Choosing the right zircon sand grade affects your entire production line. Many industrial buyers feel unsure about the real value difference between standard and premium zircon sand. This article clears up that confusion. You will see how each grade performs, when to choose which, and how to get the best results for your specific needs. Trust this breakdown based on tested facts and industry insight.
How Do Standard and Premium Zircon Sand Differ?
Let’s get clear on this now. Standard zircon sand typically has lower purity levels, falling between 65% to 66% ZrO₂, and often features mixed grain sizes. This grade is suitable for general casting applications or the production of simple ceramics where precision is not as critical. It provides a cost-effective option for manufacturers who focus on volume and can tolerate minor variances in quality.
In contrast, premium zircon sand is characterized by its higher purity, exceeding 66% ZrO₂, and offers uniform grain sizes. This specific grade is designed for high-stakes applications where quality cannot be compromised, such as aerospace castings or the creation of fine ceramics. The consistent and refined properties of premium zircon sand enable manufacturers to achieve superior results and maintain tighter tolerances.
While manufacturers are often tempted to choose standard sand to cut costs, the potential for issues in high-precision work—such as defects or rework—can outweigh the initial savings. The higher price tag of premium sand is justified by the improved yields and reduced rejections. This makes it essential to align the choice of sand with technical requirements and production goals, rather than focusing solely on budget constraints.
Comparison | Standard Zircon Sand | Premium Zircon Sand |
---|---|---|
Purity Level | 65%-66% ZrO₂ | 66%+ ZrO₂ |
Grain Size | Mixed | Uniform |
Cost | Lower | Higher |
Applications | General use | High-spec production |
By understanding these differences, manufacturers can make informed decisions that align with their specific operational needs, ultimately leading to better performance and satisfaction in their end products. Choosing the right grade of zircon sand can be a key factor in optimizing production processes and achieving consistent results.
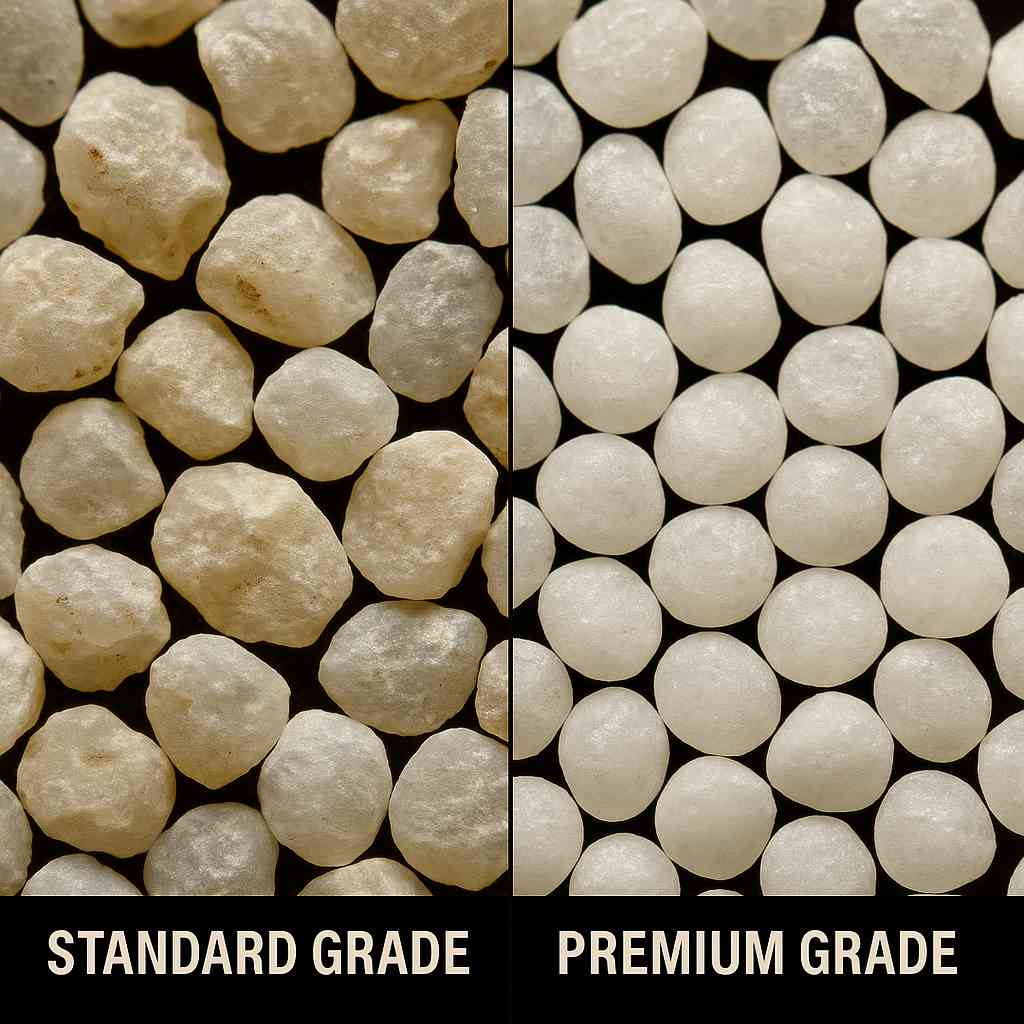
Why Does Purity Matter in Zircon Sand?
Here’s the reality. Purity levels significantly influence the final product’s strength, heat resistance, and overall quality. More impurities typically lead to a higher incidence of defects, especially during critical processes like firing ceramics or melting metal. Impurities can manifest in various forms, impacting functionality and aesthetics.
In standard grades, trace minerals such as rutile or ilmenite may introduce color spots or weak points, jeopardizing the integrity of the end product. For industries aiming for high performance and reliability, these defects can be costly. Conversely, premium grades undergo rigorous processing to eliminate these extraneous materials, ensuring greater consistency and quality. Buyers pay a premium price, but they benefit from reduced reject rates and increased reliability in production.
Laboratory tests play a crucial role in validating purity claims. They assess ZrO₂ content, silica, iron, and other potentially harmful minerals. Always review a supplier’s test report before placing bulk orders. Clean sand means steady performance and fewer surprises on your production line.
Impurity | Standard Grade (%) | Premium Grade (%) |
---|---|---|
Fe₂O₃ | 0.1–0.2 | <0.1 |
TiO₂ | 0.1–0.3 | <0.1 |
SiO₂ | 32–34 | <32 |
By prioritizing purity in zircon sand, manufacturers can enhance product quality, reduce rework, and ultimately improve profitability. Choosing the right grade is not just about immediate cost savings; it’s about long-term efficiency and product excellence.
What Are the Main Uses for Standard Zircon Sand?
Here’s where it fits best. Standard zircon sand serves industries that tolerate minor defects or color shifts. Foundries use it for mold coatings and casting shells. This sand’s moderate performance makes it ideal for applications where extreme precision is not critical.
Foundries utilize standard zircon sand for various casting applications, particularly where large volumes are produced. It is cost-effective and provides reliable mold characteristics. It also helps reduce mold sticking, improving the cast surface quality.
Ceramics is another significant application area. Standard zircon sand is widely used in the production of tiles and other ceramic products where minor imperfections can be easily masked by glazes. This grade is particularly beneficial in the base layers of ceramics, allowing manufacturers to save their premium materials for top layers, thus optimizing costs without sacrificing quality.
In the refractory industry, standard zircon sand is utilized for making furnace linings and other moderate heat applications. While it does not provide full chemical resistance, it serves adequately in environments where conditions are not overly harsh.
For example, a tile factory can use standard sand for underglaze layers, saving premium grades for top coatings. This mix helps keep margins steady while also maintaining a level of quality suitable for the end product.
Industry | Use Case |
---|---|
Foundry | Mold coating |
Ceramics | Base layers, tiles |
Refractories | Furnace linings |
Overall, the versatility of standard zircon sand makes it a practical choice for industries focused on balancing cost and performance without requiring the highest specifications.
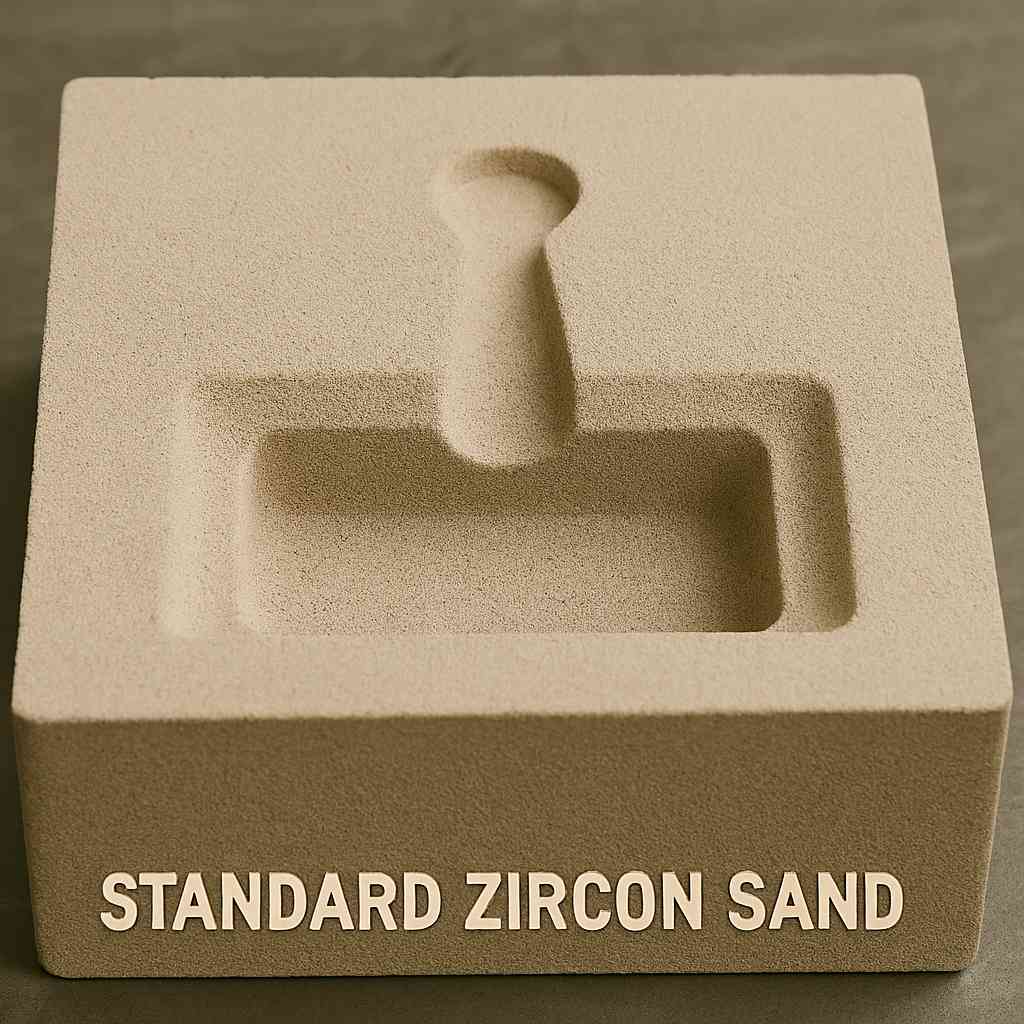
When Should Companies Choose Premium Zircon Sand?
Let’s break this down. Premium zircon sand excels in precision projects where the stakes are high. Here are some critical scenarios:
- Advanced Ceramics: In the production of high-end ceramics, zero contamination is essential to maintain color purity and the structural integrity of the final product. This is particularly important for items like fine china or high-performance ceramics used in electronic applications.
- Aerospace Parts: Aerospace industries require molds for wax casting that endure extreme temperatures and tight tolerances. Any defects can compromise safety and performance, making premium sand the safer option to ensure quality.
- Glass Manufacturing: Manufacturers in this sector demand high clarity and strength in their products. For glass intended for optics or high-heat environments, the stability provided by premium grades is crucial. Minor imperfections often lead to significant waste, which can be financially detrimental.
- Chemical Industries: Some chemical sectors utilize premium zircon sand as a foundational material for advanced compounds. The need for high purity and controlled grain size is vital for maintaining quality in these applications.
If your production runs require exceptional consistency and your customers will not accept any flaws, investing in premium zircon sand is your safest bet. It assures compliance with stringent quality requirements and enhances the overall productivity of the manufacturing process.
Industry | Why Premium? |
---|---|
Aerospace | Precision casting |
High-End Ceramics | Color purity, strength |
Glass | High heat resistance |
How Do Prices Compare Between Both Grades?
Don’t overlook this factor. Market prices change based on various elements, including region, mine output, and shipping costs. On average, standard zircon sand typically costs 30% to 50% less per ton than its premium counterpart. However, it’s crucial to look deeper: while the initial price of premium sand is higher, a single batch can significantly cut defect rates by 20% to 40%, translating to substantial savings in the long run.
Additionally, market trends and economic conditions can impact prices. For instance, during periods of high demand or supply chain disruptions, both grades may see price fluctuations. Bulk buyers often lock in annual contracts with suppliers to ensure stable pricing and mitigate the risks associated with sudden market changes.
Companies should also consider the total cost of ownership. While choosing standard sand may initially save money, frequent rework and product waste due to quality issues can negate these savings. Thus, investing in premium sand often pays off by ensuring consistency and reducing production downtime.
Plan your sourcing with cost stability in mind. Saving upfront may lead to higher overall costs if the selected grade doesn’t match your specific production needs.
Grade | Average Cost (per ton) |
---|---|
Standard | \$1,200–\$1,500 |
Premium | \$1,600–\$2,200 |
What Are the Key Quality Standards to Know?
Pay attention here. Trusted grades follow ISO or national mining standards, ensuring that the zircon sand meets specific quality thresholds essential for various applications. These specifications detail key parameters such as ZrO₂ content, grain size, moisture levels, and the presence of radioactive trace elements. It is crucial for both suppliers and buyers to adhere to these standards to guarantee product reliability and safety.
Reputable suppliers provide certificates and lab reports for each shipment, allowing buyers to assess the quality of the zircon sand before making larger orders. Always review these reports against your internal processing requirements. For example, fine ceramics may demand a ZrO₂ content of 66% or higher to ensure optimal performance, while general castings might allow for lower percentages without compromising overall quality.
Additionally, buyers should be aware of industry-specific standards that may apply in their region or sector. For instance, certain applications may have stricter limits on moisture content or require specific grain sizes to optimize casting results.
Some buyers opt to conduct random lab tests to verify the reported quality of the zircon sand. This additional step builds trust in the supplier’s claims and helps maintain operational integrity.
Parameter | Target Value |
---|---|
ZrO₂ | 65%–66%+ |
Grain Size | 75–150 microns |
Moisture | <0.5% |
Radioactive Elements | Below safety limits |
In summary, understanding these key quality standards and parameters ensures that you select the right grade of zircon sand for your specific applications, minimizing defects and optimizing production processes.
How Should Buyers Evaluate Zircon Sand Suppliers?
This part saves headaches later. When selecting zircon sand suppliers, it’s crucial to conduct a thorough evaluation to ensure you’re partnering with a reliable source that meets your quality standards. Here are key factors to consider:
- Backup Suppliers: For extra security, keep two or more approved sources ready. This strategy safeguards against disruptions in supply and helps maintain production schedules.
- Stable Mining Sources: Ensure the supplier has sustainable and stable mining operations. Consistency in sourcing leads to uniform product quality.
- Clean Handling Processes: Look for suppliers who adhere to strict cleanliness protocols during sand processing and packaging. This minimizes the risk of contamination and maintains sand purity.
- Delivery Times: Assess supplier reliability by reviewing their delivery performance. Timely shipping is essential to avoid production delays.
- Batch Consistency: Evaluate the consistency of their product batches. Reliable suppliers should provide documentation that demonstrates uniformity in quality across shipments.
- Customer Service: Strong customer support is vital. Choose suppliers who promptly answer inquiries and resolve potential issues efficiently.
- Recent Test Reports: Always request and review recent test reports from suppliers. Ensure that these documents detail ZrO₂ content, grain size, moisture levels, and any radioactive trace elements.
- Site Visits: If feasible, visit the suppliers’ mines or processing plants. Observing their operations firsthand can provide insights into their practices and commitment to quality.
Utilizing these criteria will strengthen your supplier selection process and promote long-term partnerships based on quality and reliability.
For extra security, keep two or more approved sources ready. If one mine closes or shipping slows down, your production stays on track. For buyers wanting guaranteed quality and stable supply, check our full range of zircon sand products to compare grades and arrange orders with full confidence.
Checklist | Details |
---|---|
Mine Source | Verified and stable |
Consistency | Batch reports match specs |
Service | Fast support, reliable delivery |
By ensuring your zircon sand suppliers meet these standards, you’ll build a robust supply chain that supports your operational efficiency and product quality.
Which Industries Rely Heavily on Premium Grades?
Let’s see some real cases. Premium zircon sand is invaluable across several industries, particularly those that demand high precision and exceptional quality. Each of these sectors runs tight specifications, meaning that cutting corners isn’t an option. They simply cannot risk defects in their products or components, making premium zircon sand their best choice for reliable outcomes.
Aerospace foundries can’t risk defects. They require molds that maintain their shape under extreme heat and stress, which is critical when producing components like jet engine parts. The performance and safety of aircraft rely heavily on the quality of these components, necessitating the use of premium materials.
High-end ceramics manufacturers aim for flawless finishes. In applications such as porcelain production and tile manufacturing, any specks or weak spots can compromise the aesthetic and structural integrity of the final products. Here, premium zircon sand ensures the desirable qualities like strength and visual appeal.
Glass manufacturers also prioritize high clarity and strength in their products. Whether producing optical lenses or high-quality glassware, any defects can mean significant financial losses. Premium grades provide the low impurity thresholds necessary to achieve optimal results in high heat applications.
Chemical industries leverage premium zircon sand as a base for advanced compounds. Industries involved in developing next-generation materials need zircon sand that offers purity and consistency to maintain high-performance standards in chemical reactions and formulations.
Sector | Key Application |
---|---|
Aerospace | Jet engine parts |
Fine Ceramics | Porcelain, tiles |
Glass | Optical lenses |
Chemicals | Zirconia compounds |
These sectors run tight specs, as any issues can lead to production halts and increased costs. Paying for premium zircon sand in the initial stages is a proactive approach that safeguards quality while supporting long-term operational efficiency.
How Can Companies Store Zircon Sand Properly?
Proper storage of zircon sand is crucial to maintain its quality and prevent contamination. Here’s how you can ensure the integrity of your stock:
- Keep Dry and Sealed: Moisture is the enemy of zircon sand. It can lead to clumping, which affects the flow of sand during production and can cause inconsistent results. Utilize airtight containers or sealed bags to prevent moisture from entering.
- Store Off the Ground: Elevating storage bags or bins off the ground helps avoid contact with moisture from the floor. Use pallets or racks to create distance from surfaces that may retain dampness.
- Use Lined Bins for Bulk Storage: If you’re storing sand in bulk, consider using lined bins that are moisture-resistant. This not only protects against moisture but also minimizes the risk of contamination from external sources.
- Inspect Containers Regularly: Regular inspections of storage containers for leaks, tears, or damage are vital. Address any issues immediately to prevent sand spoilage or contamination.
- Train Staff to Handle Sand Gently: Proper training for employees on how to handle zircon sand can minimize spillage and dust loss. Gentle handling ensures that the sand maintains its quality and properties during transfer and storage.
- Maintain Temperature Stability: Extreme temperature fluctuations can impact the quality of zircon sand. Where possible, store it in a climate-controlled environment to maintain consistent conditions.
- Implement FIFO Practices: Use a first-in, first-out (FIFO) approach for inventory management. This ensures that older stock is used first, reducing the chances of prolonged storage that can affect sand quality.
Good storage practices are not just about preventing waste; they ensure stable performance in every batch.
Tip | How to Do It |
---|---|
Keep Dry | Covered, sealed storage |
Off the Ground | Use pallets |
Inspect Bins | Check for leaks |
Train Workers | Prevent spillage |
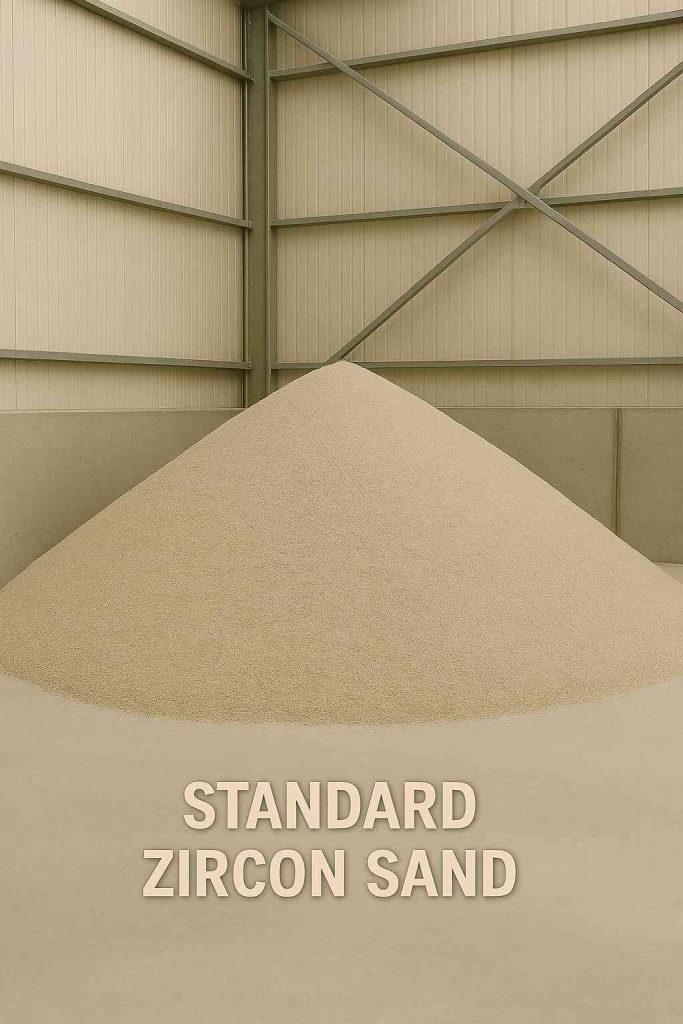
What Are Current Trends in Zircon Sand Usage?
Time to wrap this topic up smartly. Global demand for cleaner zircon sand grows yearly. New tech like 3D printing and high-temp alloys needs steady supply. Meanwhile, mines face stricter environmental checks, tightening supply.
Many buyers shift to premium grades to meet tougher standards and reduce defect costs. Recycling used sand helps too. Smart companies plan contracts early and watch policy changes.
This ensures stable production, even when raw sand prices fluctuate.
Trend | Impact |
---|---|
Tighter Environmental Rules | Lower output |
Advanced Applications | Need cleaner grades |
Recycling | Cuts waste, costs |
Long-Term Contracts | Secure supply |
Conclusion
Choosing the right zircon sand grade shapes production stability, quality, and long-term costs. This guide showed how standard and premium zircon sand differ in purity, cost, and where each grade works best. Investing in the right material cuts waste and protects profit margins. Global Industry stands ready to connect you with trusted zircon suppliers and keep your production steady. Reach out now for custom quotes and professional sourcing support that help your operation stay ahead.
FAQ Section
Q1: Can standard zircon sand replace premium in all cases?
Not always. Standard zircon sand suits general casting, tiles, or furnace linings where minor impurities won’t hurt performance. But for aerospace molds, fine ceramics, or glass, using premium sand prevents defects and keeps production smooth. Trying to cut corners with standard sand in high-spec jobs often costs more in scrap and rework.
Q2: Is premium zircon sand worth the higher price?
Yes, for demanding projects. Premium sand provides steady purity and tight grain sizes, which means fewer rejects and less downtime fixing quality issues. Many buyers find that the extra cost pays back through better yields, consistent product specs, and fewer customer complaints.
Q3: How can I test zircon sand purity myself?
You can run basic checks in-house for moisture and grain size, but for accurate ZrO₂ content and trace impurities, use a trusted lab. Some buyers test every batch on arrival, while others check samples from each shipment to catch any quality drift early.
Q4: Do storage conditions affect zircon sand quality?
Definitely. Poor storage can cause moisture buildup, clumping, or contamination with other materials. This reduces flow and heat stability. Store sand in sealed bags or covered silos, keep it off damp floors, and train staff to handle it carefully to maintain quality from warehouse to production.
Q5: Where can I find reliable zircon sand suppliers?
Look for suppliers with stable mine sources and a history of clean, consistent batches. Check customer reviews and ask for recent lab reports. A good supplier answers questions fast and helps arrange bulk orders on time. Global Industry can connect your team with trusted partners and handle the paperwork for smooth delivery.