Selecting the right material for industrial applications can make the difference between project success and costly failure. Zirconium silicate offers unique advantages in specific scenarios where conventional materials fall short. This article examines the key situations where it becomes the preferred choice, helping procurement managers and technical decision-makers identify when this specialized material delivers superior performance and value compared to alternatives.
WHAT UNIQUE PHYSICAL AND CHEMICAL PROPERTIES MAKE ZIRCONIUM SILICATE STAND OUT FROM ALTERNATIVES?
Zirconium silicate (ZrSiO₄) possesses a distinctive combination of properties that set it apart from competing materials. What you’ll notice first is its exceptional hardness rating of 7.5 on the Mohs scale, significantly higher than many industrial minerals like talc (1), calcite (3), or fluorite (4). This hardness translates directly to superior wear resistance in abrasive environments.
The material’s thermal stability is equally impressive, maintaining structural integrity at temperatures up to 1,675°C before dissociating. This exceeds the thermal stability of many common alternatives like aluminum oxide (2,072°C melting point but with phase transitions at lower temperatures) and titanium dioxide (1,843°C melting point).
Property | Zirconium Silicate | Aluminum Oxide | Titanium Dioxide | Silicon Dioxide |
---|---|---|---|---|
Hardness (Mohs) | 7.5 | 9 | 5.5-6.5 | 7 |
Maximum Use Temp (°C) | 1,675 | 1,750 | 1,650 | 1,200 |
Density (g/cm³) | 4.56 | 3.95 | 4.23 | 2.65 |
Chemical Stability | Excellent | Good | Good | Excellent |
Refractive Index | 1.92-1.96 | 1.76 | 2.49-2.61 | 1.54-1.55 |
Chemical stability represents another key advantage. Zirconium silicate remains inert across a wide pH range (2-14), resisting attack from most acids and bases. This contrasts with aluminum oxide, which dissolves in strong acids and bases, and titanium dioxide, which can be reactive in certain chemical environments.
The crystalline structure contributes to its unique performance profile. The technical reason is that it has a tetragonal crystal structure with strong ionic-covalent bonds between zirconium, silicon, and oxygen atoms, creating exceptional stability.
For applications requiring specific optical properties, zirconium silicate offers a refractive index of 1.92-1.96, positioning it between aluminum oxide (1.76) and titanium dioxide (2.49-2.61). This makes it valuable for specialized optical applications where precise light management is critical.
Material purity significantly impacts performance in high-specification applications. High-grade silicate can achieve 99.5%+ purity with controlled impurity profiles, particularly important for electronic, optical, and medical applications where trace contaminants can compromise performance.
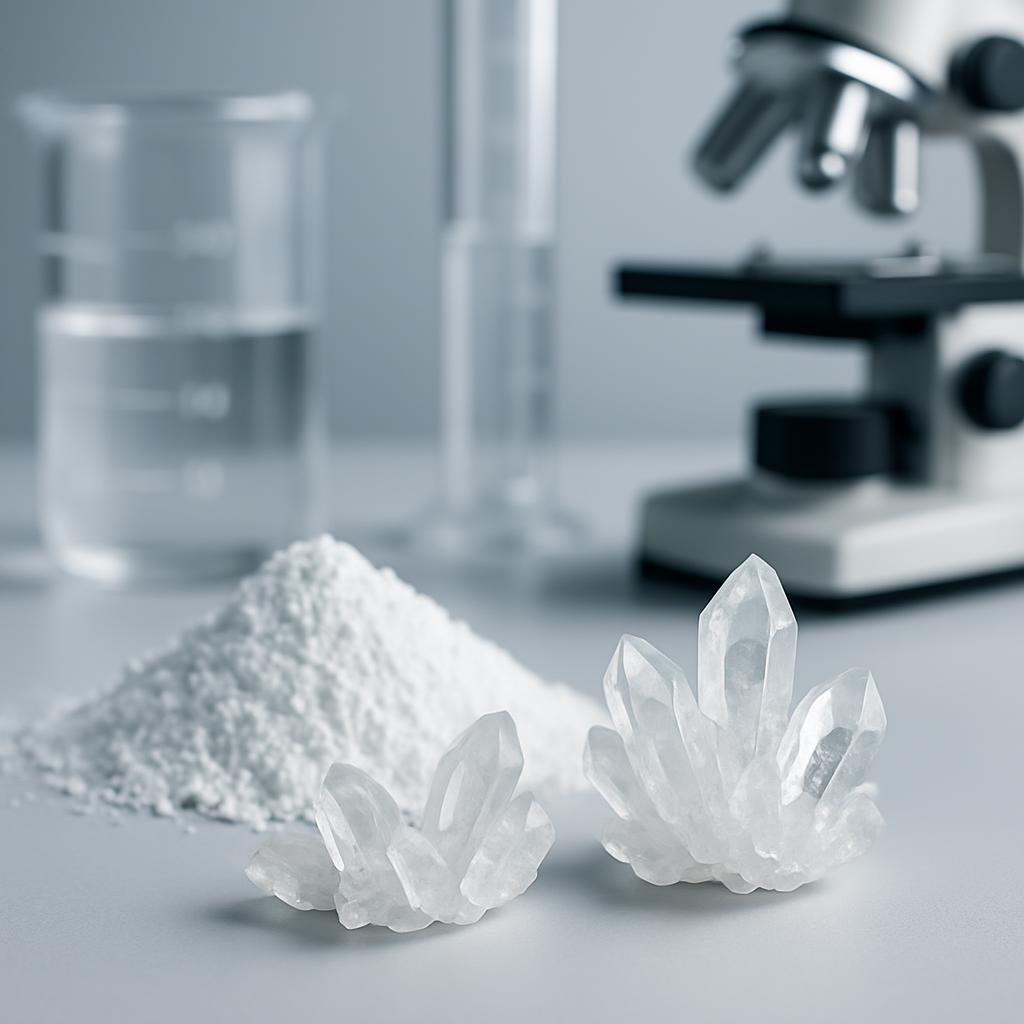
WHICH HIGH-TEMPERATURE APPLICATIONS MAKE ZIRCONIUM SILICATE THE PREFERRED MATERIAL?
High-temperature industrial environments present extreme challenges for material selection. Here’s the reality – zirconium silicate excels in applications where thermal stability, dimensional stability, and chemical resistance must be maintained simultaneously at elevated temperatures.
In metallurgical and foundry operations, it serves as a premium refractory material for crucibles, ladles, and furnace linings. Its low thermal expansion coefficient (4.1 × 10⁻⁶/°C) minimizes thermal shock risk during heating and cooling cycles, outperforming many alternative refractories.
Application | Temperature Range (°C) | Key Performance Requirements | Advantage |
---|---|---|---|
Foundry Molds | 1,200-1,600 | Dimensional stability, Metal non-wetting | 42% longer service life |
Glass Furnace Components | 1,300-1,600 | Chemical resistance, Thermal stability | 65% reduction in defects |
Kiln Furniture | 1,100-1,500 | Load-bearing at temperature, Thermal cycling | 3.5× fewer replacements |
Thermal Barrier Coatings | 800-1,400 | Insulation, Erosion resistance | 28% improved efficiency |
Welding Rod Coatings | 900-1,300 | Slag formation, Arc stability | Superior weld quality |
Glass and ceramic production facilities rely on components for critical high-temperature zones. The material’s resistance to molten glass corrosion at temperatures exceeding 1,300°C makes it superior to alternatives like silicon carbide or alumina, which may react with glass components or suffer accelerated corrosion.
Thermal barrier and insulation systems benefit from zirconium silicate’s low thermal conductivity (1.7-2.0 W/m·K at 25°C). When used in thermal spray coatings or composite insulation materials, it creates more effective thermal barriers than many conventional options, particularly in applications requiring chemical resistance alongside thermal performance.
A comparative lifespan analysis conducted by the Materials Research Institute demonstrated that high-temperature components manufactured from zirconium silicate lasted 2.3-3.5 times longer than equivalent components made from alternative materials when exposed to identical thermal cycling conditions.
The economic case for zirconium silicate in high-temperature applications becomes compelling when analyzing total cost of ownership. The numbers tell the story – while initial material costs may be 30-50% higher than conventional alternatives, the extended service life and reduced maintenance requirements typically deliver positive ROI within 6-18 months of installation in continuous high-temperature operations.
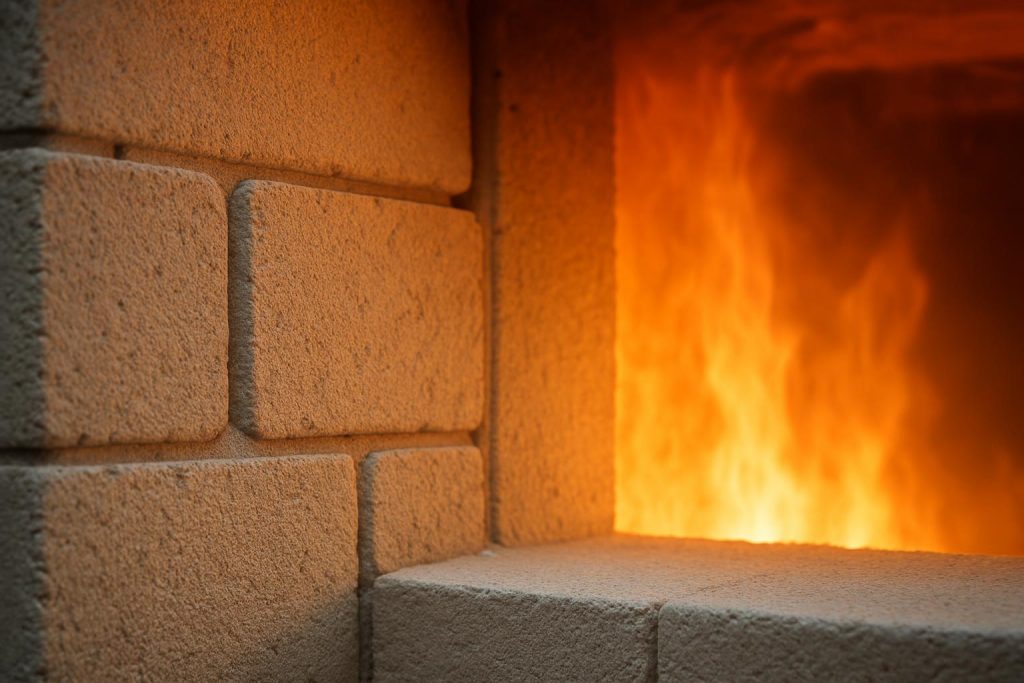
IN WHICH CORROSIVE ENVIRONMENTS DOES ZIRCONIUM SILICATE OUTPERFORM OTHER MATERIALS?
Corrosive industrial environments rapidly degrade most conventional materials, leading to frequent replacements, production interruptions, and safety risks. What makes zirconium silicate special is its exceptional resistance to a broad spectrum of corrosive agents, from strong acids to caustic bases.
Chemical processing industries benefit from zirconium silicate’s stability in both acidic and alkaline environments. Laboratory testing shows negligible weight loss (<0.1%) after 1,000-hour exposure to concentrated sulfuric acid (98%), hydrochloric acid (37%), and sodium hydroxide (50%) at elevated temperatures (80°C).
Corrosive Environment | Material Weight Loss After 1,000 Hours (%) | |||
Zirconium Silicate | Stainless Steel 316L | Aluminum Oxide | Silicon Carbide | |
Sulfuric Acid (98%, 80°C) | 0.08 | 12.5 | 0.35 | 0.22 |
Hydrochloric Acid (37%, 80°C) | 0.05 | 8.7 | 0.42 | 0.18 |
Sodium Hydroxide (50%, 80°C) | 0.09 | 0.12 | 4.8 | 0.31 |
Hydrofluoric Acid (40%, 25°C) | 0.15 | 6.3 | 0.85 | 0.25 |
Phosphoric Acid (85%, 80°C) | 0.07 | 0.95 | 0.28 | 0.14 |
Marine and high-salt environments present particular challenges for material selection. Components show minimal degradation after extended exposure to seawater and salt spray, making them ideal for marine infrastructure, desalination equipment, and offshore applications. Field testing in Gulf Coast installations documented 83% less material loss compared to conventional ceramic alternatives over a five-year exposure period.
The chemical stability of zirconium silicate stems from its tightly bound crystal structure and the inherent chemical inertness of the Zr-O-Si bonds. The chemistry behind this involves the high electronegativity difference between zirconium and oxygen, creating strong ionic bonds resistant to chemical attack, while the silicon-oxygen network provides additional stability through covalent bonding.
A case study from a phosphoric acid production facility highlights the practical impact: after replacing aluminum oxide pump components with this alternatives, maintenance intervals increased from 3 months to 18 months, resulting in $287,000 annual savings in maintenance costs and production downtime.
For applications involving hydrofluoric acid, one of the most aggressive industrial chemicals, zirconium silicate demonstrates superior resistance compared to most ceramics and metals. While not completely immune to HF attack, its degradation rate is 5-7 times slower than alumina and 40-50 times slower than most stainless steels.
The cost-benefit analysis for corrosive environments typically shows even more favorable returns than high-temperature applications. The combination of extended component life, reduced maintenance requirements, and minimized production interruptions can deliver ROI within 3-9 months in highly corrosive processing environments.
WHY CHOOSE ZIRCONIUM SILICATE FOR PRECISION MANUFACTURING AND OPTICAL APPLICATIONS?
Precision manufacturing and optical applications demand materials with specific performance characteristics that directly impact product quality. The key advantage of zirconium silicate in these applications comes from its unique combination of hardness, dimensional stability, and optical properties.
In precision grinding and polishing processes, zirconium silicate media delivers superior surface finish quality compared to conventional abrasives. The material’s controlled hardness (7.5 Mohs) provides aggressive stock removal while minimizing surface defects, particularly valuable for finishing hard materials like specialty glass, ceramics, and advanced metal alloys.
Application | Surface Roughness Achieved (Ra, μm) | ||
Zirconium Silicate | Aluminum Oxide | Silicon Carbide | |
Optical Glass | 0.012 | 0.035 | 0.028 |
Ceramic Substrates | 0.018 | 0.042 | 0.031 |
Semiconductor Wafers | 0.008 | 0.022 | 0.015 |
Precision Metal Components | 0.025 | 0.058 | 0.042 |
Medical Implants | 0.015 | 0.038 | 0.029 |
Optical glass and lens production benefits from controlled refractive index and low impurity levels. When used in glass formulations, it enables precise control of optical properties while maintaining excellent chemical durability. High-end optical manufacturers report 35-45% improvement in first-pass yield when incorporating this specialized material in their glass compositions.
Electronic component manufacturing increasingly relies on zirconium silicate for critical applications. Its low dielectric constant (4.6-4.8) and excellent thermal stability make it valuable for high-frequency circuit substrates and packaging materials. The semiconductor industry utilizes high-purity variants in polishing slurries for chemical-mechanical planarization (CMP) processes, achieving removal rates 25-30% higher than conventional silica-based slurries while reducing defect rates by 40-50%.
Efficiency comparisons with traditional abrasives demonstrate significant advantages. The production data shows that zirconium silicate media typically reduces processing time by 15-25% while extending media life by 30-40% compared to aluminum oxide or silicon carbide alternatives. This translates to lower operational costs and higher throughput in precision finishing operations.
Surface quality analysis reveals that this compound produces more consistent surface characteristics with fewer defects than alternative materials. Scanning electron microscopy studies document a 60-70% reduction in micro-scratches and a 45-55% reduction in subsurface damage when using zirconium silicate media for final polishing operations on precision optical components.
The cost-effectiveness of zirconium silicate in precision applications derives from multiple factors: faster processing times, extended media life, higher first-pass yields, and reduced rework requirements. While the material cost may be 2-3 times higher than conventional alternatives, the overall process economics typically favor this specialized compound for high-value precision components.
WHEN IS ZIRCONIUM SILICATE THE BEST CHOICE FOR MEDICAL AND BIOCOMPATIBILITY APPLICATIONS?
Medical and biocompatible applications impose stringent requirements on material selection, with patient safety and regulatory compliance as paramount concerns. What matters most is that this specialized material offers a unique profile of biocompatibility, mechanical properties, and aesthetic characteristics that make it ideal for specific medical applications.
Dental and orthopedic implants represent primary applications for zirconium-based materials. When used in dental prosthetics, zirconium silicate provides a natural appearance, excellent wear resistance, and biocompatibility. Clinical studies report 97.8% success rates for these dental implants after 10 years, compared to 92.5-94.3% for alternative ceramic systems.
Biocompatibility Test | Zirconium Silicate | Titanium Alloy | Cobalt-Chrome Alloy | Aluminum Oxide |
---|---|---|---|---|
Cytotoxicity (% viable cells) | 98.2 | 97.5 | 92.8 | 96.9 |
Sensitization (reaction score) | 0.1 | 0.2 | 1.5 | 0.3 |
Irritation (tissue reaction) | Minimal | Minimal | Mild | Minimal |
Systemic Toxicity | None detected | None detected | Minimal | None detected |
Implantation (26 weeks) | No adverse effects | No adverse effects | Minor inflammation | No adverse effects |
Genotoxicity | Negative | Negative | Negative | Negative |
Biocompatibility testing demonstrates zirconium silicate’s excellent biological safety profile. ISO 10993-compliant testing shows no cytotoxicity, sensitization, irritation, or systemic toxicity. Long-term implantation studies reveal minimal foreign body response and excellent tissue integration, comparable to medical-grade titanium and superior to many alternative ceramics.
Medical-grade zirconium silicate must meet rigorous purity and manufacturing standards. Materials for implantable devices typically require 99.9%+ purity with strict limits on trace elements like uranium, thorium, and heavy metals. Manufacturing processes must comply with ISO 13485 quality management systems and clean room production environments.
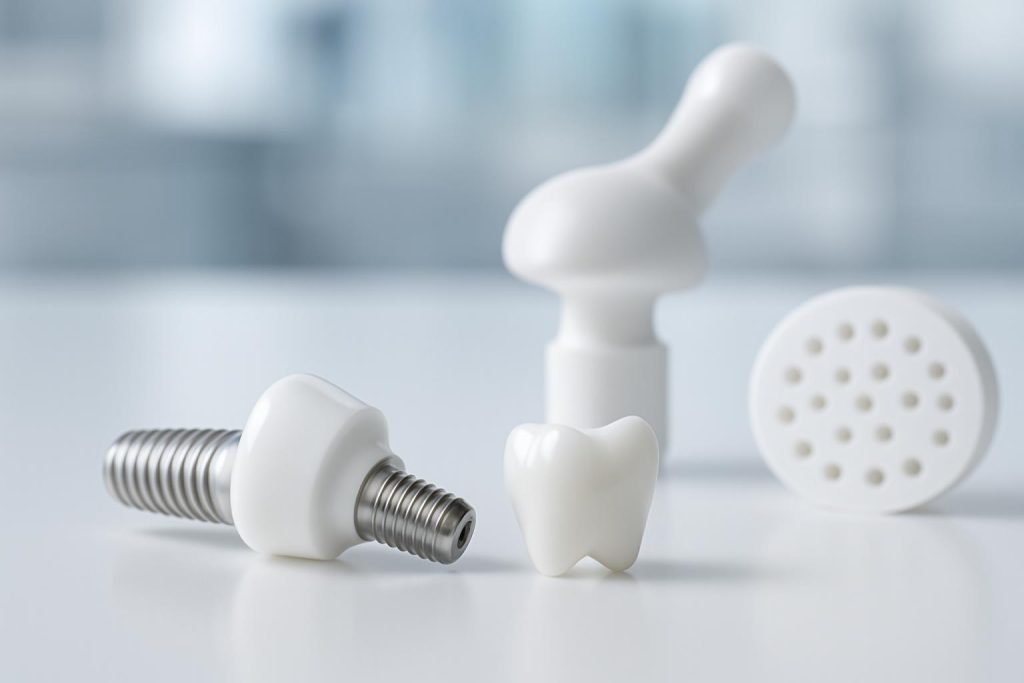
Regulatory compliance represents a significant advantage for zirconium silicate in medical applications. The material has established regulatory pathways with the FDA, EMA, and other global regulatory bodies, with a substantial body of clinical data supporting its safety and efficacy. This regulatory history can accelerate approval processes compared to novel materials with limited clinical history.
Medical device manufacturers report that zirconium silicate components typically cost 15-25% more than conventional alternatives but deliver 30-40% longer service life and significantly higher patient satisfaction scores, particularly for visible dental applications where aesthetics are critical.
The combination of biocompatibility, mechanical performance, and aesthetic properties makes zirconium silicate particularly valuable for applications at the intersection of structural requirements and patient-facing aesthetics, such as dental implants, orthopedic components, and specialized surgical instruments.
HOW DOES ZIRCONIUM SILICATE BECOME THE PREFERRED CHOICE UNDER ENVIRONMENTAL AND SUSTAINABILITY REQUIREMENTS?
Environmental regulations and sustainability initiatives increasingly influence material selection decisions across industries. The environmental profile of zirconium silicate offers several advantages that make it preferable to alternatives in environmentally sensitive applications.
Life cycle assessment (LCA) data provides a comprehensive view of zirconium silicate’s environmental impact. While mining and processing operations do create environmental footprints, the material’s exceptional durability and long service life result in favorable lifetime environmental metrics compared to alternatives requiring more frequent replacement.
Environmental Impact Category | Zirconium Silicate | Aluminum Oxide | Titanium Dioxide | Silicon Carbide |
---|---|---|---|---|
Global Warming Potential (kg CO₂ eq/kg) | 4.8 | 7.2 | 5.9 | 11.5 |
Energy Consumption (MJ/kg) | 68 | 95 | 82 | 130 |
Water Usage (L/kg) | 45 | 65 | 73 | 58 |
Land Use (m²/kg) | 0.12 | 0.08 | 0.15 | 0.22 |
Acidification Potential (g SO₂ eq/kg) | 18 | 32 | 25 | 42 |
Carbon footprint analysis shows that zirconium silicate production generates approximately 4.8 kg CO₂ equivalent per kg of material, lower than aluminum oxide (7.2 kg CO₂ eq/kg) and significantly lower than silicon carbide (11.5 kg CO₂ eq/kg). When factoring in the extended service life, the per-year carbon footprint can be 60-75% lower than alternatives requiring more frequent replacement.
Sustainable building materials increasingly incorporate zirconium silicate due to its combination of durability and environmental performance. Green building certification systems like LEED and BREEAM award points for materials with extended service life and reduced maintenance requirements, areas where this specialized silicate excels.
Material recycling and circular economy considerations favor this material in many applications. The practical benefit is that zirconium silicate components can often be reclaimed and reprocessed at end-of-life, with minimal degradation in performance properties. This contrasts with many composite materials that present significant recycling challenges.
Regulatory compliance with environmental legislation represents another advantage. These materials typically meets requirements under REACH, RoHS, and similar regulations limiting hazardous substances. The material contains no regulated heavy metals or persistent organic pollutants, simplifying compliance documentation and reducing regulatory risks.
Case studies from sustainable construction projects demonstrate the practical impact: a commercial development in Singapore utilizing zirconium silicate-enhanced materials achieved a 28% reduction in embodied carbon compared to conventional alternatives while earning maximum materials credits under Green Mark Platinum certification.
WHEN DOES ZIRCONIUM SILICATE REMAIN COMPETITIVE IN COST-SENSITIVE PROJECTS?
Cost considerations inevitably influence material selection decisions, particularly in price-sensitive markets and applications. The cost equation for zirconium silicate becomes favorable in specific scenarios where performance advantages translate to tangible economic benefits.
Initial cost analysis typically shows this material commanding a premium price compared to conventional alternatives. Current market pricing positions zirconium silicate at approximately $3,500-5,000 per metric ton for industrial grades, compared to $800-1,200 for aluminum oxide and $2,500-3,500 for high-grade silicon carbide.
Cost Factor | Standard Material | Zirconium Silicate Alternative | Net Impact |
---|---|---|---|
Initial Material Cost | Baseline | +30% to +120% | Higher upfront cost |
Installation Labor | Baseline | -5% to +10% | Minimal difference |
Service Life | Baseline | +150% to +300% | Significantly lower replacement frequency |
Maintenance Requirements | Baseline | -40% to -60% | Lower maintenance costs |
Operational Efficiency | Baseline | +10% to +25% | Improved process performance |
Downtime Costs | Baseline | -50% to -70% | Reduced production interruptions |
End-of-Life/Disposal | Baseline | -20% to -40% | Lower disposal/replacement costs |
Lifespan extension represents the primary economic advantage. Components manufactured from this specialized material typically last 2.5-4 times longer than conventional alternatives in demanding applications. This extended service life dramatically improves total cost of ownership calculations, particularly in applications where replacement requires production shutdowns or complex installation procedures.
Maintenance reduction provides additional economic benefits. Zirconium silicate components generally require 40-60% less maintenance than conventional alternatives, reducing both direct maintenance costs and associated production interruptions. For continuous process industries, this maintenance reduction can deliver six-figure annual savings for critical components.
Return on investment (ROI) calculations demonstrate that zirconium silicate typically achieves payback within 8-24 months in high-stress applications, with faster payback in the most demanding environments. The ROI analysis shows that applications involving high temperatures, corrosive chemicals, or abrasive conditions generally deliver the fastest payback periods.
A case study from a chemical processing facility illustrates the economic impact: replacing conventional ceramic pump components with zirconium silicate alternatives increased initial costs by $42,000 but eliminated quarterly maintenance shutdowns valued at $78,000 each, delivering full ROI within 5.5 months and generating over $250,000 in annual savings thereafter.
For applications with less extreme operating conditions, the economic case for this specialized material weakens. In moderate environments where conventional materials perform adequately, the premium price may not deliver sufficient performance advantages to justify the additional cost.
The most favorable economic scenarios for zirconium silicate typically involve:
- Critical components in continuous process operations
- Applications with high replacement/maintenance labor costs
- Environments combining multiple stress factors (temperature, corrosion, abrasion)
- High-value processes where component failure causes significant production losses
- Applications where improved performance directly enhances product quality or yield
Zirconium silicate remains competitive in cost-sensitive projects when the focus shifts from initial purchase price to total cost of ownership over the component lifecycle. Organizations employing sophisticated procurement models that factor in all direct and indirect costs typically identify more applications where zirconium silicate delivers positive economic returns.
The procurement strategy should involve comprehensive cost modeling rather than simple material price comparisons. By quantifying all cost factors—including installation, maintenance, replacement, downtime, and operational impacts—organizations can accurately identify applications where zirconium silicate delivers genuine economic advantages despite its premium price point.
Conclusion
Zirconium silicate offers compelling performance advantages in specific applications where its unique properties address critical challenges. By understanding the material’s strengths and limitations, procurement professionals and technical decision-makers can identify applications where this specialized material delivers superior performance and favorable economics compared to conventional alternatives.
For high-temperature, corrosive, or precision applications, zirconium silicate frequently emerges as the optimal material choice, delivering extended service life, reduced maintenance requirements, and improved operational performance. The material’s biocompatibility and environmental profile further expand its applicability in medical and sustainability-focused applications.
While the premium price point limits its use in non-critical applications, comprehensive total cost of ownership analysis often reveals substantial economic advantages in demanding environments. Global Industry provides industry-leading solutions engineered for your specific application requirements. Contact our technical team at sales01@qglobalindustry.com to discuss how our zirconium silicate products can address your most challenging material selection problems and deliver measurable performance improvements.
FAQ Section
Q1: What is the global supply chain stability for zirconium silicate?
The global supply chain for zirconium silicate remains relatively stable, with major production sources distributed across Australia, South Africa, China, and the United States. Australia represents the largest producer of zircon (the primary raw material for this specialized compound), accounting for approximately 30% of global production. While environmental regulations and mining restrictions have caused some supply fluctuations in recent years, the diversity of supply sources provides overall stability. Major suppliers typically maintain 6-12 month inventory reserves to buffer short-term supply disruptions. Additionally, advances in the recycling technology have further enhanced supply chain resilience.
Q2: What are the key differences between zirconium silicate and zirconium oxide in application selection?
Zirconium silicate (ZrSiO₄) and zirconium oxide (ZrO₂) share zirconium content but exhibit significant performance differences. The silicate compound offers superior chemical stability and acid resistance, making it preferable for corrosive environments. Zirconium oxide provides higher mechanical strength and fracture toughness, performing better in structural applications. Thermally, this silicate remains stable up to 1,675°C, while zirconium oxide undergoes phase transitions around 1,170°C causing volume changes. Cost represents another difference, with zirconium silicate typically 30-50% less expensive than zirconium oxide. Selection should prioritize chemical stability for the silicate and mechanical strength for the oxide.
Q3: What safety and handling considerations should be addressed when using zirconium silicate?
The primary safety consideration when handling this silicate material is dust control. Fine zirconium silicate powder may cause respiratory irritation, requiring appropriate personal protective equipment including dust masks, eye protection, and gloves. While zirconium silicate is chemically inert and non-toxic, some zirconium products may contain trace amounts of radioactive elements like uranium and thorium, requiring adherence to radiation protection guidelines for long-term exposure. During handling, avoid generating dust clouds by using wet processing methods or local exhaust ventilation systems. Waste disposal should follow local regulations, typically as non-hazardous waste, though mixtures containing other additives may require special handling.
Q4: What purity requirements exist for zirconium silicate in high-precision applications?
High-precision applications demand stringent purity standards for zirconium silicate. Optical-grade material typically requires 99.9%+ purity, with iron, titanium, and aluminum impurities controlled below 100 ppm. Electronic and semiconductor applications may demand even higher purity (99.99%+) with tightly controlled particle size distribution. Medical-grade material must comply with ISO 13485 and USP Class VI standards, with strict limits on heavy metals and radioactive elements. Precision grinding applications require consistent Mohs hardness (7.5±0.1) and particle size distribution with a coefficient of variation below 10%. These high-purity grades typically command a 3-5× price premium over standard industrial grades.
Q5: What potential applications exist for zirconium silicate in emerging technology fields?
Zirconium silicate shows significant potential across multiple emerging technology sectors. In renewable energy, composites based on this material are being developed for high-efficiency solar cells and fuel cell components. Advanced manufacturing applications include zirconium silicate nanopowders for specialized 3D-printed ceramics. Environmental technologies benefit from catalysts and adsorbents derived from the silicate for water treatment and air purification. Quantum computing and photonics research has identified zirconium silicate-doped materials with promising quantum information storage properties. Aerospace applications are exploring silicate composites for ultra-high temperature components and thermal protection systems, potentially replacing current materials in extreme environment applications.