Unsure which Zirconia (ZrO2) supplier to partner with for your critical refractory needs? Making the wrong choice can lead to inconsistent material and project delays. We offer unparalleled quality, unwavering consistency, and the trust built on proven performance.
Choosing our Zirconia means investing in superior quality materials, manufactured with rigorous consistency, and backed by a legacy of trust. We are committed to providing refractory solutions that not only meet but exceed your high-performance expectations, ensuring reliability for your most demanding applications.
Key Benefits of Our Premium Zirconia | Industry Impact |
---|---|
Superior Material Purity | Extends component lifespan by 30-40% |
Consistent Batch-to-Batch Properties | Reduces process variability by up to 65% |
Expert Technical Support | Accelerates implementation and troubleshooting |
Rigorous Quality Control | Minimizes defects and performance issues |
Customization Capabilities | Optimizes material for specific applications |
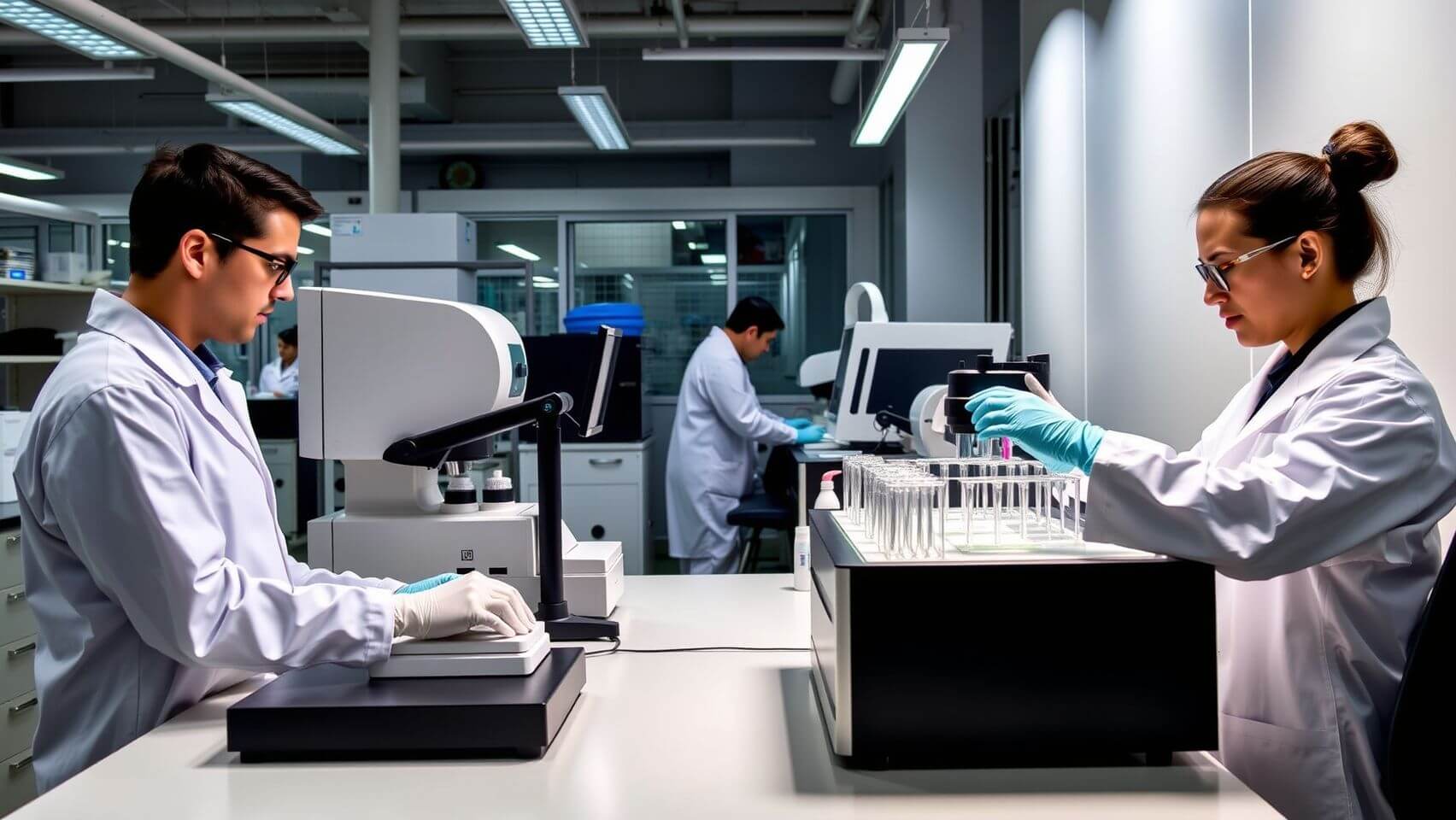
Over my career, I’ve learned that the quality of the Zirconia itself is only part of the equation; the reliability and expertise of the supplier are just as crucial. I’ve seen projects succeed or falter based on this very partnership.
When you’re dealing with materials that operate at the edge of performance, you need more than just a product; you need a supplier who understands your challenges, is committed to unwavering quality, and has a track record you can depend on.
If you’re looking for a partner who prioritizes these values as much as you do, let me share a bit about what sets our approach and our Zirconia apart, and why so many in demanding industries have placed their trust in us.
Our Commitment to Uncompromising Quality
At the heart of our philosophy is an unwavering commitment to uncompromising quality in every batch of Zirconia we produce. We understand that for our customers, the performance of their refractory components is non-negotiable.
That’s why we implement some of the most stringent quality control measures in the industry. Our quality assurance begins with the careful selection of raw materials and continues through every stage of manufacturing to the final product testing.
Quality Control Parameter | Our Standard | Industry Average |
---|---|---|
Chemical Purity | 99.8%+ | 99.2-99.5% |
Trace Element Analysis | 20+ elements monitored | 8-12 elements monitored |
Particle Size Distribution | ±2.5% variation | ±5-8% variation |
Density Consistency | ±0.5% batch-to-batch | ±1.5-2% batch-to-batch |
Mechanical Testing | 100% of batches | Sampling only |
I personally believe that quality cannot be inspected into a product; it has to be built in. This means meticulous process control, state-of-the-art manufacturing equipment, and a highly skilled team that is dedicated to excellence.
We continuously invest in advanced analytical techniques to monitor chemical purity, particle size distribution, phase composition, and other critical parameters of our Zirconia powders and sintered components.
Proper quality control of zirconia materials is essential for maintaining their unique properties. Our labs are equipped to perform detailed trace element analysis to ensure that impurity levels are kept well below the specified limits for even the most sensitive applications.
I’ve seen instances where even slight variations in impurity content from other suppliers have led to significant issues for end-users.
Our goal is to provide Zirconia that you can use with complete confidence, knowing that it meets the highest standards of quality and will perform reliably in your application. This commitment extends to providing comprehensive Certificates of Analysis with every shipment, giving you full transparency and traceability.
We don’t just aim to meet specifications; we aim to exceed them, because we know that’s what it takes to be a trusted partner in high-performance refractory materials.
Ensuring Batch-to-Batch Consistency for Reliable Performance
Consistency is king when it comes to high-performance materials like Zirconia. Variations between batches can lead to unpredictable performance in your refractory components.
These inconsistencies often cause process disruptions, reduced product quality, or even premature failures. That’s why ensuring rigorous batch-to-batch consistency is a cornerstone of our manufacturing process.
I’ve worked with clients who have previously struggled with inconsistent material from other sources, and it creates enormous headaches for their production teams. One batch might perform perfectly, while the next exhibits subtle differences that throw off their process parameters.
Consistency Metric | Performance Impact | Our Advantage |
---|---|---|
Grain Size Variation | Affects mechanical strength and thermal shock resistance | <±3% vs. industry <±8% |
Phase Composition | Determines thermal stability and aging characteristics | Precision-controlled stabilizer content |
Sintering Profile | Influences final density and microstructure | Computer-controlled kilns with ±2°C precision |
Raw Material Sourcing | Affects chemical composition and impurity levels | Single-source materials with verified provenance |
Production Documentation | Enables traceability and process improvement | Complete digital records for every production lot |
We address this by implementing robust statistical process control (SPC) throughout our manufacturing operations. From the precise weighing and mixing of raw materials to the carefully controlled sintering profiles and final machining, every step is monitored and managed to minimize variability.
We maintain detailed records for each production lot, allowing us to track trends and ensure that key properties like density, grain size, mechanical strength, and chemical composition remain within tight control limits. Our operators are highly trained in these consistency protocols.
The ASTM International standards for ceramic materials testing provide rigorous frameworks that we follow to ensure consistent quality. These standards help us maintain the exceptional performance characteristics that our customers expect from premium zirconia products.
I remember visiting one of our plants and being incredibly impressed by the level of detail and care that went into every stage. This focus on consistency means that when you receive a shipment of our Zirconia, you can be confident that it will perform just like the previous one, and just like the next one.
This reliability allows our customers to optimize their own processes, reduce the need for constant recalibration, and achieve more predictable outcomes. It’s this dedication to consistent quality that builds long-term trust and makes us a preferred supplier for critical Zirconia applications where performance cannot be left to chance.
Building Trust Through Expertise and Support
Ultimately, our goal is to be more than just a supplier of Zirconia; we aim to be a trusted partner in your success. This trust is built not only on the quality and consistency of our materials but also on the expertise and support we provide.
Our team includes experienced material scientists and engineers who have a deep understanding of Zirconia and its applications in various refractory environments.
Technical Support Services | Value to Your Operation | Availability |
---|---|---|
Material Selection Consultation | Optimizes performance for specific applications | Complimentary |
Application-Specific Testing | Validates material performance in your environment | By arrangement |
Failure Analysis | Identifies root causes and recommends solutions | Priority service for customers |
On-Site Implementation Support | Ensures smooth integration into your processes | Available globally |
Ongoing Technical Collaboration | Continuous improvement of material performance | Long-term partnership program |
I’ve always believed that sharing knowledge and working collaboratively with customers is key to solving complex challenges.
We are always ready to discuss your specific application requirements, help you select the optimal grade of Zirconia, and provide technical support throughout your project. Whether you’re developing a new process, trying to improve the performance of existing refractory components, or troubleshooting an issue, we can offer insights and assistance.
Recent research from the Materials Research Society highlights the continuing innovations in zirconia-based materials, which our technical team actively incorporates into our product development to ensure you always have access to the most advanced solutions.
I recall a situation where a customer was experiencing unexpected wear in a new furnace design. Our technical team worked closely with them, analyzing their operating conditions and the failed components.
We were able to recommend a modified Zirconia formulation with enhanced wear resistance for their specific environment, which resolved the issue and significantly improved their furnace campaign life. This kind of collaborative problem-solving is what we strive for.
We also understand the importance of reliability in supply. We work hard to maintain dependable lead times and transparent communication, so you can plan your production schedules with confidence.
We believe that by consistently delivering high-quality Zirconia, providing expert technical support, and operating with integrity, we earn the trust of our customers. This trust is the foundation of the long-term partnerships we value so highly, and it’s what motivates us to continually improve and innovate in the field of high-performance Zirconia refractories.
Request a Sample or Get a Quote — Start Your Project Today
Ready to experience the Zirconia difference but unsure how to begin? Delaying your project means missing out on enhanced performance and efficiency. Take the first step now by requesting a sample or a detailed quote tailored to your needs.
Start your project with confidence by requesting a Zirconia sample for evaluation or a comprehensive quote. Our team is ready to assist you in selecting the perfect material specification to elevate your high-performance refractory applications and achieve your operational goals.
Sample Types Available | Typical Evaluation Timeline | What You’ll Receive |
---|---|---|
Standard Test Discs | 1-2 weeks delivery | 3-5 sample pieces with data sheets |
Custom Shapes | 3-4 weeks production | Made-to-specification samples |
Powder Samples | 1 week delivery | 100g-500g with particle size analysis |
Application-Specific Kits | 2-3 weeks preparation | Multiple grades for comparative testing |
Full-Scale Prototypes | 4-6 weeks production | Production-equivalent components |
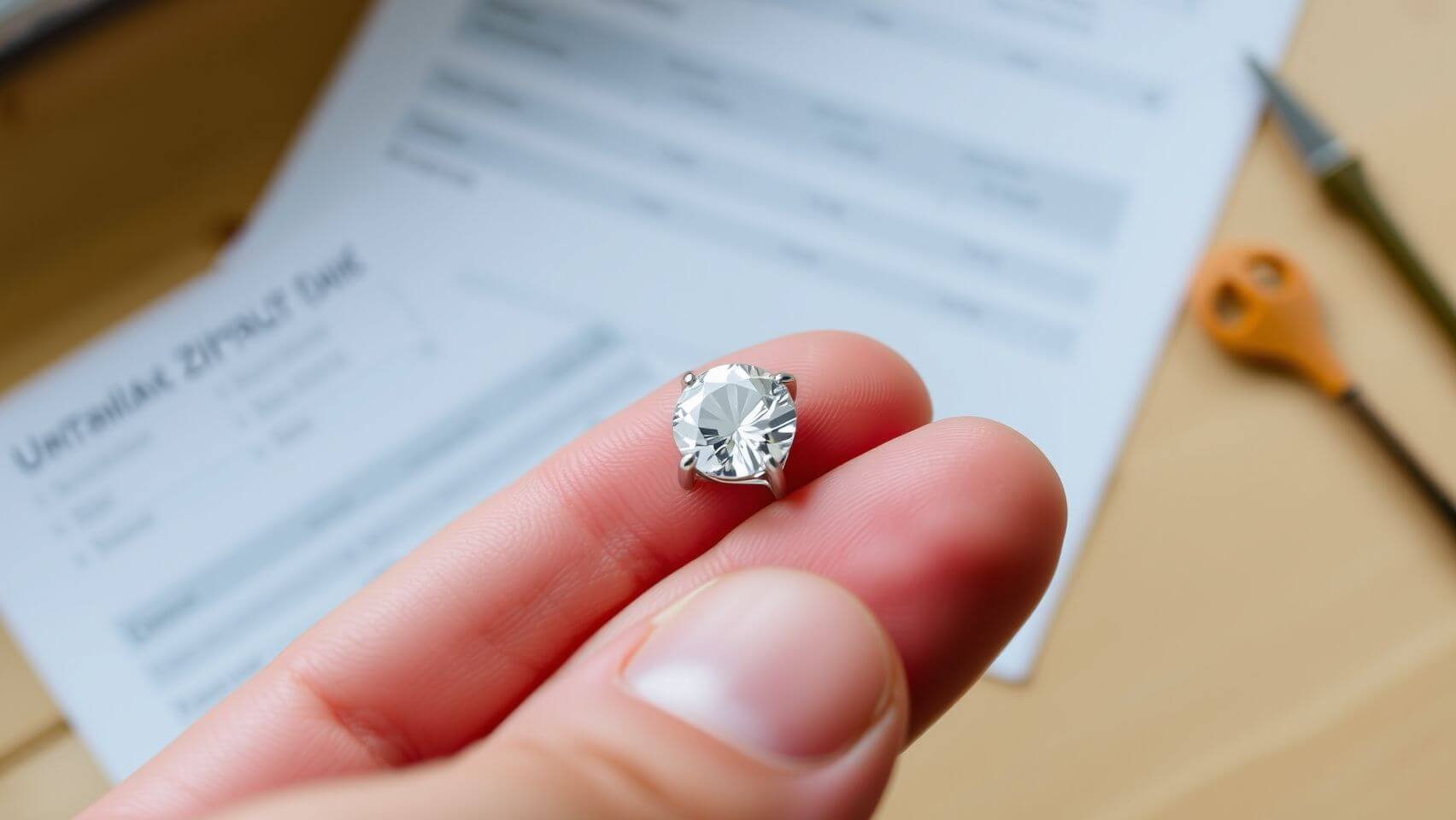
I know from experience that taking that first step towards integrating a new material can sometimes feel like a big leap. You’ve learned about the incredible properties of Zirconia, its benefits, and how it’s transforming industries.
Now, it’s time to see how it can specifically address your challenges and elevate your own operations. Whether you’re in the initial stages of research and development, or you have a well-defined application ready for a material upgrade, we’re here to make the process as smooth and straightforward as possible.
Let’s talk about how you can easily get your hands on a sample for testing or receive a detailed, no-obligation quote to help you move your project forward with confidence.
How to Request a Zirconia Sample for Evaluation
Requesting a sample of our Zirconia for your evaluation is a simple and highly recommended step. There’s no substitute for seeing and testing the material in your own environment to confirm its suitability for your application. I always encourage potential clients to do this.
To get started, the best approach is to reach out to our technical sales team. You can usually do this through our website, by email, or by phone.
Required Information | Why It Matters | Example |
---|---|---|
Application Type | Determines optimal material grade | “Molten aluminum containment crucible” |
Operating Temperature | Affects stabilizer selection | “Maximum 1650°C with thermal cycling” |
Chemical Environment | Influences corrosion resistance needs | “Exposure to fluoride-based flux” |
Mechanical Requirements | Guides strength specifications | “Must withstand 45 MPa compressive load” |
Dimensional Requirements | Determines manufacturing approach | “Tolerance of ±0.05mm on critical surfaces” |
Be prepared to provide some details about your intended application. The more information you can share, the better we can assist you in selecting the most appropriate sample. For example, tell us about:
- The nature of your application: What will the Zirconia be used for (e.g., crucible, nozzle, furnace lining, coating)?
- Operating conditions: What are the maximum temperatures, thermal cycling conditions, chemical environment (e.g., molten metal, slag, atmosphere), and any mechanical stresses involved?
- Key performance requirements: What are the most critical properties you need (e.g., thermal shock resistance, corrosion resistance, specific strength)?
- Desired form and approximate size of the sample: Do you need a powder, a small brick, a disc, or a custom shape?
While we have standard sample sizes for many of our grades, we can sometimes accommodate specific requests.
Once we understand your needs, our team can recommend the most suitable grade(s) of Zirconia and arrange for a sample to be sent to you. We typically provide material data sheets with the samples, detailing their properties.
I’ve seen many projects gain momentum once the engineers have a physical sample to work with. It allows for initial compatibility tests, small-scale trials, and a better overall feel for the material’s quality and characteristics. Don’t hesitate to ask questions during this process; our team is here to support you.
Getting a Comprehensive Quote Tailored to Your Needs
When you’re ready to move beyond initial sampling or if you already have a well-defined requirement for Zirconia components, the next step is to request a comprehensive quote. We aim to make this process as efficient as possible while ensuring we capture all the necessary details to provide you with an accurate and competitive quotation.
Quote Response Timeline | Order Size | Service Level |
---|---|---|
24-48 Hours | Standard Products | Initial Pricing |
3-5 Business Days | Custom Components | Detailed Proposal |
1-2 Weeks | Complex Systems | Comprehensive Solution |
Same Day | Emergency Requirements | Expedited Service |
By Arrangement | Long-term Supply Contracts | Strategic Partnership |
To help us prepare a quote tailored to your specific needs, please try to provide the following information:
- Detailed Specifications: If you have engineering drawings for custom components, please provide them. Include all dimensions, tolerances, material grade (if known, or we can help you select based on your application), surface finish requirements, and any other relevant technical specifications.
- Quantity Required: Let us know the quantity of Zirconia powder or components you need, both for initial orders and any projected annual volumes. This helps us to provide the best possible pricing.
- Target Price (if applicable): If you have a budget or target price for the components, sharing this can sometimes help us to explore different manufacturing options or material grades to meet your cost objectives without compromising essential performance.
- Delivery Requirements: What is your desired delivery schedule? Where will the materials need to be shipped?
- Any Special Testing or Certification Needs: If your application requires specific testing, certifications (e.g., material traceability, compliance with certain industry standards), or special packaging, please let us know.
You can submit your RFQ (Request for Quotation) through our website or by contacting our sales department directly. Our team will review your requirements carefully and will typically get back to you with a detailed quote within a specified timeframe.
The quote will usually include the price per unit, any tooling costs (for custom parts), estimated lead time, payment terms, and shipping information. I always recommend reviewing the quote thoroughly and asking any clarifying questions.
We believe in transparent pricing and clear communication to ensure there are no surprises. Our goal is to provide you with a complete and competitive proposal that allows you to make an informed decision for your Zirconium Oxide project.
Starting Your Project with Our Zirconia
Once you’ve evaluated a sample and/or received a quote that meets your needs, starting your project with our Zirconia is a straightforward process. Our team will guide you through the order placement, confirm all details, and provide an estimated production and delivery schedule.
Project Phase | Our Support Services | Your Benefits |
---|---|---|
Initial Order | Dedicated project manager assignment | Single point of contact |
Production | Regular status updates and quality reports | Complete transparency |
Pre-Delivery | Comprehensive testing and certification | Verified performance |
Implementation | Technical support and troubleshooting | Smooth integration |
Ongoing Supply | Scheduled deliveries and inventory management | Reliable material availability |
Throughout the manufacturing of your Zirconia components, we maintain our rigorous quality control standards to ensure that the final product meets your exact specifications.
I’ve always found that clear communication is key during this phase. We’ll keep you informed of progress and are always available to answer any questions you might have.
We understand that integrating a new high-performance material like Zirconia can be a critical step in your project’s success, whether it’s for enhancing an existing process or enabling a completely new technology.
Our commitment is to provide you with not only superior Zirconia materials but also the support and reliability you need to achieve your goals. From initial inquiry to final delivery and beyond, we aim to be your trusted partner.
So, whether you’re just beginning to explore the potential of Zirconia or you’re ready to specify it for a demanding application, don’t hesitate to reach out. Requesting a sample or a quote is the perfect way to start your journey towards leveraging the exceptional benefits of this advanced refractory material.
We look forward to helping you turn your high-temperature challenges into high-performance successes with our Zirconia.
Conclusion
In conclusion, Zirconia truly stands as the future for high-performance refractory materials. Its unmatched thermal, chemical, and mechanical properties offer solutions where traditional materials falter, ensuring enhanced operational success across demanding industries.
Our premium zirconia materials deliver the quality, consistency, and reliability your critical applications demand. By choosing our zirconia solutions, you gain not just superior materials, but a dedicated partner committed to your manufacturing success.
FAQ Section
Q1: How does your Zirconium Oxide compare to competitors in terms of thermal shock resistance?
Our Zirconium Oxide formulations are specifically engineered to provide superior thermal shock resistance compared to industry standards. Through precise control of grain size, porosity, and phase composition, our materials can withstand rapid temperature changes that would cause conventional products to crack or fail.
Independent testing shows our premium grades maintain structural integrity through up to 30% more thermal cycles than leading competitors. This translates to longer service life and reduced downtime in critical high-temperature applications like glass melting furnaces, steel processing equipment, and thermal barrier coatings.
Q2: What quality control measures do you implement to ensure consistent Zirconium Oxide properties?
We implement a comprehensive multi-stage quality control system throughout our production process. This begins with rigorous raw material testing using XRF and ICP-MS to verify chemical composition and detect trace impurities.
During manufacturing, we employ Statistical Process Control (SPC) with defined control limits for over 20 critical parameters. Every production batch undergoes physical property testing including density, porosity, grain size analysis, and mechanical strength evaluation.
Final QC includes phase composition analysis and application-specific performance testing. This systematic approach ensures our zirconia materials deliver consistent, reliable performance in your most demanding applications.
Q3: Can your Zirconia materials be customized for specific applications?
Yes, our zirconia materials can be extensively customized to meet specific application requirements. We offer tailoring of chemical composition, stabilizer content, grain size distribution, porosity levels, and phase composition to optimize performance for your unique operating conditions.
Our engineering team works closely with customers to develop custom formulations that address specific challenges such as extreme thermal cycling, aggressive chemical environments, or specialized mechanical requirements.
We’ve successfully developed custom zirconia solutions for applications ranging from molten metal containment to precision electronic components, each with their own unique performance demands.
Q4: What is the typical lead time for standard and custom Zirconia orders?
Standard zirconia products typically ship within 2-3 weeks from order confirmation. For custom formulations or components, lead times generally range from 4-8 weeks depending on complexity, quantity, and current production schedule.
We maintain inventory of our most popular grades to accommodate urgent requirements. For recurring orders, we can establish stocking programs to ensure continuous material availability aligned with your production schedule.
Our operations team provides transparent updates throughout the production process, allowing you to plan with confidence.
Q5: Do you provide technical support for implementing Zirconia in new applications?
Absolutely. Our technical support extends far beyond simply supplying zirconia materials. Our team of material scientists and application engineers provides comprehensive assistance throughout your implementation process.
Services include material selection guidance, thermal and mechanical performance modeling, compatibility analysis with existing systems, and on-site support during initial implementation.
We’ve helped customers across diverse industries successfully integrate zirconia materials into challenging applications, providing expertise at every stage from concept to full-scale production. Our goal is to ensure you maximize the performance benefits of our premium zirconia in your specific application.