In manufacturing processes, understanding how particle size distribution (PSD) affects zircon powder performance is crucial. Buyers and decision-makers often face challenges in ensuring optimal product quality and efficiency. This article addresses your concerns by offering insights into the relationship between PSD and performance, presenting practical solutions to enhance product results. With years of industry expertise, we aim to provide reliable, data-driven information that will assist you in making informed decisions about your zircon powder applications.
How Does Particle Size Distribution Impact Performance?
Particle size distribution (PSD) describes the range and frequency of different sizes of particles in a material. In the case of zircon powder, PSD plays a vital role in determining how the powder behaves during processing and in final applications.
A key aspect of PSD is its importance in the manufacturing process. If you have an uneven distribution of particle sizes, you can encounter issues like poor flow characteristics and inconsistent packing density. These problems can lead to variations in product performance, potentially resulting in inferior outcomes.
Key parameters for evaluating PSD include:
● Mean particle size – This average size helps to understand how the overall particle characteristics align with intended use.
● Uniformity index – This measure indicates how closely the particle sizes cluster around the mean, affecting stability and performance.
● Particle size distribution curve – This visual representation provides insight into the range of particle sizes and helps identify issues or opportunities for optimization.
Understanding these parameters allows manufacturers to select appropriate materials and processes, ensuring superior outcomes.
What Are the Effects of Particle Size on Zircon Powder?
The effects of particle size on zircon powder can significantly influence various physical properties. When particles are smaller, their surface area increases, which can change how the material behaves in applications.
One key relationship is between particle size and physical properties. Smaller zircon particles may offer improved reactivity due to their larger surface area, while larger particles might provide better mechanical strength.
Moreover, particle size influences flowability and packing density. When dealing with fine particles, you might experience better packing but poorer flow characteristics. Therefore, balancing these attributes is crucial.
Key influences of particle size include:
- Mechanical Strength: Larger particles often withstand higher stresses, making them ideal for high-load applications.
- Reactivity: Smaller particles typically exhibit higher reactivity, beneficial in ceramic applications.
- Thermal Conductivity: Fine particles can provide lower thermal conductivity, advantageous in insulation applications.
As you can see, the relationship between particle size and performance is multifaceted, highlighting the need to carefully consider your specific requirements for zircon powder applications.
How Does Particle Size Distribution Affect Process Efficiency?
While assessing the impact of particle size distribution, it’s essential to understand how it affects processing efficiency. Various processing techniques can be influenced by the PSD of zircon powder.
During processing, the role of PSD is critical. For instance, in mixing and compaction processes, an even distribution can lead to better homogeneity and consistent properties. On the flip side, uneven distributions can cause segregation, leading to inconsistencies in the final product.
The connection between PSD and energy consumption is another factor worth considering. If you have a narrow PSD, the energy needed for processing tends to decrease because smaller particles fit together more efficiently. In contrast, a wide PSD may require additional energy to achieve the desired properties.
Furthermore, the right PSD can minimize wastage during processing. With careful selection and management of particle sizes, you can reduce the need for reworking or additional processing steps, ultimately saving time and resources.
Summary of PSD Influence on Process Efficiency:
Aspect | Impact |
---|---|
Mixing and Compaction | Better homogeneity with even PSD |
Energy Consumption | Less energy with narrow PSD |
Waste Reduction | Minimized need for rework |
In summary, optimizing PSD not only enhances product performance but also significantly boosts process efficiency, making it a valuable area of focus.performance but also significantly boosts process efficiency, making it a valuable area of focus.
What Are the Applications of Zircon Powder?
Zircon powder finds various applications across multiple industries, each with specific performance requirements. Understanding where and how zircon powder is used can help you appreciate the importance of PSD in these contexts.
In the ceramics industry, zircon powder is a preferred choice due to its thermal stability and strength. Here, PSD plays a critical role, with fine particles providing a smooth finish, while larger particles can enhance structural integrity.
In glass manufacturing, zircon powder serves as a glazing material. The ideal PSD ensures consistent melting and flow during glass production, leading to superior quality finishes.
Foundry applications also utilize zircon powder, especially in making molds. The properties of the powder, influenced by its PSD, are crucial for achieving precise shapes and high-quality castings.
Specific use cases requiring special PSD include:
- High-performance ceramics that need uniform strength and lighter weight.
- Dental ceramics relying on flawless finishes and precise models for creating high-quality restorations.
- Refractory materials where thermal stability is essential for high-temperature applications.
Understanding these applications underscores the necessity of selecting the correct PSD for zircon powder to achieve optimized performance across industries.
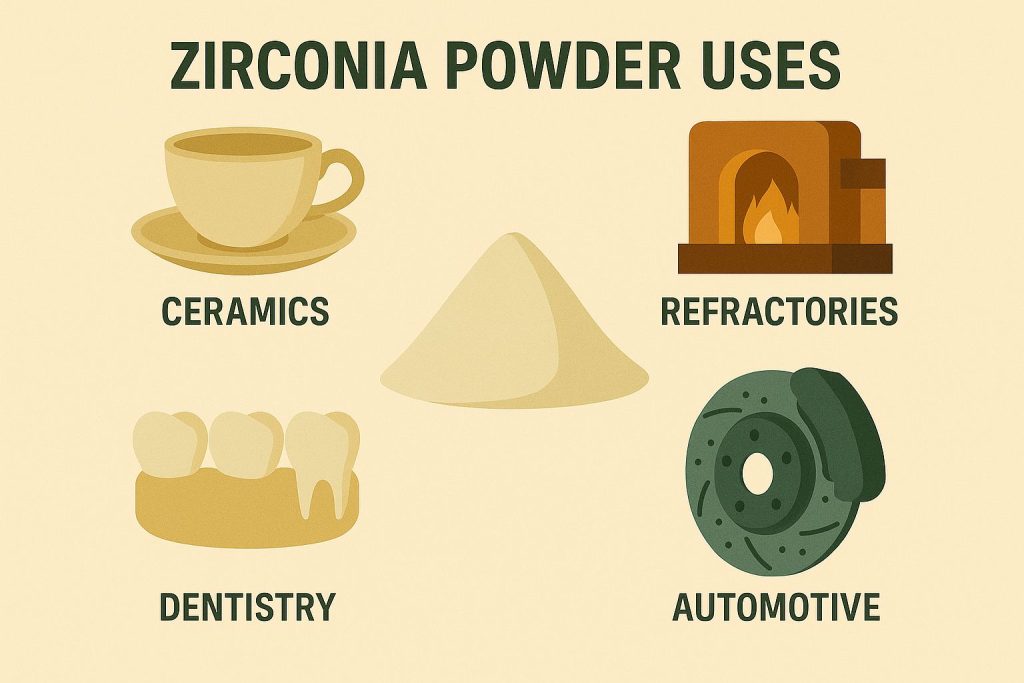
How Can You Control Particle Size Distribution?
Controlling particle size distribution is essential to achieving optimal performance for zircon powder in various applications. If you are looking to adjust the PSD, there are several techniques you can utilize.
One effective method includes mechanical milling, a common technique for reducing particle size. By adjusting the milling time, speed, and equipment type, you can achieve desired PSD characteristics.
Another option is sieving, which allows you to separate particles based on their sizes. This approach is particularly useful for achieving a narrower size range for enhanced flowability.
Techniques for Adjusting PSD:
Technique | Description |
---|---|
Mechanical Milling | Reduces particle size through controlled grinding |
Sieving | Separates particles using screens |
Additives | Modifies physical properties |
In addition to physical techniques, additives can also help in modifying PSD. These materials can enhance the flow characteristics of finer powders or improve packing density.
Best practices in laboratory settings for controlling PSD involve frequent monitoring and assessment of the particle size using advanced techniques like laser diffraction. By maintaining consistency and understanding key variables, you can achieve and control the desired PSD effectively.
Ultimately, having a thorough understanding of these methods enables you to manage and optimize the particle size distribution of zircon powder, leading to improved performance metrics.and optimize the particle size distribution of zircon powder, leading to improved performance metrics.
Why Is Consistency in Particle Size Distribution Important?
Maintaining consistency in particle size distribution is paramount for ensuring product quality and reliability. Variation in PSD can lead to significant problems in processing and end product performance.Uniformity in PSD directly affects product quality. If there are inconsistencies, you may find that the final product exhibits variable strength, reactivity, and performance characteristics. This inconsistency can lead to customer dissatisfaction and potential costs.
Key Implications of PSD Variability:
Implication | Effect |
---|---|
Product Quality | Inconsistent results |
Yield and Efficiency | Increased wastage |
Compliance | Risk of failing to meet standards |
Moreover, variations in PSD can also impact yield and efficiency. For instance, if larger clumps of zircon powder occur, you may need to reprocess those materials or face increased scrap rates. This inefficiency can lead to wasted resources and higher production costs.
Recognizing industry standards and specifications is also important. Many applications, especially in sectors like aerospace or healthcare, have stringent requirements regarding material properties. Meeting these standards is essential for compliance, safety, and reliability.
In conclusion, prioritizing consistency in PSD not only enhances the quality and reliability of zircon powder but also ensures that production processes are efficient, cost-effective, and compliant with industry standards.
What Methods Are Used to Analyze Particle Size Distribution?
Analyzing particle size distribution is crucial for understanding how zircon powder will behave in various applications. There are several common methods used to measure PSD, each offering unique advantages.
Laser diffraction is a widely used method that provides rapid and highly accurate particle size analysis. It measures how particles scatter light, giving precise results regarding size distribution.
Sieve analysis is another traditional technique where a series of sieves with different mesh sizes are used to separate particles. While it is straightforward and cost-effective, it may not offer the resolution of more advanced methods.
Additional methods to consider:
- Dynamic light scattering: Effective for nanoscale or ultra-fine particles, this technique provides valuable information about very small particles in suspension.
- Image analysis: This method uses cameras and digital processing to assess particle shapes and sizes effectively.
Here is a summary of key measurement techniques:
Technique | Advantage | Disadvantage |
---|---|---|
Laser diffraction | Rapid and precise | Requires calibration |
Sieve analysis | Straightforward and cheap | Limited resolution |
Dynamic light scattering | Effective for small sizes | More complex setup |
Image analysis | Offers shape data | Costlier equipment |
Each method has its pros and cons, and selecting the appropriate technique largely depends on the specific requirements for studying zircon powder. This knowledge will enable you to gather accurate data for optimizing PSD and enhancing performance.
How Can Particle Size Distribution Be Optimized?
Optimizing particle size distribution for zircon powder can lead to better performance and efficiency in applications. Understanding the strategies you can implement is key to achieving desired outcomes.
One typical approach is to adjust milling parameters. By changing factors such as duration, speed, and type of milling equipment, you can significantly influence the resulting PSD.
Using additives to modify particle size can also be effective. These can improve flow characteristics or adjust physical properties to suit specific applications.
Realize that optimizing PSD often involves trade-offs. For instance, while finer particles may enhance reactivity, they may also lead to issues with agglomeration. In such cases, finding that balance is essential, and this can often be achieved through appropriate formulation adjustments.
Here are key strategies for optimization:
- Regular Testing: Frequent testing of PSD can help detect variations early in the process.
- Batch Control: Implementing batch control strategies can help ensure consistency throughout production runs.
- Employee Training: Training employees on best practices for handling and processing zircon powder can greatly improve outcomes.
For effective optimization, consider monitoring your materials closely and making iterative adjustments. This approach helps identify the ideal conditions for achieving the most beneficial particle size distribution for your specific needs.
Ultimately, focusing on PSD optimization ensures that you improve performance and value across zircon powder applications.
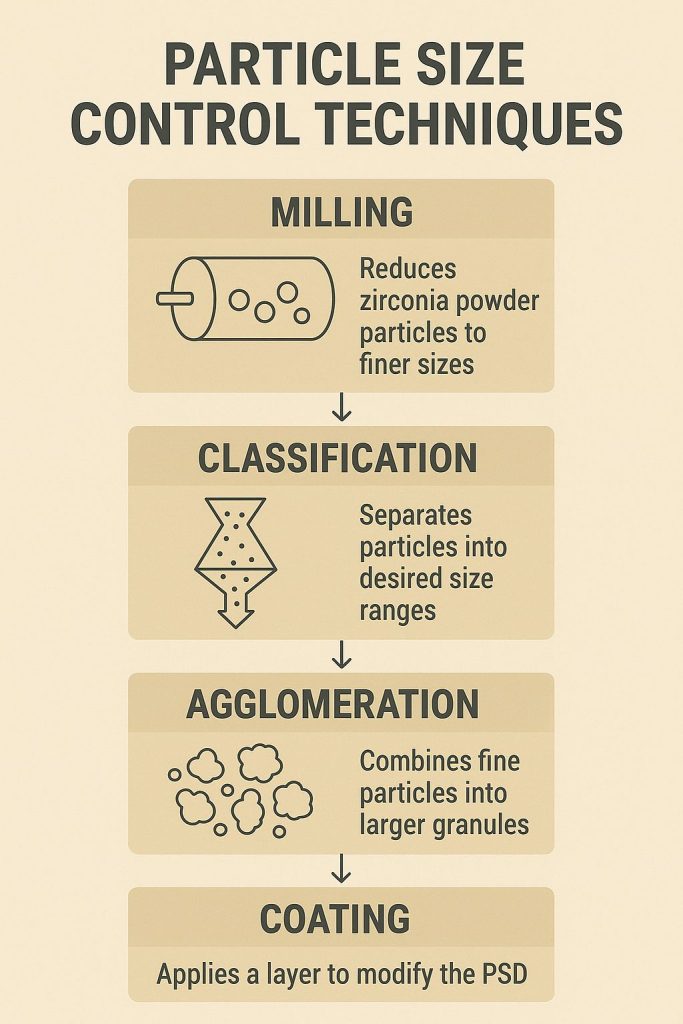
What Challenges Are Associated With Managing PSD?
Managing particle size distribution comes with its own set of challenges that industry professionals must navigate to achieve optimal outcomes. Understanding these challenges is vital for successful applications of zircon powder.
One common issue is maintaining uniformity during production. Variations in processing techniques, temperature, and raw material inconsistencies can create fluctuations in PSD, leading to unpredictable results.
Another significant challenge is effective screening for large batches of zircon powder. Inadequate separation can result in unwanted agglomerations or inconsistencies that affect performance.
Consider some of these challenges:
- Technical Limitations: Equipment may reach limitations in efficiency or precision, affecting the process.
- Environmental Factors: Humidity and temperature can affect material properties and processing efficiency.
- Cost Pressures: Balancing cost-efficiency with the need for high-quality materials can be challenging.
Implementing corrective measures can also be complicated. Once variations occur, identifying and rectifying the cause requires careful analysis and may involve process adjustments or additional testing.
To overcome these challenges, consider establishing strict quality control protocols that encompass regular monitoring of PSD throughout the production process.
By being proactive, you can minimize the effects of variation and enhance the reliability and performance of zircon powder applications.
How Do Trends in Particle Size Research Affect Industry?
Keeping up with recent trends in particle size research is essential for industry professionals. The advancements can significantly influence how zircon powder is produced and utilized.
Recent research focuses on nanoscale materials and their applications, pushing the boundaries of what is possible with particle size manipulation. This trend has led to the development of zircon powders with unique characteristics that improve their utility in various applications.
Emerging technologies also have a role in this evolution. Innovations in processing equipment can enhance the ability to control and optimize PSD more effectively than before.
Notable trends include:
- Real-time monitoring technologies: These allow for continuous PSD monitoring during production cycles.
- Biomimetic processes: New techniques that mimic natural processes for creating particles with desired characteristics.
- Sustainable methods: Research into eco-friendly techniques for producing and using zircon powder.
Future directions may include further development of smart materials that adapt to changing conditions based on their particle configuration. This evolution could significantly impact how industries utilize zircon powder.
In summary, staying informed about the latest trends ensures that you can leverage advancements to improve applications and maintain a competitive edge in the market.
Conclusion
In this article, we explored the impact of particle size distribution on zircon powder performance. Key insights revealed the significance of managing and optimizing PSD for enhanced product quality, process efficiency, and consistency. By focusing on these aspects, businesses can experience improved outcomes and satisfaction.
For tailored solutions in managing zircon powder performance, connect with Global Industry today. Our expertise will provide you with the tools and resources to enhance your applications successfully.
FAQ Section
Q1: What is particle size distribution (PSD) and why is it important for zircon powder?
A1: Particle size distribution (PSD) refers to the range and distribution of particle sizes within a material. For zircon powder, PSD is crucial as it affects the material’s reactivity, flowability, and final properties in various applications. A well-controlled PSD can lead to better processing and enhanced performance in final products.
Q2: How does the particle size of zircon powder impact its applications?
A2: The particle size of zircon powder can significantly influence its properties and suitability for different applications. Smaller particles generally offer increased surface area, which can enhance reactivity and improve performance in applications such as ceramics, refractories, and dental materials. Conversely, larger particles may provide better mechanical strength in specific contexts.
Q3: What are the typical applications of zircon powder?
A3: Zircon powder is widely used in ceramics, refractories, and foundry molds, as well as in the production of zirconium metal and zirconium compounds. Its excellent thermal stability and resistance to corrosion make it valuable in high-heat applications like glassmaking and in the aerospace industry.
Q4: How can I determine the right zircon powder for my needs?
A4: Selecting the right zircon powder depends on the specific requirements of your application, such as desired particle size, purity, and any special performance characteristics. Consulting with a supplier or expert in zircon materials can help you identify the best product for your needs.
Q5: Where can I purchase high-quality zircon powder?
A5: High-quality zircon powder can be purchased through specialized suppliers and manufacturers. It’s essential to choose a reputable supplier that provides detailed specifications and quality assurance for their products to ensure optimal performance in your applications.