In today’s high-tech manufacturing landscape, zirconia materials have gained significant attention due to their exceptional performance and diverse application potential. For procurement managers and technical decision-makers, selecting appropriate zirconia materials not only affects product quality but directly impacts production efficiency and long-term costs. However, faced with numerous zirconia materials options in the market, making informed procurement decisions becomes challenging. This article provides a comprehensive guide to evaluating and sourcing zirconia materials, helping you make optimal choices in a complex supply chain environment.
Key Characteristics of Premium Zirconia Materials
As an advanced ceramic material, zirconia materials possess performance characteristics that directly determine application effectiveness. Premium zirconia materials typically feature the following key properties:
● Chemical purity: High-quality zirconia materials usually contain over 99% ZrO₂, with impurities strictly controlled within specific ranges. Purity directly affects material stability and performance consistency.
● Microstructure: Grain size, distribution uniformity, and porosity are important indicators for evaluating zirconia materials quality. Premium zirconia typically has fine, uniform grain structure (<0.5μm) and extremely low porosity (<0.1%).
● Mechanical properties: Including hardness (typically >1200HV), flexural strength (>900MPa), and fracture toughness (>5MPa·m½). These parameters determine the reliability and service life of the material in practical applications.
● Thermal properties: Thermal expansion coefficient, thermal conductivity, and thermal shock resistance are key indicators for assessing zirconia materials stability in temperature-varying environments.
● Stabilizer type and content: Different stabilizers (such as Y₂O₃, MgO, or CaO) and their content significantly affect the phase stability and mechanical properties of zirconia materials.
The table below shows a comparison of typical performance parameters for different grades of zirconia materials:
Performance Parameter | Industrial Grade Zirconia | High-Purity Zirconia | Ultra-High-Purity Zirconia |
---|---|---|---|
ZrO₂ Content | >95% | >99% | >99.9% |
Hardness (HV) | 900-1100 | 1200-1300 | >1300 |
Flexural Strength (MPa) | 700-850 | 900-1100 | >1100 |
Fracture Toughness (MPa·m½) | 4-5 | 5-7 | 7-10 |
Porosity | <1% | <0.5% | <0.1% |
Typical Applications | General industrial components | Precision mechanical parts | Medical implants, high-end electronics |
Understanding these key characteristics and their evaluation standards is the first step in procuring premium zirconia materials. In the actual procurement process, you should determine which performance parameters are most critical based on specific application requirements and establish corresponding material specification requirements accordingly.
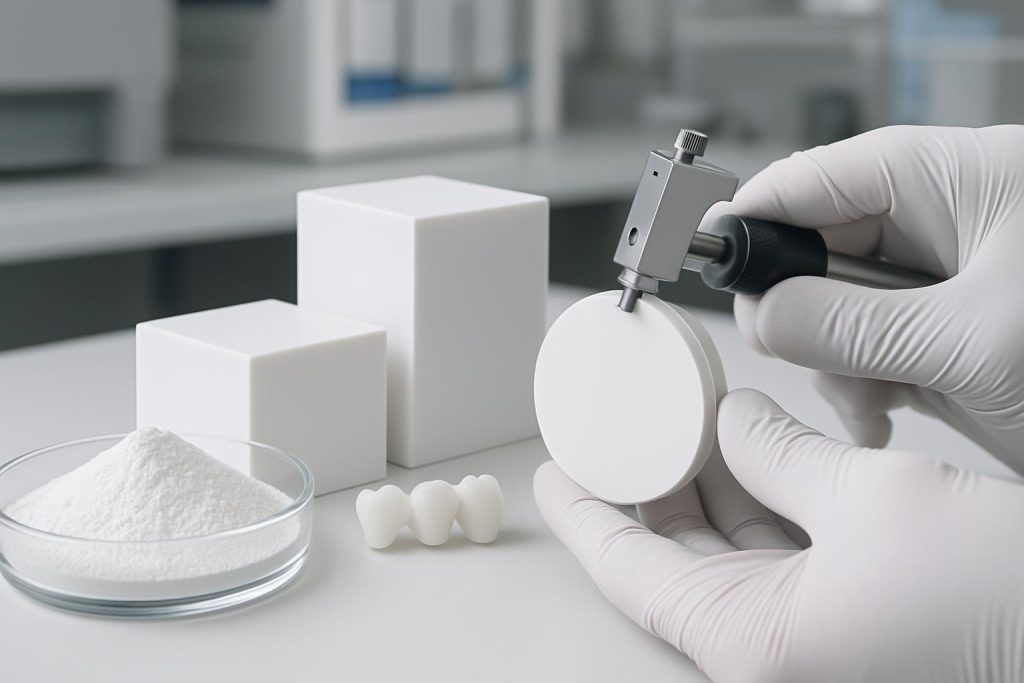
How to Determine Which Zirconia Materials Your Application Needs
Selecting suitable zirconia materials begins with clarifying application requirements. Different types of zirconia materials are suitable for different application scenarios. Blindly pursuing high specifications may lead to unnecessary cost increases, while insufficient specifications may cause performance issues.
● Application environment analysis: Thoroughly assess the temperature range, mechanical load, chemical environment, and service life requirements of the working environment. For example, high-temperature applications (>1000°C) typically require fully stabilized zirconia (FSZ), while applications subject to mechanical impact are more suitable for partially stabilized zirconia (PSZ).
● Performance priority ranking: Clarify which performance parameters are most critical for your application. Is it wear resistance, flexural strength, thermal shock resistance, or chemical stability? Different zirconia materials excel in different aspects.
● Cost-benefit analysis: Evaluate the balance point between material performance improvement and cost increase. In some applications, mid-grade zirconia materials may be sufficient without investing in higher-cost premium materials.
● Compatibility considerations: Consider the compatibility of zirconia materials with other system components, including thermal expansion matching, chemical compatibility, and mechanical connection methods.
Below is a simplified decision tree for zirconia materials selection:
- Determine working temperature range
- <500°C: Consider TZP or Mg-PSZ
- 500-1000°C: Consider Mg-PSZ or Y-TZP
- >1000°C: Consider FSZ or specialized high-temperature zirconia
- Assess mechanical load requirements
- High impact/high stress: Prioritize Mg-PSZ
- High hardness/wear resistance requirements: Prioritize Y-TZP
- Moderate mechanical requirements: Standard PSZ may be sufficient
- Analyze chemical environment
- Strong acidic environment: Select high-purity Y-TZP or FSZ
- Strong alkaline environment: Consider zirconia with special surface treatments
- Neutral/weakly corrosive environment: Most zirconia types are suitable
- Consider economic factors
- High-end applications/critical components: Choose high-purity customized zirconia
- Standard industrial applications: Commercial-grade zirconia is usually sufficient
- Large volume/cost-sensitive applications: Consider composite zirconia or lower-cost alternatives
Avoid common selection mistakes such as over-specification (increasing unnecessary costs) or under-specification (leading to premature failure). After determining the material type, it’s advisable to conduct small-scale testing and validation, especially for new applications or critical components.
Core Criteria for Evaluating Zirconia Materials Suppliers
Choosing the right zirconia materials supplier is as important as selecting the right material. A reliable supplier not only provides high-quality zirconia materials but also offers valuable technical support and solutions. Here are the core criteria for evaluating zirconia materials suppliers:
● Production capacity and quality control: Suppliers should have comprehensive production facilities and strict quality control systems. ISO 9001 certification is a basic requirement, while industry-specific certifications (such as ISO 13485 for medical-grade zirconia) provide additional reference value.
● Technical expertise: Assess the supplier’s technical team strength, including the qualifications and experience of material scientists and engineers. Excellent suppliers can provide material selection advice, application support, and problem-solving solutions.
● R&D capabilities: Suppliers with R&D capabilities typically offer more advanced materials and customized solutions. Learn about the supplier’s R&D investment, number of patents, and innovation history.
● Supply chain stability: Evaluate the supplier’s raw material sources, production flexibility, and inventory strategies. In the context of global supply chain fluctuations, supply stability becomes particularly important.
● Customer references and market reputation: Learn about the supplier’s performance from existing customers, particularly regarding product consistency, delivery reliability, and after-sales support.
● Price transparency and cost structure: Quality suppliers typically provide clear price structures and quantity discount policies, avoiding hidden costs and non-transparent charges.
Below is an example of a supplier evaluation matrix:
Evaluation Dimension | Weight | Supplier A | Supplier B | Supplier C |
---|---|---|---|---|
Product Quality | 30% | 4.5 | 4.0 | 3.5 |
Technical Support | 20% | 4.0 | 4.5 | 3.0 |
Supply Stability | 15% | 3.5 | 4.0 | 4.5 |
Price Competitiveness | 15% | 3.0 | 3.5 | 4.5 |
Innovation Capability | 10% | 4.5 | 4.0 | 3.0 |
Industry Experience | 10% | 4.5 | 3.5 | 3.0 |
Weighted Total | 100% | 4.1 | 4.0 | 3.6 |
In the evaluation process, it’s recommended to adopt a multi-round screening strategy: first screen based on basic qualifications and product range, then conduct in-depth evaluation through detailed technical exchanges and sample testing, and finally verify the supplier’s actual performance through small-batch trials. Establishing long-term relationships is usually more beneficial for ensuring material quality and supply stability than frequently changing suppliers.
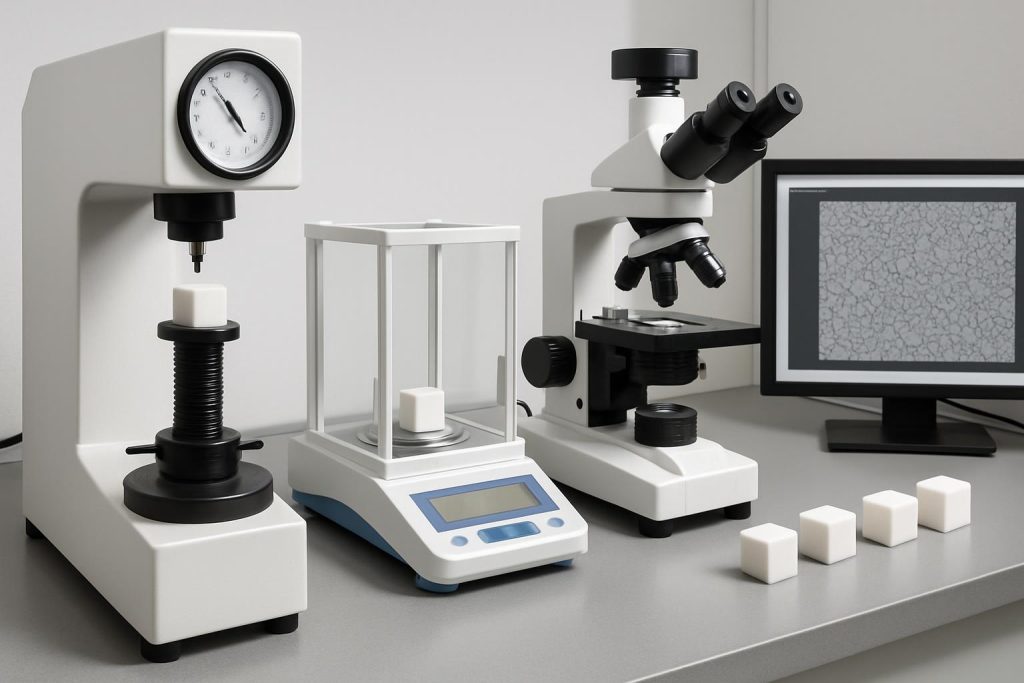
How to Verify the Quality and Performance of Zirconia Materials
When procuring zirconia materials, you cannot rely solely on supplier promotional materials and technical data sheets. A systematic quality verification process is essential to ensure that purchased materials meet expected requirements. Here are the key steps for verifying the quality and performance of zirconia materials:
● Material certificate review: Thoroughly check material certificates (COA/COC) to confirm that chemical composition, physical characteristics, and mechanical properties meet specification requirements. Pay attention to batch information and consistency of testing methods.
● Third-party testing: Conduct independent third-party testing verification for key parameters, especially for first-time procurement or critical applications. Common tests include XRD analysis (confirming phase composition), SEM observation (microstructure), and mechanical performance testing.
● Sample evaluation procedure: Establish standardized sample evaluation procedures, including appearance inspection, dimensional measurement, density determination, and simple performance tests. For samples from different batches, the same evaluation criteria should be used for comparison.
● Small-scale application testing: Before full adoption, conduct small-scale actual application testing, simulating real-use conditions to evaluate material performance in the actual environment.
● Long-term performance monitoring: Establish long-term performance monitoring mechanisms to record material performance data in actual applications, providing reference for future procurement decisions.
The table below lists common zirconia materials testing methods and their applicable scenarios:
Testing Method | Test Parameters | Applicable Scenarios | Recommended Standards |
---|---|---|---|
X-ray Diffraction (XRD) | Phase composition, crystal structure | Phase stability assessment | ASTM E975 |
Scanning Electron Microscopy (SEM) | Microstructure, grain size | Quality control, failure analysis | ISO 13383 |
Three-point/Four-point Bending Test | Flexural strength | Mechanical performance evaluation | ISO 14704 |
Vickers Hardness Test | Hardness | Wear resistance evaluation | ISO 6507 |
Thermal Expansion Coefficient Determination | Thermal expansion characteristics | Thermal application assessment | ASTM E228 |
Chemical Immersion Test | Chemical stability | Corrosive environment applications | ASTM C1285 |
During the verification process, special attention should be paid to the following points:
- Ensure test conditions match the actual application environment
- Focus on consistency and stability between batches
- Pay attention not only to average values but also to performance distribution and extreme values
- For critical applications, consider conducting accelerated aging tests
- Establish complete test records and databases for traceability and comparison
Through a systematic verification process, material quality risks can be effectively reduced, ensuring that the procured zirconia materials meet application requirements.
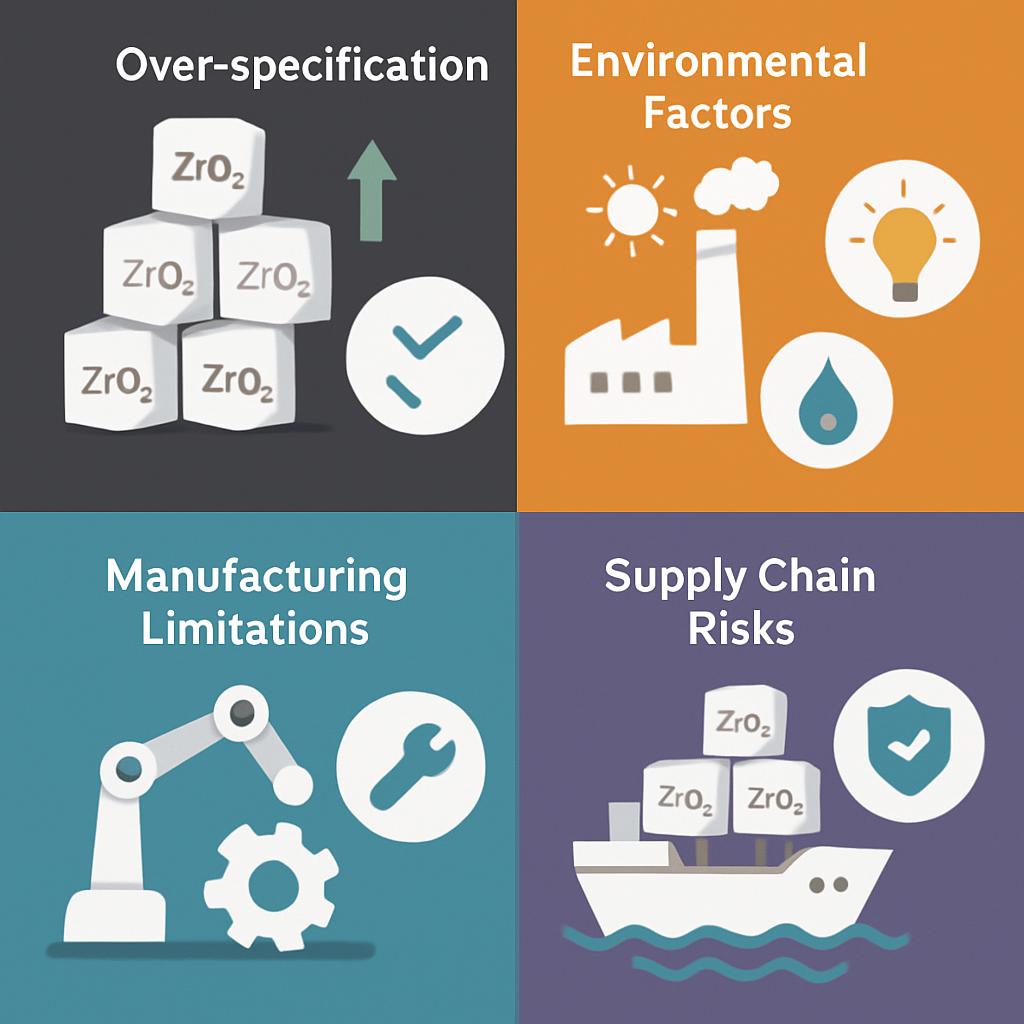
Common Pitfalls in Zirconia Materials Procurement and Avoidance Strategies
In the zirconia materials procurement process, many procurement personnel easily fall into common pitfalls, leading to undesirable procurement results. Understanding these pitfalls and mastering corresponding avoidance strategies can help you make more informed procurement decisions.
● Price pitfall: Excessive focus on initial procurement price while neglecting total cost of ownership. Low-priced zirconia materials may have issues such as poor consistency in quality and unstable performance, leading to increased maintenance costs or premature product failure.
Avoidance strategy: Adopt a total cost of ownership (TCO) analysis method, comprehensively considering factors such as material lifespan, maintenance requirements, and downtime losses. For critical applications, it’s better to choose moderately priced but reliable materials.
● Specification pitfall: Blindly pursuing high specifications or copying specification requirements from other applications, leading to over-specification or specification mismatch.
Avoidance strategy: Develop reasonable material specifications based on specific application requirements, avoiding unnecessary high specification requirements. Work with material experts and supplier technical teams to determine the most suitable material specifications.
● Supply chain pitfall: Over-reliance on a single supplier, increasing the risk of supply disruption.
Avoidance strategy: Establish a diversified supplier network, maintaining at least two qualified suppliers. For critical materials, consider establishing safety stock or signing long-term supply agreements.
● Technology pitfall: Blindly adopting new zirconia materials or new technologies, neglecting technology maturity and applicability assessment.
Avoidance strategy: Take a cautious approach to new materials or technologies, requiring suppliers to provide sufficient test data and successful case studies. Consider phased introduction of new materials, first validating in non-critical applications.
● Contract pitfall: Neglecting key clauses in contracts, such as quality assurance, delivery conditions, intellectual property, etc.
Avoidance strategy: Develop comprehensive procurement contract templates, clearly specifying quality standards, acceptance conditions, responsibility definitions, and dispute resolution mechanisms. For large procurements, consider involving legal professionals.
Here’s a case analysis demonstrating how to identify and avoid pitfalls in zirconia procurement:
A manufacturing company chose a lower-priced zirconia materials supplier to reduce costs. Initially, this decision saved approximately 30% in material procurement costs. However, six months later, components produced using these materials began experiencing premature failure issues, leading to increased customer complaints, rising repair costs, and damaged brand reputation. In-depth analysis revealed that the low-priced materials had poor batch consistency and unstable microstructure, issues that were not obvious in standard testing but gradually manifested during actual use.
Eventually, the company reassessed its zirconia materials suppliers, selecting a moderately priced but quality-stable supplier and establishing stricter material acceptance standards. Although initial costs increased by 20%, product lifespan doubled, total cost of ownership actually decreased by 15%, and customer satisfaction significantly improved.
This case illustrates that in zirconia materials procurement, decisions should not be purely price-driven but should adopt a comprehensive evaluation approach, focusing on long-term material performance and total cost of ownership.
How to Optimize the Total Cost of Ownership for Zirconia Materials
When procuring zirconia materials, wise decisions focus not only on initial procurement prices but also consider the total cost of ownership (TCO) throughout the material’s lifecycle. Optimizing TCO can help enterprises maximize long-term cost-effectiveness while ensuring performance.
● Lifecycle cost analysis: Comprehensively assess all relevant costs of zirconia materials throughout their entire use cycle, including initial procurement costs, installation/processing costs, operating costs, maintenance costs, downtime losses, and final disposal costs.
● Batch optimization strategy: Determine optimal procurement batch sizes based on demand forecasts, inventory costs, and supply risks. Large-batch procurement typically offers more favorable prices but also increases inventory costs and obsolescence risks.
● Balance between standardization and customization: Evaluate the cost-effectiveness of standard zirconia materials versus customized solutions. Standard materials are typically lower in price and more stable in supply, but customized materials may provide better performance and longer service life in specific applications.
● Supplier cooperation models: Explore strategic cooperation models with key suppliers, such as long-term supply agreements, joint development projects, or risk-sharing mechanisms, to obtain more favorable price conditions and technical support.
● Inventory management optimization: Implement scientific inventory management strategies, balancing inventory costs with supply risks. Consider vendor-managed inventory (VMI) or consignment inventory models to reduce inventory costs.
The table below shows the main components of the total cost of ownership for zirconia materials and their typical proportions:
Cost Category | Typical Proportion | Optimization Strategy |
---|---|---|
Initial Procurement Cost | 40-60% | Batch procurement, long-term agreements, multi-supplier competition |
Processing/Installation Cost | 10-20% | Select materials with better processing performance, optimize design |
Maintenance/Replacement Cost | 15-30% | Choose longer-life, higher-quality materials |
Downtime/Failure Cost | 5-15% | Improve material reliability, establish preventive maintenance plans |
Inventory/Logistics Cost | 5-10% | Optimize inventory levels, improve supply chain management |
A case study can provide a more intuitive understanding of TCO optimization value:
A precision instrument manufacturer originally used mid-grade zirconia materials (unit price $100/piece), with an annual usage of 1,000 pieces, an average material lifespan of 2 years, and labor and downtime costs for each replacement approximately 50% of the material cost. After comprehensive evaluation, the manufacturer decided to switch to premium zirconia materials (unit price $150/piece), with the new material’s average lifespan extended to 5 years.
Original solution TCO (5-year cycle):
- Material cost: $100 × 1,000 pieces × (5 years ÷ 2 years) = $250,000
- Replacement cost: $50 × 1,000 pieces × (5 years ÷ 2 years) = $125,000
- Total cost: $375,000
New solution TCO (5-year cycle):
- Material cost: $150 × 1,000 pieces × (5 years ÷ 5 years) = $150,000
- Replacement cost: $50 × 1,000 pieces × (5 years ÷ 5 years) = $50,000
- Total cost: $200,000
By choosing higher-grade zirconia materials, despite a 50% increase in initial cost, the 5-year total cost decreased by approximately 47%, while also reducing replacement frequency and related operational disruptions.
Optimizing the TCO of zirconia materials requires cross-departmental collaboration, including procurement, engineering, production, and finance departments jointly participating in the decision-making process. Establishing comprehensive cost tracking and performance monitoring systems can provide strong support for future procurement decisions.
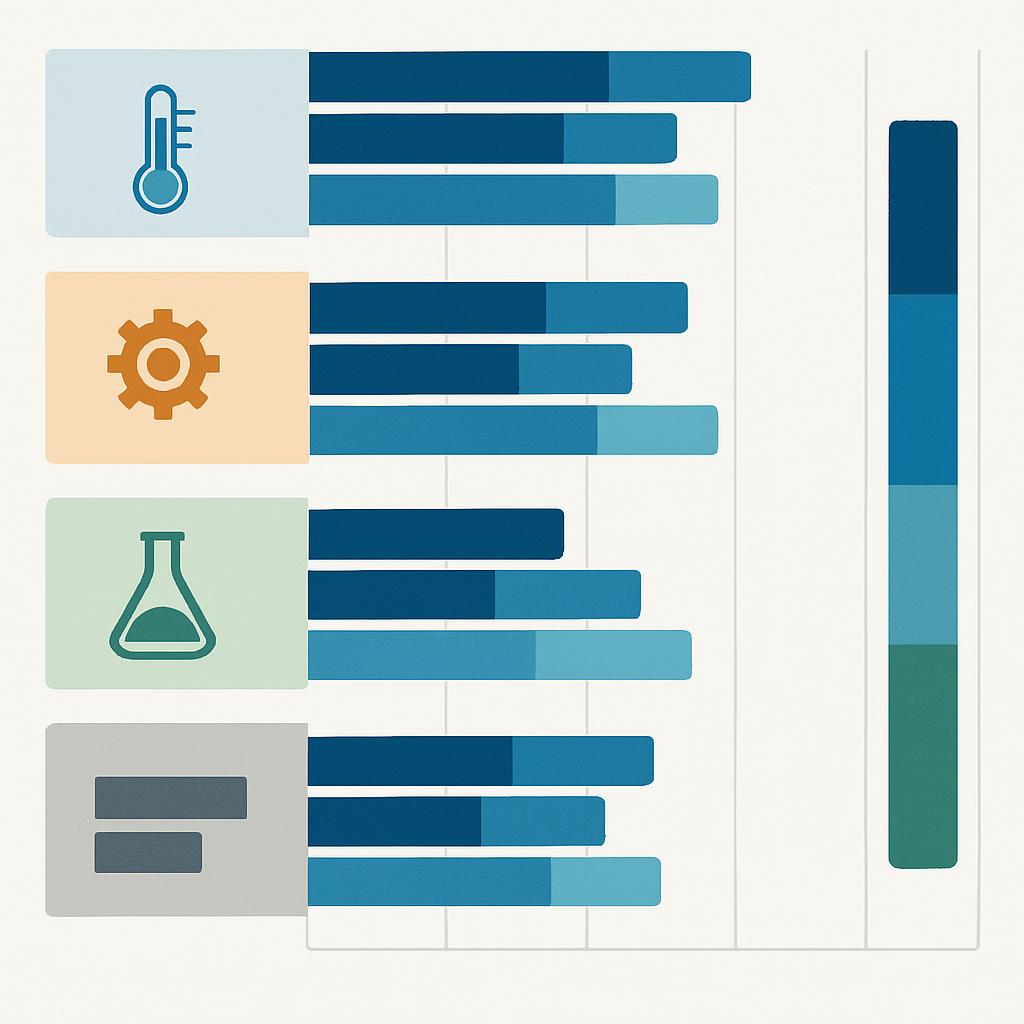
Zirconia Materials Market Trends and Future Development Directions
Understanding the latest trends and future development directions in the zirconia materials market is crucial for formulating long-term procurement strategies and seizing technological innovation opportunities. Here are the main trends and development directions in the zirconia materials field:
● Global supply chain restructuring: Influenced by geopolitics and the pandemic, the zirconia materials supply chain is undergoing significant adjustments. Policy changes in major producing countries, raw material supply fluctuations, and rising transportation costs are driving supply chain diversification and regionalization.
● Expansion into emerging application fields: Zirconia materials are expanding into more emerging fields, such as 5G communication infrastructure, renewable energy equipment, aerospace, and additive manufacturing. These new applications place higher demands on material performance and create market opportunities for innovative zirconia materials.
● Sustainable development and environmental requirements: Increasingly stringent environmental regulations and the popularization of sustainable development concepts are driving the green transformation of zirconia materials production processes. Low-energy production processes, recyclable material design, and full lifecycle assessment are becoming new industry trends.
● Growth in customized and functionalized materials: Standard zirconia materials struggle to meet the needs of specific applications, driving the development of customized and functionalized zirconia materials. Composite zirconia, functionally graded materials, and surface-modified zirconia are innovative products gaining market share.
● Application of digital technologies: Digital technologies are increasingly widely applied in zirconia materials research, development, production, and quality control. AI-assisted material design, digital twin production lines, and online quality monitoring systems are changing traditional material production and procurement models.
FAQ Section
Q1: How to distinguish between different grades of zirconia materials?
Premium zirconia materials can be distinguished through multiple indicators: first is purity, with quality materials typically containing >99% ZrO₂; second is stabilizer type and content, such as precise ratios of Y₂O₃, MgO, or CaO; third is microstructural characteristics, including grain size (typically <0.5μm), uniformity, and porosity (premium quality <0.1%); fourth is mechanical performance indicators, such as hardness (>1200HV), flexural strength (>900MPa), and fracture toughness (>5MPa·m½). Additionally, batch consistency is a key indicator for distinguishing premium zirconia materials suppliers.
Q2: What test certificates should be requested when procuring zirconia materials?
When procuring premium zirconia materials, suppliers should be asked to provide the following test certificates: chemical composition analysis reports (confirming main components and impurity content); physical property test reports (density, porosity, grain size); mechanical performance test reports (hardness, flexural strength, fracture toughness); batch consistency reports (proving production stability); and additional tests that may be required for special applications (such as biocompatibility, thermal shock performance, or electrical properties). Ideally, these tests should be performed or verified by independent third-party laboratories and comply with relevant international standards such as ASTM or ISO standards.
Q3: What factors primarily determine price differences in zirconia materials?
Price differences in zirconia materials are mainly influenced by the following factors: raw material purity (higher-purity zirconium sources cost more); stabilizer type and content (rare earth stabilizers like Y₂O₃ cost more than MgO or CaO); processing complexity (precision forming and special sintering processes increase costs); batch size (small-batch custom products are significantly more expensive than large-batch standard products); special performance requirements (such as ultra-high purity or special microstructure); and supplier brand premiums and service levels. Prices may differ by 5-10 times, but higher prices typically reflect better performance, consistency, and reliability.
Q4: How to assess a zirconia supplier’s technical support capabilities?
Key indicators for evaluating zirconia materials suppliers’ technical support capabilities include: the professional background and experience of the technical team (in relevant fields such as materials science, ceramic engineering); depth of application engineering support (ability to provide customized solutions for specific applications); response speed and problem-solving ability; completeness and quality of technical documentation; laboratory and testing facility configuration; relationships with research institutions; and history of successful cases. It’s recommended to comprehensively assess suppliers’ technical support capabilities through technical consultation meetings, reference customer interviews, and small-scale pilot projects.
Q5: How to balance quality and cost considerations when procuring zirconia materials?
Balancing zirconia materials quality and cost requires a systematic approach: first, clearly define the critical performance requirements for the application, distinguishing between “necessary” and “ideal” characteristics; second, calculate total cost of ownership rather than just considering initial price, including service life, maintenance requirements, and downtime costs; third, consider tiered procurement strategies, using premium materials for critical applications and more cost-effective options for non-critical applications; fourth, establish long-term relationships with suppliers, reducing costs through batch commitments and technical cooperation; finally, regularly evaluate the market and new technologies to ensure procurement strategies align with industry best practices. The optimal balance point is typically not the cheapest option but the most cost-effective solution that reliably meets application requirements.