Foundry operations face constant pressure to improve casting quality while controlling costs and meeting demanding production schedules. Material selection plays a critical role in achieving these objectives, yet many foundries continue using traditional materials that limit their potential for quality improvements and operational efficiency. The right refractory material choice can transform foundry performance. This comprehensive analysis examines why zircon powder has become the preferred alternative to conventional foundry materials, providing quantifiable benefits in casting quality, operational efficiency, and long-term cost savings. Leading foundries worldwide rely on zircon powder to achieve superior results in demanding applications where traditional materials fall short.
What Superior Properties Make Zircon Powder Stand Out?
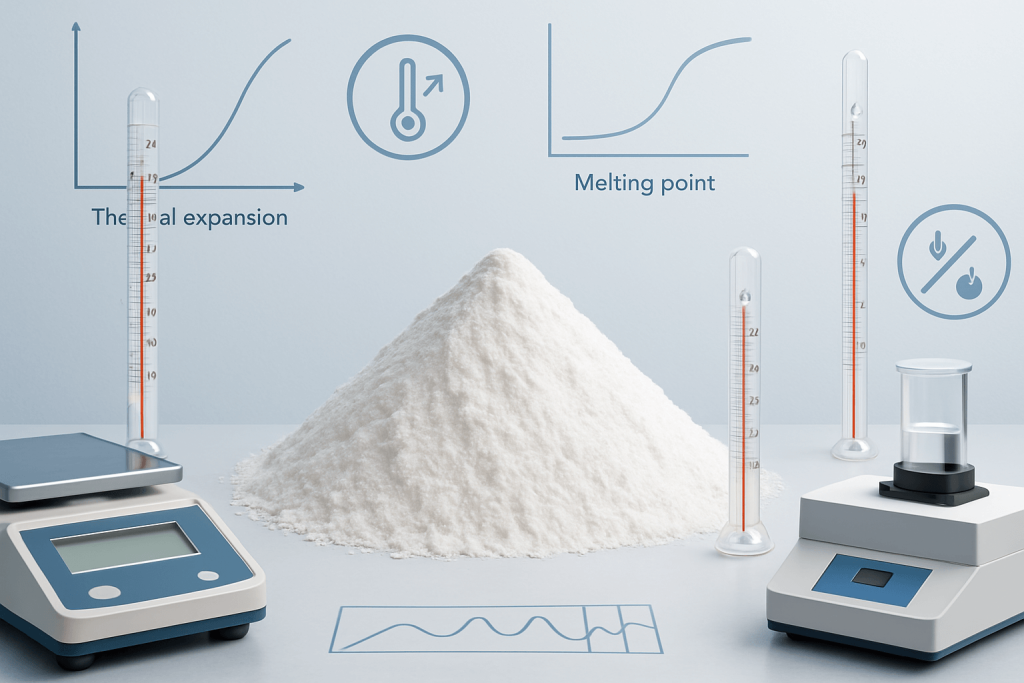
Zircon powder delivers exceptional thermal properties that set it apart from conventional foundry materials. These properties directly impact casting success. The material’s high melting point of 2,550°C provides superior refractoriness compared to silica sand (1,713°C) and chromite sand (2,180°C), allowing foundries to cast high-temperature alloys without material degradation or contamination.
Thermal stability represents a key advantage in foundry applications where materials experience rapid temperature changes. Zircon powder maintains its structural integrity during heating and cooling cycles, preventing thermal shock failures that can compromise casting quality. Thermal shock resistance prevents costly defects. The material’s low thermal expansion coefficient of 4.2 × 10⁻⁶/°C minimizes dimensional changes during temperature cycling, maintaining precise mold dimensions throughout the casting process.
Chemical inertness provides another significant advantage, particularly when casting reactive metals and alloys. Zircon powder resists chemical attack from molten metals, preventing contamination that can affect metallurgical properties and surface quality. This chemical stability becomes critical in investment casting and precision applications where material purity directly impacts final component performance.
Property | Zircon Powder | Silica Sand | Chromite Sand | Advantage |
---|---|---|---|---|
Melting Point (°C) | 2,550 | 1,713 | 2,180 | Superior refractoriness |
Thermal Expansion (×10⁻⁶/°C) | 4.2 | 14.0 | 8.5 | Better dimensional stability |
Thermal Conductivity (W/m·K) | 5.8 | 1.4 | 2.1 | Improved heat transfer |
Chemical Resistance | Excellent | Good | Very Good | Reduced contamination |
Particle characteristics of zircon powder contribute significantly to its foundry performance. The material’s angular particle shape provides excellent mechanical bonding with binder systems, creating strong molds and cores that resist erosion during metal pouring. Strong mechanical bonding prevents mold failures. Consistent particle size distribution allows for optimal packing density, reducing void spaces that could trap gases or create weak points in the mold structure.
Thermal conductivity properties of zircon powder enable controlled heat transfer during solidification, allowing foundries to manage cooling rates and achieve desired metallurgical structures. This controlled heat transfer becomes particularly valuable in directional solidification applications and when casting thick sections that require specific cooling patterns.
How Does Zircon Powder Compare to Silica Sand?
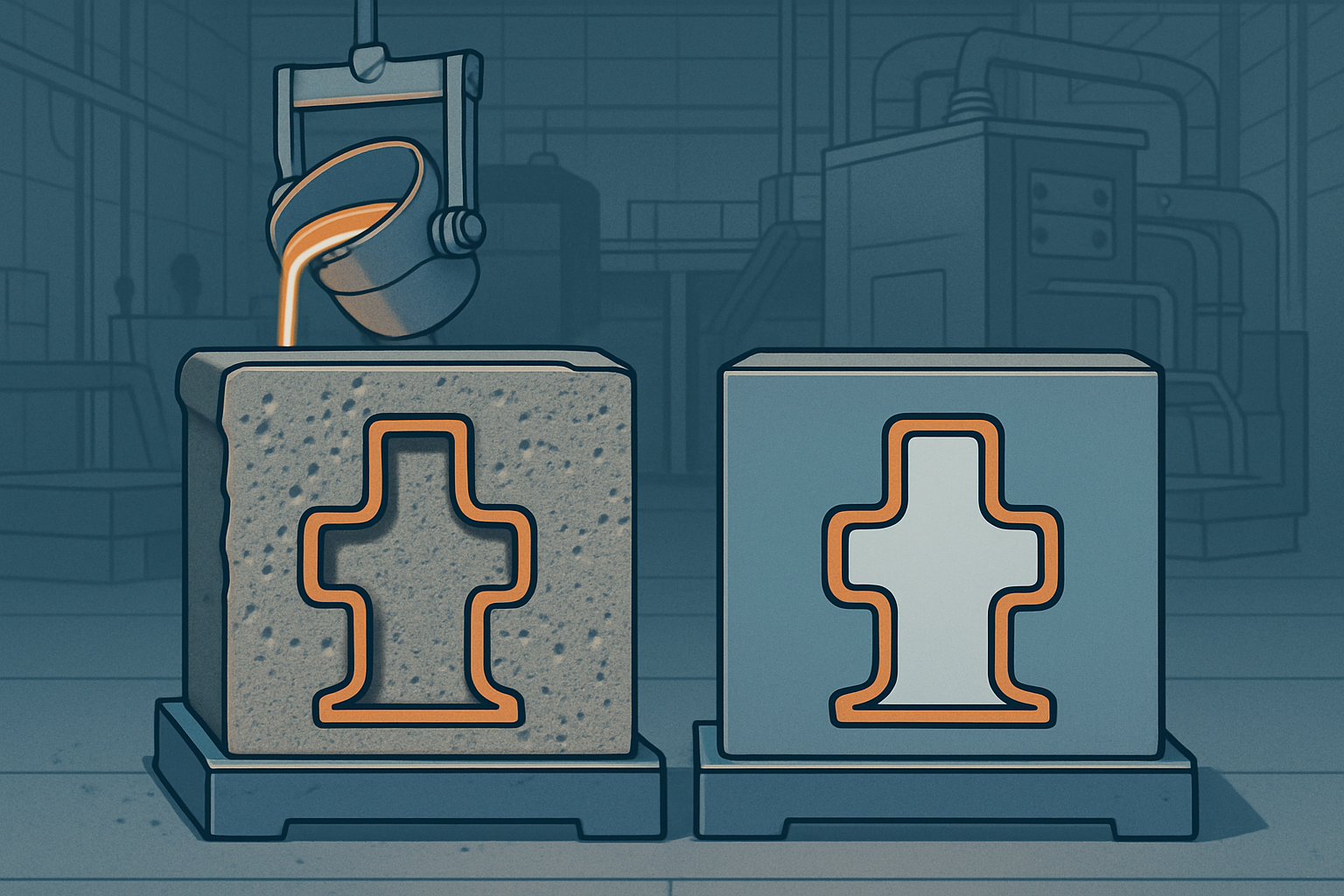
The comparison between zircon powder and silica sand reveals significant performance differences that justify the material premium in quality-critical applications. Performance differences drive material selection decisions. Thermal expansion represents the most significant difference, with silica sand exhibiting thermal expansion three times higher than zircon powder. This difference directly impacts dimensional accuracy and casting tolerances.
Metal penetration resistance shows dramatic differences between these materials. Zircon powder’s fine particle size and chemical inertness create a barrier that prevents molten metal from penetrating the mold surface, resulting in superior surface finish quality. Silica sand’s larger particle size and higher reactivity allow metal penetration, leading to rough surfaces that require extensive machining.
Thermal shock resistance favors zircon powder significantly, particularly in applications involving rapid heating or cooling. Silica sand undergoes phase transformations during heating that create volume changes and potential cracking, while zircon powder maintains structural stability throughout temperature cycling.
Comparison Factor | Zircon Powder | Silica Sand | Impact on Casting |
---|---|---|---|
Surface Finish (Ra μm) | 1.6-3.2 | 6.3-12.5 | Reduced machining |
Dimensional Tolerance | ±0.1-0.2mm | ±0.3-0.8mm | Improved accuracy |
Metal Penetration | Minimal | Significant | Better surface quality |
Reusability (cycles) | 15-25 | 3-8 | Lower material costs |
Cost considerations extend beyond initial material pricing to include total cost of ownership factors. While zircon powder costs significantly more per ton than silica sand, the improved casting quality, reduced defect rates, and extended mold life often result in lower total costs for high-value applications. Total cost analysis reveals true value.
Environmental and safety factors also differentiate these materials. Zircon powder generates less dust during handling and processing, improving workplace conditions and reducing cleanup requirements. The material’s chemical stability reduces the formation of hazardous compounds during high-temperature operations.
Reusability characteristics strongly favor zircon powder, which can be reclaimed and reused multiple times with minimal property degradation. Silica sand typically requires replacement after fewer cycles due to thermal damage and contamination, increasing material consumption and waste generation.
Which Casting Applications Benefit Most from Zircon?
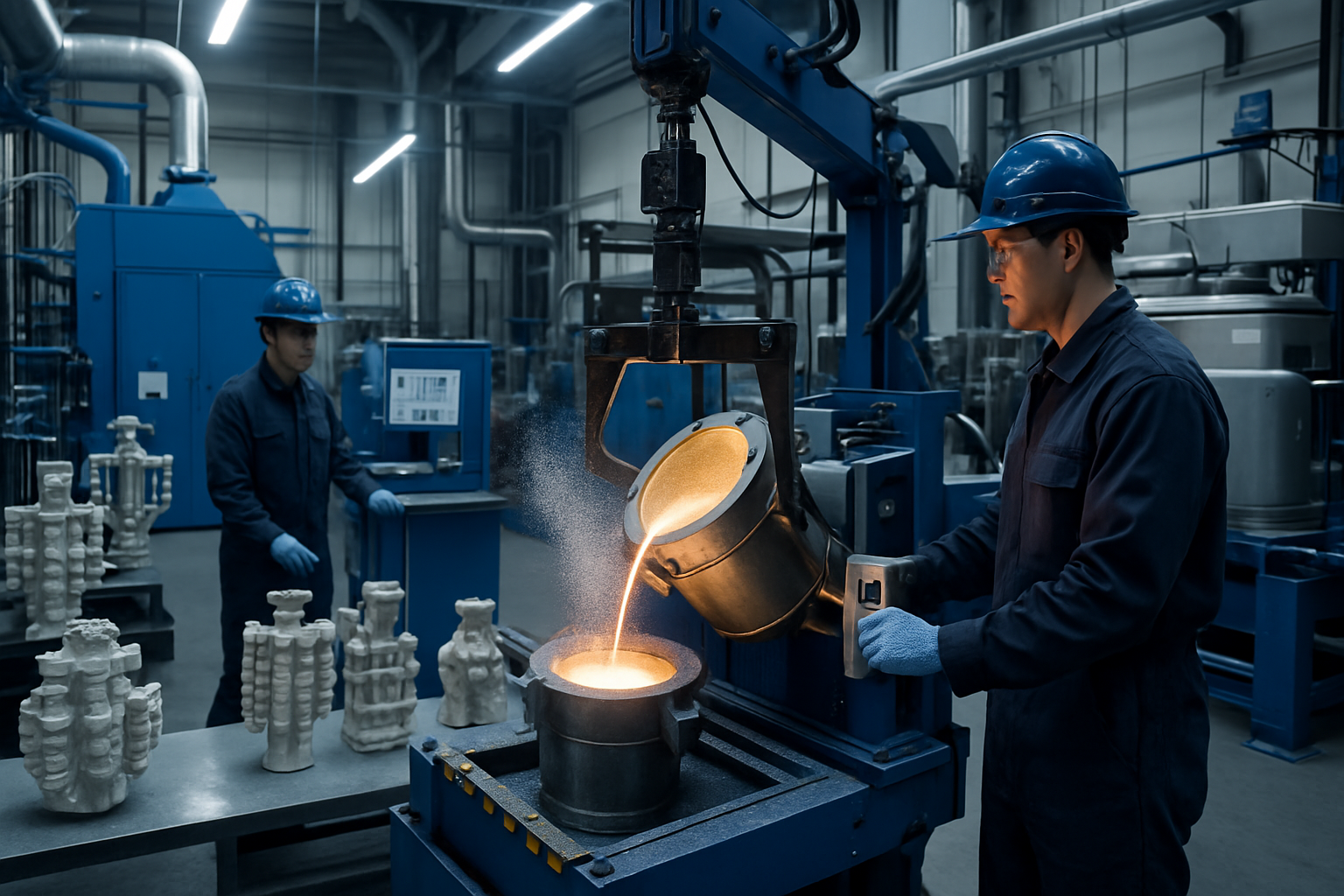
Steel casting applications represent the largest market for zircon powder due to the material’s ability to withstand the high temperatures and aggressive chemical environment of molten steel. Steel casting demands superior refractory performance. Carbon steel, alloy steel, and stainless steel casting all benefit from zircon powder’s thermal stability and chemical inertness, resulting in improved surface quality and dimensional accuracy.
Investment casting operations achieve exceptional results with zircon powder, particularly for aerospace and automotive components requiring tight tolerances and superior surface finish. The material’s fine particle size and excellent flowability enable the production of complex geometries with thin walls and intricate details that would be difficult to achieve with conventional materials.
High-temperature alloy casting benefits significantly from zircon powder’s superior refractoriness and chemical resistance. Superalloys used in gas turbine components, aerospace applications, and industrial equipment require casting materials that can withstand extreme temperatures without degradation or contamination. High-temperature applications require premium materials.
Application Type | Temperature Range (°C) | Key Benefits | Typical Industries |
---|---|---|---|
Carbon Steel | 1,500-1,600 | Surface quality, accuracy | Automotive, machinery |
Stainless Steel | 1,450-1,520 | Corrosion resistance | Food, chemical, medical |
Superalloys | 1,350-1,450 | Precision, cleanliness | Aerospace, energy |
Investment Casting | 1,200-1,600 | Complex geometry | Jewelry, aerospace |
Core making applications utilize zircon powder’s excellent collapsibility properties, which allow easy removal of cores after casting without damaging the finished component. This characteristic becomes particularly valuable in complex castings with internal passages or undercuts that require core removal through small openings.
Mold facing applications take advantage of zircon powder’s superior surface finish properties by applying a thin layer of zircon-based facing material to the mold cavity surface. This technique provides the benefits of zircon powder while minimizing material costs by using conventional backing materials for the bulk of the mold.
Specialty casting requirements in medical and defense sectors often mandate the use of premium materials like zircon powder to meet stringent quality and performance standards. These applications typically justify the material premium through improved reliability and reduced risk of component failure.
What Cost Benefits Justify Zircon Powder Investment?
Defect reduction represents the most significant cost benefit of zircon powder implementation, with foundries typically reporting 40-60% reductions in casting defects when switching from conventional materials. Defect reduction drives profitability improvements. Common defects eliminated include metal penetration, surface roughness, dimensional variations, and thermal shock cracking, all of which contribute to scrap costs and rework expenses.
Improved casting yield directly impacts foundry profitability by reducing the number of castings that require rework or scrapping. Zircon powder’s superior properties enable foundries to achieve first-pass success rates of 95% or higher in many applications, compared to 75-85% typical with conventional materials.
Extended mold life provides ongoing cost savings through reduced material consumption and labor costs. Zircon-based molds and cores can often be reused 15-25 times compared to 3-8 cycles for silica sand systems, significantly reducing material costs per casting produced.
Cost Factor | Conventional Materials | Zircon Powder | Savings Potential |
---|---|---|---|
Defect Rate | 15-25% | 5-10% | 60-75% reduction |
Rework Costs | $50-150/casting | $10-30/casting | 70-85% reduction |
Material Usage | 100% baseline | 60-75% baseline | 25-40% reduction |
Labor Costs | 100% baseline | 80-90% baseline | 10-20% reduction |
Energy savings result from zircon powder’s improved thermal properties, which enable more efficient heat transfer and reduced energy consumption during melting and casting operations. The material’s thermal conductivity allows for faster cooling and shorter cycle times, increasing foundry throughput and reducing energy costs per casting.
Labor cost reductions occur through improved handling characteristics and reduced cleanup requirements. Zircon powder’s low dust generation and excellent flowability reduce the time required for mold preparation and finishing operations. Improved handling reduces labor requirements.
Quality improvements translate directly to cost savings through reduced machining allowances and finishing operations. Castings produced with zircon powder typically require 30-50% less machining due to improved surface finish and dimensional accuracy, reducing manufacturing costs and lead times.
How Do Processing Characteristics Improve Operations?
Mixing and bonding properties of zircon powder provide superior compatibility with various binder systems used in foundry operations. Excellent bonding creates stronger molds. The material works effectively with clay-bonded, resin-bonded, and sodium silicate binder systems, allowing foundries to optimize their processes without changing existing equipment or procedures.
Flowability characteristics of zircon powder enable consistent mold filling and compaction, reducing variations in mold density and strength. The material’s angular particle shape and consistent size distribution promote uniform packing and eliminate weak spots that could lead to mold failures during casting.
Permeability control becomes critical in foundry operations to allow proper gas evacuation during metal pouring and solidification. Zircon powder’s particle characteristics can be optimized to achieve the desired permeability levels for specific applications, preventing gas-related defects while maintaining mold strength.
Collapsibility properties allow easy removal of cores and molds after casting, reducing the risk of damage to finished castings. Zircon powder-based systems can be formulated to provide excellent strength during casting while breaking down readily for removal, particularly important in complex castings with internal features.
Processing Characteristic | Benefit | Impact on Operations |
---|---|---|
Flowability | Consistent filling | Reduced variations |
Compaction | Uniform density | Improved strength |
Permeability | Gas evacuation | Fewer defects |
Collapsibility | Easy removal | Reduced damage |
Storage Stability | Long shelf life | Inventory flexibility |
Storage stability of zircon powder provides operational flexibility by maintaining consistent properties during extended storage periods. The material resists moisture absorption and chemical degradation, allowing foundries to maintain larger inventories without quality concerns.
Quality control procedures for zircon powder are well-established and standardized, enabling consistent monitoring of material properties and performance. Regular testing of particle size distribution, chemical composition, and physical properties helps maintain consistent casting results and identify potential issues before they affect production.
Processing equipment compatibility allows foundries to use zircon powder with existing mixing, molding, and handling equipment without significant modifications. This compatibility reduces implementation costs and allows for gradual transition from conventional materials.
What Performance Advantages Drive Quality Improvements?
Surface finish improvements represent one of the most visible benefits of zircon powder implementation, with castings typically achieving surface roughness values 50-70% better than those produced with conventional materials. Superior surface finish reduces finishing costs. The fine particle size and chemical inertness of zircon powder create smooth mold surfaces that transfer to the finished casting, reducing or eliminating the need for surface grinding and polishing operations.
Dimensional tolerance improvements enable foundries to achieve tighter tolerances and reduce machining allowances, resulting in material savings and reduced manufacturing costs. Zircon powder’s low thermal expansion and excellent dimensional stability allow castings to maintain their intended geometry throughout the cooling process.
Porosity reduction occurs through improved mold permeability control and reduced gas generation during casting. Zircon powder’s thermal stability prevents decomposition reactions that can generate gases and create porosity in finished castings, particularly important in pressure-tight applications.
Heat transfer control during solidification enables foundries to manage cooling rates and achieve desired metallurgical structures. Zircon powder’s thermal conductivity can be optimized through particle size selection and mold design to promote directional solidification and minimize shrinkage defects.
Performance Factor | Improvement Range | Quality Impact |
---|---|---|
Surface Roughness | 50-70% better | Reduced machining |
Dimensional Accuracy | 60-80% improvement | Tighter tolerances |
Porosity Levels | 40-60% reduction | Better integrity |
Metallurgical Quality | 20-30% improvement | Enhanced properties |
Metallurgical property improvements result from reduced contamination and controlled cooling rates achieved with zircon powder systems. The material’s chemical inertness prevents unwanted reactions that could affect alloy composition, while its thermal properties enable optimal solidification conditions.
Consistency and repeatability in production processes improve significantly with zircon powder due to the material’s uniform properties and stable performance characteristics. This consistency reduces process variations and enables foundries to achieve predictable results across multiple production runs.
Defect elimination becomes possible in many applications through zircon powder’s superior properties. Common casting defects such as metal penetration, veining, and thermal shock cracking can be virtually eliminated, resulting in higher yields and improved customer satisfaction.
What Future Trends Support Zircon Powder Adoption?
Industry demands for higher casting quality standards continue driving adoption of premium materials like zircon powder. Quality standards drive material selection. Automotive lightweighting initiatives require thinner wall castings with superior surface finish, while aerospace applications demand zero-defect quality levels that are difficult to achieve with conventional materials.
Automation and advanced foundry technologies show excellent compatibility with zircon powder systems. Robotic molding equipment, automated core production, and computer-controlled pouring systems all benefit from the consistent properties and predictable behavior of zircon powder, enabling higher levels of automation and process control.
Environmental regulations increasingly favor cleaner foundry materials that generate less dust and hazardous emissions. Zircon powder’s low dust generation and chemical stability help foundries meet environmental requirements while improving workplace conditions for employees.
Supply chain reliability for zircon powder continues improving through diversified global production and strategic inventory management. Multiple suppliers worldwide provide consistent quality material, reducing supply risks and enabling competitive pricing through market competition.
Trend Factor | Impact on Adoption | Timeline |
---|---|---|
Quality Standards | Increased demand | Ongoing |
Automation | Better compatibility | 2024-2027 |
Environmental | Regulatory compliance | 2024-2030 |
Supply Chain | Improved availability | Ongoing |
Research and development in zircon powder applications continues advancing the material’s capabilities and expanding potential applications. New binder systems, particle treatments, and processing techniques are being developed to optimize performance for specific casting requirements.
Market growth projections indicate continued expansion of zircon powder usage in foundry applications, driven by increasing demand for high-quality castings in aerospace, automotive, and energy sectors. This growth supports continued investment in production capacity and technology development.
Investment opportunities in zircon powder technology and applications continue attracting capital from foundry equipment manufacturers, material suppliers, and end-user companies seeking competitive advantages through superior casting quality and operational efficiency.
Conclusion
Zircon powder delivers transformative advantages over conventional foundry materials through superior thermal properties, chemical resistance, and dimensional stability that directly translate to improved casting quality and operational efficiency. The material’s ability to reduce defect rates by 40-60% while improving surface finish and dimensional accuracy provides compelling economic justification for implementation in quality-critical applications. Global Industry’s foundry materials team offers comprehensive technical support for zircon powder implementation, from initial feasibility studies through full-scale production optimization. Contact our foundry specialists today to evaluate how zircon powder can improve your casting quality, reduce costs, and strengthen your competitive position in demanding foundry applications.
FAQ Section
Q1: How much more expensive is zircon powder compared to silica sand?
Zircon powder typically costs 8-12 times more than silica sand initially, but the total cost of ownership is often lower due to reduced defect rates, improved casting quality, and extended mold life. The premium is justified in high-value casting applications where quality and precision are critical.
Q2: Can zircon powder be reused in foundry operations?
Yes, zircon powder can be reclaimed and reused multiple times with proper processing. The reclamation rate is typically 85-95%, making it more economical over time. Proper screening, thermal treatment, and quality testing ensure consistent performance in reused material.
Q3: What safety precautions are needed when handling zircon powder?
Zircon powder requires standard foundry safety measures including dust control, respiratory protection, and proper ventilation. While zircon contains trace amounts of naturally occurring radioactive elements, levels are well below regulatory limits and pose no significant health risks with proper handling.
Q4: Which foundry applications show the greatest return on investment with zircon powder?
Investment casting, precision steel casting, and high-temperature alloy applications typically show the highest ROI. These applications benefit most from zircon’s superior properties and justify the material premium through improved quality and reduced processing costs.
Q5: How does zircon powder perform in automated foundry systems?
Zircon powder performs excellently in automated systems due to its consistent particle size distribution, good flowability, and predictable behavior. It’s compatible with modern molding machines, core shooters, and automated handling systems, making it ideal for high-volume production environments.