Manufacturing managers across various sectors face constant pressure to boost product quality while cutting costs. Many struggle with material limitations that hamper production efficiency and product performance. Zirconium silicate offers remarkable solutions for numerous industrial applications, combining exceptional thermal stability with outstanding mechanical properties.
Manufacturing professionals who understand zirconium silicate applications gain competitive advantages through improved product durability, reduced maintenance costs, and enhanced production efficiency. This guide examines how this remarkable material solves common industrial challenges across advanced industries.
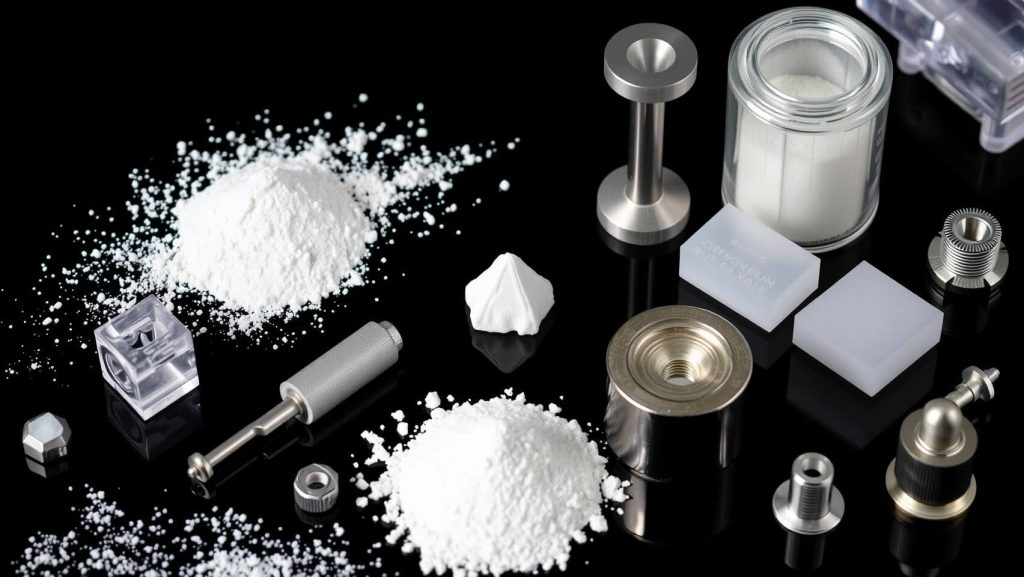
Fine white zirconium silicate powder displayed alongside various industrial components made with this material, showing its versatility across manufacturing sectors
1. Why Should Manufacturing Managers Consider Zirconium Silicate?
Manufacturing managers constantly hunt for materials that deliver superior performance without excessive costs. Zirconium silicate stands out among industrial compounds thanks to its exceptional combination of properties that address multiple production challenges simultaneously. This naturally occurring mineral, with chemical formula ZrSiO₄, possesses remarkable characteristics that make it invaluable across numerous industrial applications.
Property | Zirconium Silicate | Aluminum Oxide | Silicon Carbide | Significance |
---|---|---|---|---|
Mohs Hardness | 7.5 | 9.0 | 9.5 | Determines wear resistance and abrasion applications |
Melting Point (°C) | 2,550 | 2,072 | 2,730 | Critical for high-temperature stability |
Thermal Expansion Coefficient (10⁻⁶/°C) | 4.1 | 8.1 | 4.0 | Lower values reduce thermal stress during cycling |
Chemical Stability (pH range) | 2-14 | 4-9 | 3-14 | Determines resistance to corrosive environments |
When compared with other industrial materials, zirconium silicate demonstrates clear advantages in specific applications. Unlike aluminum oxide, it exhibits lower thermal expansion, reducing stress during heating cycles. Compared to silicon carbide, it offers better chemical stability in certain environments while typically coming at lower cost. These performance differences matter tremendously when selecting materials for critical components or processes where failure carries significant consequences.
Cost analysis reveals zirconium silicate delivers exceptional value despite its moderate price point. One refractory manufacturer documented 40% longer service life for kiln components after switching to zirconium silicate-based materials, translating to substantial savings through reduced replacement frequency and minimized production downtime.
2. How Does Zirconium Silicate Enhance Ceramic Production?
Ceramic manufacturers face persistent challenges producing consistent, high-quality products that meet increasingly stringent performance specifications. Zirconium silicate addresses these challenges through its exceptional thermal properties and contribution to material strength.
The high-temperature stability of zirconium silicate ranks among its most valuable attributes for ceramic applications. With a melting point exceeding 2,500°C, it maintains structural integrity throughout typical firing processes. More importantly, its low thermal expansion coefficient minimizes internal stresses during heating and cooling cycles. This property prevents cracking and warping that plague ceramics made with materials having mismatched expansion rates. Manufacturers report significantly reduced rejection rates after incorporating zirconium silicate into their formulations, with one tile producer noting defect reduction exceeding 30%.
Wear resistance improvements stem from zirconium silicate’s exceptional hardness and mechanical strength. When incorporated into ceramic bodies, it creates microstructural reinforcement that dramatically enhances abrasion resistance. Laboratory tests demonstrate ceramics containing 10-15% zirconium silicate withstand up to three times more abrasive wear than comparable formulations without this additive.
A precision ceramics manufacturer specializing in components for industrial pumps incorporated zirconium silicate into their formulation after experiencing premature wear issues with conventional materials. The reformulated components demonstrated 2.5 times longer service life in abrasive slurry applications, allowing their customers to extend maintenance intervals significantly.
3. What Makes Zirconium Silicate Crucial for Foundry Applications?
Foundry operations present some of manufacturing’s most demanding material challenges. Extreme temperatures, chemical reactivity, and mechanical stresses create environments where only exceptional materials survive. Zirconium silicate proves indispensable in these settings through multiple performance advantages.
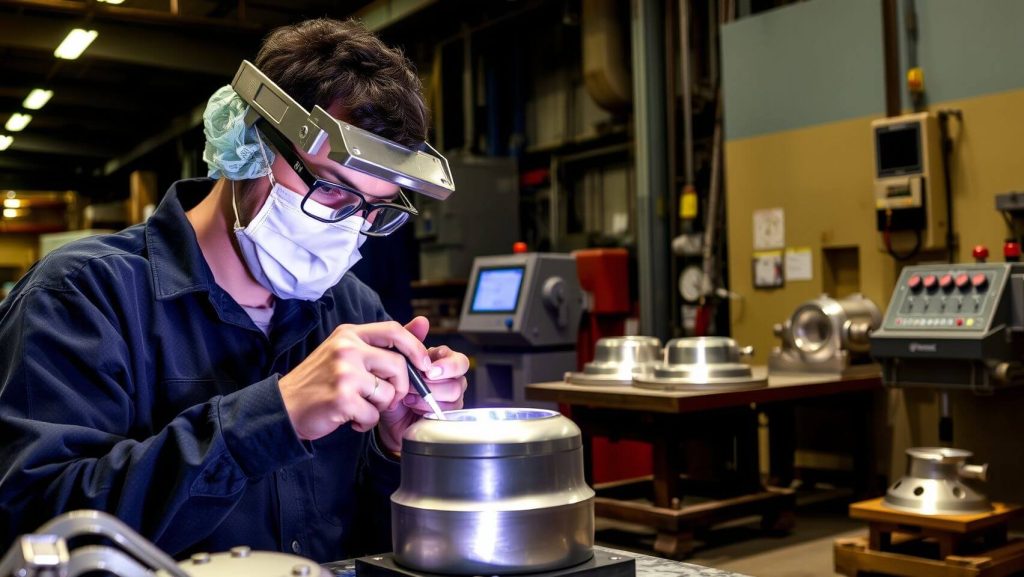
Foundry technician inspecting a precision metal casting produced using zirconium silicate mold technology, highlighting the smooth surface finish and dimensional accuracy
The refractory performance of zirconium silicate in foundry applications stems from its remarkable thermal stability and resistance to chemical attack. When used in mold facings and cores, it maintains dimensional accuracy despite exposure to molten metal temperatures. Unlike many alternative materials, it resists fluxing reactions with metal oxides that typically degrade refractory surfaces. Foundries report mold life extensions of 40-60% after switching to zirconium silicate-based facings for aluminum and copper alloy casting operations.
Surface quality improvements represent another major benefit for foundry operations. Metal castings produced using zirconium silicate mold components typically exhibit smoother surfaces with fewer defects. This advantage stems from the material’s fine particle size, uniform thermal characteristics, and minimal gas generation during casting. Manufacturers note significant reductions in post-casting finishing operations after implementing zirconium silicate in their molding systems, with one automotive components foundry documenting a 25% decrease in grinding and polishing labor.
Metal Type | Casting Temperature (°C) | Recommended Zirconium Silicate Grade | Mold Life Improvement |
---|---|---|---|
Aluminum Alloys | 660-750 | Fine (45-75μm), 99% purity | 45% longer service life |
Copper Alloys | 950-1,200 | Medium (75-150μm), 98.5% purity | 60% longer service life |
Iron (Gray/Ductile) | 1,150-1,300 | Coarse (150-300μm), 98% purity | 40% longer service life |
4. How Can Zirconium Silicate Improve Refractory Materials?
Refractory materials form the literal foundation of many high-temperature industrial processes, from steel production to glass manufacturing. These critical materials must withstand extreme thermal, chemical, and mechanical stresses while maintaining dimensional stability. Zirconium silicate dramatically enhances refractory performance through multiple mechanisms that address common failure modes and extend service life.
When added to refractory formulations, zirconium silicate particles create a dispersed phase that interrupts crack propagation pathways, enhancing thermal shock resistance. The material’s low thermal expansion coefficient reduces internal stresses during heating and cooling cycles, preventing the formation of microcracks that eventually lead to catastrophic failure. Additionally, its chemical inertness prevents reactions with process materials that typically degrade refractory surfaces over time.
Steel manufacturers report ladle lining life extensions of 30-50% after incorporating zirconium silicate into their refractory systems. Glass melting furnaces achieve similar improvements, with one manufacturer documenting 45% longer campaigns between rebuilds after reformulating their tank blocks with zirconium silicate additions. These service life extensions translate directly to reduced maintenance costs and increased production uptime, delivering substantial operational savings.
Laboratory testing shows zirconium silicate-enhanced refractories typically demonstrate 40-60% greater thermal shock resistance than conventional materials, measured through standardized quench testing protocols. Corrosion resistance improves by similar margins, particularly against alkaline slags and glass melts that rapidly attack traditional refractories.
5. Why Is Zirconium Silicate Preferred in Advanced Coating Systems?
Advanced coating systems protect critical components across numerous industries, extending service life and enhancing performance under challenging conditions. Zirconium silicate plays an increasingly important role in these sophisticated coatings, delivering unique combinations of properties that address specific application requirements.
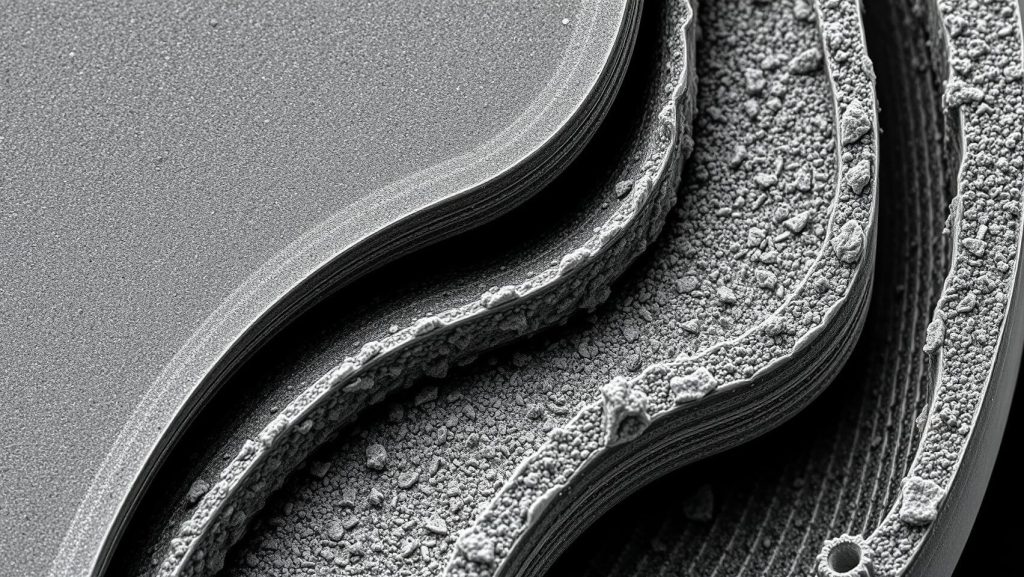
Microscopic cross-section view of a multi-layer industrial coating with zirconium silicate particles, showing the protective barrier against corrosion and wear
The hardness and wear resistance enhancement mechanisms of zirconium silicate-based coatings stem from both particle characteristics and coating microstructure. With Mohs hardness of 7.5, zirconium silicate particles provide direct abrasion resistance when incorporated into coating matrices. More importantly, they create composite structures that distribute mechanical stresses effectively, preventing crack initiation and propagation. These mechanisms combine to produce coatings that withstand severe abrasive conditions that would rapidly degrade conventional alternatives.
Corrosion resistance represents another major advantage driving zirconium silicate adoption in advanced coating systems. The material demonstrates exceptional chemical stability across a wide pH range, resisting attack from both acidic and alkaline environments. When properly incorporated into coating formulations, it creates barrier layers that prevent corrosive media from reaching substrate materials. One chemical manufacturer reported quadrupling pump component life after implementing zirconium silicate-enhanced coatings on critical flow path surfaces exposed to acidic process media.
Coating Type | Zirconium Silicate Content | Application Method | Ideal Applications |
---|---|---|---|
Ceramic-Metal Composite | 30-45% | Plasma Spray | Pump components, valve seats, wear plates |
Sol-Gel Derived | 15-25% | Dip/Spray + Heat Treatment | Chemical processing equipment, heat exchangers |
Polymer-Ceramic | 20-35% | Spray/Brush | Marine components, acid handling equipment |
6. What Role Does Zirconium Silicate Play in Glass Manufacturing?
Glass manufacturing combines art with science, requiring precise material control to achieve desired optical, mechanical, and chemical properties. Zirconium silicate serves multiple critical functions in this sophisticated industry, addressing challenges that limit product quality and production efficiency.
As a fining agent, zirconium silicate promotes bubble removal through multiple pathways. Its refractory particles provide nucleation sites for small bubbles to combine into larger ones that rise more rapidly through the melt. Additionally, trace impurities in natural zirconium silicate can release gases that sweep through the glass, collecting smaller bubbles through a scrubbing effect. As an opacifier, the material’s high refractive index (approximately 1.95) creates pronounced light scattering when dispersed as fine particles throughout the glass matrix.
Optimal fining typically requires additions of 0.1-0.3% zirconium silicate with particle sizes below 45 microns, while opacification applications generally use 3-10% with carefully controlled size distributions centered around 1-5 microns. Melting temperature profiles must account for the material’s high melting point, ensuring sufficient residence time at peak temperatures for proper dissolution and distribution.
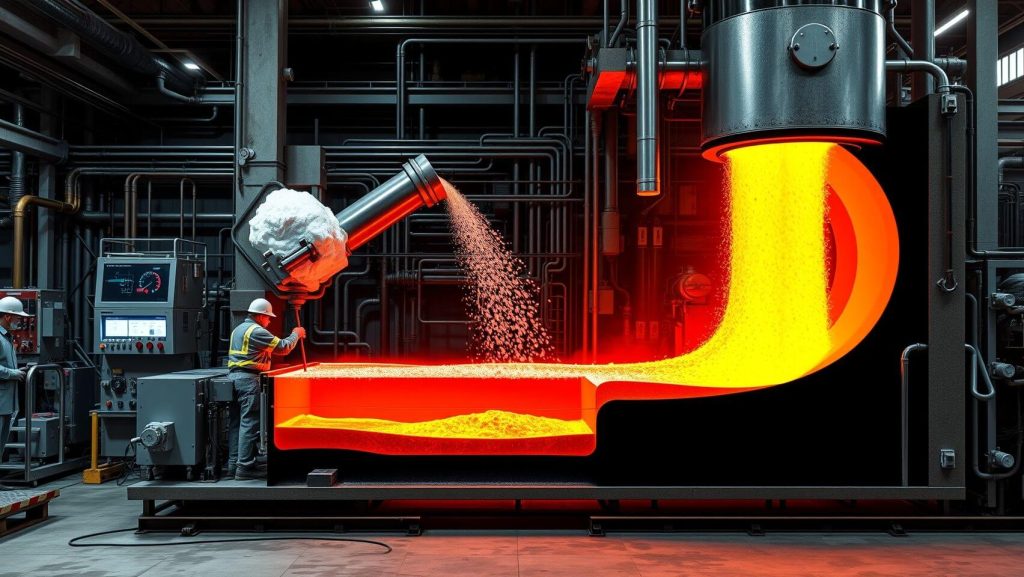
Industrial glass manufacturing facility showing molten glass production with zirconium silicate being added as a fining agent, highlighting the bubble removal process
A manufacturer of high-end decorative glassware implemented zirconium silicate-based opacification after struggling with consistency issues using traditional tin oxide systems. The reformulated products achieved more uniform appearance with fewer defects, reducing rejection rates by approximately 35%. Another case involved laboratory glassware production, where zirconium silicate fining agents resolved persistent bubble problems that had caused failure during thermal cycling.
7. How Can Zirconium Silicate Solve Abrasive Material Challenges?
Abrasive materials form the foundation of countless manufacturing processes, from precision grinding operations to large-scale surface preparation. These critical tools must deliver consistent performance while balancing cut rate, surface finish, and service life. Zirconium silicate addresses fundamental challenges in abrasive applications through its unique combination of hardness, fracture characteristics, and thermal stability.
Unlike materials that either wear flat (reducing cutting efficiency) or fracture unpredictably (causing inconsistent surface finishes), zirconium silicate particles break in a controlled manner during use. This characteristic creates continuously refreshed cutting edges that maintain efficiency throughout the abrasive product’s life. Additionally, the material’s thermal stability prevents degradation during high-speed applications where frictional heating can compromise conventional abrasives.
Precision grinding operations using zirconium silicate abrasives typically report 15-25% higher material removal rates compared to conventional aluminum oxide products of similar grit size. More importantly, surface finish consistency improves dramatically, with statistical process control data showing 30-40% reduction in finish variability across production runs.
While zirconium silicate abrasives typically carry premium pricing compared to basic alternatives, their performance advantages often justify the investment. One aerospace components manufacturer documented overall process cost reduction of 22% after switching to zirconium silicate grinding wheels, despite their 40% price premium over previously used materials.
8. What Benefits Does Zirconium Silicate Bring to Electronics Manufacturing?
Electronics manufacturing demands increasingly sophisticated materials to meet miniaturization trends and performance requirements. Zirconium silicate addresses critical challenges in this high-precision industry, particularly for substrate materials, packaging components, and specialized electronic ceramics.
Electronic ceramic substrate improvements through zirconium silicate incorporation focus on thermal management and mechanical reliability. When added to ceramic formulations for circuit substrates, the material enhances thermal conductivity while maintaining excellent electrical insulation properties. This combination allows more efficient heat dissipation from power components without compromising electrical performance. Manufacturers report significant improvements in thermal cycling reliability after incorporating zirconium silicate into substrate formulations, with one power electronics producer documenting 65% greater thermal shock resistance.
Electronic Application | Property Enhancement | Performance Improvement | Manufacturing Advantage |
---|---|---|---|
Power Module Substrates | Thermal Conductivity | 35% improved heat dissipation | Higher power density designs |
RF/Microwave Components | Dielectric Stability | 45% reduced frequency drift with temperature | Enhanced signal integrity |
Sensor Elements | Piezoelectric Response | 30% increased sensitivity | Improved detection thresholds |
Hermetic Packaging | Mechanical Strength | 65% greater thermal shock resistance | Reduced assembly failures |
LED Substrates | Optical Reflectivity | 40% enhanced light output | Improved energy efficiency |
Semiconductor Processing | Chemical Purity | <10ppb metal contamination | Higher yield in sensitive processes |
Electrical insulation performance advantages stem from zirconium silicate’s excellent dielectric properties and stability under varying environmental conditions. The material maintains consistent electrical characteristics across wide temperature ranges, with minimal variation in dielectric constant and loss tangent. This stability proves particularly valuable in high-frequency applications where temperature-induced property changes can shift circuit performance.
Its dimensional stability and controlled thermal expansion characteristics make it valuable for precision packaging components that must maintain exact tolerances despite thermal cycling. The material’s chemical inertness prevents contamination issues that plague sensitive semiconductor processes. Some advanced applications utilize zirconium silicate in specialized sensor elements, leveraging its piezoelectric properties for sensing and actuation functions.
9. How Does Zirconium Silicate Support Sustainable Manufacturing?
Sustainable manufacturing has evolved from optional corporate responsibility to essential business strategy. Manufacturers face increasing pressure to reduce environmental impacts while maintaining economic viability. Zirconium silicate contributes significantly to sustainability goals through multiple pathways that address material efficiency, energy consumption, and regulatory compliance.
The material’s exceptional durability extends component lifespans, reducing replacement frequency and associated resource consumption. In refractory applications, service life extensions of 30-50% directly translate to proportional reductions in material consumption and waste generation. Additionally, zirconium silicate’s performance characteristics often allow thinner applications while maintaining functionality, further reducing material requirements.
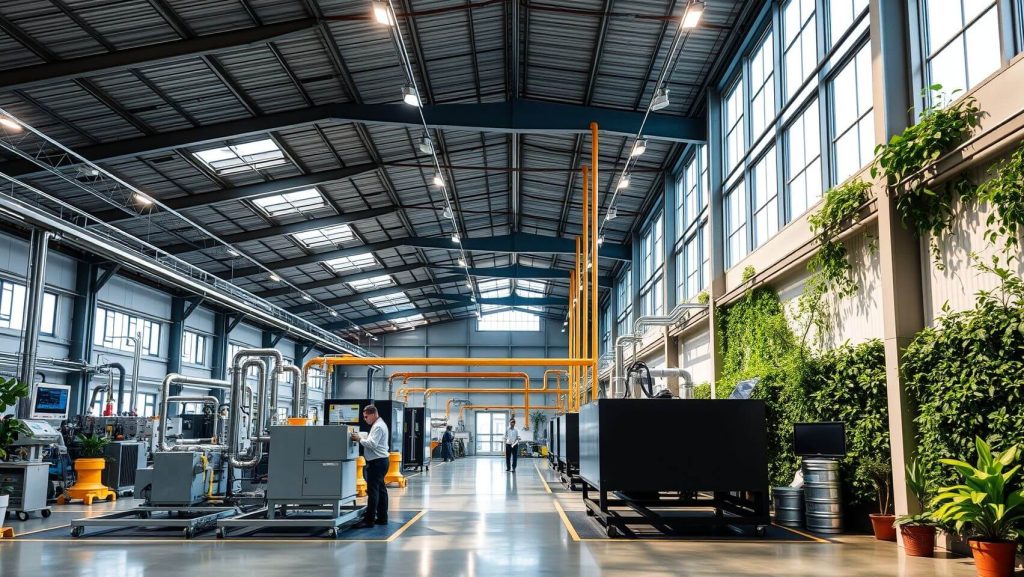
Modern manufacturing facility implementing zirconium silicate technology with visible energy efficiency measures and reduced waste production systems
A ceramic tile manufacturer documented 12% lower firing energy requirements after reformulating body compositions with zirconium silicate, which allowed lower peak firing temperatures while maintaining product quality. Similarly, a glass producer achieved 8% natural gas reduction in their melting operation after implementing zirconium silicate-based fining agents that accelerated bubble removal, reducing required residence time at peak temperatures.
Zirconium silicate typically contains lower levels of regulated heavy metals compared to some alternative materials, simplifying compliance with increasingly stringent environmental regulations. Its chemical stability minimizes leaching concerns in both manufacturing processes and end-product applications. Additionally, the material’s natural origin (primarily mined as the mineral zircon) often carries lower regulatory burdens than synthetic alternatives requiring energy-intensive manufacturing processes.
10. What Future Innovations Can We Expect with Zirconium Silicate?
The industrial applications of zirconium silicate continue evolving through ongoing research and development efforts. Current trends suggest exciting future possibilities that will further expand this versatile material’s role across manufacturing sectors.
Advanced thermal barrier coatings represent one promising direction, with researchers developing sophisticated multilayer systems incorporating zirconium silicate for turbine components and high-temperature processing equipment. Another growth area involves environmental technologies, where the material’s chemical stability and adsorption characteristics show promise for water treatment applications targeting heavy metal removal. Medical device manufacturing represents another emerging sector, with zirconium silicate’s biocompatibility and radiopacity making it valuable for certain implantable devices and diagnostic components.
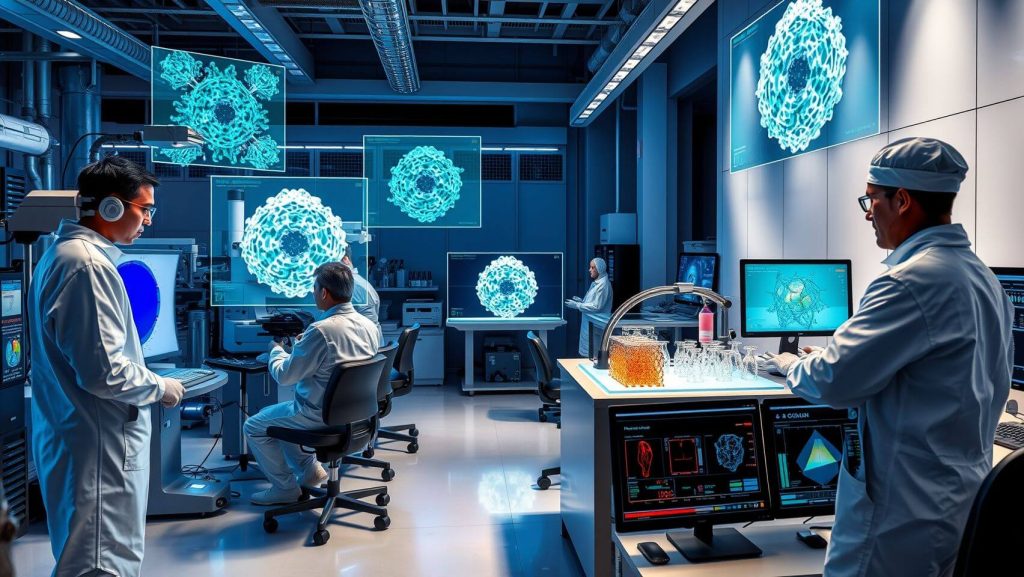
Laboratory researcher examining nano-scale zirconium silicate structures under advanced microscopy, representing cutting-edge materials science development
Nano-scale processing techniques now produce ultra-fine zirconium silicate particles with enhanced performance characteristics for specialized applications. Researchers have developed surface modification methods that improve compatibility with various matrix materials, enabling new composite systems with tailored properties. Sol-gel synthesis routes create highly pure, controlled morphology particles for advanced electronic and optical applications.
Industry experts anticipate increased focus on zirconium silicate-based environmental technologies, particularly for water treatment and emissions control applications. Others predict growing adoption in advanced energy systems, including fuel cells and next-generation nuclear technologies. Several experts highlight potential breakthroughs in biomedical applications, particularly for diagnostic imaging components and specialized implant materials.
FAQ Section
Q1: What is zirconium silicate, and how does it differ from ordinary silicates?
Zirconium silicate represents a mineral compound with chemical formula ZrSiO₄, combining zirconium oxide with silicon dioxide in a unique crystalline structure. Unlike common silicates, it exhibits exceptional thermal stability (melting point exceeding 2,500°C), superior hardness (7.5 on Mohs scale), and remarkable chemical resistance across wide pH ranges. Natural zirconium silicate occurs primarily as the mineral zircon, while synthetic versions offer controlled purity and particle characteristics for specialized applications.
Q2: How can manufacturers determine if zirconium silicate suits their specific industrial application?
Determining suitability requires systematic evaluation of application requirements against material properties. Start by analyzing operating conditions including temperature range, chemical exposure environment, and mechanical stress factors. Next, conduct cost-benefit analysis comparing initial material investment against long-term performance advantages like extended component life or reduced maintenance. Finally, perform small-scale testing under actual operating conditions, measuring relevant performance metrics before full implementation.
Q3: What procurement and supply chain considerations apply when sourcing zirconium silicate?
Procurement professionals should focus on purity specifications, particle size distribution, and batch consistency, as these factors directly impact performance in most applications. Establish diversified supply relationships to mitigate availability risks, particularly important given geographic concentration of zircon mining operations. Request comprehensive material certification documentation, especially for high-precision applications requiring consistent performance.
Q4: What safety measures should be implemented when working with zirconium silicate?
Handle zirconium silicate powder using appropriate personal protective equipment including dust respirators, safety glasses, and gloves to prevent inhalation and skin contact. Maintain adequate ventilation in processing areas, preferably with local exhaust systems near dust-generating operations. For high-temperature applications, implement standard thermal protection measures appropriate for operating temperatures. Waste disposal typically follows non-hazardous material protocols under most regulations.
Q5: What competitive advantages does zirconium silicate offer compared to other advanced ceramic materials?
Zirconium silicate provides superior price-performance balance compared to materials like alumina and silicon carbide, particularly for applications requiring moderate heat resistance and chemical stability. Its lower thermal expansion coefficient reduces thermal cycling stress issues common with alternative materials. Processing advantages include compatibility with various forming methods and relatively forgiving firing characteristics. Natural mineral availability often makes it more cost-effective than fully synthetic alternatives for many applications.