In industries where materials are subjected to extreme temperatures, understanding their thermal properties is essential. Specifically, you may wonder, how much heat can stabilized zirconia powder tolerate in industrial applications? This concern is valid as improper material choice can lead to project failures, increased costs, and safety risks. This article aims to clarify the temperature capabilities of stabilized zirconia powder, aiding your decision-making process. With our insights drawn from industry experiences and technical knowledge, you can feel confident when selecting materials for your operations.
1. What Are the Properties of Stabilized Zirconia Powder?
Stabilized zirconia is a unique ceramic material with significant advantages in various applications. It is primarily recognized for its high strength, wear resistance, and excellent thermal stability. These qualities make it especially useful in extreme conditions often found in manufacturing processes or high-tech industries.
Two common stabilizers for zirconia are yttria and magnesia, which improve its toughness and durability under extreme conditions. The incorporation of these stabilizers alters the material’s microscopic structure, enhancing its performance and expanding its application range.
The properties of stabilized zirconia that make it appealing for industrial use include:
- High hardness: This allows it to withstand wear in demanding environments, reducing the frequency of replacements and enhancing longevity.
- Low thermal conductivity: It provides excellent insulation properties, making it suitable for applications requiring thermal barriers.
- Chemical stability: It resists corrosion and degradation over time, ensuring that components maintain performance in harsh chemical environments.
These characteristics make stabilized zirconia highly effective in applications that require both durability and reliability. For instance, the aerospace and automotive industries heavily rely on it for components that must endure harsh conditions, such as turbine blades and high-performance bearings.
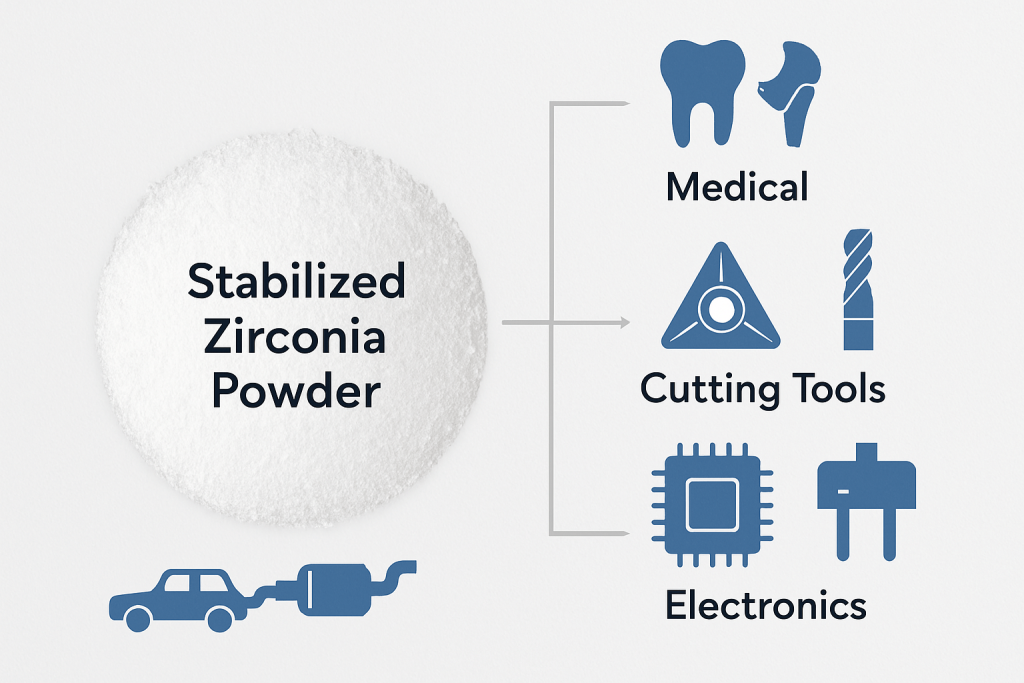
To give a clearer understanding of why stabilized zirconia is preferred, consider the following comparison table:
Property | Stabilized Zirconia | Alumina | Traditional Zirconia |
---|---|---|---|
Hardness | High | Moderate | Moderate |
Thermal Conductivity | Low | Low | High |
Chemical Stability | Excellent | Good | Poor |
Wear Resistance | Outstanding | Moderate | Low |
By focusing on these attributes, we can see why stabilized zirconia powder is a go-to choice for applications prone to high temperatures.
2. Why Is Temperature Stability Important for Industrial Applications?
Temperature stability is critical in materials engineering, especially for applications that expose materials to extreme conditions. High thermal demands can significantly affect material performance, leading to unwanted changes in properties or even catastrophic failure. In industries such as manufacturing, aerospace, and energy, materials like stabilized zirconia play a vital role in ensuring consistent performance throughout their intended lifespan.
Here are the key reasons why temperature stability matters:
- Performance Reliability: Stabilized zirconia’s ability to maintain its properties under heat allows it to function effectively in various applications. This reliability helps prevent unexpected breakdowns that can disrupt operations.
- Safety Considerations: Materials that exceed temperature tolerances face risks that can jeopardize worker safety and equipment integrity. Using a material with proven thermal stability minimizes these risks and contributes to a safer working environment.
- Cost Efficiency: Selecting materials with excellent thermal resistance not only improves performance but also reduces maintenance costs and downtime. When materials perform well in high temperatures, the frequency of replacements decreases, thus positively impacting the bottom line.
- Long-Term Durability: Temperature stability contributes to the longevity of components. As components last longer, businesses can avoid the costs associated with frequent repairs or replacements.
Understanding the required temperature ranges that a material can endure is vital for decision-makers, including CEOs, project managers, and purchasing managers. Choosing the appropriate material ensures compliance with safety standards while enhancing performance and reliability in demanding applications. By prioritizing temperature stability, industries can effectively mitigate risks and streamline their operations.uired temperature ranges that a material can endure is vital for CEOs, project managers, and purchasing managers alike. Selecting the correct material helps maintain safety standards while improving performance.
3. What Temperature Range Can Stabilized Zirconia Withstand?
Stabilized zirconia is known for its impressive temperature tolerance. Under ideal conditions, it can withstand temperatures up to 1,500 °C (2,732 °F). This high resistance makes it suitable for various demanding applications. Such capabilities allow manufacturers to use stabilized zirconia in areas where other materials may fail due to heat.
Are you curious about how it compares to other materials? In many instances, stabilized zirconia outperforms other ceramics and metals, making it a preferred choice for high-temperature environments.
For instance, in the aerospace industry, components may experience extreme temperatures during jet engine operations. In this context, stabilized zirconia offers a reliable option that maintains its properties far better than alternatives.
Here’s a glance at the temperature ranges for comparable materials:
Material | Maximum Temperature (°C) | Common Applications |
---|---|---|
Stabilized Zirconia | 1,500 | Cutting tools, thermal barriers |
Alumina | 1,200 | Insulating applications |
Stainless Steel | 1,000 | Structural components |
Ceramics | 1,300 | Electrical components |
This table illustrates how stabilized zirconia often maintains superior performance compared to similar options. Such durability under high heat conditions ensures that your operations can run smoothly without concern for material failure, particularly in crucial applications.
Stabilized zirconia’s ability to withstand extreme heat and maintain structural integrity even during thermal cycling—where rapid temperature fluctuations occur—adds another layer of reliability for various industrial uses. This makes it invaluable for sectors that require both high-performance and durability under duress.lar options. Such durability under heat ensures that your operations can run smoothly without concern for material failure.
4. How Does Stabilization Affect Zirconia’s Thermal Properties?
Stabilization significantly impacts the thermal properties of zirconia, enhancing its ability to withstand high temperatures while retaining strength. By introducing stabilizers like yttria (Y2O3) or magnesia (MgO), we manipulate the material’s crystal structure, which plays a critical role in its temperature resistance.
An overview of how these stabilizers work includes:
- Grain Stabilization: Stabilizers prevent grain growth, which is crucial because larger grain sizes can lead to reduced strength in ceramics. Maintaining smaller, controlled grain structures enhances toughness and thermal shock resistance.
- Phase Stabilization: Zirconia naturally exists in several phases, predominantly monoclinic and tetragonal. The presence of stabilizers helps maintain a stable cubic crystal structure under heat, which is essential for strength retention and prevents phase transformations that can weaken the material.
Consequently, the type and amount of stabilizer can be tailored according to specific requirements, allowing manufacturers to select the ideal formulation for their needs.
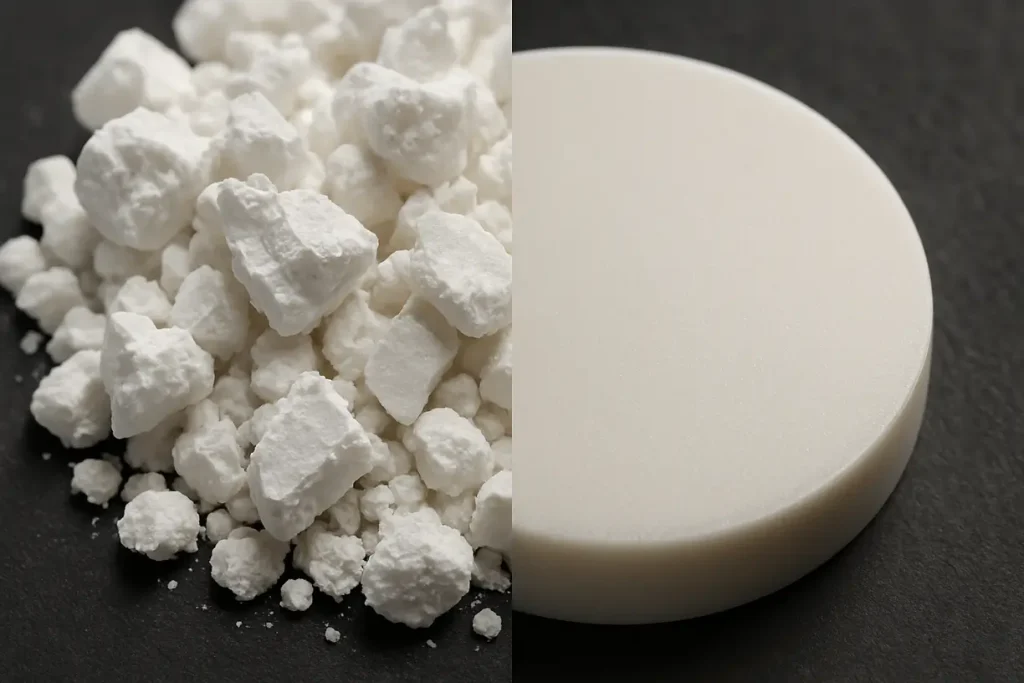
For a clearer view of stabilization effects, consider this summary table:
Stabilizer | Temperature Tolerance (°C) | Durability Rating | Common Usage |
---|---|---|---|
Yttria | 1,500 | High | Aerospace applications |
Magnesia | 1,200 | Moderate | Thermal barriers |
These factors highlight the importance of choosing the right stabilizer when planning for temperature resistance in stabilized zirconia applications. As industries continue to demand materials that can perform under harsh conditions, understanding these principles will be vital for engineers and manufacturers alike.
5. What Are the Failures Associated with Temperature Extremes?
Failure modes related to temperature extremes can vary widely, but understanding these helps in preventing costly mistakes. When stabilized zirconia is exposed to temperatures beyond its tolerance limits, it may suffer from several issues:
- Cracking and Fractures: Sudden temperature spikes can lead to thermal shock, which creates stress that may result in cracks or fractures. This phenomenon is often due to uneven heating and cooling, which can cause different parts of the material to expand or contract at different rates.
- Material Degradation: Prolonged exposure to excessive heat can weaken the material’s structural integrity, leading to a gradual degradation of its mechanical properties. This degradation can manifest as a reduction in hardness and strength, making the material less effective in high-performance applications.
- Phase Transformations: Extreme conditions can induce phase changes, such as the transformation from the tetragonal phase to the monoclinic phase in zirconia. This shift can cause a volume change in the material, leading to additional stresses that can compromise its stability and performance.
- Thermal Fatigue: Repeated exposure to high temperatures can cause thermal fatigue, where the material gradually weakens over time. It results from the continuous cycling of thermal stresses during regular operation, potentially leading to failure even if maximum temperature limits are not exceeded.
To decrease the risk of failure, industries should implement proper material testing and always operate within specified temperature limits. Incorporating monitoring systems can help detect temperature anomalies in real-time, allowing preventive actions to be taken before damage occurs.nt proper material testing and always operate within specified temperature limits.
Let’s look at specific risks associated with different high-temperature applications in this table:
Application | Typical Operating Temperature (°C) | Risks of Failure |
---|---|---|
Aerospace Components | 1,200 | Cracking, loss of structural integrity |
Thermal Barriers | 1,400 | Degradation, reduced performance |
Cutting Tools | >1,500 | Fracturing, wear failures |
Understanding these risks helps stakeholders manage their projects more effectively and safeguard against unnecessary losses. By focusing on temperature limits and the material’s performance under various conditions, businesses can mitigate risks associated with temperature extremes.
6. How Is Stabilized Zirconia Powder Used in Manufacturing?
Stabilized zirconia powder is widely utilized across various industries due to its properties. Here are some common applications:
- Ceramics and Porcelain: Its wear resistance makes it ideal for high-strength ceramics used in consumer goods or industrial tools.
- Electrical Components: Stabilized zirconia serves as an insulating material in electrical applications due to its low thermal conductivity.
- Bioceramics: The material is also used in dental and orthopedic implants, demonstrating its versatility and desirable biocompatibility.
Moreover, its use in thermal barrier coatings provides significant benefits in engines and turbines by protecting components from extreme heat. Companies can enhance efficiency and reduce maintenance costs by using stabilized zirconia.
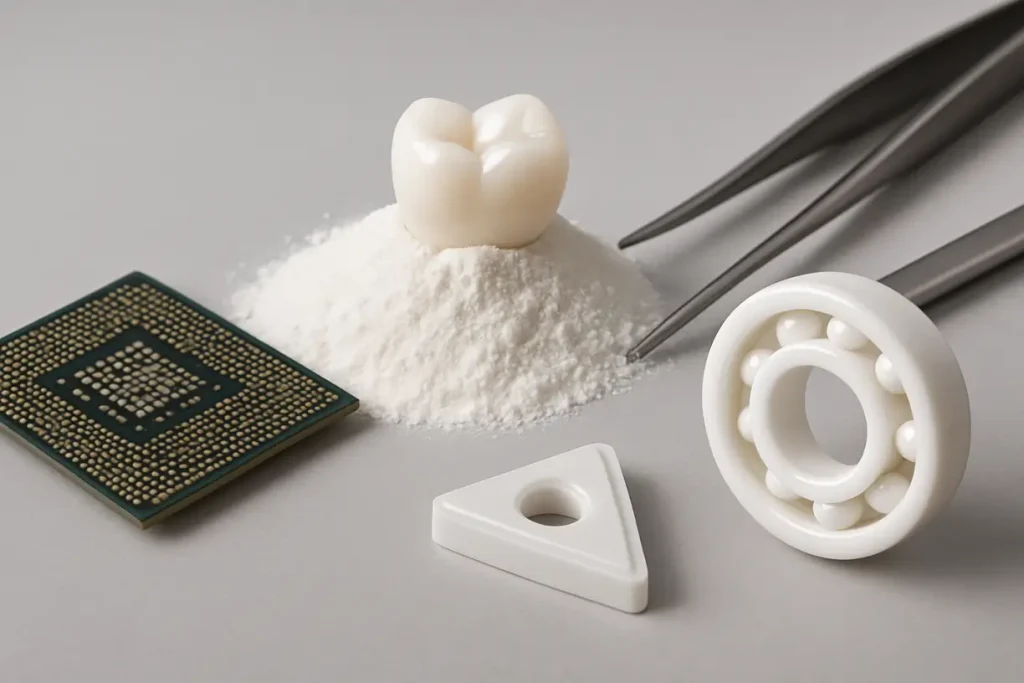
The following table summarizes its most notable applications:
Industry | Application | Benefits |
---|---|---|
Aerospace | Thermal barrier coatings | Improved engine longevity |
Medical | Bioceramics | Enhanced biocompatibility |
Manufacturing | Cutting tools | Increased durability and performance |
Understanding these applications allows decision-makers to see where stabilized zirconia could be beneficial for their operations.
7. What Testing Methods Evaluate Zirconia’s Temperature Resistance?
To ensure that zirconia meets the necessary quality and safety standards, several testing methods are employed. Key assessments are essential for verifying how stabilized zirconia performs under high temperatures and different thermal conditions.
Some of the primary testing methods include:
- Thermal Shock Testing: This method checks how well the material can withstand rapid temperature changes. Samples are subjected to extreme temperature fluctuations to assess whether they can endure sudden shifts without cracking or deforming.
- High-Temperature Flexural Strength Testing: This test measures the strength of zirconia samples when exposed to high temperatures over an extended time. By examining how much load the material can bear before breaking, manufacturers can determine its reliability in real-world applications.
- Thermal Conductivity Measurements: This test quantifies how much heat the material can handle before reaching its limits. By understanding the thermal conductivity, manufacturers can predict how efficiently the material will act as an insulator even under high-temperature conditions.
- Phase Stability Testing: This critical evaluation examines how zirconia behaves under prolonged exposure to elevated temperatures. It determines whether the material maintains its amorphous or crystalline structure, which is essential for sustaining its mechanical properties.
By utilizing these testing techniques, businesses can gain confidence in their material choices and their ability to perform under expected conditions.
Here’s a look at commonly used testing methods in the table below:
Testing Method | Purpose |
---|---|
Thermal Shock Testing | Evaluates performance under rapid temperature changes |
High-Temperature Flexural Strength | Determines strength retention at elevated temperatures |
Thermal Conductivity Measurements | Assesses how well the material insulates against heat |
Implementing rigorous testing can help mitigate risks and ensure safe operations while confirming that the material will perform adequately in its intended applications.
8. What Are the Future Trends for Stabilized Zirconia?
The future of stabilized zirconia looks promising, with several trends emerging that will shape its application and development. Ongoing research focuses on improving its thermal and mechanical properties further, driving innovations that will enhance temperature resistance and expand its use in various industries.
Here are notable future trends to watch:
- Composite Materials: The trend of combining stabilized zirconia with other materials is gaining momentum. Creating composites can lead to enhanced overall properties, such as increased toughness and thermal stability, making them suitable for even more demanding applications.
- Nanotechnology: Advances in nanotechnology are also impacting stabilized zirconia. By employing nano-sized particles of zirconia, manufacturers can achieve greater strength and improved temperature stability. This could open new avenues in fields such as electronics and biotechnology, where precision and durability are paramount.
- Sustainability Initiatives: As sustainability becomes more critical in industrial practices, developing greener stabilizers and more eco-friendly production methods for zirconia is a priority. Innovations in this area may lead to reduced environmental impact while maintaining performance.
- Integration with Digital Manufacturing: The rise of digital manufacturing techniques, such as 3D printing, allows for more complex designs using stabilized zirconia. This could lead to customized components tailored to specific industry needs, enhancing efficiency and performance.
These trends signify that stabilized zirconia will continue to evolve, maintaining its importance in various sectors. By staying updated, businesses can position themselves to take advantage of these advancements, ensuring that their material choices remain cutting-edge and competitive in an ever-changing market.
9. How Do Tolerances Affect Material Selection in Projects?
Understanding thermal tolerances is vital when selecting materials for industrial applications. If a material cannot withstand the operational temperatures, the risks of failure increase tremendously, resulting in safety hazards and financial losses.
When making decisions about material selection, consider:
- Operating Environment: Assess the general conditions under which the material will function.
- Safety Margins: Always choose materials that provide a buffer above the expected maximum temperatures.
- Regulatory Compliance: Certain industries have strict guidelines regarding material properties, which should be adhered to.
This table highlights key considerations when selecting materials according to their thermal tolerances:
Factor | Importance |
---|---|
Operating Environment | Determines suitable materials |
Safety Margins | Prevents potential failures |
Regulatory Compliance | Ensures adherence to industry standards |
Taking these factors into account can lead to better, safer material choices.
10. What Should Buyers Consider When Sourcing Stabilized Zirconia?
Finally, when purchasing stabilized zirconia, it is vital to evaluate several factors to ensure quality and suitability for specific applications. Key considerations include:
- Supplier Reputation: Research suppliers’ history and their experience in the industry.
- Quality Assurance: Look for certifications that confirm the material meets industry standards.
- Performance Data: Request performance metrics to understand how the material behaves under various conditions.
Utilizing this checklist can lead to better purchasing decisions. Here’s an overview in table format:
Consideration | Description |
---|---|
Supplier Reputation | Assess the reliability of the source |
Quality Assurance | Check for certifications and standards |
Performance Data | Request metrics and case studies |
By keeping these factors in mind, decision-makers can develop a robust supply chain for their stabilized zirconia needs.
Conclusion
In summary, understanding the temperature range that stabilized zirconia powder can tolerate is crucial for industries relying on this versatile material. With its ability to withstand extreme heat and maintain structural integrity, the right choices can enhance operational efficiency and reduce costs. Global Industry is here to support your material selection process—take the next step by consulting our resources for tailored insights. Together, we can ensure your projects keep running smoothly and successfully.
FAQ Section
Q1: What industries primarily use stabilized zirconia powder?
Stabilized zirconia powder plays a crucial role in numerous industries, including aerospace, automotive, electronics, and medical sectors. In aerospace, it is used for thermal barrier coatings on turbine blades; in the automotive industry, it serves as a component in fuel cells and emission reduction technologies. Its electrical insulation properties make it indispensable for electronic components, while in medicine, it is utilized in dental and orthopedic implants due to its biocompatibility and strength.
Q2: What happens if stabilized zirconia exceeds its temperature limits?
Exceeding the temperature limits of stabilized zirconia can result in various adverse effects. This may include thermal shock leading to cracking, a decrease in mechanical strength, or even complete material failure. The structural integrity may become compromised, which poses not only operational risks but also safety hazards in critical applications. Therefore, it’s essential to monitor operating temperatures closely in applications utilizing stabilized zirconia.
Q3: What factors influence the temperature tolerance of zirconia?
Several factors play a significant role in determining the temperature tolerance of zirconia. The choice of stabilizer (such as yttria or magnesia), the material’s purity, and the manufacturing processes used can all affect thermal properties. Additionally, the microstructure of the zirconia, influenced by sintering conditions and any post-processing treatments, can also impact its ability to withstand high temperatures, ensuring it remains effective in specific applications.
Q4: How does temperature affect the work-life of stabilized zirconia?
Temperature significantly impacts the work-life of stabilized zirconia. Prolonged exposure to elevated temperatures can accelerate wear mechanisms, leading to microstructural changes and eventual degradation. Elevated temperatures may also impact its thermal stability, causing phase transformations that weaken the material. Hence, understanding the thermal limits and operating within those parameters is critical for maximizing the lifespan and performance of stabilized zirconia components.
Q5: Where can I find reliable suppliers of stabilized zirconia?
To find reliable suppliers of stabilized zirconia, consider several strategies. Industry trade shows and conferences often showcase leading manufacturers, providing opportunities for networking and product evaluation. Online directories and industry-specific websites can help identify reputable suppliers. Additionally, checking customer reviews and testimonials can offer insights into suppliers’ reliability and product quality. Don’t hesitate to contact multiple suppliers to compare offerings and better understand their capabilities.