In the procurement of zircon powder, knowing which supplier certification standards are trustworthy is vital for businesses. Purchasing managers need to ensure they are working with reliable suppliers to avoid risks associated with quality and compliance. This article addresses the concerns surrounding supplier certification by providing a detailed overview of the most relevant standards in the industry. By equipping you with the knowledge to evaluate supplier certifications effectively, we aim to help organizations make informed decisions, thereby building stronger and more productive supply chains.
What Are Supplier Certification Standards for Zircon?
Supplier certification standards represent the requirements that a supplier must meet to demonstrate their competence and compliance with industry regulations. They are crucial in ensuring product quality and maintaining consistency throughout the supply chain. In zircon procurement, these standards help businesses identify capable suppliers who can deliver the necessary quality reliably.
Certification standards can vary significantly between industries and products. Common standards in zircon procurement often include internationally recognized frameworks like ISO 9001, which addresses quality management systems, and ISO 14001, which focuses on environmental management. These frameworks set the baseline requirements for a supplier’s operations and processes, establishing a trusted foundation for purchasing decisions.
Understanding these standards not only improves supplier selection but also helps mitigate potential risks. Companies can foster a culture of compliance by prioritizing suppliers with established certifications. Overall, recognizing the significance of supplier certification standards in zircon mining and processing can lead to a more effective procurement strategy and ultimately, better quality zircon powder for various applications.
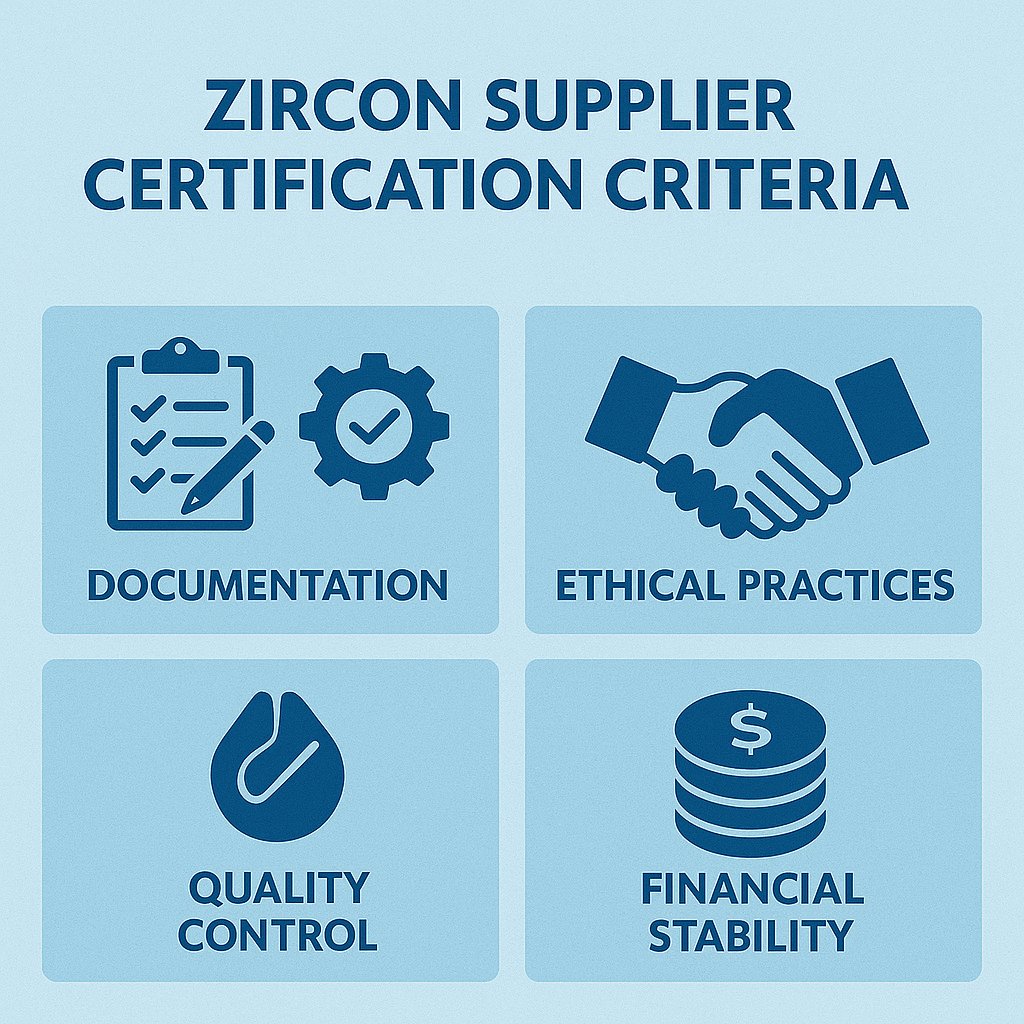
Visual representation of supplier certification standards demonstrating essential requirements for supplier evaluation.
Why Do Supplier Certifications Matter in Zircon Procurement?
Supplier certifications play an essential role in the procurement of zircon for several reasons. Firstly, they provide quality assurance, helping organizations reduce the risks associated with substandard materials. They serve as a commitment to maintaining high standards, showing that a supplier meets recognized benchmarks for quality and safety.
Additionally, certified suppliers help enhance trust in supplier relationships. When a business partners with certified suppliers, it indicates a dedication to quality and ethical practices, reinforcing the credibility of both parties. Trust is particularly vital in B2B transactions, where the stakes are often high and lasting partnerships are critical for success.
Furthermore, supplier certifications contribute to increased supply chain transparency. By ensuring that suppliers adhere to established standards, organizations can better monitor their supply chains. This transparency allows for more effective problem identification and resolution, promoting continuous improvement across all aspects of procurement.
By choosing certified suppliers, businesses not only safeguard their interests but also streamline their procurement processes, resulting in more efficient operations overall.
Key Benefits of Supplier Certifications
- Quality Assurance: Reduces risks linked to product quality.
- Increased Trust: Enhances relationships among stakeholders.
- Transparency: Promotes clearer monitoring of supply chains.
In today’s competitive market, making informed decisions regarding supplier certifications is essential for achieving sustained success.
How Are Zircon Supplier Certifications Evaluated?
Evaluating zircon supplier certifications is not merely a matter of checking a list. It involves a comprehensive review process to ensure that each potential supplier meets necessary criteria. Several key elements go into the evaluation of these certifications.
Firstly, understanding the criteria used to assess certifications is paramount. This includes the scope of the certification, duration, and the accrediting body responsible for the certification. It’s vital that companies inquire about how certifications are maintained. Regular audits are often required to ensure ongoing compliance.
Third-party accreditation bodies also play a significant role in this evaluation. These organizations conduct assessments and grant certifications to suppliers who meet their standards. Working with reliable accreditation entities is crucial, as they establish credibility and attention to detail in the certification process.
Various methodologies are used in these assessments, such as on-site evaluations, documentation reviews, and supplier self-assessments. Each method adds a layer of rigor to the evaluation process, ensuring that only the most competent suppliers are selected.
In summary, evaluating zircon supplier certifications requires diligence and a multi-faceted approach to guarantee that suppliers deliver what they promise.
Which Certifications Are Most Recognized in Zircon Procurement?
In the landscape of zircon procurement, several certifications stand out as being particularly relevant and trusted. Understanding these certifications is critical for effective supplier selection.
● ISO 9001 is a universally recognized standard for quality management systems. It ensures that suppliers have the necessary processes to consistently deliver high-quality products. For suppliers working with zircon, this certification offers assurance that they adhere to stringent quality controls.
● ISO 14001 focuses on environmental management, which is especially relevant for industries dealing with mining and minerals. It ensures that suppliers are committed to minimizing their environmental impact and properly managing ecological resources. Given the growing emphasis on sustainability, this certification can be a deciding factor in supplier selection.
Other industry-specific certifications are also notable. For example, the Responsible Minerals Initiative (RMI) addresses sourcing problems and promotes responsible supply chain practices. Suppliers who participate in RMI demonstrate a commitment to ethical sourcing, which can be a significant consideration for many companies.
Here is a summary table of recognized certifications:
Certification | Focus Area | Significance |
---|---|---|
ISO 9001 | Quality Management | Consistency and quality assurance |
ISO 14001 | Environmental Management | Sustainability and resource management |
RMI | Ethical Sourcing | Commitment to responsible practices |
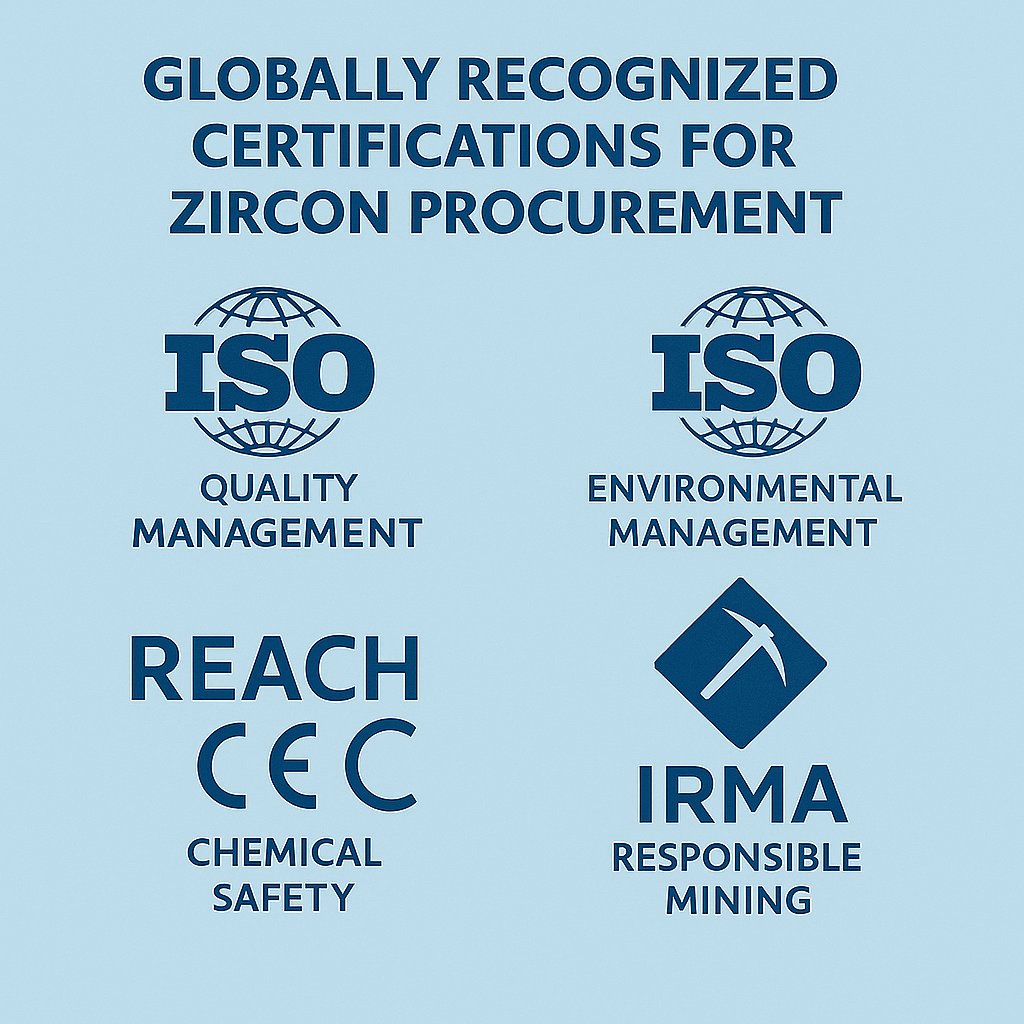
Illustration showcasing globally recognized certifications relevant to zircon procurement, emphasizing quality and sustainability.
These certifications not only enhance supplier credibility but also support businesses in forging partnerships founded on shared values.
What Challenges Exist with Supplier Certification Standards?
Despite the advantages of supplier certifications, challenges often arise that can complicate the procurement process. A common barrier is the inconsistent application of certification standards. Different regions or industries may adhere to varying regulations, which can create confusion for purchasing managers.
Misinterpretations of what certifications represent can lead to complications as well. A certification might imply a certain level of quality, but the reality may differ based on how strictly the supplier adheres to the standards. Hence, due diligence is vital when evaluating potential partners.
Regional variations in regulations can also impact suppliers’ certification processes. Some suppliers may not meet the expectations for certification due to local laws or standards that differ significantly from international norms. This discrepancy can lead to complications in meeting corporate compliance objectives.
Recognizing these challenges is critical for purchasing managers. Solutions may involve implementing rigorous vetting processes, providing training for procurement teams, or even investing in more reliable verification tools to assess supplier claims.
To summarize, while supplier certifications are valuable, decision-makers must remain vigilant to navigate the challenges that may arise during procurement.
How Can Companies Verify Supplier Certifications?
Verifying supplier certifications is a crucial step in ensuring that businesses partner with reliable vendors. The verification process should consist of several key steps for satisfactory results.
- Conduct Regular Audits: Assess suppliers to ensure compliance with the required standards.
- Require Documentation: Obtain relevant documentation, including certificates and audit reports.
- Utilize Third-party Services: Verify certifications against accredited registries through professional services.
Incorporating these steps ensures a thorough verification process, strengthening supplier relationships.
Here’s a checklist to streamline the verification process:
Verification Steps | Description |
---|---|
Conduct Regular Audits | Evaluate supplier operations against stated standards. |
Require Documentation | Obtain certifications, audit reports, and maintenance records. |
Utilize Third-party Services | Check supplier certifications against accredited registries. |
By implementing these practices, businesses can ensure strong supplier relationships built on verification and trust.
What Role Does Technology Play in Certification Processes?
Technology is essential in modern procurement strategies, including the management of supplier certifications. The integration of software solutions can significantly streamline these processes.
For instance, e-sourcing platforms can automate many aspects of supplier management. These platforms allow companies to track certifications, manage supplier information, and maintain comprehensive databases of supplier performance. Automating these tasks can lead to improved accuracy and reduced administrative workload.
Furthermore, technology assists in maintaining accurate records. Advanced systems can help businesses store and categorize certification data, making it easy to retrieve information whenever necessary. This enhanced accessibility simplifies the verification process and ensures compliance with internal standards.
Emerging technologies are reshaping certification processes as well. For example, blockchain technology offers a transparent way to document and verify certifications. By using blockchain, businesses can ensure certificates are tamper-proof and easily traced back to their source.
Adopting these technology solutions can significantly enhance the procurement process.
In summary, technology not only simplifies the management of supplier certifications but also strengthens supply chain integrity.
How Should Organizations Select Suppliers Based on Certifications?
Selecting suppliers based on their certifications requires a strategic approach. Understanding the specific criteria for evaluation is key to making informed decisions.
Firstly, organizations should clearly define the criteria that align with their quality and compliance standards. It is critical to evaluate whether those criteria are relevant to the industry and product being procured. For instance, if sustainability is a value for an organization, weightage should be given to suppliers with environmental certifications.
Aligning supplier certifications with company values and goals can also help streamline the selection process. This alignment ensures that organizations engage partners who share similar priorities. It can foster more productive collaborations and spark innovations that benefit both parties.
Additionally, it’s advisable to implement a multi-year review process. Regularly re-evaluating supplier performance against their certifications helps ensure ongoing compliance and quality.
To assist organizations in this selection process, here is a criteria table:
Selection Criteria | Considerations |
---|---|
Quality and Compliance | Ensure alignment with industry standards. |
Environmental Commitment | Consider suppliers with relevant ecological certifications. |
Historical Performance | Check past performance and audit results. |
Effective supplier selection based on certifications can yield long-term benefits and strengthen your supply chain.
What Are Best Practices for Managing Certified Suppliers?
Managing certified suppliers effectively is crucial for maintaining quality and compliance throughout the procurement process. Establishing strong supplier relationships lays the groundwork for ongoing success.
One of the best practices is to enhance supplier relationship management. Frequent communication helps reinforce expectations and allows for timely discussions about any issues. A collaborative approach fosters mutual trust and keeps suppliers aligned with company goals.
Another important aspect is to monitor supplier performance consistently. Implementing Key Performance Indicators (KPIs) allows organizations to measure and review suppliers’ adherence to certifications over time. This ongoing assessment helps identify areas for improvement and ensures sustained compliance.
Moreover, organizations should develop feedback mechanisms. Encouraging suppliers to share insights and suggestions will improve collaboration and simplify the resolution of challenges. Engagement through feedback can lead to innovations that benefit both parties.
Lastly, hosting regular management reviews acts as a platform for evaluating supplier performance and strategic alignment. This ensures that both the organization and suppliers are committed to their certification standards.
Here’s a summary of best practices for managing certified suppliers:
Best Practices | Description |
---|---|
Enhance Communication | Foster open dialogue to establish trust. |
Monitor Performance | Use KPIs to evaluate ongoing compliance and quality. |
Solicit Feedback | Encourage suppliers to contribute ideas and insights. |
Conduct Regular Reviews | Assess alignment with goals and certification standards. |
Implementing these practices will lead to stronger supplier relationships and improved procurement outcomes.
What Future Trends Are Emerging in Supplier Certification?
The landscape of supplier certification is always evolving. As demand for responsible sourcing and sustainability grows, several future trends are worth noting.
One significant trend is the anticipated changes in certification requirements. Regulators, industries, and consumers are increasing pressure on companies to demonstrate ethical sourcing. This demand may lead to the adoption of new certification standards that emphasize sustainable practices.
Additionally, the influence of sustainability on future certifications cannot be overlooked. As environmental responsibility takes center stage, we can expect more stringent standards around energy use, waste management, and sourcing practices.
Finally, the emergence of technologies such as artificial intelligence and machine learning is likely to reshape certification processes. These technologies can improve data analysis and supplier monitoring, creating more efficient systems for recognizing non-compliance.
To summarize, companies should remain vigilant and aware of these trends to adapt their procurement strategies accordingly.
Conclusion
Throughout this article, we covered the critical aspects of supplier certification standards in zircon procurement. We highlighted the significance of evaluating certifications and discussed best practices for effective management. By prioritizing suppliers with appropriate certifications, companies can enhance the quality of zircon products while fostering stable business relationships.
As a key takeaway, partnering with certified suppliers can lead to significant operational efficiencies and reduced risks. Get in touch with Global Industry today to discuss how we can assist you in navigating these standards for optimal procurement strategies. Trusting the right partners will ensure that your business thrives in a competitive environment.
FAQ Section
Q1: What are supplier certification standards?
Supplier certification standards are established criteria and guidelines that companies use to evaluate and verify the quality, reliability, and compliance of suppliers. These standards often cover various aspects such as production processes, material sourcing, quality management systems (like ISO 9001), and environmental practices (such as ISO 14001). Implementing these standards allows businesses to systematically assess supplier capabilities, ensuring that the products or services received meet rigorous quality benchmarks and regulatory obligations. Ultimately, adhering to these standards helps companies mitigate risks related to supply chain disruptions and product failures.
Q2: Why are certifications important in zircon procurement?
Certifications are crucial in zircon procurement as they provide a reliable assurance of quality and compliance with established industry standards. They serve to promote supplier accountability, ensuring that suppliers adhere to necessary regulations and ethical practices throughout their operations. For buyers, certified suppliers create a sense of trust that the products meet specific quality requirements and specifications. This, in turn, minimizes the risk of sourcing low-quality materials, leading to better overall product performance and reliability. Moreover, certifications can also enhance a buyer’s reputation by demonstrating commitment to quality and ethical sourcing practices in their supply chain.
Q3: How can I verify a supplier’s certification?
Verifying a supplier’s certification is a multi-step process that often involves conducting thorough audits of the supplier’s operations and quality management systems. Buyers should request and review relevant certification documentation, which may include certificates from recognized organizations and proof of compliance with industry standards. Additionally, utilizing third-party services can provide independent confirmation of a supplier’s certifications. Such services may offer background checks, audit reports, and even on-site assessments to validate claims. Engaging in direct communication with the certifying bodies can further enhance the verification process by confirming the authenticity and current status of the supplier’s certifications.
Q4: What challenges might buyers face with certifications?
Buyers often face several challenges when dealing with supplier certifications. One common issue is the inconsistent application of certification standards across different suppliers, which can lead to varying quality levels even among certified vendors. Additionally, misinterpretations of what a certification entails can arise, leading to confusion about the specific requirements and expectations. Regional differences in regulatory standards may also pose obstacles, as certifications valid in one country may not meet the legal demands of another. Furthermore, the evolving nature of industry standards can make it difficult for buyers to keep track of which certifications are current and relevant.
Q5: What trends should we watch regarding supplier certifications?
Several trends are emerging regarding supplier certifications that buyers should monitor closely. One notable trend is the evolving certification requirements that increasingly focus on sustainability practices, reflecting the growing importance of environmental responsibility in procurement decisions. Additionally, there is a heightened emphasis on ethical sourcing, as consumers and businesses alike recognize the need for transparency in supply chains. Moreover, advancements in technology, such as blockchain and artificial intelligence, are transforming verification processes, making them more efficient and reliable. These innovations enable real-time tracking and auditing of compliance, thereby enhancing the overall integrity and trustworthiness of supplier certifications.