Zircon powder plays a pivotal role in various composite materials, but its effectiveness often hinges on the right coating technologies. For decision-makers like purchasing managers, understanding how to improve zircon powder functionality is essential to address performance issues in composites. This article will explain the coating technologies available and how they can benefit your composite applications. You can trust that the insights provided reflect current trends and solutions within the industry.
What Are Coating Technologies for Zircon Powder?
Coating technologies are processes that apply a protective layer to zircon powder. This layer enhances the powder’s properties, making it more effective in composite materials. The importance of these coatings cannot be understated, as they significantly impact the durability, performance, and overall functionality of composites that utilize zircon.
Some common types of coatings used for zircon powder include:
● Silica Coatings: These are often applied to improve wear resistance and prevent agglomeration.
● Polymer Coatings: Polymers can enhance adhesion and modify surface properties for better compatibility with resin systems.
● Metallic Coatings: These coatings can improve thermal stability and conductivity, which is crucial in high-performance applications.
Each coating type serves a specific purpose, and the choice depends on the intended application of the composite.
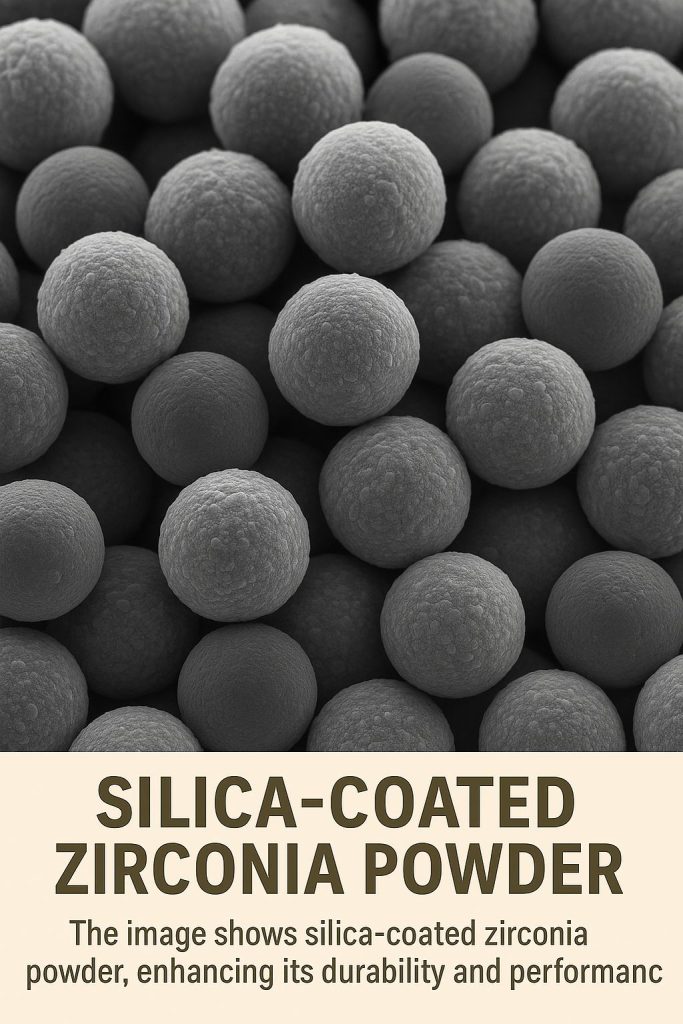
This image shows silica-coated zircon powder that enhances its durability and performance in composites.
How Do Coating Technologies Enhance Zircon Powder Functionality?
Coating technologies play a pivotal role in enhancing the functionality of zircon powder, making it a valuable component in various industrial applications. By applying a protective layer to zircon particles, these technologies significantly improve their performance characteristics. Let’s delve into some of the key benefits:
● Increased Durability: One of the primary advantages of coating zircon powder is the enhancement of its durability. The coating acts as a barrier against environmental factors, such as moisture and chemicals, which can lead to degradation. This increased resilience ensures that zircon maintains its integrity during manufacturing processes and extends the lifespan of end products.
● Improved Compatibility: Coated zircon powder exhibits enhanced compatibility with various matrices, including polymers, metals, and ceramics. This compatibility is crucial for the creation of high-performance composite materials. When zircon powder interacts more seamlessly with other components, it leads to improved mechanical properties, better thermal stability, and overall enhanced performance.
● Tailored Properties: Coating technologies allow manufacturers to tailor the properties of zircon powder to meet specific requirements. Different types of coatings can impart unique characteristics, such as increased thermal resistance or improved dispersibility. This adaptability makes coated zircon suitable for a wide range of applications, including aerospace, automotive, and electronics.
● Enhanced Surface Characteristics: The surface morphology of zircon powder can significantly impact its behavior in composite applications. Coating technologies can modify the particle surface, leading to improved adhesion between the zircon and the matrix material. This results in stronger bonds, which are essential for producing reliable and durable composites.
● Cost-Effectiveness: While initial investments in coating technologies may seem significant, the long-term benefits often outweigh the costs. Enhanced durability and performance lead to reduced failure rates and lower maintenance costs, making the overall process more economical.
As demonstrated through multiple applications, coated zircon powders consistently outperform their uncoated counterparts, demonstrating the value of incorporating these technologies in composite production.
Coating Type | Benefit | Mechanism |
---|---|---|
Silica | Wear resistance | Forms a protective barrier |
Polymer | Improved adhesion | Enhances surface interaction |
Metallic | Thermal stability | Increases heat resistance |
In summary, the application of coating technologies to zircon powder transforms its capabilities, making it an indispensable ingredient in high-quality composites. By providing increased durability, improved compatibility, tailored properties, enhanced surface characteristics, and cost-effectiveness, these innovations position coated zircon powder as a leading choice for industries seeking to push the boundaries of performance. As we continue to explore advanced coating methods, the future of zircon powder in composite materials looks exceptionally promising.
What Are the Key Coating Materials Used?
Choosing the right coating material is vital for achieving desired performance outcomes. Several key materials are commonly used for coating zircon powder:
● Silica: Offers high resistance to abrasion and contributes to better flow properties.
● Polymeric substances: They modify surface characteristics for better resin interaction.
● Alumina: Known for thermal stability, alumina coatings can improve heat resistance in demanding applications.
The effectiveness of these materials is measured by specific characteristics such as adhesion strength, wear resistance, and temperature stability. Accordingly, it’s essential to match the coating type with the intended application, considering both the composite’s performance requirements and cost implications.
Coating Material | Key Properties | Typical Uses |
---|---|---|
Silica | Abrasion resistance | Construction and industrial composites |
Polymeric | Enhanced adhesion | Aerospace components |
Alumina | High thermal stability | Electronics and automotive applications |
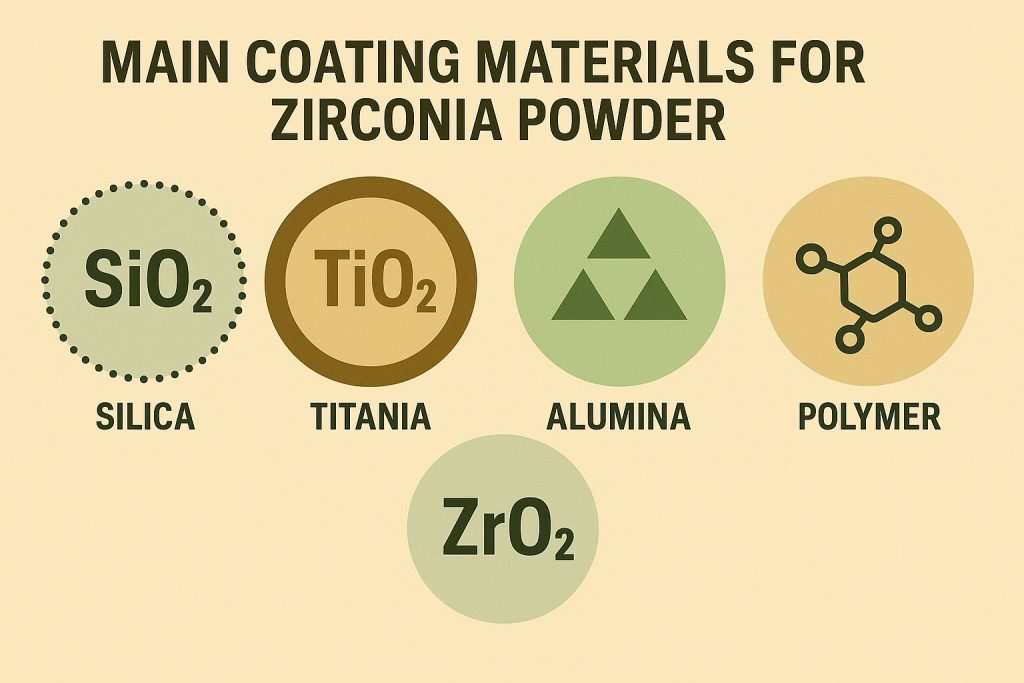
This image illustrates various key materials used in coating zircon powder to enhance its properties.
How to Choose the Right Coating Technology?
Selecting the right coating technology involves several considerations to align with specific project needs. Here are some key factors to keep in mind:
● Performance Requirements: Understand what properties are essential for the composite’s application. For example, high heat resistance may be needed for aerospace materials.
● Material Compatibility: Assess how the coating interacts with both the zircon powder and the matrix material. This ensures that the composite maintains its integrity.
● Cost-Effectiveness: Analyze the cost benefits of different coating options. Sometimes, a more expensive coating may offer savings in durability and performance over time.
Other industry-specific considerations might include regulatory compliance and supply chain logistics. Engaging with manufacturers who specialize in zircon powder coatings can further clarify options tailored to your needs.
Consideration | Description | Importance |
---|---|---|
Performance | Desired heat, wear, and strength | Determines suitability for application |
Material | Compatibility with matrix material | Prevents issues in end-use |
Cost | Analyzing ROI on coating solution | Assures financial feasibility |
What Is the Application Process for Coating Technologies?
The application process for coating zircon powder typically follows a series of well-defined steps. These steps ensure that the coatings are applied uniformly and effectively:
- Surface Preparation: This often involves cleaning and treating the zircon powder to enhance adhesion.
- Coating Application: Techniques such as spray coating or fluidized bed coating can be utilized depending on the coating material and application method.
- Curing or Drying: After application, the coated zircon powder may require curing. This step solidifies the coating and improves its properties.
- Quality Control: Rigorous testing ensures the coating meets the required specifications, guaranteeing that the production process maintains high standards.
Establishing a reliable application process is crucial for consistently achieving desired outcomes in composite materials. Each step must be methodical to avoid defects that could compromise performance.
Process Step | Description | Importance |
---|---|---|
Surface Prep | Cleaning and treating for adhesion | Ensures proper bonding |
Coating Application | Applying coating uniformly | Important for consistency |
Curing | Solidifying the coating | Enhances performance |
Quality Control | Final testing of properties | Validates production standards |
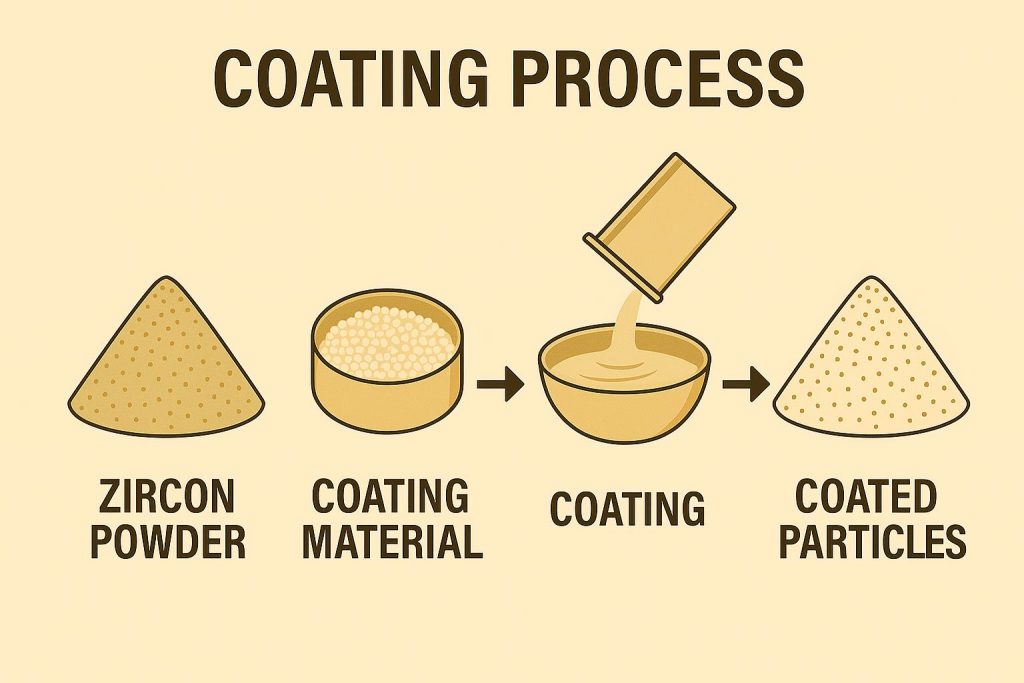
This image depicts the steps involved in the coating application process of zircon powder.
What Are the Challenges in Coating Zircon Powder?
While coating zircon powder offers many advantages, companies may encounter several challenges during the process:
● Inconsistent Coating: Variability in application techniques can lead to inconsistencies that affect performance.
● Cost Implications: High-quality coating materials can be expensive, impacting the overall product cost.
● Application Complexity: Certain coatings may require specialized equipment or expertise, complicating the coating process.
To address these challenges, companies often invest in training for their staff and explore advanced application technologies. Continuous improvement practices can help streamline the process, making it more efficient and cost-effective.
Challenge | Description | Possible Solutions |
---|---|---|
Inconsistency | Variability in coating thickness | Implement strict process controls |
Cost | High-quality materials can be pricey | Evaluate long-term ROI |
Complexity | Need for specialized equipment | Invest in staff training |
How Do Coating Technologies Impact Composite Performance?
Coating technologies can dramatically impact composite performance. Studies and real-world applications demonstrate that using coated zircon powder often results in superior outcomes. For example, composites with silica-coated zircon may exhibit enhanced mechanical strength and thermal resistance.
Case studies highlight various industries:
- Aerospace: Engine components made with coated zircon show improved thermal management, contributing to safer operations.
- Automotive: Coatings that enhance wear resistance lead to longer-lasting friction materials, reducing maintenance costs.
- Construction: Composites incorporating coated zircon powder demonstrate better durability against environmental factors.
Inserting these technologies into your manufacturing process not only addresses immediate performance issues but can also yield significant long-term savings and reliability in the final product.
Industry | Application | Benefits |
---|---|---|
Aerospace | Engine components | Improved thermal management |
Automotive | Friction materials | Durability reducing maintenance costs |
Construction | Structural composites | Resistance to environmental factors |
What Future Trends in Coating Technologies Should Businesses Watch?
The world of coating technologies is continually evolving. Businesses need to stay ahead of trends to remain competitive. Here are some noteworthy trends to consider:
● Sustainability: Eco-friendly coatings are gaining traction. These coatings reduce environmental impact while maintaining performance.
● Smart Coatings: Coatings that monitor their condition and can provide feedback are becoming more common. These technologies optimize maintenance and performance analysis.
● Advanced Nanotechnology: Nano-coatings are emerging, offering superior properties at reduced weights. This innovation allows for more efficient and effective composite materials.
Understanding these trends can help businesses adapt and thrive in an increasingly competitive market. Keeping an eye on advancements will position companies to leverage new solutions effectively.
Trend | Description | Implications for Business |
---|---|---|
Sustainability | Development of eco-friendly products | Meet growing consumer demand |
Smart Coatings | Coatings that provide performance data | Enhanced operational efficiency |
Nanotechnology | Use of nanomaterials for coating | Improved properties and reduced weight |
Conclusion
This article has explored how coating technologies can improve zircon powder functionality in composites. We covered key types of coatings, their benefits, and how to effectively apply them. Implementing the right coating technology can lead to enhanced performance in composite materials, directly translating to cost savings and improved reliability. For your projects, partner with Global Industry to leverage expert advice on selecting and applying these coating technologies. Together, we can ensure your composites meet the highest standards.
FAQ Section
Q1: What is coated zircon?
A1: Coated zircon refers to zirconium dioxide (ZrO₂) that has been treated with a protective coating to enhance its properties, such as durability, thermal stability, and resistance to corrosion. This makes it suitable for use in demanding applications across various industries.
Q2: What are the primary benefits of using coated zircon in composites?
A2: The primary benefits of coated zircon in composites include improved mechanical strength, enhanced thermal and electrical insulation, increased resistance to wear and corrosion, and a favorable strength-to-weight ratio. These properties make it ideal for applications in aerospace, automotive, construction, and medical fields.
Q3: How does coated zircon affect the performance of composites?
A3: Coated zircon significantly enhances the performance of composites by reinforcing the material matrix, leading to improved structural integrity and longevity. It allows composites to withstand extreme conditions, such as high temperatures and corrosive environments, while maintaining lightweight characteristics.
Q4: Is coated zircon environmentally friendly?
A4: Yes, coated zircon is considered more environmentally friendly compared to some traditional materials. Its durability extends the life cycle of products, reducing waste, and many formulations can be designed to minimize environmental impact during production and disposal.
Q5: What industries are currently leveraging coated zircon technology?
A5: Industries such as aerospace, automotive, construction, electronics, and medical are actively leveraging coated zircon technology. Its versatility and superior properties make it beneficial in applications ranging from aircraft components to electronic insulation and medical implants.