia to Europe can take six weeks or longer, depending on port traffic. Some buyers store buffer stock near ports or major plants to cover surprise spikes in orders.
Finally, professional buyers often request third-party inspection reports before paying the final invoice. This extra layer confirms that moisture, grain size, and chemical composition match contract terms.
In summary, sourcing isn’t just about picking the cheapest sand. It’s a balance of stable quality, fair price, and dependable shipping. Buyers who build strong supplier ties and diversify sources handle market swings better than those chasing one-off deals. Smart sourcing keeps production lines rolling and helps tile brands stay trusted in a crowded market.e iron or rutile contamination. This step prevents surprise color shifts on the final tile.
How Is Zircon Sand Processed for Tile Use?
Once miners pull zircon from the earth, raw sand must undergo careful steps before it ever touches a tile factory floor. Processing weeds out unwanted materials and readies the grains for smooth blending in glazes.
It starts with washing. Water jets remove surface clay and light dust, making the grains cleaner. Next, magnetic separators pull out iron bits. Iron can stain white tiles with ugly yellow or brown patches, so removing it early prevents costly rework later.
Grinding is another key stage. The sand passes through mills that crush lumps and grade particles by size. Different tile finishes need different sizes: fine grains for smooth glazes, coarser for rustic looks.
Here’s something smart: Some processors pre-dry the sand to low moisture levels. This stops steam bubbles from forming inside kilns, which can cause glaze pops or pinholes.
Step | Purpose | Result |
---|---|---|
Washing | Strip clay and dirt | Cleaner base sand |
Magnetic separation | Remove iron | No stain risk |
Grinding | Control grain size | Consistent texture |
Drying | Reduce moisture | Safe kiln firing |
Before shipping, quality labs test random batches. Reports show chemical content, grain size range, and moisture percentage. Buyers check these against order specs before paying full price. This tight quality loop keeps factory rejects low and production running smoothly.
What Are the Common Uses in Tile Manufacturing?
Zircon sand fits into more than just glaze. Its role spans from surface beauty to hidden structural support. For glazes, zircon adds brightness and covers imperfections on clay bodies. A light-reflective finish makes tiles pop on showroom walls and brightens living spaces.
Inside the tile body mix, zircon acts like a stabilizer. It helps raw clay hold shape during drying and firing. This cuts warping and lowers scrap rates.
Interesting point: Some plants run seasonal batches with special glaze recipes. High-end bathroom tiles might get extra zircon for a bright, crisp look, while rustic floor tiles use less for an earthy tone.
Application | Benefit |
---|---|
Glaze | Even, glossy surface |
Body | Shape control and durability |
Factories usually dose zircon by weight during batching. Technicians check flow rates to stop lumps forming in the mixing tanks. A little extra attention here saves hours of cleanup later.
How Do Tile Makers Handle Environmental Concerns?
Modern plants know buyers care about eco-standards. Even safe minerals like zircon need careful handling to protect workers and the environment.
Fine dust is the biggest worry. Inhaling too much can irritate lungs. So, plants use vacuum systems to capture airborne particles at every sanding or mixing stage. Workers wear masks and get training on safe work habits.
Waste glaze and slurry often contain leftover zircon. Instead of dumping it, many plants filter and reuse this sludge. This recycling cuts down fresh sand purchases and shrinks waste bills.
Measure | How It Helps |
---|---|
Dust filters | Cleaner air |
Masks and training | Safer staff |
Waste recycling | Fewer raw materials needed |
Certifications like ISO 14001 help buyers trust that plants run clean operations. Some big brands even audit suppliers yearly to confirm safety rules are met.
In the end, safe zircon use means lower health risks, happier staff, and a greener footprint—three wins that keep buyers and end-users confident in the final product.en highlight zircon recycling in audits. It proves commitment to cleaner production.
What Quality Standards Govern Zircon Sand Supply?
Buyers cannot take risks with poor-grade sand because a single bad shipment can halt production and cost thousands in wasted tiles. Quality standards help avoid such headaches by setting clear rules that suppliers must follow.
Most factories stick to international specs for zircon used in ceramics. Key factors include the percentage of zirconium silicate, iron content, moisture levels, and exact grain size. These numbers ensure each batch blends well and fires cleanly without defects.
One smart move: Many purchasing managers insist on getting a certificate of analysis with every shipment. This report confirms that the sand meets agreed benchmarks.
Parameter | Standard Range | Why It Matters |
---|---|---|
Zirconium silicate | 65%–66% | Reliable opacity |
Iron content | Below 0.1% | No discoloration |
Moisture | Under 0.5% | Safe kiln firing |
Grain size | Consistent microns | Smooth mixing |
Big brands sometimes hire third-party labs to test random containers on arrival. This extra step keeps suppliers honest and cuts disputes later. Good suppliers welcome spot checks because they build trust and long-term deals.
How Can Buyers Ensure Consistent Zircon Sand Supply?
Stable supply means smooth production and on-time delivery to tile retailers. Smart buyers do not rely on just one source, no matter how trustworthy.
A popular strategy is signing yearly or multi-year contracts with key miners or distributors. Locked-in volumes help protect against sudden price jumps or local export bans.
Here’s what experienced teams do: They also keep a safety stock at port warehouses. This backup covers urgent orders when ships get delayed or demand spikes.
Strategy | Benefit |
---|---|
Long-term contracts | Steady prices and priority supply |
Diversified sourcing | Less risk if one source fails |
On-hand buffer stock | Quick response to urgent orders |
Good communication with suppliers helps too. Buyers often share forecast data so miners can plan production and shipping in advance. This win-win approach cuts surprises and builds strong working relationships.
In short, stable zircon supply depends on good planning, clear contracts, and trusting partnerships. For buyers, this means fewer production hiccups and happy customers at the end of the line.
What Are Future Trends for Zircon in Tiles?
As urban housing grows, tile needs rise. Researchers keep testing ways to stretch zircon. Some glaze additives can reduce usage by 5–10% without hurting shine. Recycling gets more efficient too.
Tougher mining rules may push prices higher. Buyers who plan long-term keep cost jumps under control.
Factor | Possible Effect |
---|---|
New additives | Lower zircon use |
Better recycling | Less fresh sand needed |
Stricter mining laws | Higher supply costs |
Stay close with multiple suppliers and watch market reports.
Tile brands stick with zircon because it delivers reliable quality and keeps defect rates low. Smart sourcing keeps plants running and buyers happy.
Conclusion
Zircon sand continues to serve tile firms well by ensuring bright finishes, steady production, and minimal waste. Purchasing managers who know the right specs and secure trusted suppliers avoid costly surprises. Global Industry helps leading brands lock in top-grade zircon with steady delivery and expert advice. Contact Global Industry today to discuss your zircon sand plan and safeguard your next production run.
FAQ Section
Q1: Is zircon sand safe for factory workers?
Proper filters and training make zircon sand safe to handle daily. Regular checks cut dust risks.
Q2: Can recycled zircon be reused in new tiles?
Yes. Many plants filter and reuse zircon-rich glaze to control waste and cost.
Q3: Does the sand’s origin affect tile quality?
Definitely. Mines with higher purity give better shine and fewer glaze defects.
Q4: How do buyers test zircon sand before use?
Labs measure purity, grain spread, and moisture to match factory specs.
Q5: What trends may affect zircon prices soon?
Changes in mining permits and urban housing demand can shift prices. Many buyers plan bulk orders early.