Zirconia materials are increasingly becoming a key solution for complex engineering challenges across industries. With their exceptional properties and diverse applications, choosing the right type of zirconia can significantly impact performance and cost-effectiveness. However, many engineers and purchasing managers find themselves confused when facing the multitude of zirconia options available. This article explores the unique characteristics of zirconia, helps you systematically evaluate your application requirements, and provides a practical framework for selecting the optimal zirconia material for your specific needs.
What Are Zirconia’s Key Properties?
Zirconia (ZrO₂) is an advanced ceramic material with a unique combination of physical and chemical properties. From a structural perspective, zirconia exists in three crystalline forms: monoclinic, tetragonal, and cubic phases, which are stable at different temperatures. What’s particularly important is that pure zirconia undergoes volume changes during phase transformations, which is why stabilizers such as yttria (Y₂O₃), magnesia (MgO), or calcia (CaO) are typically added to control its structure.
The most common types of zirconia materials in the market fall into three categories:
Type | Stabilizer Content | Key Characteristics | Typical Applications |
---|---|---|---|
Partially Stabilized Zirconia (PSZ) | 3-8% | High toughness, good thermal shock resistance | Industrial valves, pump components |
Fully Stabilized Zirconia (FSZ) | >8% | Excellent high-temperature stability, ionic conductivity | Oxygen sensors, solid oxide fuel cells |
Tetragonal Zirconia Polycrystal (TZP) | 2-3% | Extremely high strength and toughness | Medical implants, precision mechanical parts |
The mechanical properties of zirconia are impressive. Its hardness ranges from 1200-1400 HV, with flexural strength typically between 900-1200 MPa, far exceeding most ceramic materials. This matters because these properties allow zirconia to perform exceptionally well in high-load applications.
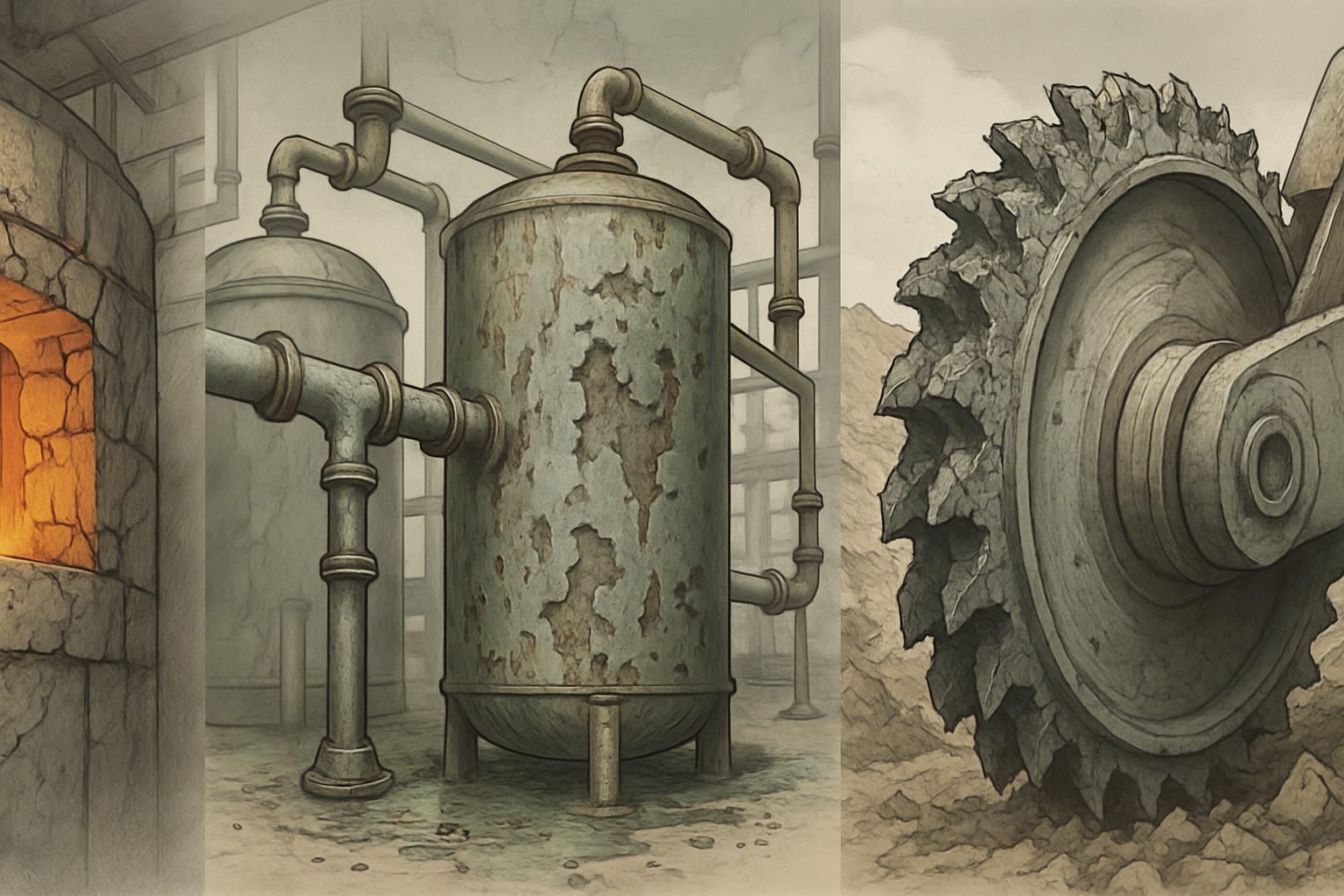
Zirconia’s thermal properties are equally remarkable. It maintains structural integrity at temperatures exceeding 2000°C, has low thermal conductivity (2-3 W/m·K), and moderate thermal expansion coefficient (approximately 10×10⁻⁶/K). This combination makes it ideal for thermal barrier coatings and high-temperature applications.
Regarding chemical stability, zirconia exhibits exceptional corrosion resistance, withstanding most acidic and alkaline solutions. This property is particularly valuable in chemical and petroleum industries, allowing zirconia components to function reliably in harsh environments for extended periods.
Zirconia also possesses excellent biocompatibility, and with its white appearance and adjustable translucency, it has become the material of choice for dental restorations and medical implants. That’s why the medical industry increasingly adopts zirconia as a replacement for traditional metallic materials.
Which Industries Use Zirconia Most Widely?
Zirconia materials have found critical applications across numerous industries thanks to their versatile performance characteristics. Let’s examine how these applications address specific challenges in various sectors.
In industrial manufacturing, zirconia is primarily used for critical components in high-wear and corrosive environments. Pump seals, bearings, valve seats, and sandblasting nozzles made from zirconia typically last 3-5 times longer than conventional materials. One chemical company reported that after switching critical pump components to zirconia, equipment failure rates decreased by 78%, saving over $200,000 in annual maintenance costs.
Industrial Application | Problem Solved by Zirconia | Performance Improvement |
---|---|---|
Pump seal rings | Wear and corrosion | 4× longer lifespan |
Bearings | High-temperature failure | 200°C higher operating temperature |
Valve seats | Corrosion and erosion | 300% extended maintenance intervals |
Sandblasting nozzles | Rapid wear | 5× lower replacement frequency |
The medical and dental fields represent one of the most innovative areas for zirconia applications. This is crucial because zirconia’s biocompatibility and aesthetic properties make it an ideal material for human implantation. Dental crowns and bridges, hip and knee prostheses, and surgical instruments widely utilize zirconia materials. Research data shows that zirconia dental restorations have a ten-year success rate exceeding 95%, significantly higher than many traditional materials.
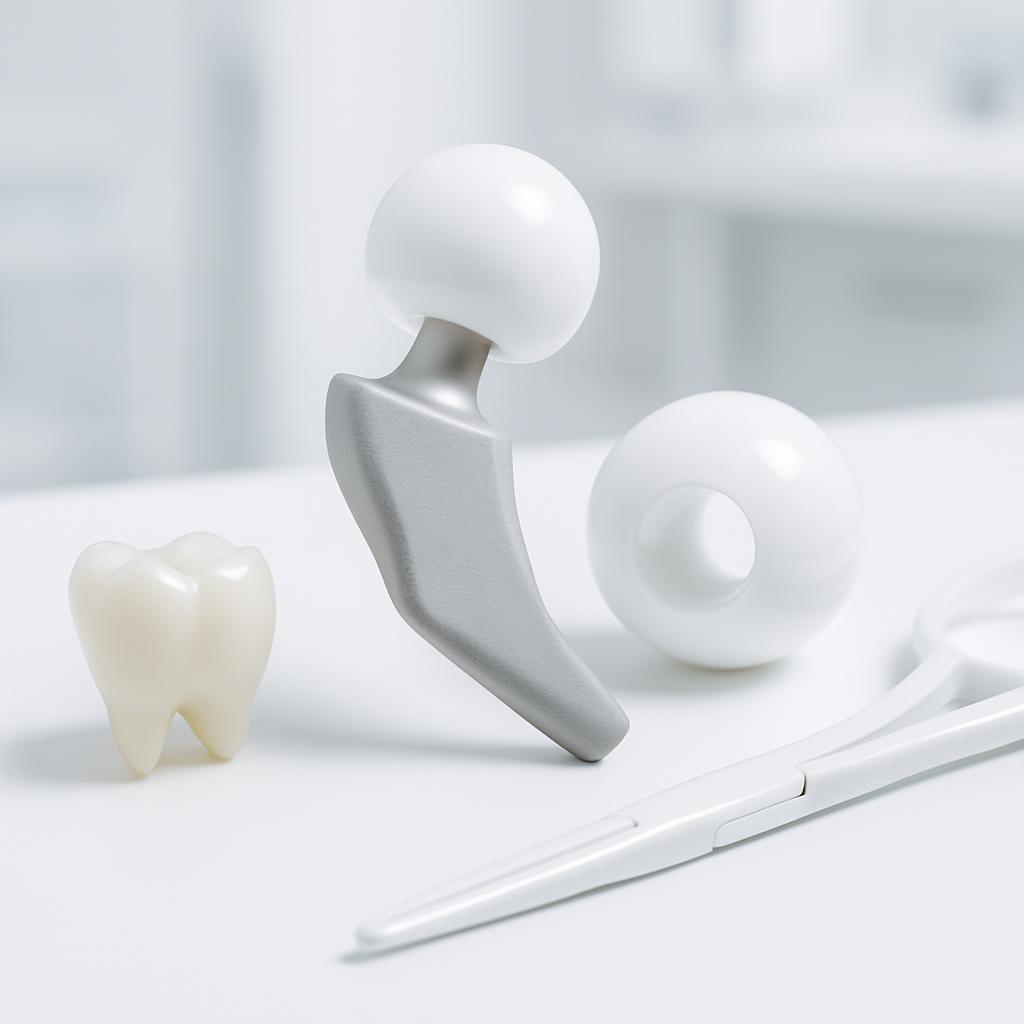
The electronics and semiconductor industries rely on zirconia to solve specific technical challenges. Zirconia films serve as dielectric layers in high-performance capacitors, while zirconia substrates provide ideal carriers for high-temperature electronic components. As device miniaturization trends strengthen, zirconia’s precision machining capabilities and dimensional stability become increasingly important.
In aerospace and automotive industries, zirconia primarily applies to high-temperature and high-pressure environments. Engine thermal shield components, combustion chamber parts, and sensor protection housings all utilize zirconia materials. These components must simultaneously withstand high temperatures, high pressures, and high-velocity gas flows, making zirconia’s comprehensive performance profile an ideal choice.
Emerging application areas include renewable energy equipment, 5G communication infrastructure, and additive manufacturing. Zirconia’s use in solid oxide fuel cells is growing rapidly, providing critical material support for clean energy technologies. That’s why materials scientists predict the zirconia materials market will grow at 7-9% annually over the next decade.
How Do You Assess Your Application’s Zirconia Needs?
Selecting the appropriate zirconia material requires systematic evaluation of your application environment and performance requirements. First, you must clearly define key application parameters.
Temperature is a primary consideration. Determining the operating temperature range, frequency, and amplitude of temperature fluctuations is critical. Different types of zirconia perform differently across temperature ranges:
Temperature Range | Recommended Zirconia Type | Considerations |
---|---|---|
<500°C | TZP or PSZ | Lower risk of low-temperature aging |
500-1000°C | PSZ | Good thermal shock stability |
>1000°C | FSZ | Avoids phase transformation volume changes |
High temperature fluctuations | Mg-PSZ | Superior thermal shock resistance |
The type and magnitude of mechanical loads are equally important. Is the load static or dynamic? Impact loading or sustained stress? Y-TZP zirconia performs excellently in high-strength applications, while Mg-PSZ is more suitable for applications requiring thermal shock resistance.
Chemical environment assessment should consider the pH, corrosiveness, and temperature of contact media. This matters because certain stabilizers may degrade in specific chemical environments. For example, Y-TZP may undergo low-temperature aging in water vapor environments, while Ce-TZP demonstrates better hydrolytic stability.
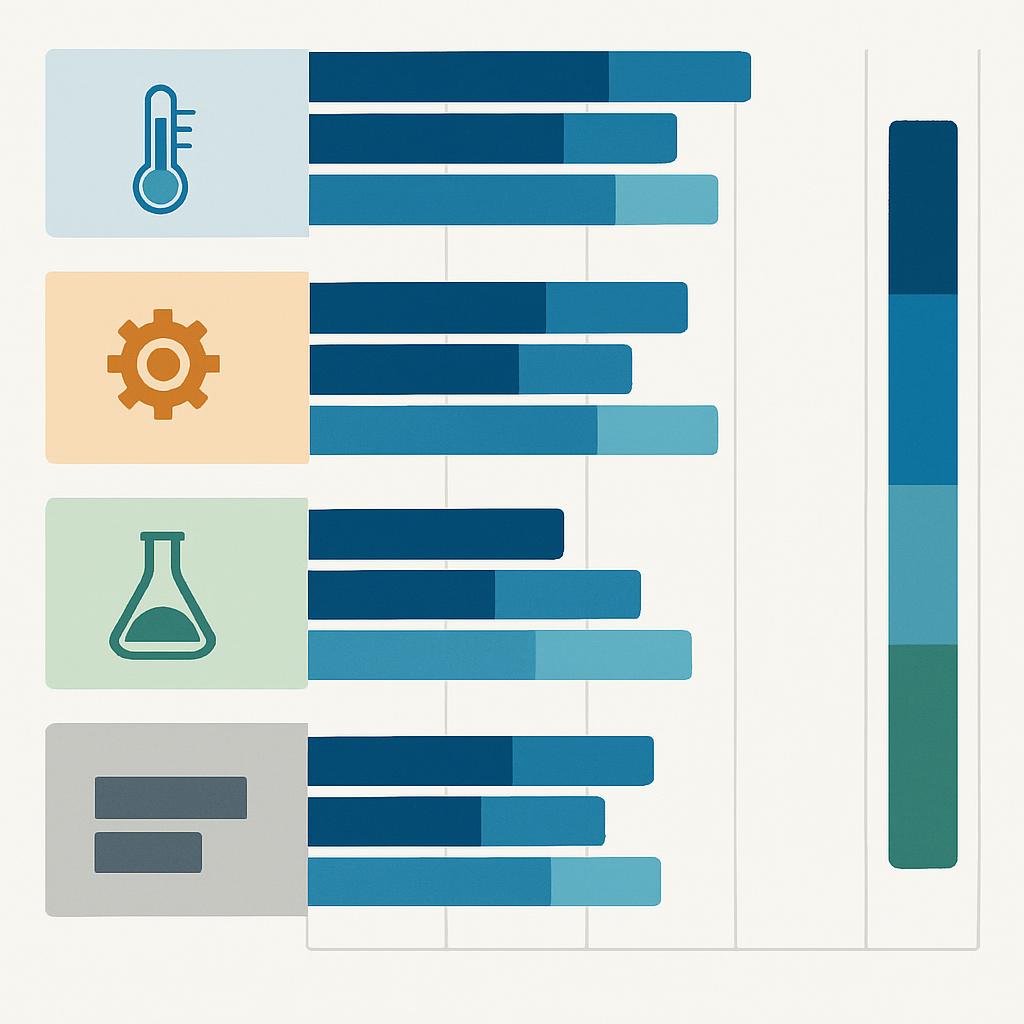
Cost-benefit analysis should consider initial investment, expected service life, maintenance requirements, and downtime costs. While zirconia components typically cost 20-50% more than traditional materials initially, the total lifecycle cost is often lower when considering extended service life and reduced maintenance needs. A study focused on the mining industry showed that zirconia pump components had approximately 35% lower five-year total ownership costs compared to metal components.
Lifecycle and reliability considerations require evaluating expected service years, failure modes, and safety factors. Critical applications typically require higher safety factors and stricter quality control.
Manufacturing process compatibility assessment should consider dimensional precision requirements, surface finish needs, geometric complexity, batch production requirements, and connection methods with other materials. By comprehensively considering these factors, you can establish a systematic decision matrix to help determine the most suitable zirconia type and grade for your specific application.
How Do Different Zirconia Types Compare?
Understanding the characteristics of different zirconia materials is essential for making informed choices. Let’s dive into the key differences between these materials.
Partially Stabilized Zirconia (PSZ) typically contains 3-8% stabilizers, forming a microstructure where tetragonal phase grains are dispersed in a cubic phase matrix. This structure gives PSZ excellent toughness and thermal shock stability. Magnesia-stabilized PSZ (Mg-PSZ) performs particularly well in thermal cycling applications, while calcia-stabilized PSZ (Ca-PSZ) offers better cost-effectiveness.
Property | Mg-PSZ | Ca-PSZ | Y-PSZ |
---|---|---|---|
Flexural Strength (MPa) | 600-800 | 500-700 | 700-900 |
Fracture Toughness (MPa·m^(1/2)) | 8-12 | 6-9 | 7-10 |
Thermal Shock Resistance | Excellent | Good | Moderate |
Relative Cost | Medium | Low | High |
Primary Applications | Pump parts, valves | Industrial furnace components | Precision mechanical parts |
Fully Stabilized Zirconia (FSZ) contains over 8% stabilizers, completely stabilizing it into a cubic structure. FSZ’s main advantages lie in its extremely high temperature stability and ionic conductivity, making it ideal for oxygen sensors and solid oxide fuel cells. However, FSZ typically has lower mechanical strength and toughness than PSZ and TZP.
Tetragonal Zirconia Polycrystal (TZP) contains a lower proportion of stabilizers (typically 2-3%), maintaining a fully tetragonal phase structure. This is particularly important because this structure gives TZP extremely high strength and toughness. Yttria-stabilized TZP (Y-TZP) is the most common type, widely used in medical implants and precision mechanical parts. Ceria-stabilized TZP (Ce-TZP), while slightly lower in strength, offers better resistance to low-temperature aging.
Zirconia composites enhance specific properties by introducing a second phase. Zirconia-alumina composites (ZTA or ATZ) combine the advantages of both ceramics, providing better overall performance. Zirconia-metal composites improve toughness and thermal conductivity by introducing a metallic phase, expanding the application range.
The cost and availability of various material types are also important selection factors. Y-TZP is typically higher priced but widely available, while specialty composites may require custom production with longer lead times. Depending on the criticality of the application and budget constraints, you may need to find a balance between performance and cost.
How Can You Avoid Common Zirconia Selection Mistakes?
When selecting zirconia materials, many engineers and purchasing managers tend to make common mistakes. Understanding these pitfalls can help you avoid costly errors.
Over-specification is one of the most common errors. Many engineers tend to select the highest-performing material without considering cost-effectiveness. For example, choosing Fully Stabilized Zirconia (FSZ) instead of Partially Stabilized Zirconia (PSZ) for moderate-temperature applications may lead to unnecessary cost increases. Establishing a clear performance requirements matrix and matching it with various zirconia options can prevent this waste.
Common Mistake | Potential Consequences | Avoidance Strategy |
---|---|---|
Over-specification | Unnecessary cost increases | Establish clear performance requirements matrix |
Ignoring working environment | Unexpected failures, shortened lifespan | Comprehensively evaluate all environmental factors |
Overlooking manufacturing limitations | Production difficulties, delivery delays | Consult manufacturing experts early |
Supply chain risk neglect | Material shortages, inconsistent quality | Establish multi-source supply strategy |
Ignoring the complete working environment is another serious mistake. This is critical because zirconia’s performance highly depends on its operating conditions. For example, Y-TZP may undergo low-temperature aging in humid environments, leading to strength degradation and potential catastrophic failure. One medical device manufacturer, by neglecting this factor, faced a batch recall of implants, resulting in millions of dollars in losses and serious reputational damage.
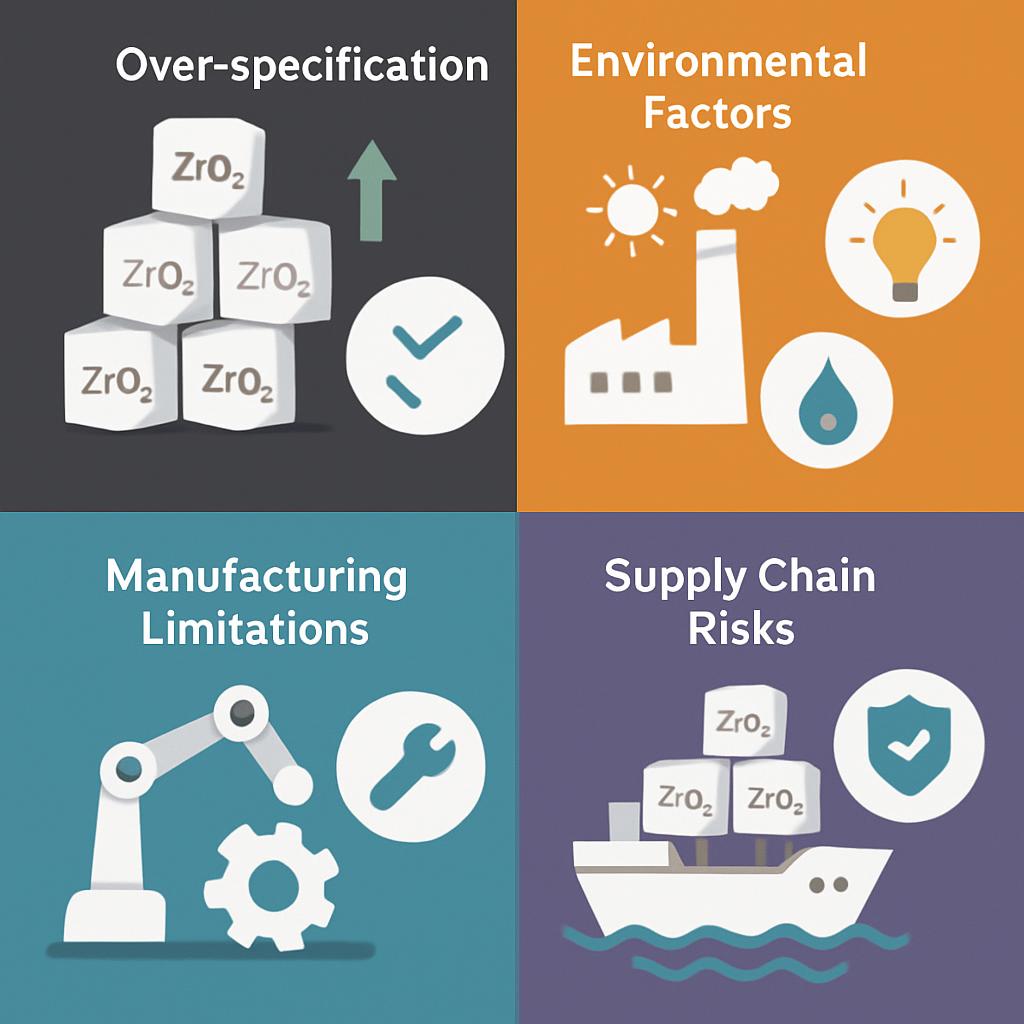
Manufacturing process limitations are also commonly overlooked. Zirconia’s high hardness makes it difficult and expensive to machine. The current mainstream method is to machine pre-sintered blanks first, then perform high-temperature sintering, but this process requires precise control of shrinkage rates to ensure final dimensional accuracy. Ignoring these limitations can lead to production difficulties, delivery delays, and cost overruns.
Supply chain and quality consistency issues are equally important. Zirconia components’ performance highly depends on their microstructure, and small process fluctuations can lead to significant performance differences. Establishing rigorous supplier qualification procedures and regular quality audits is crucial for maintaining consistent quality.
What Testing and Validation Methods Exist for Zirconia?
After selecting an appropriate zirconia material, proper testing and validation are crucial. This step cannot be overlooked because it ensures the material will achieve expected performance in actual applications.
Standard testing protocols and specifications provide the foundation for material evaluation. Commonly used standards include ASTM C1161 (flexural strength testing), ASTM C1421 (fracture toughness testing), and ISO 6872 (dental ceramics testing). These standardized tests ensure results are comparable and reproducible.
Test Type | Applicable Standard | Measured Parameter | Typical Value Range |
---|---|---|---|
Flexural Strength | ASTM C1161 | Strength (MPa) | 700-1200 MPa |
Fracture Toughness | ASTM C1421 | Toughness (MPa·m^(1/2)) | 5-12 MPa·m^(1/2) |
Hardness | ASTM C1327 | Vickers Hardness (HV) | 1200-1400 HV |
Thermal Shock Resistance | ASTM C1525 | Temperature Difference (°C) | 200-350°C |
Chemical Stability | ISO 6872 | Dissolution Rate (μg/cm²) | <100 μg/cm² |
Prototype validation and small-batch testing are key steps in the evaluation process. Before full-scale deployment, small-scale trials in actual working environments are recommended to collect performance data and verify preliminary assessment results. This step can identify potential issues early, reducing risks in large-scale applications.
Accelerated aging testing techniques can predict long-term performance in a shorter timeframe. Common methods include high-temperature aging tests, pressure cycling tests, autoclave tests for evaluating stability in water vapor environments, and corrosion immersion tests in concentrated chemical environments.
Non-destructive testing methods are essential for quality control and in-service monitoring. Common techniques include ultrasonic testing, X-ray inspection, and microscopic observation. These methods can detect microcracks, internal defects, and structural changes without damaging components.
How Can You Effectively Communicate Zirconia Requirements to Suppliers?
Effective communication with suppliers is key to obtaining suitable zirconia materials. This aspect is often underestimated, but it directly impacts the quality and performance of the final product.
Technical specifications form the foundation of communication and should include these key components:
- Material type and grade requirements
- Critical performance parameters and acceptable ranges
- Dimensional and tolerance requirements
- Surface finish and appearance standards
- Testing and certification requirements
- Batch consistency standards
Detailed and clear technical specifications can prevent misunderstandings and subsequent issues. One medical device manufacturer reduced supplier-related problems by 40% by improving its zirconia specifications.
Specification Component | Should Include | Common Communication Issues |
---|---|---|
Material Specifications | Type, stabilizer content, purity | Lack of clear material grade definition |
Performance Requirements | Strength, toughness, hardness ranges | Unspecified test methods and conditions |
Dimensional Specifications | Critical dimensions, tolerances, reference planes | Not accounting for sintering shrinkage |
Surface Requirements | Roughness, defect criteria | Subjective descriptions rather than quantified standards |
Testing Requirements | Test methods, sample size, acceptance criteria | Unclear responsibility and testing frequency |
Quality assurance and certification requirements should be clearly specified. For critical applications, ISO 9001, ISO 13485 (medical devices), or specific industry certifications may be required. Requirements for material certificates, test reports, and traceability documentation should also be clearly stated. This is important because it ensures the material meets all necessary standards and regulatory requirements.
Sample evaluation and batch consistency assurance represent another critical aspect. Sample evaluation procedures, acceptance criteria, and batch verification methods should be clearly defined. A practical strategy is to establish a phased verification process including initial sample evaluation, small batch verification, final confirmation before mass production, and regular batch audits.
Establishing long-term relationships is essential for consistently obtaining high-quality zirconia materials. This includes regular technical exchanges, joint development projects, and continuous improvement programs. One aerospace component manufacturer not only improved material quality but also shortened new product development cycles by 30% through establishing a strategic partnership with its zirconia supplier.
FAQ Section
Q1: How much more expensive are zirconia materials compared to traditional materials?
Zirconia materials typically cost 20-50% more initially than traditional materials, depending on purity, stabilizer type, and processing complexity. However, considering their extended service life (usually 3-5 times that of traditional materials) and reduced maintenance requirements, lifecycle cost analysis often shows zirconia to be more cost-effective in long-term use, particularly in high-temperature, high-wear, or corrosive environments.
Q2: At what temperatures can zirconia materials operate?
Different types of zirconia materials have varying temperature tolerances. Partially Stabilized Zirconia (PSZ) typically operates stably below 1000°C, while Fully Stabilized Zirconia (FSZ) can withstand temperatures up to 2200°C. However, long-term operating temperatures are typically recommended to be 200-300°C lower than maximum tolerance to ensure material stability and extend service life.
Q3: How do you determine zirconia material quality?
Evaluating zirconia quality involves multiple factors: first, check material density and porosity—high-quality zirconia should have >99% theoretical density; second, observe grain size and distribution uniformity; third, verify mechanical properties such as hardness, fracture toughness, and flexural strength meet specifications; finally, confirm batch consistency data and quality certifications from suppliers. Independent testing to verify key performance parameters is recommended.
Q4: What surface treatments can be applied to zirconia materials?
Zirconia materials can undergo various surface treatments, including precision grinding and polishing (achieving Ra<0.02μm), laser etching, sandblasting to increase surface roughness, plasma surface modification to enhance wettability, physical vapor deposition (PVD) coatings to enhance specific properties, and chemical treatments such as acid etching. Medical-grade zirconia can also undergo special treatments to enhance biocompatibility or antimicrobial properties.
Q5: What methods exist for joining zirconia to other materials?
Methods for joining zirconia to other materials primarily include: active metal brazing (using active elements like Ti, Zr), high-temperature glass or ceramic solder joining, mechanical connections (such as press-fitting or threaded connections), special high-temperature adhesive bonding, and gradient material transition layer connections. Selecting an appropriate joining method requires considering operating temperature, thermal expansion coefficient compatibility, mechanical loads, and chemical environment. The most complex applications may require combining multiple joining techniques.