Selecting the correct zirconium silicate grade presents a common challenge for many manufacturing professionals. The wrong choice can lead to product defects, wasted materials, and production delays. This article guides you through the key factors that affect your zirconium silicate selection, helping you match the right grade to your specific application needs. With over 50 years of combined industry experience, our technical team has helped hundreds of manufacturers optimize their material selection process for better performance and cost efficiency.
What Is Zirconium Silicate And Its Main Applications?
Zirconium silicate (ZrSiO₄) stands as a versatile industrial material with unique properties that make it valuable across multiple sectors. This naturally occurring mineral, also known as zircon, consists of zirconium oxide (ZrO₂) and silicon dioxide (SiO₂) in a 1:1 molar ratio. Its crystal structure gives it remarkable stability at high temperatures, reaching up to 1,600°C before decomposition.
Want to know what makes this material so special? The combination of physical and chemical properties sets zirconium silicate apart from many other industrial minerals. It features high hardness (7.5 on the Mohs scale), high density (4.6-4.7 g/cm³), low thermal expansion, and exceptional chemical resistance to acids, alkalis, and molten metals.
The applications of zirconium silicate span numerous industries:
Industry | Applications | Key Properties Utilized |
---|---|---|
Ceramics | Opacifiers, glazes, tiles, sanitaryware | Whiteness, opacity, hardness |
Refractories | High-temperature linings, bricks | Thermal stability, chemical resistance |
Foundry | Molds, cores, investment casting | Thermal shock resistance, dimensional stability |
Glass | Special glasses, glass-ceramics | Opacity, nucleation properties |
Abrasives | Grinding media, sandblasting | Hardness, wear resistance |
Market classification typically divides zirconium silicate into grades based on purity, particle size, and specific application requirements. Premium grades contain 65-66% ZrO₂ with minimal impurities, while standard grades may contain 64-65% ZrO₂ with slightly higher levels of titanium, iron, and aluminum oxides.
How To Select Zirconium Silicate Grades Based On Application?
Matching the right zirconium silicate grade to your specific application requires careful consideration of several factors. The material behaves differently depending on the manufacturing process and end-use requirements.
Here’s the thing about ceramic applications: They demand specific particle size distributions and chemical purity levels. For high-end porcelain and sanitaryware, micronized grades with D50 (median particle size) of 1-3 μm provide optimal opacity and whiteness. Ceramic tile manufacturers typically use coarser grades (D50 of 5-10 μm) that balance opacity with cost-effectiveness.
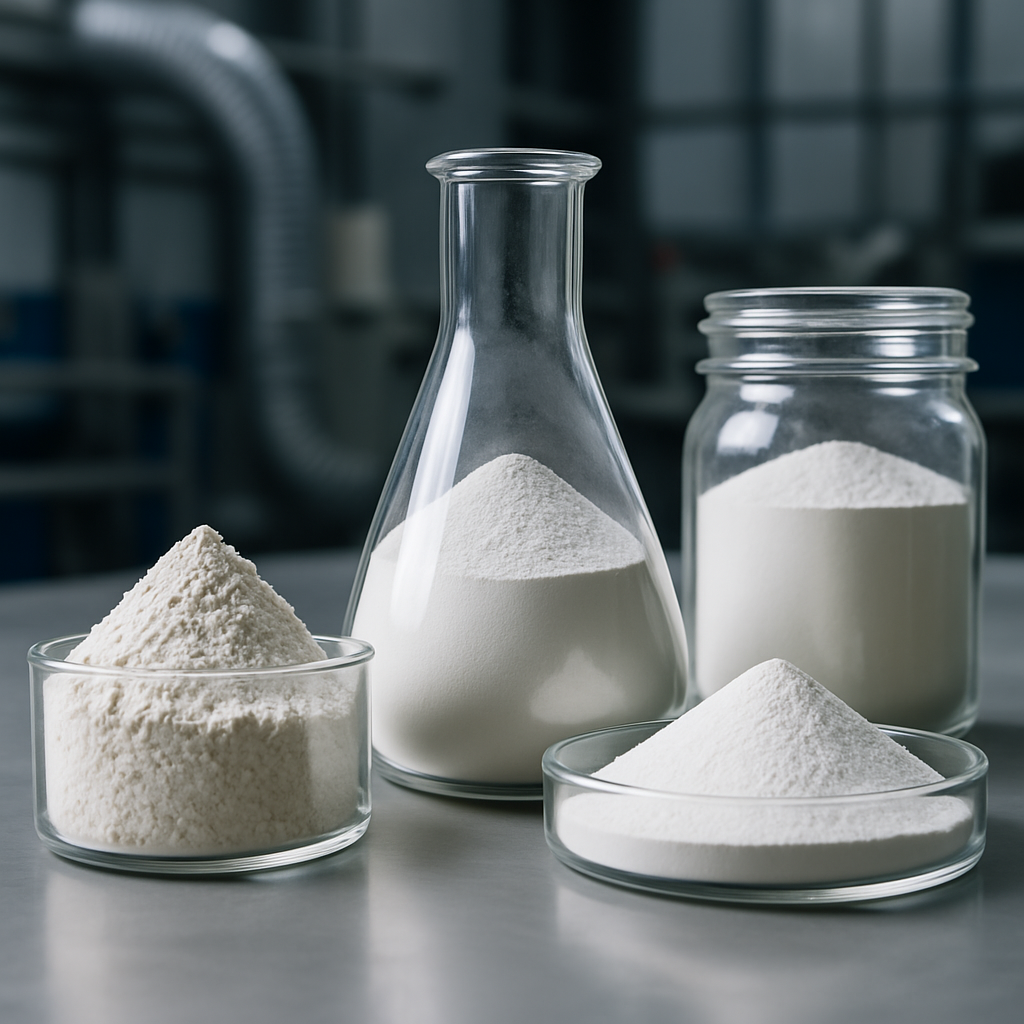
For refractory applications, the selection criteria shift toward thermal stability and resistance to chemical attack:
Application Type | Recommended Grade | Particle Size Range | Key Selection Factors |
---|---|---|---|
High-temperature kilns | Premium refractory | 45-75 μm | Thermal cycling resistance, slag resistance |
Glass contact refractories | High-purity | 45-150 μm | Corrosion resistance, non-contaminating |
Steel ladles | Standard refractory | 75-150 μm | Cost-effectiveness, thermal shock resistance |
Cement kilns | Standard refractory | 45-150 μm | Abrasion resistance, alkali resistance |
Foundry applications present another set of requirements. Investment casting shells benefit from fine zirconium silicate flours (D50 of 20-45 μm) that provide smooth surface finish and excellent detail reproduction. Sand casting operations often use coarser grades (100-300 μm) that offer good permeability while maintaining dimensional stability.
Special applications such as catalysts, electronic ceramics, and biomedical implants require ultra-high purity grades with strict limits on radioactive elements and heavy metals. These specialized grades undergo additional processing to remove impurities and may cost significantly more than standard industrial grades.
Which Physical Properties Affect Zirconium Silicate Performance?
The physical characteristics of zirconium silicate directly impact how it performs in your application. Understanding these properties helps you predict material behavior and avoid costly production issues.
You might wonder which property matters most? While all physical characteristics play a role, particle size distribution often ranks as the most critical factor for many applications. It affects everything from rheological behavior in slurries to sintering characteristics and final product properties.
Particle size distribution influences:
Property | Effect of Finer Particles | Effect of Coarser Particles |
---|---|---|
Suspension stability | Improved | Reduced |
Rheological properties | Higher viscosity | Lower viscosity |
Sintering behavior | Lower temperature required | Higher temperature required |
Surface finish | Smoother | Rougher |
Opacity | Higher | Lower |
Processing cost | Higher | Lower |
Purity levels significantly affect performance, particularly in high-temperature applications. Impurities like TiO₂, Fe₂O₃, and Al₂O₃ can lower the melting point, alter color, and reduce chemical resistance. For electronic applications, even trace impurities can dramatically change electrical properties.
Density and hardness measurements provide valuable information about material quality and processing behavior. Standard zirconium silicate should have a density between 4.6-4.7 g/cm³. Lower values may indicate contamination or incomplete processing. Hardness affects wear resistance and grinding behavior, with typical Mohs hardness values of 7.5-8.0.
Thermal and chemical stability testing methods include:
- Differential thermal analysis (DTA) to determine phase transitions
- Thermogravimetric analysis (TGA) to measure weight changes with temperature
- Chemical resistance testing in various media (acids, bases, molten glass)
- Thermal shock resistance testing through rapid heating and cooling cycles
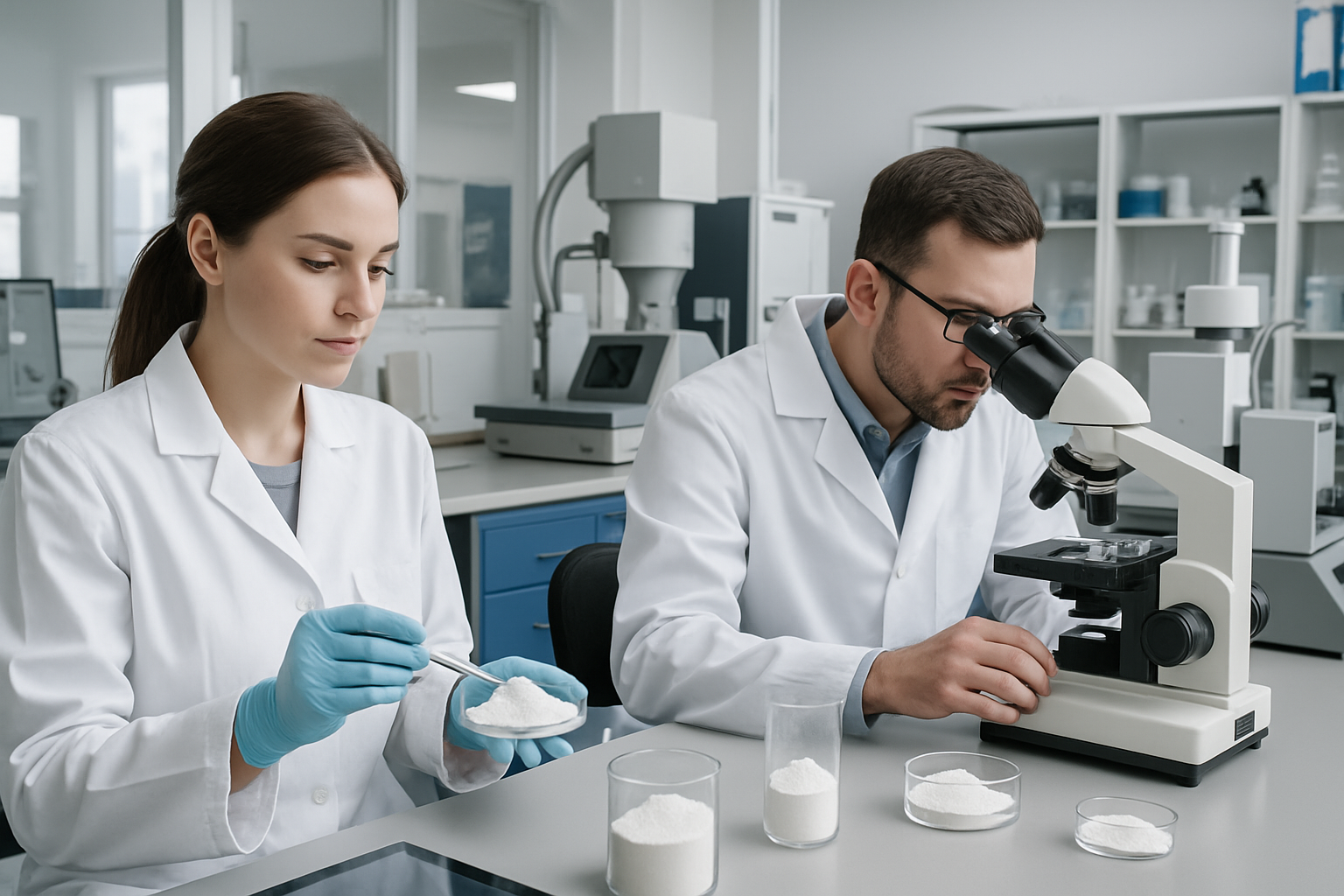
How To Evaluate Zirconium Silicate Quality From Different Suppliers?
Evaluating supplier quality represents a critical step in securing reliable zirconium silicate materials. Not all suppliers maintain the same standards, and variations can significantly impact your production process.
Let me share a practical approach: Start by assessing the supplier’s production capabilities and quality control systems. Established suppliers should willingly provide information about their raw material sources, processing methods, and quality assurance protocols. Look for ISO 9001 certification as a minimum standard, with additional certifications like ISO 14001 (environmental management) providing extra confidence.
When comparing suppliers, consider these evaluation criteria:
Evaluation Area | What to Look For | Red Flags |
---|---|---|
Production capacity | Sufficient volume to meet your needs | Frequent backorders or long lead times |
Technical support | Responsive experts who understand your application | Generic advice or sales-focused responses |
Quality control | Regular testing, documented procedures | Inconsistent specifications, limited testing |
Batch consistency | Tight control of key parameters | Significant variation between batches |
Sample availability | Willingness to provide test samples | Reluctance to provide samples before purchase |
Product consistency between batches proves particularly important for continuous manufacturing processes. Request certificates of analysis (CoA) for multiple batches and compare key parameters. Variations in particle size distribution, chemical composition, or whiteness can indicate poor process control.
Testing methods for incoming materials should include:
- X-ray fluorescence (XRF) for chemical composition
- Laser diffraction for particle size distribution
- BET surface area analysis
- Whiteness and brightness measurements (for ceramic applications)
- Scanning electron microscopy (SEM) for particle morphology
Small-scale trials before full implementation can save substantial costs. Design experiments that simulate your actual production conditions and evaluate the material’s performance against your specific requirements. Document results systematically to build a knowledge base for future reference.
How To Balance Cost And Performance For Optimal Value?
Finding the sweet spot between cost and performance challenges many purchasing managers. The lowest price rarely delivers the best overall value when selecting zirconium silicate grades.
The reality about pricing is eye-opening: Premium grades can cost 30-50% more than standard grades, but may reduce waste, improve product quality, or extend equipment life. Conversely, using an unnecessarily high-grade material wastes resources without providing proportional benefits.
Current market pricing structures vary by grade and volume:
Grade Type | Price Range (USD/ton)* | Key Cost Drivers |
---|---|---|
Standard (64-65% ZrO₂) | $1,200-1,500 | Raw material source, basic processing |
Premium (65-66% ZrO₂) | $1,500-1,800 | Additional purification, tighter specifications |
Micronized (1-5 μm) | $1,800-2,200 | Milling energy, classification costs |
Ultra-high purity | $2,500-3,500+ | Multiple purification steps, stringent testing |
*Prices are approximate and subject to market fluctuations
When analyzing long-term costs versus initial purchase price, consider these factors:
- Process yield improvements from higher-quality materials
- Reduced rejection rates and quality issues
- Energy savings from improved processing efficiency
- Maintenance costs related to equipment wear
- Inventory carrying costs for different grades
The relationship between performance improvements and cost increases often follows a non-linear curve. Initial upgrades from low to medium quality typically deliver substantial benefits for moderate cost increases. However, moving from high to ultra-high quality grades frequently shows diminishing returns, with small performance gains requiring significant price premiums.
Strategies to optimize value include:
- Blending different grades to achieve target properties at lower cost
- Working with suppliers on custom specifications that eliminate unnecessary parameters
- Consolidating purchases to gain volume discounts
- Implementing regular performance reviews to validate material selection decisions
What Storage And Handling Precautions Are Needed For Zirconium Silicate?
Proper storage and handling practices protect your investment in zirconium silicate materials and maintain their performance characteristics. Incorrect procedures can lead to contamination, moisture absorption, or safety hazards.
You should know these storage fundamentals: Zirconium silicate should be kept in a clean, dry environment with stable temperature and humidity. While not highly reactive, it can absorb moisture and contaminants that affect its processing behavior, particularly for fine grades.
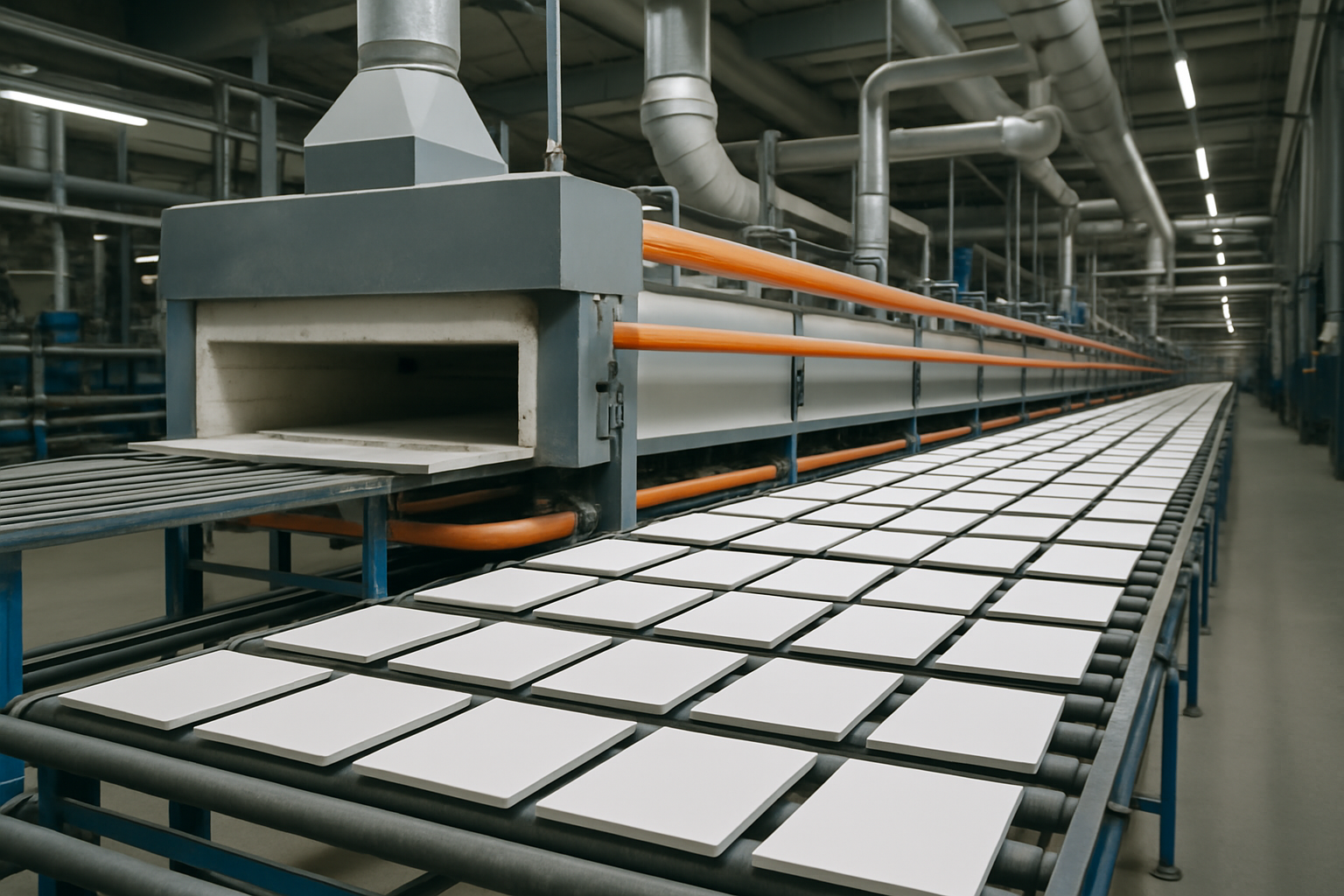
Recommended storage conditions include:
Parameter | Recommended Range | Potential Issues Outside Range |
---|---|---|
Temperature | 10-30°C | Condensation with temperature cycling |
Relative humidity | <60% | Moisture absorption, agglomeration |
Packaging | Sealed containers or moisture-resistant bags | Contamination, moisture absorption |
Storage time | Rotate stock, use within 1 year for fine grades | Agglomeration, changes in flow properties |
Safety considerations during handling focus on dust management. While zirconium silicate has low toxicity, fine particles can cause respiratory irritation and present a dust explosion hazard under specific conditions. Implement these safety measures:
- Use appropriate dust collection systems during transfer operations
- Provide workers with proper PPE including dust masks or respirators
- Implement good housekeeping practices to prevent dust accumulation
- Follow applicable regulations for handling industrial minerals
Contamination prevention requires systematic approaches:
- Dedicate handling equipment to specific materials
- Clean equipment thoroughly when changing materials
- Use color-coded containers for different grades
- Implement procedures for sampling that minimize contamination risk
Quality monitoring throughout storage involves periodic testing of key parameters. For longer storage periods, check moisture content, particle size distribution, and flow properties before use. Document any changes observed to refine storage practices.
What Future Trends Are Emerging In Zirconium Silicate Technology?
The zirconium silicate market continues to evolve, with several technological trends shaping future applications and procurement strategies. Staying informed about these developments helps you make forward-looking material selection decisions.
What’s happening in research labs right now? New processing techniques are creating nano-structured zirconium silicate with enhanced properties. These advanced materials show improved dispersion characteristics, higher reactivity, and novel catalytic properties that open possibilities for specialized applications.
Emerging trends in zirconium silicate technology include:
Trend Area | Current Developments | Potential Impact |
---|---|---|
Nano-structured materials | Controlled precipitation methods, sol-gel processing | Enhanced reactivity, lower processing temperatures |
Environmental processing | Reduced energy consumption, closed-loop water systems | Lower carbon footprint, reduced waste generation |
Functionalized grades | Surface modifications, dopants, composites | Tailored properties for specific applications |
Recycling technologies | Recovery from industrial waste streams | Reduced raw material costs, sustainability benefits |
Sustainability considerations increasingly influence material selection decisions. Manufacturers now evaluate the environmental footprint of zirconium silicate production, including energy consumption, water usage, and waste generation. Leading suppliers have implemented responsible mining practices and processing improvements that reduce environmental impact.
Application areas showing growth potential include:
- Advanced ceramics for electronic components
- Biomedical materials for implants and dental applications
- Specialized catalysts for environmental remediation
- High-performance coatings for extreme environments
- Energy storage and conversion technologies
For procurement professionals, these market signals warrant attention:
- Supply chain diversification as new producers enter the market
- Increasing emphasis on material traceability and sustainability documentation
- Development of application-specific grades with enhanced performance
- Growing demand from emerging technology sectors potentially affecting pricing
Staying informed through industry associations, technical conferences, and supplier relationships helps you anticipate changes that might affect material availability or specifications. Developing relationships with research institutions can provide early insights into emerging technologies and applications.
Conclusion
Selecting the right zirconium silicate grade requires balancing multiple factors including physical properties, application requirements, supplier quality, and cost considerations. By methodically evaluating these elements, you can identify the optimal material that delivers both performance and value for your specific manufacturing needs. Our analysis shows that companies taking this systematic approach typically reduce material-related quality issues by 40% while optimizing their material costs. Contact our technical team at ZircoMaterials today for a personalized consultation on your zirconium silicate selection challenges, and take advantage of our free material testing program to validate your choices before full implementation.
FAQ Section
Q1: What is the difference between zirconium silicate and regular silicates?
Zirconium silicate differs from regular silicates primarily through its zirconium oxide content, which grants the material superior heat resistance, wear resistance, and chemical stability. Regular silicates mainly consist of silicon dioxide, while zirconium silicate is a compound of zirconium oxide and silicon dioxide. This compositional difference gives zirconium silicate exceptional performance in high-temperature, high-wear, and corrosive environments, making it particularly suitable for demanding industrial applications.
Q2: How do I determine which particle size of zirconium silicate my application needs?
Determining the appropriate zirconium silicate particle size for your application requires considering several key factors: first, clarify your end product performance requirements, such as surface smoothness, density, or strength; second, evaluate your production process, including mixing methods, forming techniques, and sintering conditions; third, consider your equipment handling capabilities and process limitations. Generally, fine ceramics and precision coatings require finer particle sizes, while refractories and certain casting applications may benefit from coarser grades. Working with supplier technical teams and conducting small-scale tests is recommended to identify the optimal particle size.
Q3: How much does zirconium silicate purity affect final product performance?
Zirconium silicate purity significantly impacts final product performance. Higher purity products typically exhibit more consistent physical and chemical properties, resulting in more predictable processing behavior and final performance. Impurities can reduce heat resistance, chemical stability, and potentially cause unexpected reactions or phase changes in high-temperature applications. For electronic ceramics, optical applications, and certain high-performance refractories, purity is especially critical. However, some applications may not require the highest purity levels, allowing for cost optimization through selecting appropriate purity grades. The required purity level should be determined based on specific application requirements and performance standards.
Q4: What differences exist between same-grade zirconium silicate from different suppliers?
Same-grade zirconium silicate from different suppliers can vary in multiple aspects despite seemingly identical technical specifications. These differences may include: raw material sources and quality control standards; production processes and equipment precision; particle size distribution uniformity; specific composition of trace elements and impurities; batch-to-batch consistency; product aging and storage conditions; technical support and customization capabilities. These factors can cause nominally “identical” products to exhibit different processing characteristics and final performance in actual applications. Sample testing, small-scale trials, and supplier qualification assessments are recommended to identify these differences and select the product best suited for your specific application.
Q5: What common problems might occur when using zirconium silicate and how can they be solved?
Common problems when using zirconium silicate include: uneven dispersion causing inconsistent performance, which can be resolved through improved mixing techniques and appropriate dispersants; moisture-related processing difficulties, mitigated by controlling storage environment and pre-treatment processes; phase changes and volume variations in high-temperature applications, addressed by selecting properly stabilized zirconium silicate grades or adjusting sintering curves; compatibility issues with other materials, managed by adding suitable transition layers or interface modifiers; batch variation causing quality fluctuations, controlled through establishing strict supplier management and incoming inspection procedures. For specific issues, consulting with material supplier technical support teams is recommended for professional advice.