In the realm of advanced materials, the performance of zirconia powder is a significant concern for many industries. Manufacturing professionals often face challenges related to its properties, such as strength and durability. This article addresses these concerns by exploring the latest methods of surface treatment that can significantly improve zirconia powder performance. By understanding these innovative techniques, industry players can resolve their performance issues effectively. With expert insights and practical examples, this comprehensive article aims to equip decision-makers with the knowledge to enhance their products and processes.
How Do Surface Treatments Impact Performance?
Surface treatments play a vital role in improving the performance of materials like zirconia powder. The surface characteristics of zirconia directly influence its behavior in applications ranging from dental materials to advanced ceramics. For example, untreated zirconia often suffers from issues such as inadequate strength, wear resistance, and poor adhesion properties. These limitations can hinder the material’s effectiveness in critical applications.
By applying specific surface treatments, manufacturers can effectively address these challenges. These treatments enhance different physical and chemical properties, leading to better overall performance. For instance, surface treatments can increase the material’s resilience to pressure and temperature changes, which is particularly essential in high-stress environments.
Key Benefits of Surface Treatments:
- Improved Strength: Enhanced durability against mechanical stress.
- Increased Wear Resistance: Reduced degradation in demanding applications.
- Better Bonding: Improved adhesion properties for composites and coatings.
- Enhanced Thermal Stability: Ability to maintain properties under high temperatures.
As a business decision-maker, it’s important to recognize that these enhancements can result in products that meet or exceed customer expectations. But what kind of surface treatments are out there?
Understanding the latest advancements provides insight into the potential improvements in performance. Many treatments focus on creating a more robust bonding structure or altering the particle surface characteristics to enhance performance in applications.
Surface Treatment Method | Description | Key Benefits |
---|---|---|
Chemical Treatments | Use of chemical agents to modify properties | Enhances bond strength and stability |
Mechanical Treatments | Physical processes like milling | Improves particle shape and uniformity |
Thermal Treatments | High-temperature methods like sintering | Alters microstructure for better toughness |
By leveraging these surface treatments, manufacturers can ensure their zirconia products perform exceptionally well in various applications.
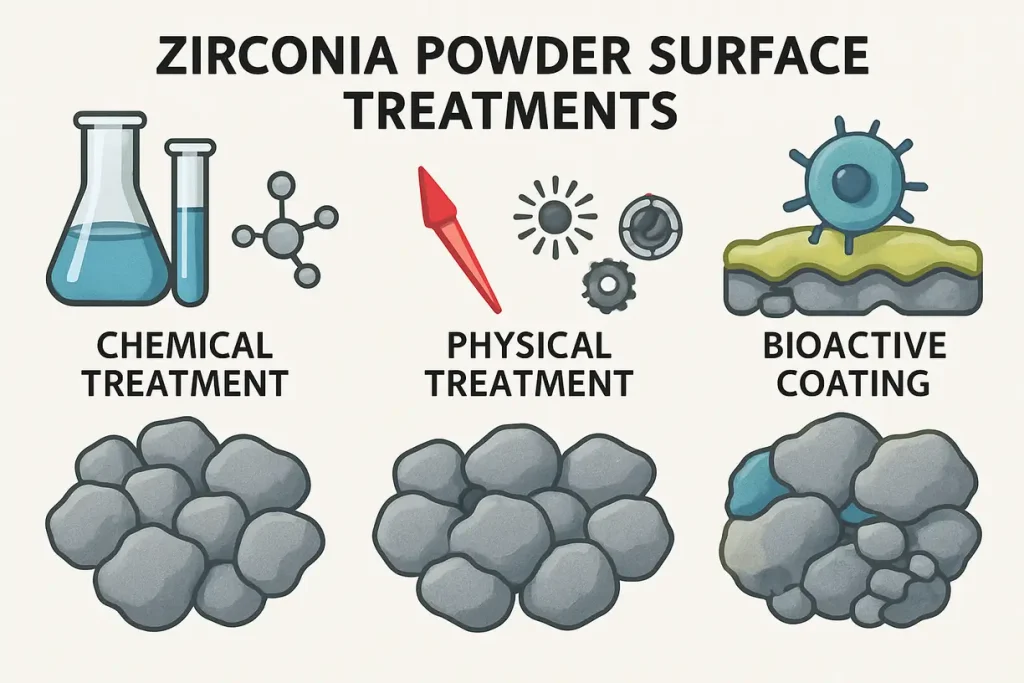
This image illustrates the various surface treatment methods applied to zirconia powder, showcasing the techniques used.
What Are the Latest Surface Treatment Techniques?
A range of emerging surface treatment techniques can significantly improve the performance of zirconia powder. Among these, chemical treatments, mechanical methods, and thermal processes stand out as leading options.
Chemical treatments often involve the use of specialized solutions that alter the chemical composition of the surface. These treatments can increase the chemical reactivity of the surface, which enhances adhesion in bonding applications. For example, using silane solutions can create stronger chemical bonds with other materials, particularly in dental applications.
Mechanical methods include processes like grinding, milling, and polishing, which refine the particle shapes for better packing density and strength. Why does this matter? When zirconia particles have a uniform shape and size, they can flow better during mixing and lead to more consistent final products. This uniformity reduces the likelihood of defects, which is critical for high-performance applications such as prosthetic dental work.
Thermal processes, such as sintering, also contribute to performance enhancements. By applying heat, manufacturers can promote the desired microstructure and phase transformations, which play a key role in performance attributes. Sintering improves the overall strength and vitality of zirconia, making it suitable for high-stress applications.
As you can see, there are several options, and understanding these can inform better decisions in treatment applications. Companies should consider their specific requirements and choose the most appropriate methods to gain the desired performance benefits.
Treatment Type | Advantages | Limitations |
---|---|---|
Chemical | Enhances chemical stability | May require special handling |
Mechanical | Improves particle uniformity | Can be labor-intensive |
Thermal | Alters microstructure | High-energy costs |
How Do Chemical Treatments Affect Zirconia?
Chemical treatments are particularly noteworthy for their ability to enhance the performance of zirconia powder. These treatments can significantly impact the physical properties of the material, including hardness, chemical reactivity, and resistance to cracking.
For example, applying silane or other bonding agents can modify the zirconia surface at a molecular level. This modification not only leads to improved adhesion properties but also enhances the overall compatibility of zirconia in composite materials. Such enhancements make zirconia powder more suitable for applications in dentistry and ceramics, where durability and aesthetic appeal are crucial.
Furthermore, chemical treatments can create a more porous surface texture, which can be beneficial for certain applications. The increased surface area allows better bonding with other materials, enhancing the performance of dental restorations or ceramic composites.
In addition to silane treatments, other notable chemical treatments include:
- Acidic Treatments: Increase surface roughness and promote stronger adhesion with restoratives.
- Alkali Treatments: Enhance dispersion and surface homogeneity, aiding in the uniformity of the final product.
Overall, understanding the nuances of chemical treatments can provide manufacturers with valuable strategies to improve performance and reliability, ensuring that zirconia remains a top choice in demanding applications.
Chemical Treatment | Effect on Performance | Common Applications |
---|---|---|
Silane Treatment | Improves bonding strength | Dental ceramics |
Acidic Treatments | Enhances surface roughness | Adhesives |
Alkali Treatments | Aids in particle dispersion | Battery components |
What Role Does Mechanical Treatment Play?
Mechanical treatments are essential for optimizing the performance of zirconia powders. These methods involve physical manipulation of the particles to enhance their characteristics, ensuring that the material performs as expected in various applications.
Techniques such as grinding, milling, and sieving play a pivotal role in achieving the desired particle size and shape. Why does this matter? Spherical or uniformly shaped particles tend to flow better, which can lead to more uniform mixing and improved performance in the final product. Enhanced particle characteristics can significantly impact the manufacturing processes and end-use applications.
In addition to improving flowability, mechanical treatments can also enhance the toughness of zirconia. Tighter control over particle size reduces porosity, resulting in denser and stronger materials—qualities that are crucial for applications requiring high durability, such as dental prosthetics and structural ceramics.
Key Mechanical Treatment Techniques:
- Grinding: Reduces particle size and improves uniformity.
- Milling: Breaks down larger agglomerates into fine particles.
- Sieving: Eliminates undesired fine particles, ensuring consistency in size distribution.
By employing these mechanical treatment techniques, manufacturers can create zirconia powders that not only meet specific application requirements but also enhance the overall quality and performance of their products.
Mechanical Treatment | Benefits | Considerations |
---|---|---|
Milling | Better particle size control | Time-consuming process |
Grinding | Increases shape uniformity | Equipment costs |
Sieving | Eliminates fine particles | Requires additional handling |
These strategies underline the importance of mechanical treatments in obtaining high-quality zirconia powder suitable for demanding industrial applications.
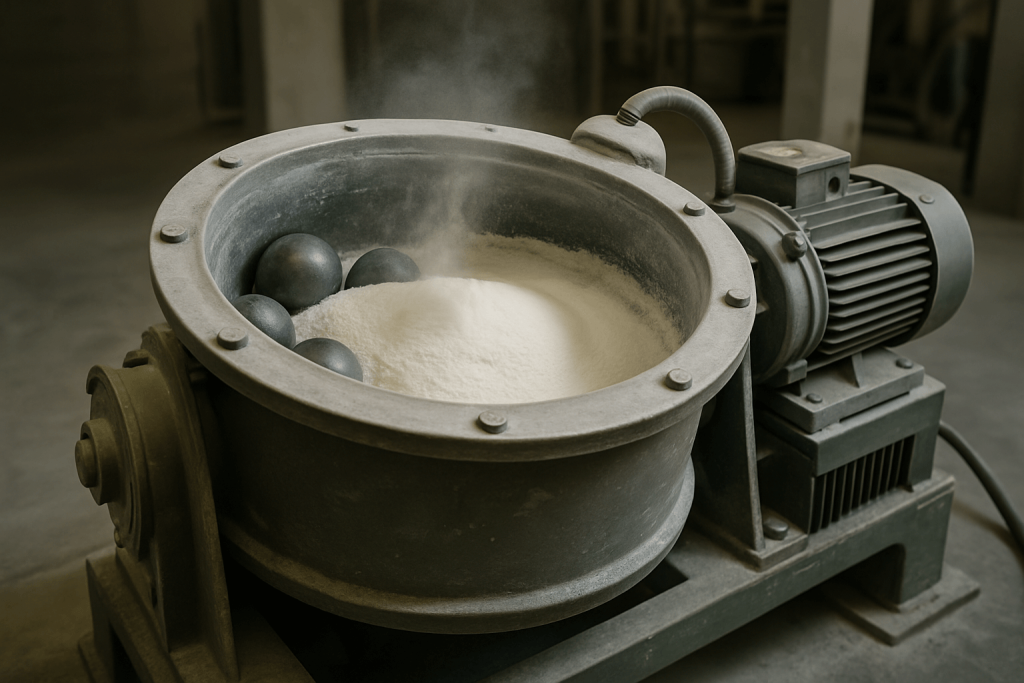
This image depicts the mechanical treatment processes such as grinding and sieving used to enhance zirconia powder quality.
How Do Thermal Treatments Enhance Zirconia?
Thermal treatments are another key approach to enhancing zirconia performance. These processes utilize heat to promote changes in the microstructure of zirconia powder. By adjusting the temperature and duration of heating, manufacturers can achieve various beneficial effects that improve the overall material properties.
For instance, sintering involves heating the zirconia powder to a temperature just below its melting point. This technique densifies the material by allowing particles to bond together, creating a stronger structure with fewer porosities. The reduced porosity not only improves the mechanical strength but also enhances the durability of the product in harsh environments.
In addition to sintering, other thermal treatments such as annealing and quenching can also have significant effects on zirconia’s properties. Annealing can relieve internal stresses that develop during production, resulting in a more stable microstructure. On the other hand, quenching can increase toughness, making zirconia resistant to crack propagation.
Here are some benefits of thermal treatments:
- Improved mechanical strength
- Enhanced thermal stability
- Reduced internal stresses
These treatments are particularly relevant for industries that require materials to withstand high temperatures and mechanical loads, such as aerospace and automotive sectors.
Curious about the impact of these treatments? They can lead to products that remain stable under extreme conditions, making them valuable in various industrial applications.
Thermal Treatment | Impact on Properties | Typical Use Cases |
---|---|---|
Sintering | Increased density | Structural ceramics |
Annealing | Reduced internal stresses | High-temperature applications |
Quenching | Enhanced toughness | Aerospace components |
How Can Hybrid Treatments Improve Results?
Hybrid treatments combine multiple surface treatment methods to optimize zirconia performance. This approach can yield superior results compared to applying a single treatment method, offering a comprehensive solution to performance issues.
For instance, combining mechanical and chemical treatments may enhance particle characteristics while also improving chemical stability. How does this help? The dual approach increases not only the toughness and durability of zirconia but also its ability to bond effectively with other materials, which is particularly beneficial in demanding environments such as dental implants or aerospace components.
Using hybrid strategies can also enable companies to tailor treatments to their specific needs. By customizing the treatment process, businesses can maximize the benefits of each method, thereby addressing unique performance challenges effectively.
Examples of hybrid treatment combinations include:
- Chemical + Mechanical: Enhances surface adhesion while refining particle size for optimal flow.
- Mechanical + Thermal: Improves microstructure and prevents defects during manufacturing.
- Thermal + Chemical: Increases stability and resistance to environmental factors, enhancing long-term performance.
Thinking about real-world applications? Many industries have already adopted hybrid treatment methods, realizing significant improvements in product quality and durability.
Moreover, the flexibility of hybrid approaches facilitates innovation by allowing companies to experiment with different combinations. This adaptability can result in unique products that stand out in the market, providing competitive advantages.
Hybrid Treatment Type | Advantages | Challenges |
---|---|---|
Combination of Chemical & Mechanical | Comprehensive enhancement | Complexity in process management |
Mechanical with Thermal | Optimal strength and stability | Increased processing time |
In summary, hybrid treatments represent a cutting-edge solution that can enhance zirconia’s performance while providing companies the opportunity to differentiate their products through innovative applications.
What Testing Methods Validate Performance Improvements?
Testing methods are crucial for validating the enhancements made through surface treatments. Various quantitative and qualitative assessments can provide insights into the performance of treated zirconia.
Common testing methods include:
- Mechanical Testing: Assess strength and toughness values.
- Adhesion Tests: Measure the bonding strength of treated surfaces.
- Thermal Conductivity Tests: Evaluate how well the treated material performs under heat.
These tests help confirm that surface treatments yield the desired improvements in performance.
But what metrics should you focus on? Metrics like hardness, tensile strength, and wear resistance are vital for assessing material performance.
Having a structured testing methodology in place allows companies to track the effectiveness of their surface treatments. This not only ensures product reliability but also fosters continuous improvement.
Testing Method | Purpose | Key Metrics |
---|---|---|
Mechanical Testing | Evaluate strength and toughness | Hardness, Yield Strength |
Adhesion Tests | Test bonding effectiveness | Adhesion Strength |
Thermal Testing | Measure temperature stability | Thermal Conductivity |
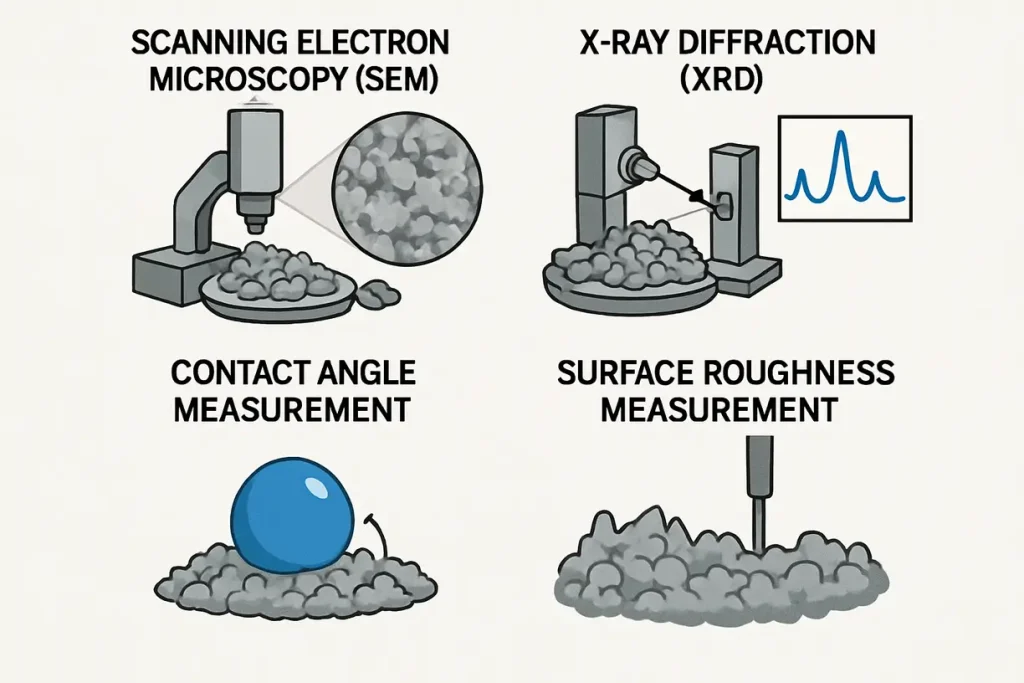
This image illustrates different testing methods used to assess the effectiveness of surface treatments for zirconia powder.
What Are the Industry Applications of Treated Zirconia?
Treated zirconia powders have found applications across various industries. Each sector leverages the enhanced properties to meet specific needs.
In the dental sector, treated zirconia is favored for crowns and bridges due to its strength and aesthetic appeal. The combination of durability and natural appearance provides significant benefits to dental professionals and patients alike.
In ceramics, treated zirconia is commonly used for high-performance components. The properties achieved through surface treatments allow for greater design flexibility and improved mechanical strength.
Industries like aerospace and automotive also utilize treated zirconia for components that require high wear resistance and thermal stability.
So, what’s next for treated zirconia? The growing use in innovative applications shows promising potential for the future of materials science.
Industry | Applications | Reasons for Use |
---|---|---|
Dental | Crowns and bridges | Aesthetic and durable |
Ceramics | High-performance components | Design flexibility |
Aerospace & Automotive | Engine components | Resistance to wear & heat |
What Challenges Exist with Surface Treatments?
While surface treatments offer numerous benefits, several challenges may arise that warrant careful consideration.
Cost Implications
Cost implications are often a significant concern for manufacturers. The investment in advanced technology and the acquisition of specialized raw materials can lead to substantial initial expenses. Businesses need to conduct a thorough cost-benefit analysis to weigh the advantages of enhanced performance against these initial outlays.
Scalability
Scalability presents another challenge. Many surface treatment processes may not be easily scalable for mass production. Companies must develop strategies to maintain quality while increasing output, ensuring that treatments applied to small batches yield the same results when applied on a larger scale.
Knowledge and Skill Requirements
Another challenge lies in the knowledge and skill required for proper implementation of these treatments. Training personnel in sophisticated techniques is essential for achieving consistent results. A lack of expertise can lead to inconsistent treatment effectiveness, resulting in subpar final products.
Considerations to Address These Challenges:
- Develop a clear framework for assessing treatment costs versus expected product longevity.
- Engage in pilot studies to understand scalability limitations and refine processes before full implementation.
- Invest in training programs to ensure staff are adept at using new technologies and treatment methods.
It’s essential to consider these factors. Addressing the challenges early can smooth the implementation of surface treatment processes, leading to more successful outcomes.
Challenges | Description | Considerations |
---|---|---|
Cost Implications | Equipment and material expenses | Initial investment vs. long-term gain |
Scalability | Difficulty in mass production | Maintaining quality at higher volumes |
Knowledge Requirements | Need for specialized skills | Investing in personnel training |
By understanding and proactively addressing these challenges, companies can better navigate the complexities associated with surface treatments, ensuring the successful enhancement of zirconia powder performance.
How Can Companies Implement These Treatments Effectively?
For successful implementation of surface treatments, companies should follow a structured approach. Start by evaluating the specific needs of your product and identifying which surface treatments would yield the best results.
Next, invest in the right equipment and technologies that support the chosen treatments. Training personnel in the proper techniques is crucial for achieving consistent results.
Finally, it’s vital to establish a monitoring and adjustment plan. Regularly assessing the results of the treatments allows for ongoing optimization.
Ready to take action? Effectively addressing performance challenges through surface treatments can lead to significant benefits for your products and ultimately, your bottom line.
Implementation Steps | Actions Required | Expected Outcomes |
---|---|---|
Identify Needs | Assess performance challenges | Tailored treatment solutions |
Invest in Technology | Acquire necessary equipment | Enhanced treatment capabilities |
Train Personnel | Provide training on techniques | Consistent application of processes |
Conclusion
In summary, the landscape of zirconia powder performance can be greatly improved through various surface treatment methods. From chemical and mechanical approaches to thermal processes and hybrid applications, the options are designed to meet specific challenges. As a manufacturer or decision-maker, adopting these treatments can lead to more robust products and satisfied customers.
At Global Industry, we are here to help you through the process of enhancing zirconia properties effectively. For expert guidance tailored to your needs, reach out to us and let’s discuss how we can partner together for success.
FAQ Section
Q1: What are surface treatments of zirconia powder?
Surface treatments involve various methods aimed at enhancing the surface characteristics of zirconia powder. These treatments can improve properties such as adhesion, strength, and wear resistance, ultimately leading to better performance in specific applications. They are particularly essential in industries like dentistry and ceramics, where precision and durability matter.
Q2: Which techniques are most effective for zirconia treatments?
Effective techniques for zirconia treatments include chemical methods (like silane treatments), mechanical methods (such as milling and grinding), and thermal treatments (including sintering). Each technique serves a specific purpose—chemical methods enhance bonding, mechanical methods improve particle uniformity, and thermal treatments refine the microstructure to increase strength.
Q3: How do surface treatments affect zirconia’s mechanical properties?
Surface treatments can significantly enhance zirconia’s mechanical properties, such as hardness, strength, and fracture toughness. By optimizing the surface characteristics, treated zirconia can withstand higher stresses and resist wear, making it highly advantageous for applications requiring durability, like dental implants and structural components.
Q4: Are treated zirconia powders more cost-effective?
While initial treatment costs may be higher, treated zirconia powders can lead to long-term savings through improved product performance and durability. Enhanced materials often reduce failure rates and maintenance expenses, translating into better value for companies over time.
Q5: What industries benefit from improved zirconia powders?
Various industries benefit from enhanced zirconia powders, including dental (for crowns and bridges), electronics (as insulators), and aerospace (for high-performance components). The improved properties of treated zirconia make it suitable for applications that demand high strength, chemical stability, and thermal resistance.