Zircon sand is a vital material used in industries like ceramics, foundry casting, and electronics. But buyers often face confusion when choosing between natural and purified zircon sand. This decision impacts product quality, processing efficiency, and cost structure. The challenge is understanding how each type differs—not just in appearance, but in performance, sourcing, and reliability.
This article addresses that concern head-on. It compares the two types in depth and helps you determine which one better suits your specific industrial use. With insights into procurement, testing, and cost analysis, this guide is written for buyers, engineers, and plant managers who need facts—not fluff. Here’s what you’ll gain: a better grasp of zircon sand categories, the ability to ask the right questions when purchasing, and more confidence when dealing with vendors or planning production.
What defines natural zircon sand versus purified?
Natural zircon sand is mined directly from zircon-rich deposits, often located near coastal regions or ancient geological formations. The material is then washed and sieved, but not chemically treated. This means it retains its native mineral impurities. These often include traces of ilmenite, rutile, and silica. Depending on the source, the impurity levels may range between 5% to 10%.
Purified zircon sand undergoes additional refining to remove those unwanted components. This process increases the zirconium silicate content, often to 98% or higher. Purification typically involves chemical leaching, magnetic separation, and sometimes high-temperature treatment to adjust grain structure.
Here’s the point: the difference isn’t just chemical—it’s operational. Natural zircon may work well for basic foundry uses, while purified zircon delivers greater consistency and optical clarity for ceramics and electronics.
Property | Natural Zircon Sand | Purified Zircon Sand |
---|---|---|
Zirconium Silicate (%) | 85–95 | 98+ |
Common Impurities | Ilmenite, Rutile | <1% (varies) |
Grain Shape | Irregular | Controlled |
Industrial Use | Refractory, Casting | Ceramics, Electronics |

This image compares raw and purified zircon under magnification, showing purity and texture differences.
How is zircon sand typically purified?
Purifying zircon sand involves multiple steps designed to isolate zirconium silicate. These methods vary depending on the quality of the mined material and end-use requirements. Processing typically begins with size grading and magnetic separation to remove iron-bearing minerals. High-tension separators then eliminate conductors like rutile and monazite.
The next step is chemical leaching. Hydrochloric or sulfuric acid removes residual iron, aluminum, and silica. The sand may also be calcined—heated to high temperatures—to improve crystallinity and phase stability.
Why does this matter? Because impurities not only affect color or composition but also impact thermal expansion, melting behavior, and grain sintering in ceramics.
Purification comes with costs—both financial and environmental. Chemical treatments generate waste streams that must be managed. That said, the result is a product suitable for demanding applications, where failure could mean costly production rework.
Purification Step | Function |
---|---|
Magnetic Separation | Removes iron-rich minerals |
Electrostatic Sorting | Segregates conductive particles |
Acid Leaching | Dissolves chemical impurities |
Calcination | Stabilizes grain structure |
What industries use each type of zircon sand?
Zircon is a multipurpose material, but different sectors have different purity and particle size demands. Foundries, for instance, use natural zircon because it meets thermal needs and is cost-efficient. In contrast, the ceramics industry depends on high-purity grades to maintain surface finish and glaze quality.
Let’s break it down:
Natural zircon is mainly used in:
- Investment casting molds
- Glass manufacturing
- Refractory bricks and crucibles
Purified zircon is preferred for:
- Ceramic tiles and sanitaryware
- Precision electronic components
- Dental ceramics and optical coatings
The use case dictates the material. A ceramics factory seeking smooth tile finishes can’t afford micro-impurities that affect gloss. A foundry, on the other hand, benefits from lower costs and tolerates some impurity.
Industry | Preferred Zircon Type | Reason |
---|---|---|
Foundry | Natural | High thermal stability, cost-effective |
Ceramics | Purified | Visual quality, whiteness |
Electronics | Purified | Insulation, fine grain |
Glass & Refractory | Natural | Bulk thermal use |
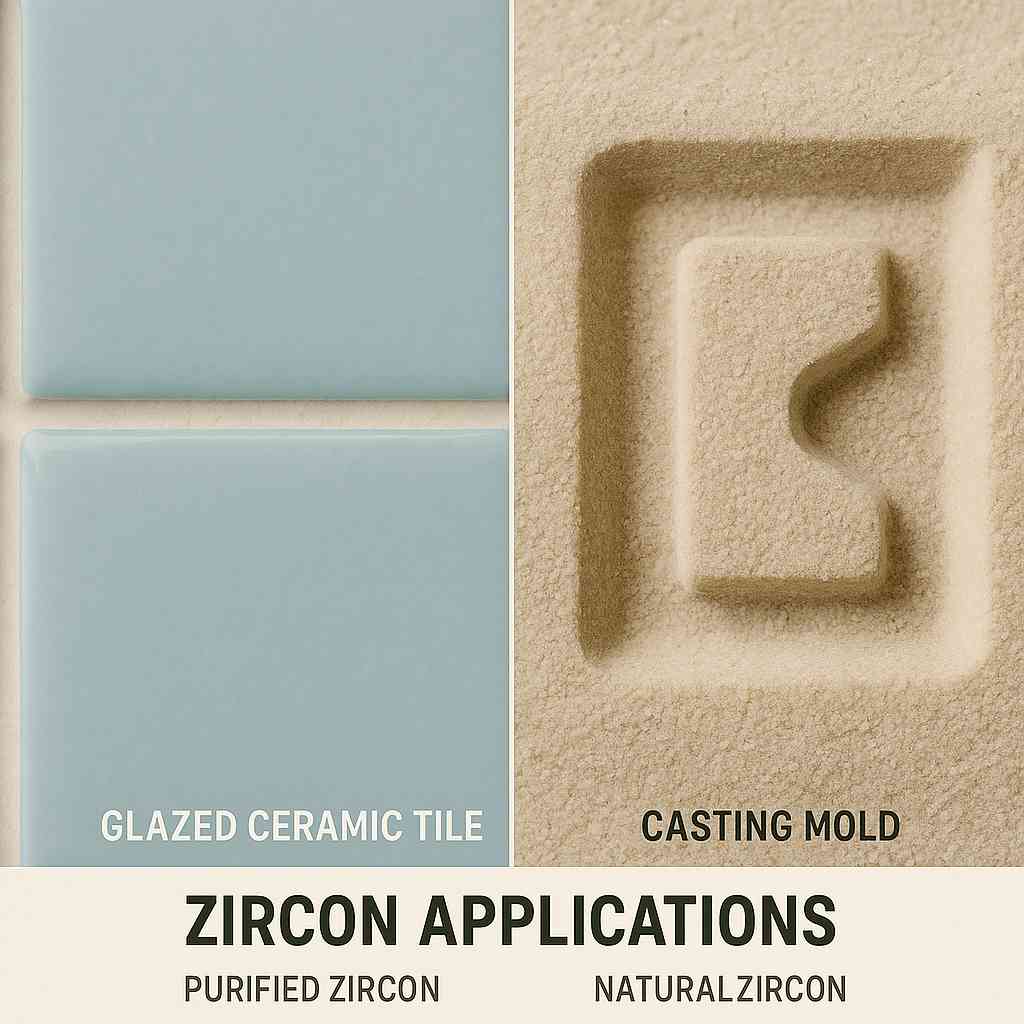
This image shows purified zircon in tile glazing and natural zircon in casting molds side by side.
How do physical properties differ between the two?
The physical properties of zircon sand influence how it performs under high heat, pressure, or chemical exposure. Purified zircon typically features smaller, more uniform particles. That makes it ideal for processes requiring precise control, such as inkjet ceramic printing or dielectric coating.
Natural zircon, being closer to its mined state, shows more variation. This can affect its flowability, packing density, and melting profile. While this inconsistency might disqualify it for microelectronics, it’s perfectly usable in bulk refractory systems.
So, what’s the impact? Impurities can discolor ceramic glaze. Irregular shapes affect mold integrity in casting. Inconsistent particle size can block spray systems. Purified zircon avoids those issues, but at a cost.
Property | Natural Zircon | Purified Zircon |
---|---|---|
Particle Size | Varies | Narrow range |
Flowability | Moderate | High |
Melting Point | Slightly lower | Higher stability |
Color | Brownish to gray | White to pale |
What are the cost differences and value trade-offs?
Natural zircon is cheaper because it involves fewer processing steps. The price difference can range from 20% to 40% depending on grade and volume. But price alone doesn’t tell the full story.
Think of it this way: if you’re manufacturing decorative porcelain tiles, surface defects from mineral contamination might cost more in rejected product than you’d save on raw materials. On the other hand, if you’re producing crucibles for steel casting, the aesthetic doesn’t matter—cost does.
This makes evaluating total lifecycle cost critical. Downtime, rework, and customer returns often trace back to materials that didn’t meet performance needs.
Comparison Factor | Natural Zircon | Purified Zircon |
---|---|---|
Unit Cost (per ton) | Lower | Higher |
Yield Consistency | Variable | Predictable |
Defect Risk | Higher | Lower |
ROI in High-Finish Use | Low | High |
How do these differences affect procurement choices?
Procurement teams must align technical requirements with budget and supply stability. The type of zircon selected needs to match not just the product but also the production environment.
Let’s look at the real-world considerations:
- RFQs should specify purity level, grain size, and origin.
- Certification (e.g., ISO 1248) may be required for some applications.
- Bulk buyers often contract suppliers with dual-sourcing: both natural and purified.
A misstep in specifying the wrong type could mean equipment failure or customer complaints. That’s why many procurement departments work directly with technical staff or use third-party labs to test incoming batches.
Procurement Checklist | Description |
---|---|
Purity Requirement | Define acceptable impurity range |
End Use Application | Casting, glazing, electronics, etc. |
Volume Needed | Consider bulk discounts |
Storage and Shelf Conditions | Moisture control and packaging type |
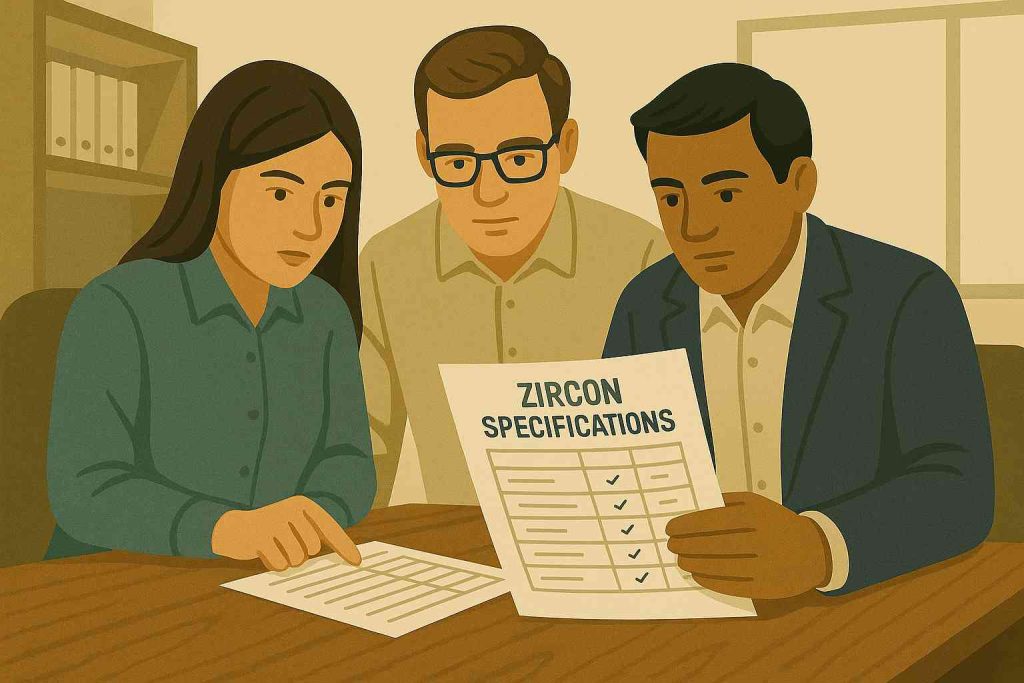
This image shows a procurement team verifying zircon specification sheets in a factory office.
Are there environmental or regulatory concerns?
Yes, especially with purification. Chemical leaching creates waste streams that require proper disposal. Some countries regulate this strictly, and suppliers must adhere to environmental standards.
Natural zircon mining also affects the landscape. Sediment runoff and habitat disruption are major concerns in coastal regions. However, certified suppliers adopt better practices to minimize damage.
What’s the takeaway? Buyers are increasingly asked to prove sourcing compliance. You may need traceability documents, REACH/ROHS declarations, or sustainability certifications.
Risk Area | Natural Zircon | Purified Zircon |
---|---|---|
Mining Impact | High (local disruption) | Moderate (post-mining) |
Chemical Waste | Low | High |
Regulation Intensity | Medium | High |
Certification Required | Sometimes | Often |
What testing methods verify zircon sand quality?
Testing confirms that what you ordered is what you got. Most labs follow standards like ISO 1248 or ASTM C876. These tests cover chemical composition, grain size, moisture content, and loss on ignition.
You can perform in-house checks or outsource to third parties. For large purchases, most buyers demand batch-level certificates with each shipment.
Let’s be clear: A high price doesn’t guarantee quality. A test report does.
Test Type | What It Verifies |
---|---|
XRF Spectrometry | Chemical makeup |
Sieve Analysis | Grain size distribution |
Moisture Content | Stability and storage risk |
Bulk Density | Packing efficiency |
Conclusion
Here’s what matters now. Choosing between natural and purified zircon sand affects everything from process consistency to product quality. This article gave you technical and economic insights to guide that choice. You’ve seen where each grade fits best—and how to source and validate it correctly. For your next material purchase, work with Global Industry. Our team supports B2B clients with verified materials, clear documentation, and global sourcing options. Contact us now for product sheets or samples tailored to your specific industrial need.
FAQ
Q1: Can natural zircon sand be used in ceramics?
It can, but lower purity may affect brightness and structural integrity. Purified zircon is typically preferred for high-end ceramic production.
Q2: Is purified zircon always better for casting?
Not necessarily. In some foundry applications, natural zircon provides sufficient performance at a lower cost.
Q3: Does purified zircon have a longer shelf life?
Shelf life depends more on storage conditions than purity. However, purified zircon is less likely to absorb moisture or degrade.
Q4: How can I tell if zircon is truly purified?
Request a technical data sheet or material certification with purity percentages, typically 98%+ for purified zircon.
Q5: What is the average cost difference between the two?
Purified zircon usually costs 20–40% more due to added processing, but the performance gains can justify the price in critical applications.