The manufacturing world is witnessing a remarkable transformation as next-generation zirconia composites redefine what’s possible in extreme industrial environments. These advanced materials are solving longstanding challenges in sectors ranging from aerospace to energy production, where traditional ceramics simply couldn’t deliver the necessary performance. This article examines the cutting-edge zirconia composite materials that are meeting these demands, providing practical insights into their properties, manufacturing methods, and economic impact for technical decision-makers.
What Makes Next-Gen Zirconia Composites Revolutionary?
The latest generation of zirconia composites represents a fundamental leap beyond traditional ceramic materials, offering performance characteristics previously thought impossible in oxide-based systems.
Here’s the reality: while conventional zirconia ceramics have served industry well for decades, they’ve reached their performance limits in many critical applications. Next-generation composites overcome these limitations through revolutionary approaches to material design and processing.
Nanostructured zirconia composites stand at the forefront of this revolution. Unlike traditional materials with grain sizes in the micrometer range, these advanced composites feature precisely controlled structures at the nanoscale. This structural refinement dramatically enhances mechanical properties, particularly fracture toughness and resistance to thermal shock. For example, nanostructured zirconia-alumina composites demonstrate fracture toughness values up to 12 MPa·m^(1/2), nearly double that of conventional zirconia.
Interface engineering represents another breakthrough area. By carefully designing the boundaries between different phases within the composite, materials scientists can now control crack propagation pathways and energy dissipation mechanisms. This approach has yielded composites with unprecedented combinations of strength and toughness that maintain their properties at elevated temperatures.
Property | Traditional Zirconia | Next-Gen Zirconia Composites | Improvement Factor |
---|---|---|---|
Fracture Toughness | 4-6 MPa·m^(1/2) | 8-12 MPa·m^(1/2) | 2x |
Maximum Service Temperature | 1200°C | Up to 1500°C | 25% higher |
Thermal Shock Resistance | Moderate | Excellent | 3-4x better |
Wear Resistance | Good | Exceptional | 5-10x longer life |
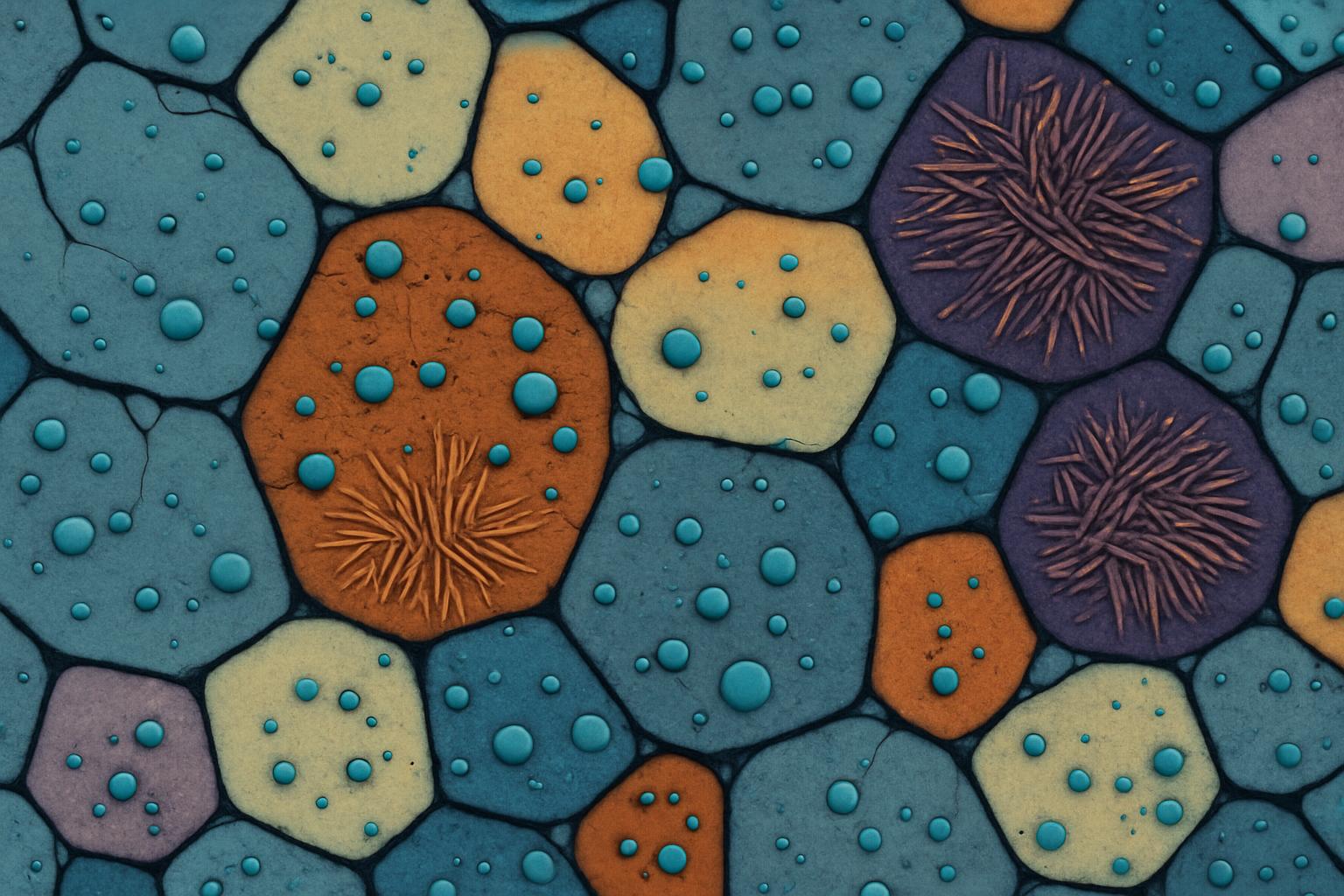
How Are Ceramic Matrix Composites Changing Manufacturing?
Ceramic matrix composites (CMCs) based on zirconia are fundamentally changing manufacturing capabilities and economics across multiple industries. These materials combine the high-temperature stability of ceramics with dramatically improved damage tolerance, opening new possibilities for component design and process efficiency.
Consider this key point: manufacturing processes that were once limited by material constraints can now operate at higher temperatures, faster speeds, and with greater energy efficiency. This translates directly to competitive advantage for early adopters.
The exceptional high-temperature performance of zirconia CMCs is transforming thermal processing applications. Components made from these materials can withstand temperatures up to 1500°C while maintaining their structural integrity and resistance to thermal cycling. This enables manufacturing equipment to operate at higher temperatures, increasing throughput and reducing energy consumption per unit produced. One automotive parts manufacturer reported a 22% increase in production capacity after retrofitting furnace components with zirconia-based CMCs.
Financial Metric | Short-Term Impact (Year 1) | Medium-Term Impact (Years 2-3) | Long-Term Impact (Years 4+) |
---|---|---|---|
Capital Investment | 30-50% higher than traditional materials | Minimal additional investment | Reduced replacement capital |
Energy Costs | 10-20% reduction | 15-25% reduction with optimization | 15-25% sustained savings |
Maintenance Costs | 40-60% reduction | 60-80% reduction | 60-80% sustained reduction |
Production Capacity | 5-15% increase | 15-25% increase with process optimization | 15-25% sustained improvement |
Which Industries Benefit Most From These Materials?
While zirconia composites offer advantages across many sectors, certain industries are experiencing particularly transformative benefits from these advanced materials.
The bottom line is: industries with the most extreme operating conditions—combining high temperatures, mechanical stress, and corrosive environments—stand to gain the most significant competitive advantages from adopting these materials.
The aerospace sector represents perhaps the most dramatic success story for advanced zirconia composites. High-temperature structural components in aircraft engines must withstand extreme thermal cycling, mechanical stress, and oxidative environments. Zirconia-based CMCs are now being used in turbine shrouds, combustor liners, and exhaust components, enabling higher operating temperatures that increase fuel efficiency by 5-8% while reducing weight by up to 30% compared to metal alternatives.
Energy generation and storage applications leverage the unique properties of these materials in multiple ways. Thermal barrier coatings based on nanostructured zirconia composites protect metal components in gas turbines, allowing higher operating temperatures and improved efficiency. Solid oxide fuel cell components manufactured from specialized zirconia composites offer enhanced ionic conductivity and durability, extending service life by 50-100% compared to conventional materials.
Industry | Key Applications | Primary Benefits | Adoption Stage |
---|---|---|---|
Aerospace | Engine components, thermal protection systems | Weight reduction, temperature capability, fuel efficiency | Commercial implementation |
Energy | Turbine components, fuel cells, nuclear applications | Efficiency, durability, safety | Early commercial/advanced pilot |
Automotive | Engine components, exhaust systems | Emissions reduction, performance, fuel economy | Growing commercial adoption |
Biomedical | Implants, surgical instruments, diagnostic equipment | Biocompatibility, wear resistance, aesthetics | Established in dental, growing in orthopedics |
Electronics | Substrates, insulators, process equipment | Thermal management, electrical properties, precision | Early adoption phase |

What Technical Properties Drive Their Performance?
The exceptional performance of next-generation zirconia composites stems from a carefully engineered set of technical properties that work together to overcome the limitations of traditional ceramics.
What you need to know: unlike conventional materials where improving one property often degrades others, advanced zirconia composites achieve synergistic combinations of properties through multi-scale design approaches.
Mechanical strength and toughness represent the most dramatic improvements in these materials. While traditional ceramics are strong but brittle, zirconia composites achieve both high strength (800-1200 MPa) and exceptional fracture toughness (8-12 MPa·m^(1/2)). This combination results from multiple toughening mechanisms operating simultaneously: transformation toughening from the zirconia matrix, crack deflection at engineered interfaces, and bridging effects from reinforcement phases.
Thermal expansion control and thermal conductivity optimization are critical for applications involving temperature gradients or thermal cycling. Engineers can now tailor these properties by adjusting composition and microstructure. Some zirconia composites achieve thermal expansion coefficients as low as 6-8 × 10^(-6)/K (compared to 10-12 × 10^(-6)/K for conventional zirconia), dramatically reducing thermal stresses during temperature changes.
Property | Conventional Ceramics | Advanced Zirconia Composites | Key Applications |
---|---|---|---|
Fracture Toughness | Low to moderate (1-5 MPa·m^(1/2)) | High (8-12 MPa·m^(1/2)) | Structural components, wear parts |
Maximum Use Temperature | Limited by phase stability | Enhanced by composite design | High-temperature processing, turbines |
Thermal Shock Resistance | Poor to moderate | Excellent | Rapid thermal cycling applications |
Corrosion Resistance | Good but brittle after exposure | Excellent with maintained toughness | Chemical processing, energy generation |
How Are These Materials Manufactured?
The exceptional properties of advanced zirconia composites result not only from their composition but also from sophisticated manufacturing processes that control structure at multiple scales.
What’s important to recognize: manufacturing methods for these advanced materials require precise control over every step from powder preparation to final sintering. Small variations in process parameters can significantly impact final properties.
Advanced powder metallurgy and sintering techniques form the foundation of zirconia composite manufacturing. The process begins with ultra-pure, nano-sized powders with precisely controlled particle size distributions. These powders undergo specialized mixing processes to achieve homogeneous distribution of different phases. Sintering typically occurs under carefully controlled atmospheres and temperature profiles, often using techniques like spark plasma sintering or hot isostatic pressing to achieve full densification while maintaining nanoscale features.
Additive manufacturing has revolutionized the production of complex geometries in zirconia composites. Direct ink writing, stereolithography, and selective laser sintering enable the creation of intricate structures impossible to produce through traditional methods. These techniques are particularly valuable for components with internal cooling channels, lattice structures, or custom geometries optimized for specific applications.
Manufacturing Approach | Advantages | Limitations | Technology Readiness |
---|---|---|---|
Advanced Sintering (SPS, HIP) | Near-theoretical density, controlled microstructure | Size limitations, equipment cost | Commercial production |
Additive Manufacturing | Complex geometries, reduced material waste | Post-processing requirements, size limitations | Early commercial/pilot |
Sol-Gel Processing | Excellent homogeneity, nanoscale control | Scaling challenges, shrinkage issues | Commercial for specific applications |
Coating Technologies | Optimized surface properties, gradient structures | Adhesion challenges at extreme conditions | Application-dependent |
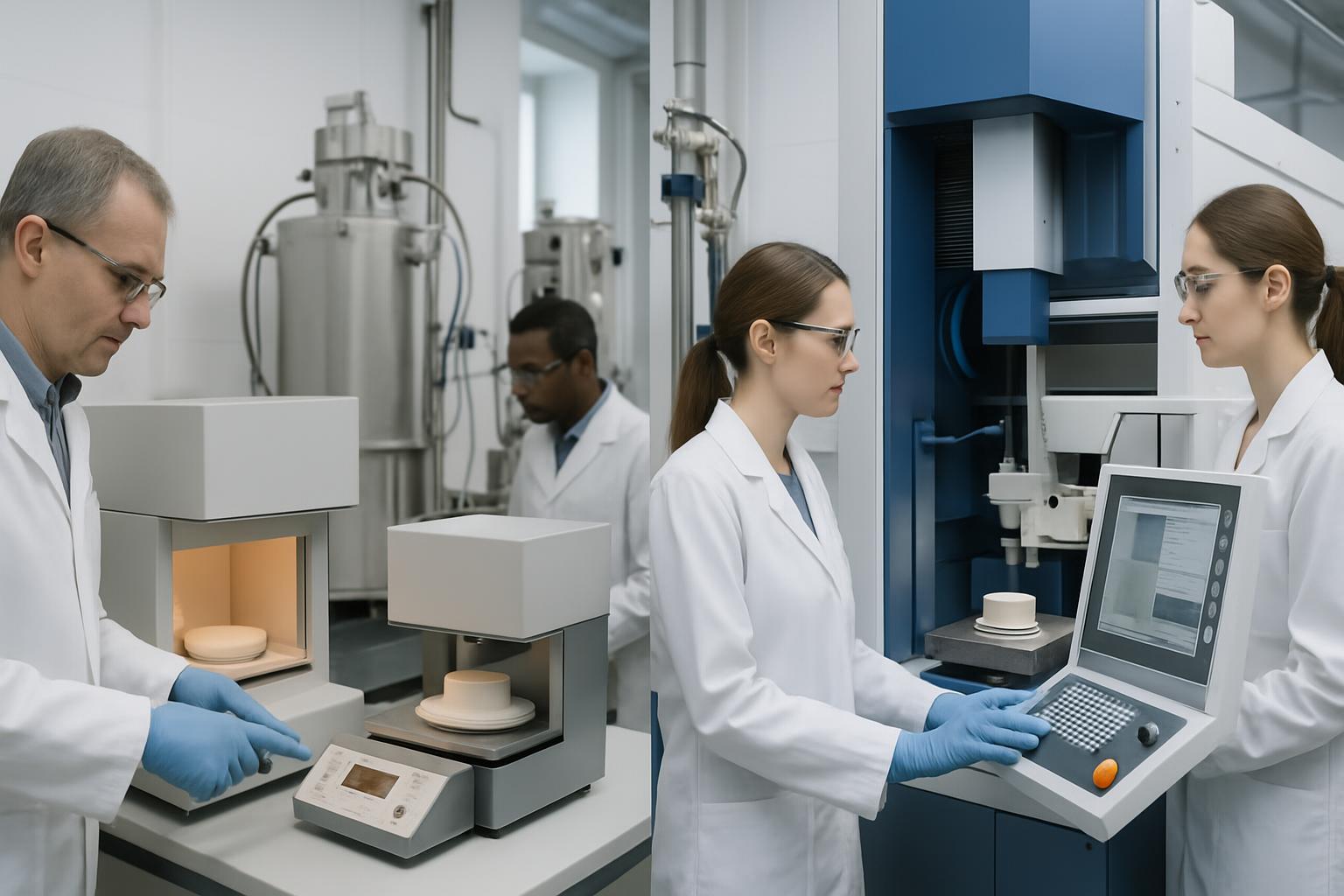
What Challenges Remain in Zirconia Composite Development?
Despite their remarkable properties, advanced zirconia composites face several challenges that limit broader adoption.
Let’s be clear: while these materials offer exceptional performance, they aren’t yet drop-in replacements for conventional materials in many applications due to cost, manufacturing, and design challenges.
Cost and consistency challenges in large-scale production represent perhaps the most significant barrier to wider adoption. Raw material costs for high-purity nanopowders and specialized reinforcements can be 5-10 times higher than conventional ceramics. Processing costs add further premiums due to specialized equipment requirements and longer processing times. These factors typically make zirconia composites 3-8 times more expensive than traditional alternatives on a component basis.
Manufacturing limitations for complex shapes and large components persist despite advances in processing technology. Current production methods struggle with components larger than approximately 30 cm in any dimension while maintaining uniform properties. Wall thickness variations, internal features, and sharp corners present particular challenges.
Standardization and certification processes have not kept pace with material development. Many industries lack established standards for testing, specifying, and qualifying these advanced materials. This creates barriers for both suppliers and end-users, as each application may require custom qualification procedures.
How Will Future Innovations Expand Applications?
The development of zirconia composites continues at a rapid pace, with several emerging technologies poised to further expand their capabilities and applications.
Here’s what’s coming: the next five years will likely bring materials with even more extreme temperature capabilities, self-healing properties, and integrated functionality that will enable entirely new classes of products and processes.
Next-generation zirconia composite systems currently in research laboratories show promising advances beyond today’s commercial materials. Ultra-high temperature compositions incorporating hafnium and tantalum compounds demonstrate stability above 2000°C—temperatures that would melt or rapidly degrade any conventional ceramic. Self-healing compositions that can repair microcrack damage during operation are showing promising results in laboratory testing.
The trend toward multifunctional composites represents a significant shift in material design philosophy. Rather than optimizing single properties, researchers are developing zirconia composites that simultaneously serve structural, thermal, electrical, and even sensing functions. For example, composites with integrated thermoelectric capabilities can generate electricity from thermal gradients while providing structural support and thermal protection.
Innovation Area | Current Development Stage | Potential Impact | Expected Commercialization |
---|---|---|---|
Ultra-High Temperature Composites | Advanced laboratory testing | Enable 2000°C+ operating environments | 3-5 years for initial applications |
Self-Healing Systems | Proof of concept demonstrated | Extend component life 2-3x in cyclic conditions | 4-7 years for commercial products |
Multifunctional Materials | Early prototypes | Combine structural, thermal, electrical functions | Application-specific, 2-6 years |
AI-Designed Composites | Algorithm development and validation | Accelerate development cycles by 50-70% | Already beginning in limited applications |
What Economic Impact Do These Materials Have?
Beyond their technical advantages, advanced zirconia composites are creating significant economic impacts across multiple industries.
The economic reality is: while these materials require higher initial investment, they often deliver substantial long-term value through performance improvements, extended service life, and system-level benefits that far outweigh their premium costs.
The global market for advanced zirconia composites is growing rapidly, with current estimates placing it at approximately $1.2 billion annually and projecting growth to $3.5-4.0 billion by 2030. This represents a compound annual growth rate of 12-15%, significantly outpacing most specialty materials markets. The aerospace sector currently accounts for the largest share (approximately 35%), followed by industrial processing (25%), energy generation (20%), medical applications (12%), and electronics (8%).
The total cost of ownership analysis typically shows compelling economics despite higher acquisition costs. For example, a chemical processing company replaced metal heat exchanger components with zirconia composites at 4.5 times the initial cost but achieved a 3-year ROI of 285% through extended service life, reduced maintenance, and higher process efficiency.
Conclusion
Advanced zirconia composites are fundamentally changing what’s possible in extreme industrial environments, offering unprecedented combinations of properties that solve longstanding materials challenges. These materials deliver exceptional performance through sophisticated engineering at multiple scales—from nanoscale reinforcements to carefully designed interfaces and optimized microstructures. Organizations that have implemented these materials report significant competitive advantages, including 30-50% longer component lifespans, 5-15% efficiency improvements, and access to operating conditions beyond the capabilities of conventional materials. To leverage these advanced materials effectively, partner with Global Industry for comprehensive technical support, from material selection through implementation and performance validation.
FAQ Section
Q1: How does the cost of zirconia composites compare to traditional materials?
Advanced zirconia composites typically cost 3-8 times more than conventional ceramics and 5-15 times more than high-performance metals on a per-unit basis. However, lifecycle cost analysis often shows favorable economics due to extended service life (typically 2-5 times longer), reduced maintenance requirements, and system-level efficiency improvements. The most compelling economic cases occur in applications where downtime is extremely costly, operating conditions are severe, or where the materials enable performance that’s impossible with alternatives.
Q2: What are the most effective supplier qualification processes for zirconia composites?
Effective supplier qualification for advanced zirconia composites should include comprehensive technical assessment and business evaluation. Technical qualification should examine material property documentation, statistical process control data, and quality management systems. Request sample components for independent testing, focusing on properties critical to your application. Business qualification should assess production capacity, financial stability, and technical support capabilities.
Q3: How can companies balance cost efficiency with performance in zirconia composite applications?
Companies can optimize the cost-performance balance by implementing application-specific material selection and design approaches. First, clearly define the critical performance requirements and operating conditions to avoid over-engineering. Consider hybrid designs that use zirconia composites only where their unique properties are essential, combined with conventional materials elsewhere.
Q4: What testing protocols best predict real-world performance of these materials?
The most effective testing protocols combine standardized mechanical and thermal testing with application-specific simulations of actual operating conditions. Standard tests should include fracture toughness (ASTM C1421), flexural strength (ASTM C1161), thermal shock resistance (ASTM C1525), and relevant environmental exposure tests.
Q5: How are sustainability requirements changing zirconia composite development?
Sustainability considerations are increasingly influencing zirconia composite development in several ways. Manufacturing processes are evolving to reduce energy consumption and waste generation, with innovations like lower-temperature sintering and near-net-shape forming. Material compositions are being reformulated to eliminate or reduce environmentally problematic elements while maintaining performance.